|
(21), (22) Заявка: 2006116574/15, 30.09.2004
(24) Дата начала отсчета срока действия патента:
30.09.2004
(30) Конвенционный приоритет:
16.10.2003 EP 03103838.3 20.10.2003 US 60/512,640
(43) Дата публикации заявки: 27.11.2007
(46) Опубликовано: 20.06.2009
(56) Список документов, цитированных в отчете о поиске:
WO 99/08782 A1, 25.02.1999. DE 2722906 А, 02.11.1978. WO 02051544 A1, 04.07.2002. RU 2140813 C1, 10.11.1999. RU 2139467 C1, 10.10.1999.
(85) Дата перевода заявки PCT на национальную фазу:
16.05.2006
(86) Заявка PCT:
EP 2004/010943 20040930
(87) Публикация PCT:
WO 2005/039745 20050506
Адрес для переписки:
129010, Москва, ул. Б.Спасская, 25, стр.3, ООО “Юридическая фирма Городисский и Партнеры”, пат.пов. Е.Е.Назиной, рег. 517
|
(72) Автор(ы):
АРЛЕТТИ Арриго (IT), ВИНЧЕНЦИ Паоло (IT)
(73) Патентообладатель(и):
БАЗЕЛЛЬ ПОЛИОЛЕФИН ИТАЛИЯ С.Р.Л. (IT)
|
(54) СПОСОБ НЕПРЕРЫВНОГО ПОЛУЧЕНИЯ ЭМУЛЬСИЙ
(57) Реферат:
Изобретение относится к способу непрерывного получения эмульсии с особенно узким распределением капелек по размеру и может использоваться при полимеризации олефинов. Способ включает обработку по меньшей мере двух несмешивающихся жидкостей последовательно в по меньшей мере двух стадиях смешивания, проводимых в последовательных статор-роторных устройствах. Периферийный выход из первого статор-роторного устройства соединен с аксиальным входом в последующее статор-роторное устройство посредством трубопровода, в котором число Рейнольдса выше 5000. Начальный участок трубопровода расположен тангенциально к окружности ротора. Окружная скорость каждого ротора составляет от 5 до 60 м/с. Технический результат состоит в минимизации слипания при образовании эмульсий, характеризующихся узким распределением капелек дисперсной фазы по размеру. 13 з.п. ф-лы, 2 ил.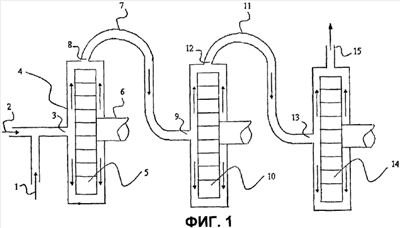
Настоящее изобретение относится к способу непрерывного получения эмульсий, имеющих однородное распределение по размеру капелек, образующих дисперсную фазу эмульсии.
В частности, настоящее изобретение относится к способу непрерывного получения эмульсий, содержащих в качестве дисперсной фазы капельки расплавленного аддукта галогенид магния-основание Льюиса, причем эмульсий с особенно узким распределением капелек по размеру.
Ближайшим и конкретным применением настоящего изобретения является непрерывное получение эмульсий, которое после стадии охлаждения позволяет получать твердые частицы аддукта дигалогенид магния-основание Льюиса, имеющего более однородное распределение по размеру. Полученные твердые частицы, принимая во внимание их узкое распределение по размеру частиц, могут быть применены преимущественно в качестве носителя в приготовлении нанесенных катализаторов для полимеризации олефинов.
Известно, что для смешивания различных материалов, таких как адгезивы, покрытия, косметика, пищевые продукты, пластмассы и т.д., применяют промышленные смесители и эмульгаторы. Обычно внутри промышленных смесителей высокую скорость и гидравлические сдвиговые усилия создают вращением ротора относительно статора: жидкости подают аксиально в ротор-статорный аппарат, а дисперсию отводят радиально от борта ротор-статорного аппарата. Когда две несмешивающиеся жидкости подвергают действию высокой скорости и гидравлических сдвиговых сил, одна жидкость может диспергироваться в форме капелек (дисперсная фаза) во второй жидкости (непрерывная фаза), приводя к образованию эмульсии.
Средний размер капелек в дисперсной фазе напрямую зависит от интенсивности энергии, создаваемой ротором. Обычно, чем выше энергия перемешивания, тем меньше средний размер капелек, полученных как дисперсная фаза эмульсии. Другим важным параметром, сильно влияющим на конечный размер полученных капелек, является степень слияния во время процесса эмульгирования. В таких процессах капельки эмульсии находятся, в основном, в динамическом равновесии между явлениями измельчения, вызванными сдвиговым действием, и слияния, стремящимися аггрегировать капельки. Слияние капелек вызывает увеличение конечного среднего размера капелек, получаемых на выходе процесса, значительно увеличивая, таким образом, фракцию крупных частиц. Такие явления слияния контрастируют со сдвиговым действием, вызванным движением ротора. В зонах смешивания, близких к ротору, сдвиговое усилие является интенсивным и, следовательно, образуются капельки, имеющие малый размер. Дальше от ротора сдвиговое усилие уменьшается, а явления слипания увеличиваются, вызывая увеличение размера капелек. Большие капельки образуются в зонах смешивания на некотором расстоянии от ротора. Как следствие, полученные эмульсии показывают неоднородное распределение капелек по размеру. В патенте США 5622650 описывается способ эмульгирования гидрофобной жидкости и гидрофильной жидкости для получения эмульсии, в частности эмульсии «вода-в-масле». Указанные эмульсии «вода-в-масле» применяют в приготовлении микрокапсул для использования в производстве безуглеродной копировальной бумаги. Такой способ эмульгирования использует измельчающую машину, включающую корпус мельницы, имеющий в нем существенно цилиндрическую полость. Измельчающая машина также имеет большое количество кольцевых, концентрических рядов выступов статора и большое количество кольцевых, концентрических рядов выступов ротора, в которой кольцевые ряды выступов статора являются концентрически соседними с, или вставляются в или чередуются с кольцевыми рядами выступов ротора. Жидкости, входящие в мельницу, проходят через зоны сдвига увеличивающейся интенсивности перед тем, как достичь внешней периферии роторного элемента. Жидкости текут радиально через первое измельчающее пространство и аксиально через второе измельчающее пространство в пределах тесного периферического просвета между насеченной внешней окружностью роторного элемента и внутренней стенкой полости перед тем, как жидкости достигнут выпуска из мельницы. Наиболее важным признаком измельчающей машины по патенту США 5622650 является применение способа непрерывной подачи за один проход для получения эмульсий, имеющих более однородный размер частиц. Указанный однопроходный способ является специальным для получения микрокапсул для применения в производстве безуглеродной копировальной бумаги и не может быть перенесен в промышленности на получение эмульсий, которые, будучи охлажденными, могут дать твердые частицы для применения в приготовлении нанесенных катализаторов.
В патенте США 5643506 описывается способ приготовления микрокапсул, имеющих существенно однородное распределение по размеру, который включает непрерывное образование эмульсии «вода-в-масле», в которой гидрофобная фаза составляет примерно 45-95 об.% и гидрофильная фаза составляет 5-55 об.%, и где размер частиц эмульсии регулируется установкой отношения масло/вода в пределах вышеуказанных интервалов. Что касается приготовления твердых компонентов катализатора, несомненно, предпочтительно избегать регулирования распределения частиц по размеру изменением отношения дисперсной фазы к непрерывной фазе. Например, уменьшение количества дисперсной фазы вызывает соответствующее уменьшение генерированных твердых частиц, приводя к неприемлемому снижению производительности. Кроме того, способ по патенту США 5643506 предполагает добавление особых химических соединений (изоцианатов) к гидрофобной фазе и гидрофильной фазе. Добавление таких химических соединений вызывает модификацию физических и химических характеристик полученной эмульсии. Этот метод не может быть применен к получению твердых каталитических компонентов, так как указанные химические соединения могут вызывать значительное снижение активности конечного катализатора.
Патент США 5632596 относится к ротор-статорному аппарату для получения субмикронного размера капелек жидкость-жидкостной эмульсии, причем этот ротор-статорный аппарат может эксплуатироваться в разнообразных операциях смешивания, например, смешивания, эмульгирования, гомогенизации, растворения, диспергирования, блендирования и т.д. Особая конфигурация ротор-статорного аппарата по патенту США 5632596 обеспечивает увеличение сдвигового усилия в обрабатываемой жидкой смеси. Указанный ротор-статорный аппарат включает ротор и статор, каждый из которых имеет большое количество зубцов, в котором высота зубцов меньше одной двадцатой диаметра ротор-статора. Патент США 6000840 относится к ротор-статорным аппаратам, пригодным для промышленных смесителей и эмульгаторов, механическая конфигурация которых представляет альтернативу конфигурации, описанной в патенте США 5632596. Особая конфигурация ротор-статорных аппаратов по патенту США 6000840 позволяет передавать увеличенные и (или) дополнительные высокоскоростные усилия и повышенные давления обрабатываемой смеси. Статор по патенту США 6000840 содержит большое количество отверстий, причем указанное большое количество отверстий выполняют попарно, обычно, в конфигурации V-формы. Ротор указанного аппарата содержит большое количество лопастей и приспособлений для поддерживания лопастей при вращении вокруг оси вращения. Оба вышеописанных ротор-статорных аппарата по патентам США 5632596 и 6000840 имеют целью улучшить эффект смешивания при одноступенчатом смешивании и никак не рассматривают явления слипания ниже по течению стадии смешивания. Как объяснялось выше, явления слипания особенно важны, вызывая увеличение размера капелек, и, как следствие, полученные эмульсии характеризуются неоднородным распределением размеров капелек.
Высокая степень слипания в указанных методах прежнего уровня техники является нежелательной, так как, когда явления слипания не контролируются, образуются эмульсии с капельками дисперсной фазы, имеющими неоднородное, более широкое распределение. Такой недостаток обязательно должен быть сведен к минимуму, особенно, когда полученная эмульсия должна быть использована для приготовления нанесенных катализаторов полимеризации олефинов. Действительно, в этом специальном применении, как можно более узкое распределение носителя по размеру является весьма желательным.
В свете вышесказанного было бы желательно иметь доступный способ непрерывного получения эмульсий, в котором явления слипания значительно минимизированы, а эффективность способа в отношении передачи энергии жидкости повышена.
Теперь разработан способ получения эмульсий двух несмешивающихся жидкостей, в котором явления слипания минимизированы с образованием эмульсий, характеризующихся узким распределением капелек по размеру в дисперсной фазе.
Таким образом, целью настоящего изобретения является многостадийный способ непрерывного получения эмульсии, включающий обработку по меньшей мере двух несмешивающихся жидкостей последовательно в по меньшей мере двух стадиях смешивания, осуществляемых в по меньшей мере двух последовательных статор-роторных устройствах, в котором: 1) периферийный выход из первого статор-роторного устройства соединяют с аксиальным входом в последующее статор-роторное устройство посредством трубопровода, в котором число Рейнольдса (ReT) внутри указанного трубопровода выше 5000, и 2) окружная скорость каждого ротора статор-роторных устройств составляет от 5 до 60 м/с.
Окружная скорость роторного диска обычно определяется как произведение угловой скорости вращения, умноженной на радиус самого ротора.
Число Рейнольдса относительно движения флюида внутри трубопровода (ReT) определяется формулой ReT=Dvd/з, в которой D – диаметр трубопровода, v – линейная скорость флюида, d – плотность флюида и з – динамическая вязкость.
Согласно способу по настоящему изобретению, смешивание двух или больше несмешивающихся жидкостей проводят в одном или более статор-роторных устройствах, причем каждую стадию смешивания соединяют с последующей стадией посредством одного или более трубопроводов, соединяющих периферийный выпуск из статор-роторного устройства с аксиальным входом в последующее статор-роторное устройство.
В настоящем описании термин «периферийный выход» означает, что выход находится вблизи внешней окружности ротора, а термин «аксиальный вход» означает, что вход размещен в центральной части статор-роторного устройства, т.е. вблизи оси ротора.
Способ по изобретению будет описан в отношении получения эмульсии, содержащей расплавленный аддукт дигалогенид магния-основание Льюиса в качестве дисперсной фазы, и жидкость, инертную и несмешивающуюся с указанным аддуктом дигалогенид магния-основание Льюиса, в качестве непрерывной фазы.
Указанной инертной и несмешивающейся жидкостью предпочтительно является органическая жидкость, выбранная из алифатических и ароматических углеводородов, силиконовых масел, жидких полимеров или смесей указанных соединений. Парафиновые масла и силиконовые масла, имеющие вязкость от 30 до 300 сСт при комнатной температуре, являются особенно предпочтительными.
Что касается отношения при подаче указанных компонентов, то расплавленный аддукт дигалогенид магния-основание Льюиса подают в первую стадию смешивания в весовом отношении к инертной и несмешивающейся жидкости обычно меньше 0,5, предпочтительно меньше 0,3.
Неожиданно было обнаружено, что когда применяются указанные величины окружной скорости (5-60 м/с) и ReT (>5000), то получают минимизацию явлений слипания во всем способе эмульгирования. В частности, лучшие результаты по минимизации явлений слипания и улучшению распределения капелек по размеру получают, когда применяют следующие параметры способа: 1) число Рейнольдса ReT выше 8000 внутри трубопровода; 2) окружная скорость роторного диска в интервале от 20 до 60 м/с; 3) время пребывания в каждой стадии смешивания меньше 1 секунды.
Время пребывания в стадии смешивания определяется как отношение между объемом, занятым жидкостью в стадии смешивания, и объемной скоростью на выходе из стадии смешивания.
Согласно способу по настоящему изобретению, вышеуказанные несмешивающиеся жидкости подают в первую стадию смешивания, осуществляемую в первом статор-роторном устройстве. Вход двух несмешивающихся жидкостей размещают вблизи оси ротора (аксиальный вход), так что входящие жидкости принуждаются вращением ротора течь от оси ротора к периферийному ободу ротора. Таким образом, жидкие компоненты текут с большой скоростью внутри ограниченного пространства между поверхностями статора и ротора. Вследствие сильного перемешивания и сдвигового усилия, вызываемых вращением ротора, образуется эмульсия вышеуказанных жидкостей. Из-за обоюдной несмешиваемости расплавленный аддукт дигалогенид магния-основание Льюиса диспергируется в форме маленьких капелек в жидкости, подаваемой как непрерывная фаза.
Когда полученная эмульсия достигает периферической области первой стадии смешивания, то она принуждается входить в трубу, соединяющую периферийный выход из первого статор-роторного устройства со входом, размещенным в центральной части следующего статор-роторного устройства. Перенос эмульсии вдоль соединительного трубопровода достигается за счет использования энергии первого роторного диска. Будучи введенной во вторую стадию смешивания, эмульсия принуждается вращением второго роторного диска течь с большой скоростью от оси ротора к периферийному ободу ротора. Те же самые эффекты, что и на первой стадии, получают во второй стадии смешивания в отношении сдвига и смешивания. Когда эмульсия достигает периферической области второй стадии смешивания, то она принуждается входить в другой трубопровод, соединяющий периферийный выход из второго статор-роторного устройства с аксиальным входом следующего статор-роторного устройства.
Ввиду интенсивного сдвигового усилия, создаваемого каждым роторным диском, когда эмульсия течет через трубопроводы, соединяющие стадии смешивания друг с другом, устанавливается турбулентный поток. Как объяснялось выше, число Рейнольдса ReT эмульсии внутри соединительных трубопроводов составляет обычно выше 5000. Заметим, что Re ниже 2000 соответствует ламинарному течению, в то время как Re выше 4000 соответствует турбулентному течению. Зона между 2000 и 4000 – это так называемая переходная зона. Соединительные трубопроводы предпочтительно имеют спиральную форму: это улучшает эффективность способа в отношении снижения явлений слипания между стадией смешивания и следующей стадией. Стадии смешивания, следующие за первой стадией, имеют функцию улучшать эффективность способа эмульгирования посредством увеличения количества энергии, сообщаемой жидкостям. Полученная эмульсия затем выгружается из последней стадии смешивания через периферический выход последнего статор-роторного устройства.
В способе эмульгирования по настоящему изобретению энергия смешивания сообщается жидкостям более равномерно относительно способов прежнего уровня техники. Многостадийный способ по настоящему изобретению является особенно новаторским, поскольку позволяет использовать больше стадий смешивания, преодолевая недостатки в известном уровне техники, вызванные явлениями слипания между одной стадией и следующей стадией. Действительно, распределение капелек по размеру, полученное на выходе из каждой стадии смешивания, поддерживается существенно неизмененным на входе следующей стадии смешивания эффектом специального соединительного звена статор-роторных устройств. В силу высокой интенсивности турбулентности (ReT>5000), создаваемой внутри каждого соединительного трубопровода, способ по настоящему изобретению позволяет минимизировать явления слипания между каждой стадией эмульгирования. Как следствие, результаты, полученные в первой стадии смешивания в отношении распределения капелек по размеру, могут быть перенесены во вторую стадию смешивания, где распределение капелек по размеру также улучшается. Это является наиболее важным преимуществом, обеспечиваемым настоящим изобретением. Действительно, минимизация явлений слипания позволяет получать эмульсию, характеризующуюся более однородным распределением капелек.
Жидким компонентам может быть передано одинаковое количество энергии в каждой стадии смешивания или, альтернативно, может передаваться возрастающее количество энергии при переходе от одной стадии смешивания к следующей стадии. Действительно, увеличить энергию, создаваемую в статор-роторном устройстве, можно должным образом, увеличивая окружную скорость ротора или, альтернативно, снижая допуск, существующий между боковой поверхностью ротора и стенками соответствующего статора. Также посредством использования роторных дисков, имеющих разную толщину, можно модифицировать указанный допуск, тем самым увеличивая или уменьшая энергию, создаваемую в стадии смешивания.
Согласно предпочтительному варианту способ по настоящему изобретению включает последовательность из трех стадий смешивания.
Что касается расплавленного аддукта дигалогенид магния-основание Льюиса, то применение MgCl2 в качестве дигалогенида магния является предпочтительным. Основание Льюиса, образующее аддукт с дигалогенидом магния предпочтительно выбирают из группы, состоящей из аминов, спиртов, сложных эфиров, фенолов, простых эфиров, простых полиэфиров и ароматических или алифатических (поли)карбоновых кислот. Среди них особенно предпочтительными являются спирты формулы ROH, в которой R – алкил, содержащий 1-10 атомов углерода.
Особенно предпочтительными расплавленными аддуктами, применяемыми в настоящем изобретении, являются аддукты формулы MgCl2·mROH·nH2O, в которой m=0,1-6,0, n=0-0,7 и R имеет значения, указанные выше. Среди них особенно предпочтительными аддуктами являются те, в которых m=2-4, n=0-0,4 и R – этил.
Другой целью настоящего изобретения является аппарат для непрерывного получения эмульсий, включающий по меньшей мере два статор-роторных устройства, причем каждый статор, за исключением последнего, соединен со следующим статором трубопроводом, идущим от периферийного выхода первого статора к аксиальному входу в последующий статор. Предпочтительно, что начальный участок указанных труб расположен в направлении, по существу тангенциальном к окружности каждого ротора, а конечный участок указанных трубопроводов расположен в направлении, существенно параллельном оси вращения каждого ротора.
Эффективность указанного аппарата в отношении минимизации явлений слипания улучшается, когда трубопроводы, транспортирующие эмульсию от одного статор-роторного устройства к следующему, выполнены в форме спирали.
Каждый ротор обычно перфорируется одним или более маленькими отверстиями, позволяющими жидкостям эмульсии перетекать с одной стороны ротора на другую сторону. Таким образом, используются и подвергаются сдвиговому усилию, создаваемому ротором, оба пространства между боковыми поверхностями каждого ротора и соответствующим статором. Необязательно окружность каждого ротора может быть слабо зарубцована для того, чтобы предотвращать явления слипания в слое жидкости вблизи статора, в котором, более вероятно, происходят явления слипания.
Аксиальный допуск между каждым ротором и соответствующим статором обычно составляет от 0,1 до 2,0 мм, предпочтительно от 0,2 до 1,2 мм. Аксиальный допуск можно определить как расстояние между боковой поверхностью ротора и поверхностью соответствующего статора.
Радиальный допуск, означающий радиальное расстояние между окружностью каждого ротора и соответствующим статором, обычно составляет от 0,2 до 5,0 мм, предпочтительно от 0,5 до 2,0 мм.
Указанные величины аксиального и радиального допусков могут быть легко выбраны простым изменением размеров роторных дисков. Это является преимуществом, обеспечивающим простоту конструкции и эксплуатацию аппарата.
Как указано, аппарат по изобретению включает по меньшей мере два статор-роторных устройства. В предпочтительном варианте изобретения аппарат включает три статор-роторных устройства, а аксиальный допуск между роторным диском и соответствующим статором уменьшается от одной стадии смешивания к следующей.
Схема способа и аппарат по настоящему изобретению представлены с отсылкой к сопроводительным чертежам, которые приведены с иллюстративной целью, не ограничивая объем изобретения.
Фиг.1 представляет способ и аппарат по изобретению, где показана последовательность из трех стадий смешивания.
Фиг.2 представляет вид спереди первого статор-роторного устройства аппарата, показанного в фиг.1.
С отсылкой к фиг.1, поток 1, содержащий расплавленный аддукт дигалогенид магния-основание Льюиса и поток 2, содержащий инертную и несмешивающуюся жидкость, подают в первую стадию смешивания, проводимую в первом статор-роторном устройстве. Аксиальный вход 3 выполнен в статоре 4, так что входящие жидкости принуждаются вращением ротора 5 течь от оси 6 ротора к периферийному ободу ротора. Таким образом, жидкие компоненты текут с большой скоростью внутри ограниченного пространства между статором 4 и боковой поверхностью ротора 5.
Вследствие сильного перемешивания и сдвигового усилия, вызываемых вращением ротора 5, образуется эмульсия вышеуказанных жидкостей. Когда эмульсия достигает периферической области первой стадии смешивания, то она принуждается входить в трубопровод 7, соединяющий периферийный выход 8 из первого статор-роторного устройства с аксиальным входом 9, размещенным в центральной части следующего статор-роторного устройства.
Будучи введенной во второе статор-роторное устройство, эмульсия принуждается вращением второго ротора 10 течь с большой скоростью от оси ротора к периферийному ободу ротора 10. Когда эмульсия достигает периферической области второй стадии смешивания, то она принуждается входить в другой трубопровод 11, соединяющий периферийный выход 12 из второго статор-роторного устройства с аксиальным входом 13 следующего статор-роторного устройства. Эмульсия принуждается вращением ротора 14 течь от оси ротора к периферийному ободу ротора 14 и затем выгружается из третьей стадии смешивания через трубопровод 15.
Фиг.2 показывает вид спереди первого статор-роторного устройства фиг.1.
Аксиальный вход 3 двух несмешивающихся жидкостей выполнен вокруг оси 6 вращения первого ротора 5. Входящие жидкости принуждаются вращением ротора 5 течь от аксиального входа 3 к периферийному ободу ротора 5, как указано радиальным направлением стрелок в фиг.2. Затем образующаяся эмульсия течет с большой скоростью внутри ограниченного объема 20 между периферическим ободом ротора 5 и соответствующим статором 4 и выгружается из первого статор-роторного устройства через периферийный выход 8, который предпочтительно имеет тангенциальное направление к окружности ротора.
Эмульсии, полученные способом по настоящему изобретению, проявляли превосходные свойства в отношении распределения капелек по размеру и морфологических свойств продуктов, полученных охлаждением капелек.
Действительно, наиболее важным применением способа по изобретению является непрерывное получение эмульсий, которые, будучи охлажденными в подходящих условиях, образуют твердые частицы, имеющие более однородное распределение по размеру. Предпочтительный способ охлаждения эмульсий описан в патентной заявке на патент WO 02/051544. Согласно этому патенту, эмульсию, содержащую капельки указанного расплавленного аддукта, охлаждают переносом в охлаждающую баню, которая содержит охлаждающую жидкость, движущуюся внутри трубчатой зоны. Как указано в патенте, отношение Vэ/Vож скорости эмульсии (Vэ), выгруженной из статор-роторного устройства по изобретению, к скорости охлаждающей жидкости (Vож) следует поддерживать в интервале 0,25-4, предпочтительно 0,5-2, для того, чтобы получить лучшие результаты по распределению частиц по размеру.
Отверждение аддукта дигалогенид магния-основание Льюиса, содержащегося в эмульсии в форме капелек, дает твердые частицы, которые, ввиду их узкого распределения по размеру, могут преимущественно быть применены в качестве носителя в приготовлении нанесенных катализаторов полимеризации олефинов.
Действительно, в приготовлении нанесенных катализаторов полимеризации олефинов весьма желательно получать, как можно более узкое распределение частиц носителя по размеру в интервале средних величин, требующихся в этом специальном применении.
Носитель частиц, полученных охлаждением указанной эмульсии, характеризуется средним размером от 4 до 120 мкм.
Распределение частиц по размеру может быть оценено согласно SPAN=(Р90-Р10)/Р50, где на кривой распределения частиц по размеру Р90 – величина диаметра такого, что 90% всех частиц имеет диаметр ниже этой величины, Р10 – величина диаметра такого, что 10% всех частиц имеет диаметр ниже этой величины, и Р50 – величина диаметра такого, что 50% всех частиц имеет диаметр ниже этой величины. Ясно, что низкая величина SPAN предполагает узкое распределение частиц по размеру.
В частном случае, когда аддукт имеет формулу MgCl2·mROH, в которой m=0,1-6 и R представляет собой алкил, содержащий 1-10 атомов углерода, способ по изобретению позволяет получить распределение капелек по размеру согласно формуле (Р90-Р10)/Р50 меньше 1,2, предпочтительно меньше 1,0. Способ по настоящему изобретению обладает большими преимуществами, так как он позволяет выбрать среднюю величину распределения частиц по размеру в широком интервале (4-120 мкм), поддерживая узкое распределение частиц по размеру (SPAN<1,2). Эти результаты показаны в рабочих примерах настоящей заявки на патент и получены без добавления к эмульсии химических соединений, ПАВ и других добавок.
Как указано, эти химические соединения несовместимы с получением твердых каталитических компонентов, так как они могут вызывать радиальное снижение активности конечного катализатора. Получение твердых каталитических компонентов, имеющих, как можно более узкую кривую распределения, снижает также образование мелких фракций во время полимеризации альфа-олефинов. Это особенно важно, поскольку в газофазном процессе полимеризации мелкие фракции ответственны за образование электростатических зарядов внутри реактора полимеризации и могут легко вызывать загрязнение стен реактора. Кроме того, мелкие фракции легко увлекаются газовым потоком, рециркулируемым на низ полимеризационного слоя для охлаждения реактора, а этот рецикл нежелателен.
Следующие примеры должны считаться представительными и не ограничивающими объем изобретения.
Примеры
В примерах 1-3 способ по изобретению проводят согласно варианту, показанному в фиг.1, где применяют три стадии смешивания.
Сравнительный пример 4 проводят в одноступенчатом аппарате, включающем только первое статор-роторное устройство фиг.1 (статор 4 и ротор 5), из которого полученную эмульсию выгружают, не подавая в следующие статор-роторные устройства.
Нижеупомянутые параметры могут быть определены следующим образом: Re=Dvd/з, в которой D – диаметр трубопровода, v – линейная скорость флюида, d – плотность флюида и з – динамическая вязкость флюида.
Окружная скорость равна произведению угловой скорости ротора, умноженной на радиус ротора.
SPAN=(Р90-Р10)/Р50, в которой Р90 – величина диаметра, такого что 90% всех частиц имеет диаметр ниже этой величины, Р10 – величина диаметра, такого что 10% всех частиц имеет диаметр ниже этой величины, и Р50 – величина диаметра, такого что 50% всех частиц имеет диаметр ниже этой величины.
Пример 1
Следующие жидкие компоненты подают при 125°С в аксиальный вход первого статор-роторного устройства: 1) минеральное масло (динамическая вязкость 52 сПуаз при 40°С и плотности 865 кг/м3) в качестве непрерывной фазы эмульсии; и 2) расплавленный аддукт формулы MgCl2·2,7С2Н5ОН в качестве дисперсной фазы эмульсии.
Отношение при подаче (по весу) указанного расплавленного аддукта к указанному минеральному маслу 0,13.
Рабочие условия таковы, что время пребывания внутри каждого статор-роторного устройства поддерживается 0,1 секунды, в то время как окружная скорость роторных дисков 7,0 м/с. ReT внутри трубопроводов, соединяющих стадии смешивания составляет примерно 8200.
Эмульсию, содержащую расплавленный аддукт в качестве дисперсной фазы и указанное минеральное масло в качестве непрерывной фазы, выгружают из выхода третьей стадии смешивания. Охлаждение полученной эмульсии приводит к получению твердых частиц, имеющих средний размер 68 мкм и SPAN=1,0. Следовательно, полученные твердые частицы характеризуются особенно узким распределением по размеру.
Пример 2
Две несмешивающихся жидкости примера 1 подают в аксиальный вход первого статор-роторного устройства с тем же отношением подачи расплавленного аддукта и минерального масла.
Рабочие условия таковы, что время пребывания внутри каждого статор-роторного устройства поддерживается 0,1 секунды, в то время как окружная скорость роторных дисков составляет 56,0 м/с. ReT внутри трубопроводов, соединяющих стадии смешивания, составляет примерно 8400.
Эмульсию, содержащую расплавленный аддукт в качестве дисперсной фазы и указанное минеральное масло в качестве непрерывной фазы, выгружают из выхода третьей стадии смешивания. Охлаждение полученной эмульсии приводит к получению твердых частиц, имеющих средний размер 12 мкм и SPAN=0,9.
Пример 3
Две несмешивающихся жидкости примера 1 подают в аксиальный вход первого статор-роторного устройства при отношении подачи (по весу) расплавленного аддукта к минеральному маслу 0,07.
Рабочие условия таковы, что время пребывания внутри каждого статор-роторного устройства поддерживается 0,1 секунды, в то время как окружная скорость роторных дисков составляет 56,0 м/с. ReT внутри трубопроводов, соединяющих стадии смешивания, составляет примерно 8000.
Эмульсию, содержащую расплавленный аддукт в качестве дисперсной фазы и указанное минеральное масло в качестве непрерывной фазы, выгружают из выхода третьей стадии смешивания. Охлаждение полученной эмульсии приводит к получению твердых частиц, имеющих средний размер 9,5 мкм и SPAN=0,8.
Пример 4 (сравнительный)
Те же две несмешивающихся жидкости предыдущих примеров подают в аксиальный вход одноступенчатого аппарата, включающего только одно статор-роторное устройство. Отношение подачи (по весу) между расплавленным аддуктом и минеральным маслом поддерживается 0,13. Устанавливаются те же рабочие условия, что и в примере 2: время пребывания внутри статор-роторного устройства поддерживается 0,1 секунды, в то время как окружная скорость роторных дисков составляет 56 м/с.
Эмульсию, содержащую расплавленный аддукт в качестве дисперсной фазы и указанное минеральное масло в качестве непрерывной фазы, выгружают из выхода указанного статор-роторного устройства. Охлаждение полученной эмульсии приводит к получению твердых частиц, имеющих средний размер 16 мкм и SPAN=1,4. Как известно специалистам в области твердых носителей катализатора, полученные частицы, следовательно, характеризуются широким распределением по размеру. Таким образом, твердые частицы, полученные в этом сравнительном примере, нуждаются в просеивании перед их использованием в приготовлении нанесенных катализаторов полимеризации олефинов.
Формула изобретения
1. Многостадийный способ непрерывного получения эмульсии, включающий обработку по меньшей мере двух несмешивающихся жидкостей последовательно в по меньшей мере двух стадиях смешивания, осуществляемых в по меньшей мере двух последовательных статор-роторных устройствах, в котором периферийный выход из первого статор-роторного устройства соединен с аксиальным входом в последующее статор-роторное устройство посредством трубопровода, в котором число Рейнольдса ReТ внутри указанного трубопровода выше 5000, начальный участок указанного трубопровода расположен в направлении, по существу, тангенциальном к окружности ротора, и окружная скорость каждого ротора указанных статор-роторных устройств составляет от 5 до 60 м/с.
2. Способ по п.1, в котором указанная эмульсия содержит в качестве дисперсной фазы расплавленный аддукт дигалогенид магния – основание Льюиса.
3. Способ по пп.1 и 2, в котором указанная эмульсия содержит в качестве непрерывной фазы любую жидкость, которая является инертной и несмешивающейся с указанным расплавленным аддуктом дигалогенид магния – основание Льюиса.
4. Способ по п.3, в котором указанную инертную и несмешивающуюся жидкость выбирают из алифатических и ароматических углеводородов, силиконовых масел, жидких полимеров или смесей указанных соединений.
5. Способ по любому из пп.1 и 2, в котором указанный расплавленный аддукт дигалогенид магния – основание Льюиса подают в указанное первое статор-роторное устройство в весовом отношении меньше 0,5 относительно указанной инертной и несмешивающейся жидкости.
6. Способ по п.1, в котором в каждой стадии смешивания время пребывания составляет меньше 1 с.
7. Способ по п.1, в котором окружная скорость каждого роторного диска составляет от 20 до 60 м/с.
8. Способ по п.1, в котором число Рейнольдса ReT внутри указанного трубопровода выше 8000.
9. Способ по п.1, включающий последовательность трех стадий смешивания.
10. Способ по п.2, в котором указанный дигалогенид магния является хлоридом магния.
11. Способ по п.2, в котором указанное основание Льюиса выбирают из аминов, спиртов, сложных эфиров, фенолов, простых эфиров, простых полиэфиров и ароматических или алифатических (поли)карбоновых кислот.
12. Способ по п.11, в котором указанным основанием Льюиса является спирт формулы ROH, в которой R представляет собой алкил, содержащий от 1 до 10 атомов углерода.
13. Способ по п.2, в котором используют расплавленный аддукт формулы MgCl2·mROH·nH2O, в которой m=0,1-6,0, n=0-0,7 и R представляет собой C1-С10-алкил.
14. Способ по п.13, в котором m=2,0-4,0, n=0-0,4 и R представляет собой этил.
РИСУНКИ
|
|