(21), (22) Заявка: 2007137241/15, 08.10.2007
(24) Дата начала отсчета срока действия патента:
08.10.2007
(43) Дата публикации заявки: 20.04.2009
(46) Опубликовано: 10.02.2010
(56) Список документов, цитированных в отчете о поиске:
RU 2149833 C1, 27.05.2000. RU 2276657 C2, 20.05.2006. SU 1318530 A1, 23.06.1987. DE 1013272 В, 08.08.1957. US 4551326 А, 05.11.1985. US 4545974 А, 08.10.1985.
Адрес для переписки:
620014, г.Екатеринбург, ул. Шейнкмана, 20, 3 этаж, ООО “Урал Процесс Инжиниринг Компания (УПЕК)”, генеральному директору А.М. Халемскому
|
(72) Автор(ы):
Халемский Арон Михайлович (RU), Смирнов Сергей Владимирович (RU), Келнер Леонид (US)
(73) Патентообладатель(и):
Общество с ограниченной ответственностью “Урал Процесс Инжиниринг Компания (УПЕК)” (RU)
|
(54) СПОСОБ ПОЛУЧЕНИЯ ОКИСЛИТЕЛЯ НА ОСНОВЕ ФЕРРАТОВ ЩЕЛОЧНЫХ МЕТАЛЛОВ И УСТАНОВКА ДЛЯ ЕГО ОСУЩЕСТВЛЕНИЯ
(57) Реферат:
Изобретение может быть использовано для получения регентов для обеззараживания и очистки хозяйственно-бытовых и промышленных сточных вод. Для получения окислителя на основе ферратов щелочных металлов проводят окисление железосодержащего вещества в расплаве соединений щелочных металлов в две стадии. На первой стадии ведут окисление исходного железосодержащего вещества в расплаве сульфатов щелочных металлов и/или промышленных отходов, содержащих сульфаты щелочных металлов, при пропускании через расплав электрического тока до получения полупродукта, содержащего оксиды железа и ферриты щелочных металлов. На второй стадии осуществляют последующее окисление оксидов железа и ферритов щелочных металлов, содержащихся в полупродукте, в расплаве гидроксидов щелочных металлов, в присутствии газообразного кислорода до получения продукта, содержащего ферраты (IV) и (VI) щелочных металлов. Предложена установка для получения указанного окислителя. Изобретение позволяет снизить энергетические затраты и продолжительность процесса получения окислителя, расширить ассортимент отходов, используемых в качестве сырья. 2 н. и 33 з.п. ф-лы, 17 ил.
Изобретение относится к области производства реагентов окислителей, которые могут быть использованы для обеззараживания хозяйственно-бытовых сточных вод после биологической очистки, разложения цианидов, сульфидов и органических примесей в технологиях очистки промышленных сточных вод, обезвреживания радиоактивных сточных вод, путем перевода радионуклидов в малорастворимые соли, разложения фосфорорганических соединений и очистки хозяйственно-бытовых и производственных сточных вод от фосфат-ионов, очистки и водоподготовки питьевой воды природных источников от токсичных соединений мышьяка, марганца и ряда других тяжелых и цветных металлов.
Окислитель на основе ферратов (IV) и (VI) щелочных металлов обладает сильными окислительными свойствами, которые обусловлены входящими в его состав ферратами (IV) и (VI) калия и натрия. Степени окисления выше «+3» являются для железа не характерными, и соединения железа (IV) и (VI) являются, как правило, неустойчивыми и сравнительно легко разлагаются при нагревании и при взаимодействии с молекулами воды или с восстановителями. Все это предъявляет достаточно высокие требования к условиям получения, хранения и применения реагентов, содержащих ферраты (IV) и (VI) калия и натрия.
Известен способ получения феррата (IV) натрия путем прокаливания феррита натрия Na2Fe2O4 при 400-600°C с трехкратным избытком соды Na2CO3 в инертной атмосфере в течение четырех часов с последующим прокаливанием в течение одного часа в токе кислорода (патент США 2835553, опубл. 1958 г.). Недостатками данного способа являются:
– большая длительность процесса (5 часов), обусловленная низкой скоростью процессов, связанной с температурным интервалом 400-600°С;
– использование дефицитного феррита натрия, который не выпускается в промышленных масштабах;
– создание инертной атмосферы, требующей герметизации установки.
Известен также способ получения ферратов (IV) щелочных металлов, при котором нагревают реакционную смесь, состоящую из частиц элементарного железа и пероксида натрия (Na2O2) в молярном отношении 1:1,8-1:1,25 при температурах выше 500°С в течение времени, достаточного для протекания экзотермической реакции между реагентами. Реакцию ведут в отсутствие свободного кислорода, в атмосфере инертного газа (патент США 4385045, опубл. 24.05.83). Недостатками способа являются:
– использование пероксида натрия, который имеет сравнительно высокую стоимость;
– создание атмосферы инертного газа, требующей герметизации установки.
Известен способ непрерывного синтеза феррата (аналог), включающий смешивание водного раствора, содержащего соль железа и окисляющий агент в смешивающей камере, доставку части водного раствора в реакционную камеру, в которой вырабатывается феррат, а также устройство для непрерывного синтеза феррата и доставки его к месту использования, содержащее два резервуара, соединенную с ними смешивающую камеру и реакционную камеру, соединенную с возможностью управления со смешивающей камерой и приспособленной для приема и удержания ферратной смеси, пока концентрация феррата не достигнет заданного уровня (патент RU 2276657, опубл. 20.05.2006). Недостатками способа являются:
– использование солей железа, большая часть которых выпускается химической промышленностью в крупных масштабах реактивной квалификации и имеет высокую стоимость, а химическое или электрохимическое окисление природного железа в водных растворах не обеспечивает высокие производительности процессов и требует применения крупномасштабных устройств для размещения больших объемов воды;
– использование окисляющих реагентов для солей железа в водном растворе приводит к загрязнению образующихся веществ продуктами восстановления окислителей и к повышенному риску вторичного загрязнения очищаемых водных растворов;
– использование устройства для непрерывного синтеза феррата, содержащего два резервуара, смешивающую и реакционную камеры, в котором железосодержащие реагенты используются в виде солей, приводит к удорожанию образующихся ферратов.
Наиболее близким аналогом, принятым за прототип, является способ получения феррата (IV) натрия путем взаимодействия натрийсодержащего соединения, взятого в виде сульфата натрия, с железосодержащим веществом, в качестве которого может использоваться лом черных металлов, в окислительной атмосфере при 850-1100°С при пропускании через расплав переменного тока с помощью съемного пакета стальных электродов. Состав расплава изменяется от сульфата до феррата (IV) натрия в образующемся едком натре. Процесс ведут до достижения массовой доли сульфата натрия в продукте не более 1%, непрерывно поддерживая расплав в жидком состоянии корректировкой напряжения на электродах, что требует значительных затрат энергии для обеспечения достаточной температуры и продолжительности протекающих реакций (патент RU 2149833, опубл. 27.05.2000).
Недостатками способа являются:
– высокий расход электроэнергии, требующийся для электрохимического разложения натрийсодержащих соединений до достижения остаточной массовой доли сульфата натрия 1%;
– высокое энергопотребление, обусловленное необходимостью плавки исходной порции сульфата натрия, которая заливается в реактор, поскольку температура плавления Na2SO4 составляет 884°С;
– необходимость поддержания высоких температур расплава, поскольку с накоплением в его составе оксида натрия, имеющего температуру плавления 1275°С, для поддержания расплавленного состояния температура в реакторе должна быть повышена до 1100°С;
– малоэффективное влияние пероксида натрия, являющегося промежуточным продуктом реакций, на образование феррата (IV) натрия в интервале температур 850-1100°С в объеме расплава, поскольку Na2O2 разлагается выше 400°С.
Известно устройство, для получения окислителя на основе феррата (IV) натрия, содержащее корпус для размещения реакционной массы, съемный пакет стальных электродов, барботер, принятое за прототип в отношении устройства (патент RU 2149833, опубл. 27.05.2000).
Недостатками устройства являются:
– необходимость использования съемного пакета электродов, требующего дополнительных затрат на его изготовление;
– необходимость поддержания температуры расплава в интервале 850-1100°С на всем протяжении процесса приводит к увеличению энергозатрат;
– необходимость использования барботера для непрерывной подачи воздуха в объем расплава и перемешивания расплавленной массы на всем протяжении процесса приводит к увеличению энергозатрат.
Задачей, на решение которой направлено данное техническое решение, является снижение энергетических затрат на получение продукта путем снижения температуры процессов и повышения скорости растворения железосодержащего вещества в расплаве соединений щелочных металлов, расширение ассортимента отходов, которые могут быть использованы в качестве дешевого сырья.
Для решения поставленной задачи в способе получения окислителя на основе ферратов щелочных металлов, включающем окисление железосодержащего вещества в расплаве соединений щелочных металлов согласно изобретению, процесс окисления ведут в две стадии, при этом на первой стадии ведут окисление исходного железосодержащего вещества в расплаве сульфатов щелочных металлов и/или промышленных отходов, содержащих сульфаты щелочных металлов при пропускании через расплав электрического тока до получения полупродукта, содержащего оксиды железа и ферриты щелочных металлов, а на второй стадии осуществляют последующее окисление оксидов железа и ферритов щелочных металлов, содержащихся в полупродукте, в расплаве гидроксидов щелочных металлов, в присутствии газообразного кислорода до получения продукта, содержащего ферраты (IV) и (VI) щелочных металлов.
В качестве исходного железосодержащего вещества используют металлическое железо, и/или его сплавы, и/или отходы металлообработки изделий из черных металлов, например скрап, и/или отходы черной металлургии.
В качестве сульфатов щелочных металлов на первой стадии способа используют сульфаты натрия и/или калия, и/или промышленные отходы, содержащие сульфаты натрия и/или калия.
В качестве гидроксидов щелочных металлов на второй стадии способа используют гидроксиды натрия и/или калия, и/или промышленные отходы, содержащие гидроксиды натрия и/или калия.
Первую стадию способа ведут при температуре 850-1100°С до достижения массовой доли соединений железа (III) в полу продукте 4-39%, в пересчете на железо.
Вторую стадию ведут при температуре 640-880°С, до достижения массовой доли соединений железа (IV) и (VI) в продукте, содержащем ферраты щелочных металлов 2,7-21,8%, в пересчете на железо (VI).
На первой стадии осуществляют электрохимическое или комбинированное химико-электрохимическое окисление железосодержащего вещества.
Электрохимическое окисление железосодержащего вещества в расплаве сульфата натрия и/или калия осуществляют переменным током или выпрямленным или переменным током с поляризацией электродов.
Газообразный кислород на второй стадии способа подают непрерывно в составе газовоздушной смеси, содержащей по объему 21-100% кислорода.
Газовоздушную смесь, содержащую газообразный кислород, барботируют через расплав гидроксида натрия или калия для одновременного окисления соединений железа, содержащихся в полупродукте, и перемешивания расплава. Возможен вариант подачи газовоздушной смеси, содержащей кислород, на поверхность расплава.
Для решения поставленной задачи установка, включающая устройство для окисления исходного железосодержащего вещества в расплаве сульфатов щелочных металлов, содержащее корпус для размещения реакционной массы и электроды, согласно изобретению, снабжена устройством для окисления железосодержащего вещества – полупродукта, содержащего оксиды железа (III) и ферриты щелочных металлов, в расплаве гидроксидов щелочных металлов до получения готового продукта, содержащего ферраты (IV) и (VI) щелочных металлов, включающим реакционную камеру с устройством внешнего нагрева, блок управления режимами нагрева и устройство для подачи кислорода в реакционную камеру, а устройство для окисления исходного железосодержащего вещества в расплаве сульфатов щелочных металлов содержит, по меньшей мере, один, железосодержащий съемный электрод и снабжено блоком управления режимами работы электродов.
Корпус устройства для окисления исходного железосодержащего вещества в расплаве сульфатов щелочных металлов может быть выполнен из огнеупорного материала, обладающего свойствами диэлектрика, при этом указанное устройство содержит, по меньшей мере, два электрода, погруженные в расплав, и снабжено средством для подачи и размещения железосодержащего вещества в объеме расплава, образующегося при пропускании через него электрического тока.
Корпус устройства для окисления исходного железосодержащего вещества в расплаве сульфатов щелочных металлов может быть выполнен металлическим, например, из стали, и является при этом одним из электродов, причем, по крайней мере, один, железосодержащий съемный электрод расположен над корпусом, для создания ограниченной зоны расплава при пропускании через расплав электрического тока, размеры которой достаточны для формирования в расплаве реакционной массы полупродукта, содержащего оксид железа (III) и ферриты щелочных металлов.
Корпус устройства для окисления исходного железосодержащего вещества может быть выполнен в виде металлической монолитной плиты произвольной формы с замкнутой прямоугольной, или трапециевидной, или овальной выемкой для размещения реакционной массы.
Возможно выполнение корпуса устройства для окисления исходного железосодержащего вещества в виде бруска, имеющего вытянутую по длине бруска выемку прямоугольной, или трапециевидной, или овальной формы для размещения реакционной массы.
По меньшей мере, один электрод установлен в корпусе устройства для окисления исходного железосодержащего вещества с возможностью взаимного перемещения относительно корпуса и/или других электродов в горизонтальной и вертикальной плоскостях для изменения положения и размеров зоны расплава и/или изменения электросопротивления расплава.
Устройство для окисления исходного железосодержащего вещества в расплаве сульфатов щелочных металлов снабжено дозирующим устройством для подачи железосодержащего вещества и/или сульфатов щелочных металлов, установленным перед, по меньшей мере, одним из электродов.
Электроды могут быть расположены вертикально, при этом дозирующее устройство для подачи железосодержащего вещества и/или сульфатов щелочных металлов установлено с возможностью размещения железосодержащего вещества на дне корпуса.
По меньшей мере, один электрод может быть расположен горизонтально, при этом дозирующее устройство для подачи железосодержащего вещества и/или сульфатов щелочных металлов установлено с возможностью размещения железосодержащего вещества в объеме расплава на поверхности этого электрода.
Блок управления режимами работы электродов включает трансформатор и блок-преобразователь для управления фазовыми характеристиками электрического тока.
Устройство для окисления исходного железосодержащего вещества в расплаве сульфатов щелочных металлов содержит вспомогательный электрод для начального перевода кристаллических соединений щелочных металлов в расплавленную форму при подключении этого электрода к блоку управления режимами работы электродов.
В качестве реакционной массы в устройстве для окисления исходного железосодержащего вещества в расплаве сульфатов щелочных металлов используют смесь исходного железосодержащего вещества и кристаллических соединений щелочных металлов.
В качестве исходного железосодержащего вещества используют металлическое железо, и/или его сплавы, и/или отходы металлообработки изделий из черных металлов, например, скрап, и/или отходы черной металлургии, а в качестве соединений щелочных металлов используют кристаллические сульфаты натрия и/или калия и/или промышленные отходы, содержащие кристаллические сульфаты натрия и/или калия.
В качестве железосодержащего вещества – полупродукта используют полупродукт, содержащий оксид железа (III) и ферриты щелочных металлов, полученный предварительно в устройстве для окисления исходного железосодержащего вещества в расплаве сульфатов щелочных металлов, а в качестве соединений щелочных металлов используют гидроксиды натрия, и/или калия, и/или промышленные отходы, содержащие гидроксиды натрия и/или калия.
Реакционная камера устройства для окисления железосодержащего вещества – полупродукта, содержащего оксид железа (III) и ферриты щелочных металлов, в расплаве гидроксида натрия или калия может быть выполнена в форме цилиндра или параллелепипеда и установлена вертикально или под углом к вертикальной оси, при этом длина реакционной камеры превышает ее поперечные размеры.
Возможен вариант, когда реакционная камера устройства для окисления железосодержащего вещества – полупродукта, содержащего оксид железа (III) и ферриты щелочных металлов, в расплаве гидроксида натрия и/или калия установлена горизонтально и имеет плоское дно произвольной формы, по которому реакционная масса равномерно распределяется тонким слоем.
Реакционная камера устройства для окисления железосодержащего вещества – полупродукта, содержащего оксид железа (III) и ферриты щелочных металлов, в расплаве гидроксида натрия и/или калия может быть установлена под углом к горизонту для обеспечения, за счет сил гравитации, продвижения реакционной массы вдоль реакционной камеры и одновременного перемешивания реагентов и взаимодействия их с кислородом, содержащимся в газовоздушной смеси, которая подается на поверхность расплава.
Устройство для окисления железосодержащего вещества – полупродукта, содержащего оксид железа (III) и ферриты щелочных металлов, снабжено устройством загрузки полупродукта, и гидроксидов натрия и/или калия и устройством выгрузки хотя бы части готового продукта, содержащего ферраты (IV) и (VI) щелочных металлов.
Установка снабжена устройством, обеспечивающим хранение полупродукта, содержащего оксид железа (III) и ферриты щелочных металлов и его транспортировку в реакционную камеру устройства для окисления полупродукта, содержащего оксид железа (III) и ферриты щелочных металлов в расплаве гидроксидов натрия и/или калия.
Получение ферратов щелочных металлов в две стадии предусматривает на первой стадии окисление металлического железа расплавом сульфатов щелочных металлов до, преимущественно, соединений железа (III) и на второй стадии дальнейшее их окисление кислородом в расплаве гидроксидов щелочных металлов. При осуществлении первой стадии процесса, которая требует применения достаточно высоких температур, снижаются требования к однородности состава получающихся веществ и, как следствие, уменьшаются продолжительность процесса и затраты энергии на проведение реакций, а в качестве исходных веществ могут быть использованы технологические отходы различных производств.
Использование расплава гидроксидов щелочных металлов, имеющих по сравнению с сульфатами щелочных металлов более низкие температуры плавления, позволяет снизить границы температурного интервала, в котором происходит образование ферратов щелочных металлов и, тем самым, уменьшить общее энергопотребление.
Стадия получения полупродукта, содержащего оксид железа (III) и ферриты натрия и/или калия, резко снижает продолжительность процесса окисления железа в расплавах сульфатов натрия и/или калия, т.к. не требует их подачи в расплавленном виде, исключая их предварительное расплавление, не требует снижения массовой доли соединений серы до 1% и не требует непрерывной подачи кислорода в расплав. В результате резко сокращаются затраты энергии и снижаются требования к качеству исходных веществ.
Замена расплавов сульфатов натрия и/или калия на расплавы гидроксидов натрия и/или калия на второй стадии окисления железосодержащего вещества при непрерывной подаче кислорода позволяет снизить температуру получения целевого (готового) продукта и повысить его окислительную способность за счет образования смеси ферратов (IV) и (VI) натрия и/или калия.
Для сокращения энергозатрат окисление железосодержащего вещества в расплаве сульфатов натрия и/или калия осуществляется в реакционной камере при отсутствии устройства для барботирования газовоздушной смеси. Окисление, в соответствии с реакциями (2), осуществляют до образования оксидов железа и ферритов натрия и/или калия, а контроль полноты протекания реакций окисления железосодержащего вещества проводят по содержанию окисленных форм железа, что резко сокращает продолжительность процесса окисления железа и/или железного лома по сравнению с прототипом, в котором процесс ведут до достижения остаточного содержания сульфатов щелочных металлов 1%.
В отличие от прототипа корпус реакционной камеры может быть выполнен как из диэлектрического материала, так и быть металлическим, например, сделанным из стали, нагрев реакционной массы может осуществляться за счет электрического тока, пропускаемого через расплав, или внешним нагревателем любого типа, например, с помощью теплоэлектронагревателей или газовых горелок, а вместо пакета электродов использован хотя бы один съемный электрод, который изготавливается из теплоэлектронагревателей или газовых горелок, а вместо пакета электродов использован хотя бы один съемный электрод, который изготавливается из металлического лома, что позволяет использовать металлические отходы различных размеров, формы и происхождения.
Блок управления режимами работы электродов позволяет плавно изменять фазовые и амплитудные характеристики переменного тока, глубину погружения хотя бы одного из электродов в расплав соли, а также взаимное положение хотя бы одного из электродов относительно другого или других электродов и/или относительно корпуса.
Блок управления режимами работы электронагревателей позволяет плавно изменять фазовые и амплитудные характеристики переменного тока, поддерживая заданные температурные режимы процесса получения готового продукта.
На фиг.1 представлена схема устройства для окисления исходного железосодержащего вещества в расплаве сульфатов щелочных металлов до получения полупродукта (корпус для размещения реакционной массы выполнен из огнеупорного материала, электроды вертикально расположены в расплаве сульфата щелочного металла).
На фиг.2 представлена схема устройства для окисления исходного железосодержащего вещества в расплаве сульфатов щелочных металлов до получения полупродукта (корпус для размещения реакционной массы выполнен из огнеупорного материала, один или несколько электродов вертикально расположены в расплаве сульфата щелочного металла, один из электродов горизонтально расположен в расплаве).
На фиг.3 представлена схема устройства для окисления исходного железосодержащего вещества в расплаве сульфатов щелочных металлов до получения полупродукта (корпус для размещения реакционной массы выполнен металлическим в виде монолитной плиты (круга) с замкнутой прямоугольной выемкой, электроды вертикально расположены в расплаве сульфата щелочного металла).
На фиг.4 представлена схема устройства для окисления исходного железосодержащего вещества в расплаве сульфатов щелочных металлов до получения полупродукта (корпус для размещения реакционной массы выполнен металлическим в виде бруска с вытянутой по длине трапециевидной выемкой, электроды вертикально расположены в расплаве сульфата щелочного металла).
На фиг.5 представлена схема устройства для окисления полупродукта в расплаве гидроксидов щелочных металлов, содержащего вертикально расположенную реакционную камеру.
На фиг.6 представлена схема устройства для окисления полупродукта в расплаве гидроксидов щелочных металлов, содержащего горизонтально расположенную реакционную камеру.
На фиг.7 представлена схема устройства для окисления полупродукта в расплаве гидроксидов щелочных металлов, содержащего реакционную камеру, расположенную под углом к горизонту.
На фиг.8 представлена схема изогнутой реакционной камеры в устройстве для окисления полупродукта в расплаве гидроксидов щелочных металлов.
На фиг.9 представлена схема наклонной реакционной камеры в устройстве для окисления полупродукта в расплаве гидроксидов щелочных металлов.
На фиг.10 представлена схема наклонной вращающейся реакционной камеры в устройстве для окисления полупродукта в расплаве гидроксидов щелочных металлов.
На фиг.11 представлена форма электрического напряжения сети Uf, которое используется для преобразования в питающее напряжение.
На фиг.12 представлена форма питающего напряжения Ui на выходе блока управления для пакетно-импульсного режима преобразования.
На фиг.13 представлена форма питающего напряжения Ui на выходе блока управления для импульсно-фазового режима преобразования.
На фиг.14 представлена форма питающего напряжения Ui на выходе блока управления для выпрямляющего режима преобразования.
На фиг.15 представлена форма питающего напряжения Ui на выходе блока управления для поляризующего режима преобразования.
На фиг.16 представлен общий вид устройства для окисления исходного железосодержащего вещества в расплаве сульфатов щелочных металлов до получения полупродукта, разрез которого показан на фиг.3 (корпус для размещения реакционной массы выполнен металлическим в виде монолитной плиты (круга) с замкнутой прямоугольной выемкой, электроды вертикально расположены в расплаве сульфата щелочного металла).
На фиг.17 представлен общий вид устройства для окисления исходного железосодержащего вещества в расплаве сульфатов щелочных металлов до получения полупродукта, разрез которого показан на фиг.4 (корпус для размещения реакционной массы выполнен металлическим в виде плоского бруска линейной формы с вытянутой по длине трапециевидной выемкой, электроды вертикально расположены в расплаве сульфата щелочного металла).
Способ получения окислителя на основе ферратов щелочных металлов осуществляют в две стадии. На первой стадии ведут окисление исходного железосодержащего вещества в расплаве сульфатов щелочных металлов при пропускании через расплав электрического тока до получения железосодержащего вещества – полупродукта, содержащего оксиды железа (III) и ферриты щелочных металлов. На второй стадии осуществляют последующее окисление оксидов железа и ферритов щелочных металлов, содержащихся в полупродукте, в расплаве гидроксидов щелочных металлов, в присутствии кислорода до получения продукта, содержащего ферраты (IV) и (VI) щелочных металлов.
При выборе сырья преимущество отдавалось нетоксичным и недорогим материалам, производимым в достаточных количествах химической промышленностью или образующихся в виде отходов в металлургических и металлообрабатывающих технологиях. На первой стадии процесса окисления в качестве исходного железосодержащего вещества используют металлическое сырье в виде металлического железа, и/или его сплавы и/или отходы металлообработки изделий из черных металлов, например, скрап, и/или отходы черной металлургии.
В качестве исходных веществ – сульфатов щелочных металлов – на первой стадии способа используют сульфаты натрия и/или калия, и/или промышленные отходы, содержащие сульфаты натрия и/или калия.
В качестве гидроксидов щелочных металлов на второй стадии способа используют гидроксиды натрия и/или калия и/или промышленные отходы, содержащие гидроксиды натрия и/или калия.
Суммарный процесс превращения сульфата натрия и стальных электродов в феррат (IV) натрия представлен следующей схемой:

Окисление железосодержащего вещества осуществляют в фазе расплава. Температурный интервал первой стадии процесса определяется температурами плавления сульфатов натрия, калия, а также продуктов их разложения и составляет 850-1100°С. Ниже 850°С наблюдается загустевание реакционной массы, а выше 1100°С происходит образование магнетита, который в дальнейшем практически не поддается переводу в ферраты (IV) и (VI) щелочных металлов.
Основные реакции, связанные с окислением железосодержащего вещества в расплаве сульфатов натрия и/или калия приводят к образованию смеси, содержащей преимущественно оксид железа (III), ферриты натрия и/или калия и оксиды натрия и/или калия:

Продукт окисления железа в расплаве сульфата натрия и/или калия после охлаждения представляет собой поликристаллический многокомпонентный сплав, состав которого зависит от исходного отношения (Na,K)2SO4:Fe, температуры и продолжительности взаимодействия железа с расплавами сульфатов щелочных металлов.
Первую стадию ведут до достижения массовой доли соединений железа (III) в полупродукте 4-39%, в пересчете на железо. Содержание железа в полупродукте контролируется химическими методами анализа.
В основе процессов, протекающих на первой стадии, лежат химические реакции взаимодействия металлического железа в расплаве (Na,K)2SO4 в соответствии с уравнением (2). В простейшем случае для проведения этих реакций требуется расплав, для получения которого используется косвенный нагрев от независимого источника тепла, например муфельная или шахтная или тоннельная печи. В заявляемом способе осуществляется электрохимическое окисление железного анода в указанных расплавах, причем электрический ток используется одновременно для поддержания необходимой температуры расплава.
В заявляемом способе реализованы два варианта первой стадии, различающиеся условиями окисления железосодержащего вещества в расплаве сульфатов натрия или калия – электрохимическое растворение железного анода, который изготавливается из железосодержащего вещества, например, лома черных металлов и комбинация химического и электрохимического окисления железа.
Электрический ток обеспечивает прямой нагрев реакционной массы, поддерживая необходимую температуру расплава, и служит для интенсификации процессов окисления металлического железа.
Для электрохимического растворения железа используют выпрямленный или переменный ток любой конфигурации. В случае использования выпрямленного тока окислению подвергается электрод из железосодержащего вещества, соединенный с положительным полюсом внешнего источника тока, а при использовании знакопеременного тока окисляется электрод (анод), на который подается положительный импульс или положительная полуволна.
В результате окисления железного анода в расплаве последовательно образуются соединения железа (II) и железа (III).
Одновременно с окислением железосодержащего вещества на аноде происходит разложение сульфат-ионов. Образующиеся в результате этих процессов оксид серы (VI) и кислород ускоряют растворение металлического железа в расплаве сульфатов натрия и калия.
Электрод, который поляризован отрицательно (катод) является инертным, и материал, из которого он изготовлен, электрохимическому окислению не подвергается и расходуется только в результате окисления кислородом воздуха. Основные реакции, которые протекают в катодном пространстве, связаны с восстановлением сульфат-ионов в соответствии со схемой (3)
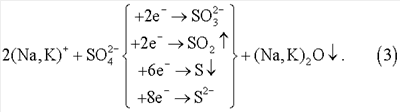
В объеме расплава из образующихся катионов и анионов формируются оксиды и сульфиды железа (II) и железа (III), оксиды щелочных металлов, сульфаты и сульфиты железа (III), сульфит и сульфиды щелочных металлов. Между катионами железа (II) и сульфат-ионами протекают реакции, приводящие к образованию феррит-ионов:

которые после охлаждения образуют ферриты щелочных металлов.
Поскольку реакции осуществляются в атмосферном воздухе, образующиеся феррит-ионы в присутствии кислорода частично окисляются до феррат(IV)-анионов:

соответствующих образованию ферратов (IV) щелочных металлов.
В условиях проведения первой стадии процесса реакция (5) протекает с небольшим выходом ферратов щелочных металлов, и в дальнейшем они рассматриваются как примеси, существенно не влияющие на качество образующегося полупродукта, хотя и облегчающие проведение второй стадии получения реагента-окислителя.
Комбинация химического и электрохимического окисления железа является предпочтительным вариантом первой стадии осуществления способа. Электрический ток одновременно используется для окисления железного анода, который может быть выполнен из железосодержащего вещества, например железного лома, и для поддержания необходимой температуры расплава, в котором растворяется железосодержащее вещество в виде технологических отходов, например отходов металлообработки железа и его сплавов, в частности стружки или сыпучих полидисперсных металлических масс.
Для электрохимического растворения железа используется выпрямленный или переменный ток любой конфигурации. Протекающий через расплав электрический ток увеличивает скорость химического окисления железа сульфатом натрия или калия. Для уменьшения поляризационных процессов, связанных с накоплением вблизи поверхности растворяемого железосодержащего вещества продуктов электролиза, которые замедляют окисление металлического железа, предпочтительно использовать знакопеременную форму тока или комбинацию переменного тока с частичной поляризацией одного из электродов выпрямленным напряжением.
Особенности комбинированного химического и электрохимического взаимодействия железосодержащего вещества с расплавом сульфатов щелочных металлов связаны с направленным перемещением ионов в расплаве электролита, что приводит к росту скорости окисления металлического железа. Также в результате катодного восстановления катионов щелочных металлов в объеме расплава образуются металлические натрий и калий, окисляющиеся при контакте с кислородом воздуха до пероксида Na2O2 и надпероксида КО2, которые обладают сильными окислительными свойствами и ускоряют окисление железосодержащего вещества.
По окончании первой стадии окисления железосодержащего вещества в расплаве сульфата натрия и/или калия образуется полупродукт, содержащий преимущественно оксид железа (III) и ферриты натрия и/или калия. Полупродукт применяется в качестве железосодержащего вещества на второй стадии процесса для получения ферратов (IV) и (VI) натрия и/или калия, как в виде расплавленной массы непосредственно после окончания первой стадии процесса, так и в виде кристаллической массы по истечении любого интервала времени после охлаждения. Охлажденный полупродукт представляет собой поликристаллический многокомпонентный сплав от темно-бурой до темно-коричневой окраски. Основу полупродукта составляет поликристаллическая смесь оксида железа (III) и ферритов натрия и калия, содержащая в виде примесей сульфиды, сульфаты и сульфиты железа, оксиды, сульфаты, сульфиты и сульфиды натрия и калия. Полупродукт содержит также ферраты (IV) натрия и калия, которые облегчают протекание второй стадии получения реагента-окислителя на основе ферратов (IV) и (VI) щелочных металлов.
Срок хранения полупродукта не ограничен, что позволяет накапливать его в необходимых количествах, транспортировать на любые расстояния и использовать по мере необходимости. Перед применением кристаллический полупродукт рекомендуется измельчать.
На второй стадии процесса получения ферратов (IV) и (VI) щелочных металлов в качестве железосодержащего вещества используют полупродукт, содержащий соединения железа (III) в виде оксида железа (III) и ферритов натрия и/или калия, а в качестве соединений щелочных металлов используют гидроксиды натрия и/или калия, и/или промышленные отходы, содержащие гидроксиды натрия и/или калия. Вторая стадия осуществляется в расплаве при непрерывной подаче кислорода в объем или на поверхность расплава в составе газовоздушной смеси, содержащей по объему 21-100% газообразного кислорода.
Протекающие на второй стадии реакции превращения железосодержащего вещества в расплаве при непрерывной подаче кислорода приводят к образованию смеси, содержащей ферраты (IV) и (VI) натрия и калия

Поскольку гидроксиды натрия и калия имеют значительно меньшие температуры плавления, по сравнению с сульфатами натрия и калия, окисление железосодержащего вещества на второй стадии процесса осуществляют при более низких температурах расплава, что резко снижает расход энергии на осуществление всего процесса. Температурный интервал второй стадии процесса составляет 640-880°С. Ниже 640°С скорости реакций становятся настолько малыми, что процесс образования ферратов (IV) и (VI) практически прекращается, а выше 880°С происходит термическое разложение образующихся ферратов (IV) и (VI) щелочных металлов.
Вторую стадию ведут до достижения массовой доли соединений железа (IV) и (VI) в продукте 2,7-21,8%, в пересчете на железо (VI). Содержание окисленных форм железа в продукте контролируется химическими и спектрофотометрическими методами анализа.
Заявляемая установка для получения окислителя на основе ферратов щелочных металлов обеспечивает получение окислителя на основе ферратов (IV) и (VI) щелочных металлов в две стадии и включает устройство для окисления исходного железосодержащего вещества в расплаве сульфатов щелочных металлов до получения полупродукта, содержащего оксиды железа (III) и ферриты щелочных металлов, и устройство для окисления полупродукта, содержащего оксид железа (III) и ферриты щелочных металлов, в расплаве гидроксидов щелочных металлов.
Устройство для окисления исходного железосодержащего вещества в расплаве сульфатов щелочных металлов (фиг.1, 2, 3, 4) содержит корпус 1 для размещения реакционной массы, электроды 2, по меньшей мере, один их которых является железосодержащим съемным электродом, вспомогательный электрод 3, блок управления 4 режимами работы электродов 2 и 3, дозирующее устройство 5. Электроды 2 установлены в расплаве вертикально (фиг.1). В качестве варианта один из электродов 2 может быть установлен в объеме расплава горизонтально (фиг.2). Блок управления 4 включает понижающий трансформатор и преобразователь, которые обеспечивают пакетно-импульсный или импульсно-фазовый режим Ui работы электродной системы.
Корпус 1 может быть выполнен как из огнеупорного материала, обладающего свойствами диэлектрика, и/или из металла, футерованного диэлектрическим материалом, стойким в расплавах сульфатов щелочных металлов (фиг.1, 2), так и быть металлическим, например, сделанным из стали (фиг.3, 4). В качестве химически стойкого диэлектрика может быть использован специальный кирпич, алунд, цирконаты и другие керамические материалы.
Нагрев реакционной массы осуществляется за счет электрического тока, пропускаемого через расплав. Блок управления 4 режимами работы электродов позволяет плавно изменять фазовые и амплитудные характеристики переменного тока, глубину погружения хотя бы одного из электродов в расплав соли, а также взаимное положение хотя бы одного из электродов 2 относительно другого или других электродов и/или относительно корпуса 1.
Устройство для окисления железосодержащего вещества в расплаве солей щелочных металлов, например, сульфата натрия и/или калия может работать как в непрерывном, так и в периодическом режимах.
На фиг.1, 2 представлено вышеуказанное устройство, в котором осуществляется электрохимическое окисление анода, изготовленного из железосодержащего вещества, например лома черных металлов, в расплаве {Na,K)2SO4 в соответствии с реакциями (2) с прямым нагревом реакционной камеры электрическим током, пропускаемым через расплав. Устройство содержит корпус 1, который выполнен из диэлектрического материала или футерован диэлектрическим материалом, стойким в расплавах сульфатов щелочных металлов. Блок управления 4 включает понижающий трансформатор и преобразователь, которые обеспечивают пакетно-импульсный или импульсно-фазовый режим Ui работы электродной системы. Электроды 2 в виде стержней или пластин различного профиля располагаются в массе сульфата натрия и/или калия. Начальная стадия процесса связана с получением расплава кристаллических солей, для чего используется вспомогательный электрод 3, удаляемый в ходе основного процесса. Два или более электродов 2 располагаются в объеме расплава вертикально или под углом предпочтительно 0-60 градусов к вертикальной оси, таким образом, что с расплавом контактирует только часть электродов, которая подвергается анодному растворению (фиг.1).
Возможно расположение электродов, когда один электрод постоянно погружен в расплав и располагается горизонтально или под углом предпочтительно 0-20 градусов к горизонтальной оси, а другой электрод или любое число электродов располагается в объеме расплава вертикально или под углом предпочтительно 0-60 градусов к вертикальной оси, таким образом, что с расплавом контактирует только часть электродов (фиг.2).
В устройстве для окисления железосодержащего вещества в расплаве сульфата натрия и/или калия, в котором осуществляется процесс комбинированного химического и электрохимического окисления железосодержащего вещества в расплаве (Na,K)2SO4 с прямым нагревом реакционной камеры электрическим током, пропускаемым через расплав (фиг.1, 2), электроды 2 в виде стержней или пластин различного профиля располагаются в массе сульфата натрия и/или калия, смешанной с измельченным железосодержащим веществом, взятым в виде опилок, стружки, листовых обрезков, проволоки и других железосодержащих отходов с развитой поверхностью, обеспечивающей достаточно высокую скорость протекания реакций (2). При этом два или большее число электродов располагаются в объеме расплава вертикально или под углом предпочтительно 0-60 градусов к вертикальной оси, таким образом, что с расплавом контактирует только часть электродов, которая подвергается анодному растворению (фиг.1), а измельченное железосодержащее вещество, участвующее в химическом растворении, с помощью дозирующего устройства 5 подается в расплав и концентрируется преимущественно в межэлектродном пространстве на дне диэлектрического реакционной камеры, не касаясь электродов.
Возможен вариант, когда один электрод постоянно погружен в расплав и располагается горизонтально или под углом предпочтительно 0-20 градусов к горизонтальной оси, другой электрод или любое число электродов располагается в объеме расплава вертикально или под углом предпочтительно 0-60 градусов к вертикали, таким образом, что с расплавом контактирует только часть электродов (фиг.2), а измельченное железосодержащее вещество, участвующее в химическом растворении, с помощью дозирующего устройства 5 подается в расплав и концентрируется на токопроводящей поверхности горизонтального электрода.
Вариант устройства для окисления исходного железосодержащего вещества в расплаве солей щелочных металлов, в котором корпус 1 для размещения реакционной массы выполнен металлическим, например из стали, представлен на фиг.3, 4. При этом корпус 1 выполняет функцию одного из электродов и выполнен или в виде монолитной плиты (круга) с замкнутой прямоугольной выемкой (фиг.3), или в виде в виде бруска с вытянутой по длине трапециевидной выемкой – желобом 6 (фиг.4). Возможны варианты выполнения корпуса в виде бруска с вытянутой по длине выемкой – желобом прямоугольной или овальной формы в поперечном разрезе.
Желоб 6 предназначен для размещения реакционной массы в виде смеси сульфата натрия и/или калия, смешанного с измельченным железосодержащим веществом, взятым в виде опилок, стружки, листовых обрезков, проволоки и других железосодержащих отходов с развитой поверхностью, обеспечивающей достаточно высокую скорость протекания реакции (2). Электроды вертикально расположены в расплаве сульфата щелочного металла.
Блок 4 управления включает понижающий трансформатор и преобразователь, которые обеспечивают пакетно-импульсный или импульсно-фазовый режим Ui работы электродной системы. Один или несколько электродов 2 в виде стержней или пластин различного профиля располагаются вдоль желоба 6 в реакционной массе и имеют возможность взаимного перемещения относительно корпуса 1 и/или других электродов 2 в горизонтальной и вертикальной плоскостях для изменения положения и размеров зоны расплава и изменения электросопротивления расплава, необходимых для обеспечения непрерывности процесса. Для получения расплава кристаллических солей на начальной стадии процесса используется вспомогательный электрод 3, удаляемый в ходе основного процесса.
В процессе окисления железосодержащего вещества в расплаве (Na,K)2SO4 осуществляют взаимное перемещение хотя бы одного из электродов 2 относительно расположенного на корпусе 1 желоба 6, в результате чего происходит перемещение зоны расплава, в которой происходит электрохимическое окисление электрода, являющегося анодом, и химическое окисление измельченного железосодержащего вещества, смешанного с сульфатом натрия и/или калия, так, что новые порции исходной смеси подвергаются плавке и участвуют в окислительных процессах, а окисленные вещества при охлаждении кристаллизуются.
Полученный полупродукт, содержащий преимущественно оксид железа (III) и ферриты натрия и/или калия, выгружается из желоба 6, а новые порции смеси исходных веществ непрерывно подаются в желоб и равномерно распределяются в нем с помощью дозирующего устройства 5, которое устанавливается, как правило, перед электродом 2, осуществляющим расплавление исходной смеси сульфата натрия и/или калия и железосодержащего вещества.
Полупродукт в дальнейшем применяется в качестве железосодержащего вещества на второй стадии процесса для получения ферратов (IV) и (VI) натрия и/или калия, как в виде расплавленной массы непосредственно после окончания первой стадии процесса, так и в виде кристаллической массы по истечении любого интервала времени после охлаждения.
Устройство для окисления полупродукта, содержащего оксид железа (III) и ферриты щелочных металлов (фиг.5, 6, 7), в расплаве гидроксидов щелочных металлов содержит реакционную камеру 7 с устройством 8 внешнего нагрева, например, газовыми горелками или теплоэлектронагревателями, блок управления 9 режимами нагрева, который преобразует пакетно-импульсным или импульсно-фазовым способом переменное напряжение промышленной частоты Uf в напряжение Ui, подаваемое на нагревательные элементы и устройство 10 для подачи кислорода в реакционную камеру 7.
Кроме этого различные варианты устройства могут содержать устройства 5 для загрузки исходных веществ и выгрузки 11 продукта (фиг.7).
Устройства для окисления полупродукта, содержащего оксид железа (III) и ферриты щелочных металлов, в расплаве гидроксидов щелочных металлов могут различаться конструктивными особенностями реакционной камеры.
На фиг.5 представлено устройство для осуществления второй стадии способа с реакционной камерой 7 цилиндрической или прямоугольной формы, у которой длина превышает поперечные размеры, расположенной вертикально или под углом, как правило, 0-20 градусов, к горизонту.
Корпус реакционной камеры 7 выполнен из металла, например из нержавеющей стали, стойкой к термической коррозии в присутствии расплавов гидроксидов щелочных металлов. Реакционная камера 7 закрыта съемной крышкой, предотвращающей разбрызгивание расплава (не показана). Реакционная камера 7 помещена в шахтную печь с вертикально расположенными электронагревателями 8. Блок управления 9 работает в пакетно-импульсном или импульсно-фазовом режимах и преобразует переменное напряжение промышленной частоты Uf в последовательность импульсов Ui, которая обеспечивает необходимый температурный режим работы электронагревателей. Устройство 10 для подачи газовоздушной смеси, содержащей кислород, включает компрессор, баллон с кислородом и систему трубок, которые опущены в расплавленную реакционную массу и обеспечивают барботирование газовоздущной смеси через объем расплава. При барботировании осуществляется доставка в реакционную массу кислорода, необходимого для протекания реакции (6), и перемешивание реакционной массы. В этом случае газовоздушную смесь, содержащую кислород, непрерывно барботируют через расплав гидроксида натрия и/или калия для одновременного окисления соединений железа, содержащихся в полупродукте, и перемешивания расплава. Высота расплава превышает поперечные линейные размеры реакционной камеры и достаточна для взаимодействия кислорода с компонентами расплава через поверхность пузырька газа.
На фиг.6 представлено устройство для осуществления второй стадии способа с горизонтально расположенной реакционной камерой произвольной формы с плоским дном, по которому тонким слоем равномерно распределяется реакционная масса.
Корпус реакционной камеры 7 выполнен из металла, например из нержавеющей стали. Реакционная камера помещена в муфельную или тоннельную печь с горизонтально расположенными электронагревателями 8. Блок управления 9 работает в пакетно-импульсном или импульсно-фазовом режимах. Устройство 10 для подачи газовоздушной смеси, содержащей кислород, включает компрессор, баллон с кислородом и систему трубок, которые располагаются над поверхностью расплавленной реакционной массы и обеспечивают доставку кислорода, входящего в состав газовоздушной смеси и необходимого для протекания реакции (6), к поверхности расплава. Перемешивание реакционной массы осуществляется за счет конвекционных потоков, поскольку температуры стенок реакционной камеры и различных участков расплава различаются. В этом случае высота расплава значительно меньше линейных размеров реакционной камеры и достаточна для перемешивания компонентов расплава за счет конвекционных потоков. В качестве реакционной камеры может использоваться лоток цилиндрической, прямоугольной или более сложной формы. В указанной реакционной камере, высота которой значительно меньше ее линейных размеров, подача газовоздушной смеси осуществляется на поверхность расплавленной реакционной массы. Кислород взаимодействует с компонентами расплава благодаря тому, что поверхность реакционной массы находится в контакте с газовоздушной смесью и эффективно обдувается ею.
На фиг.7 представлено устройство для осуществления второй стадии способа с установленной под углом к горизонту реакционной камерой 7, обеспечивающей за счет сил гравитации продвижение реакционной массы вдоль реакционной камеры и непрерывность процесса.
Корпус реакционной камеры 7 выполнен из металла, например из нержавеющей стали. Форма и конструкция реакционной камеры обеспечивают одновременно перемешивание реагентов и взаимодействие с кислородом, содержащимся в газовоздушной смеси, подаваемой в реакционную камеру с помощью устройства 10, включающего баллон с кислородом и компрессор. Реакционная камера 7 снабжена загрузочным устройством 5, которое обеспечивает непрерывную подачу исходной смеси полупродукта и гидроксидов натрия и/или калия. Реакционная камера помещена в муфельную или тоннельную печь. Блок управления 9 работает в пакетно-импульсном или импульсно-фазовом режимах. При расположении реакционной камеры под углом к горизонту подача газовоздушной смеси в объем или на поверхность расплавленной реакционной массы осуществляется с возможностью постоянного или периодического продвижения реакционной массы, обеспечивающего ее эффективное перемешивание.
В этом случае под действием гравитационных сил происходит перемещение вдоль реакционной камеры расплавленной реакционной массы с одновременным ее эффективным перемешиванием, обеспечивая непрерывность процесса окисления. Газовоздушная смесь подается в объем или на поверхность расплавленной реакционной массы, а кислород, входящий в ее состав, эффективно взаимодействует с компонентами расплава благодаря тому, что реакционная масса перемешивается в процессе перемещения вдоль реакционной камеры.
По форме и конструкции реакционная камера может быть выполнена по крайней мере в трех вариантах.
1. Реакционная камера прямоугольного, или кругового, или овального сечения, изогнутая таким образом, что вдоль продвижения реакционной массы образуется колено, в полости которого происходит задержка реакционной массы на интервал времени, необходимый для формирования готового продукта (фиг.8).
2. Реакционная камера прямоугольного, или кругового, или овального сечения, имеющая вдоль продвижения реакционной массы две или большее число перегородок, выполняющих функции сифона, в полости которого происходит задержка реакционной массы на интервал времени, необходимый для формирования готового продукта (фиг.9).
3. Реакционная камера прямоугольного, или кругового, или овального сечения, имеющая вдоль продвижения реакционной массы одну, две или большее число перегородок, которые делят объем реакционной камеры на две, три или большее число полостей, в которых происходит задержка реакционной массы на интервал времени, необходимый для формирования продукта, а перемещение реакционной массы из одной полости в другую происходит в результате того, что реакционная камера приводится внешним механическим устройством во вращательное или колебательное движение (фиг.10).
Загрузочное устройство 5 (фиг.7, 8, 9, 10) обеспечивает равномерное смешение полупродукта с гидроксидами натрия и/или калия. Были использованы три варианта получения смеси полупродукта с гидроксидами натрия и/или калия.
1. Предварительно измельченный полупродукт с помощью обычных смесителей смешивается с поликристаллическими гидроксидами натрия и/или калия, и полученная смесь устройством 5 подается в реакционную камеру 7.
2. Полупродукт, предпочтительно измельченный, смешивается в устройстве 5 при температурах 320-640°C с расплавом гидроксидов натрия и/или калия, и полученная смесь подается в реакционную камеру 7.
3. Полупродукт, предпочтительно измельченный, загружается устройством 5 при температурах 640-880°С в расплав гидроксидов натрия и/или калия, которые непрерывно подаются в реакционную камеру тем же устройством.
В процессе обработки реакционной массы на второй стадии возможно варьирование интервалами температур в процессе подачи смеси полупродукта и гидроксида натрия и/или калия в зону нагрева, в процессе формирования ферратов (IV) и (VI) натрия и/или калия и в процессе выгрузки продукта.
1. Смесь полупродукта и гидроксида натрия и/или калия выдерживается при 640-660°С в течение интервала времени, необходимого для разложения по массе не менее 50% соединений серы и удаления их из реакционной массы в виде газообразного SO2. Далее реакционная масса выдерживается при температуре 700-780°С до достижения необходимого содержания ферратов (IV) и (VI) натрия и калия и выгружается в условиях быстрого охлаждения расплава.
2. Смесь полупродукта и гидроксида натрия и/или калия выдерживается при 700-780°С до достижения необходимого содержания ферратов (IV) и (VI) натрия и калия. Далее реакционная масса выдерживается при температуре 640-660°С в течение интервала времени, необходимого для разложения по массе не менее 50% соединений серы и удаления их из реакционной массы в виде газообразного SO2, после чего продукт выгружается в условиях быстрого охлаждения расплава.
3. Смесь полупродукта и гидроксида натрия и/или калия выдерживается при 640-660°С в течение интервала времени, необходимого для разложения по массе не менее 50% соединений серы и удаления их из реакционной массы в виде газообразного SO2, после чего реакционная масса выдерживается при температуре 700-780°С до образования не менее 3% ферратов (IV) и (VI) натрия и калия, в пересчете на массовую долю железа. Далее реакционная масса выдерживается при 640-660°С до достижения необходимого содержания ферратов (IV) и (VI) натрия и калия и выгружается в условиях быстрого охлаждения расплава.
Блок управления 9, служащий для изменения мощности тока, используемого для регулировки температуры термоэлектронагревателей (фиг.5, 6, 7), содержит тиристорный преобразователь, управляемый датчиками температуры. Напряжение промышленной частоты Uf (фиг.11) поступает на вход блока управления, который может работать в пакетно-импульсном или импульсно-фазовом режиме. В случае пакетно-импульсного режима преобразованное напряжение на выходе блока управления представляет собой серии из одного, двух или большего числа синусоидальных импульсов (фиг.12), при этом выделяемая на нагрузке мощность определяется как числом синусоидальных импульсов в каждой серии, так и скважностью серий импульсов. В случае импульсно-фазового режима преобразованное напряжение на выходе блока управления представляет собой серию знакопеременных импульсов Ui, полученных фазовой регулировкой входного напряжения Uf (фиг.13), при этом выделяемая на нагрузке мощность определяется амплитудой и скважностью импульсов Ui.
Блок управления 4, служащий для подключения электродной системы (фиг.2, 3, 4), содержит понижающий трансформатор, предназначенный для согласования поступающего на вход блока блока управления напряжения промышленной частоты
Uf (фиг.11) с низкоомной нагрузкой сопротивления расплава, и тиристорный преобразователь, управляемый датчиками температуры. Преобразованное напряжение Ui (фиг.12, 13, 14, 15) соответствует пакетно-импульсному, или импульсно-фазовому, или выпрямляющему, или поляризующему режиму. В случае пакетно-импульсного режима преобразованное напряжение на выходе блока управления представляет собой серии из одного, двух или большего числа синусоидальных импульсов Ui (фиг.12), при этом выделяемая на нагрузке мощность определяется как числом синусоидальных импульсов в каждой серии, так и скважностью серий импульсов. В случае импульсно-фазового режима напряжение на выходе блока управления представляет собой серию знакопеременных импульсов Ui (фиг.13), полученных фазовой регулировкой преобразованного трансформацией напряжения Uf, при этом выделяемая на нагрузке мощность определяется амплитудой и скважностью импульсов Ui. В случае выпрямляющего режима напряжение на выходе блока управления представляет собой серию униполярных синусоидальных импульсов Ui (фиг.14), полученных соответствующим преобразованием трансформированного синусоидального напряжения Uf, при этом выделяемая на нагрузке мощность определяется амплитудой импульсов Ui. В случае поляризующего режима напряжение на выходе блока управления представляет собой комбинацию любого из преобразованных напряжений Uf (фиг.11) или Ui (фиг.12, 13) и выпрямленного напряжения Ui (фиг.14), в результате чего происходит поляризация, по крайней мере, одного из электродов за счет постоянного смещения, как показано, например, для синусоидальных импульсов Ui, смещенных в положительную сторону (фиг.15).
Феррат (VI) натрия и/или калия является неустойчивым и разлагается при хранении, в связи с чем готовый продукт – окислитель, в состав которого входят ферраты (IV) и (VI) щелочных натрия и/или калия, производят в количестве, которое соответствует потребностям технологии очистки загрязненных водных растворов, чтобы исключить продолжительное хранение продукта, а также осуществляют производство вблизи от места потребления, чтобы сократить время на его транспортировку. При организации технологии очистки загрязненных водных растворов на крупных специализированных предприятиях, например на очистных сооружениях, целесообразно совмещение первой и второй стадии в одной установке. При этом расплавленная масса полупродукта без охлаждения до комнатной температуры передается в вязкотекучем состоянии на вторую стадию в расплав гидроксида натрия и/или калия.
Возможно первую стадию производства полупродукта осуществлять отдельно от второй стадии получения готового продукта, накапливать полупродукт и расходовать его по мере необходимости для обеспечения второй стадии получения реагента-окислителя и непрерывности технологии очистки воды. Такой вариант целесообразен при создании небольшого по масштабам производства готового продукта непосредственно на месте его применения, использующего устройства модульного типа, которые легко подвергаются транспортировке и монтажу без значительных капитальных затрат.
Примеры выполнения способа
Пример 1. Получение полупродукта в реакционной камере из шамотного кирпича (вертикальные электроды).
Берут 500 г сульфата натрия декагидрата Na2SO4·10H2O и помещают его в реакционную камеру 1 с вертикально расположенными плоскими электродами 2 (фиг.2). На электроды подается переменное синусоидальное напряжение и с помощью специального устройства в виде вспомогательного электрода 3 получают расплав сульфата натрия. С помощью блока управления 4 задается на электродах преобразованное пакетно-импульсное напряжение Ui (фиг.12), чтобы мощность, выделяемая током, обеспечивала температуру расплава 940±60°С. Берут 90 г железосодержащего вещества в виде железной стружки, что соответствует примерно эквимолярному отношению Fe:Na2SO4, и помещают его в расплав, таким образом, чтобы железосодержащее вещество не касалось электродов 2. Процесс окисления железосодержащего вещества проводят в течение 15 минут, после чего расплавленную массу выгружают в устройство для хранения и транспортировки полупродукта, где происходит кристаллизация полупродукта.
Масса образовавшегося полупродукта составляет 270 г, что соответствует выходу полупродукта относительно массы исходного железосодержащего вещества и безводного сульфата натрия 87%. Содержание соединений железа (III) в полупродукте, найденное методами химического анализа, составляет 27,3%.
Массовая доля соединений железа (III) в полупродукте в пересчете на железо, найденная методами химического и рентгеновского анализов, составляет 27,3%, в том числе, оксидов железа (III) – 3,1% и ферритов натрия 60,2%.
Пример 2. Получение полупродукта аналогично примеру 1, за исключением температуры процесса, которая в данном опыте составляет 1040±60°С.
Процесс растворения железосодержащего вещества проводят в течение 12 минут, после чего расплавленную массу выгружают в устройство для хранения и транспортировки полупродукта, где происходит кристаллизация полупродукта.
Масса образовавшегося полупродукта составляет 276 г, что соответствует выходу полупродукта относительно массы исходного железосодержащего вещества и безводного сульфата натрия 89%. Содержание соединений железа (III) в полупродукте, найденное методами химического анализа, составляет 27,5%.
Массовая доля соединений железа (III) в полупродукте в пересчете на железо, найденная методами химического и рентгеновского анализов, составляет 27,5%, в том числе оксидов железа (III) – 3,3% и ферритов натрия 60,3%.
Берем 500 г гидроксида натрия и помещаем его в реакционную камеру, выполненную в виде стального цилиндра, установленного вертикально в шахтной печи с нихромовыми электронагревателями (фиг.5). С помощью блока управления подаем на электроды пульсирующее напряжение (фиг.12) таким образом, чтобы скважность синусоидальных импульсов обеспечивала мощность тока через электронагреватели, обеспечивающую температуру расплава 650±10°С. Устанавливаем в объеме расплава устройство для подачи воздуха от компрессора и подаем его под давлением, достаточным для барботирования, в нижнюю часть расплава гидроксида натрия. Берем 125 г полупродукта, полученного на стадии 1, что составляет четверть от массы гидроксида натрия, и вводим его в расплав гидроксида натрия при непрерывном барботировании расплава воздухом.
Процесс получения готового продукта, содержащего ферраты (IV) и (VI) натрия, осуществляем в изотермическом режиме при постоянной подаче в расплавленную массу воздуха в течение 90 минут. По истечении указанного времени отключаем питание электронагревателей, вынимаем реакционную камеру с продуктом в виде вязкотекучей массы из обогреваемого объема печи, переворачиваем реакционную камеру и выгружаем образовавшийся продукт в стальной поддон, используя механические приспособления для отделения его от стенок. После охлаждения продукта до 40-70°С переносим его в пластиковую тару и закрываем герметично пробку, во избежание контакта атмосферной влаги с ферратами щелочных металлов.
Масса образовавшегося продукта составляет 405 г, что соответствует выходу продукта относительно массы исходного железосодержащего вещества и гидроксида натрия 79%. Содержание ферратов (IV) и (VI) натрия в продукте, в пересчете на
Na2FeO4, составляет 31,4% или 10,6% в пересчете на железо (VI).
Пример 3. Получение полупродукта в реакционной камере из шамотного кирпича (горизонтальный электрод) (фиг.2); получение готового продукта в горизонтально расположенной прямоугольной реакционной камере (подача воздуха на поверхность расплава) (фиг.6).
Количество и условия получения расплава сульфата натрия такие же, как в примере 1. С помощью блока управления 4 подают на электроды выпрямленное напряжение (фиг.14) таким образом, чтобы горизонтальный электрод 2 был поляризован анодно. Задают силу тока 105 А таким образом, чтобы выделяемая им мощность обеспечивала температуру расплава 940±60°С. Берут 130 г железосодержащего вещества в виде железной стружки, что соответствует молярному отношению Fe:Na2SO4 1,5, и помещают его в расплав таким образом, чтобы железосодержащее вещество равномерно располагалось на горизонтальном электроде 2. Процесс окисления железосодержащего вещества проводят в течение 12 минут, после чего расплавленную массу выгружают в устройство для хранения и транспортировки полупродукта, где происходит кристаллизация полупродукта.
Масса образовавшегося полупродукта составляет 287 г, что соответствует выходу полупродукта относительно массы исходного железосодержащего вещества и безводного сульфата натрия 82%. Содержание соединений железа (III) в полупродукте, найденное методами химического анализа, составляет 36,2%.
Массовая доля соединений железа (III) в полупродукте в пересчете на железо, найденная методами химического и рентгеновского анализов, составляет 36,2%, в том числе, оксидов железа (III) – 5,7% и ферритов натрия 77,2%.
Охлажденный полупродукт измельчался и в виде мелкокристаллической массы использовался для проведения второй стадии в течение одного часа после его получения.
Берем 500 г гидроксида калия и помещаем его в реакционную камеру, выполненную в виде стальной прямоугольной ванны с плоским дном (фиг.6), установленной горизонтально в муфельной печи с нихромовыми электронагревателями 7. С помощью блока управления подаем на электроды последовательность знакопеременных импульсов (фиг.13) таким образом, чтобы скважность и амплитуда импульсов обеспечивала мощность тока через электронагреватели, обеспечивающую температуру расплава 950±10°С. Устанавливаем над поверхностью расплава устройство для подачи воздуха от компрессора и подаем его со скоростью, достаточной для отвода образующихся летучих соединений серы. Берем 125 г измельченного полупродукта, полученного на стадии 1, и вводим его в расплав гидроксида калия при непрерывной подаче воздуха на поверхность расплава.
Процесс получения продукта, содержащего ферраты (IV) и (VI) натрия и калия, осуществляем в изотермическом режиме при постоянной подаче на поверхность расплава воздуха в течение 70 минут. По истечении указанного времени отключаем питание электронагревателей, вынимаем реакционную камеру с продуктом в виде вязкотекучей массы из обогреваемого объема печи и выгружаем образовавшийся продукт в стальной поддон, используя механические приспособления для отделения его от дна и стенок. После охлаждения продукта до 40-70°С переносим его в пластиковую тару и закрываем герметично пробку, во избежание контакта атмосферной влаги с ферратами щелочных металлов.
Масса образовавшегося продукта составляет 452 г, что соответствует выходу продукта относительно массы исходного железосодержащего вещества и гидроксида натрия 83%. Содержание ферратов (IV) и (VI) натрия и калия в продукте, в пересчете на K2FeO4, составляет 42,5% или 12,0% в пересчете на железо (VI).
Пример 4. Аналогично примеру 3, за исключением температуры первой стадии процесса получения полупродукта, которая в данном опыте составляет 910±60°С, загрузка реакционной камеры на второй стадии смесью кристаллических гидроксида калия и полупродукта и использовании газовоздушной смеси с повышенным содержанием кислорода.
Процесс растворения железосодержащего вещества проводим в течение 18 минут, после чего расплавленную массу выгружаем в стальной поддон, где происходит кристаллизация полупродукта.
Масса образовавшегося полупродукта составляет 273 г, что соответствует выходу полупродукта относительно массы исходного железосодержащего вещества и безводного сульфата натрия 78%. Содержание соединений железа (III) в полупродукте, найденное методами химического анализа, составляет 34,3%.
Массовая доля соединений железа (III) в полупродукте в пересчете на железо, найденная методами химического и рентгеновского анализов, составляет 34,3%, в том числе оксидов железа (III) – 4,4% и ферритов натрия 74,8%.
Охлажденный полупродукт выгружаем из стального поддона в бункер, предназначенный для его сбора и хранения. Полупродукт хранился при комнатных условиях в течение 90 суток, после чего измельчался и в виде мелкокристаллической массы использовался для проведения второй стадии процесса получения продукта.
Берем 500 г гидроксида калия и 125 г измельченного полупродукта, полученного на стадии 1, механически перемешиваем эту смесь и ровным слоем размещаем ее на дне реакционной камеры. С помощью блока управления 9 поддерживаем температуру обогреваемого объема муфельной печи 950±10°С. Помещаем реакционную камеру с реакционной массой в муфельную печь. Устанавливаем над поверхностью реакционной массы устройство для подачи газовоздушной смеси от устройства, включающего компрессор и баллон с газообразным кислородом, и подаем ее со скоростью, достаточной для отвода образующихся летучих соединений серы.
Процесс получения готового продукта, содержащего ферраты (IV) и (VI) натрия и калия, осуществляем в изотермическом режиме при постоянной подаче на поверхность расплава газовоздушной смеси в течение 60 минут. По истечении указанного времени отключаем питание электронагревателей, вынимаем реакционную камеру с продуктом в виде вязкотекучей массы из обогреваемого объема печи и выгружаем образовавшийся продукт в стальной поддон, используя механические приспособления для отделения его от дна и стенок. После охлаждения продукта до 40-70°С переносим его в пластиковую тару и закрываем герметично пробку, во избежание контакта атмосферной влаги с ферратами щелочных металлов.
Масса образовавшегося продукта составляет 441 г, что соответствует выходу продукта относительно массы исходного железосодержащего вещества и гидроксида натрия 81%. Содержание ферратов (IV) и (VI) натрия и калия в продукте, в пересчете на K2FeO4, составляет 46,9% или 13,3% в пересчете на железо (VI).
Пример 5. Получение полупродукта в реакционной камере из стали (неподвижные электроды) (фиг.4); получение продукта в горизонтально расположенной прямоугольной реакционной камере (продвижение реакционной камеры вдоль тоннельной печи) (фиг.6).
Берем 100 г сульфата калия безводного K2SO4 и помещаем его в реакционную камеру, выполненную из стали с трапециевидной выемкой и играющую роль электрода, над которой вертикально расположен второй электрод цилиндрической формы (фиг.4). На электроды подаем переменное синусоидальное напряжение и с помощью специального устройства в виде дополнительного электрода получаем расплав сульфата калия. С помощью блока управления подаем на электроды пульсирующее напряжение (фиг.12) таким образом, чтобы сважность синусоидальных импульсов обеспечивала мощность тока, выделяемую на электродах, достаточную для поддержания температуры расплава 940±60°С. Берем 32 г железосодержащего вещества в виде скоски – гранулообразного отхода производства гвоздей, – что соответствует эквимолярному отношению Fe:K2SO4, и помещаем его в расплав таким образом, чтобы железосодержащее вещество равномерно располагалось на нижнем электроде. Процесс окисления железосодержащего вещества проводим в течение 18 минут, после чего расплавленную массу выгружаем в стальной поддон, где происходит кристаллизация полупродукта.
Масса образовавшегося полупродукта составляет 95 г, что соответствует выходу полупродукта относительно массы исходного железосодержащего вещества и безводного сульфата калия 72%. Содержание соединений железа (III) в полупродукте, найденное методами химического анализа, составляет 4,04%.
Массовая доля соединений железа (III) в полупродукте в пересчете на железо, найденная методами химического и рентгеновского анализов, составляет 4,04%, в том числе оксидов железа (III) – 0,7% и ферритов натрия 8,5%.
В качестве возвратного отхода образуется до 60% железосодержащего гранулированного материала, поскольку сравнительно небольшая поверхность исходной скоски не обеспечивает ее полное окисление в течение времени обработки расплава исходных веществ. Для отделения непрореагировавшего железа охлажденный плав подвергали размолу с помощью шаровой мельницы и далее подвергали классификации. Мелкокристаллические фракции соответствуют полупродукту, а крупные фракции – железосодержащему веществу, которое используется вновь для получения полупродукта.
Охлажденный полупродукт помещаем в бункер, предназначенный для его сбора и хранения. Полупродукт хранился в атмосферных условиях в течение 300 суток, после чего измельчался и в виде мелкокристаллической массы использовался для проведения второй стадии получения продукта.
Берем 400 г гидроксида калия и 200 г измельченного полупродукта, полученного на стадии 1, механически перемешиваем эту смесь и с помощью загрузочного устройства ровным слоем размещаем ее на дне реакционной камеры. С помощью блока управления поддерживаем температуру обогреваемого объема тоннельной печи 850±20°С. Включаем устройство для подачи воздуха от компрессора, которое установлено постоянно вдоль тоннельной печи в верхней ее части и обеспечивает подачу воздуха на поверхность реакционной массы со скоростью, достаточной для отвода образующихся летучих соединений серы, на всем протяжении обогреваемого объема печи. Подаем реакционную камеру с реакционной массой в тоннельную печь с постоянной скоростью, обеспечивающей нахождение реакционной камеры в зоне с установившейся температурой 850±20°С в течение 45 минут. Далее реакционную камеру протягиваем через выходную часть тоннельной печи, в которой происходит частичное остывание реакционной массы до температуры 400-500°С.
Общая продолжительность получения продукта, содержащего феррат (IV) и (VI) калия, в тоннельной печи при перемещении реакционной камеры с постоянной скоростью и при постоянной подаче на поверхность расплава воздуха составляет 70 минут. По истечении указанного времени вынимаем реакционную камеру с продуктом в виде вязкотекучей массы из обогреваемого объема печи и выгружаем образовавшийся продукт в стальной поддон, используя механические приспособления для отделения его от дна и стенок. После охлаждения продукта до 40-70°С переносим его в стальной цилиндр и закрываем его герметично крышкой, используя расплав сургуча, во избежание контакта атмосферной влаги с ферратами щелочных металлов.
Масса образовавшегося продукта составляет 359 г, что соответствует выходу продукта относительно массы исходного железосодержащего вещества и гидроксида натрия 67%. Содержание ферратов (IV) и (VI) калия в продукте, в пересчете на K2FeO4, составляет 9,8% или 2,7% в пересчета на железо (VI).
Пример 6. Получение полупродукта в реакционной камере из стали (верхний электрод перемещается относительно нижнего) (фиг.3); получение готового продукта в горизонтально расположенной прямоугольной реакционной камере (фиг.6) с ее продвижением вдоль тоннельной печи (непрерывная подача расплава полупродукта, образующегося на первой стадии процесса).
Берем 500 г сульфата натрия безводного Na2SO4 и помещаем его в реакционную камеру, выполненную из стали с прямоугольной выемкой и играющую роль электрода, над которой вертикально расположен второй электрод цилиндрической формы (фиг.4), снабженный устройством для его перемещения относительно прямоугольной выемки, заполненной реакционной массой. На электроды подаем переменное синусоидальное напряжение и с помощью специального устройства в виде дополнительного электрода получаем расплав сульфата калия. С помощью блока управления подаем на электроды знакопеременное импульсное напряжение (фиг.13) таким образом, чтобы длительность импульсов обеспечивала мощность тока, выделяемую на электродах, достаточную для поддержания температуры расплава 940±60°С. Берем 240 г железосодержащего вещества в виде скоски, что соответствует эквимолярному отношению Fe:Na2SO4 1,5, и помещаем его в расплав таким образом, чтобы железосодержащее вещество равномерно располагалось по длине желоба. Процесс окисления железосодержащего вещества проводим в течение 24 минут при продвижении верхнего электрода над зоной расплава с постоянной скоростью, после чего расплавленную массу выгружаем в устройство, предназначенное для подачи расплава в реакционную камеру для проведения второй стадии получения продукта.
Масса образовавшегося полупродукта составляет 599 г, что соответствует выходу полупродукта относительно массы исходного железосодержащего вещества и безводного сульфата калия 81%. Содержание соединений железа (III) в полупродукте, найденное методами химического анализа, составляет 19,2%.
Массовая доля соединений железа (III) в полупродукте в пересчете на железо, найденная методами химического и рентгеновского анализов, составляет 19,2%, в том числе оксидов железа (III) – 1,9% и ферритов натрия 42,8%.
В качестве возвратного отхода образуется до 33% железосодержащего гранулированного материала.
Для отделения непрореагировавшего железа плав пропускали через стальную сетку и далее с помощью устройства для подачи расплавленной массы направляли его в реакционную камеру для проведения второй стадии процесса получения продукта. Задержанное стальной сеткой гранулообразное железосодержащее вещество используется вновь для получения полупродукта.
Берем 450 г гидроксида натрия и помещаем его в реакционную камеру, выполненную в виде стальной прямоугольной ванны с плоским дном и устанавливаем ее горизонтально в начальной части обогреваемого объема муфельной печи с нихромовыми электронагревателями таким образом, что температура расплава составляет 400-500°С. С помощью блока управления поддерживаем температуру обогреваемого объема тоннельной печи 800±20°С. Включаем устройство для подачи воздуха от компрессора, которое установлено постоянно вдоль тоннельной печи в верхней ее части и обеспечивает подачу воздуха на поверхность реакционной массы со скоростью, достаточной для отвода образующихся летучих соединений серы, на всем протяжении обогреваемого объема печи. С помощью загрузочного устройства направляем часть расплава полупродукта после стадии 1 массой 150 г в реакционную камеру с расплавом NaOH. Подаем реакционную камеру с реакционной массой в рабочую зону тоннельной печи с постоянной скоростью, обеспечивающей нахождение реакционной камеры в зоне с установившейся температурой 800±20°С в течение 50 минут. Далее реакционную камеру протягиваем через выходную часть тоннельной печи, в которой происходит частичное остывание реакционной массы до температуры 400-500°С.
Общая продолжительность получения продукта, содержащего феррат (IV) и (VI) натрия, в тоннельной печи при перемещении реакционной камеры с постоянной скоростью и при постоянной подаче на поверхность расплава воздуха составляет 80 минут. По истечении указанного времени вынимаем реакционную камеру с продуктом в виде вязкотекучей массы из обогреваемого объема печи, выгружаем и упаковываем его аналогично примеру 5.
Масса образовавшегося продукта составляет 359 г, что соответствует выходу продукта относительно массы исходного железосодержащего вещества и гидроксида натрия 72%. Содержание ферратов (IV) и (VI) натрия в продукте, в пересчете на
Na2FeO4, составляет 22,5% или 7,6% в пересчете на железо (VI).
Пример 7. Получение полупродукта в реакционной камере из стали (два верхних электрода перемещается относительно нижнего) (фиг.3); получение продукта в установленной под углом к горизонту реакционной камере, обеспечивающей продвижение реакционной массы (фиг.7, 8).
Берем 1000 г сульфата калия безводного K2SO4 и помещаем его в реакционную камеру, выполненную из стали с выемкой в форме полуокружности и играющую роль электрода, над которой вертикально расположены два электрода в форме прямоугольного стержня, опущенные в реакционную массу. Реакционная камера снабжена устройством для перемещения с постоянной скоростью относительно неподвижных вертикально расположенных электродов. На электроды подаем переменное синусоидальное напряжение и с помощью специального устройства в виде дополнительного электрода получаем расплав сульфата калия. С помощью блока управления подаем на электроды знакопеременное импульсное напряжение (фиг.13) таким образом, что первый по ходу продвижения зоны расплава электрод поляризуется положительными импульсами анодно, а второй – отрицательными импульсами катодно относительно электрода – реакционной камеры; при этом длительность импульсов обеспечивала мощность тока, выделяемую на электродах, достаточную для поддержания температуры расплава 940±60°С. Берем 640 г железосодержащего вещества в виде стружки, что соответствует молярному отношению Fe:K2SO4 2, и помещаем его в расплав таким образом, чтобы железосодержащее вещество равномерно располагалось по длине желоба. Процесс окисления железосодержащего вещества проводим в течение 30 минут при продвижении электрода – реакционной камеры с зоной расплава с постоянной скоростью, после чего расплавленную массу охлаждаем до комнатной температуры и кристаллический полупродукт выгружаем в бункер для хранения.
Масса образовавшегося полупродукта составляет 1443 г, что соответствует выходу полупродукта относительно массы исходного железосодержащего вещества и безводного сульфата калия 88%. Содержание соединений железа (III) в полупродукте, найденное методами химического анализа, составляет 38,6%.
Массовая доля соединений железа (III) в полупродукте в пересчете на железо, найденная методами химического и рентгеновского анализов, составляет 38,6%, в том числе оксидов железа (III) – 9,9% и ферритов натрия 75,8%.
Охлажденный полупродукт помещаем в бункер, предназначенный для его сбора и хранения. Полупродукт хранился в атмосферных условиях в течение 420 суток, после чего измельчался и в виде мелкокристаллической массы использовался для проведения второй стадии получения продукта.
Реакционную камеру кругового сечения, изогнутую таким образом, что вдоль продвижения реакционной массы образуется колено, в полости которого происходит задержка реакционной массы на интервал времени, необходимый для формирования продукта (фиг.8), устанавливаем в обогреваемом объеме муфельной печи с нихромовыми электронагревателями. С помощью блока управления поддерживаем температуру обогреваемого объема тоннельной печи 900±20°С. Включаем устройство для подачи воздуха от компрессора, которое постоянно подает его во входную часть реакционной камеры и обеспечивает подачу воздуха на поверхность реакционной массы со скоростью, достаточной для отвода образующихся летучих соединений серы, на всем протяжении обогреваемого объема печи. Берем 876 г кристаллического гидроксида калия, смешиваем его с 455 г измельченного полупродукта и с помощью загрузочного дозирующего устройства подаем смесь КОН и железосодержащего вещества после стадии 1 в реакционную камеру с постоянной скоростью в течение 60 минут. На выходе реакционной камеры расплав продукта под действием гравитационных сил разгружается в стальной поддон, в котором происходит кристаллизация и охлаждение реакционной массы до температуры 40-70°С.
Общая продолжительность непрерывного получения 1 кг продукта, содержащего ферраты (IV) и (VI) калия, в наклонной реакционной камере при постоянной скорости подачи реакционной массы в ее объем и при постоянной подаче на поверхность расплава воздуха составляет 60 минут. Охлажденный продукт упаковываем аналогично примеру 5.
Масса образовавшегося продукта составляет 1000 г, что соответствует выходу продукта относительно массы исходного железосодержащего вещества и гидроксида калия 84%. Содержание ферратов (IV) и (VI) калия в продукте, в пересчете на K2FeO4, составляет 74,9% или 21,2% в пересчете на железо (VI).
Пример 8. Получение полупродукта аналогично примеру 7, за исключением питания электродов электрическим током, которое в данном опыте осуществляется выпрямленным током (фиг.14); получение продукта в вертикальной реакционной камере аналогично примеру 1 (использование газообразного кислорода).
Масса образовавшегося полупродукта составляет 1460 г, что соответствует выходу полупродукта относительно массы исходного железосодержащего вещества и безводного сульфата калия 89%. Содержание соединений железа (III) в полупродукте, найденное методами химического анализа, составляет 38,7%.
Массовая доля соединений железа (III) в полупродукте в пересчете на железо, найденная методами химического и рентгеновского анализов, составляет 38,7%, в том числе оксидов железа (III) – 8,9% и ферритов натрия 77,9%.
Охлажденный полупродукт выгружаем в бункер, предназначенный для его сбора и хранения. Полупродукт в бункере хранится в виде крупнокристаллической массы. Для проведения второй стадии полупродукт в необходимом количестве берем через 10 суток после его получения.
В реакционную камеру помещаем 500 г гидроксида натрия, поддерживаем температуру расплава 650±10°С. Устанавливаем в объеме расплава устройство для подачи газообразного кислорода в нижнюю часть расплава гидроксида натрия от баллона под давлением, достаточным для барботирования газа. Добавляем в расплав 125 г измельченного полупродукта, полученного на стадии 1, при непрерывном барботировании расплава газообразным кислородом.
Процесс получения продукта, содержащего ферраты (IV) и (VI) натрия и калия, осуществляем в изотермическом режиме при постоянной подаче в расплавленную массу воздуха в течение 100 минут. По истечении указанного времени отключаем питание электронагревателей, выгружаем и упаковываем продукт аналогично опыту 1.
Масса образовавшегося продукта составляет 479 г, что соответствует выходу продукта относительно массы исходного железосодержащего вещества и гидроксида натрия 84%. Содержание ферратов (IV) и (VI) натрия и калия в продукте, в пересчете на K2FeO4 составляет 77% или 21,8% в пересчета на железо (VI).
Приведенные примеры показывают, что первая стадия процесса окисления железосодержащего вещества в расплаве сульфатов натрия и/или калия, требующая соответствующих прототипу температур 850-1100°С протекает в течение 12-30 минут, а продолжительность второй стадии получения готового продукта путем окисления содержащегося в полупродукте железосодержащего вещества, протекающей при более низких температурах 640-880°С, не превышает 120 минут. Таким образом, общая продолжительность получения готового продукта меньше продолжительности получения готового продукта в прототипе, по меньшей мере, на 30 минут. При этом вторая стадия протекает при более низких температурах, по сравнению с первой стадией и с прототипом, что резко снижает затраты энергии на поддержание необходимой температуры расплава. Низкие требования к составу полупродукта, который представляет собой многокомпонентную смесь, содержащую преимущественно оксид железа (III) и ферриты натрия и/или калия, оксиды и сульфиды щелочных металлов и железа, позволяет использовать в качестве исходных веществ для получения полупродукта как химически чистые реагенты (металлическое железо и сульфаты натрия и калия), так и разнообразные отходы холодной и горячей обработки металлов, в том числе сплавы железа, скрап и т.п., а также производственные отходы, содержащие сульфаты натрия и/или калия, в том числе образующийся при очистке хромсодержащих сточных вод сульфат натрия или технический сульфат калия, участвующий в технологии получения ксантогенатов. Приведенные примеры также показывают, что на второй стадии получения готового продукта могут быть использованы без ухудшения его качества наряду с химически чистыми гидроксидами натрия и калия технологические отходы и полупродукты, содержащие гидроксиды этих щелочных металлов.
Таким образом, преимущества заявляемого изобретения заключаются в следующем:
– снижение энергетических затрат на получение продукта, путем снижения продолжительности окисления железосодержащего вещества в расплаве сульфатов щелочных металлов на первой стадии процесса получения полупродукта и снижения температуры второй стадии процесса получения целевого продукта при окислении содержащегося в полупродукте железосодержащего вещества в расплаве гидроксидов щелочных металлов;
– снижение энергетических затрат на получение продукта за счет исключения непрерывной подачи кислорода в расплав сульфатов щелочных металлов на первой стадии процесса получения полупродукта;
– снижение продолжительности процесса и затрат энергии на проведение второй стадии получения готового продукта при окислении содержащегося в полупродукте железосодержащего вещества в расплаве гидроксидов щелочных металлов в результате использования газовоздушной смеси, обогащенной газообразным кислородом;
– использование в качестве исходных веществ технологических отходов и полупродуктов различных производств;
– возможность создания небольшого по масштабам производства готового продукта непосредственно на месте его применения, использующего устройства модульного типа, которые легко подвергаются транспортировке и монтажу без значительных капитальных затрат;
– возможность создания крупномасштабного массового производства в условиях специализированных предприятий с транспортировкой полупродукта или готового продукта к месту их применения.
Формула изобретения
1. Способ получения окислителя на основе ферратов щелочных металлов, включающий окисление железосодержащего вещества в расплаве соединений щелочных металлов, отличающийся тем, что процесс окисления ведут в две стадии, при этом на первой стадии ведут окисление исходного железосодержащего вещества в расплаве сульфатов щелочных металлов и/или промышленных отходов, содержащих сульфаты щелочных металлов, при пропускании через расплав электрического тока до получения полупродукта, содержащего оксиды железа и ферриты щелочных металлов, а на второй стадии осуществляют последующее окисление оксидов железа и ферритов щелочных металлов, содержащихся в полупродукте, в расплаве гидроксидов щелочных металлов, в присутствии газообразного кислорода до получения продукта, содержащего ферраты (IV) и (VI) щелочных металлов.
2. Способ по п.1, отличающийся тем, что в качестве исходного железосодержащего вещества используют металлическое железо и/или его сплавы, и/или отходы металлообработки изделий из черных металлов, например, скрап, и/или отходы черной металлургии.
3. Способ по п.1, отличающийся тем, что в качестве солей щелочных металлов на первой стадии способа используют сульфаты натрия и/или калия, и/или промышленные отходы, содержащие сульфаты натрия и/или калия.
4. Способ по п.1, отличающийся тем, что в качестве гидроксидов щелочных металлов на второй стадии способа используют гидроксиды натрия и/или калия, и/или промышленные отходы, содержащие гидроксиды натрия и/или калия.
5. Способ по п.1, отличающийся тем, что первую стадию ведут при температуре 850-1100°С.
6. Способ по п.1, отличающийся тем, что вторую стадию ведут при температуре 640-880°С.
7. Способ по п.1, отличающийся тем, что первую стадию ведут до достижения массовой доли соединений железа (III) в полупродукте 4-39%, в пересчете на железо.
8. Способ по п.1, отличающийся тем, что на первой стадии осуществляют электрохимическое или комбинированное химико-электрохимическое окисление железосодержащего вещества.
9. Способ по пп.1 и 8, отличающийся тем, что на первой стадии осуществляют электрохимическое окисление железосодержащего вещества в расплаве сульфата натрия и/или калия переменным током.
10. Способ по пп.1 и 8, отличающийся тем, что на первой стадии осуществляют электрохимическое окисление железосодержащего вещества в расплаве сульфата натрия и/или калия выпрямленным током.
11. Способ по пп.1 и 8, отличающийся тем, что на первой стадии осуществляют электрохимическое окисление железосодержащего вещества в расплаве сульфата натрия и/или калия переменным током с поляризацией электродов.
12. Способ по п.1, отличающийся тем, что газообразный кислород на второй стадии способа подают непрерывно в составе газовоздушной смеси, содержащей по объему 21-100% кислорода.
13. Способ по пп.1 и 12, отличающийся тем, что газовоздушную смесь, содержащую газообразный кислород, барботируют через расплав гидроксида натрия или калия для одновременного окисления соединений железа, содержащихся в полупродукте, и перемешивания расплава.
14. Способ по пп.1 и 12, отличающийся тем, что газовоздушную смесь, содержащую газообразный кислород, подают на поверхность расплава.
15. Способ по пп.1 и 12, отличающийся тем, что вторую стадию ведут до достижения массовой доли соединений железа (IV) и (VI) в продукте, содержащем ферраты щелочных металлов, 2,7-21,8%, в пересчете на железо (VI).
16. Установка для получения окислителя на основе ферратов щелочных металлов, включающая устройство для окисления исходного железосодержащего вещества в расплаве сульфатов щелочных металлов, содержащее корпус для размещения реакционной массы и электроды, отличающаяся тем, что установка снабжена устройством для окисления железосодержащего вещества – полупродукта, содержащего оксиды железа (III) и ферриты щелочных металлов, в расплаве гидроксидов щелочных металлов до получения готового продукта, содержащего ферраты (IV) и (VI) щелочных металлов, включающим реакционную камеру с устройством внешнего нагрева, блок управления режимами нагрева и устройство для подачи кислорода в реакционную камеру, а устройство для окисления исходного железосодержащего вещества в расплаве солей щелочных металлов содержит, по меньшей мере, один железосодержащий съемный электрод и снабжено блоком управления режимами работы электродов.
17. Установка по п.16, отличающаяся тем, что корпус устройства для окисления исходного железосодержащего вещества в расплаве сульфатов щелочных металлов выполнен из огнеупорного материала, обладающего свойствами диэлектрика, при этом указанное устройство содержит, по меньшей мере, два электрода, погруженных в расплав, и снабжено средством для подачи и размещения железосодержащего вещества в объеме расплава, образующегося при пропускании через него электрического тока.
18. Установка по п.16, отличающаяся тем, что корпус устройства для окисления исходного железосодержащего вещества в расплаве сульфатов щелочных металлов выполнен металлическим, например, из стали, и является при этом одним из электродов, причем, по крайней мере, один железосодержащий съемный электрод расположен над корпусом для создания ограниченной зоны расплава при пропускании через расплав электрического тока, размеры которой достаточны для формирования в расплаве реакционной массы полупродукта, содержащего оксид железа (III) и ферриты щелочных металлов.
19. Установка по пп.16 и 17, отличающаяся тем, что корпус устройства для окисления исходного железосодержащего вещества выполнен в виде монолитной плиты произвольной формы с замкнутой прямоугольной или трапециевидной, или овальной выемкой для размещения реакционной массы.
20. Установка по пп.16 и 17, отличающаяся тем, что корпус устройства для окисления исходного железосодержащего вещества выполнен в виде бруска, имеющего вытянутую по длине выемку прямоугольной или трапециевидной, или овальной формы для размещения реакционной массы.
21. Установка по п.16, отличающаяся тем, что, по меньшей мере, один электрод установлен в корпусе устройства для окисления исходного железосодержащего вещества с возможностью взаимного перемещения относительно корпуса и/или других электродов в горизонтальной и вертикальной плоскостях для изменения положения и размеров зоны расплава и/или изменения электросопротивления расплава.
22. Установка по п.16, отличающаяся тем, что устройство для окисления исходного железосодержащего вещества в расплаве сульфатов щелочных металлов снабжено дозирующим устройством для подачи железосодержащего вещества и/или солей щелочных металлов.
23. Установка по п.22, отличающаяся тем, что дозирующее устройство установлено перед, по меньшей мере, одним из электродов.
24. Установка по пп.16, 17, 22, отличающаяся тем, что, электроды расположены вертикально, а дозирующее устройство для подачи железосодержащего вещества и/или солей щелочных металлов установлено с возможностью размещения железосодержащего вещества на дне корпуса.
25. Установка по пп.16, 17, 22, отличающаяся тем, что, по меньшей мере, один электрод расположен горизонтально, при этом дозирующее устройство для подачи железосодержащего вещества и/или солей щелочных металлов установлено с возможностью размещения железосодержащего вещества в объеме расплава на поверхности этого электрода.
26. Установка по п.16, отличающаяся тем, что блок управления режимами работы электродов включает трансформатор и блок-преобразователь для управления фазовыми характеристиками электрического тока.
27. Установка по п.16, отличающаяся тем, что устройство для окисления исходного железосодержащего вещества в расплаве солей щелочных металлов содержит вспомогательный электрод для начального перевода кристаллических соединений щелочных металлов в расплавленную форму при подключении этого электрода к блоку управления режимами работы электродов.
28. Установка по п.16, отличающаяся тем, что в качестве реакционной массы в устройстве для окисления исходного железосодержащего вещества в расплаве сульфатов щелочных металлов используют смесь исходного железосодержащего вещества и кристаллических соединений щелочных металлов.
29. Установка по пп.16 и 28, отличающаяся тем, что в качестве исходного железосодержащего вещества используют металлическое железо и/или его сплавы, и/или отходы металлообработки изделий из черных металлов, например, скрап, и/или отходы черной металлургии, а в качестве соединений щелочных металлов используют кристаллические сульфаты натрия и/или калия, и/или промышленные отходы, содержащие кристаллические сульфаты натрия и/или калия.
30. Установка по п.16, отличающаяся тем, что в качестве железосодержащего вещества – полупродукта используют полупродукт, содержащий оксид железа (III) и ферриты щелочных металлов, предварительно полученный в устройстве для окисления исходного железосодержащего вещества в расплаве сульфатов щелочных металлов, а в качестве соединений щелочных металлов используют гидроксиды натрия и/или калия, и/или промышленные отходы, содержащие гидроксиды натрия и/или калия.
31. Установка по п.16, отличающаяся тем, что реакционная камера устройства для окисления железосодержащего вещества – полупродукта, содержащего оксид железа (III) и ферриты щелочных металлов, в расплаве гидроксида натрия и/или калия имеет форму цилиндра или параллелепипеда и установлена вертикально или под углом к вертикальной оси, при этом длина реакционной камеры превышает ее поперечные размеры.
32. Установка по п.16, отличающаяся тем, что реакционная камера устройства для окисления железосодержащего вещества – полупродукта, содержащего оксид железа(Ш) и ферриты щелочных металлов, в расплаве гидроксида натрия и/или калия установлена горизонтально и имеет плоское дно произвольной формы, по которому реакционная масса равномерно распределяется тонким слоем.
33. Установка по п.16, отличающаяся тем, что реакционная камера устройства для окисления железосодержащего вещества – полупродукта, содержащего оксид железа (III) и ферриты щелочных металлов, в расплаве гидроксида натрия и/или калия установлена под углом к горизонту для обеспечения за счет сил гравитации продвижения реакционной массы вдоль реакционной камеры и одновременного перемешивания реагентов и взаимодействия их с кислородом, содержащимся в газовоздушной смеси, которая подается на поверхность расплава.
34. Установка по пп.16, 31, 33, отличающаяся тем, что устройство для окисления полупродукта, содержащего оксид железа (III) и ферриты щелочных металлов, снабжено устройством загрузки полупродукта и гидроксидов натрия и/или калия и устройством выгрузки хотя бы части готового продукта, содержащего ферраты (IV) и (VI) щелочных металлов.
35. Установка по п.16, отличающаяся тем, что она снабжена устройством, обеспечивающим хранение полупродукта, содержащего оксид железа (III) и ферриты щелочных металлов, и его транспортировку в реакционную камеру устройства для окисления полупродукта, содержащего оксид железа (III) и ферриты щелочных металлов в расплаве гидроксидов натрия и/или калия.
РИСУНКИ
|