|
(21), (22) Заявка: 2009123720/06, 22.06.2009
(24) Дата начала отсчета срока действия патента:
22.06.2009
(46) Опубликовано: 20.09.2010
(56) Список документов, цитированных в отчете о поиске:
RU 2344400 C1, 20.01.2009. RU 2006811 C1, 30.01.1994. RU 2259549 C1, 27.08.2005. DE 3510408 A1, 02.10.1986. JP 57042836 A, 10.03.1982.
Адрес для переписки:
454085, г.Челябинск, пр-кт Ленина, 75, ФГОУ ВПО “Челябинский государственный агроинженерный университет”, кафедра ЭА и ПО
|
(72) Автор(ы):
Куков Станислав Семенович (RU), Гриценко Александр Владимирович (RU)
(73) Патентообладатель(и):
Федеральное государственное образовательное учреждение высшего профессионального образования “Челябинский государственный агроинженерный университет” (RU)
|
(54) СПОСОБ БЕЗРАЗБОРНОЙ ДИАГНОСТИКИ СТЕПЕНИ ИЗНОСА ПОДШИПНИКОВ ДВИГАТЕЛЯ ВНУТРЕННЕГО СГОРАНИЯ
(57) Реферат:
Изобретение относится к области эксплуатации машин и может быть использовано при диагностировании двигателей внутреннего сгорания (ДВС). Способ диагностики степени износа подшипников двигателя внутреннего сгорания заключается в определении величины мгновенного давления в центральной масляной магистрали. Величина мгновенного давления определяется при работе в течение цикла под максимальной нагрузкой и последующего цикл без нагрузки. После определения производят сравнение участков осциллограммы, полученных при рабочем цикле диагностируемого цилиндра и нерабочем цикле. Измерение величины мгновенного давления производят в конце центральной масляной магистрали. Для снижения погрешности оценки технического состояния подшипников кривошипно-шатунного механизма дополнительно устанавливают кран (6) и дроссель (7). При помощи крана (6) и дросселя (7) устанавливают среднее давление в центральной масляной магистрали. Среднее давление в центральной масляной магистрали устанавливается независимо от степени износа отдельных подшипников (4). При указанных условиях определяют разность нормированных амплитуд мгновенных значений давления и сравнивают их с разностью нормированных амплитуд, полученных на эталонном двигателе. Путем сравнения нормированных амплитуд определяют степень износа любого из диагностируемых подшипников двигателя. С увеличением степени износа подшипников увеличивается приведенная разность нормированных амплитуд давлений. Технический результат заключается в возможности безразборного определения степени износа любого подшипника ДВС и повышении точности оценки технического состояния двигателя. 2 ил.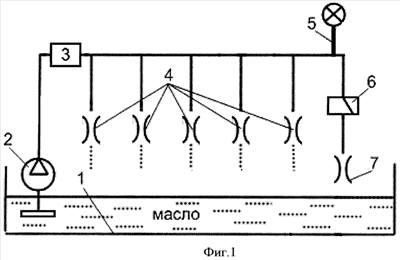
Изобретение относится к области эксплуатации машин и может быть использовано при диагностировании двигателей внутреннего сгорания (ДВС).
Известен ряд способов диагностики степени износа подшипников двигателя внутреннего сгорания.
Способ по патенту 2006811 (кл. G01M 15/00) используют при безразборной диагностике подшипников двигателя внутреннего сгорания. Он предусматривает установку двух манометров на выходе из нагнетательного насоса и на входе в диагностируемый участок при чистых фильтрах. При использовании метода измеряют величины давлений, определяют отношение первого давления при разности первого и второго давлений к второму давлению и сравнивают это отношение с его зависимостью от степени износа подшипников. Увеличение указанного отношения соответствует росту степени износа подшипников.
Однако этот способ, несмотря на всю свою простоту, не позволяет определить износ конкретного подшипника (невозможность селективной оценки), низкая достоверность диагностирования, малая информационная емкость способа.
Способ по патенту 2259549 (кл. G01M 15/00) используют при безразборной диагностике технического состояния двигателя внутреннего сгорания. Он предусматривает установку двух измерителей давления масла на входе и выходе из фильтра. При использовании метода задают режимы работы двигателя, измеряют показатели состояния диагностируемых систем двигателя, определяют отклонения показателей состояния, проводят вычисления и по результатам оценивают техническое состояние двигателя. Причем в качестве показателей состояния принимают параметры пульсаций давления среды. Способ отличается тем, что кривую пульсаций давления на входе и выходе фильтрующего элемента, диагностируемой системы, раскладывают в гармонический ряд. Строят амплитудные и фазовые частотные характеристики в заданном диапазоне частот, а сравнение проводят в диапазоне наибольшей чувствительности измеряемых частот, в качестве результата определяют величину и скорость отклонения амплитудных и фазовых частотных характеристик от эталонных, полученных при условии наиболее эффективной работы системы, и по ним определяют остаточный ресурс работы двигателя.
Данный способ не позволяет определить неисправности отдельных подшипников кривошипно-шатунного механизма ДВС, а также фактический износ подшипников коленчатого вала.
Принятый в качестве прототипа способ безразборной диагностики степени износа подшипников ДВС по патенту 2344400 (кл. G01M 15/00) заключается в измерении величины мгновенного давления в центральной масляной магистрали на участке масляной магистрали от фильтра до подшипников коленчатого вала при работе диагностируемых подшипников в течение цикла под максимальной нагрузкой в последующий цикл без нагрузки. При этом сравнивают участки осциллограммы, полученные при рабочем цикле диагностируемого цилиндра и нерабочем (достигаемым отключением следующего рабочего цикла). Затем определяют отношение амплитуд мгновенных значений давления при указанных условиях и сравнивают их с отношением амплитуд, полученных на эталонном двигателе (технически исправном). Определяют путем их сравнения степень износа любого из диагностируемых подшипников двигателя. Причем с увеличением степени износа подшипников увеличивается приведенное отношение.
Недостатком данного способа является удаленность датчика давления от коренных шеек коленчатого вала ДВС, которые в наибольшей степени подвержены износу (четвертая и пятая коренные шейки), т.к. наиболее удалены от масляного насоса и связанная с этим погрешность определения технического состояния этих шеек. А также влияние исходного уровня давления в центральной масляной магистрали на результат оценки, т.к. износ отдельных шеек может значительно уменьшать величину давления в центральной масляной магистрали. А отношение амплитуд мгновенных значений давления при тех же зазорах, но при меньшем давлении в центральной масляной магистрали будет несколько отличаться, что вносит погрешность в оценку технического состояния подшипников кривошипно-шатунного механизма. При этом также может быть внесена существенная погрешность при определении отношения амплитуд мгновенных значений давлений в связи с тем, что развертка осциллограммы давления на экране осциллографа может отличаться от измерения к измерению. Причем при меньшем значении зазора в подшипнике отношение амплитуд мгновенных значений давлений может быть больше, чем при большем зазоре в подшипнике.
Анализ известных способов позволяет сделать вывод о целесообразности поиска способа оценки технического состояния подшипников ДВС с сохранением преимуществ ранее существующих способов и возможностью определения технического состояния любого подшипника ДВС, независимо от их месторасположения в масляном тракте, а также исключении влияния удаленности датчика от наиболее подверженных износу шеек коленчатого вала и исходного уровня давления в центральной масляной магистрали для исключения погрешности при оценке технического состояния подшипников ДВС. Также для уменьшения погрешности, вызванной определением отношения амплитуд мгновенных значений давлений.
Целью изобретения является безразборное определение степени износа любого подшипника ДВС, независимо от месторасположения их в масляном тракте и повышение точности оценки технического состояния двигателя.
Эта цель достигается тем, что в предлагаемом способе диагностики степени износа подшипников ДВС определяют величину мгновенного давления в центральной масляной магистрали при работе диагностируемых подшипников в течение цикла под максимальной нагрузкой в последующий цикл без нагрузки. При этом сравнивают участки осциллограммы, полученные при рабочем цикле диагностируемого цилиндра и нерабочем цикле. В отличие от прототипа для повышения достоверности оценки технического состояния подшипников кривошипно-шатунного механизма измерение величины мгновенного давления производят в конце центральной масляной магистрали, а для снижения погрешности оценки технического состояния подшипников кривошипно-шатунного механизма дополнительно устанавливают кран и дроссель, при помощи которых устанавливают среднее давление в центральной масляной магистрали, независимо от степени износа отдельных подшипников. Определяют разность нормированных амплитуд мгновенных значений давления при указанных условиях и сравнивают их с разностью нормированных амплитуд, полученных на эталонном двигателе. Путем их сравнения определяют степень износа любого из диагностируемых подшипников двигателя: с увеличением степени износа подшипников увеличивается приведенная разность нормированных амплитуд давлений.
На фиг.1 представлена функциональная схема системы смазки двигателя, включающая нагнетательный насос 2 (фиг.1), маслосборник 1, фильтр 3, подшипники двигателя 4. На выходе из главной масляной магистрали установлены последовательно кран 6 и дроссель 7, через который часть масла сливается в маслосборник 1. В конце масляной магистрали установлен тензометрический датчик давления и измерительный комплекс MIC-400, обозначенные позицией 5, которые измеряют мгновенное давление масла.
Способ осуществляется следующим образом: при работе ДВС в главной масляной магистрали формируется давление, которое распространяется последовательно от масляного насоса 2 к фильтру 3, а далее – к подшипникам 4. При этом дополнительно предусматривается подсоединение в конце главной масляной магистрали крана 6 и дросселя 7, которые установлены последовательно. Как только установится частота вращения коленчатого вала двигателя на постоянном уровне (например, 880 мин-1) и стабилизируется величина давления в центральной масляной магистрали, которую измеряют датчиком давления 5, начинают открывать кран 6 и часть масла начинает утекать через дроссель 7. Для уменьшения погрешности, связанной с местом установки датчика давления, он устанавливается в конце центральной масляной магистрали. При износе отдельных подшипников кривошипно-шатунного механизма величина давления в центральной масляной магистрали может заметно варьировать (вариация давления в центральной масляной магистрали также зависит от марки двигателя). Однако, для исключения влияния снижения давления в центральной масляной магистрали на результаты диагноза предусматривается установление постоянного уровня давления в центральной масляной магистрали путем перепуска части жидкости через дроссель 7. Известно например, что для двигателя ЗМЗ-4062 предельным считается давление в центральной масляной магистрали – 1 кгс/см, таким образом, для двигателя ЗМЗ-4062 независимо от его технического состояния устанавливается давление в центральной масляной магистрали 1 кгс/см путем перепуска части масла и установлении краном 6 заданного давления в центральной масляной магистрали.
Далее при использовании устройства (отключателя цилиндров), позволяющего отключать полностью цилиндры двигателя и периодически отдельные циклы работы диагностируемого цилиндра путем отключения импульсов электрической форсунки двигателя или искры свечи, добиваются чередования участков осциллограммы с рабочим и нерабочим циклами. При первом цикле сила давления газов воздействует на вал, при последующем цикле – нет. Тензодатчиком давления 5 (фиг.1) измеряется осциллограмма мгновенной величины давления в центральной масляной магистрали.
Таким образом, получают осциллограмму давления в центральной масляной магистрали при чередовании рабочего и нерабочего циклов. Отношение давлений на осциллограмме, как установлено нами, определяют по формуле
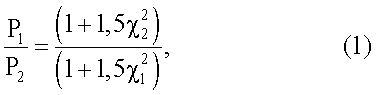
где Р1 – мгновенная амплитуда давления масла при работе без нагрузки;
P2 – мгновенная амплитуда давления масла при работе с нагрузкой;
1 – относительный эксцентриситет при работе подшипника без нагрузки;
2 – относительный эксцентриситет при работе подшипника с нагрузкой.
Отношение амплитуд давлений без нагрузки и под нагрузкой в выражении (1) будет зависеть только от величин относительных эксцентриситетов (связи давления с другими факторами, такими как производительность насоса, вязкость масла, температура масла и др., были устранены). Из анализа формулы (1) можно сделать вывод, что наиболее чувствительным диагностическим параметром при определении технического состояния коренного подшипника является отношение амплитуд давлений без нагрузки и под нагрузкой. Однако при определении отношения мгновенных амплитуд давлений может быть внесена значительная погрешность в связи с тем, что развертка осциллограммы давления но вертикали и горизонтали может отличаться от измерения к измерению. Для преодоления данной погрешности отношение амплитуд давлений при работе через цикл с нагрузкой и без нагрузки заменяем на разность нормированных амплитуд давлений при работе через цикл с нагрузкой и без нагрузки. При этом достаточно будет нормировать одну из амплитуд (амплитуду под нагрузкой), или по-другому, коэффициентом усиления осциллографа сжать одну из амплитуд под шаблон (шаблон представлен на фиг.2), а вторую наложить на первую и по разности нормированных амплитуд давления определить техническое состояние диагностируемого элемента. Наложение нормированных амплитуд давлений представлено на фиг.2, причем и по вертикали и по горизонтали всегда развертка осциллограммы укладывается под шаблон постоянных размеров, что исключает погрешность, связанную с изменением размеров развертки осциллограммы от измерения к измерению.
Таким образом, формула для определения действительного зазора в коренной шейке по разности нормированных амплитуд давлений определенная нами экспериментально имеет вид

где ZK – зазор в диагностируемом подшипнике, мм;
A – разность нормированных амплитуд давления (А на фиг.2) двух соседних циклов при работе через цикл, с нагрузкой и без нагрузки, МПа;.
Таким образом, измерив разность нормированных амплитуд давлений двух соседних циклов при работе диагностируемого цилиндра через цикл, с нагрузкой и без нагрузки, по формуле (2) определяют действительный износ любого подшипника.
Предельное значение разности нормированных минимальных амплитуд давлений под нагрузкой и без нагрузки для выбраковки коренного подшипника при частоте вращения коленчатого вала двигателя n=880 мин-1, составляет 0,02 МПа.
Технический результат заключается в повышении точности оценки технического состояния отдельных подшипников двигателя внутреннего сгорания.
Использование предлагаемого способа оценки технического состояния ДВС позволяет грамотно и своевременно определять неисправности подшипников кривошипно-шатунного механизма с достоверностью 0,95 (что было подтверждено эксплуатационными испытаниями на двигателе ЗМЗ-4062), а также прогнозировать время безаварийной работы двигателя.
Формула изобретения
Способ диагностики степени износа подшипников двигателя внутреннего сгорания, заключающийся в определении величины мгновенного давления в центральной масляной магистрали при работе диагностируемых подшипников в течение цикла под максимальной нагрузкой в последующий цикл без нагрузки; при этом производят сравнение участков осциллограммы, полученных при рабочем цикле диагностируемого цилиндра и нерабочем цикле, отличающийся тем, что измерение величины мгновенного давления производят в конце центральной масляной магистрали, а для снижения погрешности оценки технического состояния подшипников кривошипно-шатунного механизма дополнительно устанавливают кран и дроссель, при помощи которых устанавливают среднее давление в центральной масляной магистрали, независимо от степени износа отдельных подшипников определяют разность нормированных амплитуд мгновенных значений давления при указанных условиях и сравнивают их с разностью нормированных амплитуд, полученных на эталонном двигателе; путем их сравнения определяют степень износа любого из диагностируемых подшипников двигателя: с увеличением степени износа подшипников увеличивается приведенная разность нормированных амплитуд давлений.
РИСУНКИ
|
|