(21), (22) Заявка: 2008117805/03, 07.05.2008
(24) Дата начала отсчета срока действия патента:
07.05.2008
(43) Дата публикации заявки: 20.11.2009
(46) Опубликовано: 27.08.2010
(56) Список документов, цитированных в отчете о поиске:
RU 2323339 С2, 10.12.2007. SU 63942 A1, 31.05.1945. SU 1573159 A1, 23.06.1990. RU 2167290 C1, 20.05.2001. RU 2224888 С2, 27.02.2004. RU 2269003 С2, 27.01.2006. JP 2061288 A, 01.03.1990. US 6224162 B1, 01.05.2001.
Адрес для переписки:
115583, Москва, ул. Елецкая, 23, кв.41, С.А.Кариману
|
(72) Автор(ы):
Кариман Станислав Александрович (RU)
(73) Патентообладатель(и):
Кариман Станислав Александрович (RU)
|
(54) ОЧИСТНОЙ МЕХАНИЗИРОВАННЫЙ КОМПЛЕКС С ДОБЫЧЕЙ ИСКОПАЕМОГО КРУПНЫМИ БЛОКАМИ И ДОСТАВКОЙ ЭСКАЛАТОРАМИ
(57) Реферат:
Изобретение относится к горному делу, в частности к очистным механизированным комплексам для подземной разработки залегающего пологими пластами ископаемого. Техническим результатом является увеличение производительности очистного забоя, обеспечение высокого уровня безопасности, сокращение выделения газа и пыли в атмосферу лавы. Очистной механизированный комплекс для добычи залегающего пологими пластами ископаемого, его разработки крупными блоками и доставки этих блоков эскалаторами включает секции механизированной крепи, гидрорезную очистную машину с катками, обеспечивающими ее передвижение, для вырезания ископаемого из призабойного массива крупными блоками с возможностью прорезания поперечных щелей при неподвижной гидрорезной машине и прорезания задней вертикальной щели посредством непрерывного перемещения гидрорезной машины с исполнительными органами и гидрорежущими головками, соединенными через металлические трубки, на которых они жестко закреплены, с водоподводящей магистралью, идущей от мультипликаторов, придающих воде сверхвысокое давление, гидроусилитель, установленный с возможностью его непрерывного питания водой и эмульсией посредством постоянно подключенных рукавов гидрорезной машины к водоподводящей и эмульсионной магистралям, укладчик магистралей для обеспечения возможности переукладки упомянутых магистралей при движении гидрорезной машины и смене направления ее перемещения при холостом перегоне. Гидрорезная машина выполнена с возможностью прорезания продольных щелей, параллельных плоскости пласта, одновременно с прорезанием задней вертикальной щели с использованием специальных гидрорежущих узлов, гидроусилитель выполнен с возможностью подачи воды сверхвысокого давления на исполнительные органы, обеспечивающие прорезание задней вертикальной и продольной щелей при перемещении гидрорезной машины, а при неподвижной гидрорезной машине – с возможностью подачи всей воды на исполнительные органы, обеспечивающие поперечное гидрорезание, причем длины всех участков по длине лавы непрерывного прорезания поперечных щелей с одной стороны и задней вертикальной и продольной щелей с другой стороны одинаковы. При этом комплекс снабжен пристыкованной с завальной стороны второго эскалатора навесной площадкой для перемещения по ней по длине лавы гидрорезной машины посредством электропривода, соединенного с приводной звездочкой, входящей в зацепление с траковой цепью, располагающейся в желобе, проложенном также на навесной площадке, а в корпусе траковой цепи располагаются все коммуникации, обеспечивающие работу гидроусилителя: эмульсионные напорная и сливная магистрали, водная магистраль и электрокабель. 3 з.п. ф-лы, 10 ил.
Изобретение относится к горному делу в области подземной разработки полезных ископаемых, залегающих пологими пластами.
Известны очистные механизированные комплексы для разработки пологих пластов с использованием комбайнов или стругов. Это комплексы КМ-138, КМ-142, КМ-143, КМ-144 и др. (1). В состав оборудования входят гидравлические механизированные крепи, скребковые конвейеры, комбайны или струги. Для работы механизированных крепей используется гидравлическая энергия эмульсии, которая вырабатывается насосными станциями, расположенными на примыкающей к лаве транспортной выработке.
Наиболее близким является очистной комплекс профессора Каримана (см. патент РФ 2323339, С2, Е21С, зарегистрированный 27 апреля 2008 г.). Добыча ископаемого производится путем его вырезания из призабойного массива крупными блоками врубовыми агрегатами и гидрорезными машинами. В процессе вырезания в нижнюю и среднюю щели вводятся металлические поддоны, с помощью которых производится выемка блоков ископаемого из массива, погрузка на доставочные средства, транспортировка и перегрузка под землей и на поверхности. После выемки из массива перед погрузкой на блоки ископаемого надевается предварительно чехольная и тросовая оснастка для обеспечения целостности блоков и удобства перегрузочных работ.
Погрузка вырезанных блоков на доставочные платформы производится гидроталями или специальными гидроподъемниками, установленными под каждой секцией крепи. Перемещение груженых платформ к транспортным выработкам производится вдоль доставочных дорожек по металлическим направляющим с помощью шахтных грузовых лебедок, расположенных в бермах рядом с транспортными выработками.
Данная конструктивная разработка имеет множество крупных достоинств, поэтому весьма прогрессивна, позволяет достигнуть особенно высоких технико-экономических показателей, обеспечивает высокий уровень безопасности по газовому фактору и экологии, однако ее в настоящее время практически невозможно внедрить в производство. Дело в том, что в связи с полной приватизацией горно-добывающей промышленности в России из госбюджета была исключена статья затрат на создание новой техники. Поэтому создание любого нового изделия очистного оборудования возможно путем финансирования работ частными горно-добывающего компаниями. Однако, как показывает практика, даже весьма крупные частные компании принимают участие в финансировании создания только отдельных образцов ГШО, и то только в плане их модернизации и совершенствования, но не в создании совершенно новых изделий. Для внедрения в производство новой технологии, которая принята за прототип, необходимо разработать и изготовить и запустить в производство семь совершенно новых видов очистного оборудования и два изделия существенно модернизировать. Это:
1) специальная призабойная гидравлическая механизированная крепь, обеспечивающая возможность
– перемещения сквозь нее к выработанному пространству для закладки крупных блоков ископаемого;
– перемещения внутри секций крепи блоков ископаемого для погрузки на доставочные платформы;
– безразборного передвижения 3-х линий металлических направляющих для движения доставочных платформ и гидропускательного агрегата;
– размещения внутри секций крепи гидроподъемников для погрузки блоков ископаемого на доставочные платформы;
2) специальная доставочная платформа грузоподъемностью до 100 т, устойчиво перемещающаяся с грузом из 6-ти блоков ископаемого весом до 17 т каждый по наклонной поверхности почвы лавы с углом наклона до 18 град со скоростью движения 1 м/с;
3) врубовый агрегат на базе 3-х врубовых машин типа Урал – 33 для прорезания продольных щелей у почвы пласта, у кровли пласта и по середине его мощности на глубину 2,2 м по всей длине лавы; при этом врубовый агрегат высотой до 6-ти м должен устойчиво перемещаться со скоростью 2,8 м/мин по наклонной поверхности почвы лавы с углом наклона до 18 град;
4) гидроопускательный агрегат для извлечения блоков ископаемого из верхнего слоя и опускания вниз при погрузке на доставочные платформы;
5) гидроусилитель гидрорезной машины для выработки воды сверхвысокого давления и подачи ее на исполнительные инструменты;
6) гидроподъмник для перемещения на расстояние до 9 м блоков ископаемого весом до 17 т и их погрузки на доставочные платформы;
7) эскалатор, устанавливаемый на доставочную платформу для их разгрузки от блоков на транспортную выработку;
8) гидроцилиндр фронтального действия для передвижки секций крепи и гидроцилиндр поперечной передвижки гидростоек 1-й и 2-й линии.
В свете изложенного выше в связи с отсутствием централизованного финансирования НИОКР по созданию новой очистной техники Кариману С.А. не представляется возможным создание очистного комплекса, принятого за прототип. Необходимо осуществить новую конструктивную разработку, обеспечивающую добычу ископаемого из полого залегающих пластов ископаемого с выемкой его и транспортировкой крупными блоками, которая бы базировалась на использовании существующего серийного очистного оборудования при минимальном его переоснащении. Применение нового изделия возможно только, если оно было ранее хорошо апробировано и на его изготовление имеется вся рабочая документация. Это очень тяжелые ограничения, однако их выполнение. Совершенно необходимо для внедрения в производство новых технологий в современных условиях горнодобывающей промышленности.
Цель изобретения аналогична цели прототипа и состоит в создании технологии, обеспечивающей существенное увеличение производительности очистного забоя по сравнению со средней производительностью комбайновых и струговых комплексно-механизированных очистных забоев, обеспечении высокого уровня безопасности очистных работ, в том числе по газовому фактору, ликвидации запыленности атмосферы лавы пылью, образуемой при добыче ископаемого, ликвидации тяжелого немеханизированного труда, обеспечении высоких технико-экономических показателей производства при работе очистных забоев в сложных горногеологических условиях. Поставленная цель должна быть достигнута без создания новых видов очистного оборудования, а лишь использованием по-новому уже существующего оборудования, либо переоборудованием его небольшого числа новыми деталями. При этом в основе новой технологии добычи должна оставаться прежняя концепция как и в технологии-прототипе: вырезание ископаемого крупными блоками с помощью тонких гидроабразивных струй воды сверхвысокого давления с доставкой ископаемого по лаве и транспортировкой по примыкающим к лаве транспортным выработкам также крупными блоками.
Сохранение данной концепции как основополагающей при разработке новой технологии обеспечивает потенциальную возможность достижения поставленной цели, поскольку в этом случае сохраняются качественно новые технические возможности за счет, с одной стороны, максимального использования преимуществ резания ископаемого тонкими гидроабразивными струями воды сверхвысокого давления по сравнению с резанием массива ископаемого металлического резцами, установленными на шнеках комбайна, с другой стороны, за счет минимального разрушения ископаемого при добыче его блоками.
Таким образом, задача изобретения состоит в достижении той же цели, как и в прототипе, но за счет других технологических решений, обеспечивающих возможность внедрения новой технологии в производство при существующих реальностях в горно-добывающей промышленности.
В новом очистном комплексе впервые предлагается производство подрывки нижней части пласта стругом с перемещением в полость подрывки двух спаренных ставов доставочных эскалаторов, которыми затем производится доставка вырезанных блоков ископаемого к транспортной выработке.
В новом очистном комплексе не создается новая механизированная крепь, как это делается в прототипе, а для крепления лавы используется существующая серийная механизированная крепь, имеющая достаточное по размерам бессточное пространство около забоя.
В новом очистном комплексе не используются врубовый агрегат и две гидрорезные машины для прорезания щелей, поскольку прорезание всех видов щелей обеспечивается одной гидрорезной очистной машиной (сокращенно ГРОМ), для чего она снабжается двумя исполнительными инструментами с многоструйными гидроабразивными режущими узлами.
В новом очистном комплексе впервые в мире для доставки добытого ископаемого по лаве используются эскалаторы, которые создаются на базе существующих серийных скребковых конвейеров путем замены скребков на грузонесущие пластины, перемещающиеся на роликах по днищу рештаков с помощью конвейерных тяговых цепей.
В новом очистном комплексе впервые используется новый способ погрузки добываемого ископаемого на доставочное средство путем сброса под действием собственного веса вырезаемых блоков из нижнего слоя на расположенные под ними два става ранее передвинутых эскалаторов. Спуск блоков ископаемого верхнего слоя при погрузке на эскалаторы также впервые предлагается осуществлять с использованием передвижного ската, перемещающего на катках по ставам эскалаторов.
Также предлагаются новые виды оборудования:
– гидрорезная очистная машина в составе гидроусилителя и двух исполнительных инструментов многоструйного гидроабразивного резания тонкими струями воды сверхвысокого давления: первый для прорезания одновременно нескольких поперечных щелей, второй для одновременного прорезания продольной в плоскости пласта щели и задней вертикальной щели; при этом инструмент прорезания каждой щели имеет несколько режущих узлов, каждый из которых в своем составе имеет гидроабразивную режущую головку с камерой смещения воды с абразивом и две трубки: одна для подачи воды сверхвысокого давления из магистрали подачи воды, другая для подачи абразива из магистрали подачи абразива;
– эскалатор для транспортировки блоков ископаемого, создаваемый на базе существующих серийных скребковых конвейеров путем замены скребков на грузонесущие пластины, перемещающиеся на роликах по днищу рештаков тяговыми цепями с использованием существующих в скребковых конвейерах барабанов, электроприводов и системы управления.
Это дает множество преимуществ, основными из которых являются следующие:
– при разработке высокометаноносных угольных пластов создаются безопасные условия на очистных работах, т.к. исключается возможность взрывов метана в связи с резким сокращением метановыделений в очистном забое и на примыкающих выработках, поскольку уголь не разрушается; при этом остаточная метаноносность угольных блоков, уходящих за пределы свежей струи, достигает 70%;
– резко сокращается запыленность атмосферы очистного забоя, поскольку ликвидируется источник пылеобразования – работа шнеков комбайна по разрушению массива ископаемого, создается экологически чистое производство;
– многократно сокращаются энергозатраты на добычу ископаемого, поскольку при вырезании ископаемого крупными блоками более чем в 10 раз уменьшается объем разрушаемого ископаемого по линиям резания;
– многократно улучшаются технико-экономические показатели добычи: производительность очистного забоя, производительность труда рабочего по очистному забою, себестоимость очистных работ и др.; так, при разработке пологого угольного пласта мощностью 3,2 м расчетная нагрузка на очистной забой составляет 20 тыс.т в сутки, при мощности пласта 6 м – 28,6 тыс.т в сутки; в действующих очистных забоях в настоящее время даже рекордные уровни нагрузки меньше в 1,5-2 раза, а средние показатели меньше в 4-5 раз;
– новый очистной комплекс может быть использован не только на вновь строящихся предприятиях подземной добычи ископаемого, но и на уже действующих с применением существующего очистного оборудования.
Изобретение поясняется чертежами, на каждом из которых показано следующее:
Фиг.1 – гидрорезная очистная машина ГРОМ – 1 ; прорезание поперечных вертикальных щелей; вид в профиль: 1 – факел гидроабразивной струи; 2 – прорезанная плоскость поперечной щели; 3 – не прорезанная плоскость щели; 4 – гидроабразивная режущая головка; 5 – трубка подвода воды сверхвысокого давления (СВД); 6 – трубка подачи абразива к режущей головке; 7 – гибкий рукав подвода воды СВД; 8 – гидроусилитель; 9 – струг; 10 – эскалаторы; 11 – траковая цепь с коммутациями для гидрорезной очистной машины; 12 – приводная звездочка перемещения рабочей площадки с гидроусилителем; 13 – панель расположения исполнительного инструмента поперечного гидрорезания; 14 – направляющие перемещения панели по горизонтали; 15 – направляющие перемещения панели по вертикали.
Фиг.2 – прорезание поперечных щелей гидроабразивным режущим исполнительным инструментом поперечной резки; вид в плане: 2 – поперечные щели в призабойном массиве ископаемого; 4 – гидроабразивные режущие головки; 5 – трубки подвода воды сверхвысокого давления (СВД); 6 – трубки подачи абразива; 13 – панель расположения исполнительного инструмента поперечного гидрорезания; 16 – магистральные трубки подачи воды СВД; 17 – магистральные шланги подачи абразива; 18 – механизированные подъемники (левый и правый) для перемещения по вертикали панели с исполнительным инструментом поперечной резки: 19 – переключающее устройство подачи воды СВД на исполнительный инструмент поперечной резки при остановленной гидрорезной очистной машине; 20 – клапан забора абразива из расходного бункера.
Фиг.3 – вырезание блоков ископаемого из 2-го слоя призабойного массива; вид в профиль; работа гидрорежущего узла прорезания продольной щели во 2-м слое: 4 – гидроабразивная режущая головка; 5 – трубка подачи воды СВД; 6 – трубка подачи абразива; 15 – направляющие; 21 – продольная щель во 2-м слое; 22 – задняя вертикальная щель 2-го слоя; 23 – вырезаемый из 2-го слоя блок ископаемого; 24 – передвижной скат; 25 – струг; 26 – эскалаторы; 27 – механизированная крепь.
Фиг.4 – исполнительный инструмент продольного и заднего щелевого гидрорезания; разрез по А-А на Фиг.3: 28 – гидрорежущий узел наружного резания продольной щели; 29 – гидрорежущий узел внутреннего резания продольной щели; 30 – гидрорежущий узел наружного резания задней щели; 31 – гидрорежущий узел внутреннего резания задней щели; 32 – магистраль подачи воды СВД инструмента продольного и заднего щелевого резания; 33 – магистраль подачи абразива; 34 – площадка размещения инструмента продольного и заднего щелевого резания.
Фиг.5 – прорезание задней вертикальной щели; гидрорежущие узлы задней щелевой резки; разрез по Б-Б на фиг.3: 4 – абразивные гидрорежущие головки; 5 – трубки подачи воды СВД; 6 – шланги подачи абразива.
Фиг.6 – вырезание и выемка блоков ископаемого из призабойного массива 2-го слоя гидрорезной очистной машиной ГРОМ-1 ; фронтальный вид: 4 – гидроабразивные режущие головки поперечного гидрорезания; 8 – гидроусилитель; 13 – панель расположения исполнительного инструмента поперечного гидрорезания; 15 – направляющие по вертикали инструмента поперечного гидрорезания; 23 – вырезаемые блоки ископаемого; 24 – передвижной скат для спуска блоков ископаемого 2-го слоя; 34 – площадка размещения инструмента продольного и заднего щелевого резания; 35 – исполнительный гидрорежущий инструмент продольного и заднего щелевого резания; 36 – исполнительный инструмент поперечного гидрорезания; 37 – направляющие по вертикали инструмента продольного и заднего гидрорезания; 38 – передвижная рабочая площадка размещения гидроусилителя и исполнительных инструментов; 39 – рабочая поверхность навесной площадки для передвижной гидрорезной очистной машины.
Фиг.7 – доставка блоков ископаемого системой спаренных эскалаторов вдоль очистного забоя к транспортной выработке; вид в профиль: 23 – доставляемые блоки ископаемого; 40 – рештаки; 41 – грузонесущие пластины; 42 – тяговые цепи; 43 – ролики; 44 – опорные швелера.
Фиг.8 – расположение и перемещение пластин в рабочей и холостой ветвях эскалаторов; по А-А на чертеже фиг.7: 40 – рештак; 41 – грузонесущие пластины; 46 – днище рештака; 47 – ось.
Фиг.9 – конструкция и расположение роликов в грузовой и холостой ветвях эскалатора; разрез по Б-Б на чертеже фиг.7: 40 – рештак; 43 – ролики; 46 – днище рештака; 47 – ось.
Фиг.10 – транспортировка блоков ископаемого спаренными эскалаторами по транспортным горным выработкам; вид в профиль и в плане: 23 – блок ископаемого; 40 – рештак; 41 – грузонесущие пластины; 42 – тяговые цепи; 43 – ролики; 44 – опорные швелера; 45 – оградительные борта; 46 – днище рештака; 47 – ось.
Оборудование очистного забоя включает:
– механизированную гидравлическую крепь серийного изготовления;
– струговую установку серийного изготовления;
– два доставочных эскалатора, переоборудуемых из скребковых конвейеров серийного производства, путем замены скребков на грузонесущие пластины, перемещающиеся на роликах по днищу рештаков с помощью тяговых цепей;
– гидрорезную очистную машину, создаваемую на базе апробированной ранее гидрорезной машины, изготовленной предприятием НПП Уголь под руководством профессора Каримана С.А. Таким образом, для создания данного очистного комплекса нет препятствий, которые в настоящее время оказываются непреодолимыми для комплекса, принятого за прототип в данном изобретении.
Технология добычи полезных ископаемых, рассматриваемая в данном изобретении, – комплексно-механизированная, широкозахватная и цикличная. Технологический цикл добычи полезного ископаемого состоит из двух этапов: струговой подрубки пласта снизу и затем вырезании из него блоков ископаемого гидрорезной очистной машиной при остановленном струге.
Струговая подрубка пласта
Струговая подрубка пласта производится с целью заглубления ставов обоих эскалаторов под вынимаемый за цикл массив ископаемого. Глубина заглубления равна ширине двух эскалаторов. Это позволяет максимально упростить погрузку вырезаемых блоков ископаемого на доставочные эскалаторы. Выемка ископаемого из полости в нижней части пласта производится работой струга, перемещающегося вдоль создаваемой полости с помощью тяговой цепи струги, расположенного с забойной стороны эскалатора. Цепь протягивается вдоль забоя и при ее перемещении струг снимает стружку ископаемого. Постоянное прижатие струга к забою осуществляется гидроцилиндрами передвижки секций крепи. Погрузка на эскалатор добываемого при этом ископаемого производится самим стругом в процессе передвижки эскалаторов. На эскалаторе погруженное ископаемое в россыпи попадает на грузонесущие пластины, которые, перемещаясь на роликах тяговой цепью, доставляют россыпное ископаемое на транспортную выработку.
Вырезание блоков ископаемого
Вырезание блоков ископаемого производится после полного заглубления обоих эскалаторов в подрубленную призабойную полость. Вырезание блоков включает операции: прорезание поперечных щелей снизу вверх на всю мощность пласта и после заглубления в прорезанные щели гидрорежущих узлов производится обратное движение сверху вниз, прорезание продольной щели, параллельной плоскости пласта, прорезание задней вертикальной щели, доставка эскалаторами блоков ископаемого к транспортной выработке.
Вырезание блоков начинается с прорезания поперечных щелей, которое всегда производится при остановленной гидрорезной машине (см. фиг.1 и 2). Одновременно прорезается несколько поперечных щелей. На фиг.2 показано одновременное прорезание 4-х поперечных щелей. Расстояние между прорезаемыми поперечными щелями равно размеру блока по длине лавы. Этот размер не может превосходить ширину двух транспортных эскалаторов, устанавливаемых на транспортной выработке добычного участка. Поскольку ширина рештаков эскалаторов, которые оборудуются из скребковых конвейеров равна 0,7 м, то размер блоков по длине лавы равен 1,4 м. Тогда размер участка по длине лавы, на котором производится одновременное прорезание поперечных щелей, равен 1,4 м×4=5,6 м. Поскольку доставка блоков по лаве производится также двумя спаренными ставами эскалаторов, то размер блоков ископаемого по направлению подвигания лавы также равен 0,7 м×2=1,4 м. Высота добываемых блоков ископаемого зависит от мощности пласта. По условию устойчивости блока при его доставке по лаве высота блока не может превышать удвоенный его размер в поперечном сечении, т.е. 2,8 м. Поэтому при мощности пласта до 3,2 м с учетом величины подрывки пласта по высоте на 0,4 м разработка пласта ископаемого принимается в один слой и высота блоков принимается равной мощности пласта, уменьшенной на 0,4 м. При мощности пласта свыше 3,2 м разработка пласта принимается в два слоя одинаковой высоты. Так, при мощности пласта 6 м мощность разрабатываемых слоев и, следовательно, высота блоков ископаемого будет равна 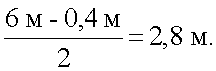
Прорезание поперечных щелей производится сразу на всю мощность пласта. Поскольку глубина эффективного прорезания поперечных щелей за один проход не может обеспечить необходимой глубины 1,4 м, то прорезание поперечных щелей производится в два этапа: сначала движением гидрорежущих узлов снизу вверх производится прорезание на глубину не менее 0,7 м, затем на высоте прорезания, равной мощности пласта, происходит реверсирование движения, при этом гидрорежущие узлы исполнительного инструмента поперечного резания вводятся на всю глубину прорезанных щелей 0,7 м и производится при обратном движении сверху вниз углубление щелей еще на 0,7 м.
На фиг.1 представлен момент окончания прорезания поперечной щели на одном из участков. Гидрорежущий узел, состоящий из гидроабразивной режущей головки 4, металлической трубки 5 подачи воды СВД и трубки подачи абразива 6, заглублен в ранее частично прорезанную щель и движется сверху вниз. Об этом свидетельствует положение треугольника, который образует факел гидроабразивной струи при резании материала в щели: тупой угол треугольника обращен вниз – в направлении движения. На чертеже показано заглубленное положение струга 9 и двух доставочных эскалаторов 10 в полости под разрезаемым поперечными щелями призабойном массиве ископаемого. Ко второму эскалатору со стороны выработанного пространства пристыкована навесная площадка, по которой на роликах перемещается передвижная рабочая площадка с расположенными на ней гидроусилителем и исполнительными инструментами. На фиг.1 показано положение на рабочей площадке направляющих по вертикали 15 перемещения исполнительного инструмента поперечного гидрорезания. При этом панель 13, на которой непосредственно расположен инструмент поперечного гидрорезания, по направляющим 14 может перемещаться также в горизонтальном направлении.
На фиг.1 показано также, что для обеспечения подачи воды СВД к инструменту поперечной резки из гидроусилителя 8 в связи с перемещением инструмента по вертикали и горизонтали эта подача осуществляется по гибкому рукаву 7. Аналогично по гибкому шлангу производится подача к инструменту и абразива из расходного бункера. На фиг.1 справа показано положение желоба для размещения траковой цепи кабелеукладчика, в которой располагаются коммуникации для обеспечения работы гидроусилителя: магистраль подачи воды, эмульсионные напорная и сливная магистрали и электрокабель. Передвижение рабочей площадки гидроусилителя производится вращением приводной звездочки 12 при ее зацеплении с траковой цепью.
На фиг.2 полностью представлено устройство гидрорежущего исполнительного инструмента поперечного гидрорезания. Как видно из чертежа, инструмент включает:
– четыре узла гидроабразивного резания поперечных щелей, каждый состоящий из гидроабразивной режущей головки 4, трубки подвода воды СВД 5, трубки засасывания абразива 6;
– магистраль подачи воды СВД 16;
– магистраль засасывания абразива 17;
– гибкий рукав 7 подачи воды СВД от переключателя 19 к магистрали 16;
– гибкий шланг для засасывания абразива от клапана 20 забора абразива из расходного бункера к магистральному шлангу;
– панель расположения инструмента поперечного резания 13;
– механизированные подъемники 18 (левый и правый) для перемещения по вертикали инструмента поперечной резки;
– направляющие 14 перемещения панели по горизонтали (см. фиг.1);
– направляющие 15 перемещения панели по вертикали (см. фиг.1).
Прорезание поперечных щелей производится инструментом поперечного гидрорезания (см. фиг.1 и 2) движением гидрорежущих головок 4 снизу вверх по всей разрабатываемой мощности пласта, а затем сверху вниз на то же расстояние. После включения подачи воды сверхвысокого давления (СВД) на гидрорежущие головки оператором гидроусилителя оператор – гидрорезчик поперечной резки включает электропривод подъемников 18 (см. фиг.2), который обеспечивает подъем панели 13 (см. фиг.2). Поднимаясь вверх с помощью подъемной цепи механизированного перемещения по вертикали по направляющим с приводной и обводной звездочек, панель поднимает вверх гидрорежущие узлы поперечной резки. Последние, создавая гидроабразивные струи 1 (см. фиг.1), прорезают поперечные щели 2 (см. фиг.2) в призабойном массиве. После поднятия панели на максимальную высоту мощности пласта происходит реверсирование работы привода, заглубление гидрорежущих головок вглубь массива в прорезанные щели на всю глубину путем перемещения панели 13 по горизонтальным направляющим, затем панель опускается вниз на то же расстояние. При этом за счет работы гидроабразивных струй производится углубление поперечных щелей до необходимой глубины. Таким образом, прорезание поперечных щелей производится в два этапа: сначала снизу вверх с прорезанием щелей на половину глубины, а затем сверху вниз с углублением щелей на вторую половину глубины. В процессе гидрорезания к каждому из четырех режущих узлов подводится водяной поток поды СВД с расходом до 10 л/мин и подводится абразив с расходом до 1 кг/мин.
Водяные струи на выходе из форсунок внутри режущих головок имеют скорость до 1,8-2 км/с. Проходя через камеру смешения в режущей головке с такой скоростью, они создают в трубке подвода абразива мощную эжекционную силу, которая засасывает абразив в камеру смешения. Поступающий абразив приобретает в камере смещения от водяных струй скорость до 800 м/с. Полученная водоабразивная смесь извергается сквозь насадки из карбида вольфрама, установленные в соплах режущих головок, на угольный массив, создавая в нем с большой скоростью глубокие щели.
На фиг.3 представлены способ вырезания блоков ископаемого из 2-го слоя призабойного массива, а также работа гидрорежущего узла наружной резки при прорезании продольной щели 2-го слоя. Вырезание блоков ископаемого в два слоя применяется при разработке пологих пластов мощностью свыше 3-х метров, чтобы не вырезать блоки чрезмерно большой высоты в связи с неудобством их транспортировки. При 2-х слойной выемке 1-й слой вынимается при прямом ходе гидрорезной очистной машины от транспортной выработки вверх, а 2-й слой блоков снимается при обратном ходе гидрорезной машины сверху вниз.
Поскольку поперечные щели прорезаются при 2-х слойной выемке сразу на всю мощность пласта же при прямом ходе, то при обратном ходе производятся прорезание только продольной щели на границе пласта с кровлей и прорезание задней вертикальной щели в верхней части пласта. В связи с этим вырезание блоков 2-го слоя производится при непрерывном перемещении гидрорезной машины вдоль лавы при ее обратном ходе к транспортной выработке.
На фиг.3 представлено положение гидрорежущего узла наружной резки инструмента продольного гидрорезания, которое фиксирует направляющими 15 вертикального перемещения положение продольной щели 21 второго слоя. Прорезание данной щели по всей длине лавы необходимо для отделения ископаемого от породы кровли пласта. На фиг.3 представлены положение задней вертикальной щели 22 верхнего слоя, положение гидрорежущих головок 4 узла наружной резки продольной щели и положение его трубок подачи воды СВД 5 и абразива 6 при прорезании продольной щели верхнего слоя, положение самого вырезаемого блока 23 ископаемого и положение передвижного ската 24 для спуска вырезаемых блоков 2-го слоя на эскалаторы.
Прорезание продольной и задней вертикальных щелей производится одновременно и одним исполнительным инструментом, который тем не менее для разных щелей имеет соответствующие гидрорежущие узлы. При вырезании блоков нижнего слоя или при разработке пласта в один слой прорезание продольной и задней щелей производится также участками одинаковой длины и равной длине участков поперечного гидрорезания. Если прорезание поперечных щелей производится при неподвижном положении гидрорезной очистной машины, то прорезание продольной и задней вертикальных щелей производится только при ее непрерывном и равномерном перемещении. Аналогично, если при прорезании поперечных щелей вся вода сверхвысокого давления, вырабатываемая в гидроусилителе, передается только на исполнительный инструмент поперечного гидрорезания, то при прорезании продольной и задней щелей вся вода СВД передается только на инструмент продольного и заднего щелевого гидрорезания.
На фиг.4 представлен исполнительный инструмент продольного и заднего щелевого гидрорезания, а также устройство гидрорежущих узлов прорезания продольной щели. Прорезание продольной и задней щелей при прямом ходе гидрорезной очистной машины начинается в начале каждого цикла с завода исполнительного инструмента из пространства транспортной выработки к прорезаемому массиву ископаемого. Поэтому прорезание щелей начинается одновременной работой всех режущих узлов. Прорезание продольной щели обеспечивается работой двух гидрорежущих узлов: наружной резки 28, когда гидрорежущая головка инструмента находится снаружи продольной щели, и гидрорежущего узла продольной внутренней резки 30, когда гидрорежущая головка находится внутри продольной щели в той ее части, которая только что была прорезана гидрорежущим узлом наружной резки.
При вводе исполнительного инструмента продольного и заднего резания в работу из пространства расположения транспортной выработки сначала начинается прорезание продольной щели вначале режущим узлом наружного резания, а затем узлом внутреннего резания. При этом трубки подачи воды СВД и абразива узла внутренней резки перемещаются по прорезанной узлом наружного резания первой половине продольной щели. Далее в работу вступает гидроабразивная струя узла внутренней резки продольной щели, которая и прорезает вторую половину продольной щели. Вся прорезанная продольная щель используется в дальнейшем для перемещении по ней трубок подачи воды СВД и абразива к гидрорежущим узлам заднего щелевого резания. На фиг.4 представлены также положение магистралей подачи воды СВД 32 и абразива 33 к режущим узлам инструмента, площадка 34 размещения инструмента продольного и заднего щелевого резания.
На фиг.4 и 5 представлено расположение гидрорежущих узлов прорезания задней вертикальной щели. Как видно на фиг.5 для прорезания задней щели используются три режущих узла: один наружной резки, поскольку его режущая головка находится за пределами задней щели, и два узла внутренней резки. Как видно из чертежа, факелы гидроструй всех трех гидрорежущих узлов образуют единую линию резания массива ископаемого. Количество гидрорежущих узлов прорезания вертикальной щели может быть разное в зависимости от мощности разрабатываемого пласта и количества слоев, а также в зависимости от крепости массива.
Поскольку гидрорежущие узлы продольного резания всегда должны опережать прорезание задней вертикальной щели, то при обратном ходе движения гидрорезной очистной машины при вырезании блоков верхнего слоя, положение площадки 34 необходимо разворачивать на противоположное. Чтобы в этом не возникала потребность, т.к. это технически весьма сложно, целесообразно применение исполнительного инструмента продольного и заднего щелевого резания с симметричным расположением гидрорежущих узлов и вырезание блоков в два слоя: при прямом ходе машины работает левое расположение узлов, а при обратном ходе работает правое.
На фиг.6 представлен фронтальный вид расположения оборудования при вырезании блоков ископаемого из 2-го слоя при обратном ходе гидрорезной очистной машины. Показан спуск вырезанного блока ископаемого 23 верхнего слоя по передвижному скату 24 на спаренные эскалаторы. При работе гидрорезной очистной машины по вырезанию блоков верхнего слоя находятся в работе гидроусилитель 8 и исполнительный инструмент продольного и заднего щелевого резания 35, установленный на площадке 34, занимающей самое верхнее положение, фиксированное направляющими по вертикали 37, инструмент поперечного гидрорезания 36 отключен и его положение фиксировано направляющими по вертикали 15. Оба исполнительных инструмента и гидроусилитель 8 расположены на передвижной рабочей площадке 38, которая перемещается на катках по рабочей поверхности навесной площадки 39.
Перемещение рабочей площадки расположения гидрорезной машины обеспечивается работой приводной звездочки 12 (см. фиг.1) по траковой цепи 11, которая укладывается в желоб, также расположенный на краю навесной площадки.
При спуске блоков верхнего слоя по скату последний опирается своими катками на пластины эскалаторов и стационарно закрепляется с площадкой гидрорезной очистной машины, так что при ее перемещении скат передвигается параллельно по ставу доставочных эскалаторов и спускает блоки ископаемого, которые быстро уходят вперед, т.к. скорость движения грузонесущих пластин значительно превышает скорость движения гидрорезной очистной машины.
На фиг.7 показано положение блока ископаемого на доставочном средстве лавы – двух спаренных ставах эскалаторов. Эскалатор оборудуется на базе существующих серийных скребковых конвейеров, например СПЦ 271 путем замены скребков на грузонесущие пластины 41 (см. фиг.7), перемещающиеся на роликах 43 по днищу рештаков 40 с помощью тяговых цепей 42. Из новых деталей используются только грузонесущие пластины, ролики, оси и опорные швелера. Все остальное, из чего состоят скребковые конвейеры используется без изменений. Благодаря произведенным заменам трение-скольжение груза о сталь днища рештака заменяется на трение-качение ролика по днищу.
Расчеты показывают, что при переоборудовании скребкового конвейера СПЦ 271 длиной 200 м в соответствующий эскалатор производительность возрастает с 12 т/мин до 203 т/мин, т.е в 17 раз. Ниже приводятся для доказательства расчеты.
Грузонесущие пластины устанавливаются на оси, которые при движении под грузом опираются на 6 роликов, катящихся по днищу рештаков. Грузонесущая пластина (см. фиг.10) имеет рабочую контактную с грузом площадку размером 70 см по ширине става и 11 см по его длине, а также семь проушин, которыми пластина опирается на ось. Наружный диаметр проушины 40 мм, внутренний – 30 мм.
Размеры оси: длина 700 мм, диаметр 20 мм. Размеры роликов: наружный диаметр 100 мм, внутренний – 30 мм. Ширина 15 мм.
1. Определение веса движущихся частей эскалатора
а) Ролики. Количество – 6. Диаметр: наружный – 100 мм; внутренний – 30 мм.
Объем тела ролика 
Вес одного ролика 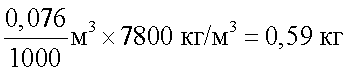
Общий вес роликов 0,59 кг×6=3,5 кг
б) Ось. Диаметр 20 мм. Объем оси R2l=3,14×12см70см=220 см3=0,22 дм3
Вес оси 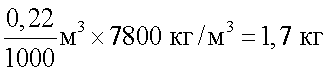
в) Пластина. Толщина пластины 10 мм. Размеры 70 см×11 см
Объем пластины 70 см×11 см×1 см=770 см3
Определим объем семи проушин пластины

Общий объем пластины 770 см3+154 см3=924 см3=0,92 дм3
Вес пластины 
г) Тяговые цепи. Вес 1 п.м. цепей 12 кг/м. На длину 0,11 м вес цепей равен
12 кг/м×0,11 м=1,32 кг
Общий вес движущихся частей на длину 11 см равен
3,5 кг+1,7 кг+7,2 кг+1,32 кг=13,7 кг
Удельный вес движущихся частей на 1 п.м. длины
13,7 кг:0,11 м=124 кг/м
Вес движущихся частей одной ветви эскалатора равен
124 кг×200 м=24800 кг=24,8 т
2. Определение производительности системы двух спаренных эскалаторов.
а) Вес движущихся частей холостых ветвей двух эскалаторов
24,8 т×2=49,6 т
б) сила сопротивления движению двух холостых ветвей обоих эскалаторов за счет трения скольжения стальных осей о стальные направляющие рештаков
0,17×49,6=8,4 т,
где 0,17 – коэффициент трения скольжения стали о сталь;
в) сила сопротивления трения качения двух грузовых ветвей обоих эскалаторов 
где 0,05 см – коэффициент трения качения стального колеса о сталь,
5 см – радиус роликов;
Ру – вес угольных блоков на ставе обоих эскалаторов, кг;
г) общая сила сопротивления движению груза равна
8400 кг+0,01Ру+496 кг=8900 кг+0,01 Ру
д) время на перемещение груза на ставе 2-х эскалаторов на 1 п.м. длины равно 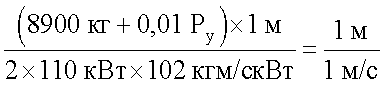
110 кВт – мощность привода одного эскалатора;
2 – количество спаренных эскалаторов;
102 кгм/с кВт – соотношение пересчета киловатт в кгм/с;
1 м/с – скорость движения тяговых цепей эскалаторов СПЦ 271.
После вычислений Ру=1350 т
Таким образом, система 2-х спаренных эскалаторов способна перемещать по длине лавы со скоростью 1 м/с груз угольных блоков весом 1350 т
Следовательно, минутная производительность средств доставки составляет 
Поскольку в доставке участвуют два эскалатора, то производительность одного будет в два раза меньше 405_2=202,5 т/мин, что в 17 раз выше исходной 12 т/мин производительности скребкового конвейера СПЦ 271, из которого он переоборудован. На фиг.8 представлен разрез по А-А фиг.7. Это конструкции грузонесущих пластин эскалатора. Поскольку при подрывке пласта стругом эскалаторами доставляется также ископаемое в россыпи, то необходимо, чтобы россыпь не попадала в пространство под пластинами, чтобы не происходила заштыбовка рештаков, что препятствует движению роликов. Поэтому пластины должны максимально плотно прилегать друг к другу и выступать над бортами рештаков. Как видно из чертежа, пластины одним своим концом – проушиной – опираются на ось, другим концом – на проушину соседней пластины.
На фиг.9 представлен разрез по Б-Б фиг.7. Это конструкция и расположение роликов эскалатора. Как видно из чертежа, в грузовой (верхней) ветви ролики катятся по днищу рештаков и сами являются опорой для осей, проходящих через их середину. В холостой нижней ветви сами оси являются опорами для роликов, на которых они находятся в подвешенном состоянии при перемещении.
На фиг.10 представлена система двух спаренных эскалаторов для транспортировки блоков ископаемого по участковой транспортной выработке. Как видно из чертежа, отличие состоит лишь в сооружении бортов с каждой стороны транспортной линии для недопущения осыпания россыпного ископаемого, образующегося от разрушения блоков при их транспортировке.
Определение максимальной загрузки эскалаторных ставов добываемыми блоками ископаемого
Минимальное время вырезания из массива блоков ископаемого возникает при выемке блоков 2-го слоя при разработке пласта мощностью до 6 м. В этом случае не происходит остановок очистной гидрорезной машины, а скорость прорезания продольных и задней щелей максимальна и может достигать 0,25 м/с. Тогда время вырезания одного блока равна
1,4 м:0,25 м/с=5,6 с.
С учетом спуска блока по скату принимаем это время равным 6 с.
С учетом веса блока 7,7 т и его длины на ставе 1,4 м загрузка эскалаторного става ископаемым равна 7,7 т:(1,4 м+6 с х 1 м/с)=1,05 т/м
С учетом движущихся частей спаренных эскалаторов общий вес движущегося груза на 1 п.м равен 1050 кг/м +240 кг/м=1300 кг/м
Определение допустимой длины транспортировки блоков ископаемого одним спаренным ставом
Сила сопротивления движению за счет тpeния-скольжения двух холостых ветвей спаренных эскалаторов равна
0,17 х 248 кг/м х l=42,5 кг/мl, где l – длина става.
Сила сопротивления движению за счет трения-качения двух груженых ветвей эскалаторов 0,05 см 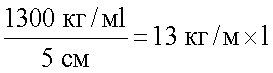
Общая сила сопротивления движению равна
l(42,5 кг/м+13 кг/м)=55,5 кг/мl
Время на перемещение груза на расстояние 1 м определяется отношением величины работы на мощность приводов и одновременно отношением длины перемещения на скорость тяговых цепей

Из данного равенства выявляется возможная длина спаренного эскалаторного става из условия мощности приводов
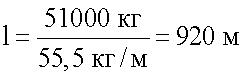
Сила натяжения всех 4-х тяговых цепей двух спаренных эскалаторов равна
55,5 кг/м×920 м=51 т.
Натяжение одной тяговой цепи составит 51 т:4=13,7 т
Учитывая, что разрывное усилие тяговых цепей СПЦ 271 равно не менее 40 т, определяем, что коэффициент запаса прочности тяговых цепей будет равен
40 т:13,7 т=2,9.
Определение производительности очистного работающего по технологии профессора Каримана с выемкой ископаемого блоками и транспортировкой эскалаторами
а) мощность пласта 6 м
1. Продолжительность подрубки пласта стругом
Время снятия одной стружки 200 м:1,89 м/с=105 с
Необходимое количество стружек 1,43 м:0,1 м=14 стружек
1,89 м/с – скорость движения струга
0,1 м – толщина стружки
Время подрубки пласта 105 с×14=1460 с=24 мин
2. Продолжительность прорезания продольной и задней щелей в первом слое
200 м:0,15 м/с=1330 с=22 мин,
где 0,15 м – скорость прорезания отжатого угольного массива в нижней части пласта.
3. Продолжительность прорезания поперечных щелей в массиве ископаемого на высоту 5,6 м от става (1-й и 2-й слой)
продолжительность одной поперечной резки
2×5,6 м:0,25 м/с=44,8 с
количество поперечных резок на цикл 200 м:5,6 м=36
продолжительность поперечных резок на цикл
44,8 с×36=1660 с=27 мин
4. Продолжительность прорезания продольной и задней щелей верхнего слоя
200 м:0,25 м/с=800 с=13 мин
5. Продолжительность цикла выемки угля
24 мин + 27 мин + 22 мин + 13 мин=86 мин=90 мин
6. Количество добычных циклов за смену 360 мин:90 мин=4 цикла
7. Запасы добычи в одном цикле
200 м×1,43 м×6м×1, 4 т/м3=2400 т
8. Добыча за смену 2400 т×4 цикла=9600 т
9. Добыча за сутки 9600 т×3 смены=28600 т/сут
б) мощность пласта 3,2 м
1. Продолжительность подрубки пласта аналогично равна 24 мин
2. Продолжительность прорезания поперечных щелей
37 с×36=22 мин
Продолжительность одной резки 2×2,8 м:0,15 м/с=37 с
Количество поперечных резок 200 м:5,6 м=36
3. Продолжительность прорезания продольной и задней щелей
200 м:0,15 м/с=22 мин
Холостой перегон гидрорезной машины совмещается с работой струга.
4. Продолжительность цикла 24 мин + 22 мин + 22 мин=68 мин
5. Количество добычных циклов за три добычные смены
1080 мин:68 мин=16 циклов
6. Добыча с одного цикла равна 200 м×1,43 м×3,2 м×1,4 т/м3=1290 т
7. Добыча очистного забоя за сутки равна 1290 т×16 циклов=20640 т/сут
Использованная литература
1. Комплексная механизация и автоматизация очистных работ в угольных шахтах. Под общей редакцией Б.Ф.Братченко. М.: Недра, 1977, 415 с.
Формула изобретения
1. Очистной механизированный комплекс для добычи залегающего пологими пластами ископаемого, его разработки крупными блоками и доставки этих блоков эскалаторами, включающий секции механизированной крепи, гидрорезную очистную машину с катками, обеспечивающими ее передвижение, для вырезания ископаемого из призабойного массива крупными блоками с возможностью прорезания поперечных щелей при неподвижной гидрорезной машине и прорезания задней вертикальной щели посредством непрерывного перемещения гидрорезной машины с исполнительными органами и гидрорежущими головками, соединенными через металлические трубки, на которых они жестко закреплены, с водоподводящей магистралью, идущей от мультипликаторов, придающих воде сверхвысокое давление, гидроусилитель, установленный с возможностью его непрерывного питания водой и эмульсией посредством постоянно подключенных рукавов гидрорезной машины к водоподводящей и эмульсионной магистралям, укладчик магистралей для обеспечения возможности переукладки упомянутых магистралей при движении гидрорезной машины и смене направления ее перемещения при холостом перегоне, отличающийся тем, что гидрорезная машина выполнена с возможностью прорезания продольных щелей, параллельных плоскости пласта, одновременно с прорезанием задней вертикальной щели с использованием специальных гидрорежущих узлов, гидроусилитель выполнен с возможностью подачи воды сверхвысокого давления на исполнительные органы, обеспечивающие прорезание задней вертикальной и продольной щелей при перемещении гидрорезной машины, а при неподвижной гидрорезной машине – с возможностью подачи всей воды на исполнительные органы, обеспечивающие поперечное гидрорезание, причем длины всех участков по длине лавы непрерывного прорезания поперечных щелей с одной стороны и задней вертикальной и продольной щелей с другой стороны одинаковы, при этом комплекс снабжен пристыкованной с завальной стороны второго эскалатора навесной площадкой для перемещения по ней по длине лавы гидрорезной машины посредством электропривода, соединенного с приводной звездочкой, входящей в зацепление с траковой цепью, располагающейся в желобе, проложенном также на навесной площадке, а в корпусе траковой цепи располагаются все коммуникации, обеспечивающие работу гидроусилителя: эмульсионные напорная и сливная магистрали, водная магистраль и электрокабель.
2. Комплекс по п.1, отличающийся тем, что в состав комплекса входит струговая установка, состоящая из струга с расположением струговой цепи с забойной стороны, двух приводов струга, гидрофицированных столов и двух эскалаторов, собираемых на базе серийных скребковых конвейеров, в которых вместо скребков смонтированы грузонесущие пластины, установленные с возможностью перемещения на роликах, катящихся по днищу рештаков.
3. Комплекс по п.1, отличающийся тем, что для доставки блоков ископаемого по лаве и по участковой транспортной выработке комплекс включает систему спаренных эскалаторов, обеспечивающих вместе необходимую приемную способность ставов для размещения на них блоков полезного ископаемого под действием их собственного веса и перемещения блоков, при этом грузонесущие пластины ставов эскалаторов, выполненные с возможностью перемещения на роликах по рештакам, обеспечивают доставку блоков ископаемого к транспортной выработке, а для спуска блоков ископаемого из верхнего слоя комплекс снабжен передвижным скатом, установленным с возможностью передвижения на катках по ставам обоих эскалаторов, будучи стационарно связанным с гидрорезной машиной.
4. Комплекс по п.1, отличающийся тем, что для крепления лавы комплекс включает серийные механизированные крепи, имеющие достаточное бесстоечное пространство с забойной стороны для размещения двух спаренных эскалаторов.
РИСУНКИ
|