|
(21), (22) Заявка: 2007129122/06, 31.07.2007
(24) Дата начала отсчета срока действия патента:
31.07.2007
(46) Опубликовано: 20.04.2009
(56) Список документов, цитированных в отчете о поиске:
RU 2291736 C2, 20.02.2006. RU 2016630 C1, 30.07.1994. SU 176354 A1, 01.01.1965. WO 02/056999 A1, 25.07.2002. US 5306330 A, 26.04.1994.
Адрес для переписки:
142110, Московская обл., г. Подольск, а/я 29
|
(72) Автор(ы):
Запорожец Евгений Петрович (RU), Зиберт Алексей Генрихович (RU), Зиберт Генрих Карлович (RU), Валиуллин Илшат Минуллович (RU)
(73) Патентообладатель(и):
Закрытое акционерное общество “Центральное конструкторское бюро нефтегазовой промышленности” (ЗАО “ЦКБ НГП”) (RU), Зиберт Генрих Карлович (RU)
|
(54) СПОСОБ ГАЗОДИНАМИЧЕСКОЙ СЕПАРАЦИИ
(57) Реферат:
Способ газодинамической сепарации относится к технике низкотемпературной обработки многокомпонентных углеводородных газов (природных и нефтяных), а именно для осушки газа путем конденсации из него водного и (или) углеводородных компонентов, и может быть использован в системах сбора, подготовки и переработки многокомпонентных углеводородных газов. Способ газодинамической сепарации включает подачу потока высоконапорного многокомпонентного углеводородного газа в сопло, его изоэнтальпийное расширение и охлаждение при течении в сопле, конденсацию компонентов в охлажденном потоке газа, отделение конденсата от газовой фазы, удаление очищенного газа и конденсата, повышение давления очищенного газового потока путем его торможения в диффузоре. Исходный поток газа предварительно охлаждают путем теплообмена с потоком газа, истекающего из сопла, компоненты конденсируют, отделяют от газовой фазы и удаляют при давлении исходного газа или (и) давлении газа после его расширения в сопле, газовую фазу подают в сопло после ее очистки от конденсата при давлении исходного газа, а давление расширенного и очищенного газового потока повышают после его теплообмена с исходным газом. Использование изобретения позволит повысить эффективность газодинамической сепарации и снизить затраты энергии. 4 з.п. ф-лы, 7 табл., 6 ил.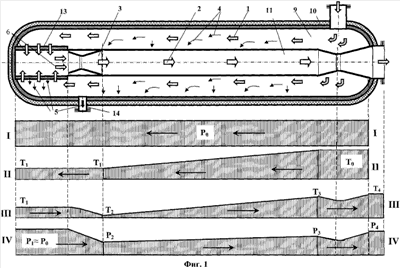
Изобретение относится к технике низкотемпературной обработки многокомпонентных углеводородных газов (природных и нефтяных), а именно для осушки газа путем конденсации из него водного и (или) углеводородных компонентов. Изобретение может быть использовано в системах сбора, подготовки и переработки многокомпонентных углеводородных газов.
Известен способ газодинамической сепарации [Бекиров Т.М., Ланчаков Г.А. Технология обработки газа и конденсата. – М.: ООО «Недра-Бизнесцентр», 1999. – С.336], включающий закрученную подачу потока высоконапорного многокомпонентного углеводородного газа в сопло, его изоэнтальпийное расширение с охлаждением при истечении с околозвуковой скоростью, конденсацию компонентов из расширенного и охлажденного газа, осаждение конденсата из вращающегося охлажденного потока газа на твердую поверхность с образованием на ней жидкой пленки и удаление последней через щелевое коаксиальное отверстие в зону с пониженным давлением, которую создают циркуляционным эжектированием из нее газовой фазы исходным газом, повышение давления очищенного газового потока путем его торможения в диффузоре и подачу его потребителю.
При изоэнтальпийном расширении газа в сопле при его истечении с околозвуковой скоростью (300-360 м/с) потенциальная энергия – давление газа – переходит в кинетическую энергию, при этом газ охлаждается и приобретает статическую температуру, около минус 50°С (при исходной температуре газа +10°С). При низкой температуре происходит конденсация углеводородных компонентов С3 + выше. Чем сильнее охлаждение газа, тем глубже его осушка от жидкости (уменьшение температуры точки росы конденсируемых компонентов). Поэтому для обеспечения эффективной работы газодинамического сепаратора необходимо усилить охлаждение газа, что на околозвуковых скоростях недостижимо.
6 – 2002 – С.41-44], включающем закрученную подачу потока высоконапорного многокомпонентного углеводородного газа в сопло, его изоэнтальпийное расширение с охлаждением при истечении со сверхзвуковой скоростью, конденсацию компонентов из расширенного и охлажденного газа, осаждение конденсата из вращающегося охлажденного потока газа на твердую поверхность с образованием на ней жидкой пленки и удаление последней сквозь щелевое коаксиальное отверстие в зону с пониженным давлением, которую создают циркуляционным эжектированием из нее газовой фазы исходным газом, повышение давления очищенного газового потока путем его торможения в диффузоре и подачу его потребителю.
При истечении газа со сверхзвуковыми скоростями достигается статическая температура в потоке порядка минус 100°С и интенсифицируется конденсация компонентов из газа.
Однако при сверхзвуковых скоростях отделение сконденсировавшихся компонентов от вращающегося охлажденного потока газа неэффективно. Высокая турбулентность, порожденная большими скоростями истечения газа, срывает осевшие жидкие частицы с твердой поверхности и уносит их из газодинамического сепаратора. Поэтому необходимо очень быстро удалять осевшие жидкие частицы с твердой поверхности в зону с пониженным давлением. Перемещение осевших частиц обуславливается действием разности давлений в потоке газа и в зоне пониженного давления. С целью создания разряжения в этой зоне из нее эжектируется газ исходным газом. Причем, чем большее количество газа эжектируется из этой зоны, тем глубже разрежение в этой зоне и тем быстрее удаляется осевшая жидкость с твердой поверхности. Вместе с жидкостью в зону пониженного давления поступает и газ из основного потока. Поэтому получается замкнутое циркуляционное движение газа из зоны пониженного давления в охлажденный поток и из охлажденного потока опять в эту зону.
Однако создание зоны с пониженным давление путем циркуляционного эжектирования из нее газа исходным газом приводит к потерям энергии – давления исходного газа. Потери энергии тем больше, чем глубже создаваемое разряжение в зоне. Но потери энергии влекут за собой снижение скорости охлаждаемого газа и, как следствие, повышение его температуры и снижение интенсивности конденсации компонентов. Таким образом, описанное техническое противоречие обуславливает большие расходы энергии в виде потерь давления газа при реализации работы по данному способу газодинамического сепаратора.
Некоторое повышение эффективности газодинамической сепарации и снижение затрат энергии – давления газа достигается в способе (патент RU 2291736, приоритет 13.09.2004 г., МПК B01D 45/12, B01D 53/26), включающем подачу закрученного исходного потока высоконапорного многокомпонентного углеводородного газа в сопло; ввод в исходный поток конденсируемых компонентов в жидкой или паровой фазах; изоэнтальпийное расширение газа с охлаждением при его истечении с околозвуковой или сверхзвуковой скоростью; конденсацию компонентов в расширенном и охлажденном вращающимся потоке газа; отделение от газа конденсата; сбор конденсата в зоне с пониженным давлением, которую создают путем эжектирования из нее газовой фазы потоком очищенного газа; повышение давления очищенного газового потока путем его торможения в диффузоре; удаление очищенного газа и конденсата; охлаждение исходного газа жидкостью, удаляемой из зоны пониженного давления, и (или) очищенным газом.
Однако в данном способе газодинамической сепарации эффективность улавливания сконденсировавшихся компонентов при сверхзвуковых скоростях не превышает 15÷20%. Потери энергии в виде давления также высоки и составляют порядка 30% от исходного давления.
Задачей настоящего изобретения является повышение эффективности газодинамической сепарации и снижение затрат энергии – давления газа.
Технический результат при осуществлении изобретения достигается тем, что в способе газодинамической сепарации, включающем подачу потока высоконапорного многокомпонентного углеводородного газа в сопло, его изоэнтальпийное расширение и охлаждение при течении в сопле, конденсацию компонентов в охлажденном потоке газа, отделение конденсата от газовой фазы, удаление очищенного газа и конденсата, повышение давления очищенного газового потока путем его торможения в диффузоре, исходный поток газа предварительно охлаждают путем теплообмена с потоком газа, истекающего из сопла, компоненты конденсируют, отделяют от газовой фазы и удаляют при давлении исходного газа или (и) давлении газа после его расширения в сопле, газовую фазу подают в сопло после ее очистки от конденсата при давлении исходного газа, а давление расширенного и очищенного газового потока повышают после его теплообмена с исходным газом. Теплообмен производят в противотоке. При теплообмене исходному газу придают винтообразное движение. При теплообмене исходный газ подают сквозь капиллярно-пористую структуру. При теплообмене в исходный газ вводят ингибиторы гидратообразования и (или) абсорбенты.
Охлаждение исходного потока газа предварительно путем теплообмена с потоком газа, истекающего из сопла, конденсация компонентов, отделение от газовой фазы и удаление при давлении исходного газа или (и) давлении после расширения газа в сопле, подача газовой фазы в сопло после ее очистки от конденсата при давлении исходного газа, повышение давления расширенного и очищенного газового потока после его теплообмена с исходным газом позволили достигнуть повышения эффективности газодинамической сепарации и снижение затрат энергии – давления газа.
Осуществление теплообмена в противотоке, придание при теплообмене исходному газу винтообразного движения, подачи при теплообмене исходного газа сквозь капиллярно-пористую структуру, введение при теплообмене в исходный газ ингибиторов гидратообразования и абсорбентов также способствует достижению поставленной задачи.
Авторам и заявителям не известны способы газодинамической сепарации, в которых бы технический результат был бы достигнут подобным образом.
На фиг.1 – представлена схема теплообмена исходного газа с холодным расширенным газом и эпюры, отображающие изменения давления и температуры взаимодействующих потоков при теплообмене.
На фиг.2 – представлена схема конденсации компонентов из исходного газа при теплообмене.
На фиг.3 – представлена схема теплообмена при винтовом движении исходного газа.
На фиг.4 – представлен разрез А-А на фиг.3.
На фиг.5 – представлена схема процесса конденсации при подаче исходного газа сквозь капиллярно-пористую структуру.
На фиг.6 – представлена схема теплообмена с подачей в исходный газ ингибиторов гидратообразования и (или) абсорбентов.
Способ газодинамической сепарации осуществляется следующим образом.
Охлаждение исходного потока газа 1 (фиг.1) путем его теплообмена с потоком газа 2, истекающего из сопла 3, позволяет достаточно глубоко охладить газ при его исходном высоком давлении P0 – эпюра I (фиг.1). Охлаждение исходного газа происходит от максимальной – исходной температуры T0 – эпюра II (фиг.1), до температуры T1, величина которой может отличаться на 5÷10 градусов от температуры Т2 (эпюра III) газа 2 на выходе из сопла 3.
Проведение конденсации компонентов 4 в исходном газе при высоком исходном давлении P0 и низкой температуре T1 повышает количество выделяемой из газа жидкой фазы, что в конечном итоге улучшает процесс сепарации.
Отделение конденсата 5 от газовой фазы 6 при давлении P0 исходного газа и небольшой скорости его перемещения, величина которой на два порядка меньше скорости газа 2, истекающего из сопла 3, позволяет эффективно очищать газовую фазу от жидкости, например за счет гравитации или фильтрации. Это повышает эффективность процесса сепарации практически без потерь давления.
Удаление конденсата 5 (фиг.1) под давлением исходного газа ускоряет его вывод из области конденсации и отделения от газа, это также повышает эффективность сепарации.
Конденсация компонентов 7 (фиг.2) при давлении газа после его расширения в сопле при максимально низкой температуре Т2 – эпюра III (фиг.1) протекает с максимальной эффективностью, особенно при скоростях потока в сопле, превышающих скорость звука. При снижении скорости такого газожидкостного потока его давление и температура повышаются, и конденсат, испаряясь, переходит в газовую фазу. Поэтому выполнение отделения конденсата 7 (фиг.7) от газовой фазы наиболее эффективно при давлении газа сразу после его расширения в сопле.
Удаление этого конденсата 7 при давлении расширенного газа позволяет сохранить низкую температуру, при которой конденсат не испаряется, что увеличивает эффективность процесса сепарации.
Конденсация компонентов 4, 7 (фиг.2), отделение их от газовой фазы и удаление при давлении исходного газа и давлении после расширения газа в сопле 3 (фиг.2) позволяет эффективно очистить газовую фазу от жидкости, сконденсировавшейся при высоком давлении, и от жидкости 6, которая сконденсировалась при самой низкой достигаемой температуре Т2 (эпюра III, фиг.1), и тем самым повысить эффективность процесса сепарации.
Подача газовой фазы 6 в сопло 3 (фиг.1) после ее очистки от конденсата при давлении исходного газа позволяет эффективно выполнить процесс изоэнтальпийного расширения и охлаждения газа, без больших затрат энергии на конденсацию. Это в конечном итоге снижает температуру Т2 (эпюра III, фиг.1) потока очищенного газа 2 и, как следствие, температуру Т1 (эпюра II, фиг.1) охлажденного исходного газа, что в свою очередь повышает количество конденсируемых компонентов 4 и эффективность сепарации в целом.
Повышение давления в диффузоре 8 (фиг.2) очищенного газового потока 2 после его теплообмена с исходным газом 1 позволяет: во-первых, повысить температуру очищенного газа от величины Т2 до величины Т3 (эпюра III, фиг.1), которая может отличаться на 5÷10 градусов ниже температуры T0 исходного газа; во-вторых, увеличить статическое давление потока от величины Р2 (эпюра IV, фиг.1) на срезе сопла 3 до величины Р3 на входе диффузора 8 (фиг.2), которая тем больше, чем выше температура Т3. С помощью этого технического приема повышается общая энергия потока 2 очищенного газа, и при его торможении в диффузоре 8 полное давление восстанавливается до величины P4 (эпюра IV, фиг.1), которая всего на 15÷20% ниже давления P0 исходного газа. Таким образом, достигается снижение затрат энергии – давления.
Проведение теплообмена в противотоке (фиг.1, 2) позволяет эффективно выполнить этот процесс, увеличить количество выделяемого из газа конденсата и тем самым повысить эффективность процесса сепарации.
Придание при теплообмене исходному газу 1 (фиг.3, 4) винтообразного движения увеличивает время его теплообмена, повышает эффективность последнего и в конечном итоге увеличивает эффективность процесса сепарации.
Подача исходного газа при теплообмене сквозь капиллярно-пористую структуру 9 (фиг.5) позволяет за счет капиллярных явлений ускорить процесс конденсации и эффективность сепарации.
Ввод в исходный газ при его теплообмене ингибиторов гидратообразования позволяет не допустить появления кристаллогидратов, на которые затрачивается холод и при этом ухудшается конденсация компонентов.
Ввод в исходный газ при его теплообмене абсорбентов позволяет расширить возможности способа газодинамической сепарации и тем самым повысить его эффективность. Например, ввод:
– керосиновых фракций позволяет повысить эффективность конденсации углеводородных компонентов в интервале температур 15÷40°С охлаждаемого газа 1 и не допустить их дегазации при удалении конденсата, что в конечном итоге повышает эффективность сепарации;
– диэтиленгликоля или триэтиленгликоля позволяет предварительно осушить исходный газ от паров воды при температурах 15÷30°С, тем самым снизить энергетические затраты холода на ее конденсацию, уменьшить вероятность появления кристаллогидратов и в конечном итоге повысить эффективность очистки газа;
– моноэтаноламина позволяет очистить газ от кислых компонентов (CO2 и H2S), тем самым расширить функциональные возможности способа и повысить в конечном итоге его эффективность.
Реализация способа газодинамической сепарации иллюстрируется следующими примерами в аппаратах, представленных на фиг.1-6. В эти аппараты подается исходный многокомпонентный углеводородный газ. Компонентный состав исходного газа в массовых долях: СН4 – 0,778819; С2Н6 – 0,06861; С3Н8 – 0,041102; С4Н10 – 0,026154; C5H12 – 0,01383; С6 + выше – 0,071485.
Исходный газ имеет термодинамические параметры, которые представлены в таблице 1.
Таблица 1 |
Начальные параметры исходного газа |
Пп. |
Наименование параметра |
Размерность |
Газовая фаза |
Жидкая фаза |
1 |
2 |
3 |
4 |
5 |
1 |
Давление, Р0 |
МПа |
16,0 |
16,0 |
2 |
Температура, Т0 |
°С |
40 |
40 |
3 |
Молекулярная масса |
 |
18,71 |
65,46 |
4 |
Плотность |
кг/нм3 |
8,038 |
643,0 |
5 |
Доля фазы, масс. |
 |
0,9951 |
0,0049 |
6 |
Вязкость |
Па·с |
1,91 10-5 |
9,28 10-2 |
7 |
Cp/Cv |
 |
1,816 |
 |
8 |
Удельная теплоемкость |
кДж/(кмоль·град) |
62,22 |
145,90 |
9 |
Фактор сжимаемости |
 |
0,7694 |
 |
Пример 1.
Исходный многокомпонентный углеводородный газ 1 (фиг.1, 2) подают по кольцевому каналу 10 между цилиндрическим корпусом 11 аппарата и цилиндрической термогазодинамической камерой 12. Исходный поток газа 1 охлаждается путем теплообмена в противотоке с газом 2, истекающего из сопла 3. Газ при истечении из сопла 3 имеет начальные параметры, которые представлены в таблице 2. После охлаждения поток 1 имеет параметры, представленные в таблице 3. Во время охлаждения исходного газа 1 углеводородные компоненты 4 конденсируются и отделяются от газовой фазы за счет гравитации и в фильтре 13 (фиг.1, 2) при давлении исходного потока. Жидкая фаза отводится под давлением исходного газа по патрубку 14. Очищенная газовая фаза перед соплом 3 имеет параметры, представленные в таблице 4.
Таблица 2 |
Начальные параметры потока 2 на выходе из сопла 3 |
П.п. |
Наименование параметра |
Размерность |
Газовая фаза |
Жидкая фаза |
1 |
2 |
3 |
4 |
5 |
1 |
Режим истечения |
число Маха |
1,5 |
 |
2 |
Статическое давление, Р2 |
МПа |
4,51 |
 |
3 |
Статическая температура, Т2 |
°С |
минус 88 |
 |
4 |
Массовая доля |
 |
0,9877 |
0,0123 |
5 |
Молекулярная масса фаз |
 |
16,0 |
30,98 |
6 |
Плотность фаз |
кг/м3 |
74,66 |
434 |
7 |
Удельная теплоемкость фаз |
кДж/(кмоль град.) |
75,07 |
78,66 |
8 |
Фактор сжимаемости |
 |
0,6041 |
 |
9 |
Cp/Cv |
 |
1,125 |
 |
10 |
Вязкость |
Па·с |
1,049 10-5 |
1,28, 10-4 |
Таблица 3 |
Параметры потока 1 после теплообмена |
П.п. |
Наименование параметра |
Размерность |
Газовая фаза |
Жидкая фаза |
1 |
2 |
3 |
4 |
5 |
1 |
Давление, P1 |
МПа |
16,0 |
 |
2 |
Температура, T1 |
°С |
минус 30 |
 |
3 |
Массовая доля фаз в сверхзвуковом потоке |
 |
0,63 |
0,37 |
4 |
Молекулярная масса фаз |
 |
16,2 |
30,98 |
5 |
Плотность фаз |
кг/м3 |
74,66 |
430 |
6 |
Удельная теплоемкость фаз |
кДж/(кмоль град.) |
75,07 |
78,66 |
7 |
Фактор сжимаемости |
 |
0,6041 |
 |
9 |
Cp/Cv |
 |
1,125 |
 |
10 |
Вязкость |
Па·с |
1,049·10-5 |
1,28·10-4 |
Таблица 4 |
Параметры очищенного газовой фазы после фильтра 13 перед соплом 3 |
П.п. |
Наименование параметра |
Размерность |
Газовая фаза |
Жидкая фаза |
1 |
2 |
3 |
4 |
5 |
1 |
Давление, P1 |
МПа |
15,95 |
 |
2 |
Температура, T1 |
°С |
Минус 30 |
 |
3 |
Массовая доля фаз |
 |
0,999 |
0,001 |
4 |
Молекулярная масса фаз |
 |
16,2 |
30,98 |
5 |
Плотность фаз |
кг/м3 |
74,66 |
434 |
6 |
Удельная теплоемкость фаз |
кДж/(кмоль град.) |
75,07 |
78,66 |
7 |
Фактор сжимаемости |
 |
0,6041 |
 |
9 |
Cp/Cv |
 |
1,125 |
 |
10 |
Вязкость |
Па·с |
1,049·10-5 |
1,28·10-4 |
Очищенная газовая фаза подается в сопло 3, в котором она изоэнтальпийно расширяется. Расширенный поток на выходе из сопла 3 имеет параметры, представленные в таблице 2. При температуре минус 88°С происходит дополнительная конденсация углеводородных компонентов. Конденсат отделяется от расширенного и охлажденного газа 2 за счет вихревого движения после завихрителя 15. Этот конденсат поступает в камеру 16 и отводится по патрубку 17 под давлением расширенного газа. После такой очистки газовая фаза имеет параметры, представленные в таблице 5.
Таблица 5 |
Параметры очищенного потока 2 |
Пп. |
Наименование параметра |
Размерность |
Газовая фаза |
Жидкая фаза |
1 |
2 |
3 |
4 |
5 |
1 |
Режим истечения |
число Маха |
1,5 |
 |
2 |
Статическое давление, Р2 |
МПа |
4,51 |
 |
3 |
Статическая температура, Т2 |
°С |
минус 88 |
 |
4 |
Массовая доля |
 |
0,9988 |
0,00012 |
5 |
Молекулярная масса фаз |
 |
16,1 |
19,9 |
6 |
Плотность фаз |
кг/м3 |
73,89 |
234 |
7 |
Удельная теплоемкость фаз |
кДж/(кмоль гр.) |
75,6 |
77,66 |
8 |
Фактор сжимаемости |
 |
0,70 |
 |
9 |
Ср/Сv |
 |
1,125 |
 |
10 |
Вязкость |
Па·с |
1,049·10-5 |
1,28·10-4 |
По мере продвижения потока 2 очищенной таким образом газовой фазы по термогазодинамической камере 11 он нагревается при теплообмене с исходным газом 1. Перед диффузором 8 нагретый поток очищенного газа 2 имеет параметры, представленные в таблице 6.
В диффузоре 8 очищенный газовый поток затормаживается и восстанавливает давление. Параметры очищенного потока после диффузора представлены в таблице 7.
Таблица 6 |
Параметры потока 2 на входе в диффузор 8 |
П.п. |
Наименование параметра |
Размерность |
Газовая фаза |
Жидкая фаза |
1 |
2 |
3 |
4 |
5 |
1 |
Режим истечения |
число Маха |
1,5 |
 |
2 |
Статическое давление, Р3 |
МПа |
4,5 |
 |
3 |
Статическая температура, Т3 |
°С |
минус 28 |
 |
4 |
Массовая доля |
 |
0,9999 |
0,0001 |
5 |
Молекулярная масса фаз |
 |
16,2 |
20,98 |
6 |
Плотность фаз |
Кг/м3 |
73,89 |
234 |
7 |
Удельная теплоемкость фаз |
кДж/(кмоль град.) |
75,6 |
78,6 |
8 |
Фактор сжимаемости |
 |
0,70 |
 |
9 |
Ср/Сv |
 |
1,125 |
 |
10 |
Вязкость |
Па·с |
1,049·10-5 |
1,28·10-4 |
Таблица 7 |
Параметры потока 2 на выходе диффузора 8 |
П.п. |
Наименование параметра |
Размерность |
Газовая фаза |
Жидкая фаза |
1 |
2 |
3 |
4 |
5 |
1 |
Режим истечения |
число Маха |
М<<1 |
 |
2 |
Скорость |
м/с |
20 |
 |
2 |
Статическое давление, Р4 |
МПа |
13,34 |
 |
3 |
Статическая температура, Т4 |
°С |
плюс 30,1 |
 |
4 |
Массовая доля |
 |
0,999999 |
0,000001 |
5 |
Молекулярная масса фаз |
 |
16,2 |
19,87 |
6 |
Плотность фаз |
кг/м3 |
90,66 |
237 |
7 |
Удельная теплоемкость фаз |
кДж/(кмоль град.) |
75,62 |
78,67 |
8 |
Фактор сжимаемости |
 |
0,75 |
 |
9 |
Ср/Сv |
 |
1,125 |
 |
10 |
Вязкость |
Па·с |
1,049·10-5 |
1,28·10-4 |
Очищенный газ предложенным способом практически не содержит жидкой фазы и имеет следующий компонентный состав: СН4 – 0,9969766; С2Н6 – 0,00301; C3H8– 0,000012; С4Н10 – 0,000011; C5H12 – 0,0000003. Он не содержит компонентов С6 + выше, и из него практически удалены С3Н8, С4Н10, C5H12. Таким образом, предложенный газодинамический способ сепарации обладает высокой эффективностью. Причем энергетические затраты на его реализацию составляют 16,25% от исходного давления.
Пример 2.
При реализации предлагаемого способа газодинамической сепарации придание при теплообмене исходному газу 1 винтообразного движения путем его закрутки через тангенциально установленный входной патрубок 18 (фиг.3, 4) увеличивает на 7÷10% время его теплообмена. При этом на 1,5÷3% повышается эффективность конденсации компонентов. За счет центробежных сил дополнительно увеличивает эффективность отделения жидкости от газа. В комплексе эффективность процесса сепарации повышается на 3÷4%.
Пример 3.
При реализации способа подача исходного газа сквозь капиллярно-пористую структуру 19 (фиг.5), например сквозь металлокерамический фильтрационный материал, имеющий радиусы капилляров от 2 до 7 мкм и пористость 0,3÷0,4, ускоряет процесс конденсации. За счет капиллярных явлений температура точки росы для всех конденсируемых компонентов снижается на 1,5÷2°С без затрат энергии давления. Затраты энергии давления газа, как известно, оцениваются по интегральному эффекту Джоуля-Томпсона, который для углеводородов имеет значение 0,33÷0,36°С на 0,1 МПа. Следовательно, снижение затрат энергии давления составляет 0,417÷0,606 МПа.
Пример 4.
При реализации предлагаемого способа ввод (фиг.6) в исходный газ при его теплообмене ингибитора гидратообразования, например метанола, по трубопроводу 20 в нескольких местах 21-23 по потоку позволяет не допустить:
– появления кристаллогидратов при наличии в газе паров воды, тем самым снизить затраты холода (соответственно энергию давления) на кристаллизацию;
– аварийных ситуаций, связанных с перекрытием кристаллогидратами гидравлических сечений, по которым протекает обрабатываемый газ.
Этим повышается энергетическая эффективность и надежность данного способа сепарации.
Пример 5.
Ввод в исходный газ при его теплообмене абсорбентов позволяет расширить возможности способа газодинамической сепарации. Например, ввод:
– керосиновых фракций по трубопроводу 20 в трех точках аппарата 21-23 (фиг.6) позволяет повысить эффективность конденсации на 15-25% углеводородных компонентов в интервале температур 15-40°С охлаждаемого газа 1 и не допустить их дегазации при удалении конденсата, что повышает эффективность сепарации;
– диэтиленгликоля или триэтиленгликоля позволяет предварительно осушить исходный газ при температурах 15÷30°С от паров воды, тем самым снизить энергетические затраты холода на ее конденсацию, уменьшить вероятность появления кристаллогидратов и в конечном итоге повысить эффективность очистки газа;
– моноэтаноламина позволяет очистить газ от кислых компонентов (CO2 и Н2S), тем самым расширить функциональные возможности способа и повысить в конечном итоге его эффективность.
Таким образом, в заявленном способе газодинамической сепарации было достигнуто повышение эффективности газодинамической сепарации и снижение затрат энергии – давления газа.
Формула изобретения
1. Способ газодинамической сепарации, включающий подачу потока высоконапорного многокомпонентного углеводородного газа в сопло, его изоэнтальпийное расширение и охлаждение при течении в сопле, конденсацию компонентов в охлажденном потоке газа, отделение конденсата от газовой фазы, удаление очищенного газа и конденсата, повышение давления очищенного газового потока путем его торможения в диффузоре, отличающийся тем, что исходный поток газа предварительно охлаждают путем теплообмена с потоком газа, истекающего из сопла, компоненты конденсируют, отделяют от газовой фазы и удаляют при давлении исходного газа или (и) давлении газа после его расширения в сопле, газовую фазу подают в сопло после ее очистки от конденсата при давлении исходного газа, а давление расширенного и очищенного газового потока повышают после его теплообмена с исходным газом.
2. Способ по п.1, отличающийся тем, что теплообмен производят в противотоке.
3. Способ по п.1, отличающийся тем, что при теплообмене исходному газу придают винтообразное движение.
4. Способ по п.1, отличающийся тем, что при теплообмене исходный газ подают сквозь капиллярно-пористую структуру.
5. Способ по п.1, отличающийся тем, что при теплообмене в исходный газ вводят ингибиторы гидратообразования и (или) абсорбенты.
РИСУНКИ
PC4A – Регистрация договора об уступке патента СССР или патента Российской Федерации на изобретение
Прежний патентообладатель:
Закрытое акционерное общество “Центральное конструкторское бюро нефтегазовой промышленности”, Зиберт Генрих Карлович
(73) Патентообладатель:
Зиберт Генрих Карлович
(73) Патентообладатель:
Валиуллин Илшат Минулович
Договор № РД0058360 зарегистрирован 17.12.2009
Извещение опубликовано: 27.01.2010 БИ: 03/2010
|
|