|
(21), (22) Заявка: 2008109571/04, 14.03.2008
(24) Дата начала отсчета срока действия патента:
14.03.2008
(46) Опубликовано: 20.12.2009
(56) Список документов, цитированных в отчете о поиске:
RU 2275398 C2, 27.04.2006. RU 2288095 C1, 27.11.2006. US 2005070644 A1, 31.03.2005. US 2948691 А, 09.08.1960.
Адрес для переписки:
119526, Москва, пр-кт Вернадского, 101, корп.1, ИПМех РАН, патентный отдел
|
(72) Автор(ы):
Куликов Олег Леонидович (RU)
(73) Патентообладатель(и):
Куликов Олег Леонидович (RU)
|
(54) ТЕРМОПЛАСТИЧНЫЙ ПОЛИМЕРНЫЙ МАТЕРИАЛ
(57) Реферат:
Изобретение относится к переработке расплавов термопластичных органических полимеров, в частности полиолефинов с узким распределением молекулярного веса. Описывается термопластичный полимерный материал, включающий органический термопластичный полимер и комплексную добавку для улучшения формования в количестве 0,02-1 вес.%. В качестве комплексной добавки используют композицию, содержащую полиэфиры с температурой плавления от 35 до 120°С и молекулярным весом 1000-10000 дальтон, и загустители, выбранные из группы, включающей растворимые в полиэфирах полимеры с молекулярным весом от 100000 до 20000000 дальтон, высокодисперсные порошки оксидов кремния и титана с размерами частиц от 1 до 1000 нанометров и фосфорсодержащие органические соединения. Предложенный термопластичный полимерный материал позволяет снизить расход энергии и температуру формования при его переработке, а также уменьшить потери полимера при формовании. 7 з.п. ф-лы, 16 ил.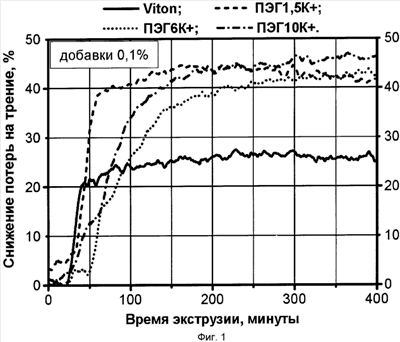
Изобретение относится к переработке расплавов термопластичных органических полимеров экструзией, инжекционным формованием и раздуванием полимерного рукава. В частности, заявляемое техническое предложение направлено на улучшение переработки расплава полиолефинов с узким распределением молекулярного веса.
Переработка чистых полимеров экструзией или инжекционным формованием, как правило, не производится. На практике перерабатывают «полимерные составы», содержащие разнообразные компоненты в относительно небольших, но часто критических количествах. Эти компоненты могут быть отнесены к двум классам, а именно:
– добавки для улучшения свойств полимерных изделий;
– добавки для улучшения формования расплава полимеров,
см. подробнее в [J.T.Lutz Jr., R.F.Grossman. Polymer Modifiers and Additives. JL Enterprises, Bensalem Pennsylvania U.S. A. (2000) /1/] и [Н.Zweifel, Plastic Additives Handbook. 5th Ed. Hanser Publishers: Munich (2000), /2/], [Flick E W (Ed.) (2001), Plastics Additives: An Industrial Guide, Knovel Corporation, N.Y. /3/].
Примеры добавок для улучшения свойств полимерных изделий – это наполнители и заполнители, добавки для улучшения взаимной адгезии компонентов, антиблоковые добавки, добавки, улучшающие диспергирование наполнителей, красители, пластификаторы, разнообразные химические стабилизаторы и антиокислители. Антиблоковые добавки, например, применяют, чтобы уменьшить слипание полимерных пленок между собой. Эти добавки могут включать мелкодисперсные порошки синтетического кварца, диатомовой земли и талька.
Добавки для улучшения формования полимеров или процессинговые добавки облегчают переработку полимеров [Е.С.Achlleos, G.Georgiou, S.G.Hatrikiriakos. Role of Processing Aids in the Extrusion of Molten Polymers. J. Vinyl & Additive Technology, 8 (2002) 7-24 /4/]. Часто переработка без них не была бы возможной. Особенно важные среди этих добавок – это смазки, иногда называемые «антиадгезивы», которые предотвращают налипание расплавленного термопластического полимера на поверхность оборудования, например, на винт экструдера, мундштука, роликов, формы для инжекционного формования и т.п. Как исключение из правила, некоторые добавки для улучшения свойств полимерных изделий являются одновременно и добавками для улучшения формования полимеров. Например, стеарат цинка – это одновременно смазка и ингибитор химического разложения полимеров при повышенной температуре.
Когда органические полимеры, которые характеризуются высоким молекулярным весом и узким его распределением, формуют экструзией, то гладкий экструдат может быть получен только ниже определенной скорости формования. Выше этого предела начинает появляться шероховатость поверхности. Появление поверхностной шероховатости, известной специалистам как дробление расплава или «акулья кожа», ограничивает производительность формования полимеров в промышленности. Чтобы увеличить скорость формования применяют добавки для улучшения формования полимеров. Использование этих добавок должно задержать или устранить появление поверхностной шероховатости.
Некоторые фторированные полимеры, например: Viton от DuPont, Dynamar от 3М, Kynar от Atofina, и т.д., см. подробнее в [S.Hatzikiriakos and К.Migler, Polymer Processing Instabilities: Control and Understanding. Marcel Dekker 2005. vol. 102. /5/], подавляют дробление расплава и появление дефектов типа «акулья кожа». Их применение в качестве добавок обеспечивает более высокую производительность формования экструзией. Такие добавки обычно используют в количестве от 0,025 до 0,3% от веса термопластичного полимерного материала. Главная проблема, возникающая в коммерческом использовании этих добавок, – это накопление продуктов разложения добавок на металлических поверхностях, например на винте экструдера и/или на мундштуке. Накопление продуктов разложения происходит часто настолько интенсивно, что необходимо периодически останавливать оборудование для очистки. Применение этих добавок также ограничено их высокой стоимостью. Фторированные добавки – это гидрофобные вещества, поэтому их применение увеличивает гидрофобность поверхности полимерной пленки.
Обобщая анализ аналогов предлагаемого технического решения, связанных с использованием фторированных полимеров, можно отметить, что их недостатком является дороговизна и миграция гидрофобных полимеров на поверхность, что затрудняет сварку полимерных изделий нагревом, снижает адгезию краски и клея к полимерной поверхности и приводит к накоплению статического электрического заряда на поверхности пленки. Изготовление и использование фторированных полимеров приводит к выбросу в атмосферу фторсодержащих газов, которые разрушают озоновый слой нашей планеты и, возможно, провоцирует заболевания раком, поэтому использование добавок на основе фторированных полимеров нежелательно.
Известно, что применение комплексных процессинговых добавок, включающих комбинацию частиц нитрида бора или деламинированной глины с фторированными полимерами, а также только частиц деламинированной глины, снижает время индукции для процессинговой добавки и потери на трение, см. [Е.В.Muliawan, N Rathod, S.G.Hatzikiriakos and M.Sentmanat. Boron Nitride and Fluoropolymer Combinations: Interactions and their performance as processing aids. Polym Eng Sci., 45, 669-677 (2005) /6/] и [S.G.Hatzikiriakos, N.Rathod and E.B.Muliawan, The Effect of Nanoclays on the Processability of Polyolefins. Polym. Eng. Sci., 45, 1098-1107 (2005) /7/]. Частицы глины и Нитрида Бора имеют пластинчатую форму. Толщина частички деламинированной глины может составлять около 1 нм, а продольный размер составляет при этом от 300 до 600 нм. Частички нитрида бора для использования в составе процессинговой добавки имеют размер 1-2 мкм и толщину 30-60 нм, см. [Е.A.Pruss, Т.М.Clere, S.K.Randa. Polymer processing aid and method for processing polymers. U.S. Pat. Appl. No. 20040220288 A1. Nov.4, 2004. U.S. C1.: 521/50 /8/].
Обобщая анализ аналогов предлагаемого технического решения, связанных с использованием комплексных добавок, включающих комбинацию минеральных порошков с фторированными полимерами, можно отметить трудность смешивания минеральных порошков с фторированными полимерами, которые характеризуются высокой вязкостью.
Добавки на основе органо-силиконов, например силоксанов, много лет эффективно используются в промышленности с целью улучшить переработку полимеров инжекционным формованием, облегчить отделение изделий от металлической формы, и увеличить скорость формования экструзией. Однако использование этих добавок может быть осложнено трудностью введения их в состав термопластичного полимерного материала. Например, при подаче этих добавок совместно с гранулированным полимерным материалом винт экструдера проскальзывает, и подача материала прекращается. Дополнительно, силоксаны с высоким молекулярным весом – это гидрофобные вещества, которые характеризуются низкой электрической проводимостью. Силоксаны мигрируют к поверхности продукта, и их присутствие понижает адгезию поверхности изделий к клею, ярлыкам и краске, затрудняет сварку полимерных изделий, а также приводит к накоплению статического электрического заряда на поверхности пленки, аналогично применению фторированных процессинговых добавок.
Обобщая анализ аналогов предлагаемого технического решения, связанных с использованием силоксанов, можно отметить, что их недостатком является относительно высокая стоимость, миграция гидрофобных полимеров на поверхность, что затрудняет сварку полимерных изделий нагревом и снижает адгезию краски и клея к полимерной поверхности, приводит к накоплению статического электрического заряда на поверхности пленки.
Полиэтиленгликоли различного молекулярного веса и их производные используются в промышленности в качестве компонентов смазки, тормозной и охлаждающей жидкости, разделительных составов для обработки металлов прессованием и резкой, например см. [О.Н.Дымент. Гликоли и другие производные окисей этилена и пропилена. – М.: Химия, 1976. 188 с. /12/], [Polyalkylene Oxides and Other Polyethers. ed. by N.Gaylord. New York, Interscience, 1963. 491 p. /13/]. Известно использование полиэтиленгликоля (ПЭГ), эфиров ПЭГ и высокомолекулярного полиэтиленоксида (ПО) в качестве антиадгезива и процессинговой добавки. DeJuneas, et al. сообщили в своем патенте [J.V. DeJuneas, G.L.Mclntyre, J.F. O Horo Jr. Method of reducing breakdown in polyethylene film. U.S. Pat. No. 4,013,622. Mar. 22, 1977. U.S. C1.: 524/388 /14/], что добавление ПЭГ с молекулярным весом от 1300 до 7500 дальтон в количестве от 0,02 до 0,05% от веса полимерного материала при производстве полиэтиленовой пленки уменьшает число остановок оборудования для очистки при стандартных условиях работы. L.E.Wolinski сообщил в своем патенте [L.E.Wolinski. Polyethylene resin containing a solid polyethylene glycol. U.S. Pat. No. 3,222,314. Dec. 07, 1965. U.S. C1.: 260-32.2 /15/], что ПЭГ с молекулярным весом от 1000 до 6500 дальтон могут быть использованы в количестве от 0,1 до 10 вес.% как добавки в полиэтилен для улучшения качества печати на поверхности полимерной пленки. Использование полиэтиленгликолей с молекулярным весом менее 10000, согласно Duchesne, см. [D.J.Duchesne, V.Bryce. Extrudable thermoplastic hydrocarbon polymer composition, U.S. Pat. No. 4,855,360, Aug. 8, 1989. U.S. CI: 525/187 /16/], не обеспечивает улучшения качества формования полиолефинов, в частности не обеспечивает подавления дефектов при экструзии полиолефинов с узким распределением молекулярного веса.
Известно предложение использовать высокомолекулярный ПЭГ с молекулярным весом от 10000 до 50000 дальтон в качестве добавки для улучшения формования полиолефинов, см. [Т Т.Tikuisis, et al. High molecular weight polyethylene glycol as polymer process aids. U.S. Pat. Appl. No. 20050070644 A1. Mar.31, 2005. U.S. CI.: 524/115 /19/]. Blong и Lavallee предложили использовать ПЭГ и полиэтиленоксид (ПО) как процессинговую добавку при переработке фторированного полимера экструзией, см. [T.J. Blong, С.Lavallee. Meltprocessable fluoroplastic. U.S. Pat. No. 5,527,858. Jun. 18, 1996. U.S. CI.: 525/187 /20/]. Недостатком использования высокомолекулярного ПЭГ в качестве добавки для улучшения формования является его высокая стоимость. Использование сложных полиэфиров, полученных реакцией поликонденсации карбоновых кислот и многоатомных спиртов, с температурой плавления до 150°С как процессинговой добавки для полиэтилена известно из патента [P.Bauer, U.Seeliger, U.Faller. Thermoplastic molding compounds based on ethylene polymers and thermoplastic polyesters. U.S. Pat. No. 6,048,937. Apr. 11, 2000. U.S. CI.: 525/131 /21/].
Известно использование смесей простых полиэфиров с неорганическим порошком с размером частиц от 3,5 до 12 микрон в качестве процессинговой добавки. Corwin et al. в своем патенте [М.А.Corwin, G.N.Foster. Anti-block compounds for extrusion of transition metal catalyzed resins. U.S. Pat. No. 4,540,538. Sep.10, 1985. U.S. CI.: 264/211 /22/] сообщает, что накопление продуктов термического разложения полиолефинов внутри горячего экструдера снижается, если используется процессинговая добавка, приготовленная смешиванием ПЭГ или полипропиленгликоля (ППГ) с молекулярным весом в диапазоне от 200 до 4000000 дальтон в комбинации с фенольным антиоксидантом и неорганической антиблоковой добавкой с размерами частиц от 0,5 до 10 микрон. Li et al. описали использование бинарных смесей ПЭГ и диатомовой земли, которая обычно используется в качестве антиблоковой добавки, в соотношении 1 часть ПЭГ к 2 частям диатомовой земли и при концентрации бинарной смеси от 0,5 до 3 вес.% для улучшения переработки полиэтилена и подавления дефектов экструзии типа «акулья кожа», см.: [М.Xie, X.Liu, H.Li. Influence of PEG-containing additives on extrusion of ultrahigh molecular weight PE/PP blend. J. Appl. Polym. Sci. 100 (2006) 1282-1288 /23/], [X.Liu, H.Li. Effect of diatomite/polyethylene glycol binary processing aid on the melt fracture and the rheology of polyethylenes. Polym. Eng. Sci. 45 (2005) 898-903 /24/], [J. Chen, X. Liu, H. Li. Improvement in processability of metallocene polyethylene by ultrasound and binary processing aid. J. Appl. Polym. Sci. 103 (2007) 1927-1935 /25/]. Диатомовая земля (кристаллический кварц), которая используется как антиблоковая добавка в производстве полимерной пленки, характеризуется нерегулярной угловатой формой частиц со средним размером от 3,5 до 12 микрон, см. [А.С.Cornett. Antiblock agent for polyolefin films. U.S. Pat. No. 5,908,890. Jun. 1, 1999. U.S. Class: 524/448 /26/]. Недостатком использования бинарной смеси ПЭГ с минеральными порошками с размером частиц от 0,5 до 10 мкм является их низкая эффективность, так что для улучшения формования необходимо их использовать в количестве от 0,5 до 3 вес.%.
Известно использование эфиров борной кислоты, ПЭГ и/или пропиленгликоля как антиадгезива для обработки металлических форм, предназначенных для инжекционного формования термопластичных полимерных материалов, и для очистки экструдера, см. [S.Sato, Release agent for metallic mold. U.S. Pat. Appl. No. 20040083925 A1. May 6, 2004 /27/] и [S.Sato, Resin composition for purging contaminant in the plastic processing machine. U.S. Pat. Appl. No. 20040132878 A1. July 8, 2004 /28/]. Существенно, что полиэфир борной кислоты, предложенный для использования в качестве антиадгезива, характеризуется молекулярным весом от 280 до 4600 дальтон, то есть приготовлен с использованием полиэфира с молекулярным весом менее 1500 дальтон, а молярное отношение атомов бора к молекулам полиэфиров не превышает 1/3. Из описания следует, что покрытие форм производят кистью, распылением или погружением формы при комнатной температуре в жидкий антиадгезив, т.е. указанный жидкий полиэфир борной кислоты не предназначен для использования в качестве процессинговой добавки. Для использования в качестве компонента композиции для очистки экструдера и другого оборудования для формования расплавов полимеров указанный жидкий полиэфир борной кислоты используют как добавку в соотношении от 0,1 до 10 частей на 100 частей термопластичного полимера. При смешивании жидкого эфира борной кислоты с гранулами винт экструдера будет проскальзывать, и подача материала замедлится и даже может полностью прекратиться. Поэтому жидкий полиэфир борной кислоты предварительно смешивают с полимерным материалом в виде гранул или порошка и с помощью специального экструдера формуют гранулы концентрата.
Обобщая анализ аналогов предлагаемого технического решения, связанных с использованием полиэфиров и их производных, можно отметить, что известные добавки для улучшения формования на основе полиэфиров либо дороги, либо недостаточно эффективны, так что улучшение формования полимерных изделий достигается только при высоком содержании таких добавок в термопластичном полимерном материале.
Использование комплексных добавок, относящихся к комбинации фторированных полимеров и ПЭГ в качестве процессинговой добавки, широко известно из технической литературы, см. список:
[Fluoroelastomer processing aids meet extrusion needs. Plastics, Additives and Compounding. 4 (Jan. 2002) 23-25. DOI: 10.1016/S1464-391X(02)80025-3 /29/],
[D.J.Duchesne, V.Bryce, Extrudable thermoplastic hydrocarbon polymer composition, U.S. Pat. No. 5,015,693. May 14, 1991. U.S. CI.: 525/187 /30/],
[D.E.Priester. Processing aid system for polyolefins. U.S. Pat. No. 5,587,429. Dec. 24, 1996. U.S. CI.: 525/187 /31/],
[R.Chiu, J.W.Taylor, D.L.Cooke, S.K.Goyal, R.E.Oswin. Melt fracture elimination in film production. U.S. Pat. No. 5,550, 193. Aug. 27, 1996. U.S. CI.: 525/199 /32/],
[T.J.Blong, M.P.Greuel, С.Lavallee. Extrudable thermoplastic hydrocarbon compositions. U.S. Pat. No. 5,710,217. Jan. 20, 1998. U.S. CI.: 525/199 /33/],
[T.J.Blong, M.P.Greuel, С.Lavallee. Extrudable thermoplastic hydrocarbon compositions. U.S. Pat. No. 5,830,947. Nov. 3, 1998. U.S. CI.: 525/187 /34/],
[K.Focquet, G.Dewitte, S.E.Amos. Polymer processing additive having improved stability. U.S. Pat. No. 6,294,604. Sep.25, 2001. U.S. CI.: 524/433 /35/],
[G.R.Chapman JR and S.R.Oriani. Process aid for melt processible polymers. U.S. Pat. Appl. No. 20030236357 A1. Dec. 25, 2003. U.S. CI.: 525/415 /36/],
[S.S.Woods. Melt processable thermoplastic polymer composition employing a polymer processing additive containing a fluorothermoplastic copolymer. U.S. Pat. No. 6,734,252. May 11, 2004. U.S. CI.: 525/187 /37/],
[G.R.Chapman JR and S.R.Oriani. Process aid for melt processible polymers. U.S. Pat. Appl. No. 20040204544 A1. Oct. 14, 2004. U.S. CI.: 525/178 /38/],
[J.Briers, J.J.Cemohous, R.R.Nuyttens. Melt processable compositions. U.S. Pat. Appl. No. 20050101722 A1, May 12, 2005. U.S. CI.: 524/520 /39/],
[G.R.Chapman Jr., S.R.Oriani. Process aid for melt processable polymers. U.S. Pat. No. 6,894,118. May 17, 2005. U.S. CI.: 525/186 /40/],
[S.R.Oriani, S.D Uva, V.P.Trilokekar. Process aid masterbatch for melt processable polymers U.S. Pat. No. 6,906,137. Jun. 14, 2005. U.S. CI.: 525/165 /41/],
[B.Barriere, A.Bonnet, J.Laffargue and G. Marot. Fluoropolymer-based masterbatch and its use for the extrusion of polyolefins. U.S. Pat. Appl. No. 20060025523 A1. Feb. 2, 2006. U.S. CI.: 525/1 /42/],
[G.R.Chapman JR and S.R.Oriani. Process aid for melt processable polymers. U.S. Pat. Appl. No. 20060116477 A1. Jun. 1, 2006. U.S. CI.: 525/165 /43/].
Комбинация ПЭГ с фторированными полимерами для использования в качестве процессинговой добавки коммерчески доступна под торговыми марками Куnar и Dynamar. При использовании комбинации ПЭГ и фторированных полимеров не наблюдается накопление статического разряда на поверхности полимерной пленки, а потери на трение и время индукции для процессинговой добавки снижаются.
Обобщая анализ аналогов предлагаемого технического решения, связанный с использованием смесей ПЭГ и фторированных полимеров, можно отметить, что их недостатком является дороговизна фторированных полимеров и их вредное воздействие на окружающую среду.
Применение термопластических эластомеров (ТПЭ) на основе полиуретанов как добавок для улучшения формования полимеров было предложено в [О. Куликов. Термопластичный полимерный материал. RU 2275398. Апр. 27, 2006. МКИ С08D 23/02 /44/]. Термопластичный эластомер на основе силоксана и диизоцианата для использования в качестве процессинговой добавки коммерчески доступен под торговой маркой Geniomer от компании Wacker Chemie.
Полиуретановые полимеры на основе ПЭГ известны с конца 50-х годов, см. [Е.Windemuth, H.Schnell, О.Bayer. High molecular weight polyether urethane polymers. U.S. Pat. No. 2,948,691. Aug. 9, 1960. U.S. CI: 260-2.5 /45/]. Широко известно использование растворимых в воде полиуретанов в качестве загустителей водных суспензий и растворов, см. например: [Е.А.Blair and D.E.Hudgin. Hydrophilic polyurethane polymers. U.S. Pat. No. 3,822,238. Aug. 2, 1972. U.S. CI.: 260-75 NK /46/], [H.Meffert, S.N.Kim. Polyurethane and the use thereof for modifying rheological properties. U.S. Pat. No. 7,019,061. Mar. 28, 2006. U.S. CI.: 524/284 /47/].
Обобщая обзор аналогов предлагаемого технического решения, связанных с использованием термопластичных полиуретановых эластомеров, можно отметить, что их недостатком является сложность изготовления таких полимеров (высокий вакуум, точное дозирование компонентов и их химическая чистота, точный температурный режим процесса синтеза), что увеличивает их стоимость.
В промышленности переработки термопластичных полимеров существует значительная потребность в недорогих и эффективных добавках, обеспечивающих получение продукта без ухудшения его механических и органолептических свойств. Особенно это касается получения пленок для использования в упаковке из полиолефинов, приготовленных на основе металлоценовых катализаторов.
Наиболее близким к предлагаемому изобретению является известное техническое решение о применении в качестве процессинговой добавки вязко-упругого компаунда, представляющего собой продукт реакции между химическими соединениями, содержащими бор и кислород (отвердителем), и основным компонентом компаунда, которым служит полимерный материал, способный к реакции с этим отвердителем, что было предложено недавно в [О.Куликов. Способ формования термопластичного органического полимерного материала, состав термопластичного полимерного материала и смазка. RU 2288095 С1, Нояб. 27, 2006. МПК В29С 33/62 /48/]. В качестве основного компонента компаунда могут быть выбраны силанолы или полиоли, в частности полиэтиленгликоли. Эти химические соединения недороги и разрешены для использования в контакте с пищевыми продуктами и кожей. Упомянутое техническое решение включает, как частный случай, применение полиолей и силанолов в качестве основного компонента компаунда, в смеси с неорганическим наполнителем, но не показано преимущество использования наполнителя-загустителя в составе такого компаунда. Не показано, что использование в составе компаунда неорганического наполнителя-загустителя с размерами частиц от 1 до 1000 нм увеличивает эффективность процессинговой добавки. Также не показано преимущество использования в качестве процессинговой добавки смеси полиолей с силанолами и боратами, где силанолы составляют от 1 до 10% от веса компаунда. Применение силанолов в смеси с полиолями, в частности с полиэтиленгликолями, позволяет увеличить вязкость компаунда и эффективность процессинговой добавки.
Заявляемое изобретение направлено на то, чтобы увеличить скорость и качество формования термопластичного полимерного материала с узким распределением молекулярного веса, уменьшить его потери, расход энергии и температуру формования, а также на то, чтобы упростить и удешевить изготовление добавок для улучшения формования.
Указанный результат достигается тем, что термопластичный полимерный материал включает органический термопластичный полимер в качестве основного компонента и комплексную добавку для улучшения формования, при следующем соотношении компонентов, вес.%:
комплексная добавка: 0,02-1;
термопластичный полимер: остальное,
при этом в качестве комплексной добавки используют композицию, содержащую один или несколько полиэфиров, выбранных из группы простых и сложных, линейных и разветвленных алифатических полиэфиров с температурой плавления в диапазоне от 35 до 120°C и с молекулярным весом от 1000 до 10000 дальтон, и один или несколько загустителей, при следующем соотношении компонентов, вес.%:
загустители: 0,01-20;
полиэфиры: остальное,
причем загустители выбирают из следующей группы:
растворимые в полиэфирах полимеры с молекулярным весом от 100000 до 20000000 дальтон,
высокодисперсные порошки оксидов кремния и титана с размерами частиц от 1 до 1000 нанометров,
химические соединения, содержащие фосфор и кислород из следующей группы: окислы фосфора в степенях окисления фосфора +3 или +5, кислородные кислоты фосфора в степенях окисления фосфора +3 или +5, сложные эфиры указанных кислот фосфора, кислые соли указанных кислот фосфора, а также смеси указанных химических соединений.
Указанный результат достигается также тем, что в качестве полиэфиров используют полигидроксильные соединения, которые выбирают из группы полиэтиленгликолей с молекулярным весом от 1000 до 10000 дальтон, или смеси указанных полиэтиленгликолей с многоатомными спиртами, растворимыми в полиэтиленгликолях, или сополимеры многоатомных спиртов и полиэтиленгликолей, где весовое содержание многоатомных спиртов в смеси или в сополимере с полиэтиленгликолями не превышает 20%.
Указанный результат достигается также тем, что органический термопластичный полимер выбирают из группы полиолефинов или смеси полиолефинов с узким распределением молекулярного веса.
Указанный результат достигается также тем, что органический термопластичный полимер выбирают из группы полиолефинов или смеси полиолефинов с узким распределением молекулярного веса.
Указанный результат достигается также тем, что органический термопластичный полимер выбирают из группы полиэтиленов или смеси полиэтиленов с узким распределением молекулярного веса.
Указанный результат достигается также тем, что органический термопластичный полимер выбирают из группы полиэтиленов или смеси полиэтиленов с узким распределением молекулярного веса.
Указанный результат достигается также тем, что в качестве загустителя или одного из загустителей, содержащих фосфор и кислород, используют органические фосфаты или фосфиты, которые выбирают из сложных эфиров фосфорной или фосфористой кислоты, а также смеси и сополимеры указанных эфиров.
Указанный результат достигается также тем, что в качестве загустителя или одного из загустителей используют полиэтиленоксид с молекулярным весом от 100000 до 20000000 дальтон.
Определение терминов
Термопластичный полимерный материал
Термин «термопластичный полимерный материал» или для краткости «термопластичный материал», «термопласт» означает материал на основе органического полимера, который размягчается и приобретает способность к пластической деформации при нагреве до температуры меньше температуры его термического разложения. Термин «пластическая деформация» означает необратимую деформацию без разрушения под действием многократной или долговременной нагрузки. Термопластичные органические полимеры, имеющие отношение к предлагаемому техническому решению, включают полиолефины, фторированные полимеры, винилы, полистирол, полиакрил и полиметакрил, диеновые эластомеры, термопластические эластомеры и полиацетаты. Другая важная группа полимеров включает полиэстеры, полиамиды, поликарбонаты, полисульфоны и полиуретаны. Третья важная группа полимеров – термопластичные эфиры целлюлозы и сложные эфиры, а также эластомеры, если они могут быть переработаны подобно стандартным термопластам.
Наиболее предпочтительная группа полимеров – полиолефины, сополимеры, терполимеры и смеси полиолефинов с узким распределение молекулярного веса. Примеры: HDPE (полиэтилен высокой плотности), LLDPE (линейный полиэтилен низкой плотности), РР (изотактический полипропилен), EPR (эластомер на основе сополимера этилена/пропилена), EPDM (сополимер этилена/пропилена/диена), ЕВА (сополимер ацетат этилена/винила), ЕЕА (сополимер акрилат этилена/этила) и ЕАА (сополимер этилена/акриловой кислоты) и т.п.
Термопластический полимер может также быть смесью двух или более полимеров из указанного списка. Вышеупомянутые полимеры и сополимеры известны и доступны коммерчески, поэтому их подробное описание мы считаем ненужным. Эти полимеры могут быть переработаны в пластмассовые изделия разнообразными способами. Предлагаемое техническое решение особенно полезно при формовании полимеров экструзией и инжекцией расплавов термопластичного полимерного материала.
Добавка для улучшения свойств полимерных изделий и добавка для улучшения формования полимеров (процессинговая добавка)
Определения терминов «добавка для улучшения свойств полимерных изделий» и «добавка для улучшения формования полимеров» сделаны выше в обзоре уровня техники. Добавки для улучшения формования полимеров (процессинговые добавки) обычно не совместимы термодинамически с термопластическими органическими полимерами, т.е. при смешивании они не растворяются и не образуют одной фазы с основным термопластическим полимером. Такие добавки предназначены для уменьшения давления формования и устранения дефектов при формовании.
Простые и сложные полиэфиры
Термин простые полиэфиры означает гетероцепные полимеры, содержащие регулярно повторяющиеся группировки С-О-С в основной цепи. Простые эфиры получают реакцией поликонденсации многоатомных спиртов (полиолей) с полиалкиленоксидами, например, реакцией этиленгликоля с этиленоксидом в присутствии катализатора – едкой щелочи. Алифатические линейные простые полиэфиры включают полиацетали [-CHR-О-]n, где R=Н или алкил; полимеры алкиленоксидов [-(CHR)x-О-]n; сополимеры алкиленоксидов друг с другом, с ацеталями или виниловыми мономерами. Полиэтиленгликоль (ПЭГ) – простой алифатический линейный полиэфир. Температура плавления ПЭГ с молекулярным весом 600 дальтон составляет 17-23°С, для ПЭГ 1000 составляет 35-40°С, а ПЭГ 1500 составляет 44-48°С. Температура плавления ПЭГ растет с увеличением молекулярного веса и достигает значения 67°C, см. [F.E.Bailey. Alkylene Oxides and Their Polymers. CRC Press Science, 1991. ISBN 0824783840] и [О.Н.Дымент. Гликоли и другие производные окисей этилена и пропилена. – М.: Химия, 1976].
Сложный полиэфир – это категория полимеров, которая содержит функциональную группу эфира карбоновой кислоты С(O)-O- в своей основной молекулярной цепи. Карбоновые кислоты – класс органических соединений, молекулы которого содержат одну или несколько функциональных карбоксильных групп -СООН. Сложные полиэфиры обычно получают реакцией поликонденсации между многоатомным спиртом (полиолем) и многоосновной карбоновой кислотой, например, в реакции между диолем и дикарбоновой кислотой получают линейные сложные полиэфиры. Сложные эфиры, полученные в реакции между многоатомным спиртом и многоосновной неорганической кислотой, например борной кислотой, фосфорной кислотой, фосфористой кислотой, серной кислотой могут быть первичными, вторичными и третичными, то есть с замещением одного, двух или трех атомов водорода. Сложные эфиры, полученные из полиэтиленгликоля с молекулярными весом от 1000 до 10000 дальтон и многоосновной кислотой являются гидрофильными веществами. Сложные полиэфиры высокой молекулярной массы обычно имеют температуру плавления выше, чем простые полиэфиры. Все ароматические полиэфиры обычно обладают высокой температурой плавления. Пример ароматического полиэфира – полиэтилентерефталат (PET), его температура плавления+260°С.
Для целей настоящего технического предложения алифатические полиэфиры предпочтительно содержат, по крайней мере, одну гидроксилгруппу в молекуле. Еще лучше, если алифатические полиэфиры содержат, по крайней мере, две гидроксилгруппы. Гидроксилгруппы могут быть расположены в концах молекулы, они могут быть распределены вдоль молекулы, или они могут быть расположены и на концах и вдоль молекулы. Когда гидроксилгруппы расположены только вдоль цепи, то концевые группы могут быть любой нереактивной группой, например, метилгруппой. Дополнительно, предпочтительно использовать полигидроксильные алифатические полиэфиры, и наиболее предпочтительно использовать полиэтиленгликоли, с молекулярной массой от 1000 до 10000 дальтон. Для целей предлагаемого технического решения могут быть использованы смеси на основе таких полиэтиленгликолей, а также смесь, включающая низкомолекулярные многоатомные спирты, например, глицерин, полимеризованный глицерин, ксилит, сорбит, маннитол и гидрохинон, при условии, что температура плавления этой смеси не ниже 35°С. Для целей предлагаемого технического решения могут применяться сополимеры на основе указанных полиэтиленгликолей и многоатомных спиртов.
Силоксаны и Силанольные жидкости
Вязкоупругий материал, вязкоупругая жидкость
Упругий материал под нагрузкой может изменять форму и размеры без разрушения и восстанавливать исходные размеры после снятия нагрузки. Вязкоупругий материал определен в литературе, как тот материал, который обладает и упругими и вязкими свойствами. Вязкоупругие материалы могут демонстрировать как уменьшение, так и увеличение вязкости с увеличением скорости нагрузки. Вязкоупругая жидкость – это вязкоупругий материал, способный течь под нагрузкой. Механические свойства вязкоупругих материалов характеризуют с помощью динамического модуля Юнга, G*=G1+iG2, и тангенса угла потерь tan(.alpha.)=G2/G1, т.е. отношения мнимой части модуля Юнга G2 к его действительной части G1. Материал считается упругим, если G1/G2>1 или тангенс угла потерь tan(.alpha.)<1. Материал считается вязким, если G1/G2<1 или тангенс угла потерь tan(.alpha.)>1. Механические свойства вязкоупругих материалов изменяются с частотой нагрузки. Большинство расплавов полимеров проявляют вязкое поведение (G1/G2<1) при низких частотах и упругое поведение (G1/G2>1) на высоких частотах нагрузки. Комплексную вязкость определяют через динамический модуль Юнга как.eta.*=|G*|/(2.pi.f), где f – частота приложенной нагрузки. В литературе иногда используют термины «упруго-вязкий материал» и «упруго-пластичный материал», особенно для того, чтобы указать на преимущественно упругое поведение материала в диапазоне частот, характерном для его переработки или использования.
Золь, суспензия, взвесь, гель, студень
Органозоль – коллоидный раствор, состоящий из частиц очень малого размера 1-1000 нм, равномерно распределенных в органической жидкости. Золи отличаются от грубодисперсных систем (суспензий, эмульсий) размером частиц. Стабильные суспензии, не оседающие под действием силы тяжести, называются взвесями. Увеличение концентрации дисперсной фазы в золе приводит к появлению коагуляционных контактов между частицами и началу структурирования – гелеобразования. Коагуляционные структуры характеризуются низкой прочностью, определяемой ван-дер-ваальсовыми и водородными силами. Коагуляционные структуры характеризуются полным самопроизвольным восстановлением после механического разрушения. Дальнейшее повышение объемной концентрации приводит к постепенному исчезновению способности к тиксотропному восстановлению, а по мере снижения содержания дисперсионной среды теряются эластичные и пластические свойства, см. [«Химическая энциклопедия», – М.: изд. «Советская энциклопедия», 1988 /50/].
В русскоязычной технической литературе гель определяют как суспензию высокодисперсных частиц в коагуляционном контакте друг с другом, в отличие от студня, который представляет собой набухший в растворителе сетчатый полимер. Разновидностью студней являются системы, в которых устойчивые контакты между макромолекулами обеспечиваются локальной кристаллизацией группы цепей. При температуре выше температуры плавления кристаллических узлов студни превращаются в полимерные растворы. Студнеобразное состояние систем полимер-растворитель возникает также в случае взаимодействия с растворителем полимеров, имеющих сверхвысокий молекулярный вес. Свойства сетки межмолекулярных переплетений цепей аналогичны свойствам сеток с химическими или кристаллизационными узлами. Даже при продолжительном механическом воздействии в такой системе развиваются большие, практически полностью обратимые деформации, хотя такое студнеобразное состояние неустойчиво из-за постепенной перестройки межмолекулярных контактов. Эти системы занимают промежуточное положение между студнями и вязкоупругими растворами полимеров. В иностранной (англоязычной) технической литературе понятие студень (jelly) относится почти исключительно к пищевым продуктам, в то время, как набухшие в растворителе сшитые полимерные системы, растворы блок-сополимеров и полимеров сверхвысокого молекулярного веса, показывающие обратимые деформации и упругие свойства, относят к гелям (gel) вместе с коагулированными суспензиями высокодисперсных неорганических частиц в воде или органических растворителях.
Загустители пассивные и активные
Термин «загуститель полимерной жидкости» означает вещество, увеличивающее вязкость и упругость этой полимерной жидкости при смешивании с ней, но так, что сохраняется ее способность течь под нагрузкой. Загуститель не должен обязательно растворяться в полимерной жидкости, но образовывать золь или суспензию в ней. Загуститель можно назвать пассивным, если он химически не реагирует с полимерной жидкостью. Примеры пассивного загустителя: высокодисперсная окисью кремния (белая сажа) с размерами частиц от 1 до 1000 нм, соли металлов и растворимых в полимерной жидкости карбоновых кислот, высокомолекулярные полимеры и блок сополимеры, растворимые в полимерной жидкости, а также суспензии высокомолекулярных полимеров и блок сополимеров, набухающих в этой полимерной жидкости. Пассивные загустители часто используют в промышленности для создания золей, гелей, студней, взвесей, пасты. Например, для загущения нефтяных масел в целях получения пластичной смазки, промышленность широко использует мыла (соли высших карбоновых кислот, а также: литий, калий, натрий, кальций, алюминий, цинк), димочевину, бентонит, высокодисперсную окись кремния, см. [Т.Mang and W.Dresel (Eds). Lubricants and Lubrication (2-nd Edition), Wiley-VCH Verlag GmbH & Co. KgaA. 2007 /51/]. Загустители различаются удельной эффективностью увеличения вязкости. Содержание пассивных загустителей в пластичной смазке лежит в интервале от 5 до 40%, а обычно от 10 до 15%.
Для загущения алифатических полиэфиров промышленность использует высокодисперсные минеральные частицы с размером от 1 до 1000 нм, т.е. коллоидные частицы, см., например [М.Brauer, Y.C.Chu. Cable grease composition and articles incorporating same. U.S. Pat. No. 5,348,669. Sep.20, 1994. U.S. CI.: 508/136 /52/]. Другие загустители для полиэтиленгликолей и их производных известны из технической литературы. Например, известно использование солей лития, см. [T.R.Forbus, Jr. Polyglycol lubricants comprising trifluoromethane sulfonate. U.S. Pat. No. 4,569,774. Feb. 11, 1986. U.S. CI.: 508/406 /53/]. Cody et al. сообщают в патенте [S.L.Cody, M.R.Hoy, E.J.Roche, E.J.Walter. Soft gelatin pharmaceutical dosage form. U.S. Pat. No. 5,916,590. Jun. 29, 1999. U.S. CI.: 424/452 /54/] об использовании для загущения полиэтиленгликолей поливинилового спирта, эфиров целлюлозы, сополимеров этиленгликоля и пропиленгликоля, сорбита, а также натрия стеарата, натрия пальмината и кальция ацетата.
Для загущения растворимых в воде алифатических полиэфиров и, в частности, для загущения полиэтиленгликолей можно использовать высокомолекулярные полигидроксильные соединения, растворимые в воде, но нерастворимые в самом полиэтиленгликоле, например, выбранные из группы: поливинилпирролидон, полиакриламид, некоторые полисахариды и их производные (эфиры целлюлозы). Такие высокомолекулярные полимеры разбухают в полиэтиленгликоле. Их стабильную суспензию (взвесь) в полиэтиленгликоле можно приготовить с использованием воды, как общего растворителя, а затем удалить воду испарением.
В качестве загустителя можно использовать также такие вещества, которые реагируют с полимерной жидкостью. Активный загуститель, который реагирует с полимерной жидкостью, мы здесь называем также «отвердитель». Понятие «отверждение» соответствует изменению свойств полимерной системы и образованию химических связей в ходе реакции, которая, например, может быть конденсацией, полимеризацией или вулканизацией. Активный загуститель, т.е. отвердитель, может реагировать с частью маловязкой полимерной жидкости с образованием не сплошной пространственной сетки, а блок сополимера, растворенного в этой жидкости. Продукт такой реакции работает как пассивный загуститель. Например, смешивание полиэфиров и полиизоцианатов при условии, что количество полиизоцианата меньше стехиометрического, может приводить к образованию в объеме полиэфира высокомолекулярного разветвленного блок-сополимера полиуретана-полимочевины, но избыточное количество будет приводить к образованию трехмерной полимерной сетки. Полимерная жидкость, сшитая в трехмерную сетку, не показывает термопластичных свойств. При использовании полиэфиров с гидроксилгруппами, то есть полиолей, количество изоцианат групп должно быть меньше количества гидроксилгрупп полиоля. Преимущественно, количество изоцианат групп должно быть меньше двух третей от количества гидроксилгрупп полиоля в смеси.
Промышленность использует полиизоцианаты, в частности диизоцианаты, для загущения минеральных масел. Для этого в минеральном масле растворяют высокомолекулярные амины и добавляют полиизоцианаты, которые реагируют с аминами с образованием полимочевины. Аналогично, можно использовать растворы высокомолекулярных аминов и полиаминов в полиолях и добавлять полиизоцианат при условии, что молярное количество полиизоцианата примерно соответствует стехиометрическому соотношению для реакции с аминами или полиаминами. Скорость реакции изоцианат группы с амингруппой значительно превышает скорость реакции с гидроксилгруппой, поэтому в результате смешения компонентов получается полиоль, загущенный полимочевиной.
В качестве загустителя можно использовать также такие вещества, которые при смешивании с полиэфирами увеличивают водородные силы взаимодействия между молекулами полиэфира. Например, для загущения полиэтиленгликолей можно использовать многоатомные спирты, кислоты фосфора, сложные эфиры указанных кислот, растворимые в полиэтиленгликолях, например органические фосфиты и фосфаты, кислые соли указанных кислот и металлов, растворимые в полиэтиленгликолях, кислые соли указанных кислот и амония. Особый случай активного загустителя, т.е. отвердителя для полигидроксильных соединений, представляют такие химические соединения, которые содержат бор и кислород, а также такие химические соединения, которые содержат фосфор и кислород. Подробнее эти отвердители обсуждаются ниже.
Смесь полимерной жидкости с пассивным загустителем или с комбинацией пассивного загустителя и отвердителя называется компаундом. Механические свойства полимерной жидкости и компаунда измеряют при температуре формования полимерного материала.
Бораты и борные кислоты
В качестве активного загустителя (отвердителя) для низко- и высокомолекулярных полигидроксильных соединений, в том числе для силанолов, простых и сложных алифатических полиэфиров, содержащих, по крайней мере, две гидроксилгруппы, т.е. полиолей, можно использовать такие химические соединения, которые содержат бор и кислород: окись бора, борные кислоты, растворимые в воде соли борной кислоты, эфиры борной кислоты, кислые соли аминов и борной кислоты и смеси этих веществ. Понятие «борные кислоты» относится к трем составам: ортоборная кислота (также борная кислота, НЗВОЗ или В2О3·3Н2О), метаборная кислота (НВО2 или В2О3·Н2О), и тетраборная кислота (также пироборная, Н4 В4О7 или 2(В2О3)·Н2О). Примеры водорастворимых солей борной кислоты – соли щелочных металлов, соли аммония, кислые соли щелочноземельных металлов. Экономически привлекательные примеры водорастворимых солей борной кислоты – натрия метаборат (NaBO2), и натрия тетраборат (Na2B4O7). Борные кислоты и окись бора при нагревании до 100-170°C с готовностью реагируют с полигидроксильными соединениями, образуя эфиры: простыми спиртами, фенолами, гликолями, глицеринами, многоатомными спиртами, поливиниловым спиртом, моносахаридами, дисахаридами и полисахаридами. Борные эфиры включают моно-, ди- и три- замещенные органические эфиры борной кислоты.
Реакция поликонденсации между активным загустителем (отвердителем), содержащим бор и кислород, и полигидроксильными соединениями относится к обратимым реакциям. На открытом воздухе, т.е. в присутствии паров воды, прямая и обратная реакция находятся в равновесии, т.е. ковалентные связи в такой полимерной системе разрываются и воссоздаются с характерным временем, зависящим от количества воды в системе. При увеличении количества воды в системе характерное время существование ковалентной связи снижается. Если такая полимерная система находится под механической нагрузкой, время которой короче характерного времени существования ковалентной связи, то она проявляет упругие свойства, а под длительной нагрузкой она течет. Продукты реакции гидрофобных силанолов с боратами проявляют упругие свойства под механической нагрузкой с характерным временем короче 0,1 сек. Добавлением небольшого количества гидрофобных силанолов к гидрофильным полиолям можно снизить количество воды в системе и увеличить характерное время существования ковалентных связей, усредненное по системе. Для ускорения скорости реакции поликонденсации и смещения равновесия в сторону образования соединений боратов и полиэфира может быть использован катализатор. Примеры катализаторов реакции конденсации и обменной реакции между эфирами известны из технической литературы. В частности, катализатор может быть выбран из группы, которая включает неорганические кислоты, органические кислоты, металлические соли органических кислот (железа, олова, свинца, кобальта, марганца), алкоголяты некоторых металлов (титана, циркония), третичные амины, кислые соли аминов и органических кислот.
Фосфаты, фосфиты, окислы и кислоты фосфора (III и V)
В качестве пассивного и активного загустителя (отвердителя) для высокомолекулярных полиэтиленгликолей можно использовать такие химические соединения, которые содержат фосфор и кислород: окислы фосфора в степенях окисления фосфора +3 или +5; кислородные кислоты фосфора в степенях окисления фосфора +3 или +5; сложные эфиры указанных кислот фосфора, кислые соли указанных кислот фосфора, а также смеси указанных химических соединений.
Понятие «окислы фосфора в степенях окисления фосфора +3 или +5» относится к следующим веществам: Р2О3; Р2О5. Понятие «кислородные кислоты фосфора в степенях окисления фосфора +3 или +5» относится к следующим веществам: фосфористая кислота НЗРОЗ; мета- (НРО3), пиро(Н4Р2О7) и орто- (Н3РО4) фосфорная кислота. Окислы фосфора и кислоты фосфора реагируют с высокомолекулярными алифатическими полигидроксильными соединениями. Условия таких реакций известны из технической литературы. При использовании смеси кислот фосфора или окислов фосфора с полиэтиленгликолями в качестве процессинговой добавки внутри экструдера частично происходит образование сложных эфиров кислот фосфора и полигидроксильных соединений.
Привлекательные примеры активного загустителя – сложные эфиры кислот фосфора и, прежде всего, органические фосфиты и фосфаты. Понятие «органические фосфаты» относится к эфирам фосфорной кислоты общей формулы (RO)nP(O)(OH)(3-n), где R – органическая группа; n=1 – 3, и соли кислых эфиров фосфорной кислоты. Органические фосфаты широко применяются в промышленности в качестве добавок для модификации пластмасс (как пластификаторы, добавки для повышения огнестойкости). Понятие «органические фосфиты» относится к эфирам фосфористой кислоты общей формулы (RO)nP(OH)(3-n), где R – органическая группа; n=1-3, и солям кислых эфиров фосфористой кислоты. Органические фосфиты (вторичные и третичные) широко применяются в промышленности в качестве антиоксиданта для полимеров. В промышленности фосфиты для использования в качестве антиоксиданта приготавливают преимущественно из низкомолекулярных фосфитов по реакциям переэстерификации, т.е. обмена низкомелекулярных спиртов с высокомолекулярными спиртами и гликолями при нагреве в присутствии катализаторов. Для загущения полиэтиленгликолей можно использовать сложные эфиры кислот фосфора и многоатомных спиртов, которые имеют от 3 до 6 гидроксильных групп (глицерол, ксилит, сорбит, манитол), см. [L.Friedman, Hydroxy propoxy propyl phosphites, U.S. Pat. No. 3,009,939, Nov. 21, 1961, U.S. CI.: 260-461 /55/], [N.Mayer, G.Pfahler, H.Wiezer, Phosipites of Polyalcohols, USA Pat. No. 4,207,270. Jun.10, 1980 U.S. CI.: 260/927 /56/]. При использовании смеси низкомолекулярных эфиров сложных кислот фосфора или кислых солей кислот фосфора с полиэтиленгликолями в качестве процессинговой добавки образование сложных эфиров кислот фосфора и полиэтиленгликолей частично происходит внутри экструдера по реакции переэстерификации.
Органические фосфиты, которые применяются в промышленности в качестве антиоксиданта, описаны и классифицированны в [D.R.Stevenson, Т.С.Jennings, M.E.Harr, M.R.Jakupca. Phosphite ester additive compositions. U.S. Pat. No. 7,320,764, Jan. 22, 2008. U.S. CI.: 252/400.24 /57/]. Органофосфиты при комнатной температуре могут быть как жидкими, так и твердыми веществами с температурой плавления от 40 до 230°С. Большинство органических фосфитов, применяемых как антиоксидаты – это ароматические фосфиты или смешанные арил-алкил фосфиты. Ароматические фосфиты легко гидролизуются и образуют эффективные стабилизаторы-фенолы. При смешивании низкомолекулярных фосфитов с полиэтиленгликолями высокой молекулярной массы и при нагреве смеси происходит реакция переэстерификации, когда низкомолекулярный фенол или спирт отщепляется и замещается на высокомолекулярный полиэтиленгликоль. При добавлении полиэтиленгликоля с молекулярной массой от 1000 до 10000 дальтон в полимерный материал, содержащий органофосфиты в качестве антиоксидантов и при переработке расплава происходит частичное растворение антиоксидантов в указанном полиэтиленгликоле с увеличением вязкости смеси за счет увеличения водородных сил взаимодействия между молекулами полиэтиленгликолей, а часть компонентов реагирует внутри экструдера с синтезом высокомолекулярных органофосфитов, которые служат пассивным загустителем полиэтиленгликоля.
Серная кислота. Сульфаты
Улучшение качества формования наблюдается при использовании смеси указанных полиэтиленгликолей с серной кислотой или сложными эфирами серной кислоты. Однако серная кислота вызывает коррозию металла и не может быть рекомендована для использования в качестве компонента процессинговой добавки.
Для целей предлагаемого технического решения используется такой состав термопластичного полимерного материала, который содержит комплексную добавку для улучшения формования в количестве от 0,02 до 1 вес.%. Использование добавки в количестве более 1 вес.% допускается для ускоренного снижения потерь на трение при формовании и для ускоренного подавления дефектов экструзии, а также для приготовления концентрата добавки. Концентрат добавки, с ее содержанием от 1 до 10 вес.%, используется для более равномерного распределения указанной добавки в полимерном материале, но дополнительная операция приготовления концентрата удорожает производство. Применение комплексной добавки в количестве менее 0,02 вес.% не обеспечивает снижения давления при формовании полимерного материала и подавления дефектов формования полимеров с узким распределением молекулярного веса.
Полиэтиленгликоли с молекулярной массой от 1000 до 10000 дальтон дешевы и разрешены для использования в контакте с пищей и телом человека. Полиэтиленгликоли уже используют в промышленности как добавки при переработке полиэтилена, например для улучшения печати на полимерной пленки или улучшения качества сварки полимерной пленки нагревом. Применение полиэтиленгликолей с молекулярной массой менее 1000 дальтон с загустителями не показывает улучшения формования термопластичного полимерного материала. Более того, использование таких полиэтиленгликолей, как основного компонента добавки, приводит к проскальзыванию винта в шнек-экструдере и снижению подачи полимерного материала. Таким образом, применение низкомолекулярных полиэтиленгликолей в качестве основного компонента процессинговой добавки невозможно, но они могут присутствовать в небольшом количестве в смеси, при условии, что температура плавления такой смеси не менее 35°С.
Вязкость полиэтиленгликолей при температуре выше температуры их плавления, резко нарастает с увеличением молекулярного веса, поэтому эффект от использования загустителей снижается для ПЭГ с молекулярной массой от 6000 до 10000 дальтон. ПЭГ с молекулярной массой более 10000 дальтон уже используют в промышленности как процессинговую добавку без загустителя, но такие ПЭГ относительно дороги, поэтому их использование в качестве основного компонента добавки экономически нецелесообразно. Однако ПЭГ с молекулярным весом более 10000 дальтон могут присутствовать в небольшом количестве в смеси.
Для целей предлагаемого технического решения могут быть использованы смеси ПЭГ с молекулярным весом от 1000 до 10000 дальтон с небольшим количеством (менее 20%) низкомолекулярных полигидроксильных соединений, например из следующего списка: глицерин, полимеризованный глицерин, ксилит, сорбит, гидрохинон, низкомолекулярный поливиниловый спирт. При использовании низкомолекулярных полигидроксильных соединений в составе процессинговой добавки в количестве более 20 вес.% происходит снижение эффективности добавки.
Для приготовления процессинговой добавки в соответствии с предлагаемым техническим решением загуститель смешивают с полиэфиром перед формованием, а затем перемешивают с термопластичным полимером, или полиэфир и загуститель раздельно, одновременно или последовательно смешивают с термопластичным полимером перед формованием.
Загустители для полимерных жидкостей известны из технической литературы. Это, прежде всего, коллоидные минеральные частицы. Коллоидные минеральные частицы, как загуститель полимерной жидкости, например, нефтяного масла, давно используют в промышленности. Преимущественно, в промышленности применяют высокодисперсную окись кремния, приготовленную по технологии Aerosil, или бентонит. В частном случае реализации предлагаемого технического решения в качестве загустителя используют высокодисперсные минеральные порошки оксидов с размерами частиц от 1 до 1000 нм. Например, могут быть использованы окись кремния и окись титана, полученные по технологии Aerosil, т.е. взаимодействием газообразного четыреххлористого кремния или титана с парами воды. Коллоидные порошки окислов могут иметь гидрофобную поверхность, что достигается обработкой их парами силанов. Использование коллоидных минеральных порошков в количестве менее 0,02 вес.% показывает малый эффект, а при их концентрации более 20 вес.% смешивание их с полимерной жидкостью затруднено из-за значительного увеличения вязкости смеси. Дополнительно, использование более 20% этих загустителей в составе добавки для улучшения формования экономически не оправдано.
В качестве загустителей полимерных жидкостей используют также высокомолекулярные полимеры и блок сополимеры, растворимые в этой жидкости в количестве от 0,01 до 10 вес.%. Способы смешивания таких загустителей с жидкостью описаны в технической литературе. Использование указанных высокомолекулярных полимеров и блок сополимеров в количестве менее 0,01 вес.% показывает малый эффект, а при их концентрации более 10 вес.% смешивание их с полимерной жидкостью затруднено. Для растворения в жидкости полимеров со сверхвысоким молекулярным весом в количестве более 1-3 вес.% необходимо использовать маловязкий растворитель, который после смешивания компонентов удаляют испарением. Поэтому использование в качестве загустителя высокомолекулярных полимеров в количестве более 1 вес.% нерационально, а применение в количестве более 10% технически затруднено.
В промышленности известно применение термопластичного блок-сополимера (эластомера), растворимого в полиэфире, в качестве загустителя для приготовления гелей. Такой блок-сополимер смешивают с полиэфиром при температуре выше температуры плавления эластомера. В качестве загустителя можно использовать высокомолекулярный термопластичный эластомер на основе полиизоцианата с высокомолекулярным спиртом или амином, растворимым в полиэфире. В частности, такой загуститель может быть получен по известному в промышленности способу, а именно смешиванием высокомолекулярного амина с полиэфиром, а затем добавлением в раствор полиизоцианата. Преимущественно такой загуститель может быть приготовлен растворением высокомолекулярного амина в полиэфире и добавлением диизоцианата до получения блок сополимера димочевины.
В качестве загустителя полиэтиленгликолей можно использовать полиизоцианат или полиизоцианатный форполимер. Загуститель и полиэтиленгликоль перемешивают в виде порошков или в виде расплавов при нагревании. Количество изоцианатгрупп в смеси должно быть меньше количества гидроксилгруппполиэтиленгликолей. Преимущественно, количество изоцианатгрупп выбирают меньше двух третей от количества гидроксилгрупп. При использовании менее 0,1% полиизоцианата от массы полиэтиленгликоля добавка показывает малое улучшение качества формования по сравнению с использованием полиэтиленгликолей без загустителей. Использование более 10% полиизоцианата при условии, что количество изоцианатгрупп полиизоцианатов в молях меньше молярного количества гидроксилгрупп в полиэтиленгликолях, например, смешивание ПЭГ 1000 с высокомолекулярным изоцианатфорполимером экономически нецелесообразно.
Для загущения полимерной жидкости могут быть использованы не только золи минеральных частиц, но и суспензии полимерных частиц, не растворимых в этой полимерной жидкости. Такие суспензии наиболее стабильны, если они разбухают в полимерной жидкости. В частности, в качестве загустителя полиэтиленгликолей можно использовать высокомолекулярный полимеры, растворимые в воде, но не растворимые, а разбухающие в полиэтиленгликоле, например, поливинилпирролидон, полиакриламид. Способы приготовления суспензии полимерных частиц с использованием растворителя или простым смешиванием также описаны в технической литературе. Использование таких полимеров как загустителей в количестве менее 0,1 вес.% показывает малый эффект, а использование более 10% этих загустителей в составе добавки для улучшения формования экономически не оправдано.
Как загустители в промышленности широко применяются также металлические соли карбоновых кислот, растворимых в полимерной жидкости, например жирных кислот. Промышленность применяет для загущения полимерных жидкостей и получения пластичных смазок соли высших карбоновых кислот и следующих металлов: литий, калий, натрий, кальций, алюминий, цинк. Из технической литературы известно, что для загущения полигликолей применяется уксуснокислый кальций, стеарат натрия и пальминат натрия. Использование таких солей как загустителей в количестве менее 0,1 вес.% показывает малый эффект, а использование более 1% этих загустителей в составе добавки для улучшения формования технически не целесообразно, но может использоваться для других целей – например, для увеличения стабильности термопластичного полимерного материала при нагреве или увеличения стойкости полимерного материала к воздействию пламени.
В качестве загустителя можно использовать пассивный загуститель в сочетании с боратами. Бораты можно растворять в полиэфирах, или использовать в виде концентрированного раствора в многоатомных спиртах, например в глицерине, ксилите или сорбите. Такой раствор при комнатной температуре твердый и может использоваться в виде порошка. Перед формованием порошок раствора боратов смешивают с полиэфиром, затем смешивают с загустителем, а уже потом с термопластичным полимером; или приготавливают раствор боратов в полиэфире и этот раствор одновременно или последовательно с загустителем смешивают с термопластичным полимером; или три компоненты: полиэфир, загуститель и бораты, одновременно или последовательно в любом порядке смешивают с термопластичным полимером. Смешивание компонентов добавки для улучшения формования можно производить с нагревом или при комнатной температуре. Преимущественно загуститель смешивают с порошком полиэфира при комнатной температуре, а затем эту смесь и бораты в порошке или растворе смешивают при комнатной температуре с термопластичным полимером. Количество боратов выбирают из диапазона 0,1-19 вес.%, в пересчете на окись бора. Количество боратов в количестве менее 0,1 вес.% не показывает значительного улучшения свойств комплексной добавки, а добавление боратов в количестве более 19 вес.% снижает эффективность применения комплексной добавки.
В качестве загустителя можно использовать силанольную жидкость в сочетании с боратами. Силанолы выдерживают длительный нагрев без химического разложения, поэтому их применение в составе комплексной добавки увеличивает ее стабильность и эффективность при температуре формования термопластичного полимерного материала. Количество силанольной жидкости выбирают из диапазона 1-10 вес.%. Количество силанольной жидкости менее 1 вес.% не показывает значительного улучшения свойств комплексной добавки, а если количество силанольной жидкости превышает 10 вес.%, то приготовленный порошок или гранулы процессинговой добавки слипаются между собой при хранении. Силанольную жидкость смешивают при комнатной температуре с порошком полиэтиленгликолей для последующего смешивания с боратами и термопластичным полимером, или силанольную жидкость смешивают с порошком или расплавом раствора боратов в полиэтиленгликоле. Смешивание силанольной жидкости с порошком полиэтиленгликоля или порошком раствора боратов в полиэтиленгликоле при комнатной температуре обеспечивает более равномерное ее распределение в термопластичном полимерном материале. Смешивание силанольной жидкости при комнатной температуре с порошком полиэтиленгликоля для последующего смешивания с отвердителем и термопластичным полимером имеет техническое преимущество, так как увеличивается скорость осаждения компонентов комплексной добавки на внутреннюю поверхность оборудования для формования. Компоненты добавки осаждаются на внутреннюю поверхность оборудования для формования и реагируют там при повышенной температуре с увеличением вязкости продукта реакции относительно вязкости исходных компонентов.
В качестве загустителя полиэтиленгликолей можно использовать окислы фосфора, кислоты фосфора, серную кислоту, кислые соли указанных кислот, сложные эфиры кислот фосфора или сложные эфиры серной кислоты. Указанные химические соединения характеризуются сильными водородными связями. Они также реагируют с полиэтиленгликолями с образованием высокомолекулярных сложных эфиров. В качестве загустителя полиэтиленгликолей можно использовать органические фосфаты и фосфиты, т.е. сложные эфиры фосфорной и фосфористой кислот, например жидкие и твердые органические фосфиты, которые применяются в промышленности как добавки-антиоксиданты для полиолефинов. Высокомолекулярный полиэтиленгликоль реагирует с органофосфитами при нагреве по реакции переэстерификации. Перед формованием сложный эфир указанных кислот в виде порошка или жидкости или смесь указанных эфиров смешивают с полиэтилен гликолем, затем смешивают с другим загустителем, например с высокодисперсной окисью кварца, а уже потом с термопластичным полимером; или приготавливают раствор указанных сложных эфиров в полиэтиленгликоле и этот раствор одновременно или последовательно с загустителем смешивают с термопластичным полимером; или три компоненты: полиэтиленгликоль, загуститель и указанные сложные эфиры, одновременно или последовательно в любом порядке смешивают с термопластичным полимером. Смешивание компонентов добавки для улучшения формования можно производить с нагревом или при комнатной температуре. Преимущественно загуститель смешивают с порошком полиэтиленгликоля при комнатной температуре, а затем эту смесь и указанные сложные эфиры в порошке или жидкие смешивают при комнатной температуре с термопластичным полимером. Количество указанных сложных эфиров кислот фосфора выбирают из диапазона 0,1-20 вес.% от общего веса комплексной процессинговой добавки, в пересчете на окись фосфора. Количество указанных сложных эфиров кислот фосфора в количестве менее 0,1 вес.% не показывает значительного улучшения свойств комплексной добавки, а добавление их в количестве более 20 вес.% не приводит к увеличению эффективности комплексной добавки, но может использоваться для других целей – например, для увеличения стабильности термопластичного полимерного материала при нагреве или увеличения стойкости полимерного материала к воздействию пламени.
Если в качестве загустителя используют растворимые в полиэтиленгликоле соли металлов и карбоновых кислот, или органические фосфиты, или смесь указанных химических компонентов, то такие химические соединения часто уже присутствуют в составе некоторых сортов полимерного материала, выпускаемого промышленностью. Например, в качестве антиокислительной добавки для полиэтилена используют смеси стеарата цинка с органическими фосфитами. Для улучшения формования такого полимерного материала достаточно добавить только полиэтиленгликоль.
Полиэфир может содержать добавки, уменьшающие его термическое разложение – антиоксиданты, например гидрохинон. Дополнительно полиэфир может содержать добавки, подавляющие коррозию металла, например, третичные амины. Использование антиоксидантов и добавок, предотвращающих коррозию металла, в составе смазок и антиадгезивов на основе полиэфиров известно из патентной и технической литературы. Предлагаемые добавки или реагирующие компоненты для приготовления добавки в количестве от 1 до 10 вес.% могут быть смешаны с таким термопластичным полимерным материалом, который термодинамически совместим с основным термопластичным полимером, т.е. может быть изготовлен концентрат процессинговых добавок. Концентрат может быть гранулирован, чтобы эти гранулы могли быть в свою очередь дозированы и смешаны с гранулами основного компонента. Использование концентрата процессинговой добавки обеспечивает более однородное распределение добавок в термопластичном полимере, но удорожает производственный процесс. Для упрощения и удешевления производства можно подавать добавку в экструдер в виде жидкости при температуре выше ее плавления для смешивания с гранулами полимерного материала. Иначе добавку можно приготовить в виде гранул и смешать при комнатной температуре с гранулами полимерного материала для переработки в экструдере. Предлагаемую добавку можно смешать с минеральными пигментами или антиблоковой добавкой и использовать для приготовления соответствующих концентратов. Поскольку предлагаемая процессинговая добавка характеризуется низкой вязкостью при температуре формования, то она улучшает диспергирование минеральных частиц в полимерном материале.
Не связывая себя теорией, ниже мы предлагаем предположительное описание механизма действия добавки. Промышленное оборудование для формования полимеров изготавливают из разнообразных материалов, но преимущественно из металлов. Обычно используемые металлы – это сталь, латунь, бронза, никель и алюминиевые сплавы. В процессе формования термопластичного полимерного материала на металлическую поверхность, которая находится в контакте с расплавом термопласта, самопроизвольно осаждается из расплава слой процессинговой добавки, которая характеризуется более высокой адгезии к металлу. Наличие разделяющего слоя добавки на поверхности оборудования обеспечивает множество преимуществ в формовании полимеров. В частности, указанный слой работает как смазка и может подавлять неустойчивость «акулья кожа» при экструзии полимеров с узким распределением молекулярного веса. Скорость осаждения добавок из расплава полимерного материала растет пропорционально их количеству в термопласте, но также зависит от вязкости добавок. Скорость осаждения добавок резко возрастает, если вязкость расплава полимерного материала превышает вязкость добавок при температуре формования в 10 и более раз, см. [Joseph D.D. Steep wave fronts on extrudates of polymer melts and solutions: lubrication layers and boundary lubrication Journal of Non-Newtonian Fluid Mechanics, 70 (1997) 187-203 /58/]. Загуститель в полиэфире взаимодействует с молекулами растворителя силами межмолекулярного притяжения и водородными силами. При использовании добавки с загустителем для формования термопластичного полимера жидкий полиэфир самопроизвольно осаждается на поверхность металла вместе с загустителем. Маловязкий полиэфир стекает вдоль стенки, а загуститель за счет взаимодействия со стенкой отделяется и накапливается на поверхности металла так, что тонкий слой смеси полиэфира с загустителем превращается в вязкоупругий компаунд – пластичную смазку. Упругость компаунда поддерживает более толстый слой смазки по сравнению с использованием полиэфира без загустителя. При очень низкой концентрации загустителя (менее 0,01 вес.%) в полиэфире, накопление загустителя на границе с металлом происходит слишком медленно, а при слишком высоком содержании загустителя (10 вес.%) из-за повышенной вязкости смеси снижается скорость переноса добавки на поверхность металла. При переработке полимерного материала, который имеет широкое распределение молекулярного веса, например полиэтилена высокого давления, или полимера, содержащего значительное количество низкомолекулярной добавки-пластификатора, предлагаемая добавка работает не эффективно, так как количество пластификатора или низкомолекулярного маловязкого полимера в термопластичном материале превышает содержание добавки, разжижает слой добавки на поверхности металла и препятствует накоплению загустителя на поверхности металла
Сущность заявляемого изобретения проясняется примерами реализации и чертежами:
На Фиг.1 представлены для сравнения характеристические кривые снижения потерь на трение в стальном мундштуке 2×60 мм от времени для использования 0,1 вес.% известной процессинговой добавки Viton и с предлагаемыми добавками на основе полиэтиленгликолей ПЭГ 1500, ПЭГ 6000 и ПЭГ 10000 с загустителем.
На Фиг.2 представлены характеристические кривые снижения потерь на трение в стальном мундштуке 2×60 мм от времени для использования 0,1 вес.% известных процессинговых добавок.
На Фиг.3 представлены кривые изменения комплексной вязкости смесей ПЭГ 1000 и ПЭГ 10000 с высокодисперсной окисью кремния.
На Фиг.4. представлены кривые изменения механических свойств (G1/G2) смесей ПЭГ 1000 и ПЭГ 10000 с высокодисперсной окисью кремния.
На Фиг.5 представлена зависимость снижения потерь на трение при экструзии полиэтилена с добавками (0,2%) из смеси ПЭГ 1000 с окисью кремния от содержания окиси кремния.
На Фиг.6 представлена зависимость снижения потерь на трение при экструзии полиэтилена с добавками (0,2%) из смеси ПЭГ 1000 с Полиэтиленоксидом (ПО) от содержания ПО.
На Фиг.7 представлена зависимость снижения потерь на трение при экструзии полиэтилена с добавками (0,1%) из смеси ПЭГ 1500 с борной кислотой от содержания окиси бора.
На Фиг.8 представлена зависимость снижения потерь на трение при экструзии полиэтилена с добавками (0,1%) из смеси ПЭГ 1500 с фосфорной кислотой от содержания окиси фосфора (V).
На Фиг.9 представлены характеристические кривые снижения потерь на трение в стальном мундштуке 2×60 мм от времени при экструзии полиэтилена с добавками (0,2%) раствора боратов (ВМ) в ПЭГ 1500 и смеси этого раствора боратов с загустителями (содержание загустителей в смеси 2 вес.%): окись кремния (AS), силанол (SP) и окись полиэтилена ПО.
На Фиг.10 представлены характеристические кривые снижения потерь на трение в стальном мундштуке 2×60 мм от времени при экструзии полиэтилена с добавками (0,2%) ПЭГ 1500 и смеси ПЭГ 1500 с загустителями (содержание в смеси 4%): натрия стеарат (мыло); окись титана (AT) и полиакриламид (ПАА).
На Фиг.11 представлены характеристические кривые снижения потерь на трение в стальном мундштуке 2×60 мм от времени при экструзии полиэтилена с добавками (0,1%) из ПЭГ 2000; смеси ПЭГ 2000 с окисью кремния (содержание в смеси 4%); раствора боратов в ПЭГ 2000 (ВМ); смеси ПЭГ 2000 с MDI форполимером Suprasec (1088).
На Фиг.12 представлены характеристические кривые снижения потерь на трение в стальном мундштуке 2×60 мм от времени при экструзии полиэтилена с добавками ПЭГ 1000 с полиэтиленоксидом (0,1 вес % ПО в добавке) при содержание добавки в смеси с полиэтиленом 0,1; 0,2; 0,5; 1 вес.%%.
На Фиг.13 представлены характеристические кривые снижения потерь на трение в стальном мундштуке 2×60 мм от времени при экструзии полиэтилена с добавками (0,2%) смеси раствора боратов в глицерине (GL+BM), указанного раствора в ПЭГ 1500 с добавкой окиси кремния (GL+BM+AS) или с добавкой полиэтиленоксида (0,1 вес.% ПО в добавке) (GL+BM+ПО), а также смеси раствора боратов в глицерине с гидрофобным сложным эфиром и с окисью кремния (AG+GL+BM+AS).
На Фиг.14 представлены характеристические кривые снижения потерь на трение в стальном мундштуке 2×60 мм от времени при экструзии полиэтилена с добавками смеси раствора фосфатов и сорбита в ПЭГ 6000. Содержание добавки в смеси с полиэтиленом 0,05 и 0,1 вес.%.
На Фиг.15 представлены характеристические кривые снижения потерь на трение в стальном мундштуке 2×60 мм от времени при экструзии полиэтилена с добавками смеси раствора фосфатов и сорбита в ПЭГ 1500 с добавлением высокодисперсной окиси кремния как пассивного загустителя. Содержание добавки в смеси с полиэтиленом от 0,025 до 0,1 вес.%.
На Фиг.16 представлены характеристические кривые снижения потерь на трение в стальном мундштуке 2×60 мм от времени при экструзии полиэтилена с добавками (0,1%) из смесей: ПЭГ 1500 и фосфорной кислоты (РА), ПЭГ и фосфорной кислоты и сорбита (PA+SO), ПЭГ и фосфорной кислоты и сорбита с добавлением высокодисперсной окиси кремния как пассивного загустителя (PA+SO+AS), а также раствора органофосфита Hostanox PAR 62 (HTNX) в ПЭГ 1500.
Примеры реализации
Эксперименты были выполнены, используя коммерчески доступный сорт LLDPE «LL1201 XV» от компании ExxonMobil. Этот материал был выбран из-за его чистоты и низкого уровня добавок в его составе. Материал имеет плотность – 0,925 г/см3, точка плавления – 123°С и индекс расплава – 0,7.
Следующие материалы использовались в экспериментах, нашедших свое отражение в примерах реализации:
Dynamar Е-15653 от компании 3М,
Viton Free Flow SC-PW от компании DuPont,
Kynar от компании Atofina,
Geniomer 140 от компании Wacker Chemie,
Линейный сложный полиэфир Baycoll AD5027 от компании Bayer, эквивалентное содержание гидроксила – 0,85 вес.%,
Глицерин, Сорбит,
Натрия стеарат,
Борная кислота, Фосфорная кислота,
Органофосфит Hostanox PAR 62 от компании Clariant,
Полиакриламид ПАА, молекулярный вес 11000000 дальтон,
Полиэтиленгликоли: ПЭГ-200, ПЭГ-600, ПЭГ-1000, ПЭГ-1500, ПЭГ-2000, ПЭГ-4000, ПЭГ-6000, ПЭГ-8000, ПЭГ-10000,
Полиэтиленоксид ПО, молекулярный вес 5000000 дальтон, от компании Alfa Aesar,
PPDI диазоцианат (para-phenyl diisocyanate) Hylene от компании DuPont Polymer Specialties, содержание NCO – 52,5%,
MDI-форполимер Suprasec 1088 от компании Huntsman,
Силиконовая жидкость DOW 3-0133 POLYMER от компании Dow Corning, эквивалентное содержание силанол-групп (Si-OH) – 0,153%,
Высокодисперсная окисью кремния Aerosil 300,
Высокодисперсная окись титана Aerosil P25 от компании Degussa.
Пример 1. Экструзия полиэтилена с известными процессинговыми добавками
Порошок известной процессинговой добавки Viton FF смешали с полиэтиленом в количестве 1 г добавки на 1 кг полиэтилена. Экструзию провели на скорости около 40 мм/сек. Характеристическая кривая уменьшения потерь на трение от времени экструзии показана на Фиг.1. Видно, что добавка начинает действовать не сразу, а примерно через 35 минут. Это время ожидания называют также временем индукции. Для промышленности важно знать не только время индукции, но и время восстановления, то есть прекращения действия добавки, если переходят на экструзию полимера без добавки. Для этой цели в примерах реализации проводили экструзию 1 кг смеси полиэтилена с добавкой, а потом проводили экструзию чистого полиэтилена. Момент смены полиэтилена с добавками на чистый полиэтилен показан на Фиг.2, и Фиг.9 – Фиг.13 вертикальной штриховой линией.
Порошки известных фторированных процессинговых добавок Viton FF, Dynamar и Kynar смешали с полиэтиленом в количестве 2 г добавки на 1 кг гранул полиэтилена. Эти смеси полиэтилена с добавками загрузили в шнек-экструдер. Экструзию вели на скорости около 40 мм/сек. Экструзия 1 кг смеси на такой скорости продолжается около 2 часов 20 минут. После экструзии 1 кг смеси полиэтилена с добавками проводили экструзию около 1 кг чистого полиэтилена. Снижение потерь на трение при использовании добавки Dynamar мало отличается от использования добавки Viton FF. При использовании фторированных полимеров Viton и Dynamar в качестве процессинговых добавок экструдат накапливал значительный статический электрический заряд. При использовании добавки Kynar (смесь фторированных полимеров, около 60 вес.%, с полиэтиленгликолем, около 40 вес.%) накопление заряда не происходило, но на выходе мундштука вокруг отверстия накапливался фторированный полимер, который на воздухе окислялся.
Приготовили термопластичный полиуретановый эластомер (TPUE) из ПЭГ 8000 и диизоцианата PPDI через стадию изоцианат форполимера. Полимеризовали форполимер добавкой диэтиленамина. Гранулы (1 г) следующих термопластичных полиуретановых эластомеров: Geniomer (TPUE на основе силоксана); Baymod (TPUE на основе сложного полиэфира) и приготовленного TPUE на основе полиэтилен гликоля ПЭГ 8000, смешали каждый с 1 кг гранул полиэтилена. Смешиванием боратов и силанола с добавками фосфорной кислоты, как катализатора, приготовили продукт, который напоминал по свойствам известную «прыгающую замазку» Silly Putty. Приготовление добавки на основе силанола и боратов намного проще по сравнению с процессом приготовления термопластичного полиуретанового эластомера. Кусочки продукта Silly Putty, приготовленного из силанола и боратов, также смешали отдельно с 1 кг гранул полиэтилена. Смеси полиэтилена с добавками использовали в шнек-экструдере. Экструзию вели так, как указано выше. Характеристические кривые уменьшения потерь на трение от времени экструзии представлены на Фиг.2. Сравнением с Фиг.1 видно, что добавки на основе термопластичных полиуретанов, кроме Baymod, а также добавка, полученная реакцией силанола с боратами, показывают более эффективное снижение потерь на трение, чем добавка на основе фторированных полимеров Viton. Дополнительно видно, что эти добавки не накапливаются в экструдере. При использовании добавки Geniomer накапливался статический электрический заряд, но меньше, чем при использовании добавок Viton и Dynamar.
Пример 2. Механические свойства смесей ПЭГ с высокодисперсной окисью кремния как загустителем
При температуре около 75°С приготовили ряд образцов смеси ПЭГ 10 000, а также смеси ПЭГ 1000 с высокодисперсным аморфным оксидом кремния Aerosil 300. С помощью прибора Rheotest RT-20 произвели измерения динамического модуля Юнга, в зависимости от частоты. На Фиг.3 представлены зависимости комплексной вязкости,.eta.*=G*/f. На Фиг.4 представлены зависимости отношения G2/G1 на частоте 2,5 Гц от содержания окиси кремния в смеси. Видно, что вблизи содержания в смесях окиси кремния 7,5-8 вес.% резко нарастает упругость смеси. Аналогично отмечено нарастание вязкости смеси. Увеличение вязкости и упругости смеси при увеличения содержания окиси кремния в смеси соответствует установлению коагуляционных контактов между коллоидными частицами окиси кремния и превращению смеси в вязкоупругий гель.
Пример 3. Экструзия полиэтилена с добавками ПЭГ различного молекулярного веса с высокодисперсным порошком оксидов как загустителями
Для получения предлагаемой добавки загуститель (высокодисперсный порошок окиси кремния Aerosil 300 или сокращенно AS) смешали с ПЭГ в количестве 6 частей на 100 частей ПЭГ. Добавки (2 г) смешали с гранулами полиэтилена (1 кг) и загрузили в питатель шнек-экструдера. Экструзию вели на скорости около 40 мм/сек при температуре 185°С. Для сравнения мы провели экструзию с чистым ПЭГ без загустителя. При экструзии полиэтилена с добавками ПЭГ 200 с окисью кремния Aerosil 300 наблюдали снижение скорости подачи материала на 25-30% и осцилляции силы тока для вращения мотора экструдера, которые можно объяснить проскальзыванием винта при подаче материала. При экструзии полиэтилена с добавками ПЭГ 600 с Aerosil 300 наблюдали снижение скорости подачи материала на 23-28% и осцилляции силы тока для вращения мотора экструдера на постоянной скорости вращения. Подавления дефектов экструзии «акулья кожа» не наблюдалось для обоих типов полиэтиленгликоля. При использовании ПЭГ с молекулярным весом: 1000; 1500; 2000; 4000; 6000; 8000; 10000 в качестве основного компонента добавки и высокодисперсного порошка окиси кремния в качестве загустителя мы наблюдали подавление дефектов экструзии «акулья кожа», когда потери на трение уменьшались на 15-20%. Мы также наблюдали небольшое (от 1 до 5%) увеличение скорости экструзии при неизменной скорости вращения винта шнек-экструдера при использовании добавок этих ПЭГ с загустителями при содержании добавок менее 0,5 вес.%. Таким образом, использование смеси ПЭГ с молекулярным весом от 1000 до 10 ООО дальтон с загустителем позволяет подавить дефекты экструзии «акулья кожа» и улучшить качество формования.
Пример 4. Экструзия с добавками смеси ПЭГ 1000 и высокодисперсной окиси кремния как загустителя
Для определения влияния количества высокодисперсной окиси кремния как загустителя на эффективность процессинговой добавки мы использовали смеси ПЭГ 1000 с окисью кремния Aerosil 300. Полиэтиленгликоль смешали с загустителем при температуре около 75°С при содержании 0,025; 0,1; 1; 6 и 10 вес.%%. Для равномерного распределения загустителя использовали ультразвуковой смеситель. Приготовленную добавку (2 г) смешали с чистым полиэтиленом (1 кг). Экструзию вели, как описано выше. Зависимость максимального достигнутого снижения трения от содержания высокодиспесной окиси кремния представлено на Фиг.5. Предполагая непрерывность и монотонность изменения эффективности от содержания загустителя, можно ожидать, что влияние загустителя будет заметно при содержании в интервале от 0,02 до 20 вес.%. Смеси с содержанием загустителя 7 вес.% и выше трудно приготавливать из-за их высокой вязкости. Таким образом, для целей настоящего технического предложения содержание высокодисперсной окиси кремния в добавке преимущественно выбирают из диапазона от 0,05 до 7 вес.%.
Пример 5. Экструзия с добавками смеси ПЭГ 1000 и полиэтиленоксида как загустителя
Для определения влияния количества оксида полиэтилена как загустителя на эффективность процессинговой добавки использовали смеси ПЭГ 1000 с высокомолекулярным полиэтиленоксидом (ПО) с молекулярным весом 5000000 дальтон. Полиэтиленгликоль смешали с загустителем при температуре около 75°С при содержании 0,005; 0,025; 0,065 и 1 вес.%%. Приготовленную добавку (2 г) смешали с чистым полиэтиленом (1 кг). Экструзию вели, как описано выше. Зависимость максимального достигнутого снижения трения от содержания полиэтиленоксида представлена на Фиг.6. Предполагая непрерывность и монотонность изменения эффективности от содержания загустителя, можно ожидать, что влияние загустителя будет заметно при содержании в интервале от 0,01 до 10 вес.%. Для приготовления смесей с содержанием высокомолекулярного ПО от 1 до 10 вес.% необходимо использовать растворитель, воду, и удалять ее испарением после смешивания компонентов. Таким образом, для целей настоящего технического предложения содержание полиэтиленоксида в добавке преимущественно выбирают из диапазона от 0,02 до 1 вес.%.
Пример 6. Экструзия полиэтилена с добавками ПЭГ 1500 с борной и фосфорной кислотами
Приготовили смеси борной кислоты с ПЭГ 1500 при содержании борной кислоты 20 вес.%. При нагреве до 140°С растворили борную кислоту и в вакууме отогнали воду из полученного раствора. Разбавлением раствора чистым ПЭГ 1500 получили составы с содержанием борной кислоты: 1,25; 2,5; 5; 10 вес %%. Экструзию провели так, как описано выше, при содержании добавки 0,1 вес.%. Зависимость максимально достигнутого снижения трения от содержания боратов в пересчете на окись бора представлена на Фиг.7. Предполагая непрерывность и монотонность изменения эффективности от содержания окиси бора, можно ожидать, что влияние загустителя будет заметно при его содержании в интервале от 0,4 до 20 вес.%. При использовании ПЭГ с молекулярным весом от 6000 до 10000 вместо ПЭГ 1500 влияние загустителя заметно при содержании окиси бора в интервале от 0,1 до 20 вес.%.
Приготовили смеси фосфорной кислоты с ПЭГ 1500 при содержании фосфорной кислоты 10 вес.%. При нагреве до 160°С растворили фосфорную кислоту и добавили борную кислоту в количестве 1 вес.% и в вакууме отогнали воду из полученного раствора. Разбавлением раствора чистым ПЭГ 1500 получили составы с содержанием фосфорной кислоты в вес.%: 0,1; 1; 2,5; 5. Экструзию вели так, как описано выше, при содержании добавки 0,1 вес.%. Зависимость максимального достигнутого снижения трения от содержания фосфатов в пересчете на окись фосфора представлена на Фиг.8. Предполагая непрерывность и монотонность изменения эффективности от содержания борной кислоты, можно видеть, что влияние загустителя заметно при его содержании в интервале от 0,2 до 20 вес.%. При использовании ПЭГ с молекулярным весом от 6000 до 10000 вместо ПЭГ 1500 влияние загустителя заметно при содержании окиси фосфора в интервале от 0,1 до 20 вес.%.
Пример 7. Экструзия полиэтилена с добавками раствора боратов в ПЭГ 1500 с загустителями
Приготовили раствор боратов в ПЭГ 1500. В качестве боратов на 1 кг ПЭГ использовали смесь борной кислоты (24,8 г) и безводного боракса (5 г). При нагреве до 100°С растворили бораты и в вакууме отогнали воду из полученного раствора. В качестве загустителей ПЭГ 1500 с боратами использовали высокодисперсную окись кремния Aerosil 300 (AS), полиэтиленоксид (ПО) и силанольную полимерную жидкость D0W 3-0133 POLYMER (SP) в количестве 6 частей на 100 частей ПЭГ по весу. Для сравнения использовали раствор боратов в ПЭГ 1500 без загустителей. Добавки (2 г) в виде порошка смешали с гранулами полиэтилена (1 кг) и смеси загрузили в питатель шнек-экструдера. Экструзию провели так, как описано выше. Характеристические кривые уменьшения потерь на трение от времени представлены на Фиг.9. Из сравнения кривых видно, что применение загустителей снижает потери на трение.
Пример 8. Экструзия полиэтилена с добавками ПЭГ 1500 с различными загустителями
В качестве загустителя ПЭГ 1500 использовали полиакриламид с молекулярным весом 11000000 дальтон в количестве 6 частей на 100 частей ПЭГ. Полиакриламид разбухает в ПЭГ, но не растворим в нем. Смеси приготовили растворением ПЭГ и загустителя в воде и удалением растворителя при нагреве. Окончательную сушку провели с нагревом в вакууме. В другом случае в качестве загустителя использовали соль карбоновой кислоты – стеарат натрия (мыло) в количестве 1 часть на 100 частей ПЭГ. Смесь приготовили растворением мыла в жидком ПЭГ. Приготовили смесь коллоидной окиси титана в количестве 6 частей и 100 частей ПЭГ. Для сравнения использовали ПЭГ 1500 без загустителя. Характеристические кривые уменьшения потерь на трение от времени представлены на Фиг.9. Из сравнения кривых видно, что применение загустителей снижает потери на трение, а в качестве загустителей можно использовать металлические соли карбоновых кислот, высокодисперсную окись титана и высокомолекулярные полимеры, не растворимые в ПЭГ, но растворимые в воде и разбухающие в ПЭГ.
Пример 9. Экструзия полиэтилена с добавками ПЭГ 2000 с различными загустителями
В качестве загустителя ПЭГ 2000 использовали высокодисперсный (коллоидный) порошок окиси кремния (4 части на 100 частей ПЭГ); MDI-форполимер Suprasec 1088 (или сокращенно 1088) и раствор боратов в ПЭГ в комбинации с высокодисперсной окисью кремния. Для сравнения использовали ПЭГ 2000 без загустителя. Смеси готовили с жидким ПЭГ. После смешивания продукт измельчали при комнатной температуре. Полученные порошки смешивали с гранулами полиэтилена при содержании добавки 0,1 вес.%. Экструзию провели так, как описано выше. Характеристические кривые уменьшения потерь на трение от времени представлены на Фиг.11. Из сравнения кривых видно, что применение загустителей снижает потери на трение.
Пример 10. Экструзия полиэтилена с добавками ПЭГ 10000 с различными загустителями
В качестве загустителя ПЭГ 10000 использовали коллоидный порошок окиси кремния (6 частей на 100 частей ПЭГ) или PPDI диазоцианат (0,16%, обозначено как ppdi; 0,8%, обозначено как PPDI). Для сравнения использовали ПЭГ 10 ООО без загустителя. Смеси готовили с жидким ПЭГ. После смешивания продукт измельчали при комнатной температуре. Полученные порошки смешивали с гранулами полиэтилена при содержании добавки 250 частей на миллион, т.е. 0,025 вес.%. Экструзию вели как описано выше. При использовании чистого ПЭГ 10000 снижение потеря на трение зарегистрировано на 14,5%. Применение полиизоцианатов как загустителя снижает потери на трение по сравнению с чистым ПЭГ 10000 еще на 14% для ppdi (28,5%) и на 19% для PPDI (33,5%). Смесь ПЭГ 10000 с PPDI диазоцианатом (0,16%) в количестве 3 г смешали с 3 кг гранул полиэтилена и использовали для экструзии, как описано выше. Характеристическая кривая представлена на Фиг.1 для сравнения с используемой в промышленности добавкой для улучшения формования на основе фторированных полимеров. Видно, что при том же содержании в смеси предлагаемая добавка на основе ПЭГ с загустителем обеспечивает более эффективное снижение потерь на трение, чем используемая в промышленности добавка на основе фторированных полимеров Viton.
Пример 11. Экструзия полиэтилена с добавками смеси ПЭГ 1000 с ПО при разном содержании смеси
Смесь полиэтиленгликоля ПЭГ 1000 с полиэтиленоксидом (0,1%), приготовленную в Примере 5 смешали с полиэтиленом при содержании добавки от 0,1 до 1 вес.%. Характеристические кривые уменьшения потерь на трение от времени представлены на Фиг.12. Видно, что содержание добавки 1 вес.% обеспечивает лишь небольшое снижение потерь на трение по сравнению с содержанием добавки 0,5 вес.%. Из характеристической кривой видно, что при содержании добавки 1 вес.% значительно удлиняется время, за которое добавка может быть удалена из экструдера путем экструзии полиэтилена без добавки. Дополнительно обнаружено, что массовая скорость экструзии при содержании добавки 1 вес.% снижается на 10% по сравнению с экструзией без использования добавки. Можно сделать вывод, что применение предлагаемой добавки в количестве более 1 вес.% для экструзии нецелесообразно, но может быть использовано для экструзии полимера с наполнителями.
Пример 12. Экструзия полиэтилена с добавками полиэфира или ПЭГ с загустителями и с добавлением отвердителя в порошке
Приготовили раствор борной кислоты (окиси бора) и боракса в глицерине (глицероле): на 100 г глицерина взяли 100 г борной кислоты и 25 г безводного боракса. При нагреве до 100°С в вакууме отогнали воду из раствора. Полученный раствор, напоминающий прозрачное и бесцветное хрупкое стекло, размололи в порошок при комнатной температуре. Порошок раствора боратов использовали как компонент комплексной процессинговой добавки в количестве 16 г раствора боратов на 100 г полиэфира с загустителем. Использование раствора бората в виде отдельного компонента процессинговой добавки упрощает ее изготовление. Провели экструзию с добавками смеси гидрофобного сложного полиэфира Baycoll AD5027 с Aerosil 300 как загустителем и с раствором боратов в глицерине при соотношениях компонентов, указанных выше. Смешали жидкий ПЭГ 1500 с высокодисперсной (коллоидной) окисью кремния (1 часть на сто частей ПЭГ) или с полиэтиленоксидом ПО. Полученные смеси при комнатной температуре перемололи в порошок, смешали с порошком раствора боратов в глицерине и использовали аналогично описанному выше в качестве процессинговой добавки при содержании 0,2 вес.%. Характеристические кривые приведены на Фиг.13. Видно, что в случае использования гидрофобного сложного полиэфира с загустителем и боратами снижение потерь на трение меньше, чем для применяемых в промышленности процессинговых добавок. Дополнительно замечено, что при использовании гидрофобных полиэфиров в качестве компонента процессинговой добавки массовый расход полиэтилена при заданной скорости вращения винта экструдера снижается на 4-6%. Это снижение может быть объяснено проскальзыванием винта экструдера.
Пример 13. Экструзия полиэтилена с добавками раствора фосфатов в ПЭГ 6000
Приготовили органофосфат следующим образом: 18,1 г сорбита смешали с 22,4 г ортофосфорной кислоты и нагрели при помешивании до 130°С до получения темно-янтарного цвета смеси. Полученный продукт в количестве 3,7 г смешали с 100 г ПЭГ 6000, нагрели до 130°С и остудили до комнатной температуры. Добавки (0,5 или 1,0 г) смешали с гранулами полиэтилена (1 кг) и смеси загрузили в питатель шнек-экструдера. Экструзию вели как описано выше. Добавки (5 г) в виде порошка смешали с гранулами полиэтилена (5 кг) и смесь загрузили в питатель шнек-экструдера. Экструзию вели как описано выше. Характеристические кривые уменьшения потерь на трение от времени представлены на Фиг.14 сплошной, штриховой и пунктирной линиями.
Приготовили органофосфат следующим образом: 15,3 г Сорбита (SO) смешали с 49 г ортофосфорной кислоты (РА) и нагрели при помешивании до 130°С до получения темно-янтарного цвета смеси. Полученный продукт в количестве 2,17 г смешали с 100 г ПЭГ 6000, нагрели до 130°С и остудили до комнатной температуры. Добавки (0,25 или 1,0 г) смешали с гранулами полиэтилена (1 кг) и смеси загрузили в питатель шнек-экструдера. Экструзию вели как описано выше. Добавки (2,5 г) в виде порошка смешали с гранулами полиэтилена (5 кг) и смесь загрузили в питатель шнек-экструдера. Экструзию вели как описано выше. Характеристическая кривая уменьшения потерь на трение от времени для использования 0,05% добавок представлена на Фиг.14 штрихпунктирной линией, а для использования 0,1% добавок представлена штрих-штрихпунктирной линией. Характеристическая кривая для использования 0,025% не показана, так как снижение потерь на трение было незначительным. Видно, что при том же содержании в смеси предлагаемые добавки из ПЭГ 6000 с загустителем на основе органофосфатов обеспечивает более эффективное снижение потерь на трение, чем используемая в промышленности добавка на основе фторированных полимеров. Увеличение содержания фосфатов в составе добавки дает более эффективное снижение потерь на трение при содержании добавок 0,05%.
Пример 14. Экструзия полиэтилена с добавками раствора органофосфатов в ПЭГ 1500 и высокодисперсной окиси кремния как загустителя
Приготовили органофосфат следующим образом: 2,0 г сорбита смешали с 6,44 г ортофосфорной кислоты и нагрели при помешивании до 130°С до получения темно-янтарного цвета смеси. Полученный продукт смешали с 41,5 г ПЭГ 1500, нагрели до 130°С и остудили до комнатной температуры. В качестве пассивного загустителя в эту смесь добавили 0,53 г высокодисперсной окиси кремния Aerosil 300 (AS). Добавки (0,5 или 1,0 г) смешали с гранулами полиэтилена (1 кг) и смеси загрузили в питатель шнек-экструдера. Экструзию вели как описано выше. Характеристические кривые уменьшения потерь на трение от времени представлены на Фиг.15. Добавки (5 г) в виде порошка смешали с гранулами полиэтилена (5 кг) и смесь загрузили в питатель шнек-экструдера. Экструзию вели как описано выше. Характеристическая кривая уменьшения потерь на трение от времени представлена на Фиг.1. При сравнении характеристических кривых на Фиг.1 видно, что при том же содержании в смеси предлагаемая добавка из ПЭГ 1500 с загустителем на основе органофосфатов обеспечивает более эффективное снижение потерь на трение, чем используемая в промышленности добавка на основе фторированных полимеров Viton.
Пример 15. Экструзия полиэтилена с добавками раствора фосфатов, многоатомного спирта и высокодисперсной окиси кремния в ПЭГ 1500
50 г ПЭГ 1500 смешали с 2 г фосфорной кислоты. 50 г ПЭГ 1500 и 2 г сорбита смешали с 4,3 г фосфорной кислоты и 0,5 г борной кислоты. 41.5 г ПЭГ 1500 смешали с 2 г сорбита, с 0,5 г высокодисперсной окиси кремния и 6,44 г фосфорной кислоты. Нагрели каждую смесь до 160°С и в вакууме отогнали воду из полученного раствора. Полученные продукты использовали как добавки в полиэтилен при количестве добавок 0,1 вес.%. Экструзию вели как описано выше. Характеристические кривые уменьшения потерь на трение от времени представлены на Фиг.16. Видно, что при использовании смеси ПЭГ с высокодисперсной окисью кремния, многоатомным спиртом и фосфорной кислотой предлагаемая добавка обеспечивает наивысшее снижение потерь на трение.
Пример 16. Экструзия полиэтилена с добавками раствора органо-сульфата в ПЭГ 1500
Во всех приведенных выше примерах реализации мы использовали линейный полиэтилен низкой плотности, который содержал антиоксидант. Обычно промышленность использует смеси стеарата цинка с органофосфитами в качестве антиоксиданта. Выше в Примере 7 было показано, что стеарат натрия в смеси с полиэтиленгликолем снижает потери на трение. Чтобы изучить эффект применения смесей полиэтиленгликоля с органофосфатами 40 г ПЭГ 1500 смешали с 10 г органофосфита Hostanox PAR 62 от компании Clariant, который используется как антиоксидант для полиолефиров. Характеристическая кривые уменьшения потерь на трение от времени представлена на Фиг.16. Видно, что применение органофосфата в смеси с полиэтиленгликолем снижает потери на трение по сравнению с чистым ПЭГ 1500.
В технической литературе отмечено, что применение чистого полиэтиленгликоля в качестве добавки в полиэтилен, не содержащий антиоксидант, не приводит к снижению трения. Снижение потерь на трение с применением чистого ПЭГ без загустителя в примерах реализации мы объясняем наличием антиоксиданта в составе используемого полиэтилена, который является загустителем для полиэтиленгликоля. Дополнительное снижение потерь на трения наблюдается при использовании предлагаемых составов процессинговой добавки, содержащих загустители.
Выводы
Добавки для улучшения формования термопластичного полимерного материала, приготовленные на основе простых и сложных, линейных и разветвленных алифатических полиэфиров с температурой плавления полиэфиров от 35 до 120°С с загустителями, не были известны из патентной и специальной технической литературы. Применение загустителей для приготовления смазок широко используется в промышленности, но такие составы наносят на поверхность трущихся деталей, а не используют в качестве добавок при формовании термопластичных материалов. Из уровня техники не следует очевидным образом, что эффективность процессинговых добавок, приготовленных на основе алифатических полиэфиров, улучшится при использовании загустителей. Из примеров реализации предлагаемого технического решения видно, что добавки могут быть использованы для улучшения формования термопластичного полимерного материала в количестве от 0,02% до 1%, а количество загустителя для улучшения эффективности добавки по сравнению с использованием только полиэфиров без загустителя, необходимо в количестве от 0,01 до 20%.
Использование высокодисперсного минерального порошка с размерами частиц от 1 до 1000 нанометров в качестве пассивного загустителя алифатического полиэфира отличается от использования минерального порошка с размерами частиц свыше 3500 нанометров в качестве компонента комплексной процессинговой добавки, известной из литературы, см. ссылки и обсуждение выше. Использование высокодисперсного (коллоидного) минерального порошка в комбинации с полиэфиром также отличается от известного использования только порошка деламинированной глины или в комбинации этого порошка с фторированным полимером в качестве процессинговой добавки. Использование высокомолекулярного полиэтиленоксида (ПО) в качестве добавки для улучшения формования термопластичного полимера известно из литературы, но использование ПО в качестве пассивного загустителя в составе комплексной процессинговой добавки на основе полиэтиленгликолей не было известно. Использование полиизоцианатов как компонента процессинговой добавки, когда молярное количество изоцианат групп меньше количества гидроксилгрупп в полиэтиленгликоле не известно из технической литературы и отличается от известного применения термопластичных эластомеров и блоксополимеров на основе диизоцианатов в качестве процессинговой добавки. Использование суспензии высокомолекулярных полимеров, которые растворяются в воде, но не растворяются в полиэфире, а разбухают в нем, отличается от известных суспензий фторированного полимера в полиэтиленгликоле для использования в качестве процессинговой добавки, т.к. фторированный полимер не разбухает в полиэтиленгликоле и не растворяется в воде. Применение смесей полиэтиленгликоля с химическими соединениями, содержащими бор и кислород, в качестве комплексной добавки для улучшения формования термопластичного полимерного материала известно, однако, не было показано техническое преимущество применения таких смесей в комбинации с другими загустителями, в частности с силанолом. Применение смесей полиэтиленгликоля с химическими соединениями, содержащими фосфор и кислород, в качестве комплексной добавки для улучшения формования термопластичного полимерного материала не было известно. Из технической литературы известны другие загустители для полиэфиров и для полиэтиленгликолей, например стеараты металлов, но не известно применение составов, содержащих полиэтиленгликоль и стеарат металла, в качестве комплексной процессинговой добавки. Предлагаемое техническое решение также относится к использованию в качестве загустителя полиэфира комбинации нескольких предлагаемых загустителей.
Таким образом, предлагаемое изобретение является новым и отвечает требованию изобретательского уровня. Примеры реализации технического предложения указывают на промышленную применимость.
В рамках заявляемого изобретения возможны очевидные для специалистов модификации заявляемого изобретения. Поэтому должно быть понятно, что все примеры реализации, в частности условия формования, химикаты, температуры и т.п.предназначены для общей иллюстрации предлагаемого изобретения, и не должны быть истолкованы как неоправданное ограничение пределов защиты заявляемого изобретения.
Поскольку использование боратов и борных кислот в качестве загустителя и смесей на основе полиолей и силанолов с боратами в качестве процессинговой добавки известны из прототипа заявляемого изобретения [481, то представляется целесообразным не указывать в Формуле изобретения, но оставить в описании изобретения рекомендации по составам на основе указанных боратов и смесей боратов с другими загустителями. Аналогично представляется целесообразным не указывать в Формуле, но оставить в описании изобретения рекомендации по составам с использованием смесей полиолей с силанолами и боратами, которые соответствуют частному случаю реализации прототипа заявляемого изобретения.
Представляется целесообразным не указывать в Формуле изобретения, но оставить в описании изобретения использование в качестве загустелей растворимых в воде, но не растворимых в полиэфирах высокомолекулярных соединений, так как приготовление смесей с использованием растворителей экономически нецелесообразно. Представляется целесообразным не указывать в Формуле изобретения, но оставить в описании изобретения использование в качестве загустителей солей карбоновых кислот и щелочных металлов, так как введение щелочных металлов в состав полимерного материала может снизить его стойкость к ультрафиолетовой радиации и нагреву, что, как правило, нежелательно.
Представляется целесообразным ограничить выбор минерального порошка в Формуле изобретения высокодисперсными окислами кремния и титана, так как эти минеральные порошки дешевы и доступны, а использование других минеральных порошков, например деламинированной глины, в качестве загустителя представляется экономически не выгодным. Представляется целесообразным не указывать в Формуле изобретения, но оставить в описании изобретения использование в качестве загустителей полиизоцианатов. Полиизоцианаты не рекомендованы для контакта с пищей и телом человека. Хотя при реакции полиизоцианатов с полиолами их токсичность снижается до приемлемого уровня, нельзя исключить, что в процессе формования полимерного материала будут выделяться токсичные газы, что нежелательно.
Специалистам в области полимеров и реологии понятно, что растворимые в полиэфирах полимеры с молекулярным весом от 100000 до 20000000 дальтон могут быть использованы в качестве загустителей полиэфиров и, если полиэтиленоксид с молекулярным весом 5000000 дальтон показывает хорошие результаты, то такое же улучшение будет наблюдаться для всех растворимых в полиэфирах полимеров и любого молекулярного веса добавок из указанного диапазона.
Специалистам в гидромеханике и реологии понятно, что высокодисперсные порошки оксидов кремния и титана с размерами частиц от 1 до 1000 нанометров могут быть использованы в качестве загустителей полимерных жидкостей и, если в примерах реализации показано, что если порошки оксидов кремния и титана с размерами частиц около 10 нанометров показывают хорошие результаты, то и другие высокодисперсные порошки оксидов кремния и титана с размерами частиц из указанного диапазона могут быть использованы для приготовления заявляемых составов полимерного материала.
Специалистам в области химии и полимеров понятно, что если фосфорная кислота, органофосфаты и органофосфиты. использованные в примерах реализацмм заявляемого изобретения, показывают хорошие результаты, то и другие химические соединения, содержащие фосфор и кислород из следующей группы: окислы фосфора в степенях окисления фосфора +3 или +5, кислородные кислоты фосфора в степенях окисления фосфора +3 или +5, сложные эфиры указанных кислот фосфора, кислые соли указанных кислот фосфора, а также смеси указанных химических соединений могут быть использованы для приготовления заявляемых составов полимерного материала.
Должно быть понятно, что все документы, цитируемые в описании изобретения, так же, как и цитаты из какого-либо указанного документа, не могут ограничивать область защиты заявляемого изобретения. В случае несовпадения терминов в настоящем описании и в цитируемых документах именно настоящее описание изобретения устанавливает смысл и определение используемых терминов.
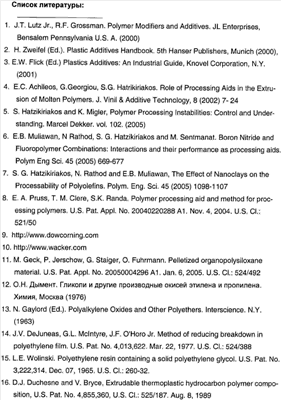 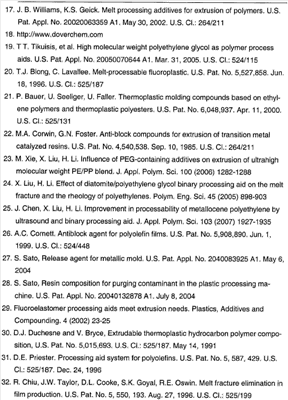 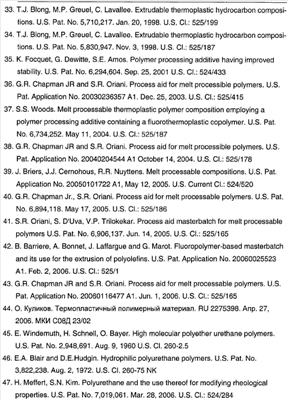 
Формула изобретения
1. Термопластичный полимерный материал, включающий органический термопластичный полимер в качестве основного компонента и комплексную добавку для улучшения формования, при следующем соотношении компонентов, вес.%:
комплексная добавка |
0,02-1 |
термопластичный полимер |
остальное, |
при этом в качестве комплексной добавки используют композицию, содержащую один или несколько полиэфиров, выбранных из группы простых и сложных, линейных и разветвленных алифатических полиэфиров с температурой плавления в диапазоне от 35 до 120°С и с молекулярным весом от 1000 до 10000 Да, и один или несколько загустителей, при следующем соотношении компонентов, вес.%:
загустители |
0,01-20 |
полиэфиры |
остальное, |
причем загустители выбирают из следующей группы: растворимые в полиэфирах полимеры с молекулярным весом от 100000 до 20000000 Да, высокодисперсные порошки оксидов кремния и титана с размерами частиц от 1 до 1000 нм, химические соединения, содержащие фосфор и кислород из следующей группы: окислы фосфора в степенях окисления фосфора +3 или +5, кислородные кислоты фосфора в степенях окисления фосфора +3 или +5, сложные эфиры указанных кислот фосфора, кислые соли указанных кислот фосфора, а также смеси указанных химических соединений.
2. Термопластичный полимерный материал по п.1, отличающийся тем, что в качестве полиэфиров используют полигидроксильные соединения, которые выбирают из группы полиэтиленгликолей с молекулярным весом от 1000 до 10000 Да, или смеси указанных полиэтиленгликолей с многоатомными спиртами, растворимыми в полиэтиленгликолях, или сополимеры многоатомных спиртов и полиэтиленгликолей, где весовое содержание многоатомных спиртов в смеси или в сополимере с полиэтиленгликолями не превышает 20%.
3. Термопластичный полимерный материал по п.1, отличающийся тем, что органический термопластичный полимер выбирают из группы полиолефинов или смеси полиолефинов с узким распределением молекулярного веса.
4. Термопластичный полимерный материал по п.2, отличающийся тем, что органический термопластичный полимер выбирают из группы полиолефинов или смеси полиолефинов с узким распределением молекулярного веса.
5. Термопластичный полимерный материал по п.1, отличающийся тем, что органический термопластичный полимер выбирают из группы полиэтиленов или смеси полиэтиленов с узким распределением молекулярного веса.
6. Термопластичный полимерный материал по п.2, отличающийся тем, что органический термопластичный полимер выбирают из группы полиэтиленов или смеси полиэтиленов с узким распределением молекулярного веса.
7. Термопластичный полимерный материал по пп.1-6, отличающийся тем, что в качестве загустителя или одного из загустителей, содержащих фосфор и кислород, используют органические фосфаты или фосфиты, которые выбирают из сложных эфиров фосфорной или фосфористой кислоты, а также смеси и сополимеры указанных эфиров.
8. Термопластичный полимерный материал по пп.2, 4, 6, отличающийся тем, что в качестве загустителя или одного из загустителей используют полиэтиленоксид с молекулярным весом от 100000 до 20000000 Да.
РИСУНКИ
|
|