|
(21), (22) Заявка: 2008138714/04, 30.03.2007
(24) Дата начала отсчета срока действия патента:
30.03.2007
(30) Конвенционный приоритет:
31.03.2006 JP 2006-098730
(46) Опубликовано: 20.06.2010
(56) Список документов, цитированных в отчете о поиске:
WO 2005102523 A1, 03.11.2005. GB 1156398 A, 25.06.1969. US 4921829 A, 01.05.1990. EP 1457249 A1, 15.09.2004. EP 0525677 A1, 03.02.1993. WO 2006009327 A1, 26.01.2006. RU 2026738 С1, 20.01.1995. RU 2146174 C1, 10.03.2000. SU 1834706 A3, 15.08.1993.
(85) Дата перевода заявки PCT на национальную фазу:
29.09.2008
(86) Заявка PCT:
IB 2007/000980 20070330
(87) Публикация PCT:
WO 2007/113674 20071011
Адрес для переписки:
129090, Москва, ул.Б.Спасская, 25, стр.3, ООО “Юридическая фирма Городисский и Партнеры”, пат.пов. Е.Е. Назиной
|
(72) Автор(ы):
МИУРА Масахиде (JP), ТАКАГИ Нобуюки (JP), МАТСУМОТО Синити (JP), ТАНАБЕ Тоситака (JP), НАГАИ Ясутака (JP), ДОХМАЕ Казухико (JP), ИКЕДА Ясуо (JP)
(73) Патентообладатель(и):
ТОЙОТА ДЗИДОСЯ КАБУСИКИ КАЙСЯ (JP)
|
(54) ЧАСТИЦА МЕТАЛЛОКСИДНОГО НОСИТЕЛЯ КАТАЛИЗАТОРА И КАТАЛИЗАТОР ОЧИСТКИ ОТХОДЯЩЕГО ГАЗА
(57) Реферат:
Настоящее изобретение относится к частицам металлоксидного носителя катализатора, к способу получения таких частиц, к катализатору очистки отходящего газа, выполненному из частиц металлоксидного катализатора, и к способу регенерации катализатора очистки отходящего газа. Описана частица металлоксидного носителя катализатора, которая имеет центральную часть и наружную оболочечную часть, в которой центральная часть и наружная оболочечная часть каждая содержит первый оксид металла и второй оксид металла, центральная часть и наружная оболочечная часть отличаются по составу друг от друга, мольная фракция металла первого оксида металла является более высокой в центральной части, чем в наружной оболочечной части, мольная фракция металла второго оксида металла является более высокой в наружной оболочечной части, чем в центральной части, и первый оксид металла представляет оксид алюминия или оксид циркония, а второй оксид металла выбран из группы, состоящей из оксидов неодима, празеодима, лантана, скандия и иттрия. Описан катализатор очистки отходящего газа, содержащий вышеописанную частицу металлоксидного носителя катализатора и платину, нанесенную на частицу металлоксидного носителя катализатора. Описан способ регенерации катализатора очистки отходящего газа, включающий нагревание катализатора очистки отходящего газа при температуре 500°С или выше в окислительной атмосфере, которая содержит кислород. Также описан способ получения частицы металлоксидного носителя катализатора, содержащей центральную часть и наружную оболочечную часть, где каждая содержит первый оксид металла и второй оксид металла, и центральная часть и наружная оболочечная часть отличаются по составу друг от друга, который включает получение раствора материала, содержащего, по меньшей мере, коллоидные частицы первого оксида металла и металлические соли второго оксида металла, где первый оксид металла представляет оксид алюминия или оксид циркония, а второй оксид металла выбран из группы, состоящей из оксидов неодима, празеодима, лантана, скандия и иттрия; доведение рН раствора материала близко к изоэлектрической точке коллоидных частиц первого оксида металла с тем, чтобы коагулировать коллоидные частицы первого оксида металла; увеличение рН раствора материала с тем, чтобы осадить коллоидные частицы второго оксида металла из металлических солей и коагулировать коллоидные частицы второго оксида металла вокруг коагулированных коллоидных частиц первого оксида металла, причем изоэлектрическая точка коллоидных частиц второго оксида металла является более высокой, чем изоэлектрическая точка коллоидных частиц первого оксида металла; и сушку и прокаливание коагулированного продукта. Технический эффект – увеличение удельной площади поверхности катализатора очистки отходящего газа, увеличение степени регенерации платиновых частиц. 4 н. и 6 з.п. ф-лы, 3 ил., 2 табл.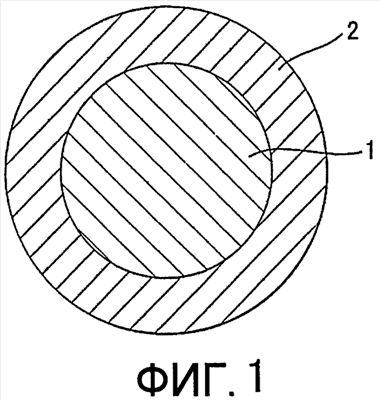
Предпосылки создания изобретения
1. Область техники, к которой относится изобретение
Настоящее изобретение относится к частицам металлоксидного носителя катализатора, к способу получения таких частиц, к катализатору очистки отходящего газа, выполненному из частиц металлоксидного катализатора, и к способу регенерации катализатора очистки отходящего газа.
2. Описание прототипа
Отходящий газ из двигателя внутреннего сгорания, такого как двигатель автомобиля, содержит оксид азота (NOx), монооксид углерода (СО), углеводород (НС) и т.д. Указанные вещества могут быть удалены катализатором очистки отходящего газа, который способен окислять СО и НС и восстанавливать NOx. Типичным примером такого катализатора очистки отходящего газа является тройной катализатор, который выполнен из пористого металлоксидного носителя, такого как -глинозем, и благородного металла, такого как платина (Pt), родий (Rh) и палладий (Pd), который нанесен на пористый металлоксидный носитель.
Обычно в качестве благородного металла для тройных катализаторов используется платина. Однако при использовании платины имеется проблема в том, что при воздействии высокотемпературного отходящего газа в течение длительного периода времени платиновые частицы растут в размере, и, таким образом, удельная площадь поверхности каждой платиновой частицы соответственно снижается, снижая уровень активации катализатора. Для противодействия этому разработаны различные способы подавления такого роста платиновых частиц.
Например, было установлено, что поскольку оксид церия имеет высокое сродство к благородному металлу очистки отходящего газа, особенно платине, когда оксид церия используется в качестве носителя катализатора, рост (спекание) частиц благородного металла подавляется. Для того чтобы использовать указанные характеристики оксида церия при компенсировании недостатков использования оксида церия, имеющего относительно низкую теплостойкость, JP-A-2005-313024, JP-A-2005-314133, JP-A-2004-141833 и JP-A-2005-254047 каждый описывают использование в качестве носителя платины как каталитического металла металлоксидных частиц, каждая из которых имеет наружную оболочечную часть, содержащую много оксида церия, и центральную часть, содержащую много оксида алюминия, который является оксидом металла, имеющим высокую теплостойкость.
В качестве способа получения металлоксидной частицы, имеющей наружную оболочечную часть и центральную часть, которые являются различными по составу, JP-A-2005-314133 описывает способ, в котором получают золь, содержащий коллоидные частицы первого оксида металла и коллоидные частицы второго оксида металла, который имеет изоэлектрическую точку, отличающуюся от изоэлектрической точки коллоидных частиц первого оксида металла; рН золя регулируют так, чтобы он был ближе к изоэлектрической точке коллоидных частиц первого оксида металла, чем к изоэлектрической точке коллоидных частиц второго оксида металла, так что коллоидные частицы первого оксида металла коагулируются; затем рН золя регулируют так, чтобы он был ближе к изоэлектрической точке коллоидных частиц второго оксида металла, чем к изоэлектрической точке коллоидных частиц первого оксида металла, так что коагулируются коллоидные частицы второго оксида металла; и затем коагулированный продукт сушат и прокаливают.
Между тем, JP-A-2000-202309 и JP-A-2003-74334 каждый описывают способ редиспергирования платиновых частиц, которые растут в размере при использовании, на носителе. В способе редиспергирования платины, описанном в JP-A-2000-202309, нагревают катализаторы очистки отходящего газа, каждый состоящий из носителя, такого как оксид щелочноземельного металла и оксид редкоземельного металла, и платины, нанесенной на носитель, при 500-1000°C в окислительной атмосфере, которая содержит атомов кислорода больше, чем число молей платины на носителе.
Когда платина нагревается таким образом в окислительной атмосфере, на поверхности каждой платиновой частицы, которая растет в размере при использовании, появляются оксиды платины. Поскольку оксиды платины имеют высокую способность к взаимодействию с оксидами редкоземельных металлов, оксиды платины на поверхности платиновой частицы движутся к поверхности носителя, и, таким образом, платина оказывается оголенной на поверхности платиновой частицы. Оголенная платина затем окисляется кислородом до оксидов платины, и указанные оксиды платины движутся к поверхности носителя таким же образом, как описано выше. Когда это происходит повторно, платиновые частицы, нанесенные на оксид редкоземельного металла или подобное, постепенно диспергируются на поверхности носителя, и размеры частиц снижаются, таким образом, позволяя оксидам платины быть дисперсно нанесенными на носитель. Когда катализатор, в котором оксиды платины дисперсно нанесены на носитель, как указано выше, помещается в контакт с отходящим газом, имеющим стехиометрическую атмосферу или восстановительную атмосферу, оксиды платины восстанавливаются до платины, поэтому катализатор очистки отходящего газа регенерируется. Следует отметить, что оксиды платины легко восстанавливаются, и, таким образом, реакции их восстановления являются легко осуществимыми.
Краткое описание изобретения
Настоящее изобретение предусматривает катализатор очистки отходящего газа, в котором платина соответствующе редиспергирована, способ редиспергирования платины для такого катализатора очистки отходящего газа, частицу металлоксидного носителя катализатора, используемую для получения такого катализатора очистки отходящего газа, и способ получения такой частицы металлоксидного носителя катализатора.
Один аспект данного изобретения относится к частице металлоксидного носителя катализатора, имеющей центральную часть и наружную оболочечную часть, причем каждая содержит первый оксид металла и второй оксид металла. Центральная часть и наружная оболочечная часть отличаются друг от друга по составу. В указанной частице металлоксидного носителя катализатора мольная фракция металла первого оксида металла выше в центральной части, чем в наружной оболочечной части, мольная фракция металла второго оксида металла выше в наружной оболочечной части, чем в центральной части, и второй оксид металла выбран из группы, состоящей из оксидов редкоземельных металлов, кроме оксида церия, и оксидов щелочноземельных металлов.
Согласно данному аспекту, когда катализатор благородного металла образуется при связывании платины на частице металлоксидного носителя катализатора, свойства (особенно теплостойкость) достигаются за счет первого оксида металла, получаемого в центральной части частицы металлоксидного носителя катализатора, и редиспергируемость платины достигается за счет получаемого второго оксида металла. Т.е. согласно первому аспекту данного изобретения, когда катализатор, несущий благородный металл, получается при связывании платины на частицах металлоксидного носителя катализатора согласно данному аспекту изобретения, большая удельная площадь поверхности каждой частицы металлоксидного носителя катализатора может поддерживаться благодаря высокой теплостойкости первого оксида металла, и платина может очень эффективно редиспергироваться благодаря второму оксиду металла в наружной оболочечной части каждой частицы металлоксидного носителя катализатора.
Частица металлоксидного носителя катализатора, описанная выше, может быть такой, что первый оксид металла является выбранным из группы, состоящей из оксида алюминия, оксида циркония, оксида кремния, оксида титана и комбинаций из оксида алюминия, оксида циркония, оксида кремния и оксида титана. В данном случае предпочтительно используемым является оксид алюминия.
Частица металлоксидного носителя катализатора, описанная выше, может быть такой, что второй оксид металла является выбранным из группы, состоящей из оксидов редкоземельных металлов (кроме оксида церия), которые включают, например, оксид неодима, оксид празеодима, оксид лантана, оксид скандия и оксид иттрия. Предпочтительно второй оксид металла выбран из группы, состоящей из оксида неодима, оксида празеодима и оксида иттрия.
Частица металлоксидного носителя катализатора, описанная выше, может быть такой, что удельная площадь поверхности частицы металлоксидного носителя катализатора составляет более 15 м2/г, предпочтительно 20 м2/г, более предпочтительно 30 м2/г, еще более предпочтительно 40 м2/г, после того как металлоксидный носитель катализатора был поочередно подвергнут воздействию обогащенного газа (монооксид углерода (2 об.%) + азот) и обедненного газа (кислород (2 об.%) + азот) при 1000°C в течение 5 ч, так что газ, в котором выдерживается металлоксидный носитель катализатора, переключается между обогащенным газом и обедненным газом каждую минуту.
Частица металлоксидного носителя катализатора, описанная выше, может быть такой, что первый оксид металла представляет собой оксид алюминия, второй оксид металла выбран из группы, состоящей из оксида неодима, оксида празеодима и оксида иттрия, и удельная площадь поверхности частицы металлоксидного носителя катализатора составляет более 40 м2/г, после того как металлоксидный носитель катализатора был поочередно подвергнут воздействию обогащенного газа (монооксид углерода (2 об.%) + азот) и обедненного газа (кислород (2 об.%) + азот) при 1000°C в течение 5 ч, так что газ, в котором выдерживается металлоксидный носитель катализатора, переключается между обогащенным газом и обедненным газом каждую минуту.
Другой аспект данного изобретения относится к катализатору очистки отходящего газа, содержащему частицу металлоксидного носителя катализатора согласно приведенному выше аспекту изобретения и платину, нанесенную на частицу металлоксидного носителя катализатора.
Другой аспект данного изобретения относится к способу регенерации катализатора очистки отходящего газа согласно настоящему изобретению. Данный способ включает нагревание катализатора очистки отходящего газа при температуре в интервале 500-1000°C в окислительной атмосфере, которая содержит кислород.
Способ регенерации, описанный выше, может быть таким, что процесс восстановления платины осуществляется после нагревания катализатора очистки отходящего газа в окислительной атмосфере, содержащей кислород.
Другой аспект данного изобретения относится к способу получения частицы металлоксидного носителя катализатора, имеющей центральную часть и наружную оболочечную часть, причем каждая содержит первый оксид металла и второй оксид металла, где центральная часть и наружная оболочечная часть отличаются друг от друга по составу. Данный способ включает получение раствора материала, предпочтительно водного раствора соли, который содержит, по меньшей мере, коллоидные частицы первого оксида металла и металлические соли второго оксида металла; коагулирование коллоидных частиц первого оксида металла при регулировании рН раствора материала до точки ближе к изоэлектрической точке коллоидных частиц первого оксида металла предпочтительно при регулировании рН раствора материала в интервале ±1,0 от изоэлектрической точки коллоидных частиц первого оксида металла, более предпочтительно при регулировании рН раствора материала в интервале ±0,5 от изоэлектрической точки коллоидных частиц первого оксида металла, еще более предпочтительно при изменении рН раствора материала после изоэлектрической точки коллоидных частиц первого оксида металла, даже еще более предпочтительно при увеличении рН раствора материала после изоэлектрической точки коллоидных частиц первого оксида металла с тем, чтобы коагулировать коллоидные частицы первого оксида металла; увеличение рН раствора материала с тем, чтобы высадить коллоидные частицы второго оксида металла из металлических солей и коагулировать коллоидные частицы второго оксида металла вокруг коагулированных коллоидных частиц первого оксида металла, где изоэлектрическая точка коллоидных частиц второго оксида металла выше, чем изоэлектрическая точка коллоидных частиц первого оксида металла; и сушку и прокаливание коагулированного продукта.
Способ получения, описанный выше, может быть таким, что первый оксид металла выбран из группы, состоящей из оксида алюминия, оксида циркония, оксида кремния, оксида титана и комбинаций из оксида алюминия, оксида циркония, оксида кремния и оксида титана, и/или второй оксид металла выбран из группы, состоящей из оксидов редкоземельных металлов (кроме оксида церия) и оксидов щелочноземельных металлов.
В данном описании термин «коллоидные частицы» охватывает оксиды металлов, диспергированные в жидкой дисперсионной среде, или частицы, содержащие каждая металл, связанный с кислородом, которые могут быть преобразованы в оксиды металлов путем удаления дисперсионной среды и прокаливания. Дисперсионной средой обычно является вода, но альтернативно ею может быть органическая дисперсионная среда, такая как спирт или ацетилацетон. Обычно подразумевается, что «коллоидные частицы» имеют диаметр 1-1000 нм, в частности 1-500 нм. Например, коллоидные частицы, каждая имеющая диаметр 100 нм или 50 нм, являются пригодными. Коллоидные частицы, диспергированные в жидкой дисперсионной среде, т.е. коллоидные частицы дисперсного типа, часто называются «золем» или «коллоидным раствором».
Краткое описание чертежей
Вышеуказанное и другие задачи, характеристики и преимущества настоящего изобретения станут очевидными из последующего описания предпочтительных вариантов со ссылкой на прилагающиеся чертежи, на которых подобные числа используются для представления подобных элементов и на которых
на фиг.1 представлено поперечное сечение частицы металлоксидного носителя катализатора согласно аспекту изобретения;
на фиг.2 представлена графическая зависимость, показывающая, как дзета-потенциал первого и второго оксида металлов используется в способе получения частицы металлоксидного носителя катализатора согласно изменениям изобретения;
на фиг.3 представлена диаграмма, показывающая степень регенерации платины в соответствующих примерах и сравнительных примерах.
Подробное описание аспекта изобретения
Настоящее изобретение будет описано со ссылкой на фиг.1. На фиг.1 представлено поперечное сечение частицы металлоксидного носителя катализатора согласно аспекту изобретения.
Как представлено на фиг.1, частица металлоксидного носителя катализатора согласно аспекту изобретения имеет центральную часть 1, содержащую относительно большое количество первого оксида металла, которым является, например, оксид алюминия, и наружную оболочечную часть 2, содержащую относительно большое количество второго оксида металла, которым являются, например, оксиды редкоземельных металлов.
Граница раздела между центральной частью 1 и наружной оболочечной частью 2 не должна быть обязательно четко определена. Т.е. состав на границе раздела может постепенно изменяться, что является желательным с точки зрения теплостойкости. Кроме того, граница раздела между центральной частью 1 и наружной оболочечной частью 2 может состоять из смеси первого оксида металла и второго оксида металла, в частности твердого смешанного раствора первого оксида металла и второго оксида металла. Должно быть отмечено, что наружная оболочечная часть 2 может быть не непрерывной, хотя видно, что она является непрерывной на фиг.1.
Каждая из центральной части 1 и наружной оболочечной части 2 частицы металлоксидного носителя катализатора может состоять из множества первичных частиц. В том случае, когда частицы металлоксидного носителя катализатора получаются с использованием коллоидных частиц, коллоидные частицы, которые используются для образования центральной части и наружной оболочечной части соответственно, соответствуют первичным частицам соответствующих частей. Однако в некоторых случаях четкая граница раздела между первичными частицами отсутствует.
Частицы металлоксидного носителя катализатора, например, могут иметь средний диаметр частиц менее 10 мкм, 5 мкм, 1 мкм, 500 нм, 200 нм, 100 нм или 50 нм. Например, когда диаметр частицы коллоидных частиц, используемых в качестве материала, составляет в среднем примерно 5 нм, средний диаметр частицы частиц металлоксидного носителя катализатора может быть 50 нм или менее.
Оксиды произвольно выбранного металла могут быть использованы в качестве первых оксидов металла для частиц металлоксидного носителя катализатора. В качестве первых оксидов металла могут использоваться, например, оксиды металлов, которые обычно используются для получения частиц носителя катализатора, такие как оксид алюминия, оксид циркония, оксид кремния, оксид титана или их заданная комбинация, в частности оксид алюминия или оксид циркония, более строго говоря, оксид алюминия является предпочтительным с точки зрения теплостойкости и удельной площади поверхности.
Второй оксид металла для частицы металлоксидного носителя катализатора выбран из группы, состоящей из оксидов редкоземельных металлов, кроме оксида церия, и из оксидов щелочноземельных металлов. Предпочтительно, с точки зрения теплостойкости, что второй оксид металла для частицы металлоксидного носителя катализатора выбран из группы, состоящей из оксидов редкоземельных металлов, кроме оксида церия. Оксиды указанных металлов, как описано в JP-A-2000-202309, имеют относительно высокое сродство к платине и оксидам платины. Т.е. оксид церия как один из оксидов редкоземельных металлов имеет относительно высокое сродство к платине и оксидам платины. Однако использование иных, чем оксид церия, оксидов редкоземельных металлов дает возможность значительно эффективнее редиспергировать платину в каждой частице металлоксидного носителя катализатора. Это обусловлено тем, что, например, оксид церия подавляет получение оксидов платины при поглощении кислорода при использовании его способности хранить и высвобождать кислород (способность хранения кислорода) в окислительной атмосфере, и/или поскольку сродство оксида церия к платине и оксиду платины снижается кислородом, который хранится на поверхности оксида церия благодаря способности хранить кислород.
Помимо первого и второго оксидов металлов, наружная оболочечная часть и центральная часть могут также содержать менее 50 мол.% других оксидов металла соответственно. В частности, когда центральная часть содержит оксид циркония или оксид алюминия, центральная часть может дополнительно содержать менее 1-50 мол.% металла, предпочтительно 1-10 мол.% металла, который выбран из группы, состоящей из щелочноземельных металлов и редкоземельных металлов. Такое введение оксидов щелочноземельных металлов и оксидов редкоземельных металлов, особенно оксидов иттрия, увеличивает теплостойкость содержащихся оксида циркония и оксида алюминия и поэтому является желательным.
Катализатор очистки отходящего газа согласно аспекту настоящего изобретения получается при связывании платины на частице металлоксидного носителя катализатора согласно аспекту изобретения.
Для связывании платины на частицах металлоксидного носителя катализатора может быть использован известный способ. Например, платина может быть связана на частицах носителя пропиткой частиц носителя в растворе, содержащем платиновые соли или платиновые комплексные соли, и затем их сушкой и прокаливанием. Количество платины, нанесенной на каждую частицу металлоксидного носителя катализатора, составляет, например, 0,01-5 мас.%, предпочтительно 0,1-2 мас.% по отношению к частице металлоксидного носителя катализатора. Должно быть отмечено, что на катализатор очистки отходящего газа согласно данному аспекту изобретения также могут быть нанесены так называемые NOx-хранящие элементы, выбранные из благородных металлов (например, платины и родия), неблагородных металлов (например, меди, железа, никеля и кобальта), щелочных металлов, щелочноземельных металлов и/или редкоземельных элементов.
Катализатор очистки отходящего газа, полученный, как описано выше, может использоваться нанесенным на монолитную подложку, такую как керамическая сотовая подложка, а также формованным в специальную форму.
Способ регенерации согласно другому аспекту настоящего изобретения представляет собой способ регенерации катализаторов очистки отходящего газа согласно аспекту изобретения. Данный способ включает нагревание катализатора очистки отходящего газа до 500°C или выше, например в интервале 600-1000°C, предпочтительно в интервале 600-800°C, в окислительной атмосфере, содержащей кислород. В частности, указанная температура нагревания зависит от состава окислительной атмосферы, содержащей кислород, периода времени, в течение которого осуществляется способ регенерации катализатора очистки отходящего газа, и т.д. Если температура нагревания является слишком низкой, платина может быть не в состоянии достаточно окисляться и редиспергироваться. Наоборот, если температура нагревания является слишком высокой, уровень активации катализатора может снизиться благодаря спеканию частиц металлоксидного носителя катализатора и т.д.
Согласно способу, в котором платина редиспергируется в окислительной атмосфере, как описано в JP-A-2000-202309, оксиды платины получаются на поверхности каждой платиновой частицы, которая растет в размере при использовании, и такие оксиды платины затем движутся к поверхности носителя. Когда это происходит повторно, платиновые частицы диспергируются на поверхности носителя, и размеры их частиц постепенно снижаются. Таким образом, оксиды платины могут быть дисперсно нанесены на носитель.
Кислородсодержащая окислительная атмосфера, используемая в вышеуказанном способе регенерации, представляет собой окислительную атмосферу, имеющую окислительную способность, которая является достаточно сильной для получения оксидов платины при окислении платины, нанесенной на частицы металлоксидного носителя катализатора. В качестве кислородсодержащей окислительной атмосферы используется, например, азотная атмосфера, содержащая 10 об.% или более кислорода, предпочтительно воздух. Прокаливание в указанной атмосфере осуществляется в течение, например, 1-5 ч, предпочтительно 2-4 ч.
При осуществлении вышеуказанного способа регенерации катализаторов очистки отходящего газа, например, устройство катализатора очистки отходящего газа отсоединяется от выводящей системы, и вышеуказанный способ регенерации осуществляется в отсоединенном устройстве катализатора в предварительно описанном устройстве. Однако предпочтительно способ регенерации осуществляется в устройстве катализатора очистки отходящего газа в выводящей системе без его отсоединения. В данном случае, например, окисление катализаторов осуществляется при увеличении соотношения воздух-топливо (A/F) воздушно-топливных смесей до очень высокого соотношения введением большого количества воздуха через воздушный клапан, предусмотренный вверх по потоку от устройства катализатора очистки отходящего газа, и/или резким снижением количества подаваемого топлива. Кроме того, катализаторы очистки отходящего газа могут нагреваться с использованием отдельного нагревательного устройства или при использовании тепла реакции катализаторов очистки отходящего газа.
В том случае, когда процесс окисления катализаторов очистки отходящего газа осуществляется без отсоединения устройства катализатора очистки отходящего газа от выводящей системы, как указано выше, можно осуществлять процесс очистки в реальное время в соответствии с ухудшением характеристики катализатора. Например, способ регенерации может регулярно осуществляться в соответствии с периодом времени, в течение которого движется автомобиль, или с расстоянием, которое преодолел автомобиль до сих пор. Кроме того, если датчик NOx или датчик СО предусмотрен ниже по потоку от устройства катализатора очистки отходящего газа для определения плотности NOx или СО для контроля характеристики катализатора, способ регенерации может быть задействован в ответ на определение датчиком значения плотности больше, чем пороговое значение.
Способ восстановления платины после ее редиспергирования может быть осуществлен, например, при нагревании катализатора очистки отходящего газа в газе-восстановителе, таком как газообразный водород и газообразный монооксид углерода. Например, в том случае, когда катализатор очистки отходящего газа используется в автомобиле, отходящий газ, имеющий стехиометрическое соотношение воздух-топливо или топливообогащенное соотношение воздух-топливо, может использоваться в качестве газа-восстановителя. Таким образом, процесс окисления и процесс восстановления катализаторов очистки отходящего газа могут быть осуществлены без отсоединения устройства катализатора очистки отходящего газа от выпускающей системы и как часть регулирования соотношения воздух-топливо. Необходимо отметить, что температура нагревания, используемая в процессе окисления, устанавливается при значении, которое вызывает восстановление оксидов платины, например, 300°C или выше.
Частицы металлоксидного носителя катализатора согласно аспекту данного изобретения могут быть получены любым способом, таким как способ, описанный в JP-A-2005-314133, который используется для получения металлоксидных частиц, каждая из которых имеет центральную часть и наружную оболочечную часть, которые отличаются по составу друг от друга.
Кроме того, частицы металлоксидного носителя катализатора согласно аспекту изобретения могут быть получены способом получения частицы металлоксидного носителя катализатора согласно аспекту изобретения.
Например, металлоксидные частицы носителя катализатора согласно аспекту изобретения, каждая из которых имеет центральную часть и наружную оболочечную часть, которые отличаются по составу друг от друга, могут быть получены способом, включающим следующие стадии: получение раствора материала, содержащего, по меньшей мере, коллоидные частицы первых оксидов металла и металлических солей вторых оксидов металла; корректирование рН раствора материала до точки ближе к изоэлектрической точке коллоидных частиц первого оксида металла с тем, чтобы коагулировать коллоидные частицы первых оксидов металла; увеличение рН раствора материала с тем, чтобы высадить коллоидные частицы второго оксида металла из металлических солей и коагулировать осажденные коллоидные частицы вторых оксидов металла вокруг коагулированных коллоидных частиц первых оксидов металла, где изоэлектрическая точка коллоидных частиц вторых оксидов металла выше, чем изоэлектрическая точка коллоидных частиц первых оксидов металла; и сушку и прокаливание коагулированного продукта.
Далее описывается каждая стадия способа получения частицы металлоксидного носителя катализатора согласно аспекту данного изобретения.
Согласно данному аспекту сначала получают раствор материала, содержащего, по меньшей мере, коллоидные частицы первых оксидов металла и металлические соли вторых оксидов металла.
Коллоидные частицы первых оксидов металла, используемых здесь, получают, например, гидролитическим разрушением и конденсацией первого металла, который выбран из соли алкоголята, ацетилацетоната, ацетата, нитрата и т.д. Альтернативно могут использоваться золи, такие как золь оксида алюминия, золь оксида циркония, золь оксида титана и золь оксида церия, которые являются известными и коммерчески доступными материалами.
рН каждого коммерчески доступного золя не является близкой к изоэлектрической точке коллоидных частиц, содержащихся в золе, так что коллоидные частицы не коагулируются в результате электростатического отталкивания между ними. Т.е. золь, содержащий коллоидные частицы, имеющие изоэлектрическую точку на щелочной стороне, стабилизируется при подкислении золя (стабилизированный кислотой золь), и золь, содержащий коллоидные частицы, имеющие изоэлектрическую точку на кислотной стороне, стабилизируется при подщелачивании золя (стабилизированный щелочью золь).
Изоэлектрическая точка коллоидных частиц не только зависит от материала коллоидных частиц, таких как оксиды, составляющие частицы. Т.е. изоэлектрическая точка коллоидных частиц может быть произвольно установлена при преобразовании поверхности коллоидных частиц, предпочтительно при преобразовании поверхности коллоидных частиц с использованием органических соединений.
Как указано, изоэлектрическая точка коллоидных частиц может быть установлена произвольным способом на уровне, необходимом для способа получения согласно аспекту изобретения. Установленная таким образом изоэлектрическая точка может быть измерена, например, методом электрофореза со световым рассеянием.
Между тем, металлические соли вторых оксидов металла, используемых здесь, представляют собой, например, карбоксилат, такой как ацетат, или минеральные соли, такие как нитрат и сульфат.
Раствор материала, содержащий, по меньшей мере, коллоидные частицы первых оксидов металла и металлические соли вторых оксидов металла, может быть получен любым способом. Например, такой раствор материала может быть получен растворением металлических солей вторых оксидов металла в золе, содержащем коллоидные частицы первого оксида металла, или смешением золя, содержащего коллоидные частицы первого оксида металла, и золя, содержащего металлические соли второго оксида металла. Соотношение смешения между коллоидными частицами первого оксида металла и металлическими солями второго оксида металла может быть установлено при произвольном соотношении в зависимости от желаемых характеристик металлоксидных частиц.
В способе получения согласно указанному аспекту изобретения оксиды металла, которые могут содержаться в частицах металлоксидного носителя катализатора в дополнение к первому и второму оксидам металла, могут содержаться в растворе материала в форме коллоидных частиц и/или металлических солей, таких как нитрат.
В способе получения согласно указанному аспекту изобретения рН раствора материала затем устанавливают ближе к изоэлектрической точке коллоидных частиц первого оксида металла (точка a на фиг.2) с тем, чтобы коагулировать коллоидные частицы первого оксида металла. На фиг.2 представлена графическая зависимость, показывающая, как изменяются дзета-потенциалы коллоидных частиц первого и второго оксидов металла.
Как описано выше, рН каждого коммерчески доступного золя не является близкой к изоэлектрической точке коллоидных частиц, содержащихся в золе, так что коллоидные частицы не будут коагулировать благодаря электростатическому отталкиванию между ними. Поэтому если рН раствора материала устанавливается ближе к изоэлектрической точке коллоидных частиц первого оксида металла, как в вышеуказанном способе, дзета-потенциал коллоидных частиц первого оксида металла снижается, что подавляет электростатическое отталкивание между коллоидными частицами и способствует их коагуляции.
рН раствора материала может регулироваться введением щелочи, такой как аммиачная вода и гидроксид натрия, или кислоты, такой как уксусная кислота, азотная кислота и хлористоводородная кислота. Кроме того, рН раствора материала может регулироваться простым смешиванием золя, содержащего коллоидные частицы первых оксидов металла, и золя, содержащего металлические соли вторых оксидов металла.
При регулировании рН раствора материала, например, кислоту или щелочь вводят в раствор материала при измерении рН раствора материала с использованием рН-метра. Альтернативно регулирование рН раствора материала может быть таким, что количество кислоты или щелочи, необходимое для получения определенной рН образца раствора материала, измеряется заранее, и количество кислоты или щелочи, необходимое для всего раствора материала, определяется на основе измеренного количества и определенного количества кислоты или щелочи, введенного в раствор материала.
Осаждение и коагуляция коллоидных частиц вторых оксидов металла
В способе получения согласно аспекту изобретения рН раствора материала увеличивается так, что коллоидные частицы второго оксида металла высаждаются из металлических солей (точка b на фиг.2), и осажденные коллоидные частицы вторых оксидов металла затем коагулируются вокруг коагулированных коллоидных частиц первых оксидов металла (точка с на фиг.2).
Раствор соли, предпочтительно водный раствор соли, такой как раствор ацетата металла и раствор нитрата металла, является относительно эффективным для осаждения коллоидных частиц оксидов металла при щелочном рН. Поэтому если рН раствора материала, содержащего металлические соли второго оксида металла, увеличивается, как на указанной стадии получения, коллоидные частицы вторых оксидов металла высаждаются из металлических солей.
В способе получения изоэлектрическая точка осажденных коллоидных частиц вторых оксидов металла выше, чем изоэлектрическая точка коллоидных частиц первого оксида металла. Как указано выше, изоэлектрическая точка коллоидных частиц не ограничивается материалами коллоидных частиц, такими как оксиды, но она может быть произвольно установлена преобразованием поверхностей коллоидных частиц, особенно преобразованием поверхностей коллоидных частиц с использованием органических соединений.
Таким образом, для того чтобы создать положение, когда изоэлектрическая точка осажденных коллоидных частиц вторых оксидов металла выше, чем изоэлектрическая точка коллоидных частиц первого оксида металла, коллоидные частицы, имеющие относительно низкую изоэлектрическую точку, выбираются, например, в качестве коллоидных частиц первых оксидов металла. В частности, коллоидные частицы первых оксидов металла и металлические соли вторых оксидов металла выбираются так, что разность между рН в изоэлектрической точке коллоидных частиц вторых оксидов металла и рН в изоэлектрической точке коллоидных частиц первых оксидов металла (т.е. разность между точкой а и точкой с на фиг.2) составляет 3 или более, предпочтительно 4 или более и более предпочтительно 5 или более.
В том случае, когда изоэлектрическая точка коллоидных частиц второго оксида металла выше изоэлектрической точки коллоидных частиц первого оксида металла, когда дзета-потенциал коллоидных частиц первого оксида металла является достаточно низким, чтобы вызвать коагуляцию коллоидных частиц первых оксидов металла, вторые оксиды металла присутствуют в растворе материала в форме растворенных в нем солей или в форме коллоидных частиц, имеющих относительно высокий дзета-потенциал, и поэтому коагуляция коллоидных частиц вторых оксидов металла подавляется.
Затем, когда рН раствора материала, содержащего коагулированные коллоидные частицы первых оксидов металла, изменяется до точки, близкой к изоэлектрической точке коллоидных частиц вторых оксидов металла, дзета-потенциал коллоидных частиц вторых оксидов металла становится низким, так что электростатическое отталкивание между указанными коллоидными частицами снижается, и, таким образом, вызывается коагуляция коллоидных частиц вторых оксидов металла. В это время, поскольку разность между рН раствора материала и изоэлектрической точкой коллоидных частиц первых оксидов металла является относительно большой, коагуляция коллоидных частиц первых оксидов металла подавляется, и коллоидные частицы второго оксида металла коагулируются вокруг коллоидных частиц первого оксида металла.
Необходимо отметить, что рН раствора материала регулируют таким же образом, как для коагуляции первых оксидов металла.
Затем в результате сушки и прокаливания коагулированного продукта получаются металлоксидные частицы, имеющие каждая центральную часть, которая, главным образом, состоит из компонентов, полученных из коллоидных частиц первых оксидов металла, и наружную оболочечную часть, которая, главным образом, состоит из коллоидных частиц вторых оксидов металла.
Способ удаления дисперсионной среды из раствора материала и сушки раствора материала может быть осуществлен любым способом и при любой температуре. Например, раствор материала нагревают в печи при 120°C. Материал, полученный при удалении дисперсионной среды из раствора материала и сушке раствора материала, затем прокаливают с получением металлоксидных частиц. Указанное прокаливание может осуществляться при температуре, которая обычно используется для синтеза оксидов металлов, такой как 500-1100°C.
Далее описываются примеры изобретения. Необходимо отметить, что изобретение не ограничивается указанными примерами.
В экспериментах, описанных ниже, рН каждого раствора измеряется с использованием рН-метра, в частности, при непосредственном погружении электрода рН-метра в раствор.
Пример 1
В примере 1 получают частицы металлоксидного носителя катализатора, каждая из которых имеет центральную часть, которая состоит, главным образом, из оксида циркония, и наружную оболочечную часть, которая состоит, главным образом, из оксидов скандия, и затем платину связывают на полученных частицах металлоксидного носителя катализатора, так что происходит нанесение платины.
К 10 мас.% стабилизированного щелочью золю оксида циркония (т.е. золю, имеющему относительно кислотную изоэлектрическую точку) добавляют азотную кислоту с тем, чтобы довести его рН до 1. Затем в дистиллированную воду вводят тетрагидрат нитрата скандия, причем масса воды в шесть раз больше массы введенного тетрагидрата нитрата скандия. Данный раствор затем добавляют к золю оксида циркония, так что количество скандия составляет 30 мол.% по отношению к цирконию, содержащемуся в золе оксида циркония. Затем полученный таким образом смешанный раствор перемешивают в течение часа. Затем к смешанному раствору добавляют 28% аммиачную воду с доведением рН до 9, затем смешанный раствор сушат при 120°C с удалением из него воды и затем прокаливают при 600°C в течение 5 ч. Продукт, полученный в результате прокаливания, затем измельчают в ступке. Таким образом получают частицы металлоксидного носителя катализатора согласно примеру 1.
Затем полученные частицы металлоксидного носителя катализатора диспергируют в дистиллированной воде, которая в шесть раз больше по массе, чем частицы металлоксидного носителя катализатора, затем добавляют раствор динитроамина платины, так чтобы присутствовало 1,0 мас.% платины по отношению к частицам металлоксидного носителя катализатора, и раствор затем перемешивают в течение часа. Затем раствор сушат при 120°C с удалением из него воды и затем прокаливают при 500°C в течение 2 ч.
Пример 2
В примере 2 частицы металлоксидного носителя катализатора, каждая из которых имеет центральную часть, которая состоит, главным образом, из оксида циркония, и наружную оболочечную часть, которая состоит, главным образом, из оксидов иттрия, получают по методике, которая является такой же, как методика примера 1, за исключением того, что гексагидрат нитрата иттрия используется вместо тетрагидрата нитрата скандия. Затем платину связывают на полученных частицах металлоксидного носителя катализатора таким же образом, как в примере 1, так что происходит нанесение платины на частицы металлоксидного носителя катализатора.
Пример 3
В примере 3 частицы металлоксидного носителя катализатора, каждая из которых имеет центральную часть, которая состоит, главным образом, из оксида циркония, и наружную оболочечную часть, которая состоит, главным образом, из оксидов неодима, получают по методике, которая является такой же, как методика примера 1, за исключением того, что гексагидрат нитрата неодима используется вместо тетрагидрата нитрата скандия. Затем платину связывают на полученных частицах металлоксидного носителя катализатора таким же образом, как в примере 1, так что происходит нанесение платины на частицы металлоксидного носителя катализатора.
Пример 4
В примере 4 частицы металлоксидного носителя катализатора, каждая из которых имеет центральную часть, которая состоит, главным образом, из оксида циркония, и наружную оболочечную часть, которая состоит, главным образом, из оксидов празеодима, получают по методике, которая является такой же, как методика примера 1, за исключением того, что гексагидрат нитрата празеодима используется вместо тетрагидрата нитрата скандия. Затем платину связывают на полученных частицах металлоксидного носителя катализатора таким же образом, как в примере 1, так что происходит нанесение платины на частицы металлоксидного носителя катализатора.
Пример 5
В примере 5 частицы металлоксидного носителя катализатора, каждая из которых имеет центральную часть, которая состоит, главным образом, из оксида циркония, и наружную оболочечную часть, которая состоит, главным образом, из оксидов лантана, получают по методике, которая является такой же, как методика примера 1, за исключением того, что гексагидрат нитрата лантана используется вместо тетрагидрата нитрата скандия. Затем платину связывают на полученных частицах металлоксидного носителя катализатора таким же образом, как в примере 1, так что происходит нанесение платины на частицы металлоксидного носителя катализатора.
Пример 6
В примере 6 частицы металлоксидного носителя катализатора, каждая из которых имеет центральную часть, которая состоит, главным образом, из оксида алюминия, и наружную оболочечную часть, которая состоит, главным образом, из оксидов скандия, получают по методике, которая является такой же, как методика примера 1, за исключением того, что стабилизированный щелочью золь оксида алюминия используется вместо стабилизированного щелочью золя оксида циркония. Затем платину связывают на полученных частицах металлоксидного носителя катализатора таким же образом, как в примере 1, так что происходит нанесение платины на частицы металлоксидного носителя катализатора.
Пример 7
В примере 7 частицы металлоксидного носителя катализатора, каждая из которых имеет центральную часть, которая состоит, главным образом, из оксида алюминия, и наружную оболочечную часть, которая состоит, главным образом, из оксидов иттрия, получают по методике, которая является такой же, как методика примера 1, за исключением того, что гексагидрат нитрата иттрия используется вместо тетрагидрата нитрата скандия, и стабилизированный щелочью золь оксида алюминия используется вместо стабилизированного щелочью золя оксида циркония. Затем платину связывают на полученных частицах металлоксидного носителя катализатора таким же образом, как в примере 1, так что происходит нанесение платины на частицы металлоксидного носителя катализатора.
Пример 8
В примере 8 частицы металлоксидного носителя катализатора, каждая из которых имеет центральную часть, которая состоит, главным образом, из оксида алюминия, и наружную оболочечную часть, которая состоит, главным образом, из оксидов неодима, получают по методике, которая является такой же, как методика примера 1, за исключением того, что гексагидрат нитрата неодима используется вместо тетрагидрата нитрата скандия, и стабилизированный щелочью золь оксида алюминия используется вместо стабилизированного щелочью золя оксида циркония. Затем платину связывают на полученных частицах металлоксидного носителя катализатора таким же образом, как в примере 1, так что происходит нанесение платины на частицы металлоксидного носителя катализатора.
Пример 9
В примере 9 частицы металлоксидного носителя катализатора, каждая из которых имеет центральную часть, которая состоит, главным образом, из оксида алюминия, и наружную оболочечную часть, которая состоит, главным образом, из оксидов празеодима, получают по методике, которая является такой же, как методика примера 1, за исключением того, что гексагидрат нитрата празеодима используется вместо тетрагидрата нитрата скандия, и стабилизированный щелочью золь оксида алюминия используется вместо стабилизированного щелочью золя оксида циркония. Затем платину связывают на полученных частицах металлоксидного носителя катализатора таким же образом, как в примере 1, так что происходит нанесение платины на частицы металлоксидного носителя катализатора.
Пример 10
В примере 10 частицы металлоксидного носителя катализатора, каждая из которых имеет центральную часть, которая состоит, главным образом, из оксида алюминия, и наружную оболочечную часть, которая состоит, главным образом, из оксидов лантана, получают по методике, которая является такой же, как методика примера 1, за исключением того, что гексагидрат нитрата лантана используется вместо тетрагидрата нитрата скандия, и стабилизированный щелочью золь оксида алюминия используется вместо стабилизированного щелочью золя оксида циркония. Затем платину связывают на полученных частицах металлоксидного носителя катализатора таким же образом, как в примере 1, так что происходит нанесение платины на частицы металлоксидного носителя катализатора.
Сравнительный пример 1
В сравнительном примере 1 частицы металлоксидного носителя катализатора, каждая из которых имеет центральную часть, которая состоит, главным образом, из оксида циркония, и наружную оболочечную часть, которая состоит, главным образом, из оксида церия, получают по методике, которая является такой же, как методика примера 1, за исключением того, что нитрат диаммонийцерия используется вместо тетрагидрата нитрата скандия. Затем платину связывают на полученных частицах металлоксидного носителя катализатора таким же образом, как в примере 1, так что происходит нанесение платины на частицы металлоксидного носителя катализатора.
Сравнительный пример 2
В сравнительном примере 2 получают частицы металлоксидного носителя катализатора, состоящие из твердого раствора оксида церия-оксида циркония, и платину затем связывают описанным ниже образом.
Нитрат диаммонийцерия и оксинитрат циркония вводят в дистиллированную воду и затем дистиллированную воду перемешивают, так что введенные нитрат диаммонийцерия и оксинитрат циркония растворяются в ней. Количества введенных нитрата диаммонийцерия и оксинитрата циркония являются такими, что частицы металлоксидного носителя катализатора имеют такой же состав, как частицы металлоксидного носителя катализатора в сравнительном примере 1. Затем введением 28% аммиачной воды регулируют рН смешанного раствора для осуществления осаждения. Затем смешанный раствор сушат при 120°C с удалением из него воды и затем прокаливают при 600°C в течение 5 ч. Продукт, полученный в результате прокаливания, затем измельчают в ступке. Таким образом получают частицы металлоксидного носителя катализатора согласно сравнительному примеру 2. Затем платину связывают на полученных частицах металлоксидного носителя катализатора таким же образом, как в примере 1, так что происходит нанесение платины на частицы металлоксидного носителя катализатора.
Сравнительный пример 3
В сравнительном примере 3 получают частицы металлоксидного носителя катализатора, состоящие только из оксида алюминия, и платину затем связывают описанным ниже образом.
28% аммиачную воду добавляют к 10 мас.% стабилизированному щелочью золю оксида алюминия с доведением рН до 9. Указанный смешанный раствор сушат при 120°C с удалением из него воды и затем прокаливают при 600°C в течение 5 ч. Продукт, полученный в результате прокаливания, затем измельчают в ступке. Таким образом получают частицы металлоксидного носителя катализатора, состоящие только из оксида алюминия. Затем платину связывают на полученных частицах металлоксидного носителя катализатора таким же образом, как в примере 1, так что происходит нанесение платины на частицы металлоксидного носителя катализатора.
Сравнительный пример 4
В сравнительном примере 4 частицы металлоксидного носителя катализатора, состоящие только из оксида циркония, получают по методике, аналогичной методике сравнительного примера 3, за исключением того, что стабилизированный щелочью золь оксида циркония используют вместо стабилизированного щелочью золя оксида алюминия. Затем платину связывают на полученных частицах металлоксидного носителя катализатора таким же образом, как в примере 1, так что происходит нанесение платины на частицы металлоксидного носителя катализатора.
Сравнительный пример 5
В сравнительном примере 5 получают частицы металлоксидного носителя катализатора, состоящие только из оксидов скандия, и платину затем связывают описанным ниже образом.
Тетрагидрат нитрата скандия вводят в дистиллированную воду, которая в шесть раз больше по массе, чем введенный тетрагидрат нитрата скандия, и затем 28% аммиачную воду добавляют к полученному раствору с доведением его рН до 9. Раствор затем сушат при 120°C с удалением из него воды и затем прокаливают при 600°C в течение 5 ч. Продукт, полученный в результате прокаливания, затем измельчают в ступке. Таким образом получают частицы металлоксидного носителя катализатора, состоящие только из оксидов скандия. Затем платину связывают на полученных частицах металлоксидного носителя катализатора таким же образом, как в примере 1, так что происходит нанесение платины на частицы металлоксидного носителя катализатора.
Сравнительный пример 6
В сравнительном примере 6 частицы металлоксидного носителя катализатора, состоящие только из оксидов иттрия, получают по методике, аналогичной методике сравнительного примера 5, за исключением того, что гексагидрат нитрата иттрия используют вместо тетрагидрата нитрата скандия. Затем платину связывают на полученных частицах металлоксидного носителя катализатора таким же образом, как в примере 1, так что происходит нанесение платины на частицы металлоксидного носителя катализатора.
Сравнительный пример 7
В сравнительном примере 7 частицы металлоксидного носителя катализатора, состоящие только из оксидов неодима, получают по методике, аналогичной методике сравнительного примера 5, за исключением того, что гексагидрат оксидов неодима используют вместо тетрагидрата нитрата скандия. Затем платину связывают на полученных частицах металлоксидного носителя катализатора таким же образом, как в примере 1, так что происходит нанесение платины на частицы металлоксидного носителя катализатора.
Сравнительный пример 8
В сравнительном примере 8 частицы металлоксидного носителя катализатора, состоящие только из оксидов празеодима, получают по методике, аналогичной методике сравнительного примера 5, за исключением того, что гексагидрат оксидов празеодима используют вместо тетрагидрата нитрата скандия. Затем платину связывают на полученных частицах металлоксидного носителя катализатора таким же образом, как в примере 1, так что происходит нанесение платины на частицы металлоксидного носителя катализатора.
Сравнительный пример 9
В сравнительном примере 9 частицы металлоксидного носителя катализатора, состоящие только из оксидов лантана, получают по методике, аналогичной методике сравнительного примера 5, за исключением того, что гексагидрат нитрата лантана используют вместо тетрагидрата нитрата скандия. Затем платину связывают на полученных частицах металлоксидного носителя катализатора таким же образом, как в примере 1, так что происходит нанесение платины на частицы металлоксидного носителя катализатора.
Определяют изоэлектрические точки частиц металлоксидного носителя катализатора в соответствующих примерах и сравнительных примерах. В таблице 1 представлены результаты определения. Для сравнения в таблице 1 также представлены изоэлектрическая точка оксидов, образующих наружную оболочечную часть, и изоэлектрическая точка оксидов, образующих центральную часть, в частицах металлоксидного носителя катализатора, полученных в соответствующих примерах и сравнительных примерах.
Таблица 1 |
Изоэлектрическая точка частиц металлоксидного носителя катализатора |
 |
Изоэлектрическая точка (рН) |
Простое вещество |
Наружная оболочечная часть |
Оксиды наружной оболочечной части |
Оксиды центральной части |
Наружная оболочечная часть и центральная часть |
Пример 1 |
Pt/Sc2O3 (наружная оболочечная часть) и ZrO2 (центральная часть) |
9,2 |
5,3 |
9,3 |
Пример 2 |
Pt/Y2O3 (наружная оболочечная часть) и ZrO2 (центральная часть) |
9,3 |
8,9 |
Пример 3 |
Pt/Nd2O3 (наружная оболочечная часть) и ZrO2 (центральная часть) |
10,1 |
 |
10,0 |
Пример 4 |
Pt/Pr6O11 (наружная оболочечная часть) и ZrO2 (центральная часть) |
9,8 |
10,4 |
Пример 5 |
Pt/La2O3 (наружная оболочечная часть) и ZrO2 (центральная часть) |
10,5 |
9,9 |
Пример 6 |
Pt/Sc2O3 (наружная оболочечная часть) и Al2O3 (центральная часть) |
9,2 |
6,9 |
9,5 |
Пример 7 |
Pt/Y2O3 (наружная оболочечная часть) и Al2O3 (центральная часть) |
9,3 |
9,1 |
Пример 8 |
Pt/Nd2O3 (наружная оболочечная часть) и Al2O3 (центральная часть) |
10,1 |
10,2 |
Пример 9 |
Pt/Pr6O11 (наружная оболочечная часть) и Al2O3 (центральная часть) |
9,8 |
9,7 |
Пример 10 |
Pt/La2O3 (наружная оболочечная часть) и Al2O3 (центральная часть) |
10,5 |
10,7 |
Сравнительный пример 1 |
Pt/CeO2 (наружная оболочечная часть) и ZrO2 (центральная часть) |
9,6 |
5,3 |
9,1 |
Сравнительный пример 2 |
Pt/(Zr, Ce)O2 |
– |
8,3 |
Сравнительный пример 3 |
Al2O3 |
6,9 |
– |
Сравнительный пример 4 |
ZrO2 |
5,3 |
– |
Сравнительный пример 5 |
Sc2O3 |
9,2 |
– |
Сравнительный пример 6 |
Y2O3 |
9,3 |
– |
Сравнительный пример 7 |
Nd2O3 |
10,1 |
– |
Сравнительный пример 8 |
Pr6O11 |
9,8 |
– |
Сравнительный пример 9 |
La2O3 |
10,5 |
– |
Как видно из таблицы 1, в соответствующих примерах и в сравнительном примере 1 изоэлектрическая точка каждой частицы металлоксидного носителя катализатора является почти равной изоэлектрической точке оксидов, образующих наружную оболочечную часть частицы металлоксидного носителя катализатора. Т.е. в таблице 1 показано, что в соответствующих примерах и в сравнительном примере 1 каждая частица металлоксидного носителя катализатора имеет центральную часть, которая состоит, главным образом, из оксида циркония или оксида алюминия, и наружную оболочечную часть, которая состоит, главным образом, из оксидов скандия, оксидов иттрия и т.д.
Катализаторы, полученные в соответствующих примерах и в сравнительном примере 1, испытывают в виде кубических образцов размером 1 мм × 1 мм × 1 мм для испытаний соответствующих катализаторов.
При исследовании каждый катализатор помещают для испытания в условия, когда каждый катализатор поочередно выдерживается в обогащенном газе (монооксид углерода (2 об.%) + азот) и в обедненном газе (кислород (2 об.%) + азот) при 1000°C в течение 5 ч. В процессе этого подаваемый газ переключается между обогащенным газом и обедненным газом каждую минуту, скорость потока каждого газа составляет 5 л/мин, и температура газа составляет 1000°C.
Затем в качестве способа редиспергирования катализатор помещают в электрическую печь и нагревают при 600°C в течение 2 ч в воздушной атмосфере в ней.
Затем с использованием импульсного метода адсорбции монооксида углерода измеряют при -80°C диаметр платиновых частиц, которые еще не были редиспергированы после испытания вышеуказанного условия, и диаметр платиновых частиц, которые были редиспергированы после испытания вышеуказанного условия. Степень редиспергирования рассчитывают с использованием следующего уравнения:
степень редиспергирования (%) = {1-(диаметр редиспергированной платиновой частицы)/(диаметр нередиспергированной платиновой частицы)} × 100
Когда степень диспергирования является относительно большой, это показывает, что платина хорошо редиспергирована способом редиспергирования. Результаты представлены в таблице 2 и на фиг.3.
Таблица 2 |
Результаты испытаний |
 |
Удельная площадь поверхности носителя после испытания условия (м2/г) |
Диаметр Pt-частиц (нм) |
Степень регенерации Pt-частиц (%) |
перед редисперги-рованием |
после редисперги-рования |
Пример 1 |
Pt/Sc2O3 (наружная оболочечная часть) и ZrO2 (центральная часть) |
19 |
68 |
25 |
63 |
Пример 2 |
Pt/Y2O3 (наружная оболочечная часть) и ZrO2 (центральная часть) |
31 |
46 |
14 |
69 |
Пример 3 |
Pt/Nd2O3 (наружная оболочечная часть) и ZrO2 (центральная часть) |
25 |
57 |
18 |
68 |
Пример 4 |
Pt/Pr6O11 (наружная оболочечная часть) и ZrO2 (центральная часть) |
21 |
61 |
23 |
63 |
Пример 5 |
Pt/La2O3 (наружная оболочечная часть) и ZrO2 (центральная часть) |
21 |
63 |
27 |
57 |
Пример 6 |
Pt/Sc2O3 (наружная оболочечная часть) и Al2O3 (центральная часть) |
32 |
48 |
15 |
69 |
Пример 7 |
Pt/Y2O3 (наружная оболочечная часть) и Al2O3 (центральная часть) |
43 |
42 |
4 |
90 |
Пример 8 |
Pt/Nd2O3 (наружная оболочечная часть) и Al2O3 (центральная часть) |
45 |
43 |
5 |
88 |
Пример 9 |
Pt/Pr6O11 (наружная оболочечная часть) и Al2O3 (центральная часть) |
41 |
45 |
6 |
87 |
Пример 10 |
Pt/La2O3 (наружная оболочечная часть) и Al2O3 (центральная часть) |
35 |
49 |
16 |
67 |
Сравнительный пример 1 |
Pt/CeO2 (наружная оболочечная часть) и ZrO2 (центральная часть) |
25 |
43 |
24 |
44 |
Сравнительный пример 2 |
Pt/(Zr, Ce)O2 |
38 |
51 |
41 |
32 |
Сравнительный пример 3 |
Al2O3 |
67,0 |
– |
– |
– |
Сравнительный пример 4 |
ZrO2 |
13,0 |
– |
– |
– |
Сравнительный пример 5 |
Sc2O3 |
11,2 |
– |
– |
– |
Сравнительный пример 6 |
Y2O3 |
11,1 |
– |
– |
– |
Сравнительный пример 7 |
Nd2O3 |
3,7 |
– |
– |
– |
Сравнительный пример 8 |
Pr6O11 |
5,1 |
– |
– |
– |
Сравнительный пример 9 |
La2O3 |
5,3 |
– |
– |
– |
Из таблицы 2 видно, что удельная площадь поверхности катализатора очистки отходящего газа каждого примера является значительно большей, чем в сравнительных примерах 5-9. Также из таблицы 2 и фиг.3 видно, что степень регенерации платиновых частиц, достигнутая в соответствующих примерах, является значительно более высокой, чем в сравнительных примерах 1 и 2.
Формула изобретения
1. Частица металлоксидного носителя катализатора, отличающаяся тем, что она имеет центральную часть и наружную оболочечную часть, в которой центральная часть и наружная оболочечная часть, каждая, содержит первый оксид металла и второй оксид металла, центральная часть и наружная оболочечная часть отличаются по составу друг от друга, мольная фракция металла первого оксида металла является более высокой в центральной части, чем в наружной оболочечной части, мольная фракция металла второго оксида металла является более высокой в наружной оболочечной части, чем в центральной части, и первый оксид металла представляет оксид алюминия или оксид циркония, а второй оксид металла выбран из группы, состоящей из оксидов неодима, празеодима, лантана, скандия и иттрия.
2. Частица металлоксидного носителя катализатора по п.1, в которой центральная часть содержит менее 1-50 мол.% второго оксида металла, выбранного из группы, состоящей из оксида неодима, оксида празеодима, оксида лантана, оксида скандия и оксида иттрия.
3. Частица металлоксидного носителя катализатора по п.1 или 2, в которой удельная площадь поверхности частицы металлоксидного носителя катализатора составляет более 15 м2/г после того, как частица металлоксидного носителя катализатора поочередно выдерживается в обогащенном газе (монооксид углерода (2 об.%)+азот) и в обедненном газе (кислород (2 об.%)+азот) при 1000°С в течение 5 ч, так что газ, в котором выдерживается металлоксидный носитель катализатора, переключается между обогащенным газом и обедненным газом каждую минуту.
4. Частица металлоксидного носителя катализатора по п.1, в которой первый оксид металла представляет собой оксид алюминия, второй оксид металла выбран из группы, состоящей из оксида неодима, оксида празеодима и оксида иттрия, и удельная площадь поверхности частицы металлоксидного носителя катализатора составляет более 40 м2/г после того, как частица металлоксидного носителя катализатора поочередно выдерживается в обогащенном газе (монооксид углерода (2 об.%)+азот) и в обедненном газе (кислород (2 об.%)+азот) при 1000°С в течение 5 ч, так что газ, в котором выдерживается металлоксидный носитель катализатора, переключается между обогащенным газом и обедненным газом каждую минуту.
5. Частица металлоксидного носителя катализатора по п.1 или 2, в которой состав на границе раздела между центральной частью и наружной оболочечной частью постепенно изменяется.
6. Частица металлоксидного носителя катализатора по п.1 или 2, в которой граница раздела между центральной частью и наружной оболочечной частью состоит из смеси первого оксида металла и второго оксида металла.
7. Катализатор очистки отходящего газа, содержащий частицу металлоксидного носителя катализатора по любому из пп.1-6 и платину, нанесенную на частицу металлоксидного носителя катализатора.
8. Способ регенерации катализатора очистки отходящего газа по п.7, включающий нагревание катализатора очистки отходящего газа при температуре 500°С или выше в окислительной атмосфере, которая содержит кислород.
9. Способ по п.8, дополнительно включающий восстановление платины после того, как катализатор очистки отходящего газа был нагрет в кислородсодержащей окислительной атмосфере.
10. Способ получения частицы металлоксидного носителя катализатора, содержащей центральную часть и наружную оболочечную часть, где каждая содержит первый оксид металла и второй оксид металла, и центральная часть и наружная оболочечная часть отличаются по составу друг от друга, отличающийся тем, что он включает получение раствора материала, содержащего, по меньшей мере, коллоидные частицы первого оксида металла и металлические соли второго оксида металла, где первый оксид металла представляет оксид алюминия или оксид циркония, а второй оксид металла выбран из группы, состоящей из оксидов неодима, празеодима, лантана, скандия и иттрия; доведение рН раствора материала близко к изоэлектрической точке коллоидных частиц первого оксида металла с тем, чтобы коагулировать коллоидные частицы первого оксида металла; увеличение рН раствора материала с тем, чтобы осадить коллоидные частицы второго оксида металла из металлических солей и коагулировать коллоидные частицы второго оксида металла вокруг коагулированных коллоидных частиц первого оксида металла, причем изоэлектрическая точка коллоидных частиц второго оксида металла является более высокой, чем изоэлектрическая точка коллоидных частиц первого оксида металла; и сушку и прокаливание коагулированного продукта.
РИСУНКИ
|
|