|
(21), (22) Заявка: 2007128703/02, 25.07.2007
(24) Дата начала отсчета срока действия патента:
25.07.2007
(46) Опубликовано: 27.05.2009
(56) Список документов, цитированных в отчете о поиске:
RU 2169798 С1, 27.06.2001. RU 2156838 С1, 27.09.2000. RU 2178599 С2, 20.01.2002. JP 2002206198 А, 26.07.2002.
Адрес для переписки:
659322, Алтайский край, г. Бийск, ул. Социалистическая, 1, ФГУП “ФНПЦ “Алтай”, патентно-лицензионный сектор
|
(72) Автор(ы):
Ларионова Ирина Семеновна (RU), Беляев Вячеслав Николаевич (RU), Ильиных Константин Федорович (RU), Фролов Александр Валериевич (RU), Бычин Николай Валерьевич (RU), Митрофанов Вячеслав Михайлович (RU)
(73) Патентообладатель(и):
Федеральное государственное унитарное предприятие Федеральный научно-производственный центр “Алтай” (RU)
|
(54) СПОСОБ ПОЛУЧЕНИЯ КОМПОЗИЦИОННЫХ ПОКРЫТИЙ
(57) Реферат:
Изобретение относится к области гальванотехники. Способ включает приготовление водной суспензии детонационных наноалмазов, введение водной суспензии в электролит для осаждения покрытия и электролиз, при этом водную суспензию, содержащую 1-5% детонационных наноалмазов, для дезагрегации подвергают обработке на роторно-пульсационной или ультразвуковой установке или на дезинтеграторе, нагревают 2 часа в 15% растворе соляной кислоты с отмывкой осадка от избытка кислоты до значений рН 3,5-6,0, затем обрабатывают 2 часа 0,5-2,0% раствором натриевой щелочи с последующим удалением избытка щелочи до значений рН 6,0-8,0. Технический результат: повышение технологичности процесса, расширение эксплуатационных возможностей и эффективности использования наноразмерной дисперсной фазы, исключение ресурсо- и энергоемких внешних воздействий на электролит в процессе получения покрытия. 2 табл., 3 ил.
Изобретение относится к гальванотехнике, а именно к способу получения композиционных электрохимических покрытий.
Электролитические покрытия широко используются в машиностроении для увеличения износостойкости, коррозионной стойкости деталей машин и инструмента, при восстановлении изношенных деталей, снижении коэффициента трения в парах трения и др.
В настоящее время повышение качества электролитических покрытий достигается за счет использования мелкодисперсных частиц твердых наполнителей (SiC, В4С, Si3N4, различные алмазы и др.)
Известен способ получения композиционного электролитического покрытия по патенту 2169798 (опубл. бюллетень 18, 27.06.2001 г.), в котором используют электролит, содержащий в качестве твердых частиц ультрадисперсные алмазы (УДА), полученные детонационным синтезом. Алмазы, используемые при реализации указанного способа, образуют седиментационно- и коагуляционно-устойчивые системы в электролитах, но при этом перед началом работы электролит перемешивают механически или продувкой газом, что снижает экономическую привлекательность способа. Дальнейшее перемешивание не производят, но при этом ограничивают верхний предел содержания наноалмазов в электролите – 30 г/л, т.к. повышение содержания УДА приводит к сильному загущению и структурированию электролита, что затрудняет конвекцию электролита и протекание тока и, соответственно, снижает качество получаемых покрытий.
Существует способ приготовления электролита для получения композиционных покрытий по патенту 2088689 (опубл. бюллетень 24, 27.08.1997 г.), включающий введение в электролит дисперсной фазы в виде твердых ультрадисперсных частиц. В указанном способе осуществляют диспергирование электролита воздействием ультразвуковых колебаний. Под влиянием ультразвукового воздействия частицы ультрадисперсной фазы приобретает большое количество энергии, достаточное для перехода в состояние высокодисперсного метастабильного коллоида с увеличением седиментационной и агрегативной устойчивости дисперсной системы. Недостатками способа является необходимость использования дорогостоящих ультразвуковых колебательных систем и генераторов, что снижает экономическую эффективность процесса, необходимость перемешивания приготовленных электролитов для сохранения свойств пептизации и тиксатропии, невысокая производительность процесса.
Известен способ получения композиционных металлоалмазных покрытий по патенту 2156838 (опубл. бюллетень 27, 27.06.2001 г.), принятый за прототип, включающий электролиз в присутствии детонационных нанонаноалмазов (ДНА). Недостатками способа являются: большая трудоемкость процесса приготовления алмазной суспензии (50-80 часов при перемешивании) и электролита (выдержка 6-48 часов при 50-60°С); сложность технологического процесса, обусловленная необходимостью равномерного небольшими порциями введения суспензии УДА в электролит; низкая седиментационная и коагуляционная устойчивость ДНА в электролите, требующая ограничения верхнего предела содержания ДНА и, как следствие, невысокие качественные показатели получаемых покрытий.
Согласно расчетам частица детонационного наноалмаза размером 4 нм содержит 1,2-104 атомов углерода, из которых примерно 25% являются поверхностными. Исследования элементного состава ДНА, проведенные ФГУП ФНПЦ “Алтай”, показали, что в состав ДНА входят, кроме углерода (75-90%), азот (1,0-4,5), водород (0,6-1,5) и кислород (остальное). На каждые 100 поверхностных атомов углерода приходится 20-140 атомов водорода, 16-128 атомов кислорода и 8-16 атомов азота, образующих различные (гидроксильные, карбонильные, карбоксильные и др.) химически активные поверхностные группы. Устойчивость, размеры и свойства сорбционной оболочки, образующейся вокруг ДНА при введении его в жидкость, зависят от рН среды, химического состава жидкости, наполненной ДНА и других внешних факторов.
В ФГУП ФНПЦ «Алтай» проведены исследования по влиянию концентрации соли NiCl2 в электролите на седиментационную устойчивость ДНА. Было выявлено (Фиг.1), что при увеличении концентрации (С, г/л) С12 (числа анионов и катионов в дистиллированной воде) в электролите седиментационная устойчивость (А, ч) кластерных частиц алмаза резко снижается. Физический механизм данного процесса можно объяснить следующим. В чистой дистиллированной воде частицы ДНА образуют гидратную оболочку, рН среды – нейтральная. При введении NiCl2, соли, диссоциирующей на Ni2+ и Cl–, происходит образовании гидратной оболочки вокруг катионов (К) и анионов хлористой соли, а также изменение рН среды (фиг.2). С увеличением концентрации NiCl2 число свободных молекул воды уменьшается и, с определенной концентрации диссоциирующей соли, молекулы воды становятся общими между ионами соли и ДНА (фиг.3) и далее, т.к. ионы энергетически сильнее, возможен и отрыв гидратной оболочки от ДНА. Таким образом, у частицы ДНА снижается седиментационная устойчивость и возрастает вероятность образования крупных агрегатов за счет «схлопывания» с другими наноалмазными частицами. В итоге все это приводит к осаждению, под действием силы тяжести, крупных агрегатов ДНА на дно ванны.
Проведенные исследования показали, что без применения специальных внешних устройств, обеспечивающих перемешивание электролита с ДНА, седиментационная и коагуляционная устойчивость частиц твердой фазы невозможна. При этом механическое перемешивание электролита не снижает размеры агрегатов ДНА, образовавшихся при «схлопывании» частиц. Таким образом, недостаток прототипа заключается в использовании ДНА с низкой седиментационной стабильностью и большими размерами агрегатов наноалмазов в электролите, что, при применении матрицы из металла, обладающего недостаточно высокими физико-механическими характеристиками (медь, никель), снижает эффективность использования наноразмерной дисперсной фазы и качество получаемого электролитического покрытия.
Задачей настоящего изобретения является создание способа получения композиционного покрытия, позволяющего повысить технологичность процесса, расширить эксплуатационные возможности и эффективность использования наноразмерной дисперсной фазы путем создания условий для обеспечения высокой седиментационной и коагуляционной устойчивости наноалмазов в электролитах при одновременном исключении ресурсо- и энергоемких внешних воздействий на электролит в процессе получения покрытия.
Поставленная задача решается предложенным способом получения композиционного покрытия, включающим приготовление водной суспензии детонационных наноалмазов, введение суспензии в электролит для осаждения покрытия и электролиз. Согласно изобретению водную суспензию, содержащую 1-5% детонационных наноалмазов, для дезагрегации подвергают обработке на роторно-пульсационной или ультразвуковой установке или на дезинтеграторе, нагревают 2 часа в 15% растворе соляной кислоты с отмывкой осадка от избытка кислоты до значений рН 3,5-6,0, затем обрабатывают 2 часа 0,5-2% раствором натриевой щелочи с последующим удалением избытка щелочи до значений рН 6,0-8,0.
Установлено, что электрокинетический потенциал поверхности используемых при воплощении заявляемого способа детонационных наноалмазов составляет от -30 до -80 мВ, что обеспечивает седиментационную стабильность наноалмазных золей в электролите металлоосаждения.
Электрокинетический потенциал частиц зависит от количества гидрофильных групп на поверхности и возрастает со степенью гидрофильное материала в целом. Обычно детонационные наноалмазы имеют электрокинетический потенциал поверхности от -10 до -30 мВ, недостаточный для их седиментационной устойчивости в электролите и требующий определенных ограничений по содержанию вводимых в электролит ДНА и условиям их введения (небольшие порции).
Для достижения значений электрокинетического потенциала от -30 до -80 мВ при реализации заявляемого способа водную суспензию детонационных наноалмазов, содержащую 1-5% дисперсной фазы, для дезагрегации подвергают обработке на роторно-пульсационной или ультразвуковой установке или на дезинтеграторе, а затем последовательно обрабатывают растворами кислоты и щелочи по следующей схеме:
– нагревают 2 часа в 15% растворе соляной кислоты с отмывкой осадка от избытка кислоты до значений рН 3,5-6,0;
– затем обрабатывают 2 часа 0,5-2% раствором натриевой щелочи с последующим удалением избытка щелочи до значений рН 6,0-8,0.
Осаждение покрытия проводят при температуре электролита и плотности тока в соответствии с технологией нанесения конкретного металла.
Измерение электрокинетического потенциала проводят перед введением суспензии в электролит, например, с помощью измерительной ячейки прибора Чайковского для электрофореза или на приборе Zeta-size марки ZPW388.
Пример 1
В медный электролит вводят суспензию ДНА при следующем соотношении компонентов, г/л:
Медный купорос (CuSO4·5Н2O) – 45-55
Натрий пирофосфорнокислый (Na4P2O7) – 200-240
Калий азотнокислый (KNO3) – 10-20
ДНА – 2-42
Электрокинетический потенциал поверхности ДНА составляет от – 32 до -80 мВ.
В Таблице 1 приведены характеристики медных покрытий при различных концентрациях ДНА в электролите.

Пример 2
В никелевый электролит вводят суспензию ДНА при следующем соотношении компонентов, г/л:
Никель сернокислый семиводный (NiSO4·7H2O) – 200-240
Никель хлористый шестиводный (NiSO4·6Н2O) – 20-25
Натрий сернокислый десятиводный (Na2SO4·10Н2О) – 80-90
Магний сернокислый семиводный (MgSO4·7H2O) – 80-85
Янтарная кислота – 25-30
ДНА – 2-42
Электрокинетический потенциал поверхности ДНА составляет от – 36 до -78 мВ.
В таблице 2 приведены характеристики никелевых покрытий при разных концентрациях ДНА.
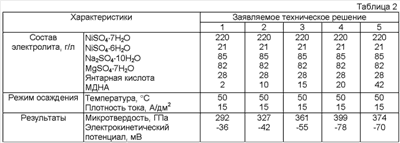
Реализация данного изобретения позволит удовлетворить давно существующую потребность в технологичном с расширенными эксплуатационными возможностями способе получения композиционных покрытий, воплощение которого обеспечивает более эффективное использование наноразмерной дисперсной фазы.
Формула изобретения
Способ получения композиционного покрытия, включающий приготовление водной суспензии детонационных наноалмазов, введение водной суспензии в электролит для осаждения покрытия и электролиз, отличающийся тем, что водную суспензию, содержащую 1-5% детонационных наноалмазов, для дезагрегации подвергают обработке на роторно-пульсационной или ультразвуковой установке или на дезинтеграторе, нагревают 2 ч в 15%-ном растворе соляной кислоты с отмывкой осадка от избытка кислоты до значений рН 3,5-6,0, затем обрабатывают 2 ч 0,5-2,0%-ным раствором натриевой щелочи с последующим удалением избытка щелочи до значений рН 6,0-8,0.
РИСУНКИ
|
|