|
(21), (22) Заявка: 2007135856/02, 28.09.2007
(24) Дата начала отсчета срока действия патента:
28.09.2007
(46) Опубликовано: 27.04.2009
(56) Список документов, цитированных в отчете о поиске:
SU 549485 A, 06.05.1977. SU 836156 A, 09.06.1981. RU 2124056 C1, 27.12.1998. RU 2140997 C1, 10.11.1998. JP 55-23885 A, 25.06.1980.
Адрес для переписки:
127220, Москва, ул. Полтавская, 2, кв.114, С.Н. Киселеву
|
(72) Автор(ы):
Киселев Сергей Николаевич (RU), Саврухин Андрей Викторович (RU), Неклюдов Алексей Николаевич (RU), Кузьмина Галина Дмитриевна (RU), Киселев Алексей Сергеевич (RU), Киселев Александр Сергеевич (RU)
(73) Патентообладатель(и):
Киселев Сергей Николаевич (RU), Саврухин Андрей Викторович (RU), Неклюдов Алексей Николаевич (RU), Кузьмина Галина Дмитриевна (RU), Киселев Алексей Сергеевич (RU), Киселев Александр Сергеевич (RU)
|
(54) СПОСОБ ТЕРМИЧЕСКОГО УПРОЧНЕНИЯ ЖЕЛЕЗНОДОРОЖНЫХ КОЛЕС
(57) Реферат:
Изобретение относится к области термической обработки. Для обеспечения твердости не ниже 300 НВ на глубине не менее 50 мм от поверхности катания обода колеса, исключения в процессе охлаждения образования закалочных структур и обеспечения максимального снижения остаточных напряжений цельнокатаные колеса из стали с содержанием углерода не менее 0,60 мас.% нагревают до температуры аустенизации и интенсивно охлаждают, при этом в процессе охлаждения с момента его начала за 50-100 секунд осуществляют увеличение интенсивности охлаждения поверхности катания гребня и боковых поверхностей обода по всей их высоте от 0 до значения 2-3 Вт(см2·с), затем охлаждают в течение 40-300 секунд с постоянной интенсивностью охлаждения указанных поверхностей обода, равной значению 2-3 Вт/(см2·с), для обеспечения упрочнения во всем объеме обода. 2 ил., 3 табл.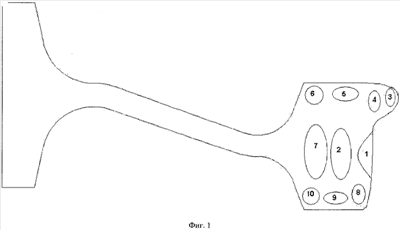
Изобретение относится к термической обработке стальных изделий и может быть использовано при изготовлении железнодорожных цельнокатаных колес из стали с содержанием углерода не менее 0,60%.
Известен способ термического упрочнения железнодорожных колес, см. Бибик Г.А. и др. Производство железнодорожных колес. М.: Металлургия, 1982, с.164-171, предусматривающий нагрев изделий под термообработку, подачу охладителя на различные поверхности обода колеса (боковые и поверхность катания) с требуемой скоростью охлаждения и отпуск. Указанная технология термического упрочнения колес включает в себя их нагрев до 840-870°С равномерно по всему объему в зависимости от содержания в стали углерода и марганца, передачу нагретого колеса к закалочной машине с минимальным промежутком во времени, указанном в нормативной документации.
Использование такой технологии обеспечивает невысокий уровень прочностных свойств металла и износостойкости обода при эксплуатации.
Из известных технических решений наиболее близким по технической сущности к заявляемому способу является способ термической обработки железнодорожных колес, см. а.с. СССР 549485, кл. C21D 9/34, 1977, который выбран в качестве прототипа. Данный способ включает в себя нагрев железнодорожных колес до температуры Ас3+(30-50)°С, выравнивание температуры внутренних и поверхностных зон обода выдержкой при температуре Ас3+(30-50)°С, термическое упрочнение обода охлаждением его водой, снижение температуры колес подстуживанием на воздухе и их последующий отпуск.
Недостатком этого способа является тот факт, что в момент окончания охлаждения в поверхностных зонах обода образуются закалочные структуры (до 100% мартенсита), пластические деформации, а также высокий уровень растягивающих напряжений, что увеличивает вероятность образования трещин в момент окончания охлаждения. Определить напряженно-деформированное и структурное состояние обода колеса в различные моменты на этапе охлаждения можно только методами компьютерного моделирования.
Техническим результатом изобретения является повышение свойств материала железнодорожных цельнокатаных колес – стали с содержанием углерода не менее 0,60%, а именно обеспечение твердости не ниже 300 НВ на глубине не менее 50 мм от поверхности катания обода колеса при исключении или максимальном уменьшении в процессе охлаждения образования закалочных структур и максимального снижения остаточных напряжений в момент окончания закалки.
Для достижения технического результата в процессе охлаждения с момента его начала за 50-100 секунд происходит постепенное увеличение интенсивности охлаждения поверхности катания, гребня и боковых поверхностей обода по всей их высоте от 0 до значения 2-3 Вт/(см2·с), затем охлаждение продолжается в течение 40-300 секунд с постоянной интенсивностью охлаждения указанных поверхностей обода, равной значению 2-3 Вт/(см2·с), для обеспечения упрочнения во всем объеме обода.
Изобретение поясняется прилагаемыми чертежами, где:
– на фиг.1 показана схема расположения зон оценки и сравнения напряженно-деформированного состояния в радиальном сечении железнодорожного колеса для различных вариантов технологии закалки;
– на фиг.2 показано типичное распределение температур в радиальном сечении железнодорожного колеса в момент завершения закалки (см. табл.).
Обод колеса (см. фиг.1) в радиальном сечении разделен на следующие зоны: 1 – поверхность катания, 2 – зона под поверхностью катания на глубине 10-20 мм, 3 – вершина гребня, 4 – основание гребня, 5 – середина внутренней боковой стороны обода, 6 – угол обода с внутренней стороны, 7 – зона вблизи перехода от обода к диску, 8 – угол с внешней стороны обода у поверхности катания, 9 – середина внешней боковой стороны обода, 10 – угол обода с внешней стороны.
Материал в указанных зонах отличается структурным состоянием, значениями температуры, скоростей охлаждения, напряжений и деформаций в процессе и после закалки.
Кроме того, в описании изобретения даны 3 таблицы. В таблицах для указанных зон после закалки представлены следующие параметры:
Б – содержание закалочной структуры бейнита, %;
М – содержание закалочной структуры мартенсита, %;
НВ – твердость по Бринеллю, МПа;
r, o и  – соответственно радиальные, осевые и окружные напряжения, МПа;
i – интенсивность напряжений, МПа;
i пл – интенсивность пластических деформаций, %.
Сущность заявляемого способа заключается в следующем. Колесо целиком нагревается до температуры аустенизации Ас3+(30-50)°С, и производится выравнивание температуры внутренних и поверхностных зон обода. Далее по разработанной методике производится термическое упрочнение обода интенсивным охлаждением и отпуск колеса.
Упрочнение производится при постепенном увеличении интенсивности охлаждения с поверхностей обода колеса от нуля до максимального значения, которое соответствует 2-3 Вт / (см2·с), по линейному или нелинейному закону в течение 50-100 секунд с последующим охлаждением обода при максимальной интенсивности охлаждения в течение 40-300 секунд. Время изменения интенсивности охлаждения определяет величину и характер распределения напряжений во всем объеме колеса в момент окончания упрочнения.
Методами имитационного, компьютерного моделирования, прошедшими необходимую аттестацию и верификацию, были выполнены сравнительные расчеты указанных выше параметров в момент окончания упрочнения для способа, выбранного в качестве прототипа (см. таблицу 1), и заявляемого способа для различного времени нарастания интенсивности охлаждения (см. таблицы 2 и 3).
Таблица 1 Время закалки 160 с, интенсивность охлаждения постоянная и соответствует максимальному значению 2-3 Вт/(см2·с) |
зон |
М, % |
НВ, МПа |
r, МПа |
0, МПа |
 , МПа |
i, МПа |
i пл, % |
1 |
до 97 |
6070 |
~0 |
-1700 |
-1800 |
1750 |
1,6 |
2 |
– |
3550 |
~0 |
429 |
483 |
400 |
~0 |
3 |
до 97 |
6200 |
179 |
-850 |
-1300 |
1300 |
0,7 |
4 |
– |
3920 |
617 |
-179 |
711 |
850 |
~0 |
5 |
до 97 |
6070 |
-570 |
~0 |
483 |
1450 |
0,7 |
6 |
до 97 |
6070 |
-900 |
~0 |
254 |
900 |
0,5 |
7 |
– |
3200 |
-40 |
-179 |
254 |
41 |
~0 |
8 |
– |
6070 |
-0 |
214 |
480 |
1450 |
0,8 |
9 |
до 97 |
6070 |
400 |
~0 |
480 |
1450 |
1,6 |
10 |
до 97 |
6070 |
~0 |
~0 |
480 |
1100 |
1,0 |
Таблица 2 Время закалки 160 с, интенсивность охлаждения возрастает от 0 до максимального значения 2-3 Вт/(см2·с) за 40 с |
зон |
М, % |
НВ, МПа |
r, МПа |
о, МПа |
 , МПа |
i, МПа |
i пл, % |
1 |
до 35 |
5100 |
~0 |
-700 |
-550 |
630 |
0,008 |
2 |
0 |
3300 |
~0 |
470 |
315 |
450 |
~0 |
3 |
до 49 |
5500 |
~0 |
~0 |
-340 |
350 |
0,08 |
4 |
0 |
3600 |
280 |
~0 |
650 |
540 |
~0 |
5 |
до 21 |
4800 |
-620 |
~0 |
-200 |
540 |
~0 |
6 |
до 11 |
4800 |
-210 |
~0 |
-200 |
270 |
~0 |
7 |
0 |
3300 |
~0 |
~0 |
-120 |
170 |
0,02 |
8 |
до 55 |
5500 |
120 |
80 |
-300 |
360 |
0,008 |
9 |
до 25 |
5100 |
-700 |
~0 |
-120 |
540 |
0,008 |
10 |
до 25 |
4800 |
~0 |
~0 |
-120 |
200 |
~0 |
Таблица 3 Время закалки 160 с, интенсивность охлаждения возрастает от 0 до максимального значения 2-3 Вт/(см2·с) за 60 с |
зон |
М, % |
НВ, МПа |
r, МПа |
о, МПа |
 , Мпа |
i, МПа |
i ПЛ, % |
1 |
до 18 |
4900 |
~0 |
-430 |
-240 |
280 |
0,02 |
2 |
~0 |
3500 |
~0 |
390 |
300 |
390 |
~0 |
3 |
до 30 |
4900 |
~0 |
-100 |
-80 |
119 |
0,02 |
4 |
~0 |
3500 |
320 |
~0 |
600 |
550 |
~0 |
5 |
~0 |
4300 |
~517 |
0 |
-100 |
500 |
~0 |
6 |
~0 |
4300 |
~150 |
0 |
-100 |
220 |
~0 |
7 |
~0 |
3200 |
~0 |
~0 |
-100 |
120 |
0,02 |
8 |
до 36 |
5300 |
~0 |
-200 |
-100 |
120 |
0,02 |
9 |
~0 |
4600 |
-500 |
~0 |
-100 |
550 |
0,02 |
10 |
~0 |
4600 |
-160 |
~0 |
140 |
280 |
~0 |
Сравнивая величины параметров, приведенных в таблицах 1-3, можно сделать вывод о том, что во всех рабочих (контактирующих с рельсом) зонах обода колеса при увеличении времени нарастания интенсивности охлаждения:
– растягивающие напряжения в момент окончания охлаждения снижаются в несколько раз;
– количество мартенсита в гребне обода, подверженном наиболее интенсивному износу, снижается от 97% до значений в отдельных зонах от 0% до 30%;
– интенсивность пластических деформаций снижается с 1,6% почти до 0.
Как показали расчеты, в заявляемом способе для достижения наибольшей эффективности рекомендуется выбирать значение времени нарастания интенсивности охлаждения в интервале от 50 до 100 секунд. Дальнейшее увеличение времени нарастания интенсивности охлаждения нецелесообразно в связи со снижением твердости и механических характеристик металла обода колеса.
Формула изобретения
Способ термического упрочнения железнодорожных колес из стали с содержанием углерода не менее 0,60 мас.%, включающий нагрев колеса до температуры аустенизации Ас3+(30-50)°С, выравнивание температуры внутренних и поверхностных зон обода, термическое упрочнение обода интенсивным охлаждением и отпуск колеса, отличающийся тем, что с момента начала охлаждения за 50-100 с осуществляют постепенное увеличение интенсивности охлаждения поверхности катания, гребня и боковых поверхностей обода по всей их высоте от 0 до 2-3 Вт/(см2·с), а затем охлаждение продолжают в течение 40-300 с с постоянной интенсивностью охлаждения указанных поверхностей обода, равной 2-3 Вт/(см2·с), для обеспечения упрочнения во всем объеме обода колеса.
РИСУНКИ
|
|