(21), (22) Заявка: 2007130716/04, 10.08.2007
(24) Дата начала отсчета срока действия патента:
10.08.2007
(43) Дата публикации заявки: 20.02.2009
(46) Опубликовано: 20.06.2009
(56) Список документов, цитированных в отчете о поиске:
CN 1443741 A, 24.09.2003. SU 165691 A, 15.10.1964. US 2002/0183566 A1, 05.12.2002. US 4895989 A, 23.01.1990.
Адрес для переписки:
191186, Санкт-Петербург, ул. Миллионная, 3, ЗАО “Химтэк Инжиниринг”, первому зам.ген.директора А.В.Маруеву
|
(72) Автор(ы):
Михайлова Татьяна Алексеевна (RU), Никущенко Наталья Трофимовна (RU), Нагродский Михаил Иосифович (RU), Потехин Вячеслав Вячеславович (RU), Луговской Сергей Анатольевич (RU)
(73) Патентообладатель(и):
Закрытое акционерное общество “Химтэк Инжиниринг” (RU)
|
(54) СПОСОБ ПОЛУЧЕНИЯ МЕТИЛАТА КАЛИЯ
(57) Реферат:
Изобретение относится к способу получения метилата калия, который в виде сухого вещества или безводного раствора в метиловом спирте используется в качестве катализатора при расщеплении масел и жиров, в реакциях этерификации при производстве биодизеля, поверхностно-активных веществ, фармацевтических и косметических препаратов. Способ включает взаимодействие гидроксида калия и метанола при повышенной температуре с удалением образовавшейся воды парами осушенного метилового спирта. При этом синтез осуществляют в реакционно-разделительном процессе в противоточном колонном реакторе пленочного типа при температуре 92-130°С, одинаковой по всей высоте реактора, при подаче сверху исходного раствора, приготовленного растворением гидроксида калия в метиловом спирте, снизу – паров осушенного метилового спирта. Способ позволяет повысить эффективность десорбции образующейся воды и производительность процесса, а также снизить его энергоемкость. 1 табл., 1 ил.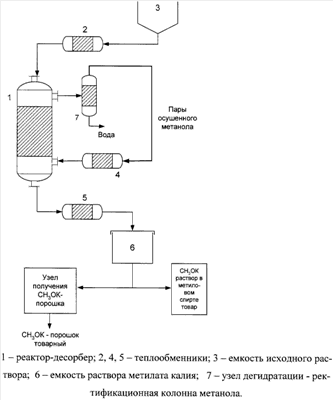
Изобретение относится к способу получения алкоголятов щелочных металлов, а именно к способу получения метилата калия.
Метилат калия в виде сухого вещества или безводного раствора в метиловом спирте используется в качестве катализатора при расщеплении масел и жиров, в реакциях этерификации при производстве биодизеля, поверхностно-активных веществ, фармацевтических и косметических препаратов. Наиболее распространенными являются товарные формы, содержащие 25-33% метилата калия в метаноле.
Известны способы получения алкоголятов щелочных металлов реакцией щелочного металла и низшего спирта (C1-C3) при комнатной температуре с образованием водорода, в частности способ [US 2965663, кл 200-448, оп. 25.11.1957].
Недостатком способа является взрыво-пожароопасность, связанная с выделением значительного количества водорода (1/2 моля Н2 на моль метанола), и сложностью обращения с щелочным металлом.
Известен способ получения растворов метилатов щелочных металлов из низших спиртов C1-C4 электролизом растворов хлоридов щелочных металлов в соответствующем спирте [US 5,425,856, кл. С25В 3/00, оп. 20.06.1995].
В процессе электролиза выделяются водород и хлор. Недостатком способа является сложность его реализации в промышленном масштабе из-за особенности аппаратурного оформления и энергоемкости процесса.
Известен способ получения алкоголятов щелочных металлов из предварительно осушенного карбоната щелочного металла и соответствующего спирта [патент России 2178402 С1, кл. С07С 29/70, 31/30, оп. 20.01.2002].
Недостатком способа является высокое, до 15% вес., содержание карбоната щелочного металла в конечном продукте и сложность очистки готового продукта от карбоната до принятой технической нормы – не более 0.1 г карбоната на 100 г метилата.
Аналогами предлагаемого способа являются способы [US 3,479,381, кл. С07С 31/28, оп. 23.05.67 и DE 100701, кл. С07С 31/30, оп. 05.10.73; CN 1186302C, кл. С07С 31/30, 29/70, оп. 26.01.2005] получения алкоголятов щелочных металлов при взаимодействии низшего алифатического спирта ряда C1-C3 с гидроксидом щелочного металла в соответствии с реакцией

где R – алкильный радикал;
М – щелочной металл.
Реакция обратима, поэтому авторы способа [US 3,479,381, кл. С07С 31/28, оп. 23.05.67] связывают образующуюся воду введением в зону реакции синтетических цеолитов. Основным недостатком способа является ограниченная поглощающая способность цеолитов и необходимость их регенерации.
Авторы способа [DE 100701, кл. С07С 31/30, оп. 05.10.78] удаляют реакционную воду азеотропной ректификацией, вводя органический реагент, образующий с водой азеотропную смесь. Недостатком способа является введение в реакционную смесь дополнительного органического реагента, образующего азеотропную смесь с водой, что значительно осложняет его осушку для использования вновь.
Способ [CN 1186302 C, кл. С07С 31/30, 29/70, оп. 26.01.2005] производства метилата калия (СН3ОК), в соответствии с которым в качестве сырья для получения метилата калия используют метиловый спирт (СН3ОН) и гидроксид калия (КОН). Исходные вещества смешивают, нагревают и удаляют воду путем подачи осушенного метанола. Процесс организован в периодическом режиме.
В соответствии с описанием получение метилата калия проводят в реакторе, представляющем собой куб-испаритель, в который загружают исходные вещества 64% масс. КОН и 36% масс. СН3ОН (1:1 в мольном соотношении). Смесь нагревают при перемешивании до 94-104°С и затем в термостатированную реакционную смесь дозируют осушенный метиловый спирт. Образующаяся при взаимодействии метилового спирта и гидроксида калия вода выводится из реакционной зоны с парами метанола. Обводненные пары метанола направляют на дегидратацию. Количество осушенного метанола, подаваемого в зону реакции, должно быть таким, чтобы обеспечить отвод воды, которая образуется в количестве 0.26 г Н2O на 1 г метилата калия.
Проведенная авторами заявляемого изобретения экспериментальная проверка показала, что в указанных в способе условиях для отвода образующейся воды необходим избыток осушенного метанола на уровне 64-68 г на 1 г СН3ОК, т.е. для получения 1 тонны СН3ОК в рецикле должно быть не меньше 64-68 тонн осушенного метанола. Необходимость такого рецикла метанола обусловлена неэффективным массообменным процессом в зоне реакции.
При реализации этого способа в непрерывном режиме концентрация воды в реакторе должна быть на таком же уровне, как в товарной форме ( 0,2%), т.е. упругость паров над таким раствором низкая, и для удаления ее из реактора требуется дополнительное многократное увеличение расхода осушенного метанола.
Недостатком способа является периодический режим, высокие энергозатраты, обусловленные необходимостью многократного рецикла метанола.
Известен способ [SU 165691] – прототип, в котором метилат натрия (аналог метилата калия) получают в реакционно-разделительном процессе в противоточном колонном реакторе с насадкой при температуре 85-95°С при подаче сверху исходного раствора, приготовленного растворением безводного гидроксида натрия в метиловом спирте, снизу – паров осушенного метилового спирта.
Удаляемые из верхней части реактора пары обводненного метанола направляются на осушку в ректификационную колонну. Пары осушенного метанола конденсируются, затем часть их через испаритель и пароперегреватель подают в реактор, часть используют для приготовления исходного раствора NaOH в метаноле.
В кубе реакционной колонны полученный раствор концентрируют, испаряя метанол.
Из куба реакционной колонны непрерывно выводят раствор метилата натрия в метиловом спирте, а из куба ректификационной колонны – воду.
Способ позволяет уменьшить количество осушенного метанола, используемого для удаления воды, и снизить энергоемкость процесса в сравнении с известными. Однако способ имеет ряд недостатков.
В способе [SU 165691] сырьевые компоненты поступают в реактор без нагревания. Низкая упругость паров воды не обеспечивает эффективной десорбции. Чтобы нагреть реакционную смесь, в реактор подается дополнительное количество перегретых паров осушенного метанола.
Концентрирование раствора испарением метанола в кубе реакционной колонны увеличивает поток метанола, поступающий на ректификацию для осушки, что также повышает его энергоемкость.
Необоснованные затраты энергии происходят при конденсации паров осушенного метанола, выходящих из ректификационной колонны, и их дальнейшем испарении перед подачей в реактор.
Задачей предлагаемого способа является снижение энергоемкости процесса получения метилата калия.
Сущность предлагаемого способа заключается в том, что метилат калия получают при повышенной температуре и постоянном давлении, удаляя образовавшуюся воду парами рециклизируемого метилового спирта. Синтез осуществляют при температуре 92-130°С, одинаковой по всей высоте реактора, непрерывно в реакционно-разделительном процессе в противоточном колонном реакторе пленочного типа при подаче сверху исходного раствора КОН в метиловом спирте, пары осушенного метилового спирта подают в противотоке к исходному раствору.
Схема реакторного узла представлена на чертеже.
Способ осуществляется следующим образом.
КОН и СН3ОН в нужном соотношении непрерывно через подогреватель (поз.3) подают для удаления воды в верхнюю часть реактора-десорбера колонного типа (поз.1), снизу в реактор-десорбер подают пары осушенного метанола, нагретые в пароперегревателе (поз.4). В примерах описано получение 33%-ного и 46%-ного растворов метилата калия в метаноле. Температура кипения метанольных растворов гидроокиси калия соответствующей концентрации (25% КОН и 35% КОН) 94°С и 127°С соответственно. Температура перегретого пара в заявленном способе эквивалентна количеству воды, которую надо испарить в реакторе. Снизу реактора-десорбера отводится безводный раствор метилата калия в метаноле. При необходимости из него может быть получен сухой метилат калия испарением метанола известными способами.
Пары обводненного метанола поступают на стадию дегидратации, откуда пары осушенного метанола без конденсации подаются в пароперегреватель и рециклизируются в реактор.
Отличительными признаками способа являются:
1. Нагревание исходного раствора щелочи в метаноле. При этом для нагревания используется экономичный теплоноситель – водяной пар, используемый в теплообменнике, а не пары осушенного метанола, полученные в ректификационной колонне с флегмовым числом 2÷3 и нагретые в пароперегревателе.
2. Раствор нужной концентрации СН3ОК в метаноле получают прямым растворением соответствующего количества КОН в метаноле без упаривания в реакторе, увеличивающего поток метанола, направляемый на энергоемкую стадию обезвоживания метанола.
3. Нагретые до нужной температуры пары осушенного метанола поступают из ректификационной колонны в реактор-десорбер, минуя стадии конденсации и испарения.
Преимущества предложенного решения:
снижение энергоемкости в сравнении с прототипом за счет
– уменьшения ~ в 2 раза количества рециклизируемого осушенного метанола;
– исключения стадий конденсации и испарения осушенного метанола, направляемого в десорбер;
– исключения стадии концентрирования раствора метилата калия в реакторе.
Примеры конкретного выполнения
Синтез метилата калия проводили на установке при атмосферном давлении. Схема представлена на чертеже. Результаты опытов представлены в таблице.
Приготовленный в емкости (поз.3) гомогенный раствор гидроксида калия в метиловом спирте с содержанием влаги 0.03% нагревали до температуры кипения в теплообменнике (поз.2) и непрерывно подавали в реактор-десорбер (поз.1), который представляет собой стеклянную колонку диаметром 20 мм, высотой 400 мм, снабженную теплоизолирующей рубашкой и заполненную насадкой из нержавеющей стали типа «спираль с замкнутыми витками» d=3 мм. Одновременно с вводом в реактор-десорбер реакционного раствора начинали подачу паров осушенного метанола из ректификационной колонны (содержание влаги не более 0.05%) в теплообменник (поз.4), в котором пары нагревали до заданной температуры. Пары осушенного метилового спирта непрерывно подавали в нижнюю часть реактора-десорбера противотоком к исходному раствору. Из верхней части реактора-десорбера обводненные пары метанола поступали на ректификацию для обезвоживания, а из нижней части реактора-десорбера непрерывно выводили целевой раствор метилата калия в метаноле с содержанием воды 0.2%, который охлаждали в теплообменнике (поз.5) и накапливали в сборнике (поз.6).
Пример 1
Реализован по прототипу с использованием КОН вместо NaOH. Раствор 75 г/л NaOH в метаноле эквивалентен раствору 109 г/л КОН в метаноле. Расход осушенного метанола представлен в виде двух слагаемых: 2620 г/час – требуется для удаления реакционной воды, 452 г/час – требуется для концентрирования целевого раствора до 33% (определяется температурой кипения 94°С). Осушенный метанол подается в реактор в виде паров, полученных испарением и перегревом сконденсированного дистиллата колонны обезвоживания метанола.
Пример 2
Реализован по прототипу, но исходная концентрация КОН в метаноле увеличена до 25%, что обеспечивает получение целевого раствора с концентрацией 33% без дополнительного испарения метанола. Осушенный метанол подавали в реактор в виде паров, полученных испарением и перегревом сконденсированного дистиллата колонны обезвоживания метанола.
Примеры 3 и 4
Реализованы по заявленному способу. В зависимости от требуемой концентрации конечного продукта (33 или 46% СН3ОК в метаноле) исходный раствор нагревают до 94°С или 127°С, соответственно. Пары осушенного метанола подают через пароперегреватель из колонны без конденсации и испарения.
Пример 5
Демонстрирует увеличение расхода осушенного метанола, если температура исходного раствора ниже заявленной.
Приведенные примеры иллюстрируют заявленный способ, но не ограничивают его.
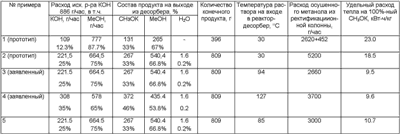
Формула изобретения
Способ получения метилата калия реакцией гидроксида калия и метанола при повышенной температуре с удалением образовавшейся воды парами осушенного метилового спирта, отличающийся тем, что синтез осуществляется в реакционно-разделительном процессе в противоточном колонном реакторе пленочного типа при температуре 92-130°С, одинаковой по всей высоте реактора, при подаче сверху исходного раствора, приготовленного растворением гидроксида калия в метиловом спирте, снизу – паров осушенного метилового спирта.
РИСУНКИ
|