|
(21), (22) Заявка: 2008126956/06, 14.11.2006
(24) Дата начала отсчета срока действия патента:
14.11.2006
(30) Конвенционный приоритет:
03.12.2005 DE 102005057858.6
(43) Дата публикации заявки: 10.01.2010
(46) Опубликовано: 20.04.2010
(56) Список документов, цитированных в отчете о поиске:
EP 1413769 A1, 28.04.2004. SU 1236180 A1, 07.06.1986. SU 1798536 A1, 28.02.1993. EP 0774583 A1, 21.05.1997. DE 20106608 U1, 30.08.2001.
(85) Дата перевода заявки PCT на национальную фазу:
03.07.2008
(86) Заявка PCT:
EP 2006/010875 20061114
(87) Публикация PCT:
WO 2007/062742 20070607
Адрес для переписки:
103735, Москва, ул. Ильинка, 5/2, “Союзпатент”, А.А.Силаевой
|
(72) Автор(ы):
АДЛЕР Андреас (DE)
(73) Патентообладатель(и):
ВИЛО АГ (DE)
|
(54) КОРПУС НАСОСА С ДВУХТОЧЕЧНЫМ КРЕПЛЕНИЕМ
(57) Реферат:
Изобретение относится к корпусу насоса, имеющего элементы крепления насоса на установочной поверхности. Корпус имеет только два места крепления, которые расположены по одному на фланцах корпуса насоса. Места крепления выполнены или с помощью местного утолщения фланца вдоль установочной поверхности, или посредством среза на фланце. Изобретение направлено на экономию материала для изготовления корпуса и стандартизацию установочного размера, что делает возможной легкую замену одного насоса на другой с любой формой и величиной насосной камеры при малых затратах на монтажные работы. 13 з.п. ф-лы, 7 ил.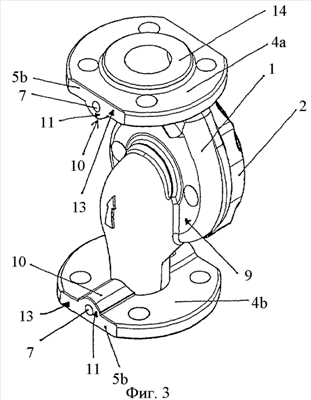
Изобретение относится к корпусу насоса, в частности центробежного насоса, имеющего элементы крепления к установочной поверхности, насосную камеру, в которой размещается вращающееся рабочее колесо, всасывающий патрубок, нагнетательный патрубок, аналогичный всасывающему патрубку, причем всасывающий и нагнетательный патрубки имеют по одному фланцу и при этом фланцы имеют общую ось.
При установке в трубопроводную систему насоса, приводимого в действие электромотором, необходима фиксация корпуса насоса на установочной поверхности, например на стене, опоре или раме каркаса. Эта необходимость возникает не только из-за того, что насос без закрепления собственным весом сильно нагружал бы помимо электромотора привода также трубы, присоединенные к насосу, и соответствующие элементы подсоединения труб к насосу. Более того, в центробежном насосе это может привести к вибрациям, которые через корпус насоса передаются на трубопроводную систему, если корпус насоса недостаточно зафиксирован в неподвижном положении.
Известно, что для крепления корпуса насоса на нем предусматриваются, по меньшей мере, минимум три места крепления, которыми корпус насоса прилегает к установочной поверхности и где используются элементы крепления, фиксирующие корпус насоса на установочной поверхности. При этом обычно, для достижения максимально возможной устойчивости, точки крепления следует располагать таким образом, чтобы они образовывали вершины треугольника. Однако расположение мест крепления различается у разных насосов, поэтому замена насоса на однотипный насос или замена на насос другого типа невозможна без значительных затрат на монтажные работы. В целом, для каждого типа насоса необходимы специальные установочные размеры и особое расположение мест крепления на установочной поверхности.
Обычно места крепления располагаются на корпусе насоса на насосной камере, причем ввиду того, что размеры и конструктивное исполнение насосной камеры различаются в зависимости от производительности насоса, приводимого в действие электромотором, различается и расположение мест крепления в зависимости от габаритов и производительности насоса. Известно также расположение мест крепления на горловине патрубка и/или дополнительного места крепления – на стороне фланца, обращенной к насосной камере, для придания статической устойчивости корпусу насоса. Число, место расположения и расстояние между местами крепления зависят от конструктивного оформления, типа, компоновки и габаритов насоса. Кроме того, недостатком подобных насосов, с тремя точками крепления, являются повышенные расходы на монтажные работы по сравнению с насосами только с двумя точками крепления.
На существующем уровне развития техники, для образования мест крепления на корпусе насоса расположены выступы в форме цилиндрических цапф, удаленных на некоторое расстояние от насосной камеры. Цапфы выполняются из прочного материала, что вызывает ненужные затраты на материал для изготовления корпуса. В цапфах, как правило, выполняются гладкие или резьбовые отверстия M10, в которые устанавливаются элементы крепления.
Задачей данного изобретения является создание корпуса насоса, фиксируемого на установочной поверхности с помощью только двух мест крепления, причем за счет отказа от обычных цапф возможна экономия материала для изготовления корпуса, и причем с помощью соответствующего расположения мест крепления оформляется стандартизированный установочный размер, что делает возможной легкую замену одного насоса на другой насос с любой формой и величиной насосной камеры при малых затратах на монтажные работы. Эта задача решается с помощью отличительных признаков пункта 1 отличительной части формулы изобретения.
В целом, насосы, приводимые в действие электромотором, для установки в существующие трубопроводные системы имеют всасывающий патрубок и аналогичный ему нагнетательный патрубок, на каждом из которых отформован неснимаемый фланец. Фланцы предназначены для установки насоса на соответствующие контрфланцы трубопроводной системы, причем фланцы привинчиваются, например, болтами. Фланцы расположены на одной оси, на основании чего насосы такого типа называются также «насосы прямоточного исполнения». Насосы такого типа изготавливаются цельнокорпусными из литейного сплава, например из стали или чугуна. В дальнейшем под «корпусом насоса» понимается узел насоса, состоящий преимущественно из насосной камеры, всасывающего и нагнетательного патрубков и фланцев, расположенных на них. Такой насос для существующего уровня развития техники изображен на фиг.1.
Согласно изобретению величина уровня затрат на монтажные работы при установке насоса такого типа в существующую трубопроводную систему, а также фиксация насоса на установочной поверхности достигаются благодаря тому, что корпус насоса имеет только два места крепления, прилегающие к установочной поверхности и имеющие элементы крепления, фиксирующие корпус на установочной поверхности.
Согласно изобретению формирование стандартизированных установочных размеров, особенно в сериях насосов различных типов, обеспечивается тем, что места крепления корпуса насоса к установочной поверхности расположены на его фланцах. Таким образом, с помощью унификации межфланцевого расстояния достижима унификация крепления насосов. Размеры фланцев насосов стандартизированы по DIN-EN 1092. Поскольку в насосах одной серии всегда существует одинаковое расстояние между обоими фланцами, то смена насоса проста и не затруднена, так как не нужно предусматривать новые точки крепления на установочной поверхности, и, более того, можно снова использовать точки крепления, использовавшиеся для ранее установленного насоса. Если всегда сохраняется одно межфланцевое расстояние во всех типах насосов у одного изготовителя, то этим достигается наибольшая универсальность замены при смене насосов, и особенно благодаря независимости расположения мест крепления от размеров и обводов насосной камеры и/или патрубков.
Наряду с существенными преимуществами корпуса с двумя точками крепления, описываемого в изобретении, а именно: простой установкой, снижением материалоемкости и стандартизацией установочных размеров, теоретически имеется недостаток, выражающийся в том, что корпус насоса, имеющий только две точки крепления на фланцах, получает еще одну степень свободы для своего движения от приводного электромотора, которое могло бы повлечь за собой неустойчивую фиксацию в неподвижном положении (в противоположность 3-точечному креплению), а в свою очередь, привести к повышенной склонности корпуса насоса к вибрациям. Это становится понятным, если посмотреть на корпус насоса сверху, по направлению оси фланцев, причем фланцы прилегают к удерживающей поверхности.
Представим себе плоскость, перпендикулярную установочной поверхности и проходящую через ось фланцев, тогда корпус насоса вместе с электромотором мог бы совершать движение перпендикулярно этой плоскости, то есть относительно ее сторон. Для устранения этого недостатка, который до настоящего времени удерживал технического специалиста от применения только двух мест крепления, на фланцах могут быть выполнены специальные опорные поверхности соответствующей ширины. Дополнительно и/или альтернативно могут применяться усиленные элементы крепления. Например, в месте крепления может выполняться резьбовое отверстие М12, которое оснащается соответствующим элементом крепления и обеспечивает лучшую фиксацию в неподвижном положении, чем при использовании резьбовых отверстий М10.
Исходя из того, что фланцы, по существу, выполняются круглыми, каждый фланец для образования места крепления может иметь, по меньшей мере, один срез, направленный к установочной поверхности, или, по меньшей мере, один выступ, направленный к установочной поверхности. В предпочтительном варианте исполнения установочных поверхностей выступы фланца могут иметь площадки, направленные к установочной поверхности и прилегающие к ней, располагающиеся в плоскости, касательной к боковине соответствующего фланца. Это решение имеет то преимущество, что для изготовления установочной поверхности может применяться минимум литейного сплава. Альтернативно площадка выступа может значительно выступать из боковины фланца таким образом, чтобы она располагалась в плоскости, параллельной плоскости, касательной к боковине соответствующего фланца. Таким образом может подбираться любое расстояние от корпуса насоса до установочной поверхности.
В альтернативном варианте исполнения фланцы также могут иметь срезы, направленные к установочной поверхности и образующие площадки, прилагающие к ней, причем в этом варианте исполнения площадки также располагаются преимущественно в плоскости, параллельной плоскости, касательной к боковине соответствующего фланца. Альтернативно могут выполняться площадки, образованные срезами или выступами также параллельно установочной поверхности, благодаря чему возможны любые виды углового монтажа корпуса насоса относительно установочной поверхности.
Согласно изобретению во фланце в местах крепления для соответствующего базирования элемента крепления может использоваться, по меньшей мере, одно отверстие, в частности резьбовое, расположенное в плоскости фланца. Под плоскостью фланца понимается плоскость, в которой располагается фланец или лежит его диаметр. Отверстие может выполняться резьбовым. При исполнении отверстия гладким, без резьбы, элемент крепления целесообразно разместить и зацементировать в отверстии. Преимуществом наличия резьбового отверстия является отказ от цементирования в нем элемента крепления. Вернее, соответствующий элемент крепления с наружной резьбой может вворачиваться в резьбовое отверстие, с помощью которого корпус насоса может фиксироваться на установочной поверхности. Места крепления могут при этом иметь и большее количество отверстий, например два, благодаря чему, особенно при использовании тяжелых насосов с приводом от электромотора и с фланцами, имеющими большие толщину и диаметр, достигается более высокая устойчивость крепления.
При использовании одного отверстия предпочтительно ориентировать его перпендикулярно к оси фланца, чтобы достичь максимально возможной неподвижности фиксации корпуса насоса с помощью этого отверстия.
Отверстия в каждом фланце предпочтительно выполнять с резьбой M12 и глубиной 20 50 мм, при наличии срезов фланца предпочтительная глубина – 30 мм. За счет этого гарантируется хорошее удержание элемента крепления во фланце.
Для повышения устойчивости крепления фланца на его стороне, обращенной к насосной камере, могут иметься расширения материала, вытянутые от оси фланцев до наружного обвода соответствующего фланца через, по меньшей мере, часть стороны фланца, обращенной к насосной камере, причем эти расширения материала имеют площадку, направленную к установочной поверхности и выполненную таким образом, что она вместе с прилегающей к установочной поверхности площадкой соответствующего выступа или среза фланца образуют единую опорную поверхность.
Для достижения наименьших возможных затрат на материалы для создания расширения материала фланцев, они могут выпукло выгибаться в направлении, параллельном оси фланцев, в сторону насосной камеры. Кроме того, в предпочтительном варианте исполнения выпуклый свод расширения материала выполняется таким образом, что в единую опорную поверхность вписывается окружность, имеющая диаметр 15 35 мм, предпочтительно – 25 мм. Такая форма расширения материала гарантирует, что толщина стенки между отверстием и наружной поверхностью фланца повсюду будет достаточна для получения достаточной устойчивости крепления. Согласно изобретению это достигается преимущественно благодаря тому, что ось отверстия проходит через центр окружности, вписанной в единую опорную поверхность.
Для формирования стандартизированных установочных размеров центр виртуальной вписанной окружности имеет поддающееся определению расстояние от плоскости поверхности фланца, отвернутой от насосной камеры, или от плоскости поверхности уплотнения фланца. В целом, поверхности уплотнения образуют на стороне фланца, отвернутой от насосной камеры, упорядоченные концентрические возвышения, причем ось отверстия располагается на расстоянии 10 20 мм, предпочтительно – 14 16 мм, от плоскости соответствующей поверхности уплотнения или на расстоянии 7 17 мм, предпочтительно – 11 13 мм, от плоскости поверхности фланца, отвернутой от насосной камеры. С определением центра вписанной окружности относительно плоскости поверхности фланца, отвернутой от насосной камеры, задается кривизна выпуклости поверхности расширения материала фланца.
Предпочтительно выбирать ширину площадки, прилегающей к установочной поверхности, или ширину единой опорной поверхности фланца с выступами выбирать в зависимости от габаритов фланца, в частности в зависимости от диаметра фланца. Предпочтительно, если ширина указанных площадок составляет от 30 до 80 мм, в частности 50 мм.
Согласно изобретению для простоты изготовления корпуса насоса выступы и расширения материала составляют единое целое с фланцем. Предпочтительно, если выступы и местные утолщения образуются непосредственно во время процесса отливки корпуса насоса. В соответствии с этим в наиболее предпочтительном варианте выполнения предложенный корпус насоса изготовлен из литьевого сплава, в частности из литейного чугуна.
Другие преимущества и отличительные признаки изобретения можно найти в зависимых пунктах формулы изобретения и в последующем детальном описании со ссылкой на фигуры 1-4.
На чертежах изображено:
фиг.1: корпус насоса с тремя местами крепления (в соответствии с уровнем развития техники);
фиг.2: корпус насоса, описываемый в изобретении, с двумя точками крепления;
фиг.3: объемное изображение корпуса насоса, описываемого в изобретении, со срезанными фланцами;
фиг.4: корпус насоса, изображенного на фиг.3, вид спереди;
фиг.5: вид сверху фланца нагнетательного патрубка с выступом;
фиг.6: вид сверху фланца нагнетательного патрубка с двумя выступами;
фиг.7: фланец всасывающего патрубка с единой опорной поверхностью, вид спереди.
На фиг.1 изображен корпус насоса согласно уровню техники, как уже описано во введении. В общем случае, для формирования мест 17 крепления корпус 1 насоса имеет, по существу, цилиндрические цапфы 18 с коническим сужением в сторону установочной поверхности, а также узкое расширение 19 материала, расположенное на фланце 4а нагнетательного патрубка 16. При этом цапфы 18 выполнены прочными и образуют корпуса для приема элементов крепления, не показанных на чертеже. Крепление корпуса 1 насоса такого типа может производится, например, к стене.
На фиг.2 изображен вариант исполнения корпуса 1 насоса, описываемого в изобретении, причем как на фланце 4а нагнетательного патрубка 16, так и на фланце 4b всасывающего патрубка 15 расположены выступы 6, направленные к установочной поверхности, выполненные как плоская площадка, направленная к установочной поверхности, и образующие соответствующие места 3а, 3b крепления. В варианте исполнения, представленном на фиг.2, выступы 6 выполнены таким образом, что плоские площадки 13 лежат в плоскости, касательной к боковой поверхности соответствующих фланцев 4а, 4b. При этом рекомендуется обратиться к фиг.6, показывающей вид сверху на фланец 4а нагнетательного патрубка 16, где отчетливо представлено, что благодаря расположению площадки 13 в вышеназванной касательной плоскости для ее формирования необходимы два выступа 6, так как в точке контакта касательной плоскости и боковой поверхности фланца 4а отсутствует выступающий материал фланца.
Кроме того, на фиг.2 показано, что оба фланца 4а, 4b имеют расширения 10 материала на своих сторонах, обращенных к насосной камере 9, которые проходят радиально от оси фланцев 8 к внешнему обводу соответствующего фланца по стороне соответствующего фланца 4а, 4b, обращенной к насосной камере 9. Расширения 10 материала располагаются без возможности съема на горловинах нагнетательного 15 и всасывающего 16 патрубков. Расширения 10 материала образуют площадки 11, направленные к установочной поверхности, которые как и площадки 13 выступов 6 выполнены плоскими и образуют вместе с площадками 13 выступов 6 единую опорную поверхность 11+13. Это схематично пояснено на фиг.7. На фиг.2 и фиг.7 хорошо видны своды расширений 10 материала, выпукло выгнутые в направлении, параллельном оси фланцев 8, в сторону насосной камеры 9.
Альтернативный вариант исполнения выступов 6 представлен на фиг.5, где отчетливо выдается выступ 6, располагающийся на боковине фланца 4а таким образом, что плоская площадка 13, направленная к установочной поверхности, лежит в плоскости, параллельной плоскости, касательной к наружной боковине фланца 4а.
Второй вариант исполнения корпуса 1 насоса, описываемого в изобретении, представлен на фиг.3. Места 5а, 5b крепления обоих фланцев 4а, 4b образованы здесь с помощью срезов, которые направлены к установочной поверхности. С помощью срезов 5а, 5b на боковинах фланцев образованы площадки 13, прилегающие к установочной поверхности. Эти площадки 13 вместе с площадками 11 выступов 10, возникающими благодаря срезам 5а, 5b, образуют общую опорную поверхность 11+13, прилегающую к установочной поверхности. На фиг.3 изображен контрфланец электромотора 2, приводящего в действие насос.
На фиг.4 показан вид спереди насоса, описываемого в изобретении и представленного на фиг.3, где хорошо видны опорные площадки 13, образованные срезами 5а, 5b. Выпуклый свод расширения 10 материала выполнен таким образом, что в опорную поверхность 11 расширения 10 материала и опорную поверхность 13, образованную срезами 5а, 5b, по их центру образуемой фигуры может быть вписана окружность 12, имеющая диаметр d. Диаметр d для варианта исполнения, приведенного на фиг.4, составляет 25 мм. Ось отверстия 7 проходит здесь через центр окружности 12, вписанной в единую опорную поверхность 13+11. Выпуклая поверхность расширения 10 материала выполнена здесь таким образом, что часть контура окружности в точности описывает форму наружной поверхности выпуклого свода. Срезы 5а, 5b имеют ширину m, зависящую от диаметра фланца. Величина ширины m определяется удалением срезов 5а, 5b от оси фланцев 8. По правилам проектирования, срезы 5а, 5b должны быть симметричны относительно оси фланцев, то есть фланцы также должны иметь срезы со стороны подключения электромотора, приводящего в действие насос 2, см. фиг.3.
При использовании выступов 6 для формирования мест 3а, 3b крепления нужно выбирать также ширину опорной поверхности 13 соответственно диаметру фланца (фиг.7). Ширина m может составлять 50 мм при диаметре фланца 140 150 мм, 60 мм – при диаметре фланца 165 185 мм или 70 мм – при диаметре фланца 200 220 мм.
Расширение 10 материала фланца в варианте исполнения, представленном на фиг.4, имеет ширину n, которая составляет 30 мм при диаметре вписанной окружности d – 12 25 мм. Выпуклый свод расширения 10 материала может, как показано на фиг.4, выполняться сначала уступом со сторон фланцев 4а, 4b, обращенных к насосной камере 9, с высотой подъема k от 2 мм, откуда на образующемся уступе начинается выпуклый свод.
Центр вписанной окружности 12 имеет удаление X от плоскости поверхности уплотнения 14, которое составляет преимущественно 14-16 мм и выбирается в зависимости от диаметра фланца. Длина L корпуса насоса зависит от диаметра фланца и составляет 220-360 мм при диаметре фланцев 140-220 мм.
Формула изобретения
1. Корпус (1) насоса, в частности центробежного насоса, с элементами для крепления на установочной поверхности, с насосной камерой (9), в которой размещается вращающееся рабочее колесо со всасывающим патрубком (15) и нагнетательным патрубком (16), аналогичным всасывающему патрубку, где всасывающий и нагнетательный патрубки (15, 16) имеют по одному фланцу (4а, 4b) и при этом фланцы расположены на одной оси, отличающийся тем, что корпус (1) имеет только два места (3а, 3b; 5a, 5b) крепления для крепления насоса на установочной поверхности, причем одно место (3а, 3b; 5a, 5b) крепления находится на одном фланце и каждый фланец (4а, 4b) имеет для образования одного места (3а, 3b; 5a, 5b) крепления, по меньшей мере, один направленный к установочной поверхности выступ (6) или срез (5a, 5b).
2. Корпус насоса по п.1, отличающийся тем, что выступы (6) фланца имеют направленные к установочной поверхности и прилегающие к ней площадки (13), находящиеся в плоскости, касательной к боковой поверхности соответствующего фланца (4а, 4b), или в плоскости, параллельной этой касательной плоскости.
3. Корпус насоса по п.1, отличающийся тем, что срезы (5a, 5b) имеют направленные к установочной поверхности и прилегающие к ней площадки (13), находящиеся в плоскости, касательной к боковой поверхности соответствующего фланца (4а, 4b).
4. Корпус насоса по одному из пп.1-3, отличающийся тем, что во фланце (4а, 4b) на участке мест (3а, 3b; 5a, 5b) крепления фланца выполнено, по меньшей мере, одно отверстие (7), в частности резьбовое, расположенное в плоскости фланца, для соответствующего размещения элемента крепления.
5. Корпус насоса по п.4, отличающийся тем, что отверстие (7) расположено перпендикулярно оси (8) фланцев.
6. Корпус насоса по п.4, отличающийся тем, что отверстия выполнены с резьбой M12 и имеют глубину в каждом фланце в пределах 20 50 мм, предпочтительно 30 мм.
7. Корпус насоса по п.1, отличающийся тем, что фланцы (4а, 4b) имеют расширения (10) материала на сторонах, обращенных к насосной камере (9), вытянутые от оси фланцев (8) до наружного обвода соответствующего фланца (4а, 4b) через, по меньшей мере, часть стороны фланца (4а, 4b), обращенной к насосной камере (9), причем эти расширения (10) материала имеют площадки (11), ориентированные параллельно установочной поверхности и выполненные таким образом, что эти площадки (11) вместе с прилегающими к установочной поверхности площадками (13) соответствующих выступов (6) или срезов (5а, 5b), образуют единую опорную поверхность.
8. Корпус насоса по п.7, отличающийся тем, что расширения (10) материала выпукло выгнуты в направлении, параллельном оси (8) фланцев, в сторону насосной камеры (9).
9. Корпус насоса по п.8, отличающийся тем, что выпуклый свод расширения (10) материала формируется таким образом, что в единую опорную поверхность вписывается окружность (12), имеющая диаметр от 15 до 35 мм, предпочтительно 25 мм.
10. Корпус насоса по п.4, отличающийся тем, что ось отверстия (7) проходит через центр окружности (12), вписанной в единую опорную поверхность.
11. Корпус насоса по п.4, отличающийся тем, что фланцы (4а, 4b) имеют соответственно поверхности (14) уплотнения, образующие упорядоченные концентрические возвышения на стороне фланца, отвернутой от насосной камеры (9), причем ось отверстия (7) располагается на расстоянии 10-20 мм, преимущественно 14-16 мм, от плоскости поверхности (14) уплотнения или на расстоянии 7-17 мм, преимущественно 11-13 мм, от плоскости стороны фланца (4а, 4b), отвернутой от насосной камеры (9).
12. Корпус насоса по п.1, отличающийся тем, что ширина площадки (13), прилегающей к удерживающей поверхности, или ширина единой опорной поверхности выбираются в зависимости от габаритов фланца, при этом предпочтительная ширина 30-80 мм, в частности 50 мм.
13. Корпус насоса по п.4, отличающийся тем, что выступы (6) и расширения (10) материала составляют с фланцами (4а, 4b) единое целое.
14. Корпус насоса по п.1, отличающийся тем, что корпус (1) насоса изготавливается из литьевого сплава, предпочтительно из литейного чугуна.
РИСУНКИ
|
|