(21), (22) Заявка: 2007147527/03, 19.12.2007
(24) Дата начала отсчета срока действия патента:
19.12.2007
(43) Дата публикации заявки: 27.06.2009
(46) Опубликовано: 10.04.2010
(56) Список документов, цитированных в отчете о поиске:
КУЗЬМИН И.В. и др. Методические рекомендации по бурению скважин с выносом керна обратным потоком промывочной жидкости. – М.: НПО “ГЕОТЕХНИКА” СКБ, 1977, с.25-42. SU 1649088 А1, 15.05.1991. SU 1002511 А2, 07.03.1987. RU 2297513 С1, 20.04.2007. US 3552779 А, 05.01.1971.
Адрес для переписки:
300026, г.Тула, ул. Скуратовская, 98, ОАО “Тульское НИГП”
|
(72) Автор(ы):
Будюков Юрий Евдокимович (RU), Спирин Василий Иванович (RU), Анненков Анатолий Алексеевич (RU), Евсеев Виктор Николаевич (RU), Наумов Олег Анатольевич (RU)
(73) Патентообладатель(и):
Открытое акционерное общество “Тульское научно-исследовательское геологическое предприятие” (ОАО “Тульское НИГП”) (RU)
|
(54) СПОСОБ БУРЕНИЯ КРЕПКИХ ПОРОД С ГИДРОТРАНСПОРТОМ КЕРНА И БУРОВОЙ СНАРЯД ДЛЯ ЕГО ОСУЩЕСТВЛЕНИЯ
(57) Реферат:
Изобретение относится к области бурения скважин в крепких породах, а именно к технологии и технике бурения с гидротранспортом керна, и обеспечивает повышение производительности бурения. Техническим результатом является повышение производительности бурения. Способ бурения включает определение критической скорости восходящего потока промывочной жидкости, Wкр. При этом скорость углубки поддерживают не больше критической величины WМкр. Керн при бурении разделяют на столбик определенной длины h. Буровой снаряд содержит кернолом, расположенный в корпусе алмазного расширителя так, что расстояние коронки определяется из математического соотношения. При этом износостойкость материала кернолома выше, чем износостойкость материала корпуса расширителя, а суммарная площадь поперечных сечений промывочных каналов расширителя, суммарная площадь поперечных сечений наружных боковых каналов алмазной коронки, суммарная площадь продольного сечения ее торцевых каналов и суммарная площадь поперечных сечений внутренних боковых каналов находятся в соотношении. 2 н.п. ф-лы, 2 ил.
Изобретение относится к области бурения скважин в крепких породах, а именно к технологии и технике бурения с гидротранспортом керна, и обеспечивает повышение производительности бурения.
Известен способ бурения с транспортировкой керна восходящим потоком очистного агента с устройством для его осуществления (см. Патент США 3552779, кл. 175-215, опублик. 1971 г.), включающий бурильные трубы, сальник с керноотводом, кернолом, керноприемную трубу и коронку. При бурении при этом способе выбуренный керн верхним своим торцом упирается в клин кернолома, отклоняется от оси скважины и скалывается.
Недостатком этого способа является то, что в начале бурения не определяется критическая скорость восходящего потока, обеспечивающая вынос шлама и керна на поверхность, не поддерживается критическое значение скорости углубки скважины путем изменения режимных параметров, а кернолом устанавливается в керноприемной трубе на произвольном расстоянии от торца буровой коронки, в результате при бурении образуются столбики керна не оптимальной длины с точки зрения требований условий его гидротранспорта в бурильных трубах и отводной трубе сальника, что приводит к снижению производительности бурения вследствие неравномерной скорости движения шлама и керна и возникающих по этой причине шламонакоплении и пробкообразовании на забое и подклинки керна в бурильных трубах (керноводе).
Наиболее близким по технической сущности является способ бурения крепких пород с гидротранспортом керна, включающий разрушение горной породы, образование керна, разрушение его на столбики, вынос керна и шлама восходящим потоком промывочной жидкости по внутреннему каналу одинарной колонны бурильных труб на поверхность и регулирование скорости углубки скважины путем изменения режимных параметров, изоляцию поглощающих горизонтов.
При бурении по этому способу применяется буровой снаряд, включающий бурильные трубы, колонковую трубу, алмазный расширитель, кернолом и алмазную буровую коронку (В.П.Дерусов. Обратная промывка при бурении геологоразведочных скважин. М.: Недра, 1984, 184 с.).
Недостатками этого способа являются: отсутствие определения критической скорости восходящего потока в начале бурения и критической скорости углубки, разделение при бурении керна на столбики различной длины, что обуславливает шламонакопление и пробкообразование на забое и подклинки керна в бурильных трубах при бурении. Недостатками применяемого при этом способе бурового снаряда являются: выбор нерационального расстояния от середины длины кернолома до торца алмазной коронки, невысокая износостойкость материала кернолома, нерациональное сечение промывочных каналов расширителя и алмазной коронки, что способствует резкому увеличению гидравлических сопротивлений внутри бурового снаряда и, следовательно, увеличению потерь промывочной жидкости на забое, и также шламонакоплению и пробкообразованию на забое и подклинки керна в бурильных трубах. В этом заключаются основные недостатки известного способа и снаряда для бурения с гидротранспортом керна.
Техническое решение направлено на повышение производительности бурения путем исключения шламонакопления и пробкообразования на забое и подклинок керна в бурильных трубах за счет оптимизации скорости восходящего потока промывочной жидкости, концентрации твердой фазы в ней, скорости углубки, высоты столбика керна и сечения промывочных каналов алмазной коронки и алмазного расширителя.
Предлагаемый способ бурения крепких пород с гидротранспортом керна и буровой снаряд для его осуществления отличается тем, что в начале бурения определяют критическую скорость восходящего потока промывочной жидкости из следующего соотношения
,
где Wкр – критическая скорость восходящего потока;
F3 – площадь забоя;
VM – скорость углубки скважины;
FT – площадь поперечного сечения внутреннего канала бурильной трубы;
n – удельный вес частиц породы;
– удельный вес промывочной жидкости, закачиваемой в скважину;
T – удельный вес промывочной жидкости в бурильных трубах;
– коэффициент, учитывающий винтообразное движение частиц ( =1,25÷1,27);
a – опытный коэффициент, определяемый по методике А.С.Денисова (a=1,14);
k – опытный коэффициент, зависящий от формы частиц и закона обтекания потоком, определяемый по методике Ф.А.Шамшева (для шара k=5,11);
dn – диаметр частицы,
и скорость углубки поддерживают не более критической величины
,
где – критическая скорость углубки скважины;
F3 – площадь забоя скважины;
Q – расход промывочной жидкости;
QT – расход твердой фазы;
FT – площадь поперечного сечения внутреннего канала бурильной трубы;
dT – диаметр внутреннего канала бурильных труб;
– опытный коэффициент, определяемый по методике P.P.Чугаева ( =2,0),
при этом керн при бурении разделяется на столбики, длина которых определяется по зависимости
,
где h – длина столбика керна;
К1 – опытный коэффициент (К1=0,7÷1,0);
dk – диаметр керна;
R, r – наружный и внутренний радиусы отверстия отводной трубы сальника соответственно, а буровой снаряд для бурения крепких пород с гидротранспортом керна отличается тем, что кернолом расположен в корпусе алмазного расширителя так, что расстояние от середины его длины до торца алмазной коронки определяется из соотношения
l=k2h,
где l – расстояние от середины длины кернолома до торца алмазной коронки;
k2 – опытный коэффициент (k2=0,80÷1,00);
h – заданная длина столбика керна,
при этом износостойкость материала кернолома выше, чем износостойкость материала корпуса расширителя, а суммарная площадь поперечных сечений промывочных каналов расширителя, суммарная площадь поперечных сечений наружных боковых каналов алмазной коронки, суммарная площадь продольного сечения ее торцевых каналов и суммарная площадь поперечных сечений внутренних боковых каналов находятся в соотношении
SP:SH:ST:Sв=1,00:1,10:1,15:1,20
где SP, SH, Sв – суммарная площадь поперечных сечений промывочных каналов расширителя, наружных боковых каналов коронки и внутренних боковых каналов коронки соответственно;
ST – суммарная площадь продольного сечения торцевых промывочных каналов коронки.
Благодаря тому, что в начале бурения определяют критическую скорость восходящего потока промывочной жидкости из следующего соотношения
,
где Wkp – критическая скорость восходящего потока;
F3 – площадь забоя;
VM – скорость углубки скважины;
FT – площадь поперечного сечения внутреннего канала бурильной трубы;
n – удельный вес частиц породы;
– удельный вес промывочной жидкости, закачиваемой в скважину;
T – удельный вес промывочной жидкости в бурильных трубах;
– коэффициент, учитывающий винтообразное движение частиц ( =1,25÷1,27);
a – опытный коэффициент, определяемый по методике А.С.Денисова (a=1,14);
k – опытный коэффициент, зависящий от формы частиц и закона обтекания потоком, определяемый по методике Ф.А.Шамшева (для шара k=5,11);
dn – диаметр частицы,
и скорость углубки поддерживают не более критической величины
,
где – критическая скорость углубки скважины;
F3 – площадь забоя скважины;
Q – расход промывочной жидкости;
QT – расход твердой фазы;
FT – площадь поперечного сечения внутреннего канала бурильных труб;
dT – диаметр внутреннего канала бурильных труб;
– опытный коэффициент, определяемый по методике P.P.Чугаева ( =2,0), создаются условия для эффективного выноса шлама и керна на дневную поверхность при допустимой концентрации твердой фазы в промывочной жидкости, что исключает шламонакопление и пробкообразование на забое скважины и подклинки керна в бурильных трубах.
Из гидравлики бурения известно, что подъем частиц породы в восходящем потоке возможен, если удовлетворяется условие

где W – скорость восходящего потока;
а – опытный коэффициент, определяемый по методике А.С.Денисова (а=1,14);
u – скорость погружения частицы породы в жидкости.
При этом скорость подъема частицы в жидкости восходящим потоком равна

где С – скорость подъема частицы.
Из уравнения (2) следует, что скорость восходящего потока W определяется по зависимости

Скорость погружения частиц породы в жидкость u определяется по формуле Риттингера с учетом данных фиг.1.

где К – коэффициент, принимаемый в зависимости от величины фракций горной породы в гидросмеси (при d=10÷20 мм значение К=2,0);
dn – диаметр частицы;
n – удельный вес породы;
– удельный вес жидкости.
Для обеспечения хорошей промывки скважины и надлежащей скорости подъема частиц породы должно быть выполнено с учетом данных фиг.1 условие равенства объемов разрушенной и удаленной с забоя породы (см. Ю.Е.Будюков, В.И.Власюк, В.И.Спирин. Алмазный породоразрушающий инструмент. – Тула: ИПП «Гриф и К», 2005. – 288 с.).

где С – скорость подъема частиц;
F3 – площадь забоя;
FT – площадь поперечного сечения проходящего канала бурильной трубы;
VM – скорость углубки скважины;
n – удельный вес частиц породы;
YT – удельный вес промывочной жидкости в бурильных трубах;
– удельный вес промывочной жидкости, закачиваемой в скважину.
Из зависимости (5) определяем минимально допустимый предел скорости подъема частиц
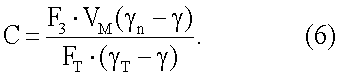
Исследованиями, проведенными в ГрозНИИ и ТулНИГП, установлено, что вращение бурильных труб уменьшает скорость падения частиц породы, с учетом этого зависимость (6) примет вид
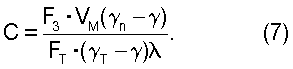
Подставив выражение (4) и (7) в формулу (3), получим выражение для определения минимальной незашламовывающей скорости восходящего потока

где WKP – минимально допустимая скорость восходящего потока промывочной жидкости исходя из условия предупреждения шламонакопления и пробкообразования в колонковых бурильных трубах при бурении;
– коэффициент, учитывающий винтообразное движение частиц
( =1,25÷1,27).
Если скорость в бурильных трубах WKP, то, как отмечено выше, они будут в значительной мере зашламовываться при бурении, а при скорости W>WKP получим неэкономичное решение, концентрация твердой фазы будет невелика, поэтому для транспортирования данного объема твердого шлама и керна придется затрачивать большое количество воды.
Поэтому принимаем такое условие, чтобы скорость W в трубопроводе (бурильных трубах) была равна минимальной назашламовывающей скорости WKP, т.е.

При этом важно определение критической концентрации твердой фазы (шлама и керна) в промывочной жидкости. Концентрация твердой фазы – отношение объема твердой фазы (теоретически обращенной в монолит, лишенный пор) к объему гидросмеси, внутри которой находится твердая фаза. Под критической понимают такую концентрацию твердого, при которой не наблюдается шламонакопление и пробкообразование при бурении на забое.
Исходя из условия (9) и используя положение из общей гидравлики о напорном гидротранспорте с учетом фиг.1, запишем выражение

где Ko – критическая концентрация твердой фазы;
T – объем твердой фазы;
FT – площадь поперечного сечения проходного отверстия бурильной трубы;
dT – диаметр внутреннего канала бурильной трубы;
– опытный коэффициент, определяемый по методике P.P.Чугаева ( =2,0).
Решая уравнение (10), находим

Используя выражение (11), находим допустимый объем твердой фазы (шлама, керна), поступающий в промывочную жидкость в единицу времени из зависимости

где – максимально допустимый объем твердой фазы;
Q – расход промывочной жидкости;
Кo – критическая концентрация твердой фазы.
Этот же объем твердой фазы, образуемый при бурении скважины с гидротранспортом керна, может быть определен по формуле Ю.Е.Будюкова, В.И.Власюка, В.И.Спирина (см. Ю.Е.Будюков, В.И.Власюк, В.И.Спирин. Алмазный породоразрушающий инструмент.- Тула: ИПП «Гриф и К», 2005. – 288 с.).

где F3 – площадь забоя скважины;
VM – скорость углубки скважины.
Допустимую концентрацию твердой фазы в промывочной жидкости поддерживают регулированием ее расхода, изменением осевой нагрузки на инструмент, изменением частоты вращения бурового снаряда или их одновременном регулировании в различных сочетаниях.
Допустимую концентрацию твердой фазы в промывочной жидкости наиболее просто поддерживают за счет увеличения ее расхода при промывке скважины с расходом, определенным по зависимостям (11), (12), не менее

где QKP – минимально допустимый расход промывочной жидкости исходя из условия предупреждения шламонакопления и пробкообразования в колонковых и бурильных трубах при бурении.
Не всегда мощность насосного оборудования позволяет увеличить расход промывочной жидкости до значения QKP, особенно при больших диаметрах бурения, в этом случае другим путем, позволяющим уменьшить концентрацию твердой фазы в промывочной жидкости до допустимых значений, является снижение скорости углубки.
Максимально допустимая механическая скорость бурения с гидротранспортом керна с фиксированным расходом промывочной жидкости составлена с учетом (11), (12).

где – критическая скорость углубки скважины:
Q – расход промывочной жидкости.
С учетом (11) запишем формулу (15) в виде

Установлено (см. Ю.Е.Будюков. Создание и производство специального алмазного бурового инструмента. – М., МГП «Геоинформмарк», 1993), что скорость углубки является в основном функцией осевой нагрузки на инструмент и частоты его вращения и имеет вид

где VM – скорость углубки скважины,
,
где Lk – постоянный коэффициент;
PШ – твердость горной породы по штампу;
Dc – диаметр коронки по ее среднему радиусу;
n – частота вращения снаряда;
P – осевая нагрузка на инструмент.
Поэтому допустимую концентрацию твердой фазы в промывочной жидкости при значительном возрастании скорости углубки (например, при входе коронки в мягкие породы) можно поддерживать путем регулирования осевой нагрузки на инструмент и частоты его вращения, при которых критическая механическая скорость углубки бурения не превысит допустимых значений.
Вследствие того, что при бурении керн разделяется на столбики, длина которых определяется по зависимости
,
где h – длина столбика керна;
К1 – опытный коэффициент (К1=0,7÷1,0);
dk – диаметр керна;
R, r – наружный и внутренний радиусы отверстия трубы сальника,
соответственно создаются условия для свободного прохождения керна в бурильных трубах и керноотвода сальника, и, благодаря этому, исключается образование пробок керна на забое скважины и возникновение подклинок керна в бурильных трубах.
Благодаря тому, что кернолом расположен в корпусе алмазного расширителя так, что расстояние от середины его длины до торца алмазной коронки определяется из соотношения
l=k2h,
где l – расстояние от середины длины кернолома до торца алмазной коронки;
k2 – опытный коэффициент (k2=0,80÷1,00);
h – задняя длина столбика керна,
при этом износостойкость материала кернолома выше, чем износостойкость материала корпуса расширителя в процессе бурения, выбуренный керн, достигая кернолома, установленного на определенном расстоянии «l» от торца коронки, скалывается на примерно одинаковые столбики с заранее заданной длиной не более h и выносится на поверхность восходящим потоком очистного агента, что способствует формированию равномерной скорости гидротранспорта шлама и керна и устранению подклинок керна в бурильных трубах.
Вследствие того, что суммарная площадь поперечных сечений промывочных каналов расширителя, суммарная площадь поперечных сечений наружных боковых каналов алмазной коронки, суммарная площадь продольного сечения ее торцевых каналов и суммарная площадь поперечных сечений внутренних боковых каналов находятся в соотношении
SP:SH:ST:Sв=1,00:1,10:1,15:1,20
где SP, SH, Sв – суммарная площадь поперечных сечений промывочных каналов расширителя, наружных боковых каналов коронки и внутренних боковых каналов коронки соответственно;
ST – суммарная площадь продольного сечения торцевых промывочных каналов коронки.
Уменьшаются возникающие при обратной промывке (в отличие от прямой промывки) высокие гидравлические сопротивления за счет содержания в жидкости породного шлама во всех элементах бурового снаряда: расширителе, коронке, колонковой трубе и бурильных трубах.
Причем соотношение суммарных площадей поперечных сечений промывочных каналов расширителя и суммарных площадей поперечных сечений наружного, внутреннего бокового каналов алмазной коронки и суммарной площади продольного сечения ее торцевых каналов в пропорции SP:SH:ST:Sв=1,00:1,10:1,15:1,20 является оптимальным, т.к. при более высоких значениях соотношений сопротивления снижаются незначительно, и при более низких значениях соотношений гидравлические сопротивления возрастают.
При такой конструкции промывочной системы расширителя и коронки обеспечивается повышение эффекта нижней промывки за счет возможности струи жидкости расширяться (при прохождении ее из наружного бокового канала в торцевой канал) в поперечном размере путем присоединения масс окружающей жидкости, что обуславливает хороший обмыв забоя, взвешивание и удаление выбуренной породы и, как следствие, повышение механической скорости бурения. При этом происходит формирование примерно одинаковых по величине скоростей (не превышающих определенного критического значения), нисходящего и восходящего потоков, что способствует возникновению ламинарного движения жидкости и существенному уменьшению разрушения стенок скважины и потери промывочной жидкости вследствие утечки ее в поглощающие горные породы на забое.
Указанное способствует поддержанию ствола скважины в состоянии, пригодном для бесперебойного его углубления без зашламования и пробкообразования до проектной глубины.
На фиг.1 приведена схема бурения с гидротранспортом керна, которая включает расположение следующего оборудования и инструмента: алмазная буровая коронка 1, алмазный расширитель 15, колонковая труба 2, керн 3, отстойник 4, насос 5, привентор 6, укрепленный на обсадной трубе 13, вращатель бурового станка 7, сальник 8, отводная труба 9, желоб 10, тройник 11, бурильная труба 12, пакер 14.
На фиг.2 показан одинарный буровой снаряд (продольный разрез) для бурения с гидротранспортом керна, включающий: алмазную буровую коронку 1 с боковыми наружными промывочными каналами 2, торцевыми промывочными каналами 3 и боковыми внутренними каналами 4, расширитель 5 с керноломом 6, бурильную (колонковую) трубу 7, внутри которой находится столбик керна 8.
Способ бурения реализуется следующим образом.
Промывочная жидкость из отстойника 4 насосом 5 через тройник 11, расположенный на обсадной трубе 13 ниже привентора 6, подается в затрубное пространство вначале между стенками обсадной трубы 13 и бурильными трубами 12, а затем между стенками скважины и бурильными трубами 12, колонковой трубой 2 и расширителем 15 поступает под рабочий торец алмазной коронки 1 через ее промывочные каналы: боковые наружные 2, внутренние 4 и торцевые 3, при этом струя жидкости расширяется в поперечных размерах путем присоединения масс окружающей жидкости, обуславливая хороший обмыв забоя со взвешиванием и удалением выбуренной породы и способствуя уменьшению сопротивления поступления породы в центральные каналы и расходу осевой нагрузки в большой степени на деформацию породы. Далее промывочная жидкость попадает в коронку 1, омывает керн 8 и после скалывания его керноломом 6 примерно на равные по длине столбики выносит их при равномерной скорости восходящего потока внутри бурильных труб 12 через отводную трубу 9 сальника 8 в желоб 10, за керном следует вынос шлама. Так происходит бесперебойное углубление ствола скважины при высокой производительности без зашламования и пробкообразования до проектной глубины.
Данное изобретение может быть осуществлено при помощи описанных в заявке средств. Оно было внедрено в геологоразведочной экспедиции «БУРЯТЗОЛОТОРАЗВЕДКА».
Технико-экономическая эффективность предлагаемого изобретения заключается в повышении производительности бурения и снижения себестоимости на 150 руб. на 1 м бурения.
Формула изобретения
1. Способ бурения крепких пород с гидротранспортом керна, включающий разрушение горной породы, образование керна, разрушение его на столбики, вынос керна и шлама восходящим потоком промывочной жидкости по внутреннему каналу одинарной колонны бурильных труб на поверхность, регулирование скорости углубки скважины путем изменения осевой нагрузки на буровой инструмент, частоты его вращения и расхода промывочной жидкости в отдельности или в их сочетании, отличающийся тем, что в начале бурения определяют критическую скорость восходящего потока промывочной жидкости из следующего соотношения:
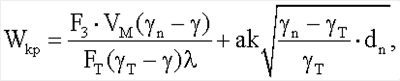 где Wкр – критическая скорость восходящего потока; F3 – площадь забоя; VM – скорость углубки скважины; FT – площадь поперечного сечения внутреннего канала бурильной трубы;
n – удельный вес частиц породы;
– удельный вес промывочной жидкости, закачиваемой в скважину;
T – удельный вес промывочной жидкости в бурильных трубах;
– коэффициент, учитывающий винтообразное движение частиц ( =1,25-1,27); а – опытный коэффициент, определяемый по методике А.С.Денисова (а=1,14); k – опытный коэффициент, зависящий от формы частиц и закона обтекания потоком, определяемый по методике Ф.А.Шамшева (для шара k=5,11); dn – диаметр частицы, и скорость углубки поддерживают не более критической величины
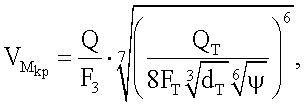 где VМkр – критическая скорость углубки скважины; F3 – площадь забоя скважины; Q – расход промывочной жидкости; QT – расход твердой фазы; FT – площадь поперечного сечения внутреннего канала бурильных труб; dT – диаметр внутреннего канала бурильных труб;
– опытный коэффициент, определяемый по методике Р.Р.Чугаева ( =2,0), при этом керн при бурении разделяется на столбики, длина которых определяется по зависимости
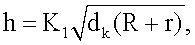 где h – длина столбика керна; K1 – опытный коэффициент (K1=0,7÷1,0); dk – диаметр керна; R, r – наружный и внутренний радиусы отверстия отводной трубы сальника соответственно.
2. Буровой снаряд для бурения крепких пород с гидротранспортом керна, включающий бурильные трубы, колонковую трубу, алмазный расширитель, кернолом и алмазную буровую коронку, отличающийся тем, что кернолом расположен в корпусе алмазного расширителя так, что расстояние от середины его длины до торца алмазной коронки определяется из соотношения l=k2h, где l – расстояние от середины длины кернолома до торца алмазной коронки; k2 – опытный коэффициент (k2=0,80÷1,00); h – задняя длина столбика керна, при этом износостойкость материала кернолома выше, чем износостойкость материала корпуса расширителя, а суммарная площадь поперечных сечений промывочных каналов расширителя, суммарная площадь поперечных сечений наружных боковых каналов алмазной коронки, суммарная площадь продольного сечения ее торцевых каналов и суммарная площадь поперечных сечений внутренних боковых каналов находятся в соотношении SP:SH:ST:Sв=1,00:1,10:1,15:1,20, где SP, SH Sв – суммарная площадь поперечных сечений промывочных каналов расширителя, наружных боковых каналов коронки и внутренних боковых каналов коронки соответственно; ST – суммарная площадь продольного сечения торцевых промывочных каналов коронки.
РИСУНКИ
|