|
(21), (22) Заявка: 2008135283/11, 29.08.2008
(24) Дата начала отсчета срока действия патента:
29.08.2008
(46) Опубликовано: 10.02.2010
(56) Список документов, цитированных в отчете о поиске:
RU 2194108 С2, 10.12.2002. RU 2289647 C1, 20.12.2006. GB 1276163 A, 01.06.1972. JP 10046507 А, 17.02.1998.
Адрес для переписки:
454006, г.Челябинск, а/я 673, А.Н. Шилкину
|
(72) Автор(ы):
Шилкин Анатолий Николаевич (RU)
(73) Патентообладатель(и):
Шилкин Анатолий Николаевич (RU)
|
(54) УПЛОТНИТЕЛЬНО-ПОДБИВОЧНЫЙ БЛОК (ВАРИАНТЫ)
(57) Реферат:
Уплотнительно-подбивочный блок предназначен для уплотнения балласта рельсового пути. Для упрощения процесса замены инструмента верхняя часть стержня инструмента выполнена в виде вилки. Между рычагами и инструментами блока, в соответствии с первым вариантом выполнения, смонтированы держатели, каждый из которых выполнен в виде головки с хвостовиком для закрепления в отверстии рычага и пазами для закрепления зубцов вилки стержня. В соответствии со вторым вариантом выполнения на рычаге выполнены пазы для закрепления зубцов вилки стержня. Зубья вилки установлены в пазах головки держателя или рычага и зафиксированы относительно нее посредством стяжного элемента, пропущенного через сквозные отверстия в головке держателя или рычага и зубьях вилки стержня. Рычаг может быть выполнен с двумя отверстиями, а держатель – с двумя хвостовиками. Плоскость вилки стержня инструмента может быть параллельна оси эксцентрикового вала. Зубья вилки стержня и соответствующие им пазы головки держателя или пазы рычага могут иметь трапециевидную форму в поперечном сечении, причем угол наклона боковой стороны трапеции к ее основанию составляет 85-75°, высота трапеции – не менее 10 мм, а торец зуба установлен в соответствующем ему пазе с упором в торец паза. Инструмент может быть дополнительно снабжен трамбующей плитой. Соединительный элемент выполнен в виде тяги или силового цилиндра с зафиксированным от перемещения штоком. Достигается упрощение замены инструмента. 2 н. и 7 з.п. ф-лы, 7 ил.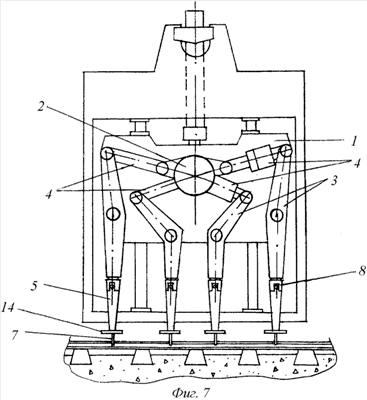
Изобретение относится к устройствам для строительства и ремонта железнодорожного пути, в частности к устройствам для уплотнения балласта железнодорожного пути.
Уплотнение балласта осуществляют при помощи инструмента, представляющего собой, чаще всего, стержень с нижним концом в виде уплотнительной лопатки. В процессе эксплуатации инструмент, испытывая интенсивное абразивное воздействие со стороны балласта, быстро изнашивается. Это приводит к необходимости его замены. Проблему восстановления изношенного инструмента пытаются решить различными путями. В частности, известен инструмент со сменной лопаткой. В этом инструменте лопатка и стержень представляют собой две отдельные детали, которые соединены между собой посредством штифта, зафиксированного в сквозных отверстиях нижнего конца стержня, и охватывающей нижний конец стержня приемной части, выполненной на лопатке. Для предупреждения выпадения штифта из отверстий предусмотрена изогнутая кольцевая пластина, опоясывающая стержень и перекрывающая эти отверстия. Штифт расположен перпендикулярно плоскости лопатки (см. патент РФ 2049841, кл. Е01В 27/16, заявл. 1.07.93, опубл. 10.12.95 «Подбойка шпалоподбивочной машины»).
Для данного решения характерна малая надежность соединения, обусловленная тем, что место соединения стержня и лопатки, располагающееся на нижнем конце стержня, в процессе уплотнения балласта погружается в слой балласта и быстро разрушается из-за абразивного износа. При этом расположение штифта таково, что оно перпендикулярно плоскости лопатки, приводит к ускоренному его выпадению, т.к. инструмент, совершая колебания в этом же направлении, способствует этому. Кроме того, следует отметить, что при уплотнении балласта изнашивается не только лопатка, но погружаемая в балласт часть стержня, т.е. замена только лопатки не позволяет полностью восстановить изношенный инструмент. В силу указанных причин на практике чаще всего инструмент меняют полностью, извлекая его из рычага машины для уплотнения балласта.
Наиболее близким по технической сущности, достигаемому результату и выбранным в качестве прототипа для заявляемого технического решения является уплотнительно-подбивочный блок, содержащий корпус с жестко закрепленным на нем эксцентриковым валом и шарнирно закрепленными двуплечими рычагами. Одно плечо каждого из рычагов соединено с эксцентриковым валом посредством закрепленного на рычаге соединительного элемента, а другое плечо несет установленный с возможностью демонтажа/монтажа инструмент для уплотнения балласта в виде стержня с нижним концом в виде уплотнительной лопатки. Верхний конец стержня имеет конусный хвостовик, который вставлен в соответствующее конусное отверстие рычага и закреплен болтом с пружинной шайбой. Болт входит в резьбовое отверстие конусного хвостовика стержня (см. Новые путевые машины./ Под ред. Ю.П. Сырейщикова. М., «Транспорт», 1984 г., с.66-67).
При работе уплотнительно-подбивочного блока основная часть нагрузки на соединение между рычагом и стержнем приходится на нагрузку от заглубления инструмента в балласт, т.е. на нагрузку, направленную вдоль конусной поверхности хвостовика стержня. Такая нагрузка приводит к заклиниванию хвостовика в отверстии рычага и часто вызывает сварку трением между рычагом и хвостовиком инструмента, в результате чего соединение становится практически неразъемным. При необходимости замены инструмента его снимают при помощи специального одностороннего клина и вкладыша. Вкладыш устанавливают вместо болта в отверстие конусного хвостовика стержня и ударами кувалды забивают клин до рассоединения инструмента и рычага. Из сказанного, очевидно, что замена инструмента весьма трудоемка, а иногда и невозможна.
Кроме того, следует отметить, что в процессе работы хвостовик инструмента и отверстие в рычаге прирабатываются друг к другу, а замена инструмента, тем более такая грубая, при которой разбивается отверстие в рычаге, приводит к тому, что из-за несовпадения рельефов поверхности отверстия в рычаге и поверхности хвостовика нового инструмента значительно снижается амплитуда колебаний лопатки инструмента и возникают дополнительные разрушающие динамические нагрузки на инструмент и блок в целом. Это снижает эффективность уплотнения балласта всего уплотнительно-подбивочного блока и вызывает ускоренный износ инструмента и блока.
При создании изобретения в соответствии с первым вариантом заявляемого уплотнительно-подбивочного блока ставилась задача – сохранение после замены инструмента эффективности уплотнения балласта и устранение опасности износа инструмента и блока вследствие динамических нагрузок от повреждения посадочной поверхности, с которой контактирует инструмент.
Техническим результатом, получаемым при реализации изобретения в соответствии с первым вариантом заявляемого уплотнительно-подбивочного блока, является упрощение процесса замены инструмента.
В соответствии с первым вариантом изобретения указанная задача решается за счет того, что в известном уплотнительно-подбивочном блоке, содержащем корпус с жестко закрепленным на нем эксцентриковым валом и шарнирно закрепленными двуплечими рычагами, одно плечо каждого из которых соединено с эксцентриковым валом посредством закрепленного на рычаге соединительного элемента, а другое плечо несет установленный с возможностью демонтажа/монтажа инструмент для уплотнения балласта в виде стержня с нижним концом в виде уплотнительной лопатки, согласно изобретению он дополнительно снабжен держателями, смонтированными между рычагами и инструментами, причем каждый из держателей выполнен в виде головки, снабженной хвостовиком для закрепления в отверстии рычага, а по крайней мере, верхняя часть стержня инструмента выполнена в виде вилки, зубья которой установлены в пазах головки держателя и зафиксированы относительно нее посредством, по крайней мере, одного стяжного элемента, пропущенного через сквозные отверстия в головке держателя и зубьях вилки стержня.
Рычаг может быть выполнен с двумя отверстиями, а держатель – с двумя хвостовиками.
Плоскость вилки стержня инструмента может быть расположена параллельно оси эксцентрикового вала.
Зубья вилки стержня и соответствующие им пазы головки держателя могут иметь трапециевидную форму в поперечном сечении, причем угол наклона боковой стороны трапеции к ее основанию составляет 85-75°, а высота трапеции – не менее 10 мм, при этом торец зуба установлен в соответствующем ему пазе с упором в торец паза.
Инструмент дополнительно может быть снабжен трамбующей плитой, закрепленной на стержне над уплотнительной лопаткой, а закрепленный на рычаге соединительный элемент выполнен в виде тяги или силового цилиндра с зафиксированным от перемещения штоком.
В качестве прототипа для второго варианта заявляемого блока выбрано то же техническое решение, что и для первого варианта. Ему присущи те же недостатки, которые указаны выше.
При создании изобретения в соответствии со вторым вариантом заявляемого блока также ставилась задача – сохранение после замены инструмента эффективности уплотнения балласта и устранение опасности износа инструмента и блока вследствие динамических нагрузок от повреждения посадочной поверхности, с которой контактирует инструмент.
Техническим результатом, получаемым при реализации изобретения в соответствии со вторым вариантом заявляемого приспособления, также является упрощение процесса замены инструмента.
В соответствии со вторым вариантом изобретения указанная задача решается за счет того, что в известном уплотнительно-подбивочном блоке, содержащем корпус с жестко закрепленным на нем эксцентриковым валом и шарнирно закрепленными двуплечими рычагами, одно плечо каждого из которых соединено с эксцентриковым валом посредством закрепленного на рычаге соединительного элемента, а другое плечо несет установленный с возможностью демонтажа/монтажа инструмент для уплотнения балласта в виде стержня с нижним концом в виде уплотнительной лопатки, согласно изобретению конец рычага, несущий инструмент, выполнен с пазами, а по крайней мере, верхняя часть стержня инструмента выполнена в виде вилки, зубья которой установлены в пазах рычага и зафиксированы относительно него посредством, по крайней мере, одного стяжного элемента, пропущенного через сквозные отверстия в рычаге и зубьях вилки стержня.
Плоскость вилки стержня инструмента может быть расположена параллельно оси эксцентрикового вала.
Зубья вилки стержня и соответствующие им пазы головки держателя могут иметь трапециевидную форму в поперечном сечении, причем угол наклона боковой стороны трапеции к ее основанию составляет 85-75°, а высота трапеции – не менее 10 мм, при этом торец зуба установлен в соответствующем ему пазе с упором в торец паза.
Инструмент дополнительно может быть снабжен трамбующей плитой, закрепленной на стержне над уплотнительной лопаткой, а закрепленный на рычаге соединительный элемент выполнен в виде тяги или силового цилиндра с зафиксированным от перемещения штоком.
Исследования, проведенные по источникам патентной и научно-технической информации, показали, что заявляемый блок неизвестен и не следует явным образом из изученного уровня техники, т.е. соответствует критериям “новизна” и “изобретательский уровень”.
Блок может быть изготовлен на любом предприятии, специализирующемся в данной отрасли, т.к. для этого требуются известные материалы и стандартное оборудование, и широко использован при производстве путевых работ, т.е. является промышленно применимым.
Выполнение уплотнительно-подбивочного блока в заявляемом виде позволяет осуществить соединение рычага и инструмента таким образом, что элементы инструмента располагаются вне рычага, в отличие от прототипа, где хвостовик стержня расположен внутри тела рычага. При этом вилкообразная часть стержня, охватывая снаружи держатель (по первому варианту выполнения), или конец рычага, несущий инструмент (по второму варианту выполнения), оказывается легко доступной для съема. Очевидно, что конструктивно стержень может быть выполнен либо в виде единой стойки, верхняя часть которой раздвоена в виде двузубой вилки, либо в виде двух отдельных стоек по всей длине стержня, которые объединены между собой в нижней части единой лопаткой. Раздвоенную верхнюю часть стержня можно без особых затруднений с помощью любого подходящего устройства (например, винтового съемника в виде болта с гайкой) разжать и снять. Простота выполнения операции по замене инструмента позволяет избежать возникновения повреждений места контакта рычага и стержня, что позволяет сохранить величину амплитуды колебаний лопатки инструмента после его замены и снижает вероятность разрушения блока и инструмента от вновь появляющихся после замены инструмента динамических нагрузок.
Таким образом, обеспечение упрощения процесса замены инструмента позволяет сохранить после замены инструмента эффективность уплотнения балласта и избежать износа инструмента и блока вследствие динамических нагрузок от повреждения посадочной поверхности, с которой контактирует инструмент.
При этом выполнение стержня в виде двух стоек, а держателя – с двумя хвостовиками позволяет увеличить длину лопатки инструмента и, тем самым, увеличить интенсивность воздействия на балласт.
Расположение плоскости (т.е. плоскости, проходящей через оба зуба вилки) вилкообразной части стержня так, что она занимает положение, параллельное оси эксцентрикового вала, позволяет передать с максимальной эффективностью колебательное движение от рычага блока к лопатке инструмента.
Выполнение зубьев вилки стержня и соответствующих им пазов на головке держателя или на рычаге с заявляемой формой поперечного сечения позволяет с одной стороны избежать заклинивания вилкообразной части стержня в этих пазах, а с другой стороны обеспечить надежное беззазорное закрепление соединяемых деталей между собой. Причем из-за того, что контактирующие друг с другом поверхности зубьев вилки и пазов держателя (или рычага – для второго варианта выполнения) имеют плоскую поверхность (в отличие от прототипа, где контактируют две криволинейные поверхности конусного хвостовика и конусного отверстия в рычаге) достигается более плотное прилегание этих соприкасающихся поверхностей. Отсутствие зазора между этими прилегающими поверхностями обеспечивает передачу лопатке инструмента требуемой величины амплитуды колебаний, снижает динамические нагрузки на блок и инструмент. Контроль беззазорности соединения обеспечивает стяжной элемент, пропущенный через зубья вилки и держатель (или рычаг). При этом глубина паза выбрана из условия обеспечения минимально необходимой площади контакта соединяемых деталей. При необходимости передачи значительных усилий эта площадь контакта может быть увеличена за счет увеличения глубины паза, причем конструктивное выполнение заявляемого соединения путем наружного расположения элементов инструмента относительно рычага позволяет изменять глубину паза в широком диапазоне. Кроме того, при выполнении соединения в заявляемом виде направление действия нагрузки, возникающей при заглублении инструмента, оказывается перпендикулярным по отношению к клиновой части (трапециевидной в поперечном сечении) зубьев вилки стержня и соответствующих им пазов, в отличие от прототипа, где нагрузка направлена вдоль клина, способствуя возникновению заклинивания и сварки трением между хвостовиком стержня и отверстием в рычаге. К тому же, в отличие от прототипа, где над хвостовиком стержня пустота, т.к. в этом месте установлен болт для соединения хвостовика и рычага, и вся нагрузка от заглубления инструмента воспринимается конусными поверхностями хвостовика и отверстия в рычаге, в заявляемом соединении торцы зубьев вилки стержня беззазорно упираются в торцы пазов, в которых они установлены, и передают на торец паза указанную нагрузку. Это снижает вероятность сварки между контактирующими поверхностями.
Снабжение инструмента трамбующей плитой и фиксирование рычага от поворота относительно корпуса за счет выполнения соединительного элемента в виде тяги или силового цилиндра с неподвижным штоком позволяет осуществить уплотнение балласта не путем подачи балласта под шпалы лопаткой инструмента, перемещаемой рычагом поперек межшпального пространства, т.е. горизонтального виброобжатия балласта, а путем вертикального вибропрессового воздействия на балласт. Такое воздействие приводит к менее интенсивному износу инструмента для уплотнения балласта, т.к. цикл обработки балласта укорачивается из-за исключения операций по сжиму-разжиму инструмента для подачи балласта под шпалы, и, следовательно, к уменьшению возникновения необходимости замены инструмента.
Заявляемое техническое решение поясняется чертежами, на которых изображены:
Фиг.1 – вид спереди на инструмент для уплотнения балласта, верхняя часть стержня которого выполнена в виде вилки и закреплена на держателе, установленном в отверстии рычага.
Фиг.2 – вид спереди на инструмент для уплотнения балласта, стержень которого выполнен в виде двух стоек с нижним концом, образующим единую лопатку, и закреплен на держателе, установленном в отверстии рычага.
Фиг.3 – вид спереди на инструмент для уплотнения балласта, стержень которого выполнен в виде двух стоек с нижним концом, образующим единую лопатку, и закреплен на держателе с двумя хвостовиками, установленными в отверстиях рычага.
Фиг.4 – вид спереди на инструмент для уплотнения балласта, стержень которого выполнен в виде двух стоек с нижним концом, образующим единую лопатку, над которой расположена трамбующая плита, стержень закреплен на держателе, установленном в отверстии рычага.
Фиг.5 – фрагмент рычага с выполненными в нем пазами и установленной в этих пазах верхней вилкообразной части стержня.
Фиг.6 – сечение по А-А на фиг.1-5.
Фиг.7 – общий вид уплотнительно-подбивочного блока (левая часть чертежа – вариант выполнения блока с соединительными элементами в виде тяг; правая часть чертежа – вариант выполнения блока с соединительными элементами в виде силовых цилиндров).
Уплотнительно-подбивочный блок содержит корпус 1 с жестко закрепленным на нем эксцентриковым валом 2 и шарнирно закрепленными двуплечими рычагами 3, одно плечо каждого из которых соединено с эксцентриковым валом 2 посредством закрепленного на рычаге 3 соединительного элемента 4, а другое плечо несет установленный с возможностью демонтажа/монтажа инструмент 5 для уплотнения балласта в виде стержня 6 с нижним концом в виде уплотнительной лопатки 7. Блок (по первому варианту выполнения) снабжен держателями 8, смонтированными между рычагами 3 и инструментами 5. Каждый из держателей 8 выполнен в виде головки 9, снабженной хвостовиком 10 для закрепления в отверстии рычага 3. По крайней мере, верхняя часть стержня 6 инструмента 5 выполнена в виде вилки. Зубья 11 вилки установлены в пазах 12 головки 9 держателя 8 (по первому варианту выполнения) или пазах 12 рычага 3 (по второму варианту выполнения) и зафиксированы относительно головки 9 или рычага 3 посредством, по крайней мере, одного стяжного элемента 13, пропущенного через сквозные отверстия в головке 9 держателя 8 (или рычаге 3) и зубьях 11 вилки стержня 6. Инструмент 5 может быть дополнительно снабжен трамбующей плитой 14, закрепленной на стержне 6 над уплотнительной лопаткой 7, а закрепленный на рычаге 3 соединительный элемент 4 может быть выполнен в виде тяги или силового цилиндра с зафиксированным от перемещения штоком.
Блок работает следующим образом.
Блок устанавливают над местом проведения работ по уплотнению балласта, при этом закрепленные на рычагах 3 инструменты 5 для уплотнения балласта располагаются между подлежащими подбивке шпалами. При опускании корпуса 1 блока инструменты 5 погружаются в балласт, а от эксцентрикового вала 2 посредством соединительных элементов 4 на рычаги 3 передаются виброколебания. Эти колебания передаются уплотнительной лопаткой 7 на балласт, в основном, в горизонтальном направлении, а трамбующей плитой 14 (в случае выполнения инструмента 5 с трамбующей плитой 14) в основном, – в вертикальном направлении. В результате балласт при уплотнении инструментом 5 без трамбующей плиты 14 (т.е. при горизонтальном виброобжатии) подается под шпалы лопаткой 7 за счет горизонтального перемещения инструмента 5 поперек межшпального пространства, а при наличии у инструмента 5 трамбующей плиты 14 – за счет вертикального вибропрессового воздействия от уплотнительной лопатки 7 и трамбующей плиты 14.
Если при работе блока возникает необходимость в замене инструмента 5, то ее производят путем извлечения стяжного элемента 13 и расклинивания зубцов 11 вилки инструмента 5 с помощью простейшего винтового съемника или просто за счет легкого постукивания по лопатке 7 в направлении ее длины, вызывающего вибрацию зубьев 11 вилки стержня 6. Из-за того, что направление усилия, воздействующее на инструмент 5 при заглублении в балласт, перпендикулярно направлению клина, образующего место соединения между головкой 9 держателя 8 (для первого варианта выполнения) или рычагом 3 (для второго варианта выполнения) и зубьями 11 вилки стержня 6, а также из-за того, что указанное усилие передается торцами зубцов 11 вилки на торцы пазов 12 в держателе 8 (для первого варианта выполнения) или торцы пазов 12 в рычаге 3 (для второго варианта выполнения), не происходит заклинивания этого соединения. К тому же это место легко доступно, т.к. расположено снаружи от держателя 8 (для первого варианта выполнения) или рычага 3 (для второго варианта выполнения), а не внутри тела рычага 3, как у прототипа. В результате такого простого и быстрого съема изношенного инструмента 5 не возникают повреждения на посадочной поверхности пазов 12 в держателей 8 (или рычаге 3), что гарантирует сохранение амплитуды колебаний лопатки 7 инструмента 5 на прежнем уровне и не вызывает ускоренного износа от дополнительных динамических нагрузок.
Так, упрощение процесса замены инструмента позволяет сохранить после замены инструмента эффективность уплотнения балласта и избежать износа инструмента и блока вследствие динамических нагрузок от повреждения посадочной поверхности, с которой контактирует инструмент.
Формула изобретения
1. Уплотнительно-подбивочный блок, содержащий корпус с жестко закрепленным на нем эксцентриковым валом и шарнирно закрепленными двуплечими рычагами, одно плечо каждого из которых соединено с эксцентриковым валом посредством закрепленного на рычаге соединительного элемента, а другое плечо несет установленный с возможностью демонтажа/монтажа инструмент для уплотнения балласта в виде стержня с нижним концом в виде уплотнительной лопатки, отличающийся тем, что он дополнительно снабжен держателями, смонтированными между рычагами и инструментами, причем каждый из держателей выполнен в виде головки, снабженной хвостовиком для закрепления в отверстии рычага, а, по крайней мере, верхняя часть стержня инструмента выполнена в виде вилки, зубья которой установлены в пазах головки держателя и зафиксированы относительно нее посредством, по крайней мере, одного стяжного элемента, пропущенного через сквозные отверстия в головке держателя и зубьях вилки стержня.
2. Уплотнительно-подбивочный блок по п.1, отличающийся тем, что рычаг выполнен с двумя отверстиями, а держатель – с двумя хвостовиками.
3. Уплотнительно-подбивочный блок по п.1 или 2, отличающийся тем, что плоскость вилки стержня инструмента параллельна оси эксцентрикового вала.
4. Уплотнительно-подбивочный блок по п.1 или 2, отличающийся тем, что зубья вилки стержня и соответствующие им пазы головки держателя имеют трапециевидную форму в поперечном сечении, причем угол наклона боковой стороны трапеции к ее основанию составляет 85-75°, а высота трапеции – не менее 10 мм, при этом торец зуба установлен в соответствующем ему пазу с упором в торец паза.
5. Уплотнительно-подбивочный блок по п.1 или 2, отличающийся тем, что инструмент дополнительно снабжен трамбующей плитой, закрепленной на стержне над уплотнительной лопаткой, а закрепленный на рычаге соединительный элемент выполнен в виде тяги или силового цилиндра с зафиксированным от перемещения штоком.
6. Уплотнительно-подбивочный блок, содержащий корпус с жестко закрепленным на нем эксцентриковым валом и шарнирно закрепленными двуплечими рычагами, одно плечо каждого из которых соединено с эксцентриковым валом посредством закрепленного на рычаге соединительного элемента, а другое плечо несет установленный с возможностью демонтажа/монтажа инструмент для уплотнения балласта в виде стержня с нижним концом в виде уплотнительной лопатки, отличающийся тем, что конец рычага, несущий инструмент, выполнен с пазами, а, по крайней мере, верхняя часть стержня инструмента выполнена в виде вилки, зубья которой установлены в пазах рычага и зафиксированы относительно него посредством, по крайней мере, одного стяжного элемента, пропущенного через сквозные отверстия в рычаге и зубьях вилки стержня.
7. Уплотнительно-подбивочный блок по п.6, отличающийся тем, что плоскость вилки стержня инструмента параллельна оси эксцентрикового вала.
8. Уплотнительно-подбивочный блок по п.6, отличающийся тем, что зубья вилки стержня и соответствующие им пазы головки держателя имеют трапециевидную форму в поперечном сечении, причем угол наклона боковой стороны трапеции к ее основанию составляет 85-75°, а высота трапеции – не менее 10 мм, при этом торец зуба установлен в соответствующем ему пазу с упором в торец паза.
9. Уплотнительно-подбивочный блок по п.6, отличающийся тем, что инструмент дополнительно снабжен трамбующей плитой, закрепленной на стержне над уплотнительной лопаткой, а закрепленный на рычаге соединительный элемент выполнен в виде тяги или силового цилиндра с зафиксированным от перемещения штоком.
РИСУНКИ
|
|