|
(21), (22) Заявка: 2008129997/02, 21.07.2008
(24) Дата начала отсчета срока действия патента:
21.07.2008
(46) Опубликовано: 20.11.2009
(56) Список документов, цитированных в отчете о поиске:
SU 1541913 A1, 20.06.1997. RU 1732572 A1, 20.06.1997. SU 1210330 A1, 11.07.1984. DE 4114669 A, 12.11.1992.
Адрес для переписки:
400131, г.Волгоград, пр. Ленина, 28, ВолГТУ, отдел интеллектуальной собственности
|
(72) Автор(ы):
Писарев Сергей Петрович (RU), Трыков Юрий Павлович (RU), Гуревич Леонид Моисеевич (RU), Шморгун Виктор Георгиевич (RU), Донцов Дмитрий Юрьевич (RU), Самарский Дмитрий Сергеевич (RU), Казак Вячеслав Федорович (RU)
(73) Патентообладатель(и):
Государственное образовательное учреждение высшего профессионального образования Волгоградский государственный технический университет (ВолгГТУ) (RU)
|
(54) СПОСОБ ПОЛУЧЕНИЯ ИЗДЕЛИЙ С ВНУТРЕННИМИ ПОЛОСТЯМИ ПУТЕМ ВЗРЫВНОГО НАГРУЖЕНИЯ
(57) Реферат:
Изобретение может быть использовано для изготовления изделий цилиндрической формы с внутренними полостями, например теплообменников, деталей электротермического и химического оборудования, теплорегуляторов и т.п. В полости центрального полостеобразующего элемента размещают симметрично его продольной оси удаляемый металлический стержень заданного диаметра. Зазор заполняют удаляемым водным наполнителем. Располагают на поверхности центрального полостеобразующего элемента вплотную друг к другу заполненные водным наполнителем наружные полостеобразующие элементы в виде труб со слоем из легкоплавкого материала на их наружных поверхностях. Размещают полученный пучок в трубчатой металлической оболочке, удаляемой после взрывного воздействия. На ее поверхности располагают кольцевой заряд взрывчатого вещества (ВВ) и производят инициирование процесса детонации. После взрывного нагружения проводят термообработку полученной заготовки с учетом температуры плавления слоев из легкоплавкого материала. В результате получают цельносварное композиционное изделие цилиндрической формы с повышенной объемной долей внутренних полостей, с пониженным расходом металла в расчете на одно изделие, с обеспечением при этом высокой эффективности теплообмена веществ, находящихся во внутренних каналах изделия, с окружающей средой. 5 з.п. ф-лы, 3 ил., 1 табл.
Изобретение относится к технологии получения изделий цилиндрической формы с помощью энергии взрыва и может быть использовано для изготовления изделий с внутренними полостями, например теплообменников, деталей электротермического и химического оборудования, теплорегуляторов и т.п.
Известен способ получения сверхпроводящих изделий с внутренней полостью с помощью энергии взрыва, при котором устанавливают соосно трубчатый полостеобразующий элемент с удаляемым наполнителем и трубчатую облицовку, в зазор между ними засыпают порошок сверхпроводящего материала и инициируют наружный заряд взрывчатого вещества, при этом для исключения повреждения поверхности трубчатой облицовки и повышения качества слоя из сверхпроводящего материала между зарядом взрывчатого вещества и трубчатой облицовкой соосно размещают защитную трубчатую прослойку, между ней и трубчатой облицовкой в зазор засыпают тонкодисперсный керамический порошок, берут взрывчатое вещество со скоростью детонации 1580-3800 м/с, а процесс ведут при отношении удельной массы взрывчатого вещества к сумме удельных масс защитной трубчатой прослойки, тонкодисперсного керамического порошка, трубчатой облицовки и порошка сверхпроводящего материала, равном 0,51-0,81 (патент РФ 1827089, М. кл. В23К 20/08, опубл. 20.02.96 в БИ 5-96).
Недостатком этого способа является использование в его схеме сварки взрывом лишь одного полостеобразующего элемента, что позволяет получать изделия цилиндрической формы лишь с одной внутренней полостью. Наличие прослойки из спрессованного керамического сверхпроводящего материала между наружной поверхностью медного полостеобразующего элемента и внутренней поверхностью трубчатой облицовки создает значительное термическое сопротивление (отношение толщины слоя к коэффициенту его теплопроводности) при теплообмене вещества, находящегося во внутреннем канале изделия, с окружающей средой, а это весьма ограничивает применение изделий, полученных данным способом в теплообменной аппаратуре.
Известен способ получения сверхпроводящих изделий с внутренней полостью сваркой взрывом, при котором устанавливают соосно трубчатый полостеобразующий элемент с удаляемым водным наполнителем и наружную оболочку, в зазор между ними засыпают порошок сверхпроводящего материала и инициируют заряд взрывчатого вещества. Между наружной поверхностью полостеобразующего элемента и слоем порошка сверхпроводящего материала помещают металлическую трубчатую упрочняющую прослойку из высокоэлектропроводного материала с внутренним диаметром, на 2-4 мм большим наружного диаметра полостеобразующего элемента, при этом берут взрывчатое вещество (ВВ) со скоростью детонации 2400-3520 м/с, а процесс ведут при отношении удельной массы ВВ к сумме удельных масс наружной оболочки, порошка сверхпроводящего материала и упрочняющей прослойки, равном 1,0-1,2 (патент РФ 1732572, опубл. 20.06.97, БИ 17/97, М.кл. В23К 20/08).
К недостаткам данного способа можно отнести возможность размещения в его схеме сварки взрывом лишь одного полостеобразующего элемента, что позволяет получать по этому способу лишь одноканальные изделия цилиндрической формы с наружной стальной оболочкой. Кроме того, наличие керамического слоя между наружной оболочкой и трубчатой упрочняющей прослойкой затрудняет теплообмен между наружным и внутренним слоем композиционного изделия, а это весьма ограничивает возможности использования данного способа при создании деталей химического, электротермического оборудования и т.п., где требуются материалы с развитой наружной поверхностью и пониженным термическим сопротивлением.
Наиболее близким по техническому уровню и достигаемому результату является способ получения изделий с внутренними полостями сваркой взрывом, при котором устанавливают наружную металлическую облицовку в виде стальной трубчатой оболочки с зазором относительно плакируемой заготовки в виде пучка труб, например, из меди с водным наполнителем в их внутренних полостях. Между трубами помещают соединительные стержни из более легкоплавкого металла, чем медь, а сварку взрывом осуществляют с помощью заряда взрывчатого вещества, расположенного на поверхности плакирующей заготовки. После взрывного воздействия с целью увеличения площади сварных соединений проводят термообработку изделия при температуре на 5-20°С выше температуры ликвидуса металла соединительных стержней (Авторское свидетельство СССР 1541913, М. кл. В23К 20/08, опубл. в БИ 17-97 – прототип).
Недостатком этого способа является наличие в его схеме сварки взрывом наружной стальной оболочки, которая остается в сваренном изделии и при его эксплуатации весьма затрудняет теплообмен теплоносителей, прокачиваемых через внутренние каналы изделия, с окружающей средой. Из-за отсутствия сплошных сварных соединений между стенками полостеобразующих элементов создаются дополнительные препятствия для передачи тепла между теплоносителями, находящимися в смежных каналах изделия. При эксплуатации изделия в условиях циклических нагрузок (вибрации) возможно разрушение локальных очагов сварки. Кроме того, объемная доля полостей в таких изделиях невелика, а это ограничивает возможные области применения изделий, полученных данным способом, в теплообменной аппаратуре.
В связи с этим важнейшей задачей является создание нового способа получения изделий с внутренними полостями путем взрывного нагружения по новой технологической схеме взрывного воздействия на свариваемую заготовку с последующей ее термообработкой, обеспечивающей получение за один технологический цикл облегченных цельносварных изделий с повышенной объемной долей внутренних полостей с сохранением при этом их осевой симметрии, высокой герметичности металла полостеобразующих элементов, с повышением эффективности теплообмена веществ, находящихся во внутренних полостях с окружающей средой.
Техническим результатом заявленного способа является создание новой технологической схемы, обеспечивающей за один акт взрывного нагружения и последующей термической обработки, приводящей к расплавлению латунных слоев, получение качественных сплошных сварных соединений между всеми полостеобразующими элементами с исключением при этом нарушений герметичности полостеобразующих элементов, увеличение объемной доли внутренних полостей и благодаря этому снижение металлоемкости изделий, обеспечение их осевой симметрии, повышение эффективности теплообмена веществ, находящихся во внутренних каналах изделия с окружающей средой.
Указанный технический результат достигается тем, что в предлагаемом способе получения изделий с внутренними полостями путем взрывного нагружения, при котором берут полостеобразующие элементы в виде труб с удаляемым наполнителем и располагают их пучком в трубчатой оболочке симметрично относительно ее продольной оси, на наружной поверхности трубчатой оболочки располагают кольцевой заряд ВВ и производят инициирование процесса детонации ВВ с помощью электродетонатора, в полости центрального полостеобразующего элемента размещают симметрично его продольной оси удаляемый металлический стержень с диаметром, составляющим 0,83-0,9 внутреннего диаметра центрального полостеобразующего элемента, зазор между стержнем и полостеобразующим элементом заполняют удаляемым водным наполнителем, располагают на наружной поверхности центрального полостеобразующего элемента вплотную друг к другу наружные полостеобразующие элементы в виде труб с толщиной стенок 0,8-1,5 мм, со слоем из легкоплавкого материала на их наружных поверхностях толщиной 10-30 мкм, размещают полученный пучок в трубчатой металлической оболочке, удаляемой после взрывного воздействия, процесс взрывного нагружения ведут при скорости детонации ВВ 3400-4060 м/с и отношении удельной массы ВВ к удельной массе стенки трубчатой оболочки, равном 0,72-0,86, после взрывного нагружения проводят термообработку полученной заготовки в течение 5-7 минут при температуре, превышающей на 5-15°С температуру плавления слоев из легкоплавкого материала на наружных полостеобразующих элементах с образованием при этом цельносварных соединений между всеми полостеобразующими элементами. При осуществлении способа в качестве материала металлического стержня используют сталь, в качестве материала центрального полостеобразующего элемента используют сталь, в качестве слоев из легкоплавкого материала на поверхностях наружных полостеобразующих элементов используют латунь, в качестве материала для изготовления наружных полостеобразующих элементов используют медь, а слои из легкоплавкого материала наносят на поверхности наружных полостеобразующих элементов плазменным напылением.
Новый способ получения изделий с внутренними полостями имеет существенные отличия по сравнению с прототипом как по построению схемы взрывного прессования заготовки, совокупности технологических приемов и режимов при осуществлении способа, так и по физическим механизмам формирования сплошных сварных соединений между всеми полостеобразующими элементами. Так, предложено в полости центрального полостеобразующего элемента размещать симметрично его продольной оси удаляемый металлический стержень с диаметром, составляющим 0,83-0,9 внутреннего диаметра центрального полостеобразующего элемента, в качестве материала металлического стержня использовать сталь, а зазор между стержнем и полостеобразующим элементом заполнять удаляемым водным наполнителем. Металлический стержень совместно с водным наполнителем обеспечивают сохранность центрального полостеобразующего элемента от неконтролируемых радиальных деформаций при взрывном нагружении. Сталь и вода, как наполнитель, выбраны в качестве материалов как наиболее дешевые материалы. При диаметре металлического стержня, составляющем менее 0,83 внутреннего диаметра центрального полостеобразующего элемента, не обеспечивается полная сохранность центрального полостеобразующего элемента от поперечных деформаций. При диаметре металлического стержня более 0,9 внутреннего диаметра центрального полостеобразующего элемента затруднено заполнение водным наполнителем зазора между стержнем и полостеобразующим элементом.
В качестве материала центрального полостеобразующего элемента предложено использовать сталь, которая обеспечивает повышенную прочность полученных изделий при растягивающих и изгибающих напряжениях, позволяет размещать в его внутренней полости химически активные вещества.
Предложено располагать на наружной поверхности центрального полостеобразующего элемента вплотную друг к другу наружные полостеобразующие элементы в виде труб с толщиной стенок 0,8-1,5 мм со слоем из легкоплавкого материала на их наружных поверхностях толщиной 10-30 мкм, при этом в качестве материала для изготовления наружных полостеобразующих элементов предложено использовать медь, а в качестве слоев из легкоплавкого материала на поверхностях наружных полостеобразующих элементов использовать латунь, причем наносить эти слои на медные предложено методом плазменного напыления. Метод плазменного напыления обеспечивает высокую производительность, необходимую прочность сцепления слоев и равномерность толщины латунных слоев по всей длине полостеобразующих элементов. При толщине стенок полостеобразующих элементов менее 0,8 мм возможна потеря герметичности металла в процессе взрывного воздействия.
Толщина этих стенок более 1,5 мм оказывается избыточной, поскольку качество изделий при этом не улучшается, но неоправданно возрастает их металлоемкость. Толщина латунных слоев 10-30 мкм является достаточной для получения сплошных сварных соединений между всеми полостеобразующими элементами при термообработке изделия после взрывного нагружения. При толщине слоев менее 10 мкм возможно появление участков в стыках полостеобразующих элементов, где отсутствует сварка, а это ухудшает прочностные и служебные свойства изделий. Толщина латунных слоев более 30 мкм является избыточной, поскольку качество изделий при этом не возрастает, но неоправданно увеличивается термическое сопротивление латунных прослоек и энергозатраты на их получение. Латунь обладает высокой прочностью, превышающей прочность медных полостеобразующих элементов, что способствует образованию высокопрочных соединений между всеми полостеобразующими элементами. Медь в качестве материала наружных полостеобразующих элементов обладает высокой теплопроводностью, достаточно высокой пластичностью и прочностью. Полостеобразующие элементы из меди с водным наполнителем в их полостях не разрушаются в процессе высокоскоростного взрывного нагружения, не нарушается их герметичность. Кроме того, латунь в процессе термической обработки хорошо смачивает медь и сталь, что способствует образованию высокопрочных соединений между всеми полостеобразующими элементами, улучшению теплофизических свойств получаемых изделий.
Предложено размещать полученный пучок в трубчатой металлической оболочке, удаляемой после взрывного воздействия, а процесс взрывного нагружения вести при скорости детонации ВВ 3400-4060 м/с и отношении удельной массы ВВ к удельной массе стенки трубчатой оболочки, равном 0,72-0,86, благодаря чему происходит радиальная деформация трубчатой оболочки, выполняющей функции сплошной среды, передающей давление от продуктов взрыва, наружные полостеобразующие элементы со слоями из легкоплавкого материала – латуни на их нагруженных поверхностях деформируются, приобретая при этом в поперечных сечениях форму криволинейных четырехугольников, промежутки между ними исчезают, происходит термодинамическая активация поверхностей контакта, что способствует при последующей термообработке образованию прочных сплошных неразъемных соединений.
При скорости детонации ВВ и отношении удельной массы ВВ к удельной массе стенки трубчатой оболочки ниже нижнего предела энергии продуктов детонации ВВ недостаточно для ликвидации промежутков между полостеобразующими элементами и при последующей термообработке не образуется сплошных сварных соединений между всеми составляющими получаемого композиционного материала. Скорость детонации ВВ и величина указанного отношения удельных масс выше верхнего предела являются избыточными, поскольку при этом возможно нарушение герметичности полостеобразующих элементов, затрудняется процесс удаления с поверхности изделия сдеформированной трубчатой оболочки из-за возможности образования нежелательных сварных соединений между латунными слоями полостеобразующих элементов и внутренней поверхностью оболочки.
Предложено после взрывного нагружения проводить термообработку полученной заготовки в течение 5-7 минут при температуре, превышающей на 5-15°С температуру плавления слоев из легкоплавкого материала на наружных полостеобразующих элементах. При такой термической обработке происходит оплавление легкоплавких слоев с образованием цельносварных соединений между всеми полостеобразующими элементами. Время выдержки и температурные режимы ниже нижнего предлагаемого предела недостаточны для протекания в достаточном объеме диффузионных процессов и образования надежных сплошных соединений между всеми полостеобразующими элементами.
Температурно-временные режимы выше верхнего предлагаемого предела являются избыточными, не улучшают качество сварных соединений, но при этом неоправданно возрастают энергозатраты на получение изделий.
На фиг.1 изображена схема взрывного нагружения, ее продольный осевой разрез, на фиг.2 – поперечное сечение А-А схемы взрывного нагружения, на фиг.3 – поперечное сечение сваренного изделия с внутренними полостями, где позиция 18 – сдеформированные наружные полостеобразующие элементы; 19 – сдеформированные слои из легкоплавкого материала; 20, 21 – зоны сварки слоев из легкоплавкого материала между собой и с центральным полостеобразующим элементом, соответственно; 22, 23 – внутренние полости изделия.
Предлагаемый способ получения изделий с внутренними полостями путем взрывного нагружения осуществляется в следующей последовательности. Изготавливают центральный полостеобразующий элемент в виде трубы 1 и размещают в его полости симметрично продольной оси металлический стержень 2 с диаметром, составляющим 0,83-0,9 внутреннего диаметра центрального полостеобразующего элемента. Зазор между стержнем и полостеобразующим элементом заполняют удаляемым водным наполнителем 3, а герметизацию и центровку осуществляют с помощью втулок 4, 5, например, из резины. Берут наружные полостеобразующие элементы в виде труб 6 с толщиной стенок 0,8-1,5 мм и наносят на их наружные поверхности, например, плазменным напылением слои из легкоплавкого материала 7 толщиной 10-30 мкм. Заполняют полости водным наполнителем 8 и герметизируют по концам заглушками 9, 10, например, из резины. Полученные сборки располагают вплотную друг к другу на наружной поверхности центрального полостеобразующего элемента. Полученный пучок размещают внутри трубчатой оболочки 11 симметрично относительно ее продольной оси, предварительно на ее внутренней поверхности создают противосварочное покрытие 12, например оксидируют, а затем натирают поверхность графитом. Устанавливают направляющий конус 13, например, из стали. На наружной поверхности трубчатой оболочки располагают контейнер 14 с кольцевым зарядом ВВ 15. Для осуществления процесса используют заряд ВВ со скоростью детонации 3400-4060 м/с, при этом отношение его удельной массы к удельной массе стенки трубчатой оболочки обеспечивают равным 0,72-0,86. Размещают полученную сборку на песчаном грунте 16 и производят инициирование процесса детонации в заряде ВВ с помощью электродетонатора 17. При взрывном нагружении происходит высокоскоростная радиальная деформация трубчатой оболочки, наружные полостеобразующие элементы со слоями из легкоплавкого материала – латуни на их наружных поверхностях деформируются, приобретают при этом в поперечных сечениях форму криволинейных четырехугольников, ликвидируются воздушные промежутки между всеми полостеобразующими элементами, при этом происходит термодинамическая активация поверхностей контакта всех металлических слоев. Извлекают из полости центрального полостеобразующего элемента металлический стержень, водный наполнитель удаляется из всех полостей после взрывного нагружения самопроизвольно при разгрузке сжатой системы. После этого на торцевые части полученной заготовки наносят обмазку, например, на основе борной кислоты для защиты металлов от окисления и проводят ее термообработку в течение 5-7 минут при температуре, превышающей на 10-15°С температуру плавления слоев из легкоплавкого материала на наружных полостеобразующих элементах с образованием при этом цельносварных соединений между всеми полостеобразующими элементами. После этого удаляют механической обработкой сдеформированную трубчатую оболочку и металл с краевыми эффектами.
В результате получают цельносварное изделие с внутренними полостями цилиндрической формы без нарушений осевой симметрии и герметичности металлических слоев с пониженным термическим сопротивлением металлических слоев, с повышенной в сравнении с прототипом объемной долей внутренних полостей и пониженным благодаря этому расходом металла в расчете на одно изделие.
Пример 1 (см. также таблицу)
Центральный полостеобразующий элемент изготавливают из коррозионностойкой стали 12Х18Н10Т (ГОСТ 5632-72) с наружным зазором 34,4 мм, внутренним Dвн=30 мм, длиной 280 мм. В его полости симметрично продольной оси размещают металлический стержень из стали Ст3 длиной 285 мм, диаметром 27 мм, что составляет 0,9 Dвн. Температура плавления стали 12Х18Н10Т – 1397°С. Зазор между стержнем и полостеобразующим элементом заполняют водным наполнителем, а герметизацию и взаимную центровку указанных деталей осуществляли с помощью резиновых втулок. Наружные полостеобразующие элементы в виде труб в количестве 12 штук изготавливали из меди Ml (ГОСТ 859-78) длиной 280 мм с наружным диаметром 12 мм, внутренним – 10,4 мм, с толщиной стенок Тст=0,8 мм. Температура плавления меди – 1083°С. На наружные поверхности наружных полостеобразующих элементов наносят плазменным напылением слои из легкоплавкого материала – латуни Л63 (ГОСТ 15527-70) толщиной Тсл=10-12 мкм. Температура плавления латуни Л63 tпл=905°C, что значительно ниже, чем у остальных металлических слоев из стали и меди. Заполняют полости наружных полостеобразующих элементов водным наполнителем и герметизируют по концам заглушками из резины. Полученные сборки располагают вплотную друг к другу на наружной поверхности центрального полостеобразующего элемента. Полученный пучок размещают внутри трубчатой оболочки из стали Ст3 симметрично относительно ее продольной оси. Наружный диаметр оболочки – 66 мм, внутренний – 58,5 мм, толщина стенки Тоб=0,375 см, плотность стали Пст=7,8 г/см3. Удельная масса стенки трубчатой оболочки Моб=Тоб·Пст=0,375·7,8=2,925 г/см2. Внутреннюю поверхность трубчатой оболочки предварительно оксидировали в окислительной среде, а затем натирали поверхность графитом, создавая при этом противосварочное покрытие. Устанавливают направляющий конус из стали Ст3 с углом при вершине 90°, на наружной поверхности трубчатой оболочки располагают контейнер с кольцевым зарядом ВВ, в качестве которого использовали аммонит 6ЖВ. Наружный диаметр заряда 126 мм, внутренний – 66 мм, толщина заряда Твв=3 см, его плотность
Пвв=0,7 г/см3, удельная масса Мвв=Твв·Пвв=3·0,7=2,1 г/см2. При выбранных параметрах заряда скорость детонации ВВ Dвв=3400 м/с. Отношение удельной массы заряда ВВ к удельной массе стенки трубчатой оболочки равно: Мвв:Моб=2,1:2,92=0,72.
Размещают полученную сборку на песчаном грунте и производят взрывное нагружение инициированием процесса детонации в заряде ВВ с помощью электродетонатора. После взрывного воздействия извлекают из полости центрального полостеобразующего элемента металлический стержень, наносят на торцевые части полученной заготовки обмазку на основе борной кислоты для защиты металлических слоев от окисления и проводят термообработку заготовки в электропечи в течение 7 минут при температуре tн=910°C, что на 5°С превышает температуру плавления tпл слоев из легкоплавкого материала – латуни на наружных поверхностях полостеобразующих элементов. После термической обработки механической обработкой удаляют сдеформированную трубчатую оболочку и металл с краевыми дефектами в торцевых частях изделия.
В результате получили цельносварное изделие с внутренними полостями без нарушения герметичности металлических слоев и осевой симметрии. Объемная доля внутренних полостей составляет 75,4%, что в 6,3 раза больше, чем по прототипу, а объемная доля металла, израсходованного на изготовление изделия, снизилась в 3,6 раза. Термическое сопротивление слоев металла при теплообмене веществ, находящихся во внутренних каналах изделия с окружающей средой снизилось в сравнении с прототипом в 77 раз.
Пример 2 (см. также таблицу)
То же, что в примере 1, но внесены следующие изменения. Наружный диаметр центрального полостеобразующего элемента – 34,45 мм, диаметр металлического стержня 26 мм, что составляет 0,87 Dвн. Наружные полостеобразующие элементы в виде труб имели внутренний диаметр 10,4 мм, толщину стенок – Тст=1,2 мм, толщина слоев из легкоплавкого материала – латуни Тсл=14-16 мкм. Наружный диаметр трубчатой металлической оболочки был 68 мм, внутренний – 58,5 мм, толщина ее стенки Тоб=0,475 см, удельная масса Моб=Тоб·Пст=0,475-7,8=3,7 г/см2. Наружный диаметр заряда ВВ был 148 мм, внутренний – 68 мм, толщина заряда Твв=4 см, его плотность Пвв=0,7 г/см3, удельная масса Мвв=4·0,7=2,8 г/см2. При указанных параметрах заряда скорость детонации ВВ Dвв=4800 м/с. Отношение удельной массы заряда ВВ к удельной массе трубчатой оболочки равно: Мвв:Моб=2,8:3,7=0,76.
Термообработку заготовки после взрывного нагружения проводили в течение 6 минут при температуре 915°С, что на 10°С превышает температуру плавления tпл слоя из легкоплавкого материала – латуни.
Результаты получения изделия с внутренними полостями те же, что в примере 1, но объемная доля внутренних полостей составляет 68,8%, что в 5,7 раз больше, чем у изделий, полученных по прототипу, а объемная доля металла, израсходованного на изготовление изделия, снизилась в 2,8 раза. Термическое сопротивление слоев металла при теплообмене веществ, находящихся во внутренних полостях изделия, с окружающей средой снизилось в сравнении с прототипом в 70 раз.
Пример 3 (см. также таблицу)
То же, что в примере 1, но внесены следующие изменения. Наружный диаметр центрального полостеобразующего элемента – 34,54 мм, диаметр металлического стержня 25 мм, что составляет 0,83 Dвн. Наружные полостеобразующие элементы в виде труб имели внутренний диаметр 9 мм, толщину стенок – Тст=1,5 мм, толщина слоев из легкоплавкого материала – латуни Тсл=28-30 мкм. Наружный диаметр трубчатой металлической оболочки был 70 мм, внутренний – 58,6 мм, толщина ее стенки Тоб=0,57 см, удельная масса Моб=Тоб·Пст=0,57·7,8=4,45 г/см2. Наружный диаметр заряда ВВ был 180 мм, внутренний – 70 мм, толщина заряда Твв=5,5 см, плотность Пвв=0,7 г/см3, удельная масса Мвв=5,5·0,7=3,85 г/см2. При указанных параметрах заряда скорость детонации Dвв=4060 м/с. Отношение удельной массы заряда ВВ к удельной массе трубчатой металлической оболочки равно: Мвв:Моб=3,85:4,45=0,86.
Термообработку заготовки после взрывного нагружения проводили в течение 5 минут при температуре 920°С, что на 15°С превышает температуру плавления tпл слоя из легкоплавкого материала – латуни.
Результаты получения изделия с внутренними полостями те же, что в примере 1, но объемная доля внутренних полостей составляет 64,2%, что в 5,3 раз больше, чем у изделий, полученных по прототипу, а объемная доля металла, затраченного на изготовление изделия, снизилась в 2,4 раза. Термическое сопротивление слоев металла при теплообмене веществ, находящихся во внутренних полостях изделия, с окружающей средой снизилось в сравнении с прототипом в 55 раз.
При получении изделий с внутренними полостями по прототипу (см. таблицу, пример 4) не образуется сплошных сварных соединений между всеми полостеобразующими элементами, что затрудняет теплообмен между веществами, находящимися в смежных каналах. Стальная оболочка остается в сваренном изделии, а это весьма затрудняет теплообмен веществ-теплоносителей, находящихся во внутренних каналах изделия с окружающей средой. Термическое сопротивление металла, отделяющего вещества во внутренних каналах от окружающей среды, в 55-77 раз больше, чем в изделиях, полученных по предлагаемому способу, объемная доля полостей составляет всего лишь 12%, что в 5,3-6,3 раза меньше, чем по прототипу, объемная доля металла, затраченного на изготовление каждого изделия, в 2,4-3,6 раза больше, чем по предлагаемому способу.
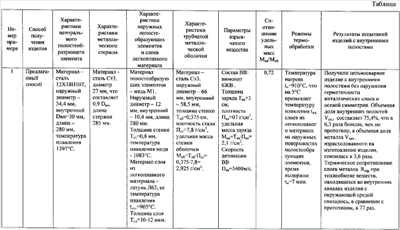
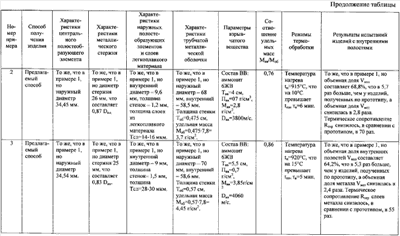
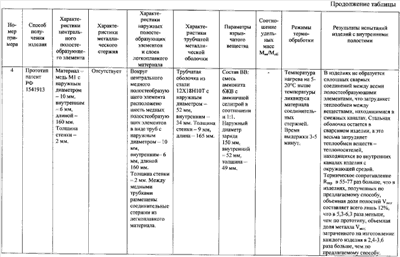
Формула изобретения
1. Способ получения изделия с внутренними полостями путем взрывного нагружения, при котором берут полостеобразующие элементы в виде труб с удаляемым наполнителем и располагают их пучком в трубчатой оболочке симметрично относительно ее продольной оси, на наружной поверхности трубчатой оболочки располагают кольцевой заряд взрывчатого вещества (ВВ) и производят инициирование процесса детонации ВВ с помощью электродетонатора, отличающийся тем, что в полости центрального полостеобразующего элемента размещают симметрично его продольной оси удаляемый металлический стержень с диаметром, составляющим 0,83-0,9 внутреннего диаметра центрального полостеобразующего элемента, а зазор между стержнем и полостеобразующим элементом заполняют удаляемым водным наполнителем, при этом располагают на наружной поверхности центрального полостеобразующего элемента вплотную друг к другу наружные полостеобразующие элементы в виде труб с толщиной стенок 0,8-1,5 мм, со слоем из легкоплавкого материала на их наружных поверхностях толщиной 10-30 мкм, размещают полученный пучок в трубчатой металлической оболочке, удаляемой после взрывного воздействия, а процесс взрывного нагружения ведут при скорости детонации ВВ 3400-4060 м/с и отношении удельной массы ВВ к удельной массе стенки трубчатой оболочки, равном 0,72-0,86, причем после взрывного нагружения проводят термообработку полученной заготовки изделия в течение 5-7 мин при температуре, превышающей на 5-15°С температуру плавления слоев из легкоплавкого материала на наружных полостеобразующих элементах с образованием при этом цельносварных соединений между всеми полостеобразующими элементами.
2. Способ по п.1, отличающийся тем, что в качестве материала металлического стержня используют сталь.
3. Способ по п.1, отличающийся тем, что в качестве материала центрального полостеобразующего элемента используют сталь.
4. Способ по п.1, отличающийся тем, что в качестве слоев из легкоплавкого материала на поверхностях наружных полостеобразующих элементов используют латунь.
5. Способ по п.1, отличающийся тем, что в качестве материала для изготовления наружных полостеобразующих элементов используют медь.
6. Способ по п.1, отличающийся тем, что слои из легкоплавкого материала нанесены на поверхности наружных полостеобразующих элементов плазменным напылением.
РИСУНКИ
|
|