|
(21), (22) Заявка: 2001124489/02, 05.09.2001
(24) Дата начала отсчета срока действия патента:
05.09.2001
(45) Опубликовано: 10.08.2003
(56) Список документов, цитированных в отчете о поиске:
SU 1061889 A, 23.12.1983. RU 2082524 C1, 27.06.1997. RU 2118219 C1, 27.08.1998. GB 792242, 26.03.1958. ЕР 1055465 А2, 29.11.2000.
Адрес для переписки:
107120, Москва, Гжельский пер., 13а, комн.51, М.А. Бабурину
|
(71) Заявитель(и):
Общество с ограниченной ответственностью “Технощит”
(72) Автор(ы):
Бабурин М.А., Сизов Е.С., Сизов В.С.
(73) Патентообладатель(и):
Общество с ограниченной ответственностью “Технощит”
|
(54) СПОСОБ ИЗГОТОВЛЕНИЯ РАЗНОТОЛЩИННЫХ ЛИСТОВЫХ ИЗДЕЛИЙ
(57) Реферат:
Изобретение относится к обработке металлов давлением и может быть использовано, например, при изготовлении панелей, лючков и других листовых деталей с утолщенными кромками, учитывающими их снижение прочности в зоне термического влияния при выполнении сварочных работ с соседними деталями. Способ изготовления разнотолщинных листовых изделий включает создание деформации сдвига в направлении силового воздействия на заготовку плоскими бойками в плоской листовой заготовке постоянной толщины, при этом проводят предварительную штамповку плоской листовой заготовки в полый полуфабрикат с выштамповкой в форме усеченного конуса. Полученный полуфабрикат помещают в пакет между двумя формообразующими элементами, которые выполнены равновысотными в осевом направлении с наружным диаметром До и с внутрипакетными рабочими поверхностями, контактирующими с соответствующими поверхностями полуфабриката. Противоположные поверхности последних для круглых изделий в плане выполняют по форме усеченных конусов. Суммарную высоту в осевом направлении полученного пакета из формообразующих элементов и полуфабриката принимают постоянной и равной (0,2-0,3) До. Затем проводят осаживание полученного пакета в контейнере диаметром До, преобразуя исходную толщину полуфабриката в утолщенную часть изделия с образованием переходных зон утолщений. Техническим результатом изобретения является устранение отмеченных недостатков ближайшего аналога при изготовлении разнотолщинных листов и заготовок, повышение коэффициента использования металла, а также снижение трудоемкости механообработки при изготовлении изделий. 5 ил.
Изобретение относится к обработке металлов давлением и может быть использовано, например, при изготовлении панелей, лючков и других листовых деталей с утолщенными кромками, учитывающими их снижение прочности в зоне термического влияния при выполнении сварочных работ с соседними деталями.
Известно техническое решение по изготовлению разнотолщинных листовых изделий за счет образования утолщений на кромках листов путем осадки металла, например, рабочим роликом в закрытую полость между плоским основанием и прижимной планкой с использованием гидравлического прижимного устройства, выполненного в виде системы роликов, расположенных по обе стороны листа напротив рабочего ролика [1]. Недостатком этого технического решения является сложность оборудования для осуществления осадки металла с наличием самостоятельных приводов прижима заготовки, осадки металла и необходимость регулирования силовыми и скоростными параметрами утолщения кромок листов.
Наиболее близким к предлагаемому изобретению по технической сущности и достигаемому эффекту является способ изготовления разнотолщинных листовых изделий, при котором создание деформаций сдвига в заготовке в направлении силового воздействия на заготовку обеспечивает получение толщин в листе, разнящихся в 2,0 и более раза [2].Однако отмеченную разнотолщинность получают, во-первых, в полом листовом изделии, а не в плоской листовой заготовке и, во-вторых, эту разнотолщинноcть получают за счет утонения исходного материала, а не за счет его утолщения, что значительно ограничивает возможности способа по прототипу.
Технический результат, достигаемый при использовании изобретения, заключается в устранении отмеченных недостатков прототипа при изготовления разнотолщинных листов и заготовок, в повышении коэффициента использования металла, а также в снижении трудоемкости механообработки при изготовлении изделий.
Достижение указанного технического результата от использования разработанного изобретения обеспечивается тем, что способ изготовления разнотолщинных листовых изделий включает создание деформации сдвига в направлении силового воздействия плоскими бойками в плоской листовой заготовке постоянной толщины, помещение в пакет между двумя деформируемыми формообразующими элементами и осаживание в контейнере между плоскими бойками с сопутствующим изменением исходной толщины до требуемой толщины изделия, при этом проводят предварительную штамповку плоской листовой заготовки в полый полуфабрикат с выштамповкой в форме усеченного конуса, образующую которого наклоняют под углом к его оси согласно зависимости: = arcsin(So/Sу), причем малое основание усеченного конуса диаметром d располагают над большим основанием диаметром D на высоте Нпф, устанавливаемой по формуле: Hпф = [(Bу+2 Bп) cos -So (1-sin ))]/sin , в пакет между двумя формообразующими элементами помещают полученный полуфабрикат, формообразующие элементы выполняют равновысотными в осевом направлении с наружным диаметром До и с внутрипакетными рабочими поверхностями, контактирующими с соответствующими поверхностями полуфабриката, а противоположные поверхности последних в плане выполняют по форме усеченных конусов с диаметрами оснований D и d и высотой между ними Нпф, причем суммарную высоту H в осевом направлении полученного пакета из формообразующих элементов и полуфабриката принимают постоянной и равной: H = (0,2-0,3) Дo, после чего осаживание полученного пакета проводят в контейнере диаметром До, преобразуя исходную толщину So полуфабриката в утолщенную часть Sy изделия с образованием переходных зон утолщений от So к Sy по линейному закону на участках шириной Вп согласно формулам: Bп = Rн cos и Sу = So/sin , где So – исходная толщина полуфабриката; Sy – толщина изделия; Вп – ширина зоны переходной толщины; By – ширина утолщенной части изделия; H – суммарная толщина формообразующих элементов с полуфабрикатом; Нпф – высота выштамповки в полуфабрикате; До – диаметр контейнера, обжимных бойков, полуфабриката и формообразующих элементов; D – диаметр большого основания усеченного конуса; d – диаметр малого основания усеченного конуса; – угол наклона стенки полуфабриката к оси устройства; Rн – наружный радиус изгиба стеночной части полуфабриката.
Изобретение поясняется чертежами, где показано: на фиг. 1 – продольное сечение устройства для утолщения кромок листов в исходном положении; на фиг.2 – то же в положении перед началом штамповки; на фиг.3 – то же в положении после окончания штамповки; на фиг.4 – то же в положении перед удалением утолщенного листа c формоизменяющими элементами из устройства; на фиг.5 – расчетная схема для определения параметров утолщения листов.
Согласно фиг. 1-5 способ изготовления разнотолщинных изделий осуществляется следующим образом. Сначала штампуют листовую заготовку в обычных штампах или на токарно-давильном станке в равнотолщинный полуфабрикат 1 (см. фиг. 1) в виде чаши диаметром До, толщина которой во фланцевой, донной и стеночной частях одинакова и равна исходной толщине заготовки Sо.
После этого полуфабрикат 1 собирают с предварительно изготовленными (отштампованными или литыми) формообразующими элементами 2 и 3 в пакет диаметром До и суммарной толщиной H и устанавливают его на нижний боек 4, прикрепленный к столу пресса 5. При рабочем ходе пресса сначала опускается вниз наружный ползун пресса 6 c контейнером 7, а затем – внутренний ползун пресса (условно не показан) с верхним бойком 8 до соприкосновения с верхним фомообразующим элементом 2 (см. фиг.2). Дальнейшее опускание ползуна пресса с верхним бойком 8 приводит к пластической деформации формообразующих элементов 2 и 3 с полуфабрикатом 1 и в крайнем нижнем положении верхнего бойка 8 они принимают вид согласно фиг.3, в результате чего формообразующие элементы принимают плоскую форму 9 и 10, а полуфабрикат 1 штампуется в плоское изделие 11, при этом фланцевая часть 12 и донная часть 13 полуфабриката 1 (находясь в прижатом состоянии между плоскими участками формообразующих элементов 9 и 10) практически не деформируются. Стеночная же часть 14 полуфабриката 1 при снижении его фланцевой части 12 относительно донной части 13 пластически деформируется в утолщенную часть 15 изделия 11 за счет деформаций сдвига в направлении силового воздействия на пластически деформируемый пакет из формообразующих элементов 2 и 3 с полуфабрикатом 1 (см. фиг.3). После окончания изготовления изделия 11 наружному ползуну пресса 6 с контейнером 7 сообщают перемещение в крайнее верхнее положение и затем поднимают вверх плоский боек 8. Оставшиеся на плите 4 сдеформированные формообразующие элементы 9 и 10 вместе с отштампованным изделием 11 удаляют из рабочей зоны пресса: первые для переплавки их в новые формообразующие элементы 2 и 3, а изделие 11 – для последующей механообработки, при этом металлом для формообразующих элементов могут служить легкоплавкие пластически деформируемые металлы, например, сплав Вуда (Тпл=60oС), сплав Гутри (Тпл=45oС), сплав Липовица (Тпл= 70oС) и др.[3]. Для предложенного способа изготовления разнотолщинных изделий применение легкоплавких металлов с цинковыми добавками по [4] имеет ряд технологических преимуществ.
Во-первых, он дешевле других сплавов, т.к. содержит меньше висмута, а дорогостоящий компонент – олово в нем отсутствует.
Во-вторых, температура плавления этого сплава ниже 100oС и поэтому для выплавления этой рабочей среды из отштампованного пакета с изделием и для изготовления новых формообразующих элементов можно применять кипящую воду.
В-третьих, содержание в легкоплавком металле по [4] цинка в 1,0, 2,0 и 3,0% обеспечивает твердость по Бриннелю соответственно в 13,9, 15,1 и 17,0 НВ [4], что позволяет применять этот сплав при штамповке разнотолщинных изделий с широким диапазоном механических свойств листовых заготовок.
Таким образом для осуществления разработанного способа не требуются жесткие носители форм изделий и поэтому переформовка равнотолщинного полуфабриката в разнотолщинное изделие осуществляется с использованием деформаций сдвига, направление и величину которым задают охватывающими полуфабрикат формообразующими элементами 2 и 3.
При диаметре контейнера 7, верхнего и нижнего бойков 8 и 4, а также полуфабриката 1 с формообразующими элементами 2 и 3, равным До, суммарную высоту H формообразующих элементов 2 и 3 вместе с толщиной фланца полуфабриката 1 следует принимать в пределах H = (0,2 0,3) Дo, (1) т. к. при H <0,2 Дo возможно искривление стеночных участков формообразующих элементов 2, 3 с полуфабрикатом 1 и, как следствие, неуправляемое утолщение изделия, а при H >0,3 Дo имеет место нецелесообразное повышение усилия деформирования рассматриваемого пакета.
Расчетная схема на фиг.5 позволяет установить соответствующие параметры осуществления способа изготовления разнотолщинных изделий из полуфабриката постоянной толщины (Sо = сonst).
В связи с тем, что стеночная часть 14 полуфабриката 1 с исходной толщиной Sо наклонена к оси устройства (или, что то же, к направлению силового воздействия на полуфабрикат 1) под углом , то толщина стенки Sу полуфабриката в этом направлении (см. отрезок “dg”) будет: Sy = dg = So/sin (2).
Значение промежуточной толщины S согласно фиг.5 записывается в виде , откуда, как и следовало ожидать, при в = 0 имеем толщину в донной части изделия S = So (1+0/tg = So (4) а при = 90- (т.е. в начале образования стеночной части полуфабриката) получаем: 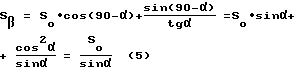 Графоаналитический метод решения уравнения (3) для углов наклона стенки полуфабриката 1 к оси устройства =30o, 45o, 60o показывает, что переход толщины Sо к Sу и толщины Sу к Sо (см. эпюры S = f( ) для =30o, 45o и 60o на фиг.5) при наружном радиусе скругления стеночной части полуфабриката 1 с его донной и фланцевой частями Rн = Sо (а также и при внутреннем радиусе скругления Rвн = 0) происходит плавно и практически линейно на участках шириной Bп = So sin = So sin(90- ) = So cos (6) Для установления геометрических параметров полуфабриката 1 и формообразующих элементов 2 и 3 необходимо определить высоту выштамповки Нпф в полуфабрикате 1, которая согласно фиг.5 может быть представлена зависимостью: Нпф = OA-OB = (By+2 Bп)/tg -(Oo -So) или, имея в виду, что tg = sin /cos ,Oo = o d/sin = So/si , получаем Нпф = [(By+2 Bп) cos -So (1-sin )]/sin (7) Представленные данные позволяют установить геометрические параметры как исходной листовой заготовки и полуфабриката 1, так и формообразующих элементов 2 и 3 для получения разнотолщинных изделий круглой, прямоугольной и др. формы в плане.
Рассмотрим пример изготовления предложенным способом лючка круглой формы в плане при наружном и внутреннем диаметрах его утолщения Dн=200 мм и Dвн= 180 мм (ширина утолщения Ву=(Dн-Dвн)/2=(200-180)/2=10 мм) и ширине фланца Вфл= 5 мм из листового алюминиевого сплава АМг6М ( в = 34 кгс/мм2) толщиной Sо=2 мм при его утолщении до Sу=4 мм (см. фиг.1, 2 и 5) с использованием для формообразующих элементов 2 и 3 легкоплавкого металла по [4] с цинковой добавкой в 1% ( в.ф.э = 7 кгс/мм2). Полуфабрикат 1 и формообразующие элементы 2 и 3 в форме усеченных конусов согласно фиг.1,2 и 5 должны иметь стенку под углом наклона к оси изделия, величина которого определяется по формуле (2): sin = So/Sy = 0,5 или = arcsin0,5 = 30 . При этом ширину переходной зоны Вп устанавливают (при Rн = Sо=2 мм) по формуле (6):  Таким образом ширина зоны утолщения изделия 11 определяется наружным и внутренним диаметрами D= Dн+2 Вп= 200+2 1,73= 203,46 мм и d=Двн-2 Вп=180-2 1,73= 176,54 мм (или ), а наружный диаметр полуфабриката 1 (следовательно, и контейнера 7) составляет До=D+2 Вф=203,46+2 5=213,46 мм.
При этом высота выштамповки в полуфабрикате 1 согласно формуле (7) составляет: 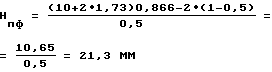 Геометрические параметры изделия 11 почти полностью определяют соответствующие параметры полуфабриката 1 за исключением того, что параллельные линии, определяющие утолщение Sу в листе толщиной Sо, направляют параллельно друг другу, но под углом к оси симметрии изделия из точек 0’и 0″, с последующим сопряжением их с соответствующими линиями в донной и фланцевой частях полуфабриката 11 радиусом Rн=Sо из точек 0′ и 0″.
Установленные параметры наружной поверхности полуфабриката 1 полностью определяют наружную и внутреннюю поверхности верхнего формообразующего элемента 2, причем наружная поверхность последнего должна быть в форме усеченного конуса при наружном его диаметре, равном До, малое и большое основания (диаметры которых соответственно будут D и d) должны отстоять друг от друга по высоте на расстоянии Нпф, а соответствующие параметры внутренней поверхности формообразующего элемента 2 определяются параметрами наружной поверхности полуфабриката 1, находящегося в контакте с формообразующим элементом 2.
Аналогично определяются геометрические параметры нижнего формообразующего элемента 3 по соответствующим данным рабочих поверхностей полуфабриката 1.
Для получения полуфабриката 1 в виде усеченного конуса (по [5], с.90, номер формулы 14) определяют диаметр заготовки Dв, которую штампуют свинцом по металлической матрице (согласно [5], с.314, рис.276), после чего из легкоплавкого металла по [4] изготавливают формообразующие элементы 2 и 3, собирают их с полуфабрикатом 1 в пакет, который помещают на нижний боек 4, и при рабочем ходе пресса осаживают верхним бойком 8 в контейнере 7. Полученное изделие 11 отправляют на последующую механообработку, а формообразующие элементы 9 и 10 на переплавку в новые элементы 2 и 3.
Усилие пресса, потребное для осуществления предложенного способа изготовления разнотолщинных изделий, определяется площадью контейнера в плане Fк = /4 D2o и пределом прочности материала формообразующих элементов в.ф.э = 7 кгс/мм2 т.е.
Рпр=Fк Ов.ф.э. = 0,785 213,5 7=317688 кгс=317,7 тнc Таким образом по приведенным данным устанавливают как геометрические параметры заготовки для штамповки полуфабриката, самого полуфабриката, формообразующих элементов и штамповой оснастки для осуществления предложенного способа изготовления разнотолщинных изделий, так и силовые параметры оборудования для его осуществления.
Аналогично изготавливаются рассматриваемым способом и неосесимметричные изделия различной формы в плане.
Источники информации 1. Авт. св. СССР 168863, МПК В 21 D, БИ 23, опубл. 22.11.1963.Штамп для образования утолщений на кромках листов. Сизов Е.С. и др.
2. Ав. св. СССР 1061889, B 21 D 22/20, БИ 47, опубл. 23.12.83. Способ штамповки полых деталей из плоских листовых заготовок. Сизов Е.С.
3. Х.М. Мунасипов. Исследование и разработка легкоплавких сплавов и неметаллических композиций для крепления заготовок лопаток при их механической обработке. Приложение к журналу АП 8.
4. Авт. св. CCCP 1226858. Легкоплавкий металл на основе висмута. (Авторы: Х.М. Мунасипов, В.К. Доронченков, О.А. Московский, Ю.М. Леонтьев).
5. В. П. Романовский. Справочник по холодной штамповке. – Л.: Машиностроение, 1973.
Формула изобретения
Способ изготовления разнотолщинных листовых изделий, включающий создание деформации сдвига в направлении силового воздействия плоскими бойками в плоской листовой заготовке постоянной толщины, помещение в пакет между двумя деформируемыми формообразующими элементами и осаживание в контейнере между плоскими бойками с сопутствующим изменением исходной толщины до требуемой толщины изделия, отличающийся тем, что проводят предварительную штамповку плоской листовой заготовки в полый полуфабрикат с выштамповкой в форме усеченного конуса, образующую которого наклоняют под углом к его оси согласно зависимости = arcsin(So/Sу), причем малое основание усеченного конуса диаметром d располагают над большим основанием диаметром D на высоте Нпф, устанавливаемой по формуле Hпф = [(Bу+2 Bп) cos -So (1-sin ))]/sin , в пакет между двумя формообразующими элементами помещают полученный полуфабрикат, формообразующие элементы выполняют равновысотными в осевом направлении с наружным диаметром До и с внутрипакетными рабочими поверхностями, контактирующими с соответствующими поверхностями полуфабриката, а противоположные поверхности последних в плане выполняют по форме усеченных конусов с диаметрами оснований D и d и высотой между ними Нпф, причем суммарную высоту H в осевом направлении полученного пакета из формообразующих элементов и полуфабриката принимают постоянной и равной H = (0,2-0,3) Дo, после чего осаживание полученного пакета проводят в контейнере диаметром До, преобразуя исходную толщину So полуфабриката в утолщенную часть Sy изделия с образованием переходных зон утолщений от So к Sy по линейному закону на участках шириной Вп согласно формулам Bп = Rн cos и Sу = So/sin , где So – исходная толщина полуфабриката; Sy– толщина изделия; Вп – ширина зоны переходной толщины; By – ширина утолщенной части изделия; H – суммарная толщина формообразующих элементов с полуфабрикатом; Нпф – высота выштамповки в полуфабрикате; До – диаметр контейнера, обжимных бойков, полуфабриката и формообразующих элементов; D – диаметр большого основания усеченного конуса; d – диаметр малого основания усеченного конуса; – угол наклона стенки полуфабриката к оси устройства; rн – наружный радиус изгиба стеночной части полуфабриката.
РИСУНКИ
MM4A Досрочное прекращение действия патента Российской Федерации на изобретение из-за неуплаты в установленный срок пошлины за поддержание патента в силе
Дата прекращения действия патента: 06.09.2003
Извещение опубликовано: 20.11.2004 БИ: 32/2004
|
|