|
(21), (22) Заявка: 2008126157/28, 27.06.2008
(24) Дата начала отсчета срока действия патента:
27.06.2008
(43) Дата публикации заявки: 10.01.2010
(46) Опубликовано: 27.04.2010
(56) Список документов, цитированных в отчете о поиске:
Адрес для переписки:
119991, Москва, Ленинский пр-кт, 49, Институт металлургии и материаловедения им. А.А. Байкова РАН
|
(72) Автор(ы):
Ермишкин Вячеслав Александрович (RU), Лепешкин Юрий Дмитриевич (RU), Мурат Дмитрий Павлович (RU), Овчинников Игорь Николаевич (RU)
(73) Патентообладатель(и):
Институт металлургии и материаловедения им. А.А. Байкова Российской академии наук (РАН) (Государственное учреждение) (RU)
|
(54) СПОСОБ ФОТОМЕТРИЧЕСКОЙ ДИАГНОСТИКИ СТРУКТУРНОГО СОСТОЯНИЯ МАТЕРИАЛОВ ПО ДАННЫМ АНАЛИЗА ЦИФРОВОГО КОДИРОВАННОГО ИЗОБРАЖЕНИЯ ИХ ПОВЕРХНОСТИ
(57) Реферат:
Изобретение относится к способам неразрушающего контроля и диагностики технического состояния объектов из конденсированных материалов по данным фотометрического анализа структурных изображений (ФАСИ) их поверхности, зафиксированных в цифровом коде и анализируемых на персональном компьютере. Способ заключается в том, что фиксируют цифровые кодированные изображения фрагментов поверхности материала до и после воздействия на материал, вызвавшего его локальное разрушение, и получают для каждого изображения спектр яркости отражения. Степень деградации материала на данном фрагменте определяют как отношение изменения спектральной плотности яркости изображения данного фрагмента к максимальному ее изменению для изображения фрагмента с предельной деградацией, соответствующей состоянию разрушения, и по степени деградации определяют значение параметра, характеризующего эксплуатационную пригодность материала. Техническим результатом является обеспечение возможности количественной оценки структурного состояния и степени эксплуатационной пригодности материалов. 3 з.п. ф-лы, 12 ил., 1 табл.
Предлагаемое изобретение относится к способам неразрушающего контроля и диагностики технического состояния объектов из конденсированных материалов по данным фотометрического анализа структурных изображений (ФАСИ) их поверхности, зафиксированных в цифровом коде и анализируемых на персональном компьютере.
Способ реализован в виде программно-аналитического комплекса в составе: 1) средства визуализации изображения поверхности материала (сканер, цифровая фотокамера, световые и электронные микроскопы; 2) средства для контролируемого внешнего физического или химического воздействия на материал (испытательная машина, высокотемпературная печь, излучающий источник); 3) персональный компьютер с устройствами для вывода цифровой и графической информации. Все элементы комплекса являются стандартным серийным многоцелевым исследовательским оборудованием. Техническая возможность реализации настоящего изобретения состоит в представлении структурных изображений в цифровом коде, что дает возможность анализировать изображения математическими средствами в автоматизированном режиме с помощью специальных компьютерных программ, входящих в состав программно-аналитического комплекса. Цифровое кодирование осуществляется путем присвоения элементарной ячейке изображения (пикселю) определенной цифры, выражающей степень ее черноты по выбранной заранее шкале градаций последовательности перехода цвета от белого к черному.
Физическая основа предлагаемого способа заключается в совместном анализе структурных изображений поверхности исследуемых объектов и спектров отражения видимого света, отснятых с них до и после внешнего воздействия на материал, позволяющего установить взаимосвязь параметров структурного состояния на исследуемой поверхности и характеристик спектра отражения с интенсивностью и продолжительностью внешних воздействий, аналитическая или графическая форма представления которой рассматривается как градуировочная зависимость, переводящая локальные структурные параметры материалов в соответствующие им параметры физического состояния. Способность поверхности материалов отражать видимый свет всецело зависит от химического состава материала поверхностных слоев исследуемого объекта и степени его шероховатости. Внешние физические или химические воздействия способны изменять оба эти фактора, тем самым вызывая структурные изменения плотности отраженного света до и после внешних воздействий на материал, измеренной в выбранном диапазоне яркости непосредственно на спектре яркости отражения. Последний представляет собой график, построенный компьютером по результатам сканирования исследуемой поверхности образца в координатах « спектральная плотность яркости отражения – соответствующая ей яркость отражения». Спектральная плотность отражения заданной яркости характеризуется отношением числа пикселов в заданном диапазоне яркости на исследуемом фрагменте поверхности объекта к общему числу пикселов, на которое разбивается исследуемая поверхность. В качестве количественной меры структурных изменений, происшедших на поверхности исследуемого объекта, нами было выбрано отношение разности спектральных плотностей яркости отражения с данного фрагмента поверхности к разности спектральных плотностей отражения фрагмента, по которому произошло разрушение образца. Именно на нем значение этой разности достигает максимального значения. В случае исследования сопротивления усталостному разрушению эта мера характеризует степень усталостной поврежденности поверхности материала. Проведенные эксперименты показали высокую чувствительность спектральной плотности яркости отражения в различных диапазонах спектра интенсивности к характеристикам внешних воздействий. В частности, при механических воздействиях в результате скольжения и выхода дислокации на поверхность заметно изменяется ее шероховатость от изначально более гладкой в сторону большей диффузности.
На участках поверхности с преобладанием впадин доминируют процессы поглощения видимого света, тогда как на выступах интенсифицируются процессы его отражения. В настоящее время, несмотря на ясное понимание взаимосвязи структурного и физического состояний материалов, сложилась практика их раздельного исследования. При этом образцы для структурных исследований микроскопические по размерам, а для оценки физических свойств, как правило, макроскопические. Характеристики физического состояния изучаются в динамических условиях, т.е. в процессах непосредственного воздействия физических полей или агрессивных химических сред на материалы, а параметры структурного состояния исследуются в статических условиях. Характеристики физического состояния интегральные, т.е. относятся ко всему образцу в целом, а параметры структурного состояния локальны. Их измерения осуществляются неодновременно и на разном оборудовании. В процессе приготовления микрообъекта для структурных исследований из макроскопического образца в его структуру вносятся дополнительные искажения, затрудняющие корректную оценку структурных параметров. Между тем, по своему смыслу физические характеристики представляют собой количественную меру структурой реакции материала на внешнее энергетическое воздействие. Единство типа образцов, экспериментального оборудования для изучения физического и структурного состояний соблюдается только в условиях экспериментов in situ, проводимых в колоннах электронных и световых микроскопов. В предлагаемом способе исследования структурного и физического состояний материалов совмещены и выполняются на одних и тех же образцах. Комплексный характер выполнения структурных и физических исследований позволил получать оценки физических характеристик по данным структурных исследований с применением ФАСИ, что невозможно при использовании стандартных способов исследования. В последние годы появились компьютерные многофункциональные анализаторы изображений (например AI-32), в которых сочетаются возможности прежних узкоспециализированных приборов для структурных исследований квантимета, денситометра, системы «Перкалор», однако ни один из них не в состоянии ни оценивать физические характеристики материалов, ни прогнозировать долговечность материала по данным анализа структурных изображений.
Предлагаемое изобретение имеет широкое поле для практического использования. В частности, оно может применяться: 1) в качестве средства технической диагностики для оценки состояния объектов промышленного, транспортного и энергетического назначения; 2) в качестве прибора, использующего в качестве датчиков ресурса материал конструкции в ее наиболее нагруженных местах; 3) в качестве средства для оценки качества проведения технологических операций; 4) для оценки остаточного и проектного ресурса промышленного оборудования и металлоконструкций; 5) для определения сроков годности пищевых продуктов, лекарств и медицинских препаратов; 6) для оценки изменений качества материалов в результате различного рода технологических обработок; 7) для количественной оценки эффективности внешних воздействий в смысле их способности повреждать конструкционные материалы.
Процедура фотометрической диагностики технического состояния материала исследуемого объекта включает в себя этапы: 1) предварительных градуировочных экспериментов, выполняемых на образцах; 2) фотометрическая диагностика наиболее опасных в смысле возможности преждевременного разрушения местах машин, оборудования и металлоконструкций. Способ осуществления фотометрического анализа структурных изображений на этих этапах идентичен и потому его можно рассмотреть применительно только к образцам. Образцы для построения градуировочных зависимостей должны обеспечить возможность формирования в них неоднородного структурного состояния в результате внешнего воздействия исследуемой природы с плавным или ступенчатым изменением его интенсивности по длине образца. Предварительно исследуемые фрагменты поверхности образца фотографируются с требуемым оптическим разрешением с использованием соответствующих средств их визуализации. Далее образец подвергается внешнему воздействию заданной природы с фиксацией кинетики изменения его интенсивности по стандартным процедурам соответствующих испытаний образцов с доведением его до предельного состояния (потеря устойчивости, пластические деформации, образование трещин, потеря несущей способности, образование каверн предельного размера или глубины и т.д.). Условия проведения экспериментов должны обеспечить измерения интенсивности внешних воздействий в пределах исследуемых фрагментов, которые предварительно фотографировались. Производится повторное фотографирование ранее отснятых фрагментов исследуемых поверхностей при соблюдении тех же условий съемки, введение в компьютер фотоизображений отснятых фрагментов поверхности до и после внешнего воздействия наряду с данными о режиме внешнего воздействия, вызвавшего изменения структурного состояния поверхности с последующим совместным анализом данных фотометрических измерений на поверхности отснятых фрагментов и данных о локальной интенсивности внешних воздействий на каждый из исследуемых фрагментов по специальным измерительным и аналитическим программам, входящих в комплекс ФАСИ.
Пример 1
В качестве конкретного примера реализации фотометрической диагностики технического состояния материала рассмотрим усталостную повреждаемость материалов. В настоящее время стандартные испытания на усталость проводятся по ГОСТ 25502-79 и их результаты представляются в виде кривой усталости в координатах « -lgN», где – амплитуда напряжений, N – число циклов до разрушения. Для построения кривой усталости для одного структурного состояния материала требуется 15-50 образцов, третья часть которых доводится до 106-107 циклов нагружения. При построении кривой усталости по предлагаемому способу на основе ФАСИ роль образцов играет поверхность каждого отдельного фрагмента. В экспериментах использовались плоские образцы малоуглеродистой стали 08КП с длиной рабочей части 140 мм шириной 10 мм и толщиной 0,77 мм. При длине фрагмента 10 мм с учетом возможности ФАСИ измерений на обоих поверхностях каждого фрагмента испытания одного образца эквивалентно испытанию 28 образцов. Однако в виду того, что фрагменты, нагруженные циклическими напряжениями с амплитудой ниже предела усталости материала, не дают информации для построения кривой усталости, эквивалент образцов снижается до 16-20. Для испытаний был использован электродинамический вибратор типа Д-0,5. Испытания проводились в режиме резонансного возбуждения колебаний образцов с частотой 27 Гц, совпадающей с частотой первой гармоники собственных колебаний для используемого типоразмера образцов. Поверхность каждого из 14 фрагментов на обоих сторонах рабочей части образца фотографировалась цифровой фотокамерой до и после испытания на усталость и для каждого из них получали спектр яркости отражения в координатах «спектральная плотность яркости отражения – относительная яркость (интенсивность) отражения», шкала последней разбивалась на 256 градаций. На фиг.1 в качестве примера показаны изображения фрагмента поверхности усталостного образца из стали 08КП до и после испытаний и соответствующие им спектры яркости отражения видимого света от их поверхности.
На фиг.1 видно, что в результате воздействия циклических нагрузок в правой части спектра, соответствующей повышенному поглощению света, спектральная плотность яркости отражения увеличилась, а область повышенной яркости отражения практически исчезла. Для оценки степени поврежденности структуры материала в результате усталостных испытаний нами была введена количественная мера поврежденности материала, определяемая через спектральные плотности в интервале спектра с повышенным поглощением в виде:

где aid – средняя спектральная плотность яркости отражения i-го фрагмента образца в выбранном нами интервале спектра с повышенной поглощательной способностью после разрушения образца при Nr циклов испытаний; admax – то же, но для фрагмента, по которому произошло разрушение образца; aod – то же, но усредненная по поверхности всего образца до начала испытаний.
По своему физическому смыслу введенная нами количественная мера поврежденности материала является функцией поврежденности, удовлетворяющая следующим начальным и конечным условиям:

Ранее такую же функцию для оценки усталостной поврежденности материалов ввел Майнер [Miner M.A. Cumulative damage in fatigue. Jor. of Appl. Mech. v.l2, 9, P.159-164], выразив ее через отношение числа циклов текущих и до разрушения:
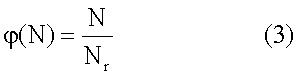
На фиг.2 показано изменение отражающей способности образца (aid) в функции локальных амплитуд циклических напряжений.
Из сопромата [Феодосьев В.И. Сопротивление материалов. М.: Из-во МГТУ им. Н.Э.Баумана. 1999. 589 с.] известно, что распределение напряжений в изогнутом консольно закрепленном призматическом стержне распределение напряжений в статическом приближении описывается формулой:
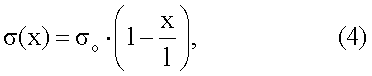
где о – напряжение в заделке образца, l – длина образца, x- расстояние от заделки образца до сечения, в котором определяется напряжение.
Приравнивая формулу, выражающую поврежденность образца, через характеристики спектра яркости отражения (1) и через параметры режима испытания (3) и разрешив полученный результат относительно Nr, получаем формулу для вычисления числа циклов до разрушения для амплитуды напряжений (х):
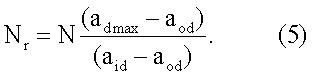
Вычислив по формулам (4) и (5) значения амплитуд напряжений и соответствующих долговечностей материала, получаем два массива данных: (х): и Nr достаточных для построения кривой усталости в координатах « -lg (Nr)». В работах [Новиков И.И., Ермишкин В.А. Физическая механика реальных материалов. М.: Наука. 2004. 323 с. и Овчинников И.Н. Виброиспытания, диагностика и прогнозирование усталостного разрушения. М.: МГТУ им.Н.Э.Баумана. 2004. 128 с.] было показано, что кривые усталости хорошо аппроксимируются уравнением вида:
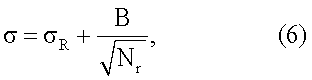
где R – предел усталости, В – константа, определяющая зависимую от числа циклов часть сопротивления усталостному разрушению.
Статистическая обработка данных ФАСИ, использованных для построения кривой усталости после их линеаризации в координатах по методу наименьших квадратов определяем значения параметров уравнения (6):
R и В. После подстановки их в уравнение (6) вычисляем аппроксимирующую экспериментальные данные кривую усталости. Фиг.3 иллюстрирует изложенную выше процедуру построения усталостной кривой для стали 08КП.
На фиг.3 изображена кривая усталости стали 08КП ( – данные ФАСИ измерений на нижней поверхности образца, – данные стандартных усталостных испытаний, – данные ФАСИ измерений на верхней поверхности образца). На основе описанного алгоритма построения кривой усталости разработано программное обеспечение, выполняющее все процедуры требуемые для анализа, вычисления и построения кривой усталости, выполнять в автоматическом режиме.
Пример 2
Разработанный способ фотометрической диагностики структурной поврежденности материалов открывает возможность количественной оценки влияния различных режимов технологических обработок на их свойства. В качестве примера приведем изучение влияния нагрева на изменение структурной однородности авиационного стекла марки ТП. На фиг.4 представлены изображения (а, б) и спектры яркости отражения от них (в, г) для стекла ТП при Т=20°С (а, в) и при Т=694°С (б, г). Из данных изображений можно видеть эти изменения в результате нагрева до Т=694°С, а в таблице приведены данные об изменении отражающей способности стекла в каждом из диапазонов спектра яркости отражения при нагреве в интервале температур 20-694°С.
Т °С |
Кр. |
Син. |
Зел. |
Жел. |
Мал. |
Чер. |
20 |
0,08861 |
0,1217 |
0,3865 |
0,2850 |
0.2598 |
0,1417 |
200 |
0,1408 |
0,00258 |
0,4451 |
0,2239 |
0,1941 |
0,0066 |
694 |
0,4521 |
0,020 |
0,2927 |
0,0710 |
0,02437 |
0,1578 |
Пример 3
Разработанный способ диагностики пригоден и для исследования кинетики структурных перестроек в процессе фазового перехода из аморфного состояния в кристаллическое. На фиг.5. показан график температурной зависимости деградации (поврежденности) аморфного сплава системы Zr-Nb-Cu- (т.е. степень его кристаллизации) при изотермических десятиминутных отжигах в интервале температур 20-400°С. При этом за фрагменты с предельной деградацией были приняты фрагменты поверхности аморфного сплава при его нагреве до максимальной температуры.
Полученные данные оказали существенную помощь для понимания причин снижения прочности этого сплава при нагреве в этом интервале температур. На фиг.6 приведен график температурной зависимости прочности этого сплава в исследуемом температурном интервале.
Разработанный способ диагностики был использован для выбора оптимальных режимов криомеханической обработки стали 08КП, что позволило поднять ее предел прочности с 420 МПа для нормализованного состояния до 1362 МПа для упрочненного.
Формула изобретения
1. Способ фотометрической диагностики структурного состояния материалов по данным анализа цифровых кодированных изображений их поверхности, заключающийся в том, что фиксируют цифровые кодированные изображения фрагментов поверхности материала до и после воздействия на материал, вызвавшего его локальное разрушение, получают для каждого изображения спектр яркости отражения и определяют степень деградации материала на данном фрагменте как отношение изменения спектральной плотности яркости изображения данного фрагмента к максимальному ее изменению для изображения фрагмента с предельной деградацией, соответствующей состоянию разрушения, и по степени деградации определяют значение параметра, характеризующего эксплуатационную пригодность материала.
2. Способ по п.1, отличающийся тем, что при воздействии на материал циклических нагрузок по степени деградации определяют усталость материала.
3. Способ по п.1, отличающийся тем, что при воздействии нагревом на стекло по степени деградации определяют изменение отражающей способности стекла в каждом из диапазонов спектра яркости отражения.
4. Способ по п.1, отличающийся тем, что при воздействии нагревом на аморфный материал по степени его деградации определяют его прочность.
РИСУНКИ
|
|