|
(21), (22) Заявка: 2007101684/12, 06.06.2005
(24) Дата начала отсчета срока действия патента:
06.06.2005
(30) Конвенционный приоритет:
21.09.2004 SE 0402296-8
(43) Дата публикации заявки: 10.08.2008
(46) Опубликовано: 10.06.2009
(56) Список документов, цитированных в отчете о поиске:
US 4292122 A, 29.09.1981. US 6361650 B1, 26.03.2002. US 6391153 B1, 18.05.1984. FR 2536097 A1, 18.05.1984. RU 2210650 C2, 20.08.2003.
(85) Дата перевода заявки PCT на национальную фазу:
05.02.2007
(86) Заявка PCT:
SE 2005/000859 20050606
(87) Публикация PCT:
WO 2006/033605 20060330
Адрес для переписки:
191036, Санкт-Петербург, а/я 24, “НЕВИНПАТ”, пат.пов. А.В.Поликарпову
|
(72) Автор(ы):
ВИКДАХЛЬ Леннарт Нильс Андерс (SE), БЕРГСТРЁМ Бернт-Олоф (SE), ШАГАЕВ Олег (SE), НЕВАНДЕР Торе Рольф (SE)
(73) Патентообладатель(и):
НОСС АБ (SE)
|
(54) СПОСОБ И УСТРОЙСТВО ДЛЯ ПРОИЗВОДСТВА ЦЕЛЛЮЛОЗНОЙ ВОЛОКНИСТОЙ МАССЫ
(57) Реферат:
Предназначено для использования в целлюлозно-бумажной промышленности. Способ и устройство, в котором дефибрированную массу сортируют для удаления костры, затем фракционируют в соответствии с удельной поверхностью, предпочтительно устройством, содержащим гидроциклоны. Указанный способ включает технологические стадии, на которых отделяют фракции волокна с более низкой удельной поверхностью, предпочтительно волокна с более толстыми стенками. Указанную целлюлозную волокнистую массу фракционируют по меньшей мере на три фракции, по меньшей мере две из которых объединяют полностью или частично. Одну или несколько фракций волокон с меньшей удельной поверхностью обрабатывают при концентрации массы в интервале 0,8-14%, предпочтительно в интервале 1-5% для разделения, фибриллирования и постоянного сплющивания, предпочтительно устройством, которое содержит измельчающее устройство (5, 5а), такое как дефибрер, рафинер, шаровая мельница или подобное оборудование. Обеспечивается повышение степени обезвоживания и экономия энергии. 2 н. и 24 з.п. ф-лы, 16 ил., 6 табл.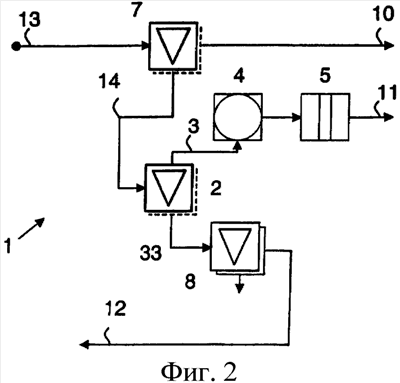
Область техники
Настоящее изобретение относится к способу подготовки волокна и устройству для подготовки волокна при обработке древесных волокон. Одной из целей настоящего изобретения является производство печатных сортов бумаги, содержащих древесину, сортов газетной бумаги и более тонких сортов бумаги (улучшенные сорта бумаги), таких как SC (проклеенной и каландрированной или лощеной на суперкаландре), либо LWC (легковесной с покрытием), предпочтительно из ТММ (термомеханической массы), ХТММ (хемотермомеханической массы) или ЦМ (целлюлозной массы). Это осуществляется со значительным энергосбережением, экономией отбеливающих химикатов и пониженными капитальными затратами на промывное и обезвоживающее оборудование. Другой целью настоящего изобретения является производство ТММ, ХТММ, ЦМ или других видов древесной массы с пониженными затратами энергии и сохранение при этом приемлемого качества волокнистой массы. Другой целью является обработка волокна после любого процесса получения волокнистой массы, например DIP, крафт-целлюлозы или любой другой целлюлозы с помощью модифицированного способа и модифицированного устройства согласно изобретению, тем самым, помимо прочего, экономя энергию и улучшая качество волокнистой массы. Другой целью является повышение степени обезвоживания и осушения волокнистой массы.
Уровень техники
Технология, используемая на сегодняшний день в производстве механической волокнистой массы, такой как ТММ, ХТММ, ЦМ, и для улучшения ее качества, осуществляется с использованием одно- или многостадийного размола в основной технологической линии, в которой энергопотребление является известной проблемой. Затем производят разделение с помощью многостадийной сортировки, в которой отделяют длинноволокнистую фракцию. Эту фракцию обрабатывают посредством простого или многостадийного размола ВК (при высокой концентрации массы) с последующими стадиями сортировки или с промежуточными стадиями сортировки. Возможно отходы после размола ВК можно обрабатывать с помощью размола НК (при низкой концентрации массы).
Усовершенствованный способ, соответствующий вышеизложенному, для повышения качества массы ТММ из газетной бумаги до качества массы для SC/LWC с применением размола НК был известен ранее, см. патент США 6361650 В1. Там описана система, в которой в одном рафинере НК размалывают весь поступающий поток массы, после чего фракционируют поток, а затем обрабатывают фракции. Фракционирование производят исходя из длины волокон с помощью фильтров с щелевидными отверстиями.
Из патента США 4731160 известно применение гидроциклонов для разделения двух фракций, которые отбеливают перекисью водорода (п.п.1 и 2 формулы).
Из патента США 5133832 известно отбеливание длинноволокнистой фракции перекисью водорода (H2O2) и коротковолокнистой фракции дитионитом (Na2S2O4).
Из ЕР 1077281 А1 известно применение размола ВК для обработки волокон (в основном из вторичной волокнистой массы) для получения содержащей древесину бумаги повышенного качества. После размола ВК проводят фракционирование в щелевидных фильтрах и гидроциклонах.
Другими документами, которые могут быть использованы в качестве ссылок, являются WO 03/000982 А1, WO 0120074 А1 и WO 2004/003288 А1.
Недостатки предшествующего уровня техники
Из уровня техники неизвестно, что следует делать, чтобы получить бумагу с хорошими поверхностными свойствами, одновременно экономя энергию и при этом получая бумагу с хорошими прочностными свойствами. Древесную массу, такую как ТММ, можно применять без обработки для получения более высококачественных сортов бумаги, но с более низким выходом и с более высоким потреблением энергии. На сегодняшний день для получения более высококачественных сортов бумаги можно применять более дорогое целлюлозное волокно, например сульфатную целлюлозу, сульфитную целлюлозу или им подобную, которую смешивают с древесной массой для достижения желаемых свойств. Упрочненная целлюлоза имеет очень прочные и длинные волокна. Ни в одном из упомянутых документов не описана система, в которой рассматривается как удельная поверхность (толщина стенки волокна), так и применение размола НК для обработки пригодной фракции с целью улучшения древесной массы для газетной бумаги с применением различных отбеливающих химикатов для различных фракций, разделенных по удельной поверхности, или альтернативно для производства волокнистой массы для газетной бумаги при существенном сокращении расходов на энергию, на отбеливающие химикаты и на оборудование для обезвоживания и промывки.
Из этого можно сделать вывод о том, что в уровне техники не показано четкое разделение по морфологии волокна, дающее возможность избирательной обработки различных фракций в сочетании с эффективной обработкой волокон или фракций волокна, отвечающих за стабильность поверхности (шероховатость) бумаги.
Общее описание изобретения
Для решения вышеупомянутой проблемы предложены следующие способ и устройство.
Способ производства целлюлозной волокнистой массы, в котором дефибрированную массу сортируют для удаления костры, фракционируют по меньшей мере на две фракции (10, 11, 12), предпочтительно по меньшей мере на три, при этом каждую фракцию обрабатывают по отдельности, затем объединяют вместе, полностью или частично, а затем осуществляют фракционирование в зависимости от удельной поверхности, предпочтительно в устройстве (1), содержащем гидроциклоны, при этом способ включает производственные стадии (6, 7), на которых фракционируют волокна, имеющие большую удельную поверхность, предпочтительно тонкостенные волокна, и способ включает производственные стадии (2), на которых фракционируют волокна, имеющие меньшую удельную поверхность, предпочтительно волокна с более толстыми стенками, и при этом одну или несколько фракций (3, 3а) волокон обрабатывают для разделения, фибриллирования и постоянного сплющивания, предпочтительно в устройстве, которое содержит какой-либо размалывающий механизм (5, 5а), такой как рафинер, шаровая мельница или другое подобное оборудование.
В результате обрабатывают только волокна, нуждающиеся в обработке в связи с проблемой поверхностной стабильности бумаги. Дополнительный эффект от сплющивания волокон, нуждающихся в этом, заключается в улучшении поверхностной стабильности бумаги.
Согласно другому варианту способ осуществляют следующим образом.
Способ производства целлюлозной волокнистой массы, в котором дефибрированную массу сортируют для удаления костры, а указанную массу затем подвергают фракционированию, при этом ее фракционирование осуществляют в соответствии с удельной поверхностью, предпочтительно в устройстве (1), содержащем гидроциклоны, отличающийся тем, что способ содержит технологические стадии (7), на которых фракционируют волокна с высокой удельной поверхностью, предпочтительно тонкостенные волокна, и способ содержит технологические стадии (2), на которых фракционируют волокна с меньшей удельной поверхностью, предпочтительно волокна с более толстыми стенками, а указанную массу фракционируют по меньшей мере на три фракции (10, 3, (3а), 12), при этом каждую фракцию обрабатывают по отдельности, а затем объединяют полностью или частично, а одну или несколько волокнистых фракций (3, 3а) обрабатывают для разделения, фибриллирования и постоянного сплющивания предпочтительно в устройстве, которое содержит измельчающее устройство (5, 5а), такое как дефибрер, рафинер, шаровая мельница или другое подобное оборудование.
Согласно варианту осуществления одна или несколько фракций (3, 3а), которые обрабатывают в измельчающем устройстве (5, 5а), содержат волокна с величиной z от 0,3 до 0,8.
Результат заключается в том, что, как указывалось выше, обрабатывают только требующие обработки волокна. Это обеспечивает экономию энергии и/или более высокое качество конечного продукта.
Согласно варианту осуществления измельчающее устройство (5, 5а) может работать так, что волокна в имеющейся фракции постоянно сплющивают благодаря возникновению в стенках волокна трещин, образованных в измельчающем устройстве.
Результат заключается в том, что волокна, подвергающиеся обработке, менее подвержены упругому последействию, и стабильность поверхности конечного продукта улучшается, особенно когда подразумевают повторное увлажнение.
Согласно одному варианту осуществления измельчающее устройство (5, 5а) может включать размол при концентрации массы в интервале 0,8-14%, предпочтительно в интервале 1-5%.
Согласно одному варианту осуществления измельчающее устройство (5, 5а) может включать размол при любой из концентраций 0,8%, 0,9%, 1%, 2%, 3%, 4%, 5%, 6%, 7%, 8%, 9%, 10%, 11%, 12%, 13%, 14%.
Согласно одному варианту осуществления измельчающее устройство (5, 5а) может включать размол при концентрации массы, составляющей 3-8%.
В результате выбора правильного интервала концентрации получают волокно, которое дает постоянно сплющенные волокна без избыточной резки волокна.
Согласно одному варианту осуществления измельчающее устройство (5, 5а) может включать рафинер, работающий при затратах энергии 10-800 кВтч/т, предпочтительно 100-600 кВтч/т, еще предпочтительнее 200-500 кВтч/т.
Результат работы в правильном энергетическом интервале состоит в том, что получение волокна и сплющивание адаптировано к поступающей фракции таким образом, что разделение и фибриллирование дает постоянное сплющивание волокон, подвергающихся в обработке.
Согласно одному из вариантов осуществления изобретения фракция (10), которая содержит волокна с высокой удельной поверхностью, выходит из базы гидроциклонной стадии.
Результат применения гидроциклонов заключается в том, что волокна разделяют по удельной поверхности, и из одной и той же фракции можно получить волокна различной длины.
Согласно одному из вариантов осуществления изобретения фракция с меньшей удельной поверхностью (3, 3а) и более толстостенные волокна, которые прошли обработку, выходят из базы гидроциклонной стадии.
Согласно одному из вариантов осуществления изобретения фракцию (10), обогащенную мелочью и содержащую волокна с высокой удельной поверхностью, отбеливают в нещелочных условиях.
Результатом этого является то, что отбеливание можно адаптировать к интересующей фракции. Нещелочные условия отбеливания менее чувствительны к влиянию примесей во фракции (10), указанные примеси могут, например, содержать ионы металлов. Кроме того, нещелочное отбеливание можно осуществить с меньшими затратами.
Согласно одному из вариантов осуществления изобретения фракцию (10) отбеливают при значении рН ниже 9.
Согласно одному из вариантов осуществления изобретения фракцию (10) отбеливают восстанавливающим отбеливателем.
Согласно одному из вариантов осуществления изобретения фракцию (10) отбеливают отбеливателем, содержащим дитионит.
Результат применения дитионита заключается в том, что отбеливание производят с меньшими затратами, и в том, что дитионит менее чувствителен к распаду до того, как он может отбеливать волокна.
Согласно одному из вариантов осуществления изобретения фракцию (3, 3а) с волокнами с меньшей удельной поверхностью отбеливают окислительным отбеливанием.
Результатом применения окислительного отбеливания во фракции (3, 3а) с меньшей удельной поверхностью является то, что эта или эти фракции имеют намного меньше примесей, обсуждавшихся ранее, которые имеют тенденцию к разрушению окислительных отбеливателей. Окислительные отбеливатели более действенны, и поэтому отбеливание этой фракции (3, 3а) отбеливателями этого типа лучше с точки зрения белизны волокнистой массы.
Согласно одному из вариантов осуществления изобретения фракцию (3, 3а) отбеливают отбеливателем, содержащим перекись водорода.
Согласно одному из вариантов осуществления изобретения фракцию (3, 3а) отбеливают отбеливателем, содержащим озон.
Согласно одному из вариантов осуществления изобретения фракцию (12), которая остается после предыдущих технологических стадий и которая имеет наименьшую удельную поверхность, очищают от песка, коры и других примесей и обрабатывают, предпочтительно в устройстве (15) для отшелушивания волоконных стенок волокон этой фракции (12), при этом устройство содержит какое-либо измельчающее устройство, такое как рафинер или ему подобное, и фракцию после обработки полностью или частично возвращают обратно, предпочтительно обратным ходом, в технологический процесс.
Согласно одному из вариантов осуществления изобретения устройство (15) осуществляет размол при концентрации >15%, предпочтительнее при концентрации >14%.
Результат заключается в том, что проводят очистку массы для удаления нежелательных частиц и примесей из конечного продукта. В этой фракции остаются волокна, которые после обработки можно использовать в конечной массе. Благодаря извлечению этих волокон повышается выход волокна.
Согласно одному из вариантов осуществления изобретения поток волокна с пониженной удельной поверхностью (3, 3а), предпочтительно с более толстыми стенками, после обработки полностью или частично смешивают с потоком (10) волокон и мелочи с высокой удельной поверхностью для улучшения обезвоживающих свойств.
Результатом частичного или полного смешивания фракции (3, 3а) с фракцией (10) является то, что будет легче извлекать воду. Фракция 10 обогащена волокнами и мелочью с низкой удельной поверхностью, эту фракцию трудно обезвоживать, поскольку она имеет тенденцию к забиванию фильтра и другого обезвоживающего оборудования, и даже если она не забивает оборудование, то процесс обезвоживания замедляется. При смешивании с фракцией 10, содержащей волокна с меньшей удельной поверхностью, которые легче обезвоживать, суммарная фракция также приобретет улучшенные свойства обезвоживания.
Согласно одному из вариантов осуществления изобретения поток волокна с пониженной удельной поверхностью (3, 3а), предпочтительно волокна с более толстыми стенками, обезвоживают отдельно до более высокой концентрации, чем конечная желательная концентрация смеси фракций, с тем чтобы для фракции с волокнами с высокой удельной поверхностью (10), предпочтительно с тонкостенными волокнами и мелочью, требовалось только частичное обезвоживание или не требовалось никакого.
Как упоминалось выше, фракцию (3, 3а) легче обезвоживать. Это происходит благодаря меньшему содержанию в этой фракции мелочи, а также различным свойствам волокон с меньшей удельной поверхностью, содержащихся в этой фракции. Путем сгущающего обезвоживания этой фракции (3, 3а) вместо попытки обезвоживания обогащенной мелочью фракции (10) можно обеспечить более оптимизированное использование обезвоживающего оборудования, что происходит, помимо прочего, благодаря уменьшению тенденции к забивке обезвоживающего оборудования. Все это дает возможность уменьшить капиталовложения в данный тип оборудования.
Согласно одному из вариантов осуществления изобретения фракции (10, 11, 11а), содержащие волокна с высокой и более низкой удельной поверхностью, после обработки подают в поток (32) волокнистой массы вместе с массой, которая была получена при более низком расходе энергии и отбеливателей, чем на традиционном комбинате для производства целлюлозы, содержащей древесную массу, для печатных бумаг, целлюлозы для газетной бумаги, целлюлозы SC, LWC, SC A++ и других видов целлюлозы.
Обрабатывая различные фракции волокнистой массы разными способами, обеспечивают более оптимизированное использование волокнистого сырья.
Результат обработки вышеописанным способом состоит в том, что проведенная обработка волокна облегчает обезвоживание потока 32 на бумагоделательной машине.
Дополнительно для решения обсуждаемой проблемы предложено устройство.
Устройство для обработки волокнистой целлюлозной массы для придания улучшенных свойств, таких как светорассеяние, коэффициент растяжения, показатель разрыва, шероховатость поверхности, расход отбеливающих веществ, энергопотребление, содержащее первую гидроциклонную установку (7), вторую гидроциклонную установку (2), рафинер (5) и передающие устройства между ними, отличающееся тем, что волокнистую целлюлозную массу подают в первую гидроциклонную установку (7), отделяющую базовую фракцию (10) и фракцию (14) из нижнего сливного отверстия гидроциклона, из которой через другую гидроциклонную установку (2) отделяют базовую фракцию (3), которая после обезвоживания поступает на дополнительную обработку в устройстве (5), содержащем рафинер, при этом обработку выполняют при концентрации в пределах 1-14%.
Результат применения гидроциклонов при разделении в устройстве для обработки волокнистой массы состоит в том, что морфология волокна является важным фактором, определяющим, какие волокна будут отделены от остальных. Это означает, что длина волокна не является тем фактором, на котором основано фракционирование, как при применении сортировок. Это означает, что устройство может отделять волокна, требуемые для обработки.
Согласно одному из вариантов осуществления устройства базовую фракцию (10) отбеливают нещелочным восстанавливающим отбеливателем.
Результатом этого является то, что отбеливание можно адаптировать к соответствующей фракции. Условия нещелочного отбеливания менее чувствительны к влиянию примесей во фракции (10), указанные примеси могут содержать, например, ионы металлов. Кроме того, нещелочное отбеливание можно проводить с меньшими затратами.
Согласно одному из вариантов осуществления устройства вторую базовую фракцию (11) отбеливают окислительным отбеливателем.
Результат применения окислительного отбеливания фракции (3, 3а) с меньшей удельной поверхностью состоит в том, что эта фракция или эти фракции имеют намного меньше примесей, рассмотренных выше, которые имеют тенденцию к разложению окислительных отбеливателей, окислительные отбеливатели более эффективны, и поэтому отбеливание этой фракции (3, 3а) этими типами отбеливателей лучше с точки зрения белизны.
Согласно одному из вариантов осуществления устройства верхнюю фракцию (33) направляют в гидроциклонную установку и разделяют на базовую фракцию (3а) и фракцию (33а) из нижнего сливного отверстия гидроциклона, при этом указанную базовую фракцию (3а) после обезвоживания обрабатывают в рафинере (5а) при концентрации в пределах 1-14%.
Согласно одному из вариантов осуществления устройства базовую фракцию (3а, 11а) отбеливают окислительным отбеливателем.
Согласно одному из вариантов осуществления устройства обработанные базовые фракции (10, 11 и/или 11а) объединяют в общий поток (32) волокнистой массы с улучшенными свойствами.
Результатом такой обработки в устройстве является то, что проведенная подготовка волокон облегчает обезвоживание потока (32) на бумагоделательной машине.
Согласно одному из вариантов осуществления устройства фракцию (33, 33а) из нижнего сливного отверстия гидроциклона продолжают очищать в гидроциклонах (8), удаляющих тяжелые примеси, такие как песок, кора и другие тяжелые загрязнения, остающиеся во фракции (12) из нижнего сливного отверстия гидроциклона.
Согласно одному из вариантов осуществления устройства базовую фракцию продолжают очищать, в том числе путем рафинирования (15), при концентрации >5%, и эту фракцию затем возвращают в поступающий поток массы, подаваемый на вход устройства.
Предложен другой вариант осуществления способа получения и обезвоживания целлюлозной массы, в котором дефибрированную целлюлозу сортируют для удаления костры, фракционируют по меньшей мере на три фракции (10, 3, (3а), 12), при этом фракционирование выполняют в соответствии с удельной поверхностью, предпочтительно в устройстве (1), содержащем гидроциклоны, отличающийся тем, что указанную волокнистую массу фракционируют по меньшей мере на три фракции (10, 3, 12), при этом способ включает технологические стадии (7), на которых фракционируют волокна с высокой удельной поверхностью, предпочтительно тонкостенные волокна, и способ включает технологические стадии (2), на которых фракционируют волокна, имеющие меньшую удельную поверхность, предпочтительно волокна с более толстыми стенками, при этом фракцию, имеющую меньшую удельную поверхность, обезвоживают в устройстве (5) до заданной концентрации, и эту фракцию (3, 3а) затем смешивают по меньшей мере частично по меньшей мере с одной другой фракцией (10) перед тем, как смешанный поток подают на следующую технологическую стадию.
Результат заключается в том, что волокна, которые легче всего обезвоживать, можно обезводить, а затем смешать с фракцией, которую труднее обезводить, при этом сумма фракций является обезвоженной волокнистой массой.
Предложен еще один вариант осуществления способа, в котором дефибрирование выполняют с помощью размола в одну или несколько стадий. Волокнистую массу сортируют для удаления более крупных частиц. Поступающий поток волокнистой массы затем подают на фракционирование по удельной поверхности, которое в случае волокон означает фракционирование по толщине стенок. Частицы, имеющие самую высокую удельную поверхность, отделяют первыми. В этой фракции находятся тонкостенные волокна и мелкие частицы, так называемая мелочь. Этой фракции не требуется последующая обработка в отношении упругости волокон (стабильности поверхности), повышения прочности, улучшения свойств шероховатости поверхности (повышенная гладкость) и так далее, но ее можно направлять в процесс. Эту фракцию отбеливают нещелочным отбеливателем, таким как дитионит. Оставшийся поток волокнистой массы фракционируют еще раз по удельной поверхности, при этом волокна с меньшей удельной поверхностью отделяют от волокон, имеющих самые толстые стенки и наименьшую удельную поверхность. Эта фракция затем идет на обработку в рафинере НК (низкой концентрации) или СК (средней концентрации) для создания трещин в стенках волокон, фибрилляции волокон и разрушения волокон без значительного нарушения длины волокон, т.е. не производя заметного снижения длины волокон. Это предотвращает, помимо прочего, упругость (пружинистость) волокна в конечном продукте. Затем эту фракцию отбеливают окислительным отбеливателем на отбельной стадии. Оставшуюся фракцию с меньшей удельной поверхностью очищают в гидроциклонах, например в каскаде гидроциклонов, для удаления примесей, таких как песок, кора и прочие тяжелые примеси. Оставшиеся волокна с толстыми стенками продолжают обрабатывать, например, в рафинере ВК (высокой концентрации) и возвращают обратно или обратным ходом в процесс.
Определения
Существует распространенное группирование волокон на раннюю древесину, летнюю древесину и позднюю древесину. В данном документе согласно фиг.1 произведено группирование по четырем типам волокон. Различия между этими типами волокон в основном заключаются в толщине стенок и зависящих от нее свойствах, т.е. шероховатости поверхности, показателе растяжения, пружинных свойствах волокна, вызываемых влагой и т.п. Четыре типа волокон, описанные в этой заявке, характеризуются величиной z согласно таблице 1 и имеют аббревиатуры РРД, ПРД, РПД и ППД, что означает раннюю раннюю древесину, позднюю раннюю древесину, раннюю позднюю древесину и позднюю позднюю древесину. Эти типы волокон отличаются удельной поверхностью, и на основе определения их можно описать по величине z, см. табл.1. Величину z рассчитывают следующим образом.
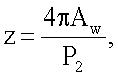
где Aw – площадь поперечного сечения волокна,
Р – окружность волокна.
В волокнах для бумажной промышленности проблемы возникают тогда, когда волокна с величиной z между 0,3 и 0,8 при повторном увлажнении бумаги, например во время печати, приподнимаются и создают грубую поверхность, даже несмотря на каландрирование бумаги и хорошие поверхностные свойства перед повторным увлажнением.
В данном описании обсуждают размол при различных концентрациях. Определение низкой, средней и высокой концентрации во время рафинирования можно видеть из следующей таблицы.
Таблица 2 |
Рафинирование |
НК (низкая) |
СК (средняя) |
ВК (высокая) |
Концентрация (мас.%) |
<5% |
5-14% |
>14% |
Ниже в примере 2 упомянута величина Rm, ее определением является отношение между потоком на входе и потоком из нижнего сливного отверстия гидроциклона (поток отходов).
Фиг.1 иллюстрирует различные типы волокон, которые фракционируют и обрабатывают в способе по изобретению.
Фиг.2 иллюстрирует основную часть системы по изобретению.
Фиг.3 иллюстрирует вариант осуществления основной части системы по изобретению.
Фиг.4 иллюстрирует вариант осуществления основной части системы по изобретению.
Фиг.5 иллюстрирует вариант осуществления основной части системы по изобретению.
Фиг.6 иллюстрирует вариант осуществления основной части системы по изобретению.
Фиг.7 иллюстрирует вариант осуществления основной части системы по изобретению.
Фиг.8 иллюстрирует экспериментальную установку по примеру 1.
Фиг.9 иллюстрирует экспериментальную установку по примеру 2.
Фиг.10 иллюстрирует результаты из примера 2.
Фиг.11 иллюстрирует результаты из примера 2.
Фиг.12 иллюстрирует результаты из примера 2.
Фиг.13 иллюстрирует результаты из примера 2
Фиг.14 иллюстрирует результаты из примера 2
Фиг.15 иллюстрирует результаты из примера 2
Фиг.16 иллюстрирует вариант осуществления изобретения по п.28.
Описание вариантов осуществления
Согласно одному из вариантов осуществления изобретения, считающемуся наилучшим способом осуществления изобретения, проиллюстрированным на фиг.2, волокнистая масса идет в потоке 13 на гидроциклонную стадию 7 с фракционирующими гидроциклонами, где поступающий поток разделяют на два потока 10 и 14. Поток 10 содержит волокна с величиной z между 0 и 0,3 (РРД) и мелочь. Поток 14 содержит волокна с величиной z больше 0,3 (ПРД, РПД, ППД). Этот поток направляют на гидроциклонную стадию 2 с фракционирующими гидроциклонами, которые разделяют поток 14 на два потока 3 и 33. Поток 3 содержит волокна с величиной z между 0,3 и 0,8 (ПРД, РПД).
Поток 3 направляют на обезвоживание 4 и на обработку в рафинер 5 с НК или СК размолом. В потоке 11, который выходит после размола 5, находятся фибриллированные, разделенные и раздавленные волокна. Поток 33 содержит волокна с величиной z больше 0,8 (ППД) и тяжелые примеси, поток 33 направляют на очистку в циклонном каскаде 8, оптимизированном для очистки от песка, коры и других тяжелых примесей. Примеси выводят из процесса, а поток 12 направляют на другие виды обработки. Потоки 10 и 11 направляют на подходящую обработку, такую как обезвоживание, комплексное связывание металлов, отбеливание и т.п. Размолом базовой фракции 3 с гидроциклонной стадии 2 можно перерабатывать волокна, которые создают самую большую проблему для поверхностных свойств конечной бумажной продукции и, концентрируясь на этом потоке, можно сэкономить энергию по сравнению с размолом всего поступающего потока 13 волокна.
Более того, потоки 10, 11 и 12 можно обрабатывать по отдельности подходящим образом, чтобы получить оптимизированный конечный продукт.
Согласно второму варианту осуществления изобретения, который можно видеть на фиг.3, поступающую волокнистую массу 13 разделяют на потоки 10, 11, 11а и 12. В этом случае поток 10 содержит волокна с величиной z меньше 0,3 (РРД) и мелочь. Поток 11 содержит волокна с величиной z между 0,3 и 0,6 (ПРД), которые прошли обработку в рафинере (концентрации СК и НК), а поток 11а содержит волокна с величиной z между 0,6 и 0,8 (РПД), которые прошли обработку в рафинере (концентрации СК и НК). В таком случае условия размола в 5 и 5а можно еще точнее регулировать и можно, например, регулировать концентрацию и энергию размола таким образом, чтобы энергия была еще больше оптимизирована.
Согласно одному варианту осуществления изобретения для всего процесса, показанному на фиг.7, предварительно нагретую щепу промывают и дефибрируют в двух рафинерных стадиях (каждая стадия может содержать несколько параллельных рафинеров или более чем две стадии). Волокнистую массу разбавляют водой до концентрации 3-4% и подают в бак для выдержки, в котором волокна оставляют для восстановления их формы после процесса размола. Затем волокнистую массу с концентрацией 1-3% закачивают через сортировки, выполненные с прорезями или отверстиями, для удаления костры и более крупных примесей. Отбракованный поток из сортировок подают в бракомолку, например, с помощью передающего устройства (не показано) в поток 12, или непосредственно в устройство (23, 24, 15, 25, 26) в системе размола брака. Если имеются химикаты или другие вещества, такие как комплексные связующие, которые требуется смыть, волокнистую массу промывают в промывателе 22, а волокнистую массу 13, которая завершила процесс дефибрирования, направляют в процесс 1 по изобретению.
На гидроциклонной стадии 7 поток 10 отделяют от волокон с величиной z меньше 0,3 (РРД) согласно фиг.1 с помощью гидроциклонов традиционного типа, например Noss AM 80F или других гидроциклонов подходящего типа. Можно представить и некоторые другие типы оборудования, производящего разделение по удельной поверхности. Волокна с величиной z меньше 0,3 вместе с мелочью составляют поток 10 волокнистой массы. В такой компоновке показан двухстадийный каскад (6 вторая стадия в каскаде) и рециркуляция, но здесь можно представить несколько вариантов. Волокна с величиной z меньше 0,3 и мелочь выходят из базы гидроциклонов 6, 7. В потоке 14 волокнистой массы содержатся волокна с величиной z больше 0,3 (ПРД, РПД, ППД). В следующей последовательности поток направляют на новую гидроциклонную стадию 2. Базовая фракция 3 из нее содержит волокна с величиной z между 0,3 и 0,8 (ПРД, РПД). Это те типы волокон, которые, в частности, вызывают пружинистость волокна в готовой продукции, которая, в свою очередь, вызывает проблемы, например, с шероховатостью. Поток 3 идет на обработку, предпочтительно НК-размол (1-5%), в качестве альтернативной обработки может быть шаровая мельница, другие устройства размола СК (5-14%) или мельницы разного типа, и обработку выполняют для создания трещин в стенках волокна, фибрилляции волокна и постоянного раздавливания волокна без значительного нарушения длины волокна. Нижнюю фракцию из сливного отверстия гидроциклонной стадии 2 направляют в гидроциклонный каскад 8 для очистки ее от тяжелых примесей, таких как песок, кора и прочие тяжелые примеси, они выходят из конусов гидроциклонов и покидают процесс. Поток 12 из базовой части этих гидроциклонов содержит волокна с величиной z более 0,8 (ППД) с очень толстыми стенками. Стенки таких волокон невозможно легко разбить НК-размолом 5, поэтому их направляют на отшелушивание стенок волокна, предпочтительно с помощью ВК-размола или другой отшелушивающей обработки, и таким образом стенки волокна становятся тоньше, потом эти обработанные волокна возвращают в процесс для еще одного пропускания в систему 1 по изобретению. Поток 10 направляют на отбеливающую стадию 17, на которой можно отбеливать отбеливателем, который допускает присутствие мелочи и мелких частиц, предпочтительно отбеливателем, который используют в нещелочных условиях (рН ниже 9), таким как дитионит, например дитионит натрия, дитионит цинка или подобным. Поток 11, который состоит из волокон с величиной z от 0,3 до 0,8 (ПРД, РПД) направляют после добавления комплексных связующих на промывку 27 и отбеливание 16, предпочтительно перекисью водорода, озоном или другими подходящими окислительными отбеливателями. Окисление различных фракций разными отбеливателями позволяет сэкономить отбеливатели, и не потребуется так много промывок. Окислительные отбеливатели чувствительны, например, к тяжелым металлам (например, Mn, Cr, Fe), которые поступают с мелочью, но в способе по изобретению большая часть мелочи находится в потоке 10 и никогда не попадает в больших количествах на стадию отбеливания, где используют окислительные отбеливатели. После дополнительной промывки 28 и 29 волокна направляют на обезвоживание в дисковый фильтр 30. Волокна после этого возвращают и смешивают с волокнами в потоке 10. В случае обезвоживания этой фракции 11 на дисковом фильтре 30 до концентрации выше, чем требуется, фракция 10 может быть более разбавленной, что обеспечивает более легкое обезвоживание волокнистой массы в целом. Фракцию 10 трудно обезвоживать из-за большого содержания мелочи. Если необходимо обезвоживать саму фракцию 10, то перемешиванием части фракции 11 с фракцией 10 можно получить волокнистую массу, которую будет легче обезвоживать. Волокнистую массу направляют на обработку и на бумагоделательную машину для производства облагороженных сортов бумаги, таких как SC, LWC, SC-A++ и им подобных.
Систему согласно изобретению можно компоновать несколькими способами. Сущность изобретения заключается в компоновке фракционирования, которое предпочтительно происходит в гидроциклонах, но может быть осуществлено на другом оборудовании, которое может фракционировать по удельной поверхности. На фиг.2, 3, 4, 5 и 6 можно увидеть различные варианты компоновки. Фиг.2 иллюстрирует укрупненную систему, на которой видно, что возможно использование каскада на первой и/или на второй гидроциклонной стадии. Пунктирная линия показывает, что при необходимости возможен каскад. Фиг.4-6 подробно иллюстрирует часть, показанную на фиг.2. Фиг.4 иллюстрирует одинарную стадию как на первой стадии 7, так и на второй стадии 2. Фиг.5 иллюстрирует систему с одинарной стадией на первой стадии 7 и каскадом на второй стадии 2. Фиг.6 иллюстрирует наличие гидроциклонных каскадов как на первой стадии 7, так и на второй стадии 2.
В другом варианте осуществления рафинер 5 исключают, а технология с гидроциклонными стадиями (7, 2 (2а), 8) остается такой же, вместо обработки волокна после второго гидроциклона в рафинере, при этом достигается преимущество в виде облегченного обезвоживания базовой фракции, выходящей из этой стадии. Достигают более эффективного использования дискового фильтра (4, 4а), см. фиг.16. Как уже упоминалось ранее, пунктирная линия означает, что возможно использование каскадов.
Пример 1
Пробу термомеханической древесной массы из мягкой древесины взяли с комбината, который производит газетную бумагу. Пробу взяли со второй стадии рафинера. После этого волокнистую массу обработали с выдержкой при температуре 90°С в течение 3 часов, а затем переработали в новой системе. Расход и различные фракции волокна представлены в таблице 3 и на фиг.8.
Таблица 3 |
Поток |
m1 |
m2 |
m3 |
m4 |
m5 |
m6 |
m7 |
Общий массовый расход (%) |
100 |
22 |
78 |
30 |
48 |
34 |
14 |
Массовый расход, фракционирование (%) |
– |
– |
100 |
39 |
61 |
43 |
18 |
R100 массовый расход, фракционирование (%) |
– |
– |
100 |
27 |
75 |
52 |
23 |
Р100 массовый расход (%) |
100 |
12 |
90 |
53 |
35 |
24 |
8 |
Коэффициент отбраковки 22% в двухстадийной щелевой сортировке с шириной прорезей, равной 0,15 мм, выбрали с целью сокращения содержания костры Соммервиль до уровня ниже 0,1% в массе, которую подавали на фракционирование. Массу с низким содержанием костры Соммервиль фракционировали в двух стадиях в гидроциклонах (Noss AM 80F), включающих первую стадию, состоящую из двухстадийного каскада, и вторую стадию (одностадийные гидроциклоны). Такая компоновка позволяет производить три фракции волокон с различным качеством массы исходя из морфологии волокна (т.е. поперечные размеры волокна, удельная поверхность).
База 1 (m4) – отсортированная масса из каскада первой стадии, обогащенная волокном с величиной z меньше 0,3 (РРД), и мелочь.
База 2 (m8) – отсортированная масса со второй стадии фракционирования, обогащенная волокном с величиной z между 0,3 и 0,8 (ПРД и РПД).
Верх 3 (m7) – брак со второй стадии фракционирования, содержащей волокна с величиной z больше 0,8 (ППД) – толстостенные волокна.
Базу 2 (m8) далее размалывали в НК-рафинере (12” Andritz) при трех различных уровнях энергии – 215, 417 и 504 кВт·ч/т. Общие затраты энергии для различных видов волокнистых масс соответствуют 73, 142 и 171 кВт·ч/т для массы, рассматриваемой в целом. Полученные размолотую и неразмолотую массы испытывали по отдельности. Кроме того, смеси волокнистой массы приготовили из Базы 1 и Базы 2 в соответствии с соотношением расходов массы в системе – 47:53% (bl1, bl2, bl3). Были подготовлены и испытаны листы бумаги, выполненные из разных фракций массы и смесей. На некоторых образцах массы проводили динамические испытания на обезвоживание, а также испытания на придание шероховатости поверхности.
Базу 1 (m4) и Базу 2(m8) и их смеси отбеливали с использованием дитионита и щелочного пероксида (щелок и перекись водорода) в различных последовательностях.
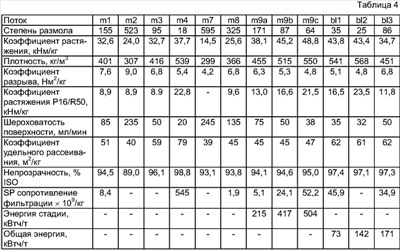
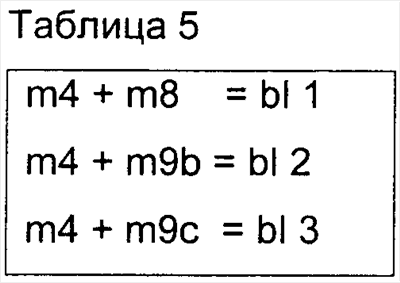
Физические свойства массы различных фракций массы и их смесей показаны в таблице 4 и таблице 5. Как можно увидеть, НК размол фракции База 2 улучшает прочность массы и гладкость листа при низких общих затратах на энергию размола. Следовательно, смеси, полученные из смесей из Базы 1 (m4) и размолотой Базы 2 (m9 b-c), имеют лучшие качества по сравнению со смесями, приготовленными из смесей из Базы 1 (m4) и неразмолотой Базы 2 (m8). Это сопровождается относительно умеренным повышением сопротивления массы обезвоживанию по сравнению с тем, что ожидалось при ВК-размоле этой фракции до такой же степени размола.
Как было измерено по относительному изменению толщины листа и шероховатости поверхности, изменение шероховатости, обусловленное действием влаги на волокно, было на 50% ниже, чем в листах, изготовленных из R100 Bauer-McNett, полученной из смеси 2, по сравнению с листами, изготовленными из волокон, полученных из смеси 1.
Кроме того, размол НК улучшил способность к связыванию в длинных волокнах Базы 2 до уровня Базы 1, как было проверено по прочности на разрыв фракции P16/R50 Bauer-McNett. Это вылилось в относительно высокую способность к связыванию у длинных волокон смеси 2 и 3.
Отбеливание волокнистой массы по примеру 1
Перед отбеливанием все виды волокнистой массы прошли обработку на стадии связывания в комплекс Q-DTPA.
Базу 2 отбеливали перекисью водорода и смешивали с неотбеленной Базой 1, а смесь затем отбеливали дитионитом.
Неотбеленную смесь Базы 1 и Базы 2 (смесь 1) отбеливали перекисью водорода в одну стадию.
Пример 2
После выдержки волокнистую массу со второй стадии размола из комбината, производящего ТММ для газетной бумаги, сортировали при заданном количестве брака для удаления костры и фракционировали в двухстадийной каскадной гидроциклонной системе. Процент отбраковки выбирали таким образом, чтобы 25% волокнистого материала (25% фракции волокон R100 Bauer-McNett подаваемой массы) оставалось в базовой фракции, База 1 (s6).
Фракцию Апекс 1 (s4) из нижнего сливного отверстия гидроциклона далее фракционировали в гидроциклонной системе с получением фракции База 2 (s7), содержащей 25% волокнистого материала (в процентах к начальной загрузке в гидроциклон) и Апекс 2 (s5). Подобным образом фракционировали Апекс 2 (s5) с получением Базы 3 (s8), содержащей 25% волокнистого материала, и Апекс 3 (s9), содержащей по меньшей мере 25% волокнистого материала в соответствии с вышеизложенным.
Полученные фракции Базы 1, 2 и 3 использовали в последующих экспериментах. Базы 2 и 3 размалывали при 300 кВт·ч/т в НК-рафинере, и массы обрабатывали таким же образом, как и неразмолотые образцы.
Базы 2, 3 разделили на две части, из которых одну часть направили на НК-рафинирование при 300 кВт·ч/т, а одну часть не размалывали. Неразмолотую часть, содержащую Базу 1 и неразмолотую часть, подвергли промывке и флотации для удаления мелочи (т.е. фракцию Р100 удалили с помощью фракционатора Bauer-McNett). Волокнистую фракцию смешали с 40 мас.% мелочи, полученной со второй стадии размола на комбинате по производству ТММ массы. Были изготовлены два комплекта бумаги ручной отливки с базовой массой 60 г/м2. Первый комплект подвергли испытанию согласно стандартам SCAN.
Второй комплект листов ручной отливки разрезали на полоски, каландрировали и использовали в экспериментах по торшонированию. После каландрирования полоски по случайному выбору разделили на две группы. Первую группу подвергли испытаниям на разрывную прочность, плотность, пористость, шероховатость поверхности и рассеяние. Вторую группу каландрированных полосок подвергли выдерживанию при 100% влажности и температуре 25°С в течение 3 часов и после этого их подвергли такому же испытанию, как и первую группу.
На Фиг.3 представлена иллюстрация комплекта по примеру 2. В таблице 5 можно изучить соответствующие зависимости от расхода. К Р100 добавили фракцию мелочи и проверили ее распределение. R100 является волокнистой фракцией. Интересно отметить, что База 1 (s6) содержит приблизительно 60% мелочи Р100 в подаваемом потоке волокнистой массы (s1).
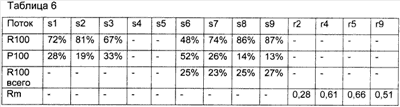
На Фиг.10 показано, как изменяется коэффициент растяжения в различных фракциях. Способность к связыванию заметно снижается в различных гидроциклонных стадиях, а в последней фракции Апекс 3 (s9) из нижнего сливного отверстия гидроциклона способность волокон к связыванию очень ограничена.
На Фиг.11 можно увидеть зависимость прочности на разрыв от степени размола. Как видно, База 1 (S6) имеет прочность, как у базовой фракции База 2 (s7), но они имеют различную степень размола. Это можно объяснить существенной разницей в содержании мелочи между Базой 1 (s6) и Базой 2 (s7), см. таблицу 5.
НК-размол базовой фракции База 2 (s7) и базовой фракции База 3 (s8) увеличивает их прочность. НК-размол снижает степень размола волокнистой массы до некоторой степени, но количество производимой мелочи не соответствует уклону регрессии зависимости степень размола – количество мелочи. НК-размолом волокна обработаны без соответствующего производства мелочи.
Шероховатость поверхности в Базе 3 (s8) – длинноволокнистой фракции (P16/R50 мл/мин) существенно снизилась после НК-размола, в то время как способность к связыванию выросла до такого же уровня, как у длинноволокнистой фракции из Базы 2 (s2), см. фиг.12. Длинноволокнистая фракция Базы 2 (s7) увеличила способность к связыванию до такого же уровня, как База 1 (s6) после НК-рафинирования, без существенного изменения шероховатости.
Подобные тенденции в улучшении шероховатости поверхности и прочности наблюдали при производстве листов ручной отливки из смеси цельной массы из Базы 2 и Базы 3 (Фиг.14). Листы, полученные из Базы 1 (s6), размолотой Базы 2 (s7) и размолотой Базы 3 (s8), которые представлены на Фиг.12, 13 и 14 в виде смеси s6 + raf s7 + raf s8, смешанные согласно общему содержанию брака, см. табл.5, показали значение шероховатости, близкое Базе 1 (s6). Степень размола смеси составила 55 мл по канадскому стандарту CSF.
Фракции Базы 2 и Базы 3 показали высокую тенденцию к повышению шероховатости поверхности по сравнению с Базой 1, выразившуюся в относительном изменении толщины листа и шероховатости поверхности после повторного смачивания (Фиг.14-15).
Склонность волокон к повышению шероховатости поверхности существенно снизилась после НК-размола (Фиг.14 и 15). После повторного увлажнения изменились толщина и шероховатость поверхности каландрированных листов, полученных из неразмолотой фракции волокна Базы 2 R100 и мелочи термомеханической массы, соответственно на 7,5% и 75%. Для сравнения, толщина и шероховатость поверхности каландрированных листов, выполненных из размолотой Базы 2 и мелочи термомеханической массы, изменились на 1,6 и 4,4% соответственно. Неразмолотая База 3 дала соответственно 10 и 55%, а для соответствующей размолотой Базы 3 изменение составило соответственно 1 и 11% (Фиг.15). Относительное изменение свойств смоченных листов было рассчитано исходя из толщины и шероховатости несмоченных листов, содержащих неразмолотую базовую фракцию.
Из вышеизложенного следует понимать, что циклонные стадии согласно изобретению модифицированы в соответствии с имеющимся волокном, подвергаемым обработке. Следует, например, понимать, что специалист в данной области может установить так называемые разомкнутые или открытые каскады везде или в избранные места в системе 1. Особенно следует отметить, что проиллюстрированное на чертежах представляет собой только варианты осуществления идеи изобретения, а количество применяемых циклонов и их физические данные зависят от адаптации конструкции системы к таким волокнам, для обработки которых ее создают. То же самое относится и к концентрациям, которые имеются в рафинерах согласно изобретению, и к падению давления в гидроциклонных стадиях.
Даже если данный документ можно было бы рассматривать в отношении волокон из одного типа древесины, изобретение в соответствии с тем, как заявлено в формуле, не следует интерпретировать таким образом. Смешанные волокна из различных образцов древесины также можно обрабатывать в системе согласно изобретению, а разделение осуществляют в соответствии с удельной поверхностью волокна.
Формула изобретения
1. Способ производства целлюлозной волокнистой массы, в котором дефибрированную массу сортируют для удаления костры и затем указанную массу фракционируют, причем фракционирование осуществляют в соответствии с удельной поверхностью, предпочтительно устройством (1), содержащим гидроциклоны, при этом указанный способ включает технологические стадии (6, 7), на которых отделяют фракции волокна с более низкой удельной поверхностью, предпочтительно волокна с более толстыми стенками, отличающийся тем, что указанную целлюлозную волокнистую массу фракционируют по меньшей мере на три фракции (10, 3, (3а), 12), по меньшей мере две из которых объединяют полностью или частично, а одну или несколько фракций (3, 3а) волокон с меньшей удельной поверхностью обрабатывают при концентрации массы 0,8-14%, предпочтительно 1-5%, для разделения, фибриллирования и постоянного сплющивания предпочтительно устройством, которое содержит измельчающее устройство (5, 5а), такое, как дефибрер, рафинер, шаровая мельница или подобное оборудование.
2. Способ по п.1, отличающийся тем, что одна или несколько фракций (3, 3а), которые обрабатывают в измельчающем устройстве, содержит волокна со значением z от 0,3 до 0,8.
3. Способ по п.1, отличающийся тем, что измельчающее устройство (5, 5а) работает так, что волокна в поступающей фракции постоянно сплющивают, вызывая образование в стенке волокна трещин, создаваемых измельчающим устройством.
4. Способ по п.1, отличающийся тем, что измельчающее устройство (5, 5а) включает рафинер, работающий при затратах энергии 10-800 кВт·ч/т, предпочтительно 100-600 кВт-ч/т, еще предпочтительнее 200-500 кВт·ч/т.
5. Способ по п.1, отличающийся тем, что фракция (10), которая содержит волокна с высокой удельной поверхностью, выходит из базы гидроциклонной стадии.
6. Способ по п.1, отличающийся тем, что фракция (3, 3а) с меньшей удельной поверхностью и более толстостенными волокнами выходит из базы гидроциклонной стадии.
7. Способ по любому из пп.1-6, отличающийся тем, что фракцию (10), содержащую волокна с высокой удельной поверхностью, отбеливают в нещелочных условиях.
8. Способ по п.7, отличающийся тем, что рН при отбеливании меньше 9.
9. Способ по п.7, отличающийся тем, что применяют восстанавливающий отбеливатель.
10. Способ по п.7, отличающийся тем, что отбеливатель содержит дитионит.
11. Способ по любому из пп.1-5, отличающийся тем, что фракцию (3, 3а) волокон с меньшей удельной поверхностью отбеливают путем окислительного отбеливания.
12. Способ по п.11, отличающийся тем, что отбеливатель содержит перекись водорода.
13. Способ по п.11, отличающийся тем, что отбеливатель содержит озон.
14. Способ по п.1, отличающийся тем, что фракцию (12), которая остается после предыдущих технологических стадий и которая имеет наименьшую удельную поверхность, очищают от песка, коры и других тяжелых включений и обрабатывают предпочтительно с помощью устройства (15) для отслаивания стенок волокон этой фракции (12), при этом устройство включает измельчающее устройство, такое, как рафинер или подобное, и при этом фракцию после обработки полностью или частично возвращают, предпочтительно обратным путем, в технологический процесс.
15. Способ по п.14, отличающийся тем, что устройство (15) для обработки по п.14 осуществляет размол при концентрации >15%, более предпочтительно при концентрации >14%.
16. Способ по п.1, отличающийся тем, что фракцию (3, 3а) волокон с меньшей удельной поверхностью, предпочтительно волокон с более толстыми стенками, после обработки полностью или частично смешивают с фракцией (10) волокон и мелочи с высокой удельной поверхностью для улучшения обезвоживающих свойств.
17. Способ по п.1, отличающийся тем, что фракцию (3, 3а) волокон с меньшей удельной поверхностью, предпочтительно волокон с более толстыми стенками, обезвоживают отдельно до более высокой концентрации, чем желательная конечная концентрация смеси фракций, так чтобы для фракции (10) волокон с высокой удельной поверхностью, предпочтительно представляющей собой тонкостенные волокна и мелочь, требовалось лишь частичное обезвоживание или не требовалось никакого.
18. Способ по п.1, отличающийся тем, что фракции (10, 11, 11а), содержащие волокна с высокой и низкой удельной поверхностью, после обработки объединяют в поток (32) волокнистой массы с волокнистой массой, полученной с более низким расходом энергии и отбеливателей, чем на традиционном целлюлозном комбинате, с получением волокнистой массы для печатных бумаг, массы для газетной бумаги, массы SC, LWC, SC A++ и других видов волокнистой массы.
19. Устройство для обработки волокнистой массы для придания улучшенных свойств в отношении светорассеяния, показателя растяжения, показателя разрыва, шероховатости поверхности, потребления отбеливающих химикатов, энергопотребления, включающее первую гидроциклонную установку (7), вторую гидроциклонную установку (2) и рафинер (5), причем указанная первая гидроциклонная установка (7) выполнена с возможностью соединения выхода ее нижнего сливного отверстия со второй гидроциклонной установкой (2), а базовый выход (3) из второй гидроциклонной установки (2) выполнен с возможностью его соединения таким образом, чтобы фракция из базового выхода проходила в указанный рафинер (5), отличающееся тем, что рафинер (5) выполнен с возможностью его работы при концентрации в пределах 1-14%.
20. Устройство по п.19, отличающееся тем, что первую базовую фракцию (10) отбеливают нещелочным восстанавливающим отбеливателем.
21. Устройство по п.19 или 20, отличающееся тем, что вторую базовую фракцию (3, 11) отбеливают окислительным отбеливателем.
22. Устройство по п.19, отличающееся тем, что фракцию (33) из нижнего сливного отверстия направляют в гидроциклонную установку (2а) и разделяют на базовую фракцию (3а) и фракцию (33а) из нижнего сливного отверстия, при этом указанную базовую фракцию (3а) после обезвоживания обрабатывают в рафинере (5а) при концентрации в пределах 1-14%.
23. Устройство по п.22, отличающееся тем, что базовую фракцию (За, 11а) отбеливают окислительным отбеливателем.
24. Устройство по п.19, отличающееся тем, что обработанные базовые фракции (10, 11 и/или 11а) объединяют в общий поток волокнистой массы (32) с улучшенными свойствами.
25. Устройство по п.19, отличающееся тем, что фракцию (33, 33а) из нижнего сливного отверстия направляют далее на очистку (8) в гидроциклонах, которые удаляют тяжелые загрязнения, такие, как песок, кора и прочие тяжелые загрязнения, остающиеся в фракции (12) из нижнего сливного отверстия.
26. Устройство по п.25, отличающееся тем, что базовую фракцию (12) со стадии очистки (8) в гидроциклонах направляют далее на обработку, включающую размол (15) при концентрации >5%, и затем эту фракцию возвращают в поступающий поток волокнистой массы, подаваемый в устройство по п.19.
РИСУНКИ
|
|