(21), (22) Заявка: 2007148885/11, 29.12.2007
(24) Дата начала отсчета срока действия патента:
29.12.2007
(46) Опубликовано: 20.04.2009
(56) Список документов, цитированных в отчете о поиске:
ПУТЬ И ПУТЕВОЕ ХОЗЯЙСТВО, 11, 1959, с.47, 48. JP 2000104202 А, 11.04.2000. JP 2006214269 А, 17.08.2006. JP 2001279602 А, 10.10.2001. CS 8208925 В1, 20.03.1984. ЖЕЛЕЗНЫЕ ДОРОГИ МИРА, 1, 2006, с.65-69.
Адрес для переписки:
127521, Москва, 17-й пр-д Марьиной Рощи, 9, ЗАО “ИМЭТСТРОЙ”, отделение интеллектуальной собственности
|
(72) Автор(ы):
Бикбау Марсель Янович (RU), Мирошников Алексей Иванович (RU), Лёвин Борис Алексеевич (RU)
(73) Патентообладатель(и):
Закрытое акционерное общество “ИМЭТСТРОЙ” (ЗАО “ИМЭТСТРОЙ”) (RU)
|
(54) УСТРОЙСТВО ВЕРХНЕГО СТРОЕНИЯ ПУТИ
(57) Реферат:
Изобретение относится к строительству железных дорог, преимущественно к устройствам верхнего строения пути. В устройстве верхнего строения пути преднапряженные железобетонные плиты стянуты вдоль полотна пути в пакеты длиной от 10 до 100 м напряженными стальными канатами, проходящими в средней части плит. Между плитами на канаты надеты уплотняющие резиновые элементы. Концы напряженных канатов снабжены анкерами, размещенными в крепежных прямоугольных пустотах и омоноличенными бетоном. Между плитами после натяжения стальных канатов и их закрепления оставлен зазор от 50 до 100 мм. Технические результаты заключаются в обеспечении надежности и равнопрочности пути по его протяжению, включая решение проблемы относительной осадки краев (стыков) соседних плит; в обеспечении высокой изгибной прочности рельсов без увеличения массы погонного метра с возможным ее снижением; в ускорении строительства и снижении продолжительности ремонтов верхнего строения пути; в повышении уровня механизации строительства и ремонта железных дорог, а также в повышении безопасности движения и долговечности подрельсовых оснований путей. 1 з.п. ф-лы, 3 ил.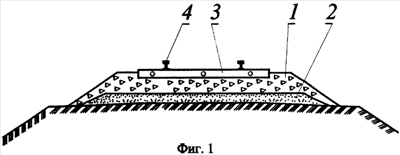
Предлагаемое изобретение относится к строительству железных дорог, преимущественно к устройствам верхнего строения пути, и предназначено для применения в технике железнодорожного транспорта.
В настоящее время железнодорожный транспорт как в России, так и во всем мире в плане повышения надежности железнодорожных путей с шпальным основанием близок к пределу возможностей.
Надежность железнодорожного пути по фундаментальной работе В.С.Лысюк, В.Н.Сазонова и Л.В.Башкатовой – свойство пути сохранить в условленных пределах значение всех параметров, характеризующих способность выполнить требуемые функции (бесперебойный пропуск поездов с установленной скоростью) в заданных условиях эксплуатации (текущего содержания и ремонтов). При этом количественно надежность пути оценивается численными значениями показателей его безотказности, долговечности и ремонтопригодности [1].
В условиях возрастания объемов перевозок, скоростей движения поездов в последние десятилетия стремление к повышению надежности железнодорожных путей в отечественной и зарубежной практике осуществлялось по направлениям:
– повышения изгибной жесткости рельсов путем увеличения погонной массы рельсов;
– повышения жесткости рельсового основания путем увеличения густоты расположения шпал;
– повышения жесткости балласта путем увеличения толщины балластного слоя щебня под шпалами.
Однако в настоящее время укрепилось общее мнение, что дальнейшее увеличение погонной массы рельсов свыше 65 кг/м нецелесообразно – в течение 1950-2000 г.г. масса рельса в России была повышена с 38,4 до 64,4 кг/м. Доля протяжения главного пути с рельсами Р65 и Р75 уже достигла 95%.
Тем не менее о низкой эффективности дальнейшего повышения погонной массы рельсов типа Р65 и Р75 свидетельствует доля их отказов по контактно-усталостным дефектам, которая по сравнению с 1950 г. для рельсов с q=38,4 кг/м возросла для всех типов в 2000 г. до 45%, а для рельсов Р75 до 64% [1].
Густота укладки шпал в настоящее время уже повысилась до 1840-2000 шт/км железнодорожного пути, что существенно удорожает как строительство новых, так и ремонт старых путей. Толщина щебеночного балласта на отечественных дорогах уже достигает 1 м, а кое-где его превышает. Наблюдающееся во всем мире повышение скоростей и осевых нагрузок при железобетонных шпальных основаниях намного увеличило вибрацию пути и понизило сопротивление вибрации всех элементов пути, ухудшило условия работы балластной призмы и земляного полотна [2, 3].
Верхнее строение пути является несущей конструкцией железнодорожного пути, воспринимающей нагрузки от колес подвижного состава и направляющей их движение [4].
Организация скоростного движения поездов и увеличение нагрузок на ось подвижного состава (в перспективе до 30 т/ось) вызывает значительный рост напряженно-деформированного состояния всех элементов железнодорожного пути. Возрастание грузонапряженности ведет к интенсивному накоплению остаточных деформаций пути, что осложняет обеспечение надежности пути.
Специалисты считают, что единственно эффективным путем повышения надежности и объемов наработки путей, обеспечения безопасности железнодорожного транспорта является интенсивные методы, связанные с повышением указанных факторов за счет конструктивного совершенствования железных дорог без увеличения их материалоемкости.
Кроме того, при поиске лучших инженерных решений для развития железнодорожного транспорта необходимо учесть следующие пожелания эксплуатационников:
– создание пути равнопрочного по его протяжению;
– высокую изгибную прочность рельсов без увеличения массы погонного метра рельса;
– минимизация неровностей на железнодорожном пути;
– ускорение строительства новых и упрощение замены при ремонте, снижение сроков простоя пути при ремонтах полотна.
Значительное внимание инженеров уже многие десятилетия привлекает возможность перехода от шпальных подрельсовых оснований к железобетонным из сборных плит, балок, рам или лежней. В отдельных странах есть определенный опыт применения сплошных железобетонных оснований [2, 3, 5].
В цитированных работах приводятся различные данные о многочисленных преимуществах сплошных железобетонных оснований, как сборных, так и монолитных, однако десятилетия упорных исследований не позволили в мировой практике железнодорожного транспорта заменить шпальное основание железнодорожных путей. Практическое применение сплошных (блочных) железобетонных опор рельсов применяется только при прокладке отдельных путей на мостах и тоннелях, а также как основания трамвайных путей.
Не случайно, современный СНиП 32-01-95 «Железные дороги колеи 1520 мм» в разделе 5 «Верхнее строение пути» не предусматривает применение железобетонных плит, рам или подобных опор.
Кроме того, авторы работы [1] в качестве будущего железных дорог предполагают переход от прочного пути к надежному с учетом двух направлений стратегий:
1 – своевременную ликвидацию неровностей на колесах и рельсах, а также укладки виброзащитных железобетонных шпал с резиновыми прокладками;
2 – повышение безотказности и долговечности пути без увеличения его материалоемкости: изменение очертания верха головки рельсов по типу американских рельсов 132 RE, применение шарнирных стыковых накладок вместо клиновых, противораспорных костыльных подкладок, ликвидация избытка возвышения наружного рельса в кривых и укладка рельсовых стыков в разбежку, а не по наугольнику.
Ведущие специалисты железнодорожники практически не видят сегодня перспективы применению сборных блочных или монолитных железобетонных оснований, что связано с тем, что такие основания обычно связаны:
– с излишней жесткостью основания, оказывающей влияние на быстрый износ колесных пар;
– незначительным влиянием на изгибную прочность рельсов;
– недостаточной равнопрочностью основания пути по протяжению, особенно при применении сборных железобетонных плит заводского изготовления, тем более применение монолитных железобетонных оснований для климатических условий России не реально;
– с большим расходом железобетона.
Это связано с определенными недостатками сплошных подрельсовых оснований из железобетона (сборных или монолитных), устранению которых посвящено предлагаемое изобретение.
Ознакомление с современным уровнем техники применения сборных блочных железобетонных оснований позволяет указать, в частности, устройство верхнего строения пути на железобетонных подрельсовых основаниях в виде продольных лежней с гнездами [6]. Лежни соединяют друг с другом горизонтальными поперечными железобетонными брусами, после чего в канавки укладывают резиновые прокладки, на которые затем устанавливают рельсы и закрепляют их рельсовыми скреплениями.
Однако известное устройство верхнего строения пути обладает значительной жесткостью, а проложенные между рельсами и лежнями резиновые прокладки быстро утрачивают упругость, а их замена требует полного снятия и новой установки рельсов. Кроме того, в этой несущей подрельсовой конструкции продольные лежни требуют точной установки по оси пути, в противном случае допущенные при их укладке нарушения положения пути в плане увеличиваются по мере пропуска многотоннажных грузов и трудно поддаются исправлению при текущем содержании.
Негативно влияет на равнопрочность пути и различная осадка соседних лежней, которую весьма сложно сделать одинаковой, так как устройство по [6] не предусматривает стыковку лежней вдоль пути.
Известно также устройство верхнего строения пути, включающее укладку на монолитное бетонное основание подрельсового основания из последовательно размещенных преднапряженных бетонных плит, установку упругих элементов между плитами и прикрепление к плитам с помощью скреплений рельсов [7]. Для сокращения времени на демонтаж верхнего строения пути между монолитным бетонным основанием, а также нижней и боковой частями подрельсового основания устанавливают упругие прокладки, а для отвода воды из подрельсовой зоны упругие прокладки между монолитным бетонным основанием и нижней частью подрельсового основания устанавливают с зазором.
Однако скрепление друг с другом преднапряженных бетонных плит подрельсового основания осуществляется в известном устройстве посредством уложенной на подрельсовое основание рельсовой колеи, что приводит под действием движущихся вертикальных нагрузок к относительным горизонтальным продольным перемещениям рельсов и плит друг относительно друга и вследствие этого – к возрастанию сил трения в зоне узла скрепления, осложнению работы промежуточных скреплений и верхнего строения пути в целом.
Наиболее близким к предлагаемому является устройство по техническому решению, описанном в [8]. По указанному техническому решению, железобетонные плиты размером 2,3×0,5×0,17 м, армированные тремя рядами продольно расположенных предварительно напряженных, двойных стальных прутьев, уложены на указанное гравийно-песчаное основание, на поверхность которого насыпается и разравнивается слой песка.
На ровную поверхность песчаного покрытия укладываются указанные выше бетонные плиты с вставкой между торцами сплошных плит резиновых прокладок толщиной в несколько мм, при этом два десятка таких плит соединяется в одно звено длиной около 10 метров. Соединение плит в звено осуществляется с помощью железобетонных пластин – лаг в виде двух десятиметровых плетей, вставленных в специальные углубления в боковой поверхности железобетонных плит и имеющих возможность предварительного напряжения. Это позволяет поднимать звено из 20 плит с помощью портальных кранов и укладывать звено на полотно. Звенья между собой соединены с помощью соприкасающихся крайних плит, скрепленных короткими железобетонными лагами, которые позволяют уложенным звеньям образовать неразрывное подрельсовое основание пути, на которое укладываются и скрепляются рельсы.
Предлагаемое по прототипу техническое решение позволяет, по мнению автора, существенно уменьшить массу балласта и ускорить строительство, замену путей при ремонте, а кроме того, радикально повысить долговечность рельсового основания. В этом случае лаги могут служить средством для подтягивания или ослабления полотна пути, так как к ним снаружи предполагаются доступы.
К недостаткам предлагаемого по прототипу решению относится то, что напряжение железобетонных лаг, расположенных вдоль полотна в боковых торцах плит, не позволяет обжать равномерно друг к другу вдоль пути боковые поверхности плит шириной 0,5 м в количестве 5 шт друг к другу по всей длине плит, так как плечо между напрягаемыми лагами составляет около 2,3 м. Кроме того, прикрепляемые плиты необходимо периодически подбивать песком или мелким щебнем, для чего авторами предлагается применение специального прибора и ручных домкратов.
Переменные нагрузки на плиты, разделенные прокладками, вызывают смещение плит относительно соседней и ее повышенное давление на монолитное основание, которое претерпевает интенсивные периодические воздействия и быстро разрушается.
Известное устройство верхнего строения пути сокращает время его монтажа. Однако из-за большого количества стыков в подрельсовом основании известной конструкции возникают значительные ударно-динамические воздействия на путь, что приводит к резкому его ослаблению, существенному снижению стабильности пути. Кроме того, в связи с увеличением осевых нагрузок и особенно грузонапряженности железнодорожного пути возрастают требования повышенной прочности блоков для подрельсового основания, что, прежде всего, сказывается на их толщине в сторону увеличения, а следовательно, возрастет расход бетона на изготовление блоков, эксплуатационные расходы на содержание пути.
Целью предлагаемого изобретения является устранение указанных недостатков, а также обеспечение:
– надежности и равнопрочности пути по его протяжению, включая решение проблемы относительной осадки краев (стыков) соседних плит;
– высокой изгибной прочности рельсов без увеличения массы погонного метра с возможным ее снижением;
– ускорения строительства и снижение продолжительности ремонтов верхнего строения пути;
– повышения уровня механизации строительства и ремонта железных дорог;
– повышения безопасности движения и долговечности подрельсовых оснований путей.
Поставленная цель достигается тем, что в устройстве верхнего строения пути, включающем уложенное на балласт подрельсовое основание из последовательно размещенных преднапряженных железобетонных плит, упругие элементы между плитами и прикрепленные к плитам с помощью рельсовых скреплений рельсы, плиты стянуты вдоль полотна пути в пакеты длиной от 10 до 100 м напряженными стальными канатами, проходящими в средней части плит, при этом между плитами на стальные канаты надеты уплотняющие упругие, предпочтительней резиновые элементы, а стальные канаты в количестве от трех до семи расположены: один на оси пути, а остальные – симметрично оси пути на расстоянии, начиная от края плит, кратном минимальной толщине плиты, причем концы напряженных канатов снабжены анкерами, размещенными в крепежных прямоугольных пустотах плит и омоноличенными бетоном, а между плитами после натяжения канатов и их закрепления выдержан зазор от 50 до 100 мм. Кроме того, крепежные прямоугольные пустоты плит и крепления анкеров с канатами смещены вдоль пути относительно друг друга на расстояние, взятое в пределах расстояний между соседними стальными канатами.
Сущность заявляемого технического решения заключается в следующем. Одновременная работа в предлагаемой конструкции верхнего строения пути стальных рельсов и стальных канатов, легко передающих подвижные нагрузки на бетон плит, которые имеют значительную поверхность опирания, в частности, превосходящую в 2 -3 раза по площади опирания на балласт применяемое сегодня шпальное подрельсовое основание, обеспечивает амортизацию движущегося состава на балластном массиве и не вызывает повышенного износа колесных пар. Весьма важна при этом функция упругих прокладок между плитами, исключающая жесткую реакцию плит железобетонного полотна на проходящие нагрузки, амортизирующая горизонтальные нагрузки, вызывающие угон рельсов и поперечный сдвиг.
Кроме того, бетонные плиты подрельсового основания, стянутые стальными канатами в пакеты, образуют преднапряженную бетонную конструкцию, в которой бетонные плиты работают с балластным основанием полным сечением в отличие от плит подрельсового основания прототипа, лишь нижняя часть сечения которых является рабочей. Это позволяет в заявляемом устройстве существенно повысить осевые нагрузки и грузонапряженность пути, уменьшить толщину бетонной плиты, что заметно снизит расход бетона на изготовление подрельсового основания, а следовательно, эксплуатационные расходы на содержание и ремонт пути. Одновременно с уменьшением толщины плит, стянутых в предлагаемом верхнем строении пути в пакеты, уменьшаются прогибы концевых участков пакетов, вследствие чего существенно повышается стабильность пути в целом.
Стягивание бетонных плит в пакеты длиной от 10 до 100 м позволяет резко сократить количество стыковых соединений, являющихся самым напряженным и слабым местом в пути, и, таким образом, уменьшить ударно-динамические воздействия на железнодорожный путь, что особенно важно для магистральных линий железных дорог с высокой интенсивностью и скоростями движения поездов.
В части преднапряженных плит предусмотрены небольшие прямоугольные пустоты, симметричные оси сквозных продольных канатов, в которых выходят для протяжки и натяжения стальные канаты и где после их натяжения концы канатов закрепляются анкерами и омоноличиваются бетоном. На готовом, как изложено подрельсовом основании, смонтированном из пакетов преднапряженных бетонных плит, с помощью скреплений крепят рельсы.
Предлагаемое устройство верхнего строения пути изображено на фиг.1 – вертикальное сечение пути; на фиг.2 – стык преднапряженных плит; на фиг.3 – двусторонний анкер со стальными канатами после натяжения. Устройство на земляном полотне 1 содержит балластный уплотненный щебеночный слой 2, на котором расположены предварительно напряженные железобетонные плиты 3 со сквозными каналами вдоль пути, в которых размещены стальные канаты 5, плиты 3 образуют подрельсовое основание, на котором закреплены стальные рельсы 4 (фиг.1). Плиты 3 стянуты стальными канатами 5 в пакеты длиной от 10 до 100 м, к которым с помощью рельсовых скреплений прикреплены рельсы. При этом стальные канаты заключены в пластиковые изолирующие оболочки, обеспечивающие долговечную антикоррозийную защиту стальных канатов, на эти канаты между плитами надеты цилиндрические упругие элементы 6, предпочтительней резиновые (фиг.2). Стальные канаты 5, расположенные в сквозных каналах 7, натягиваются с помощью домкратов, а концы их закрепляются анкерами и омоноличиваются бетоном в прямоугольных пустотах 8 (фиг.3).
Монтаж верхнего строения пути производится следующим образом. На земляное полотно 1 укладывают балластный щебеночный слой 2, а на него преднапряженные железобетонные плиты 3. Затем плиты 3 стягивают стальными канатами 5 в пакеты длиной от 10 до 100 м таким образом, чтобы после натяжения стальных канатов и их закрепления между плитами оставался зазор величиной от 50 до 100 мм, в котором на стальные канаты надеты упругие элементы 6. К смонтированному таким образом подрельсовому основанию с помощью рельсовых скреплений прикрепляют рельсы 4.
Заявляемое верхнее строение пути благодаря применению подрельсового основания из преднапряженных бетонных плит, стянутых стальными канатами в бесстыковые длинномерные конструкции, отличает устойчивость и значительная несущая способность пути. Одновременно благодаря работе бетона по всему сечению плитной конструкции подрельсового основания уменьшается не только толщина применяемых бетонных плит, что заметно сокращает расходы на содержание и ремонт пути, но и уменьшаются прогибы пакетов плит в стыках, что радикально повышает стабильность железнодорожного пути.
Размер предлагаемых пакетов плит, количество и длины стягивающих канатов (10-100 м) являются оптимальными и соответствуют достижению целей изобретения требованиям механизации строительства. При этом крепежные пустоты плит и крепления анкеров со стальными канатами могут быть смещены относительно друг друга на расстояние, взятое в пределах расстояний между соседними каналами.
Заявляемое верхнее строение пути позволяет благодаря стягиванию бетонных плит, не прогибающихся на стальных канатах, но способных к вибрации для эффективного гашения периодических нагрузок, монтировать длинномерные конструкции – пакеты плит, которые обеспечивают равномерную передачу подвижных нагрузок на основную площадку земляного полотна, невзирая на вспучивание или осадку части полотна, возникающих при традиционной рельсовошпальной решетке пути.
Предлагаемое техническое решение позволяет строить гибкое, хорошо ориентированное горизонтально, без возможности просадки в стыках соседних плит, верхнее основание пути с повышенной изгибной прочностью рельсов и обеспеченной равнопрочностью пути. Значительная площадь опирания пакетов плит на балласт и затем земляное полотно позволяет существенно более эффективно (по сравнению с шпальным основанием) передавать нагрузки от движущего состава в грунт с минимализацией угона, поперечных сдвигов и других негативных явлений. Новое решение, тем более при применении бесстыковых рельсовых путей позволит повысить скорости движения поездов, снизить основное удельное сопротивление пути движению поездов и благодаря этому экономить топливо и электроэнергию на тягу.
Кроме того, снижаются объемы работ по выправке пути, интенсивность износа рельсов и, в конечном итоге, увеличиваются сроки службы и долговечность верхнего строения пути. Существенно сокращающиеся относительные горизонтальные продольные перемещения между плитами подрельсового основания и рельсами обеспечивают, как выше отмечалось, снижение трения в зоне узла крепления рельсов, благодаря чему повышается эксплуатационная надежность, безопасность и стабильность железнодорожного пути.
Предлагаемое верхнее строение пути позволяет разработать новые конструкции верхнего строения пути, которые могут гибко реагировать на смещения земной поверхности и снизить влияние деформаций на скоростные возможности подвижного состава.
Источники информации
1. B.C.Лысюк, В.Н.Сазонов, Л.В.Башкатова. Прочный и надежный железнодорожный путь. – М.: НКЦ «Академкнига», 2003 г. – 589 с.
2. Б.И.Мушкатин. Путь на железобетоном основании. – Ж-л «Путь и путевое хозяйство». – 1957, 2, с.10-12.
3. Современные конструкции верхнего строения железнодорожного пути. Под ред. В.Г.Альберхта и А.Ф.Золотирского. – М.: Транспорт, 1975, – 280 с.
4. И.В.Прокудин, И.А.Грачев, А.Ф.Колос. Организация переустройства железных дорог под скоростное движение поездов. – М.: Изд-во Маршрут, 2005, – 716 с.
5. Ю.Д.Волошко, A.M.Микитенко. Рельсовый путь с блочными железобетонными опорами. – М.: Транспорт, 1980, – 175 с.
6. Авторское свид-во СССР 1461810, кл. Е01В 3/12, 1987 г.
7. Авторское свид-во СССР 908979, кл. Е01В 2/00, 1979 г.
8. М.Главаты. Замена шпал железобетонными плитами. Зарубежная техника. – Ж-л. «Путь и путевое хозяйство». – 1959, 11, с.47-48.
Формула изобретения
1. Устройство верхнего строения пути, включающее уложенное на балласт подрельсовое основание из последовательно размещенных преднапряженных железобетонных плит, упругие элементы между плитами и прикрепленные к плитам с помощью рельсовых скреплений рельсы, отличающееся тем, что плиты стянуты вдоль полотна пути в пакеты длиной от 10 до 100 м напряженными стальными канатами, проходящими в средней части плит, при этом между плитами на стальные канаты надеты уплотняющие резиновые элементы, а стальные канаты в количестве от трех до семи расположены: один на оси пути, а остальные – симметрично оси пути на расстоянии, начиная от края плит, кратном минимальной толщине плиты, причем концы напряженных канатов снабжены анкерами, размещенными в крепежных прямоугольных пустотах плит и омоноличенными бетоном, а между плитами после натяжения стальных канатов и их закрепления выдержан зазор от 50 до 100 мм.
2. Устройство верхнего строения пути по п.1,отличающееся тем, что крепежные прямоугольные пустоты плит и крепления анкеров со стальными канатами смещены вдоль пути относительно друг друга на расстояние, взятое в пределах расстояний между соседними канатами.
РИСУНКИ
|