|
(21), (22) Заявка: 2009108189/15, 10.03.2009
(24) Дата начала отсчета срока действия патента:
10.03.2009
(46) Опубликовано: 10.09.2010
(56) Список документов, цитированных в отчете о поиске:
SU 704648 A1, 30.12.1979. SU 1304863 A1, 23.01.1987. US 4575435 A, 11.03.1986. US 5112536 A, 12.05.1992. US 5543088 A, 06.08.1996.
Адрес для переписки:
105066, Москва, ул. Старая Басманная, 21/4, ГОУ ВПО “Московский государственный университет инженерной экологии”, ректору Д.А. Баранову
|
(72) Автор(ы):
Пушнов Александр Сергеевич (RU), Чиж Константин Валерьевич (RU), Тимонин Александр Семенович (RU)
(73) Патентообладатель(и):
Государственное образовательное учреждение высшего профессионального образования “Московский государственный университет инженерной экологии” (RU)
|
(54) НАСАДКА ДЛЯ ТЕПЛО- И МАССООБМЕННЫХ АППАРАТОВ
(57) Реферат:
Изобретение относится к конструкции насыпных насадок для массообменных аппаратов и может быть использовано в химической, нефтеперерабатывающей, нефтехимической и других отраслях промышленности при осуществлении тепломассообменных процессов в системах жидкость-газ. Насадка выполнена в форме диска с полосами максимальной длины по одной из его осей, причем длина и ширина полос уменьшается от оси диска к его периферии. Линии отгиба полос образуют ступеньки, причем расстояние от линии отгиба каждой полосы до края диска увеличивается от полосы максимальной длины до полосы минимальной длины от 0,75 до 3 соответствующей ширины каждой полосы. Технический результат: повышение эффективности процесса тепло- и массообмена. 2 ил.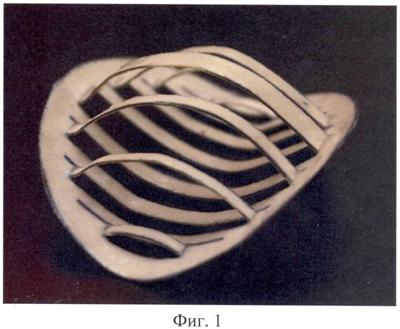
Изобретение относится к конструкции насыпных насадок для массообменных аппаратов и может быть использовано в химической, нефтеперерабатывающей, нефтехимической и других отраслях промышленности при осуществлении тепломассообменных процессов в системах жидкость-пар (газ), например ректификации, абсорбции, десорбции, дистилляции и других процессах.
Известен элемент насадки для массообменных аппаратов, представляющий собой насадку, выполненную из двух полуэлементов, образованных внутренними и наружными коаксиальными полуцилиндрическими полосами из листового материала, расположенными с взаимным смещением (см. авторское свидетельство SU 1304863, МПК B01D 53/20, 1985 г.).
Наиболее близким аналогом к разработанной конструкции является элемент насадки для массообменных аппаратов, представляющий собой насадку, выполненную из квадратной листовой карты с продольными параллельными прорезями, образующими полосы переменной длины, отогнутые в разные стороны от плоскости пластины (см. авторское свидетельство SU 704648, МПК B01D 53/20, 1977 г.).
Недостатками указанных насадок является недостаточная эффективность тепло- и массообмена из-за использования в качестве заготовки квадратной листовой карты острые углы которой могут препятствовать равномерному распределению элементов насадки по объему колонного аппарата (за счет зацепления элементов насадки), вследствие чего образующиеся пустые пространства будут увеличивать порозность, снижать удельную поверхность и тем самым способствовать снижению эффективности процесса тепло- и массообмена.
Задача изобретения – интенсификация процесса тепло- и массообмена за счет увеличения поверхности контакта взаимодействующих фаз. Это достигается за счет того, что насадка выполнена в виде эллипсоида.
Поставленная задача решается тем, что в насадке для проведения процессов тепло- и массообмена, выполненной в виде пластины с продольными параллельными прорезями, образующими полосы переменной длины, отогнутые в разные стороны от плоскости пластины, согласно изобретению пластина выполнена в форме диска с полосами максимальной длины по одной из его осей с уменьшением длины и ширины полос от оси диска к его периферии, а линии отгиба полос образуют ступеньки, причем расстояние от линии отгиба каждой полосы до края диска увеличивается от полосы максимальной длины до полосы минимальной длины от 0.75÷3 соответствующей ширины каждой полосы.
На фиг.1 представлен общий вид насадочного элемента, на фиг.2 – вид насадки в плане.
Далее приводится пример выполнения насадки.
Диаметр насадки равен 50 мм.
Ширина полосы максимальной длины b равна 6 мм.
Ширина полосы минимальной длины b3 равна 3 мм.
Значения расстояния от линии отгиба до края насадки (d) определяются следующим образом:
d=0.75·b=0.75·6=4.5 мм
d1=1.45·b1=1.45·4=5.8 мм
d2=1.9·b2=1.9·3=5.7 мм
d3=3·b3=3·3=9 мм
Из примера можно сделать вывод, что расстояние от линии отгиба центральной полосы с максимальной длиной до края диска равно 0.75 ширины этой полосы, а расстояние от линии отгиба полосы с минимальной длиной до края диска соответствует 3 ширинам этой полосы.
Заготовкой насадки служит пластина в форме диска. Внутри диска 1 параллельно одной из осей симметрии выполнены прорези 2, образующие полосы 3, длина и ширина которых уменьшаются от центра к периферии, поочередно отогнутые в разные стороны, образуют эллипсоидную форму насадки.
Насадка для массообменных аппаратов работает следующим образом.
Для ведения технологического процесса необходимый объем аппарата засыпают внавал элементами насадки. Контакт между газом и жидкостью осуществляется непрерывно в противотоке по всей высоте слоя насадки как на внешней, так и на внутренней поверхностях элементов насадки. Орошающая жидкость равномерно распределяется по поверхности слоя насадки и стекает по элементам вниз. Газ через распределительное устройство подается снизу аппарата и движется вверх.
Эллипсоидная форма, образующаяся за счет чередующегося отгиба полос в разные стороны, обеспечивает полное омывание как внутренней, так и внешней части элементов насадки, а также создает дополнительные условия для турбулизации взаимодействующих фаз, что обеспечивает значительную интенсификацию процесса тепло- и массообмена благодаря ступенькам, образованными линиями отгиба полос.
Источники информации
1. Авторское свидетельство SU 1304863, МПК B01D 53/20, 1985 г.
2. Авторское свидетельство SU 704648, МПК B01D 53/20, 1977 г.
Формула изобретения
Насадка для проведения процессов тепло- и массообмена, выполненная в виде пластины с продольными параллельными прорезями, образующими полосы переменной длины, отогнутые в разные стороны от плоскости пластины, отличающаяся тем, что пластина выполнена в форме диска с полосами максимальной длины по одной из его осей с уменьшением длины и ширины полос от оси диска к его периферии, а линии отгиба полос образуют ступеньки, причем расстояние от линии отгиба каждой полосы до края диска увеличивается от полосы максимальной длины до полосы минимальной длины от 0,75 до 3 соответствующей ширины каждой полосы.
РИСУНКИ
|
|