|
(21), (22) Заявка: 2001124870/04, 12.09.2001
(24) Дата начала отсчета срока действия патента:
12.09.2001
(45) Опубликовано: 27.08.2003
(56) Список документов, цитированных в отчете о поиске:
RU 2136703 C1, 10.09.1999. DE 1570240 A, 05.03.1970. DE 3108279 A1, 16.09.1982. US 4246152 A, 20.01.1981. RU 2059663 C1, 10.05.1996. RU 2114130 C1, 27.06.1998.
Адрес для переписки:
445653, Самарская обл., г. Тольятти, Поволжское ш., 32, ОАО “Тольяттиазот”, С.В.Афанасьеву
|
(71) Заявитель(и):
Открытое акционерное общество “Тольяттиазот”
(72) Автор(ы):
Махлай В.Н., Афанасьев С.В.
(73) Патентообладатель(и):
Открытое акционерное общество “Тольяттиазот”
|
(54) СПОСОБ ПОЛУЧЕНИЯ КАРБАМИДОФОРМАЛЬДЕГИДНОЙ СМОЛЫ
(57) Реферат:
Изобретение относится к получению карбамидоформальдегидных смол, используемых в качестве сырья при производстве вспененных теплоизоляционных материалов. Способ получения карбамидоформальдегидной смолы заключается в том, что конденсацию карбамидоформальдегидного концентрата и карбамида в течение всего процесса ведут в присутствии буферной добавки – кубового остатка моноэтаноламинной очистки производства аммиака, вводимой на щелочной стадии перед загрузкой первой порции карбамида, затем полученную смолу модифицируют амином и охлаждают. Технической задачей является оптимизация условий синтеза карбамидоформальдегидных смол с одновременным улучшением их качества. 1 табл.
Изобретение относится к получению карбамидоформальдегидных смол, используемых в качестве сырья при производстве вспененных теплоизоляционных материалов. Последние отличаются улучшенными теплофизическими характеристиками и невысокой стоимостью, что делает их конкурентоспособными на рынке пенопластов.
Известен метод получения карбамидоформальдегидной смолы [Доронин Ю.Г., Свиткина М.М., Мирошниченко С.Н. Синтетические смолы в деревообработке. – М. : Лесная промышленность, 1970, с.41-49], включающий в себя четыре основные стадии: получение метилольных производных мочевины (форконденсата) в слабощелочной или нейтральной среде при температуре 80 – 100oС продолжительностью 30-60 мин и мольном отношении формальдегида и карбамида 1,97-2,0, конденсацию смолообразных продуктов в кислой среде при рН 4,0-5,5 в течение 20-60 мин, концентрированные смолы под вакуумом при рН 6,0-7,5 и температуре 65-75oС, доконденсацию реакционной смеси с дополнительной порцией карбамида при 60-65oС, рН 6,5-7,5 в течение 30 мин до конечного мольного отношения формальдегида и мочевины 1,3-1,66. В процессе охлаждения готовой смолы ее стабилизируют аммиачной водой, диэтиленгликолем либо тетраборатом натрия.
Недостатком указанного способа является его многостадийность и продолжительность, что снижает производительность технологического оборудования, а также невысокая конверсия по формальдегиду, так как надсмольная вода на стадии концентрирования смолы содержит до 5-8 мас.% непрореагировавшего формальдегида.
Получаемые по этому способу смолы характеризуются повышенной концентрацией метанола, что препятствует выпуску экологически чистой продукции на их основе.
Известен метод получения карбамидоформальдегидной смолы из карбамидоформальдегидного концентрата (кф-концентрата), содержащего 55% “общего” формальдегида и 21% “общего” карбамида [RU 2059663, кл. С 08 G 12/12, 1996]. Он основан на добавлении к кф-концентрату первой порции карбамида с целью установления мольного отношения формальдегид : карбамид (Ф:К) = 2,0, прогреве реакционной смеси при 40oС в течение двух часов, вводе 10%-ного раствора уксусной кислоты для снижения рН смеси до 5,2 и проведение кислой конденсации при 90oС до достижения вязкости 1000 МПа с. После этого рН реакционной массы устанавливают на уровне 7,5, вводят вторую порцию карбамида и при 60oС в течение одного часа завершают процесс доконденсации.
К недостаткам данного способа следует отнести повышенную вязкость карбамидоформальдегидной смолы на стадии кислой конденсации, пониженную реакционную способность готового карбамидоформальдегидного связующего, характеризуемой показателем “время желатинизации”, трудность управления процессом синтеза смолы.
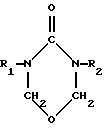 где R1 и R2 – H, CH2OH, и 1-5% триазинонов общей формулы 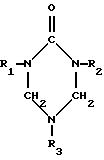 где R1 и R2 – H, CH2OH; R3 – H, CH3.
Синтез карбамидоформальдегидной смолы осуществляют путем конденсации карбамидоформальдегидного концентрата с первой порцией карбамида в присутствии регулятора вязкости – добавки деминерализованной воды или 5%-ного водного раствора метанола с рН 7,5-9,0, в течение 10 минут при 90oС с рН 7,6-8,8 до достижения мольного отношения формальдегид : карбамид = 2,0. По завершении щелочной стадии проводят быстрое охлаждение реакционной смеси до (80 2)oС, ввод кислого агента с целью снижения рН до уровня 5,0 и менее, проведение при (81 2)oС кислой конденсации до начала коагуляции смолы, подщелачивание и одновременный ввод буферной добавки и второй порции карбамида до мольного отношения Ф:К = 1,1-1,4 и завершение доконденсации при (66 2)oС в течение 30 минут.
Недостаток данного технического решения состоит в том, что используемый карбамидоформальдегидный концентрат при малом содержании примесей (метанола, формиата натрия и др.) обладает повышенной реакционной способностью, особенно на стадии кислой конденсации, что затрудняет управление процессом получения высоковязкой смолы при пониженных значениях рН. К тому же синтезируемая на его основе смола малопригодна для изготовления карбамидоформальдегидного пенопласта с требуемыми физико-механическими показателями.
Целью изобретения является оптимизация условий синтеза карбамидоформальдегидных смол с одновременным улучшением их качества.
Это достигается тем, что в известном способе с целью уменьшения колебаний рН и улучшения свойств смолы ее синтез в течение всего процесса ведут в присутствии стабилизирующей буферной добавки – кубового остатка моноэтаноламинной очистки производства аммиака, вводимой в кф-концентрат на щелочной стадии перед загрузкой первой порции карбамида, а доконденсацию проводят до достижения мольного отношения формальдегид : карбамид = 1,67-1,86 с последующей модификацией образовавшегося продукта амином.
Сущностью предлагаемого решения является синтез высокомольных карбамидоформальдегидных смол путем конденсации карбамидоформальдегидного концентрата, содержащего 0,02-0,3 мас.% буферной добавки с первой порцией карбамида в присутствии регулятора вязкости – деминерализованной воды или водного раствора метанола с рН 7,5-9,0 – в течение 10 минут при (88 3)oС и рН 7,6-9,0 до достижения мольного отношения Ф:К = 2.
По завершении щелочной стадии следует быстрое охлаждение реакционной массы до (80 2)oС, ввод кислого агента с целью снижения рН до 3,8-5,0, проведение при (80 2)oС кислой конденсации в течение 20-50 минут до начала коагуляции смол, ввод второй порции карбамида для установления конечного мольного отношения Ф: К = 1,67-1,86, завершение доконденсации при (66 2)oС в течение 30 минут, охлаждение смол и их модификация водным раствором амина при (38 6)oС.
Предлагаемое техническое решение отличается от известных тем, что процесс получения карбамидоформальдегидных смол с мольным отношением Ф:К = 1,67-1,86 проводят в присутствии кубового остатка моноэтаноламинной очистки производства аммиака, вводимого на стадии щелочной конденсации в количестве 0,02-0,30 мас. % в расчете на карбамидоформальдегидный концентрат и регулирующего реакционную способность системы с целью избежания нежелательного ее перехода в твердое состояние при добавлении кислого агента (муравьиной кислоты, хлористого аммония и пр.), причем за доконденсацией следует модификация смол водным раствором амина.
Отличительная особенность предлагаемого технического решения состоит в том, что буферную добавку вводят на щелочной стадии конденсации, а синтез смолы ведут до мольного отношения формальдегид : карбамид = 1,67-1,86, вводя на завершающей стадии 2-4 мас.% аминного модификатора от взятого количества кф-концентрата.
Введение амина в смолу существенно изменяет ее свойства за счет прививки аминосодержащих функциональных групп, что способствует возникновению солевых связей при отверждении смоляного состава многоосновными кислотами.
Предлагаемое изобретение иллюстрируется следующими примерами: карбамидоформальдегидный концентрат применяют в виде водной композиции, содержащей 41,5-59,0% “общего” формальдегида и 21,0-26,0% “общего” карбамида. Мольное отношение Ф:К = 3,2-5,4.
Кубовый остаток моноэтаноламинной очистки является промышленным отходом производства аммиака, в состав которого входят: моноэтаноламин (55 5)%, производные имидазолидона 8-10%, вода – остальное.
Для нейтрализации и подкисления реакционной смеси используют водные растворы едкого натра, муравьиной кислоты, хлористого аммония и другие основания и кислоты.
Сравнительная характеристика смол, изготовленных по примерам осуществления предлагаемого способа и по прототипу, представлена в таблице.
ПРИМЕР 1.
В реактор емкостью 5 м3 загружают 2300 кг кф-концентрата, содержащего 54,9% “общего” формальдегида, 22,7% “общего” карбамида и 22,4% воды. В него же добавляют 800 кг деминерализованной воды и 4 кг кубового остатка моноэтаноламинной очистки, очистки производства аммиака, и содержимое нагревают до 30-40oС. pН кф-концентрата должен составлять при этом 7,5-8,5. В случае несоответствия рН данному значению его доводят до требуемого уровня добавкой небольшого количества 10%-ного раствора едкого натра.
После этого в реактор подают первую порцию карбамида до достижения мольного отношения Ф: К = 2,0 и конденсационный раствор при интенсивном перемешивании нагревают до 90-92oС и выдерживают при данной температуре в течение 10 минут.
По завершении щелочной конденсации температуру реакционной смеси снижают до (80 2)oС и в реактор из мерника вводят 20 кг 10%-ного раствора хлористого аммония. Конец поликонденсации определяют по технологической пробе: в химический стакан с 50 см3 воды, охлажденной до 12-14oС, добавляют 3 см3 реакционной массы. Конденсацию прекращают после появления устойчивой мути.
По завершении кислой стадии поликонденсации содержимое реактора нейтрализуют 10%-ным раствором едкого натра до рН 7,3-7,8, добавляя его из мерника в количестве 17 кг, и вводят вторую порцию карбамида для достижения мольного отношения Ф:К = 1,72.
Температура реакционной смеси самопроизвольно снижается до (66+2)oС и поддерживается на этом уровне в течение 30 минут.
Смолу охлаждают до (38 6)oС и модифицируют 110 кг 25%-ного раствора аммиака в воде, вводимого в течение 5 минут. Температуру модифицированной смолы доводят до 20 – 25oС и перекачивают в емкость на хранение.
ПРИМЕР 2.
Условия конденсации по примеру 1.
В качестве модифицирующей добавки вместо аммиака взят 50%-ный водный раствор капролактама в количестве 150 кг.
ПРИМЕР 3.
Условия конденсации по примеру 1.
Для модификации взята смесь 75 кг 50%-ного водного раствора капролактама и 55 кг 25%-ной аммиачной воды.
ПРИМЕР 4.
Условия конденсации по примеру 1.
В качестве карбамидоформальдегидного концентрата использован продукт, содержащий 27,3% “общего” карбамида, 43,7% “общего” формальдегида, остальное вода.
Из описания изобретения и таблицы видно, что по заявленному техническому решению удается увеличить длительность кислой стадии конденсации и получать высококачественные модифицированные карбамидоформальдегидные смолы, пригодные для изготовления пенопластов.
Формула изобретения
Способ получения карбамидоформальдегидной смолы путем конденсации карбамидоформальдегидного концентрата с первой порцией карбамида в присутствии регулятора вязкости и нагревания в водном растворе с переменной кислотностью с последующей доконденсацией образовавшегося продукта с дополнительным количеством карбамида в присутствии буферной добавки при исходном и конечном мольном отношении карбамида и формальдегида 1: (1,9-2,1) и 1: (1,67-1,86) соответственно и охлаждении готовой смолы, отличающийся тем, что конденсацию карбамидоформальдегидного концентрата и карбамида в течение всего процесса ведут в присутствии буферной добавки – кубового остатка моноэтаноламинной очистки производства аммиака, вводимой на щелочной стадии перед загрузкой первой порции карбамида в количестве 0,02-0,30 мас. % в расчете на карбамидоформальдегидный концентрат, а после доконденсации смолы ее модифицируют 2-4 мас. % амина в расчете на карбамидоформальдегидный концентрат.
РИСУНКИ
|
|