|
(21), (22) Заявка: 2008144048/09, 05.11.2008
(24) Дата начала отсчета срока действия патента:
05.11.2008
(43) Дата публикации заявки: 10.05.2010
(46) Опубликовано: 27.08.2010
(56) Список документов, цитированных в отчете о поиске:
US 4600602 А, 15.07.1986. RU 2095310 C1, 10.11.1997. RU 2080288 C1, 27.05.1997. JP 02-177254 A, 10.07.1990. JP 61264682 A, 11.12.1986.
Адрес для переписки:
630090, г.Новосибирск, 90, пр-кт Акад. Лаврентьева, 3, Институт неорганической химии им. А.В. Николаева
|
(72) Автор(ы):
Митькин Валентин Николаевич (RU), Левченко Людмила Михайловна (RU), Галицкий Александр Анатольевич (RU), Галкин Петр Сергеевич (RU), Предеин Александр Юрьевич (RU), Макаров Сергей Борисович (RU)
(73) Патентообладатель(и):
Митькин Валентин Николаевич (RU)
|
(54) ЭЛЕКТРОПРОВОДНЫЙ КОМПОЗИЦИОННЫЙ УГЛЕРОДСОДЕРЖАЩИЙ МАТЕРИАЛ И СПОСОБ ЕГО ПОЛУЧЕНИЯ
(57) Реферат:
Изобретение относится к композиционным материалам с заданным удельным сопротивлением (удельной электропроводностью) на основе смесей частиц малопроводящих материалов с частицами высокоэлектропроводных углеродных материалов для их применения в электротехнике. Техническим результатом изобретения является создание новых типов электропроводных углеродсодержащих композиционных материалов с широким диапазоном удельного сопротивления ~0.1-1012 Ом·м, пригодных для использования в литиевых источниках тока. Согласно изобретению в углеродсодержащем композиционном электропроводном материале на основе малопроводящего материала, смешанного с электропроводной углеродной добавкой и связующим, используют нанокомпозиционный материал, в котором в качестве агрегатов наночастиц малопроводящего материала используют агрегаты фторуглерод, диоксид марганца, полупроводники и/или их смеси, а в качестве электропроводной углеродной добавки используют агрегаты наночастиц углерода с окисленной поверхностью, причем эти наноразмерные агрегаты в композиционном материале между собой имеют химические межповерхностные наноразмерные электрические углеродные контакты и/или токосъемы, при этом химические межповерхностные наноразмерные электрические углеродные контакты и/или токосъемы, осуществляемые межчастичными химическими связями sp2– и sp3-углерода с наружными атомами поверхности частиц малопроводящего материала, а в качестве полупроводника используют кремний, полупроводники типа А3В5, а в качестве углеродной добавки используют терморасширенный графит, технические углеводороды типа саж, содержащих поверхностные кислородсодержащие поверхностные группы окисленного sp2– и sp3-углерода, при этом соотношение частиц малопроводящего материала в смеси составляет 100:1-1:100, а величина удельного сопротивления полученных нанокомпозиционных материалов составляет 0.1-1012 Ом·см и его величину задают соотношением между количествами частиц малопроводящего материала и частиц электропроводного углерода с окисленной поверхностью, взятых в диапазоне соотношений 100:1-1:10 соответственно, при этом размер наночастиц в агрегатах малопроводящего материала составляет 2-100 нм, размер наночастиц в агрегатах электропроводящей углеродной добавки с окисленной поверхностью составляет 1-20 нм. Материал получают способом, включающим смешение исходных компонентов и их обработку, при этом частицы малопроводящего материала смешивают с электропроводной углеродной добавкой с окисленной поверхностью частиц, перед смешением со связующим порошкообразные частицы малопроводящего материала смешивают с электропроводящей углеродной добавкой с окисленной поверхностью частиц и подвергают эту смесь механохимической обработке с последующей термообработкой и получением промежуточного нанокомпозита, полученный нанокомпозит смешивают со связующим и подвергают сушке при 105-150°С до достижения постоянной массы. 2 н. и 6 з.п. ф-лы, 11 ил., 8 табл.
Изобретение относится к композиционным углеродсодержащим материалам с заданным удельным сопротивлением (удельной электропроводностью) на основе смесей частиц малопроводящих материалов с частицами высокоэлектропроводных углеродных материалов для их применения в электротехнике в качестве резистивных композитов, например, при изготовлении гибких резисторов, а также при изготовлении электропроводных электродов произвольной формы, используемых, например, в химических источниках тока (ХИТ) с повышенными эксплуатационными характеристиками – низким омическим сопротивлением, высокой электрической емкостью, повышенными плотностью тока и напряжением разряда. Изобретение относится также к способам изготовления таких материалов.
Широко известно множество электропроводных композиционных материалов на основе смесей дисперсных материалов с низкой и высокой удельной электропроводностью электронного типа, проводимость которых задается электропроводной углеродной добавкой, за счет множественных внутренних контактов между электропроводными частицами углеродного материала (сажи, графита и др.). Для придания электропроводному композиционному материалу механической целостности и возможности изготовления из него изделия заданной формы с заданным электрическим сопротивлением в подготовленную тесную смесь частиц малопроводящего материала с углеродной электропроводной добавкой обычно вводят какое-нибудь полимерное связующее, например, фторопласт или полиэтиленоксид ([1]. И.А.Кедринский и др. Химические источники тока с литиевым электродом. Красноярск, Изд-во Красноярского Университета, 1983, с.248).
В качестве малопроводящих дисперсных материалов с низкой удельной электропроводностью электронного типа для изготовления резистивных композитов можно использовать порошкообразные диэлектрики ( МП~1012-1015 Ом·см), например, силициды титана, оксиды металлов и неметаллов [Ti5Si3, TiSi2, SiO2, В2O3, BaO, SrO, CuO, ([2]. – патент США 4369391), полупроводники Si, Ge, или вещества АIIIBV (InSb, InAs, GaSb, GaAs и др.), удельное сопротивление (электронное) которых составляет пп~103-108 Ом·см, а также некоторые металлы (висмут, сурьма и др.) с достаточно высоким ( m~102-103 Ом·см) омическим сопротивлением ([3]. Таблицы физических величин. Справочник / Под ред. акад. И.К.Кикоина. М., Атомиздат, 1976, 1008 с.).
Заданное результирующее удельное сопротивление таких резистивных композитов – полидисперсных смесевых композиционных материалов обеспечивается за счет внутренних межчастичных электрических контактов между электропроводными углеродными частицами и, в целом, определяется количеством введенного в композиционный материал углерода, так как проводимость углеродных контактов на 3-15 порядков превышает проводимость малопроводящих материалов. В этой связи частицы малопроводящих материалов, по сути, являются неорганическими наполнителями в резистивных композитах. При этом ([4]. Л.Юнг, Анодные оксидные пленки, Энергия, Ленинградское отделение, 1967, с.233) общая электронная проводимость полученного композиционного материала обеспечивается перколяцией (фильтрацией) носителей заряда (электронов) на межфазных контактах между проводящими углеродными частицами.
При изготовлении катодов первичных (неперезаряжаемых) литиевых ХИТ с повышенными эксплуатационными характеристиками – электрической емкостью, плотностью тока и напряжением разряда часто используют малопроводящие порошкообразные материалы, такие, как фтористый углерод CFx (x~1) и С2F, которые применяют в катодах первичных (неперезаряжаемых) ХИТ [1]. Они обладают наиболее высокой удельной энергоемкостью в катодах литиевых ХИТ, однако они, как правило, имеют очень высокое, характерное для диэлектриков омическое сопротивление ( дс~1014-1015 Ом·см ([5]. – Митькин В.Н. Новейшие электродные материалы для литиевой химической энергетики / Под ред. акад. Ф.А.Кузнецова и д.т.н. В.В.Мухина. Новосибирск: Изд-во ОАО НЗХК, 2001, 162 с., см. также Митькин В.Н., Левченко Л.М., Галкин П.С. и др. Поликарбонофторид порошкообразный марок ФТ, ФС. Технические Условия ТУ 34 9735-0003-03533984-97. Ангарск-Новосибирск, 1997, 94 с.), и для получения хорошего катодного композиционного материала с приемлемой электропроводностью их обычно смешивают с электропроводящей углеродной добавкой (ацетиленовая сажа, графит, терморасширенный графит), в результате чего удается повысить предельную эксплуатационную плотность тока разряда до 0.1-2.5 мА/см2 при напряжениях разряда 2.0-2.6 В ([6]. – Н.Ватанабэ. Элемент с органическим электролитом – патенты Японии No 61-264679, 61-264680, 61-264682, H01m 6/16), ([7]. – патент Японии 63-334457 «Элемент системы литий – фторуглерод», H01m 4/06, 28.12.88 г.), ([8].- Патент России 2095310, Н01М 4/02, С01В 31/00. Углеродсодержащий катодный материал и способ получения катода для литиевых источников тока / В.Н.Митькин, И.И.Яковлев, Н.Ф.Юданов, А.А.Галицкий, С.В.Филатов, В.В.Мухин, В.В.Тележкин, В.В.Рожков. Опубл. 11.11.97 в БИ 31, 1997).
Из перечисленных здесь высокоомных полупроводников с известным промышленным применением следует особо отметить кремний ( Si~102-108
Одним из основных приемов получения резистивных композитов – композиционных электротехнических материалов, обладающих заданной электропроводностью электронного типа, является смешивание в заданном соотношении малопроводящих измельченных (дисперсных) материалов, обладающих высоким удельным сопротивлением ( МП~102-1015 Ом·см [1]), с мелкими (1-100 мкм) частицами технического углерода (графит, сажа и др.), имеющими низкое удельное сопротивление ( УМ~0.001-1 Ом·см) [2], с последующим введением в полученную тесную смесь этих компонентов какого-нибудь полимерного связующего для придания электропроводному композиционному материалу механической целостности и возможности формования из него изделия заданной формы с заданным электрическим сопротивлением, например, путем создания пленки на поверхности малопроводящего материала или диэлектрика. Стабилизация электропроводных свойств полученного композиционного резистивного композита (электропроводного композиционного материала) чаще всего достигается путем термообработки уже сформированного изделия, при которой изделие приобретает законченную форму, а межфазные электропроводящие контакты между углеродными частицами становятся неподвижными. Точно такие же приемы используют при изготовлении эффективных электропроводных углеродсодержащих электродов для литиевых ХИТ [6-8], в которых получаются нужные стабильные во времени углеродные контакты, распределенные между частицами малопроводящих веществ.
Из вышеприведенного рассмотрения следует, что центральным объектом, который обеспечивает стабильную электропроводность, т.е осуществление процессов переноса заряда в любом электропроводном углеродсодержащем композиционном материале – резистивном композите или электроде, является электропроводный контакт, состоящий из проводящего углеродного материала, находящегося в тесном постоянном механическом контакте с прилегающими к нему частицами малопроводящего материала. Схема электропроводного композиционного материала резистивного композита и эквивалентная электрическая схема электропроводного электрода на его основе представлена на фиг.1.
Наглядным аналогом электропроводного материала, содержащего частицы электропроводного углеродного материала (выполняющие функции электропроводного контакта), является активная катодная масса, содержащая оксид металла (диоксид марганца, оксид свинца или их смеси) и токопроводящую добавку в виде графитного экспандата ([11. Петер Фабер, Активная масса положительного электрода первичного элемента, А.С. СССР No 488432, Н01m, 13/02, 21/00, опубл. 15.10.75, БИ No 38).
Для изготовления указанной активной катодной массы используют готовый графитный экспандат кораллообразной структуры, который вводится в количестве до 25% от веса активной массы. Кораллообразная структура графитного экспандата реализуется при термолизе различных соединений графита – оксида графита (“коллоидного графита”, в качестве которого используют препарат С-1) или фтороксида графита ([12]. – Л.Л.Горностаев, С.В.Земсков, И.И.Яковлев, А.С. СССР 955654, рег. 04.05.82, Фтороксиды графита и способ их получения, С01В, 31/00).
Наиболее близким аналогом-прототипом по композиционным материалам, содержащим частицы электропроводного углеродного материала (выполняющего функции электропроводного контакта), является композиционный электропроводный материал – резистивный композит, используемый при изготовлении резисторов с заданной величиной удельного электрического сопротивления М в диапазоне 18-150 Ом·мм2/см (0.18-1.5 Ом·см) ([13]. – Прототип по материалу – Патент США 4600602, Martin F.A., Shahbazi S., Low resistance resistor compositions, 15 July 1986).
Этот резистивный композит, в соответствии с формулой патента США 4600602, состоит из смеси В, состоящей из углеродных материалов двух типов – частиц графита размером 1-10 мкм с удельной поверхностью 1-2 м2/г, частиц углеродного порошка размером 10-100 мкм с удельной поверхностью 500-1500 м2/г.
Из составов углеродно-графитного электропроводного резистивного композита прототипа – патента США 4600602 (соотношение графита к углеродному порошку, по примерам 2-5, равно 4:1) и величины достигнутого в аналоге удельного сопротивления резистивного композита (18-150 Ом·мм2/см) легко рассчитать, что удельное сопротивление частиц углеродного порошка примерно в 5-50 раз больше, чем таковое для частиц графита, которое, в зависимости от чистоты графита, составляет около 0.002-0.01 Ом·см [3. – Таблицы физических величин). Из этого следует, что, по отношению к более электропроводному графиту, углеродный порошок указанного аналога является менее электропроводным материалом, что вполне согласуется с известным фактом меньшей проводимости саж, коксов и технических углеродных порошков по сравнению с графитом.
Таким образом, из данных патента США 4600602 следует, что углеродно-графитовый композиционный электропроводный порошок аналога является смесью частиц низкоомного электрического углеродного материала (выполняющего функцию электрического контакта) на основе графита с частицами более высокоомного и, соответственно, менее проводящего углеродного материала (выполняющими функцию резистивного компонента – проводника с заданной электропроводностью).
Рассмотренные материалы (аналоги и протитип [1-2, 6-11, 13], по своей сути, содержат все признаки углеродного низкоомного электрического контакта, в качестве которого выступают мелкие частицы графита или терморасширенного графита, тесно контактирующие в указанных композиционных электропроводных материалах с частицами менее проводящего (углеродный порошок патента США 4600602 или весьма малопроводящего материала (частицы фторуглеродного материала патента RU 2095310).
Углеродсодержащий электропроводный (резистивный) композиционный материал прототипа имеет следующие недостатки:
– частицы композиционного электропроводного материала имеют размер не менее 2-5 мкм, причем электропроводность материала обеспечивается по так называемому перколяционному механизму, по которому транспорт носителей заряда (электронов) осуществляется путем межчастичных контактов между частицами малопроводящего материала и частицами высокоэлектропроводной углеродной добавки,
– реальный минимальный размер частиц композиционного электропроводного материала предопределяет и минимальную толщину резистивного слоя, который не может быть менее 2-5 мкм, и это накладывает ограничения на предельную величину электрического сопротивления получаемого минимально возможного резистивного слоя, поэтому резистивный материал прототипа имеет очень маленький диапазон достигаемых удельных сопротивлений (18-150 Ом·см/мм2),
– так как частицы графита – высокоэлектропроводной углеродной добавки, находящиеся между частицами углерода (менее проводящего материала), могут подвергаться окислению и увлажнению, то этот процесс будет приводить к изменению (чаще всего возрастанию) электрического сопротивления во всех межчастичных контактах и, в целом, к неконтролируемому изменению электрического сопротивления всего композиционного материала. Для предотвращения этого негативного явления необходимо полученный резистивный слой защищать от контакта с влагой и кислородом воздуха либо во время получения, либо сразу после его получения, что осуществляется путем смешивания электропроводного резистивного углеродно-графитового композита с многокомпонентным связующим, нанесения полученного композита на подложку и термообработки при 150-165°С, при котором происходит полимеризация фенольной смолы и образование резистивного влагоустойчивого слоя,
– резистивный материал прототипа вследствие наличия в нем полимеризованной фенольной смолы, несмотря на его влагоустойчивость, имеет незначительную термическую устойчивость и может применяться без изменения его резистивных свойств только до температуры начала термолиза связующего (не свыше 250°С),
– материал прототипа является узко специализированным и может применяться только для изготовления пленочных резисторов, однако этот материал в силу присутствия в нем фенольной полимерной смолы, использованной в качестве полимерного связующего, нельзя применять при изготовлении электродов литиевых ХИТ из-за неустойчивости полимерного связующего к неводным растворителям (пропиленкарбонат, гамма-бутиролактон [1, 6-8]), используемым в литиевых источниках тока.
Углеродсодержащий электропроводный материал (резистивный композит) прототипа-материала, в соответствии патентом США 4600602, получают из двух материалов – смеси А и смеси В. Смесь В получают путем предварительного смешивания в шаровой мельнице углеродных материалов двух типов – частиц графита размером 1-10 мкм с удельной поверхностью 1-2 м2/г и частиц углеродного порошка размером 10-100 мкм с удельной поверхностью 500-1500 м2/г. После получения углеродно-графитовой смеси В и достижения среднего размера частиц 5-8 мкм эта смесь смешивается со смесью А, которая является многокомпонентным водоотталкивающим композиционным связующим, состоящим из двух типов фенольных смол – жидкой смолы с молекулярной массой 300-400 а.е.м. (атомных единиц массы) и твердой смолы с молекулярной массой 400-500 а.е.м. По данным примера 1 патента США 4600602, при получении жидкого композиционного связующего А используют также органический растворитель для твердой фенольной смолы – бутил-карбитол ацетат.
Наиболее близким аналогом-прототипом по способам получения электропроводных композиционных углеродсодержащих электропроводных композиционных материалов является углеродсодержащий катодный материал для литиевых химических источников тока, содержащий энергоноситель, связующее, электропроводящую добавку и порообразователь ([14]. – В.Н.Митькин и др., патент RU 2187177, Катодный материал для литиевого источника тока и способ его получения). В качестве энергоносителя используют смесь фторуглерода, содержащего 62-67% фтора с диоксидом марганца, а в качестве порообразователя используют терморасширенный графит, причем доля терморасширенного графита в готовом катодном материале составляет 2÷5%ОТН..
В соответствии с формулой изобретения прототипа-способа получение электропроводного композиционного углеродсодержащего катодного материала и катода для литиевых химических источников тока заключается в смешении фторуглерода, содержащего 62-67% фтора, с диоксидом марганца, смешивании этой смеси с электропроводящей добавкой и терморасширенным графитом, ее подвергают перед изготовлением катодного материала ударной механической обработке, при которой получают промежуточный порошкообразный материал с насыпной плотностью 2.2÷2.8 г/см3, после чего вводят связующее для получения готового катодного материала, который далее сушат при 85÷120°С и формуют катоды. При этом терморасширенный графит получают термообработкой при 150-310°С фтороксида графита общей формулы Cx·zCyO·nH2O·CF, где х=1.5÷12, y=2.2÷2.5, z=0.5÷1.4, n=0.1÷0.5.
Способы получения описанных материалов прототипа и аналогов обладают недостатками.
У способа получения аналога, прототипа-материала имеются следующие недостатки:
– способ в части получения смеси графит-углеродного композита с заданным размером частиц 6-8 мкм отличается длительностью (не менее 25 часов), поскольку по способу получения материала-прототипа частицы графита, по патенту США 4600602, сначала смешивают с углеродным порошком в соотношении 90:10-50:50 и подвергают обработке в шаровой мельнице 1 час в среде жидкого фреона, после чего смесь выгружают в открытую емкость и далее фреон испаряют в течение 24 часов. В результате этой обработки получают смесевой углеродно-графитный электропроводный порошок (смесь В) со средним размером углеродных частиц 6-8 мкм,
– по способу получения прототипа-материала при заданной длительности измельчения в шаровой мельнице невозможно получение более мелких частиц, чем 2-5 мкм, необходимых для получения более высокоомных резистивных композитов, а именно это накладывает ограничения на достигаемый относительно небольшой диапазон удельного сопротивления электропроводного углеродсодержащего композита (18-150 Ом·мм2/см),
– способ получения резистивного композита прототипа-материала узко специализирован (в основном для придания материалу влагоустойчивости), так как по способу получения аналога нельзя получать эффективные электропроводные углеродсодержащие композиционные материалы для электродов литиевых ХИТ из-за того, что после термообработки при 150-165°С и получения полимерного резистивного композита углеродные частицы оказываются полностью блокированными слоем фенольной смолы и продуктов ее полимеризации.
У способа получения композиционных электропроводных углеродсодержащих материалов-прототипа имеются следующие недостатки:
– применение способа прототипа для получения углеродсодержащих электропроводных композиционных материалов известно только для изготовления катодных материалов, в то время как использование этого способа с целью получения резистивных композитов в патентной литературе пока не описано,
– при механоактивации смесей, содержащих углерод и фторуглерод, из-за присутствия в материалах адсорбционной влаги происходит взаимодействие sp3-C-F-связей фторуглерода со следами влаги (~0.1%), сопровождающееся отщеплением трудноудаляемого HF, наличие которого даже в небольших количествах 0.02-0.1% приводит к трудно контролируемому влиянию на общую величину электрического сопротивления получаемого углеродсодержащего электропроводного (резистивного) композиционного материала в силу того, что фтористый водород обладает собственным сопротивлением, что приводит к ]преждевременной деградации литиевых ХИТ ([15]. – Патент России 2080288, С01b 31/00. Способ модификации фторуглеродного материала / В.Н.Митькин, И.И.Яковлев, А.С.Назаров, В.Г.Макотченко, С.В.Филатов, В.В.Мухин, В.В.Тележкин, В.В.Рожков. Опубл. в БИ 
– при механоактивации смесей компонентов, содержащих фторуглерод, в частицах фторуглерода происходит некоторое возрастание объемной и массовой концентрации электронных центров (в 3-24 раза [5, 16]), влияющих, в целом, на повышение электропроводности, однако на фоне очень большого удельного сопротивления фторуглерода ~1014-1015 Ом·м [5], этого явно недостаточно для получения проводящего материала на основе частиц фторуглерода с требуемой для резистивных композитов универсального применения более широкого диапазона удельных сопротивлений ~0.1-1012 Ом·м,
– способ получения композиционного углеродсодержащего электропроводного материала у прототипа-способа узко специализирован и предназначен только для получения катодных материалов с высокой электропроводностью, применяемых в литиевых ХИТ [1].
Задачами настоящего изобретения по электропроводным композиционным углеродсодержащим материалам и способу являются:
– создание новых типов электропроводных углеродсодержащих композиционных материалов с широким диапазоном удельного сопротивления ~0.1-1012 Ом·м с внутренним межчастичным электрическим токосъемом между проводящими углеродными частицами-контактами и частицами малопроводящих материалов ~10-1015 Ом·м,
– повышение надежности межчастичного электрического токосъема между проводящими углеродными частицами-контактами и частицами малопроводящих материалов с целью увеличения стабильности омических параметров резистивных композитов и повышения удельных энергетических характеристик электродов литиевых ХИТ, в том числе объемной и массовой энергоемкости, эксплуатационной плотности тока разряда и разрядного напряжения,
– обеспечение пригодности новых типов электропроводных углеродсодержащих композиционных материалов для изготовления гибких резистивных композитов с широким диапазоном удельного сопротивления и/или эффективных электродов литиевых ХИТ,
– обеспечение гибкости и водооталкивающих свойств у получаемых углеродсодержащих композиционных электропроводных материалов для изготовления гибких резистивных композитов с широким диапазоном удельного сопротивления и/или эффективных электродов литиевых ХИТ.
Поставленные задачи по материалу решаются тем, что используют нанокомпозиционный материал, в котором в качестве агрегатов наночастиц малопроводящего материала используют агрегаты фторуглерод, диоксид марганца, полупроводники и/или их смеси, а в качестве электропроводной углеродной добавки используют агрегаты наночастиц углерода с окисленной поверхностью, причем эти наноразмерные агрегаты в композиционном материале между собой имеют химические межповерхностные наноразмерные электрические углеродные контакты и/или токосъемы, а также тем, что химические межповерхностные наноразмерные электрические углеродные контакты и/или токосъемы осуществляют межчастичными химическими связями sp2– и sp3-углepoдa с наружными атомами поверхности частиц малопроводящего материала, при этом в качестве полупроводника используют кремний, полупроводники типа А3В5, а в качестве углеродной добавки используют терморасширенный графит, технические углеводороды типа саж, содержащих поверхностные кислородсодержащие группы окисленного sp2– и sp3-углерода, при этом соотношение частиц малопроводящего материала в смеси составляет 100:1-1:100, величина удельного сопротивления полученных нанокомпозиционных материалов составляет 0.1-1012 Ом·см, и его величину задают соотношением между количествами частиц малопроводящего материала и частиц электропроводного углерода с окисленной поверхностью, взятых в диапазоне соотношений 100:1-1:10 соответственно, размер наночастиц в агрегатах малопроводящего материала составляет 2-100 нм, размер наночастиц в агрегатах электропроводящей углеродной добавки с окисленной поверхностью составляет 1-20 нм.
Отличительными признаками материала являются:
– используют нанокомпозиционные материалы в качестве малопроводящего материала и электропроводной углеродной добавки с окисленной поверхностью, причем эти наноразмерные агрегаты в композиционном материале между собой имеют химические межповерхностные наноразмерные электрические углеродные контакты и/или токосъемы;
– используют химические межповерхностные наноразмерные электрические углеродные контакты и/или токосъемы, осуществляют межчастичные химические связи sp2– и sp3-углерода с наружными атомами поверхности частиц малопроводящего материала;
– химические межповерхностные наноразмерные электрические углеродные контакты и/или токосъемы осуществляют межчастичными химическими связями sp2– и sp3-углерода с наружными атомами поверхности частиц малопроводящего материала, используемые материалы в качестве малопроводящих и электропроводящих составляющих, соотношения и характеристики нанокомпозитного материала.
Термины “контакт” и/или “токосъем” в настоящем изобретении применяются к одному и тому физико-химическому объекту – углеродному наноблоку, химически связанному с наноблоком малопроводящего материала, но относятся к разным процессам переноса заряда, происходящим в разных по назначению композиционных материалах. Если речь идет о резистивном композите, то используется понятие межчастичного электрического углеродного контакта, а в электродном композите для литиевых ХИТ речь идет о межчастичном химическом углеродном токосъеме.
Схема электропроводного композиционного материала резистивного композита и эквивалентная электрическая схема электропроводного электрода на его основе представлена на фиг.2. В схемах фиг.1 и фиг.2 общими элементами являются очень большие сопротивления связующего ( СВ>1015 Ом·см), и при расчете общего сопротивления композита в диапазоне 0.1-1012 Ом·см ими можно пренебречь. В отличие от ситуации с материалом прототипа (фиг.1), где общее сопротивление определяется взаимным количеством двух типов углеродных материалов и ограничено небольшим диапазоном 18-150 Ом, общее сопротивление нанокомпозитного электрода по настоящему изобретению определяется тремя параллельными сопротивлениями – RМП (малопроводящая добавка – МП~10-1012 Ом·см), RУГ (углеродный материал – УГ~0.001-1 Ом·см) и RПХК (межповерхностный углеродный химический контакт – ПХК – 0.01-10 Ом·см). Величину ПХК отдельно взятого углеродного химического контакта напрямую измерять слишком трудоемко из-за сложностей организации физического эксперимента с отдельной очень маленькой частицей композита. Однако ПХК и RПХК можно приблизительно определить (или оценить) путем простого измерения общего удельного сопротивления композита и расчета ПХК по формуле, приведенной на фиг.2, исходя из задаваемого состава многокомпонентного резистивного композита и удельных сопротивлений компонентов этого композита. Доказательством наличия межповерхностного углеродного химического контакта в полученном по настоящему изобретению резистивном композите является резкое отличие общего результирующего сопротивления RЭК от величины, рассчитанной из формулы фиг.1, и невозможность применения эквивалентной схемы независимых сопротивлений фиг.1, что демонстрируется примерами, приведенными ниже. В этих примерах достигаемые величины ПХК межповерхностного углеродного химического контакта зависят от режимов способа получения и обычно составляют 1-104 Ом·см.
В качестве малопроводящей добавки в настоящем изобретении использованы практические диэлектрики, например, фторуглеродные материалы ( МП>1015 Ом·см), полупроводники – кремний ( МП>105-8 Ом·см), или вещества класса АIIIBV (InSb, InAs, GaAs, GaSb – ( МП>101-6 Ом·см), диоксид марганца, а также смеси фторуглерода с полупроводниками в диапазоне соотношений 100:1-1:100, что обеспечивает регулировку результирующего удельного сопротивления получаемого резистивного композита в диапазоне от 10 до 1012 Ом·см. В качестве электропродного углеродного материала нами использованы поверхностно окисленные углеродные наноразмерные (наноструктурированные) материалы – терморасширенный графит (ТРГ-O) и различные технические углероды типа саж, содержащие поверхностные функциональные группы окисленного sp2-углерода (>С=O, >СООН) и sp3-углерода ( С-ОН, C-F). Содержание поверхностных функциональных групп окисленного sp2– и sp3-углерода в применяемом углеродном электропроводном материале по данному изобретению обычно составляет 0.1-10% от общего количества углерода и определяется глубиной окисления поверхности углеродных частиц и условиями процесса окисления. Удобной количественной мерой окисленности поверхности углеродных частиц является величина требуемого удельного сопротивления УГ~0.001-1 Ом·см, необходимого для изготовления углеродсодержащих композиционных электропроводных материалов с заданным удельным сопротивлением 0.1-1012 Ом·см.
Таким образом, наличие трех регулируемых параллельных сопротивлений ( МП~10-1012 Ом·см, УГ~0.001-1 Ом·см и ПХК 1-104 Ом·см) в эквивалентной схеме фиг.2 расширяет технически осуществимый диапазон регулировки общего сопротивления получаемого резистивного композита на 8-10 порядков по сравнению с материалом прототипа.
Наглядный пример реализации электрического углеродного электрического контакта (или токосъема) за счет межчастичных химических связей sp2-углерода, находящегося в наноблоках электропроводного углеродного материала графита и атомов sp3-углерода, локализованных в наноблоках малопроводящего фторуглеродного материала (практического диэлектрика) состава CF1+x, и возникновения наноразмерного внутреннего углеродного токосъема с частиц весьма малопроводящего фторуглеродного материала ( ~1014-015 Ом·см), приведен на фиг.3 [16], где представлена схема химической сшивки пограничных слоев гофрированных сеток фторуглеродного материала sp3-С-F-связей и слоев sp2-углерода из наноблоков строения графита. При этом наноразмерный межчастичный углеродный химический токосъем (углеродный электрический контакт) реализуется в пограничном переходе химической сшивки sp2-sp3-зон фиг.3, и он регистрируется в виде дополнительного диффузного рефлекса на 3D-дифрактограмме порошка нанокомпозита (фиг.4 и таблица 1), полученного механоактивацией смеси фторуглерода марки ФС (состав CF1.2) и окисленного терморасширенного графита (ТРГ-O). Этот рефлекс проявляется при 2 =21-23°, и он отражает существование дифрагирующих наноразмерных слоев С-С и C-F d1, d2, d3, d4, d5 и др. с размерами ~4.5-5.1 (0.45-0.51 нм) [16].
Межчастичный углеродный химический токосъем (углеродный электрический контакт), реализующийся в пограничном переходе химической сшивки sp2-sp3-углерода (фиг.3) также проявляется в ИК-спектрах углерод-фторуглеродных нанокомпозитов, полученных из механоактивированных смесей компонентов, в виде плеча 1090-1130 см-1 при основной полосе поглощения от валентного колебания sp3-cвязи C-F 1200-1230 см-1 во фторуглеродах и фторграфитах CFx (x~0.9-1.3) [5, 17-18]. Для спектров углерод-фторуглеродных нанокомпозитов, полученных из смесей фторуглерода CF1.2 типа ФС и окисленного углерода (ТРГ-O), взятых в соотношении 128:100, эти полосы на фиг.5 расположены соответственно при 1126 и 1217 см-1. В этих же диапазонах частот находятся упоминаемые полосы поглощения химической сшивки sp2-sp3-зон для механоактивированных смесей других фторуглеродов (например, ФТ – CF1.15-1.3 [5]) и углеродных материалов типа различных саж. Интенсивность полосы 1090-1130 см-1 пропорциональна количеству sp3-C-F связей на границе зон химической сшивки sp2– и sp3-углерода от наноблоков строения графита и фторграфитоподобных материалов (в т.ч. фторированного графита), и она обычно достигает максимума для такого фторграфитового соединения, как диграфит монофторид C2F [18-19]. Данные фиг.5 прямо показывают высокую концентрацию зон химической сшивки sp2-sp3-углерода в механокомпозите.
Как правило, размеры агрегатов наночастиц малопроводящего материала составляют 2-100 нм, размеры агрегатов наночастиц электропроводящей углеродной добавки с окисленной поверхностью составляют 1-20 нм, а размеры межповерхностных наноразмерных углеродных химических электрических контактов и/или токосъемов составляют 0.45-1 нм (фиг.4) Указанные диапазоны размеров агрегатов наночастиц использованных в настоящем изобретении материалов, определяемые размерами областей когерентного рассеяния (ОКР) рентгеновского излучения, по известной формуле Дебая-Шерера, представлены в примерах ниже.
Поставленные задачи по способу приготовления электропроводных композиционных углеродсодержащих материалов решаются тем, что частицы малопроводящего материала смешивают с электропроводной углеродной добавкой с окисленной поверхностью частиц и подвергают эту смесь механохимической обработке с последующей термообработкой, полученный нанокомпозит смешивают со связующим и подвергают сушке при 105-150°С до достижения постоянной массы, при этом окисление электропроводящей углеродной добавки проводят при 20-400°С в среде кислородсодержащих реагентов до получения окисленного углеродного материала общей формулы CxOyHz·nH2O, где х=0.9-0.99, y=0.01-0.1, z=0.005-0.05, n=0.1-1.0, с размером агрегатов частиц менее 500 мкм и удельной поверхностью 2-1000 м2/г, и образования кислородсодержащих функциональных групп на поверхностях частиц, а механохимическую обработку проводят при ускорениях ударяющих тел 20-200 g до получения промежуточного нанокомпозита, с заданным удельным сопротивлением 0.1-1012 Ом·см и размерами наночастиц в агрегате малопроводящего материала – 2-100 нм, размер наночастиц в агрегате электропроводящей углеродной добавки с окисленной поверхностью составляет 1-20 нм, термообработку промежуточного нанокомпозита после механохимической обработки проводят при 140-400°С до достижения постоянной массы.
Отличительными признаками способа являются: порядок приготовления и режимы обработки исходных и промежуточных материалов
Окисления частиц электропроводящей углеродной добавки проводят любым известным способом, что демонстрируется примером 1.
В процессе механоактивации, кроме измельчения частиц компонентов и их усреднения, происходит образование агрегатов наночастиц компонентов, а также первичная химическая межфазная сшивка с образованием наноблоков композиционного материала, в котором возникают электропроводные углеродные контакты и/или токосъемы.
Длительность и интенсивность процесса механообработки (применяемая величина ускорения ударяющего тела 20-200 g) смеси подбирается таким образом, чтобы размеры наночастиц в агрегатах частиц малопроводящего материала в промежуточном нанокомпозите после такой обработки составляли 2-100 нм, размеры наночастиц в агрегатах электропроводящей углеродной добавки с окисленной поверхностью составляли 1-20 нм, а сам процесс механоактивации занимал минимальное время (предпочтительно менее 60 мин).
Частная схема межфазной химической сшивки и возникновения наноблоков электропроводного композиционного углерод-фторуглеродного материала представлена на фиг.3, а обобщенная схема показана на фиг.6. Физико-химической основой межфазной химической сшивки и получения промежуточного нанокомпозита является протекание реакции дегидратации на межфазных границах агрегатов наночастиц компонентов с участием атомов и молекулярных группировок из контактирующих наноблоков строения этих агрегатов и образованием множества межповерхностных химических связей типа “А-О-С (sp2– или sp3-)”, где А – атом поверхности частицы малопроводящего материала (Si, Ge, As, Sb, In). В случае межфазной химической сшивки наноблоков строения окисленных углеродных и фторуглеродных материалов могут протекать как прямые реакции краевых атомов sp2– и sp3-углepoдa с образованием переходов sp2-sp3-зон и краевых sp3-C-F-связей, так и реакции межфазных (межповерхностных) химических связей типа “С-О-С” за счет реакций sp3-С-ОН и sp3-C-F с образованием и последующим отщеплением HF, а также реакций sp3-C-OH, sp2-COOH или sp2>C=O и sp3-C-OH с образованием и отщеплением воды. Из схемы фиг.6 также вполне ясно, почему для получения множественных химических углеродных электрических контактов с частицей малопроводящего материала необходимо использование именно окисленных углеродных частиц, содержащих на своей внешней (контактной) поверхности кислородсодержащие группы sp3-С-ОН, sp2-COOH или sp2>C=O. Наличие этих функциональных групп фиксируется в ИК-спектре промежуточного нанокомпозита фиг.5 полосами поглощения при 1040, 1470, 1520 и 1576 см-1 соответственно. В механохимических реакциях фторуглерода ФС и окисленного углеродного материала ТРГ-O участвует влага (полоса 3440 см-1), причем ее относительное количество после механоактивации существенно уменьшается, в связи с ее расходованием на гидролиз связей sp3-C-F.
Термообработку промежуточного нанокомпозита после механохимической обработки проводят при 150-400°С до достижения постоянной массы, причем, как правило, для достижения постоянной массы достаточно 2-3 часов. При термообработке промежуточного нанокомпозита происходят реакции дегидратации (или отщепление HF) на агрегатах наночастиц малопроводящего материала образуются поверхностные электропроводные углеродные контакты и/или токосъемы (фиг.3 и 6). Прочность этих электрических углеродных контактов обеспечивается множеством межповерхностных химических связей “А-О-С (sp2– или sp3-)”, “С-С” и “С-О-С”, а высокая электронная электропроводность обеспечивается зонами проводимости графитоподобных слоев углерода, причем наноблоки строения таких углеродных контактов при межфазной химической сшивке могут располагаться как перпендикулярно, так и параллельно поверхности частицы малопроводящего материала (фиг.6). Возможность реализации и химической фиксации на поверхности частицы малопроводящего материала двух ориентаций электрических углеродных контактов (токосъемов) обеспечивается наличием на поверхности углеродных наноблоков двух типов окисленного углерода в sp2– и sp3-координации, в виде функциональных кислородсодержащих групп sp3-C-OH, sp2-COOH или sp2>C=O.
Полученный промежуточный нанокомпозит, содержащий углеродные электрические контакты (токосъемы), смешивают известными способами [1] со связующим, взятым в количестве 5-10% от массы промежуточного нанокомпозита, и подвергают сушке при 105-150°С до достижения постоянной массы, после чего известными способами формуют изделие заданной формы – электрод или пленку, обладающее заданной электропроводностью. При этом количество связующего, в качестве которого, как правило, используют фторопластовую суспензию Ф4Д или иной фторполимер с водооталкивающими свойствами, выбирают по принципу минимальной достаточности для формования известными способами (прессованием, прокаткой и др.) гибкого изделия заданной формы – электрода или пленки. Обычно для этих целей достаточно 3-10% фторполимерного связующего от общей массы композита.
Практическая осуществимость объекта-материала и объекта-способа демонстрируется следующими типичными примерами.
Пример 1. Получение окисленных углеродных материалов
Получение окисленного углеродного материала общей формулы CxOyHz·nH2O, x=0.9-0.99, y=0.01-0.1, z=0.001-0.05, n=0.005-1.0, проводят окислением порошков углерода с размером агрегатов частиц менее 500 мкм и удельной поверхностью 2-1000 м2/г при 20-400°С в присутствии кислородсодержащих реагентов.
В качестве исходных материалов были использованы порошки технических углеродных материалов – графит марки ГАК-1 (предварительно очищенный от примесей известными способами), сажа газовая по ГОСТ 7885 “Углерод технический для производства резины” и техносорб по ТУ 38 41538-94, терморасширенный графит ТРГ-400, имеющие размеры агрегатов частиц менее 200 мкм и удельную поверхность 2-1000 м2/г. ТРГ-400 получали термолизом порошка фтороксида графита марки ФОГ-Э (ТУ 349735-0004-03533984-97) при 400°С в течение 4 час. Содержание суммы примесей Fe, Ca, Si и др. в исходных углеродных материалах – менее 0.5%. Существенные технические характеристики исходных углеродных материалов приведены в таблице 2. Окисление исходных углеродных материалов проводили тремя способами – водными растворами кислородсодержащих окислителей при 20-60°С и соотношении Т:Ж=1:2-1:5, обработкой при 200-400°С влажным воздухом или кислородом, получаемым барботажем газа через воду при комнатной температуре, а также механоактивацией (МА) в присутствии 2-5% воды на воздухе. Содержание суммы примесей Fe, Ca, Si и др. в окисленных углеродных материалах – менее 0.12%. Существенные технические характеристики окисленных углеродных материалов и условия их получения приведены в таблице 3.
Жидкофазное окисление углеродных материалов проводили водными растворами кислородсодержащих окислителей без перемешивания в указанных в таблице 3 концентрациях и диапазонах условий в течение 12-120 час. После завершения процессов жидкофазного окисления полученные продукты фильтровали, промывали до рН 5-7 и сушили 3 час при 105-120°С на воздухе.
Окисление углеродных материалов с применением механоактивации (МА) проводили в присутствии 1-5% воды с применением лабораторной планетарно-фрикционной мельницы ММЛ с ускорением ударяющего мелющего тела (болбера из карбида вольфрама) в воздушной среде. Полученные этим методом окисленные углеродные материалы сушили 3 час при 105-120°С на воздухе.
В результате указанной в настоящем примере обработки получают порошки окисленных углеродных материалов общей формулы CxOyHz·nH2O, x=0.9-0.99, y=0.01-0.1, z=0.001-0.05, n=0.005-1.0, причем обычно достигаемые размеры агрегатов частиц этих материалов составляют 5-500 мкм (в среднем 70-300 мкм), удельная поверхность – 2-1000 м2/г, предпочтительно 100-400 м2/г. Окисление исходных углеродных материалов в указанных условиях приводит к получению агрегатов наночастиц углерода с окисленной поверхностью, на которой, по данным Фурье ИК-спектроскопии, присутствуют кислородсодержащие функциональные группы sp3-C-OH, sp2-COOH или sp2>C=O, а также адсорбированная влага. По данным рентгеновской дифракции, основные рефлексы окисленных углеродных фаз 002 и 004 значительно уширены и имеют межплоскостные расстояния в диапазоне d002=3.33-3.39 и d004=1.662-1.695 . Рассчитанные с применением формулы Дебая-Шерера размеры областей когерентного рассеяния (ОКР), по величинам полуширин рефлексов 002 и 004, агрегатов наночастиц окисленных углеродных материалов составляют 20-500 (2-50 нм). В частности, размеры ОКР для окисленного терморасширенного графита (ТРГ-O) составляют (таблица 1) 230-330 , для окисленного техносорба – 20-40 , для окисленной сажи – 15-30 , для окисленного графита ГАК-1 – 350-850 .
Удельное сопротивление окисленных углеродных материалов, полученных по условиям настоящего примера, зависит от типа исходного углеродного материала, глубины его окисления и обычно составляет 0.01-1.5 Ом·см.
Перечисленные в таблице 3 окисленные углеродные материалы далее использованы в примерах 2-5 с шифрами: окисленный терморасширенный графит ТРГ-400 – “Р”, сажа газовая окисленная – “С”, графит окисленный – “Г”, техносорб окисленный -“Т”, терморасширенный графит, окисленный с применением механоактивации, “РМ”.
Пример 2. Получение резистивных композитов в системах “окисленный углерод-кремний” и “окисленный углерод-фторуглерод-кремний”
Для изготовления резистивных композитов были использованы такие малопроводящие материалы, как фторуглеродный материал марки ФС по ТУ 349735-0003-03533984-97 (поликарбонофторид порошкообразный) и кремний полупроводниковый измельченный (порошок БДМК с размером гранул менее 1 мм), их смеси и окисленные углеродные материалы – “Р”, “С” и “Т” (ТРГ, сажа и техносорб) в соответствии с шифрами примера 1.
В соответствии с исходными составами, указанными в таблице 4, были приготовлены смеси по 1 г порошков малопроводящих материалов (фторуглерода ФС и кремния) с окисленными углеродными материалами с шифрами “Р”, “С”, “Г” и “Т”, которые были подвергнуты механоактивации (МА) с использованием лабораторного планетарно-фрикционного агрегата ММЛ по способам, изложенным в формуле изобретения, и в условиях, представленных в таблице 4. Из полученных резистивных композитов путем прессования под давлением 100 атм (~1.3·107 Па/м2) были приготовлены таблетки массой 100 мг и диаметром 5 мм и известным методом измерены их удельные сопротивления постоянному току.
Из приведенных в таблице 4 составов следует, что с применением материалов и способов их получения по настоящему изобретению созданы новые композиционные углеродсодержащие резистивные материалы с удельным сопротивлением 0.05-1.4·107 Ом·см, причем величина сопротивления не может быть описана схемой эквивалентных параллельных сопротивлений исходных компонентов фиг.1. Особенно наглядно это видно из удельных сопротивлений резистивных композитов на основе ТРГ-O, которые были получены при 150°С (температура, при которой заметного окисления компонентов композита не происходит) – их удельное сопротивление всего в несколько раз больше сопротивления эквивалентной схемы фиг.1. Из этого следует, что в системах таблицы 4 – полученных композиционных материалах после обработки возникли дополнительные сопротивления в виде химических межповерхностных наноразмерных электрических углеродных контактов (токосъемов).
Наноразмерность электрических углеродных контактов доказывается данными дифракционных исследований (таблица 4, фиг.7) – размеры ОКР (областей когерентного рассеяния), полученных в изученных системах агрегатов наночастиц резистивных композиционных электропроводных углеродсодержащих материалов, составляют 20-1000 (в среднем ~300-700 ), причем размеры углеродных нанофаз составляют 18-500 (в среднем ~250-300 ). При этом в системах “окисленный углерод-кремний” и “окисленный углерод-фторуглерод-кремний” во время МА-процессов протекают следующие важные изменения:
– отношение взаимных интенсивностей основных рефлексов от кремния, ТРГ и ФС изменяется в сторону уменьшения относительного количества ТРГ и ФС в МА-продуктах,
– в продуктах после МА регистрируются нанофазы карбида кремния (SiC) с размерами ОКР ~150-200 при их относительном содержании около 1%, а также появляются рефлексы неидентифицированных нанофаз (фиг.7, справа) при 2 ~ 9, 11, 47 и 59°,
– размер наноагрегатов частиц фторуглерода ФС составляет 18-25 во всех случаях.
По данным Фурье ИК-спектров (фиг.8-9), в изученных системах “углерод-кремний” и “углерод-фторуглерод-кремний” после МА-процессов получают нанокомпозиты, в которых на поверхности частиц фиксируются различные функциональные группы – sp3-C-OH (1030-1090 см-1), sp2-C=O и колебания делокализованных С-С-связей углеродных колец ( -система окисленного графита) при 1380-1580 см-1), колебания sp2-COOH и влаги (в области ~1630-1740 см-1) sp2-sp3-переходы (1080-1120 см-1) и sp3-C-F (1200-1320 см-1).
И, наконец, в спектрах систем “углерод-кремний” и “углерод-фторуглерод-кремний” (фиг.8-9) обнаруживаются слабые линии в районе ~800 см-1, которые относятся к ковалентным связям Si-C, что полностью согласуется с данными дифракционных исследований (фиг.7) по обнаружению нанофаз карбида кремния. Полоса (Si-C) четко видна в системах фиг.8-9, причем с возрастанием времени МА она смещается в высокочастотную область для систем с фторуглеродом при 20 и 30 мин активации или не меняет положение в спектре системы с ТРГ-O.
Необходимость термообработки при 140-400°С резистивных нанокомпозитов, смешанных со связующим (5-10% фторопластовой суспензии Ф4Д – ТУ 6-05-1246-81), до достижения постоянной массы демонстрируется данными табл.4, в которой приведены величины удельных сопротивлений свежеприготовленных нанокомпозитов системы “окисленный углерод-кремний-фторуглерод”, так как при такой термообработке нанокомпозит приобретает влагоустойчивость за счет высокой гидрофобности фторполимерного связующего, а заданное удельное сопротивление для конкретной системы с кремнием регулируется условиями термообработки. Из данных табл.4 следует, что удельное сопротивление нанокомпозита при 140-400°С изменяется значительно, почти на два порядка, что происходит, по данным ИК-спектроскопии, за счет окисления поверхности агрегатов наночастиц кремния и в зависимости от состава исходной системы.
Таким образом, комплекс данных по рентгеновской дифракции, Фурье ИК-спектров и прямых измерений удельной электропроводности композитов, получаемых в системах “углерод-кремний” и “углерод-фторуглерод-кремний” подтверждает их нанокомпозитную природу и тот отличительный признак настоящего изобретения, что в углеродсодержащих композиционных электропроводных материалах с заданным удельным сопротивлением в диапазоне 0.05-1.4·107 Ом·см присутствуют химические межповерхностные наноразмерные электрические углеродные контакты и/или токосъемы, осуществляемые межчастичными химическими sp2– и sp3-связями поверхностно окисленного углерода с наружными атомами поверхности частиц малопроводящего материала.
Особо следует отметить прямую практическую полезность изобретения. Из данных последней строки таблицы 4 следует, что после получения промежуточного резистивного нанокомпозита, добавления к нему 5% связущего (фторопластовой суспензии Ф4Д) и изготовления из него известным способом путем прокатки (или прессования) гибкого электрода получается готовый гибкий резистор с удельным сопротивлением (8.5±0.5)·103 Ом·см.
Пример 3. Получение резистивных композиционных материалов в системах “окисленный углерод-фторуглерод”
Для изготовления резистивных композитов были использованы малопроводящие фторуглеродные материалы – поликарбонофториды порошкообразные марок ФС и ФТ по ТУ 349735-0003-03533984-97 с размером агрегатов частиц менее 6 мкм (удельная поверхность 350 и 450 м2/г) и окисленные углеродные материалы – “Р”, “С”, “РМ”, “Т” (ТРГ, техносорб и сажа) в соответствии с шифрами примера 1.
В соответствии с исходными составами, указанными в таблице 5, были приготовлены смеси по 1 г порошков малопроводящих материалов (фторуглеродов ФС и ФТ) с окисленными углеродными материалами с шифрами “Р”, “С”, “Г” и “Т”, которые были подвергнуты механоактивации (МА) с использованием лабораторного планетарно-фрикционного агрегата ММЛ и последующей термообработке по способам формулы изобретения и в условиях, представленных в таблице 5. Из полученных резистивных композитов путем прессования под давлением 100 атм (~1.3·107 Па/м2) были приготовлены таблетки массой 100 мг и диаметром 5 мм и известным методом измерены их удельные сопротивления постоянному току.
Из приведенных в табл.5 составов следует, что с применением материалов и способов их получения по настоящему изобретению созданы новые композиционные углеродсодержащие резистивные материалы с заданным удельным сопротивлением, изменяющимся и регулируемым в диапазоне 12 порядков – от ~2 до 1012 Ом·см, причем величина сопротивления не может быть описана схемой эквивалентных параллельных сопротивлений исходных компонентов фиг.1. Из этого следует, что в системах табл.5 – полученных композиционных материалах после обработки возникли дополнительные сопротивления в виде химических межповерхностных наноразмерных электрических углеродных контактов (токосъемов). Величина их сопротивлений является промежуточной между сопротивлениями углерода и малопроводящего материала (фторуглерода) и описывается схемой фиг.2.
Наноразмерность электрических углеродных контактов(токосъемов) доказывается данными дифракционных исследований (табл.1, фиг.4) – размеры ОКР полученных в системах агрегатов наночастиц резистивных композиционных электропроводных углеродсодержащих материалов составляют: для “Г” (окисленный графит) – 600-1000 (в среднем ~800-900 ), для “Р” (ТРГ-O) – 170-330 (в среднем ~200 ), для “С” и ФС – 15-30 (в среднем ~20-25 ), причем диапазон размеров углеродных нанофаз составляет 15-1000 (в среднем ~20-200 ). При этом в системах “окисленный углерод (например, ТРГ-O) – фторуглерод” во время МА-процессов протекают следующие важные изменения (таблица 1):
– отношение взаимных интенсивностей основных рефлексов ТРГ-O и ФС изменяется в сторону уменьшения относительного количества ТРГ к ФС в МА-продуктах (например, отношение суммарной интенсивности пиков 001 и 003 в ФС к суммарной интенсивности пиков 002 и 004 в ТРГ-O изменяется от ~70:30 до ~64:10).
– в продуктах после МА регистрируется дополнительный рефлекс при 2 ~21.7° (переходы зон sp2-sp3 [16], размеры ОКР в ТРГ-O уменьшаются от 230-330 до 170-240 при их относительном содержании к фторуглероду от ~1:100 до 10:1.
Необходимость сушки при 105-150°С (термообработки) промежуточных механоактивированных нанокомпозитов, смешанных со связующим (5-10% фторопластовой суспензии Ф4Д) до достижения постоянной массы, демонстрируется данными табл.6, в которой приведены величины удельных сопротивлений свежеприготовленных нанокомпозитов системы “окисленный углерод-фторуглерод” и их же после сушки 6 часов при 140°С. При этом удаляется остаточная влага, резистивный нанокомпозит приобретает влагоустойчивость за счет высокой гидрофобности фторполимерного связующего и достигается заданное удельное сопротивление для конкретной системы. Из данных табл.6 следует, что удельное сопротивление при таких режимах сушки изменяется незначительно (на 5-40%) в зависимости от состава исходной системы.
Пример 4. Получение резистивных композитов в системах “окисленный углерод-полупроводник АIIIBV” и “окисленный углерод-фторуглерод-АIIIBV“
Для изготовления резистивных композитов были использованы полупроводниковые материалы – антимонид индия InSb, арсенид галлия GaAs и арсенид индия InAs (представлены из Института физики полупроводников СО РАН), малопроводящий фторуглеродный материал – поликарбонофторид порошкообразный марки ФС по ТУ 349735-0003-03533984-97 с размером агрегатов частиц менее 6 мкм (удельная поверхность 350 и 450 м2/г) и окисленный углеродный материал “Р” (ТРГ-O).
В соответствии с исходными составами, указанными в табл.7, были приготовлены смеси по 1 г порошков малопроводящих материалов (полупроводников АIIIBV, фторуглерода ФС и их смесей) с окисленными углеродными материалами с шифром “Р” (ТРГ-O), которые были подвергнуты механоактивации (МА) с использованием лабораторного планетарно-фрикционного агрегата ММЛ и последующей термообработке, по способам формулы изобретения и в условиях, представленных в табл.7. Из полученных резистивных композитов путем прессования под давлением 100 атм (~1.3·107 Па/м2) были приготовлены таблетки массой 200 мг и диаметром 5 мм и известным методом измерены их удельные сопротивления постоянному току.
Из приведенных в табл.7 составов следует, что с применением материалов и способов их получения по настоящему изобретению созданы новые наноразмерные композиционные углеродсодержащие резистивные материалы с заданным удельным сопротивлением, изменяющимся и регулируемым в диапазоне 1.3-31 Ом·см, причем величина сопротивления полученных резистивных композитов не может быть описана схемой эквивалентных параллельных сопротивлений исходных компонентов фиг.1. Из этого следует, что в системах табл.7 – полученных композиционных материалах после обработки возникли дополнительные сопротивления в виде химических межповерхностных наноразмерных электрических углеродных контактов (токосъемов) с размерами 250-1000 . Величина их сопротивлений является промежуточной между сопротивлениями углерода и малопроводящих материалов (полупроводников АIIIBV и фторуглерода) и описывается схемой фиг.2.
Пример 5. Получение электропроводных углеродсодержащих композиционных материалов для литиевых источников тока в системах “окисленный углерод-фторуглерод”, “окисленный углерод-диоксид марганца-фторуглерод”.
Из малопроводящих материалов – фторуглерода ФС, диоксида марганца и окисленного углерода “Р” (ТРГ-O) по описанным в формуле настоящего изобретения способам были изготовлены электропроводные углеродсодержащие композиционные материалы, с удельными сопротивлениями 0.1-1.5 Ом·см, составы которых и особенные условия обработки приведены в таблице 8.
Путем добавления фторопластового связующего (5-10% от массы электропроводных композиционных углеродных материалов) известными способами [1] были изготовлены испытательные серии катодных материалов трех типов – на основе фторуглерода ФС, на основе диоксида марганца и на основе смеси фторуглерода ФС и диоксида марганца. Из сформованных известным способом [1] катодов были собраны дисковые литиевые химические источники тока (ХИТ) в типоразмерах BR2325 (на основе фторуглерода ФС – CF1.2), CR2325 (на основе МnО2), BR2325-M (на основе смеси CF1.2+МnО2) со стандартным электролитом 1М LiClO4 в смеси пропиленкарбоната и диметоксиэтана (1:1). После сборки и технологической выдержки 2 месяца были проведены испытания ХИТ по ГОСТ 29284-92 с получением пиковых вольтамперных характеристик и в условиях эксплуатации при разных токах путем разряда на постоянных нагрузках. Для сравнения были использованы рыночные ХИТ BR2325 фирмы Panasonic (Япония), имеющие, по данным [5, 8], удельную емкость ~500 мАч/г.
Усредненные (n=10 шт. в каждой серии) удельные пиковые и эксплуатационные характеристики полученных по настоящему изобретению катодных материалов из электропроводных композиционных углеродных материалов собранных серий приведены на фиг.10-11. Из этих данных следует, что по плотности тока эксплуатационного разряда, мощности и удельной электрической емкости
Данные таблиц 1-9 и фиг.2-11 однозначно показывают, что применение электропроводных композиционных углеродных материалов на основе малопроводящих материалов, смешанных с электропроводной углеродной добавкой и связующим, и способа их получения с вышеуказанными отличительными признаками позволило добиться следующих преимуществ заявляемого объекта и способа перед описанными прототипами:
– созданы новые типы электропроводных углеродсодержащих композиционных материалов с широким диапазоном удельного сопротивления ~0.1-1012 Ом·см с внутренним межчастичным электрическим токосъемом между проводящими углеродными частицами-контактами и частицами малопроводящих материалов ~10-1015 Ом·см,
– новые типы электропроводных углеродсодержащих композиционных материалов пригодны для изготовления гибких резистивных композитов с широким диапазоном удельного сопротивления ~0.1-1012 Ом·см и/или эффективных электродов литиевых ХИТ,
– надежность межчастичного электрического контакта (токосъема) между электропроводными углеродными частицами и частицами малопроводящих материалов обеспечена межфазными химическими связями sp2– и sp3-углерода с наружными атомами поверхности частиц малопроводящего материала путем образования в композиционном материале химических межповерхностных наноразмерных электрических углеродных контактов, которые могут выполнять также роль внутренних токосъемов, что позволило повысить удельные энергетические характеристики электродов литиевых ХИТ, в том числе эксплуатационной плотности тока разряда и отдаваемой эксплуатационной мощности,
– применение наночастиц в агрегатах малопроводящего материала размером 2-100 нм и наночастиц в агрегатах электропроводящей углеродной добавки с окисленной поверхностью размером 1-20 нм позволяет обеспечить получаемым углеродсодержащим композиционным электропроводным материалам гибкость, необходимую для изготовления гибких резисторов с широким диапазоном удельного сопротивления и/или эффективных электродов литиевых ХИТ,
– применение фторуглерода и добавки в композит фторопластового связующего позволяет обеспечить получаемым углеродсодержащим композиционным электропроводным материалам водооталкивающие свойства.
Практическая полезность изобретения связана с возможностью изготовления гибких углеродсодержаших нанокомпозитных резисторов, обладающих внутренним химически связанным углеродным токосъемом (химическим углеродным контактом) с наиболее широким известным (на текущий момент) диапазоном регулирования величин удельных сопротивлений – =0.1-1012 Ом·см, что особенно важно при изготовлении суперконденсаторов с удельной емкостью до 120-150 фарад на 1 г, и цепей управления такими устройствами.
Описываемые в изобретении гибкие нанокомпозитные резисторы на основе систем “пористый углерод-фторуглерод” целесообразно использовать в качестве ленточных электропроводных матриц для изготовления пористых электродов, наполненных термочувствительными гидридными фазами, применямыми в водородной энергетике.
Таблица 1 |
Динамика изменений в дифрактограммах при механоактивации (МА) смесей фторуглерода CF1.2 типа ФС и ТРГ-O (окисленный терморасширенный графит), взятых в соотношении 88:12 |
Параметры пиков |
001 ФС |
Доп. пик |
002 ТРГ-O |
003 ФС |
004 ТРГ-O |
ФС Сумма в % пиков 007 и 003 для ФС |
ФС Отношение пиков 001 к 003 |
ТРГ-O Сумма в % пиков 002 и 004 для ТРГ |
ТРГ-O Отношение пиков 002 к 004 |
РФС – после слабой исходной активации (40 g, 30 сек) и перемешивания |
2 , град |
13.0 |
– |
26.6 |
41.3 |
54.7 |
70.1 |
0.55 |
29.9 |
8.5 |
I, имп |
4700 |
– |
5075 |
8604 |
596 |
I, % |
54.6 |
– |
59.0 |
100 |
6.9 |
окр,  |
20-30 |
– |
500-940 |
10-20 |
230-330 |
РФС-2-МА – 2 мин интенсивной механоактивации (120-200 g) |
2 , град |
13.1 |
21.7 |
26.6 |
41.3 |
54.8 |
49.5 |
0.50 |
50.5 |
26.3 |
I, имп |
4019 |
– |
11761 |
7963 |
448 |
I, %от max. |
34.2 |
<1 |
100 |
67.7 |
3.8 |
ОКР,  |
20-30 |
– |
290-510 |
10-20 |
260-360 |
РФС-5-МА – 5 мин интенсивной механоактивации (120-200 g) |
2 , град |
12.9 |
21.7 |
26.1 |
41.3 |
54.7 |
62.7 |
0.69 |
34.9 |
26.8 |
I, имп |
4374 |
~400 |
5765 |
6363 |
215 |
I, %от max. |
68.7 |
~6.3 |
90.6 |
100 |
3.4 |
ОКР,  |
20-30 |
– |
100-140 |
10-20 |
230-340 |
РФС-10-МА – 10 мин интенсивной механоактивации (120-200 g) |
2 , град |
12.9 |
21.7 |
26.5 |
41.4 |
54.7 |
80.6 |
0.46 |
13.7 |
24.7 |
I, имп |
5263 |
~1200 |
2739 |
11548 |
111 |
I, %от max. |
45.6 |
~10 |
23.7 |
100 |
1.0 |
ОКР,  |
20-30 |
~5-10 |
150-360 |
10-20 |
180-260 |
РФС-15-МА -15 мин интенсивной механоактивации (120-200 g) |
2 , град |
13.0 |
~21.7 |
26.5 |
41.4 |
54.7 |
63.7 |
0.53 |
10.2 |
23.8 |
I, имп |
3363 |
~4000 |
1502 |
6398 |
63 |
I, %от max. |
52.6 |
~60 |
23.5 |
100 |
1.0 |
ОКР,  |
20-30 |
~5-10 |
240-380 |
10-20 |
170-240 |
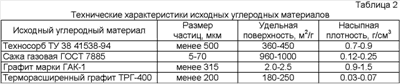
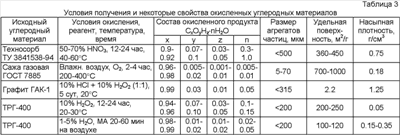
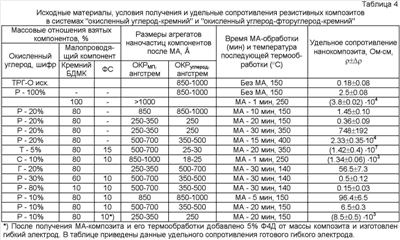
Таблица 5 |
Исходные материалы, условия получения и удельные сопротивления резистивных композитов в системах “окисленный углерод-фторуглерод” |
Массовые отношения компонентов, % |
Время МА-обработки (мин) и температура последующей термообработки (°С) |
Удельное сопротивление нанокомпозита, Ом·см, ±  |
Окисленный углерод, шифр |
Малопроводящий компонент |
ФС |
ФТ |
С – 0.99% |
 |
99.01% |
МА – 30 мин, 150 |
1012 |
Р – 0.99% |
99.01% |
 |
МА – 30 мин, 150 |
1011 |
С – 1.8% |
 |
98.2% |
МА – 30 мин, 150 |
1010 |
Р – 1.8% |
98.2% |
 |
МА – 20 мин, 150 |
109 |
С – 6.4% |
 |
93.6% |
МА – 30 мин, 150 |
7.89±0.37·107 |
Р – 6.4% |
93.6% |
 |
МА – 30 мин, 150 |
3.54±0.44·106 |
Р – 20% |
80% |
 |
МА – 1 мин, 150 |
(3.47±0.53)·103 |
РМ – 10%*) |
90% |
 |
МА – 5 мин, 150 |
(5.14±1.30)·103 |
РМ – 10%*) |
90% |
 |
МА – 10 мин, 150 |
1.15±0.03·105 |
РМ – 10%*) |
90% |
 |
МА – 20 мин, 150 |
2.69±0.35·103 |
РМ – 10%**) |
90% |
 |
МА – 5 мин, 150 |
1.47±0.12·106 |
РМ – 10%**) |
90% |
 |
МА – 10 мин, 150 |
1.18±0.02·105 |
РМ – 10%**) |
90% |
 |
МА – 20 мин, 150 |
7.39±0.37·105 |
РМ – 10%***) |
90% |
 |
МА – 5 мин, 150 |
9.09±0.33·104 |
РМ – 10%***) |
90% |
 |
МА – 10 мин, 150 |
3.42±0.67·104 |
РМ – 10%***) |
90% |
 |
МА – 20 мин, 250 |
7.39±0.4·105 |
С – 32.6% |
67.4% |
 |
МА – 1 мин, 140 |
4,37±0,08 |
С – 32.6% |
67.4% |
 |
МА – 10 мин, 140 |
10,96±0,25 |
С – 32.6% |
67.4% |
 |
МА – 20 мин, 140 |
12,42±0,74 |
Р – 32.6% |
67.4% |
 |
МА – 5 мин, 140 |
6,99±0,09 |
Р – 32.6% |
67.4% |
 |
МА – 10 мин, 140 |
5,37±0,12 |
Р – 32.6% |
67.4% |
 |
МА – 20 мин, 140 |
6,60±0,45 |
Р – 56.7% |
43.3% |
 |
МА – 1 мин, 140 |
3,55±0,12 |
Р – 56.7% |
43.3% |
 |
МА – 3 мин, 140 |
3,66±0,10 |
Р – 56.7% |
43.3% |
 |
МА – 10 мин, 140 |
3,45±0,11 |
Р – 56.7% |
43.3% |
 |
МА – 20 мин, 150 |
3,71±0,11 |
Г – 90.91% |
9.09% |
 |
МА – 20 мин, 150 |
0.09±0.01 |
С – 56.7% |
43.3% |
+10% Ф4Д |
МА – 1 мин, 150 |
6,61±0,20 |
С – 56.7%****) |
43.3% |
+10% Ф4Д |
МА – 3 мин, 150 |
10,76±0,47 |
С – 56.7%****) |
43.3% |
+10% Ф4Д |
МА – 6 мин, 150 |
10,28±0,50 |
С – 56.7%****) |
43.3% |
+10% Ф4Д |
МА – 10 мин, 150 |
12,24±0,16 |
*) Получение окисленного углерода РМ (ТРГ-O) проводят МА-обработкой в присутствии 1% влаги по условиям примера 1; **) – то же самое в присутствии 2% влаги; **) – то же самое в присутствии 5% влаги; композита и его термообработки добавлено 5% Ф4Д от массы композита и изготовлен гибкий электрод; ****) После получения МА-композита и его термообработки добавлено 10% фторопластового связующего Ф4Д от массы композита и методом прокатки изготовлен гибкий электрод. В таблице приведены данные удельного сопротивления готовых гибких электродов. |
Таблица 6 |
Изменения удельных сопротивлений механоактивированных резистивных композитов в системах “окисленный углерод-фторуглерод” после сушки при 140°С |
Массовые отношения компонентов, % |
Время МА-обработки (мин) и температура последующей термообработки (°С) |
Удельное сопротивление резистивного нанокомпозита, Ом·см, ±  |
Окисленный углерод, шифр |
Малопроводящий компонент |
ФС |
Р – 19.5% |
80.5% |
1 мин, не сушили |
6.17±0.07 |
Р – 19.5% |
80.5% |
6 мин, не сушили |
2.70±0.04 |
Р – 19.5% |
80.5% |
60 мин, не сушили |
7.82±0.08 |
Р – 19.5% |
80.5% |
1 мин, сушка 6 час |
10.93±0.45 |
Р – 19.5% |
80.5% |
6 мин, сушка 6 час |
2.81±0.05 |
Р – 19.5% |
80.5% |
40 мин, сушка 6 час |
8.04±0.05 |
Р – 26.4% |
73.6% |
1 мин, не сушили |
4.58±0.04 |
Р – 26.4% |
73.6% |
6 мин, не сушили |
1.92±0.04 |
Р – 26.4% |
73.6% |
60 мин, не сушили |
3.38±0.04 |
Р – 26.4% |
73.6% |
6 мин, сушка 6 час |
1.93±0.05 |
Р – 26.4% |
73.6% |
60 мин, сушка 6 час |
4.04±0.13 |
Таблица 7 |
Исходные материалы, условия получения и удельные сопротивления резистивных композитов в системах “окисленный углерод-АIIIBV” и системах “окисленный углерод-АIIIBV-фторуглерод” |
Массовые отношения компонентов, % |
Размеры агрегатов наночастиц компонентов, А*) |
Время МА-обработки (мин) и температура последующей термообработки (°С) |
Удельное электрическое сопротивление Ом·см, ±  |
Окисленный углерод |
Малопроводящий компонент |
ОКРМП, ангстрем АIIIBV |
ОКРуглерод, ангстрем |
АIIIBV |
ФС |
– |
InSb – 100 |
– |
300-700 |
– |
1 мин |
206.8±23,6 |
Р – 10 |
InSb – 80 |
10 |
100-300 |
850-1000 |
10 мин, 150°С |
4,34±0,14 |
Р – 10 |
InSb – 80 |
10 |
80-200 |
250 |
20 мин, 150°С |
5.40±0.21 |
Р – 10 |
InSb – 80 |
10 |
70-170 |
200-250 |
30 мин, 150°С |
6,00±0,16 |
Р – 20 |
InSb – 80 |
– |
200-400 |
250 |
10 мин, 150°С |
2.92±0.32 |
 |
GaAs – 100 |
– |
800-1000 |
250 |
1 мин |
1.40±0.01·106 |
Р – 10 |
GaAs – 80 |
10 |
не изм. |
850-1000 |
1 мин, 150°С |
4.62±0.13 |
Р – 10 |
GaAs – 80 |
10 |
не изм. |
850-950 |
5 мин, 150°С |
8.90±0.38 |
Р – 10 |
GaAs – 80 |
10 |
750-900 |
250-350 |
10 мин, 150°С |
14.19±0.56 |
Р – 10 |
GaAs – 80 |
10 |
700-900 |
200-250 |
20 мин, 150°С |
31.12±0.77 |
Р – 20 |
GaAs – 80 |
– |
750-900 |
300-350 |
10 мин, 150°С |
1.71±0.11 |
Р – 20 |
GaAs – 80 |
– |
700-900 |
250 |
20 мин, 150°С |
1.34±0.11 |
– |
InAs – 100 |
– |
500-700 |
– |
1 мин |
120±4.5 |
Р – 10 |
InAs – 80 |
10 |
300-400 |
250-500 |
10 мин, 150°С |
3.09±0.13 |
Р – 10 |
InAs – 80 |
10 |
200-350 |
200-250 |
20 мин, 150°С |
3.11±0.13 |
Р – 20 |
InAs – 80 |
– |
300-400 |
750-800 |
10 мин, 150°С |
1.78±0.13 |
Р – 20 |
InAs – 80 |
– |
150-300 |
250 |
20 мин, 150°С |
1.92±0.12 |
*) Размер наночастиц ФС в примерах 2-5 соответствует диапазону 18-25 Å. |
Таблица 8 |
Исходные материалы, условия получения и удельные эксплуатационные параметры катодов литиевых источников тока в типоразмере 2325, изготовленных из электропроводных углеродсодержащих композиционных материалов в системах “окисленный углерод-фторуглерод” и “окисленный углерод-МnО2-фторуглерод” |
Массовые отношения компонентов, % |
Размеры агрегатов наночастиц компонентов, Å |
Время МА-обработки (мин) и температура последующей термообработки (°С) |
Удельная электрическая емкость нанокомпозита, мАч/г |
Окисленный углерод |
Малопроводящий компонент |
ОКРМП, ангстрем |
ОКРуглерод, Å |
MnO2 |
ФС |
5-10 |
35-55 |
55-35 |
120-300 |
250 |
2, 180°С |
450-580 |
5-10 |
– |
90-95 |
24-28 |
250 |
2, 200°С |
600-660 |
5-10 |
35-55 |
55-35 |
120-300 |
250 |
2, 200°С |
470-560 |
5-10 |
– |
90-95 |
24-28 |
250 |
2, 180°С |
620-680 |
Формула изобретения
1. Углеродсодержащий композиционный электропроводный материал на основе малопроводящего материала, смешанного с электропроводной углеродной добавкой и связующим, отличающийся тем, что используют нанокомпозиционный материал, в котором в качестве агрегатов наночастиц малопроводящего материала используют агрегаты фторуглерод, диоксид марганца, полупроводники и/или их смеси, а в качестве электропроводной углеродной добавки используют агрегаты наночастиц углерода с окисленной поверхностью, причем эти наноразмерные агрегаты в композиционном материале между собой имеют химические межповерхностные наноразмерные электрические углеродные контакты и/или токосъемы, осуществляемые межчастичными химическими связями sp2 – и sp3-углерода с наружными атомами поверхности частиц малопроводящего материала.
2. Углеродсодержащий композиционный электропроводный материал по п.1, отличающийся тем, что в качестве полупроводника используют кремний, полупроводники типа А3B5, а в качестве углеродной добавки используют терморасширенный графит, технические углеводороды типа саж, содержащих поверхностные кислородсодержащие поверхностные группы окисленного sp2– и sp3-углepoдa, при этом соотношение масс малопроводящего материала к электропроводной углеродной добавки в смеси составляет 100:1-1:100.
3. Углеродсодержащий композиционный электропроводный материал по п.1, отличающийся тем, что величина удельного сопротивления полученных нанокомпозиционных материалов составляет 0.1-1012 Ом·см, и его величину задают соотношением между количествами частиц малопроводящего материала и частиц электропроводного углерода с окисленной поверхностью, взятых в диапазоне соотношений 100:1-1:10 соответственно.
4. Углеродсодержащий композиционный электропроводный материал по п.1, отличающийся тем, что размер наночастиц в агрегатах малопроводящего материала составляет 2-100 нм, размер наночастиц в агрегатах электропроводящей углеродной добавки с окисленной поверхностью составляет 1-20 нм.
5. Способ получения углеродсодержащего композиционного электропроводного материала, включающий смешение исходных компонентов и их обработку, отличающийся тем, что частицы малопроводящего материала смешивают с электропроводной углеродной добавкой с окисленной поверхностью частиц, перед смешением со связующим порошкообразные частицы малопроводящего материала смешивают с электропроводящей углеродной добавкой с окисленной поверхностью частиц и подвергают эту смесь механохимической обработке с последующей термообработкой и получением промежуточного нанокомпозита, полученный нанокомпозит смешивают со связующим и подвергают сушке при 105-150°С до достижения постоянной массы.
6. Способ получения углеродсодержащего композиционного электропроводного материала по п.5, отличающийся тем, что окисление электропроводящей углеродной добавки проводят при 20-400°С в среде кислородсодержащих реагентов до получения окисленного углеродного материала общей формулы СхОуНz·nН2О, где х=0.9-0.99, у=0.01-0.1, z=0.005-0.05, n=0.1-1.0, с размером агрегатов частиц менее 500 мкм и удельной поверхностью 2-1000 м2/г, и образования кислородсодержащих функциональных групп на поверхностях частиц.
7. Способ получения углеродсодержащего композиционного электропроводного материала по п.5, отличающийся тем, что механохимическую обработку проводят при ускорениях ударяющих тел 20-200 g до получения промежуточного нанокомпозита с заданным удельным сопротивлением 0.1-1012 Ом·см и размерами наночастиц в агрегате малопроводящего материала – 2-100 нм, размер наночастиц в агрегате электропроводящей углеродной добавки с окисленной поверхностью составляет 1-20 нм.
8. Способ получения углеродсодержащего композиционного электропроводного материала по п.5, отличающийся тем, что термообработку промежуточного нанокомпозита после механохимической обработки проводят при 140-400°С до достижения постоянной массы.
РИСУНКИ
|
|