(21), (22) Заявка: 2007125489/28, 05.07.2007
(24) Дата начала отсчета срока действия патента:
05.07.2007
(43) Дата публикации заявки: 10.01.2009
(46) Опубликовано: 27.09.2009
(56) Список документов, цитированных в отчете о поиске:
RU 2251072 С2, 27.04.2005. RU 2057319 С1, 27.03.1996. SU 259562 А, 12.12.1969. RU 2175411 С2, 27.10.2001.
Адрес для переписки:
630090, г.Новосибирск, ул.Терешковой, 18-11, П.Е.Котляру
|
(72) Автор(ы):
Зверев Юрий Васильевич (RU), Котляр Петр Ефимович (RU), Мишнев Виктор Иванович (RU), Назаренко Сергей Ильич (RU)
(73) Патентообладатель(и):
Государственное образовательное учреждение высшего профессионального образования Новосибирское высшее военное командное училище (военный институт) Министерства обороны Российской Федерации (RU)
|
(54) СПОСОБ ИЗМЕРЕНИЯ ИЗНОСА КАНАЛА СТВОЛА И УСТРОЙСТВО ДЛЯ ЕГО ОСУЩЕСТВЛЕНИЯ (ВАРИАНТЫ)
(57) Реферат:
Изобретение относится к измерительной технике и может быть использовано для измерения износа гладких или нарезных стволов. В нужное сечение канала ствола 1 устанавливают измерительный цилиндр 2 с известными геометрическими размерами, создают в казенной части ствола избыточное давление измерительной жидкости или газа и измеряют расход среды, вытекающей через кольцевой зазор из дульной части ствола. Устройство для реализации способа на основе гидродинамических измерений содержит измерительный цилиндр 2 с установочной штангой 3, герметизирующий фланец 4 для подвода масла к казенной части ствола, заглушки для эжекторных отверстий 12, редуктор 9 для регулирования давления и манометр 10 для его измерения, масляный насос 15, резервуар 14 с маслом, выходной дульный фланец 5 с отверстиями для выпуска масла и фиксатором 11 установочной штанги 3, мерный сосуд 16 и секундомер 17 для измерения времени наполнения мерника. В варианте устройства на основе аэродинамических измерений содержатся компрессор или баллон со сжатым воздухом и ротаметр для измерения расхода воздуха. Изобретение повышает точность измерений, увеличивает долговечность измерительного оборудования при уменьшении его стоимости. 3 н.п. ф-лы, 3 ил.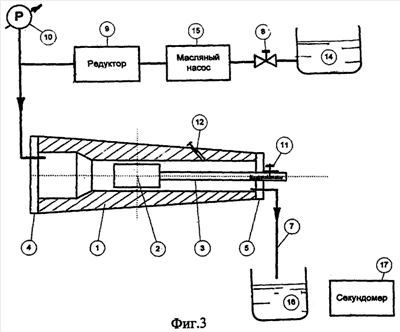
Изобретение относится к измерительной технике и может быть использовано для измерения износа гладких или нарезных стволов.
Известно, что эффективность огнестрельного оружия (дальность полета снаряда, бронепробиваемость) определяются начальной скоростью снаряда. Для оружия данного калибра и определенной массы снаряда увеличение начальной скорости снаряда достигается увеличением длины направляющей части ствола и повышением давления пороховых газов при выстреле.
Увеличение давления газов достигается применением высококалорийных порохов, подбором форм и размеров пороха, увеличением массы заряда и плотности заряжания. Во время выстрела под действием высоких температур и давлений и в результате движения снаряда происходит износ (разгар) канала ствола, который приводит к падению начальной скорости последующих выстрелов.
В войсковой практике для измерения износа канала стволов используются калибры и специализированные приборы контроля износа (Руководство по эксплуатации войсковых калибров и приборов для ракетно-артиллерийского вооружения. Воениздат. М.: 1983).
Проходные калибры, предназначенные для определения степени износа внутреннего диаметра или полей нарезов канала ствола образцов стрелкового оружия, представляют собой образцовые цилиндры, выполненные из инвара или другого материала с малым коэффициентом температурного расширения. Износ ствола характеризуется диаметром калибра, входящего в канал ствола с дульной и казенной частей без люфта. Процесс измерения износа состоит в последовательном введении в дульную (казенную) часть ствола калибров возрастающего номера без приложения к ним усилий.
Помимо проходных известны конические калибры. Применение конических калибров позволяет заменить относительно длинный ряд проходных калибров одним (с потерей точности измерений). Величина глубины вхождения калибра в канал ствола определяет величину износа.
Для более точных измерений используют микрометрические нутромеры.
Ручная механическая звездка представляет собой самоцентрирующийся нутромер с микрометрическим отсчетом. Ручная механическая звездка предназначена для измерения внутренних диаметров орудийных и минометных стволов и цилиндров противооткатных орудий начиная с 30 мм с точностью до 0,01 мм.
Диаметр измеряемого отверстия определяется по расстоянию между крайними точками измерительных штырей, разводимых с помощью клина.
Прибор контроля износа представляет собой раздвижной микрометрический нутромер с осью вращения отсчетного устройства, расположенной перпендикулярно плоскости измерения.
Основу прибора представляет измерительная головка, в которой осуществляется передача и преобразование вращательного движения отсчетного устройства в поступательное движение измерительного колка. Помимо измерительной головки в состав прибора входят соединительные штанги, центрирующие муфты и кольца, установочные фланцы и отсчетные устройства.
В приборах ПКИ-19 и ПКИ-20 вращение вала отсчетного устройства в измерительной головке с помощью конической передачи и микрометрического ходового винта и гайки передается подвижному измерительному стержню. Для ограничения измерительного усилия маховичок имеет храповое устройство (трещетку). Отсчет измерений производится по барабану со спиральной шкалой. Максимальная контролируемая величина износа 8 мм. Точность измерения износа приборами ±0,1 мм. Для установки шкалы в нулевое положение по установочному кольцу барабан имеет фрикционное устройство, которое позволяет производить холостой поворот барабана и перевод подвижного указателя на нужное деление шкалы.
В ручных механических звездках, предназначенных для измерения внутренних диаметров орудийных и минометных стволов и цилиндров противооткатных орудий, диаметр измеряемого отверстия определяется по расстоянию между крайними точками измерительных штырей, разводимых с помощью клина. Такая измерительная схема характеризуется максимальной точностью.
Приборы контроля износа и механические звездки содержат большое количество узлов и элементов точной механики. Это ограничивает их точность, приводит к очень высокой стоимости и требует высокой эксплуатационной культуры при измерениях.
В качестве прототипа рассмотрим наиболее близкую по технической сущности систему для осмотра дефектов внутренней поверхности и измерения износа каналов нарезных стволов (RU 2251072, G01B 11/03, G02B 23/00, 27.04.05).
В рассматриваемом изобретении описывается самоцентрирующаяся измерительная головка с двенадцатью подвижными измерительными колками с отверстиями. Информация о пространственном положении измерительных колков фиксируется видеокамерой. Перед измерением износа канала ствола производится калибровка измерительного зонда в специальном калибре. При работе системы ЭВМ вычисляет координаты отверстий колков, сравнивает их с паспортными значениями, полученными при калибровке, и выдает на дисплее результаты вычисления износа канала ствола по полям и по нарезам.
Недостатками известного способа являются:
– значительное усложнение аппаратуры,
– использование большого количества подвижных элементов точной механики, определяющих точность измерений;
– невозможность применения для контроля износа каналов стволов малого диаметра.
Задачей изобретения является создание универсального способа измерения износа, пригодного для измерений в стволах любых калибров, сочетающего низкую стоимость и износоустойчивость измерительной аппаратуры с простотой процесса измерений при сохранении высокой точности.
Технический результат – повышение точности измерений при уменьшении стоимости измерительного оборудования, увеличение его долговечности и снижение требований к эксплуатационному персоналу.
Решение указанной задачи достигается при использовании следующих физических закономерностей.
Так как износ канала ствола приводит к падению начальной скорости снаряда вследствие прорыва пороховых газов, для измерения износа предлагается использовать принципы гидроаэромеханики.
Принципы аэромеханики широко применяются в машиностроении для диагностики износа деталей поршневой группы двигателей внутреннего сгорания по степени сжатия воздуха (пиковые манометры или компрессометры).
В гидродинамике и газодинамике вещество, протекающее по трубе, принято называть жидкостью, независимо от того, в каком агрегатном состоянии оно находится, жидком или газообразном.
В классической гидродинамике рассматривается задача о падении напора жидкости в трубе круглого сечения за счет преодоления сопротивления течению. Выделяется два вида сопротивлений:
– сопротивления, проявляющиеся по всей длине потока, обусловленные силами трения частиц жидкости друг о друга и о стенки, ограничивающие поток;
– местные сопротивления, обусловленные разного рода препятствиями, установленными в потоке, приводящими к изменениям величины или направления скорости течения жидкости.
Если в исследуемый ствол поместить цилиндр с известными размерами, то задача измерения внутреннего диаметра ствола сводится к измерению расхода жидкости через кольцевой зазор.
Наиболее простыми и вместе с тем точными способами измерения расхода жидкости являются объемный и весовой.
При объемном способе измерения протекающая в исследуемом стволе жидкость поступает в специально тарированный сосуд-мерник, время наполнения которого точно фиксируется по секундомеру.
При весовом способе взвешиванием находят вес жидкости, поступившей в мерник за некоторое фиксированное время Т, определяют ее массу, массовый расход и, зная плотность жидкости, вычисляют объемный расход.
Известно аналитическое решение задачи осевого течения жидкости под действием перепада давлений в кольцевом зазоре, образованном двумя соосно расположенными цилиндрическими поверхностями (см. например Жоховский М.К. Теория и расчет приборов с неуплотненным поршнем М.: 1966).
Для фрикционного ламинарного течения жидкости расход в зазоре между цилиндром (внутренней поверхностью канала ствола) и неподвижным поршнем (измерительным цилиндром), если зазор b мал по сравнению с диаметром D, и если поршень расположен в цилиндре не соосно, а с максимальным эксцентриситетом (касание), определяется выражением:
;
где Q – расход жидкости;
D – диаметр измерительного цилиндра;
bo – износ канала ствола;
Р – давление в казенной части ствола;
µ – кинематическая вязкость жидкости;
l – длина измерительного цилиндра, помещенного в ствол.
Использование принципов гидроаэромеханики позволяет перейти от измерения линейного размера износа в точке касания измерительного колка к измерению расхода жидкости в кольцевом зазоре, который является функцией износа канала ствола.
Предложен способ измерения износа канала ствола (Фиг.1), включающий установку в нужное сечение канала ствола 1 измерительного цилиндра 2 с известными геометрическими размерами, создание в казенной части ствола избыточного давления измерительной жидкости или газа и измерение расхода измерительной жидкости или газа, вытекающих через кольцевой зазор из дульной части ствола.
Реализация способа возможна в виде аэродинамических или гидродинамических измерений.
Предложено устройство для измерения износа канала ствола (Фиг.2) на основе аэродинамических измерений, которое содержит помещаемый внутрь ствола 1 измерительный цилиндр 2 с известными геометрическими размерами, компрессор или баллон с сжатым воздухом 6, магистральный вентиль 8, редуктор для регулирования давления 9 и манометр для его измерения 10, фланец для подвода сжатого воздуха к казенной части ствола 4, заглушек для эжекторных отверстий 12, выходной фланец 5 с фиксатором 11 установочной штанги 3, устанавливаемый в дульный срез, линию свободного сброса 7 и ротаметр для измерения расхода воздуха 13.
Для проведения измерений износа аэродинамическим методом осуществляют:
– приведение ствола в горизонтальное положение;
– соединение измерительного цилиндра с установочной штангой;
– введение в нужное сечение ствола измерительного цилиндра;
– установку дульного фланца с отверстиями для установочной штанги и выпуска воздуха;
– установку герметизирующего фланца для подачи сжатого воздуха в казенную часть ствола;
– установку заглушек на эжекторные отверстия;
– подключение воздушной линии к герметизирующему фланцу;
– установку с помощью редуктора и манометра необходимого значения избыточного давления в казенной части ствола;
– определение положения поплавка ротаметра;
– определение износа канала ствола по тарировочному графику.
Сжатый воздух, поданный в герметизированную казенную часть ствола, пройдя через кольцевой зазор между внутренней поверхностью ствола и наружной поверхностью измерительного цилиндра, дросселируется до атмосферного давления в линии свободного сброса. Расход воздуха, измеренный с помощью ротаметра, является функцией износа канала ствола.
Предложено устройство для измерения износа канала ствола (Фиг.3) на основе гидродинамических измерений, которое содержит помещаемый внутрь ствола 1 измерительный цилиндр 2 с известными геометрическими размерами, резервуар с маслом 14, магистральный вентиль 8, масляный насос 15, редуктор для регулирования давления 9 и манометр для его измерения 10, фланец для подвода масла к казенной части ствола 4, заглушек для эжекторных отверстий 12, выходной дульный фланец 5 с фиксатором 11 установочной штанги 3, устанавливаемый в дульный срез, линию свободного сброса 7, мерный сосуд 16 и секундомер для измерения времени его заполнения 17.
Дульный фланец 5 содержит фиксатор установочной штанги и отсчетный индекс для определения положения измерительного цилиндра 2. Путем перемещения измерительного цилиндра возможно осуществление измерения износа в любом сечении ствола. Отсчет положения измерительного цилиндра осуществляется по шкале, нанесенной на установочную штангу.
Для достижения высокой точности измерений возможно изменение величины избыточного давления масла в казенной части ствола в широких пределах. Верхняя граница давления определяется условием ламинарного течения жидкости в кольцевом зазоре. Тип манометра выбирается в соответствии с заданной точностью измерений (погрешность наиболее точных эталонных манометров 0.002-0.005%).
Для проведения измерений износа гидродинамическим методом осуществляют:
– приведение ствола в горизонтальное положение;
– соединение измерительного цилиндра с установочной штангой;
– введение в нужное сечение ствола измерительного цилиндра;
– установку дульного фланца с отверстиями для установочной штанги и выпуска масла;
– установку герметизирующего фланца для подачи масла в казенную часть ствола;
– установку заглушек на эжекторные отверстия;
– подключение масляного насоса к герметизирующему фланцу;
– установку с помощью редуктора и манометра необходимого значения избыточного давления в казенной части ствола;
– достижение установившегося режима истечения масла;
– сбор масла, вытекающего из дульной части ствола в специальный мерник;
– измерение с помощью секундомера времени заполнения мерника маслом;
– определение износа канала ствола по тарировочному графику.
Предложенный способ измерения износа канала ствола обладает рядом преимуществ перед существующими:
– применим для реализации в нарезных и гладких стволах любых калибров;
– реализуем на основе массово выпускаемых узлов и не требует создания специальной аппаратуры;
– не требует центрирования измерительной головки в канале ствола;
– не требует использования быстро изнашиваемых узлов, определяющих точность измерений;
– не требует высокой квалификации эксплуатационного персонала.
Формула изобретения
1. Способ измерения износа канала ствола, включающий приведение ствола в горизонтальное положение, установку в нужное сечение канала ствола измерительного цилиндра с известными геометрическими размерами, отличающийся тем, что создают в казенной части ствола избыточное давление измерительной жидкости или газа, измеряют расход измерительной жидкости или газа, вытекающих через кольцевой зазор, образованный внутренней поверхностью ствола и наружной поверхностью измерительного цилиндра, из дульной части ствола при заданном давлении в казенной части ствола, и по величине расхода определяют износ канала ствола.
2. Устройство для измерения износа канала ствола, содержащее помещаемый внутрь ствола измерительный цилиндр с известными геометрическими размерами, отличающееся тем, что при аэродинамических измерениях оно содержит: для создания избыточного давления в казенной части ствола – компрессор или баллон со сжатым воздухом, магистральный вентиль, редуктор для регулирования давления и манометр для его измерения, фланец для подвода сжатого воздуха к казенной части ствола, для измерения расхода воздуха – заглушки эжекторных отверстий, выходной фланец с фиксатором, соединенный с измерительным цилиндром установочной штанги со шкалой, устанавливаемый в дульный срез, и ротаметр.
3. Устройство для измерения износа канала ствола, содержащее помещаемый внутрь ствола измерительный цилиндр с известными геометрическими размерами, отличающееся тем, что при гидродинамических измерениях оно содержит: для создания избыточного давления в казенной части ствола – масляный бак, магистральный вентиль, масляный редуктор для регулирования давления и манометр для его измерения, фланец для подвода масла к казенной части ствола, для измерения расхода масла – заглушки эжекторных отверстий, выходной фланец с фиксатором, соединенный с измерительным цилиндром установочной штанги со шкалой, устанавливаемый в дульный срез, мерный сосуд и секундомер для измерения времени его заполнения.
РИСУНКИ
|