(21), (22) Заявка: 2008115355/04, 18.04.2008
(24) Дата начала отсчета срока действия патента:
18.04.2008
(46) Опубликовано: 20.12.2009
(56) Список документов, цитированных в отчете о поиске:
RU 2156233 С1, 20.09.2000. JP 5194281 А, 03.08.1993. US 4695662 А, 22.09.1987.
Адрес для переписки:
626157, Тюменская обл., г. Тобольск, 7а мкрн., 8, кв.19, С.Т.Гулиянцу
|
(72) Автор(ы):
Гулиянц Сурен Татевосович (RU), Мальцева Марина Викторовна (RU), Фаткуллин Марат Галимуллович (RU), Стрепетилов Николай Фотеевич (RU)
(73) Патентообладатель(и):
Гулиянц Сурен Татевосович (RU)
|
(54) СПОСОБ ПОЛУЧЕНИЯ ОЛЕФИНОВЫХ УГЛЕВОДОРОДОВ С4
(57) Реферат:
Изобретение относится к способу получения изобутилена и бутадиена-1,3 каталитическим дегидрированием соответствующих парафиновых углеводородов на алюмохромовом катализаторе при повышенной температуре, разделением полученных продуктов дегидрирования методами абсорбции-десорбции и экстрактивной ректификации с получением товарных изобутилена и бутадиена-1,3 олефиновых углеводородов C4, непревращенных парафинов и горючих отходов производства: «легких» и «тяжелых» неабсорбированных газов и бутадиен-ацетиленового концентрата, причем смесь «тяжелых» неабсорбированных газов с бутадиен-ацетиленовым концентратом и частью «легких» неабсорбированных газов пропускают через бинарный слой катализаторов гидрирования, один из которых никель-хромовый, а другой алюмопалладиевый, и на выходе получают пропановую фракцию. Применение данного способа позволяет увеличить степень утилизации горючих отходов производства с получением товарной пропановой фракции методом каталитического гидрирования и увеличить срок службы катализатора. 1 ил.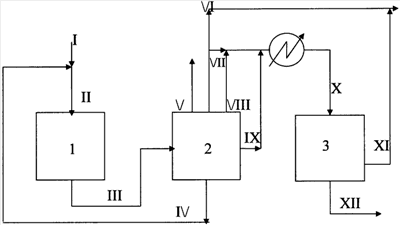
Изобретение относится к нефтехимической промышленности, а именно к процессу получения изобутилена, бутадиена-1,3 и н-бутиленов С4 каталитическим дегидрированием изобутана и н-бутана на алюмохромовых катализаторах, а именно к процессу переработки продуктов дегидрирования – контактного газа.
Изобретение может быть использовано в аналогичных производствах по получению непредельных углеводородов олефинового или диенового ряда.
Известны способы получения изобутилена, бутадиена-1,3 и н-бутиленов С4 дегидрированием соответственно изобутана и н-бутана [1,2,3].
В данных процессах наряду с целевыми продуктами образуются продукты частичного крекинга С4-углеводородов, а именно – углеводороды С1÷С3 (метан, этан, этилен, пропан и пропилен), которые после разделения контактного газа дегидрирования сжигаются в сети топливного газа, не имея квалифицированного применения. Выход углеводородов C1÷С3 достигает 10 мас.%, на товарные продукты и 20 мас.% на исходное сырье. Данные низшие углеводороды выделяются из продуктов дегидрирования под техническим названием «неабсорбированные» газы двумя потоками:
1 – «легкие» неабсорбированные газы (ЛНГ), содержащие в основном водород с массовой долей 30%, а также азот – 45%, метан – 5% и примеси СО и СО2 10%, и –
2 – «тяжелые» неабсорбированные газы (ТНГ), состоящие в основном из пропилена (до 70%) с примесями пропана, этана и этилена. Состав ТНГ: водород – 3%, азот – 7%, метан – 3%, примеси СО и СО2 3%, C2 25%, С3 65% и т.д.
Наиболее близким к заявляемому является «Способ получения олефиновых углеводородов» [4] (прототип). По данному способу получение олефиновых углеводородов осуществляют путем дегидрирования соответствующих парафиновых углеводородов на катализаторе, содержащем Сr2О3, В2О3, оксид калия, нанесенными на оксид алюминия с удельной поверхностью менее 200 м2/г. Дегидрирование осуществляют при 530÷620°C, атмосферном или несколько большем атмосферного давлении, объемной скорости газа 100÷500 час-1 и времени пребывания катализатора в реакционной зоне 5÷25 мин.
Недостатки данного способа те же, что и вышеуказанных аналогов, а именно – образование не имеющих квалифицированного применения горючих отходов и сжигание их в топливной сети.
Задачами данного изобретения являются:
– снижение количества сжигаемых углеводородов в составе горючих отходов;
– получение пропановой фракции из горючих отходов и
– увеличение срока службы катализаторов гидрирования.
Поставленные задачи решаются усовершенствованием технологии переработки продуктов дегидрирования путем вовлечения большого количества горючих отходов в каталитическую переработку с целью получения пропановой фракции. Для этого в реактор гидрирования направляется весь поток ТНГ и необходимая часть ЛНГ, а в качестве катализатора используется бинарный катализатор, состоящий из двух равных по объему слоев:
– первый каталитический слой по ходу сырья – никель-хромовый катализатор метанирования для превращения оксидов углерода в метан [5]:
– второй слой – собственно гидрирующий катализатор PdS на Аl2О3 [5], для превращения пропилена, содержащегося в ТНГ вы пропан, а непредельных С4 в н-бутан.
Режим гидрирования: температура, расход водорода в составе ЛНГ, подобран таким, чтобы облегчить полное превращение оксидов углерода, отравляющих палладиевый катализатор гидрирования, в метан, а таже – полное превращение пропилена в пропан, а непредельных С4 в бутан.
Реактор гидрирования представляет собой вертикальный цилиндрический аппарат емкостью 10 м3. Загрузка катализаторов – по 5 м3. Температура гидрирования – 150÷200°С при давлении 1,6 МПа. Обьемная скорость подачи сырья – 600 час-1. После олаждения и конденсации жидкая фаза – пропановая фракция направляется на склад, а газовая фаза -в топливную сеть.
Количество полученной пропановой фракции на установке производительностью 180000 тонн бутадиена в год составит – 20000 тонн в год.
Практическое осуществление заявляемого способа описано в нижепредставленном примере.
Пример. Получение бутадиена-1,3 дегидрированием н-бутана и переработку продуктов дегидрирования производят по схеме, представленной на чертеже, аналогично способу, описанному в примере 1.
Сырье – свежий н-бутан – поток I – в количестве 40 т/ч смешивают с рецикловой бутан-бутиленовой фракцией (ББФ) – поток IV – 140 т/ч и подают на узел дегидрирования 1. Дегидрирование производят на стационарном Al-Cr-ом таблетированном катализаторе при Т=580°С под остаточным давлением – 0,016 атм., объемная скорость – 230 час-1. Продукты дегидрирования – контактный газ – поток III – 180 т/ч подают на узел 2, где производят его закалку, охлаждение, разделение методом абсорбции-десорбции и выделение товарного бутадиена-1,3 методом экстрактивной ректификации. После узла 2 выделяют потоки: VI – товарный бутадиен-1,3 – 25 т/ч; поток V – ЛНГ – 12 т/ч; поток IV – возвратная ББФ – 140 т/ч; поток VIII – ТНГ – 2,8 т/ч и поток IX – 0,2 т/ч – горючий отход – бутадиен-ацетиленовый концентрат. Поток IV возвращают на узел дегидрирования 2, поток VI – откачивают на склад, а поток VIII смешивают с потоком IX и потоком VII – 0,5 т/ч – (часть потока ЛНГ) и полученную смесь – поток X – 3,5 т/ч подают на узел 3 для утилизации.
Утилизация смеси горючих отходов производится методом гидрирования, аналогично описанному в примере 1. После узла 3 гидрогенизат охлаждают, конденсируют и получают жидкую и газовую фазы. Жидкую фазу – поток XII – пропановую фракцию – 3,2 т/ч, направляют на склад или на смешение с товарным пропаном, а газовую фазу – поток XI – 0,3 т/ч, содержащую метан, этан, непревращенный водород и азот, возвращают в поток V – ЛНГ на сжигание в топливной сети.
Состав полученной пропановой фракции следующий: в массовых долях
C1÷C2 – 1,48;
C3 – 98,2%
C4 – 0,32%
Что соответствует требованиям и качеству стандартной пропановой фракции марки А по ТУ-0272-023-00151638-99.
Количество использованных (утилизированных) горючих отходов (степень утилизации) составляет:

При этом полностью утилизируются потоки VIII – ТНГ и IX – БАК с получением 3,2 т/ч товарного пропана.
Подписи к чертежу:
1 – узел дегидрирования н-бутана;
2 – узел разделения контактного газа;
3 – узел утилизации горючих отходов.
Потоки: I – сырье свежий н-бутан;
II – смешанное сырье;
III – контактный газ дегидрирования;
IV – рецикл ББФ;
V – бутадиен-1,3;
VI – ЛНГ;
VII – часть ЛНГ на утилизацию;
VIII – ТНГ;
IX – БАК;
X – смесь газов на утилизацию;
XI – возвратный газ;
XII – товарный пропан.
Список использованной литературы
1. Кирпичников П.А., Лиакумович А.Г., Победимский Д.Г. «Химия и технология мономеров для синтетических каучуков». Л.: Химия. 1981. С.155.
2. Адельсон С.В., Вишнякова Т.П., Паушкин Я.М. «Технология нефтехимического синтеза». М.: Химия. 1985. с.109-110.
3. «Справочник нефтехимика» под ред. С.К.Огородникова. т.2, Л.: Химия. 1978. С.350-357.
4. Патент РФ 2156233, от 04.08.1999 г., опубл. Бюл. 26 20.09.2000 г.
5. «Справочник нефтехимика» под ред. С.К.Огородникова. т.1. Л.: Химия. 1978 г. с.404, 412, 413.
Формула изобретения
Способ получения изобутилена и бутадиена-1,3 каталитическим дегидрированием соответствующих парафиновых углеводородов на алюмохромовом катализаторе при повышенной температуре, разделением полученных продуктов дегидрирования методами абсорбции-десорбции и экстрактивной ректификации с получением товарных изобутилена и бутадиена-1,3 олефиновых углеводородов С4, непревращенных парафинов и горючих отходов производства: «легких» и «тяжелых» неабсорбированных газов и бутадиен-ацетиленового концентрата, причем смесь «тяжелых» неабсорбированных газов с бутадиен-ацетиленовым концентратом и частью «легких» неабсорбированных газов пропускают через бинарный слой катализаторов гидрирования, один из которых никель-хромовый, а другой – алюмо-палладиевый и на выходе получают пропановую фракцию.
РИСУНКИ
|