|
(21), (22) Заявка: 2002107019/04, 20.03.2002
(24) Дата начала отсчета срока действия патента:
20.03.2002
(45) Опубликовано: 27.05.2003
(56) Список документов, цитированных в отчете о поиске:
GB 649680 А, 31.01.1951. SU 1836321 А, 23.08.1993. SU 363690 А, 25.12.1972.
Адрес для переписки:
630090, г.Новосибирск, пр. Акад. Лаврентьева, 5, Институт катализа им. Г.К. Борескова, Патентный отдел, Т.Д.Юдиной
|
(71) Заявитель(и):
Институт катализа им. Г.К. Борескова СО РАН
(72) Автор(ы):
Дубков К.А., Панов Г.И., Пармон В.Н., Староконь Е.В.
(73) Патентообладатель(и):
Институт катализа им. Г.К. Борескова СО РАН
|
(54) СПОСОБ ПОЛУЧЕНИЯ ЦИКЛОГЕКСАНОНА
(57) Реферат:
Изобретение относится к способу получения циклогексанона, который основан на реакции жидкофазного окисления циклогексена в циклогексанон закисью азота или ее смесью с инертным газом. Процесс ведут при температуре 150-350oС и давлении закиси азота 0,01-100 атм. Предпочтительно применяют катализатор и растворитель. Может быть использован рецикл отработанных газов. Технический результат – высокая селективность по целевому продукту и взрывобезопасность работы. 10 з.п.ф-лы, 5 табл.
Изобретение относится к способу получения циклогексанона, более конкретно к способу получения циклогексанона путем жидкофазного окисления циклогексена закисью азота N2O.
Циклогексанон является промежуточным продуктом для синтеза -капролактама и адипиновой кислоты, которые используются для производства полиамидных материалов найлон-6 и найлон-66. Он также широко применяется как растворитель жиров, красителей, природных и синтетических смол.
Основной способ промышленного производства циклогексанона состоит в жидкофазном окислении циклогексана кислородом воздуха. Процесс ведут в области 145-180oС при давлении 8-12 атм, используя в качестве катализатора соли кобальта [U.S. Pat. 3530185, 1970, К. Pugi]. При этом образуется смесь циклогексанона и циклогексанола, в которой доля циклогексанона составляет менее 50%.
Возможно также проведение процесса некаталитическим путем. В этом случае в реакционную смесь добавляют борную кислоту, которая связывает образующийся циклогексанол в виде эфира, подавляя таким путем образование побочных продуктов [U. S. Pat. 3932513, 1976, J.L. Russell]. Недостатком обоих вариантов процесса является значительное падение селективности реакции с увеличением конверсии циклогексана. Для поддержания суммарной селективности по циклогексанону и циклогексанолу на уровне 85-90% конверсия за проход не должна превышать 3-5%. Это ведет к большим затратам на выделение продуктов и рециркуляцию циклогексана.
Циклогексанон может быть получен также путем селективного каталитического дегидрирования циклогексанола [U.S. Pat. 3998884, 1976, С.A. Gibson] или путем гидрирования фенола [U.S. Pat. 3076810, 1963, R.J. Duggan et. al.; U. S. Pat. 4092360, 1978, Jan F. Van Peppen et. al.]. Однако эти методы не находят широкого применения из-за высокой стоимости исходных материалов.
В патенте GB Pat. 649, 680 (1951) заявлен способ окисления олефинов в карбонильные соединения закисью азота. Согласно этому способу, в частности, возможно получение циклогексанона путем окисления циклогексена. Недостатком этого способа является невысокая селективность по циклогексанону, а также жесткие условия реакции. (В патенте пример с циклогексеном ограничивается одним опытом, проведенным при температуре 300oС и давлении 500 атм).
Вторым серьезным недостатком этого способа является возможность образования воспламеняемых смесей. Чтобы исключить взрывоопасность, авторы патента предлагают дополнительно вводить в реакционную смесь насыщенные углеводороды. Однако, как показали более поздние исследования, смеси насыщенных углеводородов с N2O почти столь же взрывоопасны, как и смеси олефинов. Так, предельные концентрации пропилена в N20 составляют 1,8-26,8%, а предельные концентрации пропана 2,1-24,8% [G. Panetier, A.Sicard, V Symposium on Combustion, 620 (1955); Б.Б.Брандт, Л.А.Матов, А.И.Розловский, В.С.Хайлов, Хим. пром. , 1960, 5, с. 67-73]. Поэтому насыщенные углеводороды, несмотря на их меньшую реакционную способность, не могут служить средством для исключения взрывоопасности.
Настоящий патент раскрывает способ получения циклогексанона путем окисления циклогексена, который не имеет указанных недостатков. Согласно этому способу для повышения селективности реакцию ведут в более мягких условиях, когда циклогексен присутствует в виде жидкой фазы, в которой реакция окисления протекает с высокой селективностью. Излишнее повышение температуры и/или давления N2О является нежелательным, так как может приводить к понижению селективности за счет вклада газофазного окисления.
Взрывобезопасные условия работы по предлагаемому способу обеспечиваются добавлением в реакционную смесь инертного газа, не вступающего в реакцию с N2О, например такого, как азот, аргон, гелий, углекислый газ и т.д. либо их смесь. Роль инертного газа могут играть отходящие газы реакции. На разных стадиях процесса в зависимости от соотношения “циклогексен : закись азота”, доля инертного газа, необходимая для обеспечения взрывобезопасной работы, может быть различной и создаваться путем его раздельной подачи. С точки зрения простоты и максимальной безопасности процесса целесообразно иметь такое разбавление закиси азота инертным газом, чтобы реакционная смесь была невзрывоопасной при любом содержании циклогексена. Это условие выполняется, если содержание N2О в смеси с инертным газом составляет не более 25%. Применение такой смеси исключает возникновение взрывоопасных ситуаций на всех стадиях процесса.
Для уменьшения взрывоопасности в реакционную смесь могут добавляться ингибиторы горения, такие как трифторбромметан, дифторхлорбромметан, дибромтетрафторэтан и др.
В соответствии с данным изобретением окисление циклогексена в циклогексанон может быть осуществлено в широком интервале условий как в статическом, так и в проточном реакторе, который может быть изготовлен из стали, титана или другого подходящего материала. При этом могут быть использованы все известные технологические приемы, повышающие эффективность газожидкостных реакций.
В случае статического варианта процесса в автоклав загружают циклогексен в таком количестве, чтобы при температуре реакции он присутствовал в виде жидкой фазы. Затем подают закись азота или ее смесь с инертным газом, доводя давление до заданной величины. Количество N2O подбирают таким образом, чтобы ее давление при температуре реакции составляло 0,01-100 атм. Концентрацию инертного газа в смеси с закисью азота подбирают таким образом, чтобы она не превышала 99%. Реакцию ведут при температуре 150-350oС. Время реакции подбирается в зависимости от условий ее проведения, а также требований, предъявляемых к показателям процесса, и может изменяться от нескольких минут до нескольких десятков часов. При необходимости для обеспечения более глубокой конверсии циклогексена газовую фазу заменяют на новую порцию закиси азота и реакцию проводят повторно. В случае неполной конверсии закиси азота она в составе рециркулирующих газов может быть повторно использована для проведения реакции.
Предлагаемый процесс может осуществляться без растворителей. Однако возможно проведение процесса и с применением растворителей, которые могут выбираться из широкого круга веществ, применяемых в практике органического синтеза. Реакция с достаточно высокой скоростью протекает без катализатора, хотя может проводиться и в присутствии катализатора.
Предлагаемый способ получения циклогексанона не предполагает высокой чистоты исходных реагентов. Так, закись азота может быть использована как в чистом виде, так и с примесями различных газов, не оказывающими вредного влияния на показатели процесса. Циклогексен также может содержать примеси органических соединений, не оказывающих вредного влияния на показатели процесса.
Сущность предлагаемого изобретения иллюстрируется следующими примерами.
Примеры 1-6 Результаты этих примеров приведены в табл. 1 и показывают высокую селективность реакции жидкофазного окисления циклогексена в циклогексанон с использованием в качестве окислителя закиси азота.
Пример 1. В реактор объемом 100 см3 (фирма Parr), выполненный из нержавеющей стали и снабженный мешалкой, заливают 25 см3 циклогексена (Aldrich, 99%). Реактор продувают закисью азота и затем доводят ее давление до 25 атм. Реактор герметично закрывают, нагревают до 250oС и выдерживают при этой температуре в течение 5 час. После окончания реакции реактор охлаждают, измеряют давление и анализируют конечный состав газовой и жидкой фаз методами газовой хроматографии и хроматомасс-спектрометрии. Из полученных данных рассчитывают конверсию циклогексена (X) и селективность реакции по циклогексанону (S): 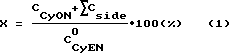 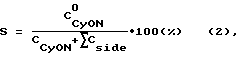 где С0 CyEN – начальная концентрация циклогексена; СCyON – концентрация циклогексанона в продуктах реакции; Cside – суммарная концентрация побочных продуктов. В случае больших конверсий величина Х может быть рассчитана также по разнице между начальной и конечной концентрациями циклогексена: 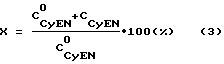 Пример 2 аналогичен примеру 1 с тем отличием, что реакцию ведут в течение 12 часов.
Пример 3 аналогичен примеру 1 с тем отличием, что реакцию ведут при 150oС в течение 23 часов.
Пример 4 аналогичен примеру 1 с тем отличием, что реакцию ведут при температуре 198oС в течение 15 часов.
Пример 5 аналогичен примеру 1 с тем отличием, что реакцию ведут при 220oС в течение 12 часов.
Пример 6 аналогичен примеру 1 с тем отличием, что реакцию ведут при 280oС в течение 3 часов.
Пример 7 Этот пример является сравнительным. Опыт проводят аналогично примеру 1 с тем отличием, что в реактор загружают 4 мл циклогексена. При такой загрузке весь циклогексен в условиях реакции находится в газовой фазе. В результате опыта конверсия циклогексена составила примерно 0,5%. Это говорит о том, что при данных условиях реакция в газовой фазе практически не идет.
Примеры 8-9 Эти примеры в сопоставлении с примерами 4 и 5 демонстрируют влияние концентрации закиси азота на показатели процесса (табл. 2). Концентрация закиси азота в реакционной смеси задается величиной ее начального давления при комнатной температуре .
Пример 8 аналогичен примеру 4 с тем отличием, что начальное давление закиси азота в этом опыте задают 40 атм.
Пример 9 аналогичен примеру 5 с тем отличием, что начальное давление закиси азота в этом опыте задают 10 атм.
Примеры 10-12 Примеры 10-12, результаты которых приведены в табл. 3, показывают возможность проведения процесса в присутствии катализатора.
Пример 10 аналогичен примеру 1 с тем отличием, что окисление циклогексена ведут 16,5 часов в присутствии 0.21 г цеолитного катализатора FeZSM-5. Цеолит (Si02/Al2O3=150, 0.56 маc.% Fe) готовят методом гидротермального синтеза с введением железа в исходный гель в виде FeCl3. После выжигания темплата и перевода цеолита в Н-форму образец прокаливают на воздухе при 550oС и затем подвергают термопаровой активации при 650oС [US Pat. 5672777, 1997, Kharitonov et al.].
Пример 11 аналогичен примеру 4 с тем отличием, что реакцию ведут 12 часов в присутствии 0.2 г Fe2O3/SiO2 (2.8 маc. % Fe2O3). Катализатор готовят путем пропитки SiO2 раствором FеС13, сушат при 110oС и прокаливают на воздухе при 500oС в течение 2 ч.
Пример 12 аналогичен примеру 4 с тем отличием, что реакцию ведут 12 часов в присутствии 0.5 г Rh/ZrO2 (1 маc. % Rh). Катализатор готовят путем пропитки ZrO2 раствором Rh(NO3)3, сушат при 110oС и прокаливают на воздухе при 500oС в течение 2 ч.
Примеры 13-16 Эти примеры показывают возможность окисления циклогексена с использованием различных растворителей (табл. 4).
Пример 13 аналогичен примеру 5 с тем отличием, что в реактор заливают 25 мл смеси циклогексена и гептана в объемном соотношении 1:1.
Пример 14 аналогичен примеру 13 с тем отличием, что вместо циклогексана используют ацетонитрил.
Пример 15 аналогичен примеру 13 с тем отличием, что вместо циклогексана используют изобутанол.
Пример 16 аналогичен примеру 13 с тем отличием, что вместо циклогексана используют воду.
Примеры 17-22 Примеры 17-22 приведены в табл. 5. Эти примеры показывают возможность проведения реакции с разбавленными смесями закиси азота.
Пример 17 аналогичен примеру 1 с тем отличием, что вместо чистой закиси азота в реактор подают ее смесь с инертным газом – азотом, в которой концентрация N2О составляет 70%. Начальное давление в реакторе (Рo) устанавливают 45 атм.
Пример 18 аналогичен примеру 17 с тем отличием, что концентрация N2O в смеси с азотом составляет 20%. Опыт проводят в течение 12 часов.
Пример 19 аналогичен примеру 18 с тем отличием, что начальное давление в реакторе устанавливают 80 атм. Опыт проводят при 220oС в течение 12 часов.
Пример 20 аналогичен примеру 19 с тем отличием, что концентрация N2О в смеси с азотом составляет 40%. Начальное давление смеси в реакторе устанавливают 40 атм.
Пример 21 аналогичен примеру 19 с тем отличием, что в качестве инертного газа вместо азота используют аргон и концентрация N2O в смеси с Аr составляет 50%. Начальное давление в реакторе устанавливают 30 атм.
Пример 22 аналогичен примеру 21 с тем отличием, что вместо аргона используют углекислый газ.
Пример 23 аналогичен примеру 19 с тем отличием, что концентрация N2O в смеси с азотом составляет 1%. Начальное давление смеси в реакторе устанавливают 200 атм.
Примеры 17-23 показывают, что циклогексен с высокой селективностью окисляется в циклогексанон с помощью закиси азота, разбавленной инертным газом. Содержание N2О в смеси с инертным газом может изменяться в широких пределах, включая область концентраций закиси азота 25% и менее, в которой исключается возможность взрывоопасных ситуаций при любых композициях с циклогексеном. Как показывают примеры 18 и 19 (табл. 5), реакция окисления циклогексена в циклогексанон в этой области протекает с высокой эффективностью.
Пример 24 Этот пример показывает возможность окисления циклогексена с использованием рециркулирующих газов.
Пример 24 аналогичен примеру 1 с тем отличием, что вместо чистой закиси азота в реактор сначала подают 12.5 атм N2O-содержащего газа, образовавшегося после окисления циклогексена согласно примеру 5. Затем в реактор добавляют чистую закись азота, доводя общее давление до 25 атм. Опыт проводят при 250oС в течение 5 часов. В результате опыта конверсия циклогексена составила 22% при селективности 95,8% В настоящем изобретении предложен новый способ получения циклогексанона, основанный на реакции жидкофазного окисления циклогексена закисью азота или ее смесью с инертным газом. Процесс обеспечивает высокую селективность, взрывобезопасность и является перспективным для промышленного применения.
Формула изобретения
1. Способ получения циклогексанона из циклогексена, отличающийся тем, что процесс осуществляют путем контакта жидкого циклогексена с закисью азота при температуре 150-350oС и давлении закиси азота 0,01-100 атм.
2. Способ по п. 1, отличающийся тем, что в реакционную смесь вводят инертный газ-разбавитель.
3. Способ по любому из пп. 1-2, отличающийся тем, что концентрация инертного газа в реакционной смеси не превышает 99%.
4. Способ по любому из пп. 1-3, отличающийся тем, что концентрацию инертного газа подбирают таким образом, чтобы исключить возможность образования взрывоопасных композиций на каждой стадии процесса.
5. Способ по любому из пп. 1-4, отличающийся тем, что реакцию проводят при температуре 150-199oС и давлении закиси азота 0,01-100 атм.
6. Способ по любому из пп. 1-5, отличающийся тем, что реакцию проводят при температуре 150-350oС и давлении закиси азота 0,01-20 атм.
7. Способ по любому из пп. 1-6, отличающийся тем, что реакцию проводят в присутствии катализатора.
8. Способ по любому из пп. 1-7, отличающийся тем, что реакцию проводят в присутствии растворителя.
9. Способ по любому из пп. 1-8, отличающийся тем, что закись азота содержит примеси других газов, не ухудшающих показатели процесса.
10. Способ по любому из пп. 1-9, отличающийся тем, что реакцию проводят в статическом или проточном варианте.
11. Способ по любому из пп. 1-10, отличающийся тем, что для проведения реакции используют рециркулирующие газы.
РИСУНКИ
|
|