|
(21), (22) Заявка: 2008149862/02, 18.12.2008
(24) Дата начала отсчета срока действия патента:
18.12.2008
(46) Опубликовано: 10.08.2010
(56) Список документов, цитированных в отчете о поиске:
JP 07-259005 А, 09.10.1995. RU 2201318 C2, 27.03.2003. RU 2111837 C1, 27.05.1998. RU 2279333 C1, 10.07.2006. RU 2281355 C1, 10.08.2006.
Адрес для переписки:
107174, Москва, ул. Новая Басманная, 2, ОАО “РЖД”, Директору по вопросам управления интеллектуальной собственностью Р.Ю. Тимофееву
|
(72) Автор(ы):
Бидуля Александр Леонидович (RU), Краснов Олег Геннадьевич (RU), Кириков Александр Константинович (RU), Астанин Николай Николаевич (RU), Ушанов Андрей Викторович (RU), Сорока Валентин Сергеевич (RU), Кузнецов Сергей Петрович (RU)
(73) Патентообладатель(и):
Открытое акционерное общество “Российские железные дороги” (RU)
|
(54) УСТРОЙСТВО ДЛЯ ФРЕЗЕРОВАНИЯ ПРОФИЛЯ РЕЛЬСА
(57) Реферат:
Устройство содержит основание, роликовые опоры рельса, датчик для фиксации наплавки в сварных рельсовых стыках, профилирующие фрезы, оснащенные пластинами из твердого сплава с приводами вращения, закрепленные на фрезерных головках, каретку для установки фрезерных головок с возможностью перемещения вдоль оси рельса приводом по направляющим основания и установкой фрезерных головок в поперечной плоскости относительно продольной оси рельса. Для повышения эффективности и надежности при обработке полного профиля рельса оно оснащено для обработки поверхностей головки рельса – одной фрезерной головкой с горизонтальным расположением оси профилирующей фрезы, для обработки наклонных поверхностей основания головки и подошвы рельса, поверхностей шейки рельса и радиусных поверхностей подошвы рельса – двумя фрезерными головками с вертикальным расположением осей профилирующих фрез, для обработки нижней поверхности подошвы рельса одной фрезерной головкой с горизонтальным расположением оси цилиндрической фрезы. При этом фрезерные головки установлены в одной общей каретке с возможностью ее перемещения приводом по направляющим основания вдоль оси рельса, причем каждая из фрезерных головок установлена в каретке на цилиндрической направляющей с возможностью перемещения вдоль оси вращения фрез и поворота вокруг этой направляющей при помощи приводов с датчиками измерения величины перемещения. При этом устройство оснащено роликовыми опорами, установленными на каретке для фиксации рельса в процессе механической обработки и проведения измерений продольного и поперечного профиля рельса, датчиками измерения величины перемещения каретки и фрезерных головок и датчиками, сигнализирующими о касании фрезами поверхностей профиля рельса, связанными с датчиком фиксации наличия поверхности наплавки в сварных стыках и с системами автоматического измерения и управления процессом механической обработки. 4 ил.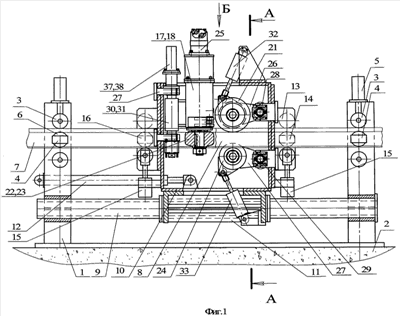
Изобретение относится к оборудованию для устранения локальных неровностей продольного и поперечного профиля рельса, в том числе в зоне сварных рельсовых стыков, методом профильного фрезерования.
Известно устройство для фрезерования профиля рельса, указанное в способе обработки рабочей поверхности головки рельса и станке для его осуществления, на котором производится фрезерование поверхности катания головки рельса и одной или двух радиусных поверхностей, сопряженных с боковыми гранями головки, на рельсофрезерном станке при базировании рельса в вертикальной и горизонтальной плоскостях и его непрерывной подаче, базирование рельса производят по неизнашиваемым наклонным поверхностям основания головки и подошвы рельса с центрированием по вертикальной плоскости симметрии рельса и горизонтальной плоскости симметрии пазух, обрабатывают одной фрезой, одновременно поверхность катания и одну или обе радиусные поверхности, сопряженные с боковыми гранями головки рельса, или последовательно обрабатывают одной фрезой предварительно радиусную поверхность головки рельса со стороны нерабочей грани, а второй фрезой – одновременно поверхность катания и одну или обе радиусные поверхности, сопряженные с боковыми гранями при попутном фрезеровании обеими фрезами, в процессе фрезерования изменяют глубину резания с учетом предварительно устанавливаемых предельных значений изменения срезаемого слоя металла и допустимого угла уклона на обработанной поверхности катания /PU, заявка на изобретение 2001100690/02, кл. В23С 3/00, опубл. 2003 г./.
Недостатками данного изобретения являются:
– указанный способ обработки рабочей поверхности головки рельса и станок для его осуществления не обеспечивает обработку сварного рельсового стыка по всему профилю, что требует применения дополнительного оборудования и снижает эффективность использования указанного способа обработки;
– перемещение в процессе обработки рельса исключает возможность проведения каких-либо других операций, совмещенных по времени с фрезерованием, например выправки сварных стыков, измерений и других операций, предусматриваемых технологическим процессом.
Известно устройство для фрезерования профиля рельса, принятое в качестве прототипа и содержащее два копира, датчики для определения перекоса рельса, роликовые опоры рельса с копирами, датчик для фиксации наличия поверхности наплавки в сварных стыках, профилирующие фрезы, оснащенные пластинами из твердого сплава с приводами вращения, закрепленными на фрезерных головках, установленных в каретках с возможностью перемещения приводом вдоль оси рельса по направляющим оснований и установкой их в поперечной плоскости относительно продольной оси рельса, две из фрезерных головок, расположенных под углом к оси симметрии рельса, предназначены для обработки боковых граней, поверхности катания и радиусных поверхностей, сопряженных с ними, и четыре фрезерные головки с горизонтальным расположением осей вращения фрез предназначены для обработки наклонных поверхностей основания головки и подошвы рельса, а также поверхностей шейки рельса и радиусных поверхностей, сопряженных с ними /JP, патент 2837628, В2 7259005 А, кл. Е01В 31/13, опубл. 1998 г./.
Недостатками указанного изобретения являются:
– большое количество фрез для обработки поверхностей профиля рельса усложняет конструкцию устройства;
– отсутствие возможности обработки нижней поверхности подошвы рельса, радиусных поверхностей основания головки и подошвы рельса требует применения дополнительного оборудования и снижает эффективность использования устройства;
– обработка поверхности катания головки рельса двумя фрезами не обеспечивает необходимое качество поверхности, так как возможны неровности в зоне работы двух фрез, и требует дополнительной обработки поверхности катания головки рельса, что снижает эффективность использования устройства.
Техническим результатом изобретения является повышение эффективности и надежности устройства для фрезерования профиля рельса.
Указанный технический результат достигается тем, что устройство для фрезерования профиля рельса, содержащее основание, роликовые опоры рельса, датчик для фиксации наплавки в сварных рельсовых стыках, профилирующие фрезы, оснащенные пластинами из твердого сплава с приводами вращения, закрепленными на фрезерных головках, каретку для установки фрезерных головок с возможностью перемещения вдоль оси рельса приводом по направляющим основания и установкой фрезерных головок в поперечной плоскости относительно продольной оси рельса, для обработки полного профиля рельса устройство оснащено: для обработки поверхностей головки рельса – одной фрезерной головкой с горизонтальным расположением оси профилирующей фрезы; для обработки наклонных поверхностей основания головки и подошвы рельса, поверхностей шейки рельса и радиусных поверхностей подошвы рельса – двумя фрезерными головками с вертикальным расположением осей профилирующих фрез; для обработки нижней поверхности подошвы рельса устройство дополнительно оснащено одной фрезерной головкой с горизонтальным расположением оси цилиндрической фрезы; фрезерные головки установлены в одной общей каретке с возможностью ее перемещения приводом по направляющим основания вдоль оси рельса, каждая из фрезерных головок установлена в каретке на цилиндрической направляющей с возможностью перемещения вдоль оси вращения фрез и поворота вокруг этой направляющей при помощи приводов с датчиками измерения величины перемещения; кроме того, устройство дополнительно оснащено роликовыми опорами, установленными на каретке для фиксации рельса в процессе механической обработки и проведения измерений продольного и поперечного профиля рельса, датчиками измерения величины перемещения каретки и фрезерных головок, а также датчиками, сигнализирующими касание поверхностей профиля рельса, связанными с датчиком фиксации наличия поверхности наплавки в сварных стыках и с системами автоматического измерения и управления процессом механической обработки.
На фиг.1 изображен общий вид устройства для фрезерования профиля рельса; на фиг.2 – сечение А-А на фиг.1; на фиг.3 – вид Б на фиг 1 и на фиг.4 изображено расположение фрез относительно рельса.
Устройство для фрезерования профиля рельса содержит основание 1 (фиг.1, 2 и 3), закрепленное на фундаменте 2, на основании 1 установлены вертикальные и горизонтальные роликовые опоры 3, 4 с гидроцилиндрами 5, 6.
В роликовых опорах установлен рельс 7 со сварным стыком 8. На цилиндрических направляющих 9 расположена каретка 10. В нижней части каретки 10 находятся направляющие втулки 11, обеспечивающие перемещение каретки вдоль оси рельса 7 посредством гидроцилиндра 12.
На раме каретки 10 установлены вертикальные 13 и горизонтальные 14 роликовые опоры с приводом от гидроцилиндров 15 и 16. Внутри каретки 10 установлены четыре фрезерные головки: две 17, 18 расположены вертикально, две 19, 20 -горизонтально.
На шпинделе каждой фрезерной головки расположены профилирующие фрезы: профилирующая фреза 21 (фиг.1, 2, 3 и 4) для обработки поверхности головки рельса, профилирующие фрезы 22, 23 для обработки шейки рельса нижней части головки и верхней части подошвы рельса, цилиндрическая фреза 24 для обработки нижней поверхности подошвы рельса.
Привод шпинделей осуществляется от высокомоментных гидромоторов 25. Корпус каждой фрезерной головки закреплен посредством кронштейнов 26, 27 на цилиндрических направляющих 28, 29, 30, 31, каждая из четырех фрезерных головок 17, 18, 19, 20 имеет возможность поворота относительно направляющих 28, 29, 30, 31 соответственно посредством приводов, выполненных в виде гидроцилиндров. Кроме того, фрезерные головки 17, 18, 19 имеют возможность перемещаться вдоль цилиндрических направляющих 28, 30, 31 соответствующими гидроцилиндрами 36, 37, 38. Величина перемещения и поворота фрезерных головок контролируется датчиками измерения.
Устройство работает следующим образом: системой перемещения рельс 7 перемещается по роликовым опорам 3 и 4 до установки сварного шва рельсового стыка 8 в средней части основания 1. После установки рельсового стыка 8 в требуемом положении рельс 7 закрепляется роликовыми опорами 13 и 14 в вертикальной и горизонтальной плоскостях посредством гидроцилиндров 15 и 16 и роликовыми опорами и посредством гидроцилиндров 6 закрепляется на основании 1 в осевом направлении. Каретка 10 находится в левом крайнем положении. Далее производится центрирование каретки 10 относительно сварного шва рельсового стыка 8 посредством гидроцилиндра 12. Профилирующая фреза 21 устанавливается в среднее относительно продольной оси рельса 7 положение посредством гидроцилиндра 36. Затем фрезы 21, 24 приводятся во вращение от гидромоторов 25, и начинают перемещения в сторону рельса соответственно сверху фреза 21, снизу фреза 24 посредством гидроцилиндров 32 и 34. При касании режущих пластин рельсов срабатывают датчики касания, которые дают команду на отключение перемещения цилиндров 32 и 34. Координаты точек касания фиксируются в памяти компьютера системы управления устройства. Затем фреза 21 перемещается совместно со шпинделем 19 вдоль направляющей 28 посредством гидроцилиндра 36. При касании фрезы 21 боковой поверхности головки рельса 7 подается команда на прекращение подачи от гидроцилиндра 36. Координата точки касания заносится в память компьютера. После выполнения этой процедуры фрезы 21, 24 отводятся от рельса 7, и каретка 10 перемещается в правое положение по отношению к сварному рельсовому стыку 8 на расстоянии 150 200 мм от него. Затем процедура по определению точек контакта фрез с рельсом повторяется. По координатам точек касания на поверхности катания и на боковой поверхности рельса определяется траектория движения фрез. Верхняя 21 и нижняя 24 фреза позиционируются относительно рельса 7 (фиг.4), привязываясь к траектории движения системой управления устройства. Вращающиеся от гидромоторов 25 фрезы 21, 24 перемещаются вдоль рельса по траекториям, задаваемым системой управления. При этом в зоне сварного рельсового стыка 8 удаляются остатки грата с верхней части поверхности катания и боковой поверхности головки рельса фрезой 21 (зона 1, 2, фиг.4) и с нижней части подошвы рельса – фрезой 24 (зона 10 фиг.4).
Продольное перемещение каретки 10 с вращающимися и с позиционированными фрезами 21, 24 реализуется гидроцилиндром 12. После прохода рельсового стыка 8 на расстоянии 150 200 мм каретка 10 останавливается. Подается команда на перемещение фрезы 24 в поперечном направлении до касания с противоположной боковой поверхностью головки рельса. Точка касания фиксируется в памяти компьютера, система управления определяет траекторию движения.
Фрезы 21, 24, спозиционированные по рельсу 7 (фиг.4), перемещаются в обратном направлении, удаляя остатки грата на головке рельса (зона 1,3, фиг.4) и подошве рельса (зона 10, фиг.4). После прохода расстояния 150 200 мм от сварного шва 8 фрезы 21, 24 отводятся от рельса 7 посредством гидроцилиндров 32, 33. Отключаются гидромоторы 25 привода шпинделей 19, 20. Фрезерная рама перемещается вправо в положение, при котором оси боковых фрез 22, 23 располагаются на расстоянии 150 200 мм от сварного шва 8. Включается подача на вращения боковых фрез 22,23 от гидромоторов 25. Фрезы в вертикальном направлении устанавливаются посредством гидроцилиндров 37, 38 в положение, при котором горизонтальные оси шейки рельса и фрез совпадают. Фрезы 22, 23 начинают подводится к шейке рельса, поворачиваясь относительно вертикальных направляющих 30, 31 посредством гидроцилиндров 34, 35. При касании режущих кромок фрез поверхности шейки рельса в точках 4, 6, фиг.4, подача прекращается, координаты точек касания заносятся в память компьютера. Далее фрезы 22, 23 перемещаются вверх вдоль направляющих 30, 31 посредством гидроцилиндров 37, 38. При касании режущей поверхности фрез 22, 23 с нижней частью головки рельса (зона 5, 7, фиг.4) срабатывает датчик касания, и подача прекращается. Координаты точек касания заносятся в память компьютера. Фрезы 22, 23 отводятся от рельса посредством цилиндров 34, 35, фрезерная головка перемещается вправо до положения, когда вертикальные оси фрез устанавливаются на расстояние 150 200 мм от сварного шва, подача прекращается. Повторяется процедура определения точек касания (зоны 4, 6; 5, 7, фиг.4). По координатам точек касания рассчитывается траектория перемещения фрез. Положение фрез 22, 23 позиционируется относительно рельса 7, подается команда на подачу, и каретка 10 с вращающими фрезами начинает перемещаться вдоль рельса 7 по направляющим 9 посредством гидроцилиндра 12. Фрезы 22, 23, перемещаясь вдоль рельса 7, удаляют остатки грата в зоне сварного шва на нижней части головки рельса (зоны 5, 7, фиг.4) и шейки рельса (зоны 4, 6, фиг.4). После перемещения каретки 10 в положение, когда вертикальные оси боковых фрез 22, 23 находятся на расстоянии 150 200 мм от сварного рельсового стыка 8, продольная подача прекращается. Подается команда на перемещение фрез 22, 23 вниз вдоль направляющих 30, 31 посредством гидроцилиндров 37, 38. При касании режущей поверхности фрез 22, 23 верхней части подошвы рельса (зоны 8, 9, фиг.4) подача прекращается. Координаты точек касания заносятся в память компьютера, система управления формирует траекторию движения фрез. Подается команда на продольное перемещение фрез 22, 23 в обратном направлении. Вращающиеся фрезы 22, 23, перемещаясь вдоль рельса 7 с фрезерной головкой по направляющим 9 посредством гидроцилиндра 12, удаляют остатки грата в зоне сварного рельсового стыка 8 на верхней части подошвы рельса (зоны 8, 9, фиг.4) и шейке рельса (зона 4, 6, фиг.4). После перемещения каретки 10 в положение, когда вертикальные оси боковых фрез 22, 23 будут находится на расстоянии 150 200 мм от сварного рельсового стыка 8, продольная подача прекращается, отключаются гидромоторы 25 вращения фрез, фрезы 22, 23 отводятся от рельса 7 посредствам гидроцилиндров 34, 35. Процесс фрезерования закончен. Далее подается команда на отвод рельсовых опор 13, 14 от рельса 7 посредствам гидроцилиндров 15, 16. Затем разжимаются рельсозахваты 3, 4 посредством гидроцилиндров 5, 6. Рельс освобождается и перемещается специальным рольгангом на пост следующей технологической операции, а в зону фрезерной головки подается следующий сварной рельсовый стык. Процесс обработки повторяется.
Формула изобретения
Устройство для фрезерования профиля рельса, содержащее основание, роликовые опоры рельса, датчик для фиксации наплавки в сварных рельсовых стыках, профилирующие фрезы, оснащенные пластинами из твердого сплава с приводами вращения, закрепленные на фрезерных головках, каретку для установки фрезерных головок с возможностью перемещения вдоль оси рельса приводом по направляющим основания и установки фрезерных головок в поперечной плоскости относительно продольной оси рельса, отличающееся тем, что для обработки полного профиля рельса устройство оснащено для обработки поверхностей головки рельса одной фрезерной головкой с горизонтальным расположением оси профилирующей фрезы, для обработки наклонных поверхностей основания головки и подошвы рельса, поверхностей шейки рельса и радиусных поверхностей подошвы рельса – двумя фрезерными головками с вертикальным расположением осей профилирующих фрез, для обработки нижней поверхности подошвы рельса – одной фрезерной головкой с горизонтальным расположением оси цилиндрической фрезы, при этом фрезерные головки установлены в одной общей каретке с возможностью ее перемещения приводом по направляющим основания вдоль оси рельса, причем каждая из фрезерных головок установлена в каретке на цилиндрической направляющей с возможностью перемещения вдоль оси вращения фрез и поворота вокруг этой направляющей при помощи приводов с датчиками измерения величины перемещения, при этом устройство оснащено роликовыми опорами, установленными на каретке для фиксации рельса в процессе механической обработки и проведения измерений продольного и поперечного профилей рельса, датчиками измерения величины перемещения каретки и фрезерных головок и датчиками, сигнализирующими о касании фрезами поверхностей профиля рельса, связанными с датчиком фиксации наличия поверхности наплавки в сварных стыках и с системами автоматического измерения и управления процессом механической обработки.
РИСУНКИ
|
|