|
(21), (22) Заявка: 2007143726/13, 26.11.2007
(24) Дата начала отсчета срока действия патента:
26.11.2007
(46) Опубликовано: 20.04.2009
(56) Список документов, цитированных в отчете о поиске:
Материалы международной научно-практической конференции «Современные проблемы технологии производства, хранения, переработки и экспертизы качества сельскохозяйственной продукции» (26-28.02.2007), т.2. – Мичуринск: Изд-во ФГОУ ВПО МичГАУ, т.2, с.323-325. RU 2278527 С1, 25.04.2005. RU 2226844 С1, 20.04.2004. RU 2079276 C1, 20.05.1997.
Адрес для переписки:
394000, г.Воронеж, пр-кт Революции, 19, Воронежская государственная технологическая академия (ВГТА), консалтинговый отдел
|
(72) Автор(ы):
Шевцов Александр Анатольевич (RU), Лыткина Лариса Игоревна (RU), Дранников Алексей Викторович (RU), Шенцова Евгения Сергеевна (RU), Маджидов Рустам Маджидович (RU), Бугакова Людмила Владимировна (RU)
(73) Патентообладатель(и):
Государственное образовательное учреждение высшего профессионального образования Воронежская государственная технологическая академия (RU)
|
(54) СПОСОБ УПРАВЛЕНИЯ ПРОЦЕССОМ ПРИГОТОВЛЕНИЯ КОМБИКОРМОВ
(57) Реферат:
Изобретение относится к автоматизации технологических процессов и может быть использовано при автоматизации процесса приготовления комбикормов. Способ включает смешивание рассыпного комбикорма с горячими гранулами, выдерживание полученной смеси в теплообменнике, ее охлаждение воздухом, измельчение, фракционирование смеси рассыпного комбикорма и измельченных гранул на крупную, среднюю и мелкую фракции с последующим покрытием в смесителе средней фракции слоем жира и выводом ее в качестве готовой продукции, возврат крупной фракции на доизмельчение и отвод мелкой фракции на гранулирование, охлаждение воздуха в испарителе и его подачей в режиме замкнутого цикла на охлаждение смеси рассыпного комбикорма и горячих гранул. Воздух перед подачей его на охлаждение смеси рассыпного комбикорма и горячих гранул охлаждают в теплообменнике-рекуператоре пароэжекторной холодильной машины, работающей по замкнутому термодинамическому циклу. Используют парогенератор для получения рабочего пара, который под давлением направляют в сопло эжектора, создавая при этом пониженное давление и температуру 4-7°С в испарителе пароэжекторной холодильной машины с подачей паров хладагента в теплообменник-рекуператор для охлаждения воздуха. Образовавшуюся смесь паров хладагента и рабочего пара после эжектора разделяют на два потока, один из которого направляют в пресс-гранулятор, а другой – в конденсатор для подогрева жира. Одну часть образовавшегося в конденсаторе водяного конденсата подают в испаритель для пополнения убыли воды, а другую вместе с конденсатом, образовавшимся при охлаждении воздуха в теплообменнике-рекуператоре, отводят сначала в сборник конденсата, а затем в парогенератор с образованием замкнутого цикла. В процессе охлаждения в теплообменнике пароэжекторной машины смеси рассыпного комбикорма с горячими гранулами дополнительно измеряют величину разрежения в испарителе и расход паров хладагента на входе и выходе из теплообменника-рекуператора, уровень конденсата в испарителе. По измеренным значениям влагосодержания воздуха до и после охлаждения смеси и его расходу в теплообменнике-рекуператоре определяют количество водяных паров в отработанном воздухе, по которому устанавливают коэффициент эжекции пароэжекторной холодильной машины воздействием на соотношение расходов рабочего пара, подаваемого в сопло эжектора, и эжектируемых паров хладагента, путем изменения расхода рабочего пара. Определяют текущее значение коэффициента теплопередачи от хладагента к воздуху через охлаждающую поверхность теплообменника-рекуператора по температуре воздуха на входе и выходе из теплообменника-рекуператора, температуре хладагента на входе в теплообменник-рекуператор и расходу воздуха, подаваемого на охлаждение смеси рассыпного комбикорма и горячих гранул. При отклонении температуры воздуха, подаваемого на охлаждение смеси рассыпного комбикорма и горячих гранул, от заданного интервала значений в сторону увеличения увеличивают коэффициент теплопередачи путем уменьшения коэффициента эжекции воздействием на увеличение расхода рабочего пара. При отклонении температуры воздуха, подаваемого на охлаждение смеси рассыпного комбикорма и горячих гранул, от заданного интервала значений в сторону уменьшения уменьшают коэффициент теплопередачи путем увеличения коэффициента эжекции воздействием на уменьшение расхода рабочего пара. По температуре жира после конденсатора устанавливают заданное давление жира перед форсунками на входе в смеситель. Использование изобретения позволит повысить качество приготовления комбикормов. 1 табл., 1 ил.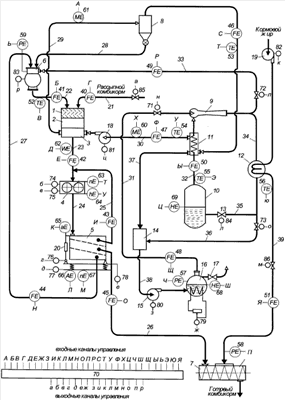
Изобретение относится к автоматизации технологических процессов и может быть использовано при автоматизации процесса приготовления комбикормов.
Наиболее близким по технической сущности и достигаемому эффекту является способ управления процессом приготовления комбикормов [Патент РФ 2278527, МПК7 A23K 1/00, A23N 17/00. Способ управления процессом приготовления комбикормов. / А.А.Шевцов, Л.И.Лыткина, О.П.Коломникова, В.В.Еремченко, С.А.Чибисов, 2005112085; заявлено 25.04.05; опубл. 27.06.06. Бюл. 18], включающий смешивание рассыпного комбикорма с горячими гранулами, вышедшими из пресс-гранулятора, выдерживание движущегося плотного слоя полученной смеси в теплообменнике, охлаждение смеси воздухом, отвод отработанного воздуха после охлаждения смеси сначала в циклон для очистки от содержащихся в нем взвешенных твердых частиц смеси, а затем на конденсацию содержащихся в нем водяных паров с последующей подачей в режиме замкнутого цикла на охлаждение смеси. В данном способе предусмотрено измельчение и фракционирование смеси на крупную, среднюю и мелкую фракции с последующим покрытием в смесителе посредством форсунок средней фракции слоем жира, подогретого в конденсаторе, и выводом ее в качестве готового продукта, возврат крупной фракции на доизмельчение и отвод мелкой фракции на гранулирование, получение насыщенного пара в парогенераторе с электронагревательными элементами и предохранительным клапаном, подачу пара в пресс-гранулятор, отвод взвешенных частиц, образовавшихся при очистке воздуха, из циклона в пресс-гранулятор. При этом предусмотрено измерение расхода рассыпного комбикорма, расхода и температуры горячих гранул, расходов крупной, средней и мелкой фракций, расхода жира, расхода и давления пара на тепловую обработку мелкой фракции в пресс-грануляторе, влагосодержания воздуха до и после охлаждения смеси, расхода и температуры очищенного воздуха, расхода и давления насыщенного пара после парогенератора, уровня конденсата в парогенераторе с воздействием на производительность парогенератора, расхода и температуры воздуха, подаваемого на охлаждение смеси рассыпного комбикорма с горячими гранулами.
Однако известный способ имеет следующие недостатки:
– вероятно отклонение качества готового продукта от требуемого вследствие выхода из строя используемой компрессионной теплонасосной установки, у которой надежность при эксплуатации ниже, чем, например, у пароэжекторной холодильной машины;
– дополнительные энергозатраты при приготовлении комбикорма, обусловленные необходимостью периодического размораживания «снеговой шубы», образующейся при охлаждении воздуха в испарителе теплонасосной установки;
– невысокая точность и надежность управления технологическими параметрами на всех стадиях процесса приготовления комбикормов в связи с отсутствием оперативного управления энергетическими потоками, что приводит к снижению качества готовой продукции.
Технической задачей изобретения является повышение качества готовой продукции, точности и надежности управления в процессе приготовления комбикормов, энергетической эффективности, снижение себестоимости готовой продукции.
Поставленная задача достигается тем, что в способе управления процессом приготовления комбикормов, включающем смешивание рассыпного комбикорма с горячими гранулами, вышедшими из пресс-гранулятора, выдерживание движущегося плотного слоя полученной смеси в теплообменнике, охлаждение этой смеси воздухом, отвод отработанного воздуха после охлаждения смеси сначала в циклон для очистки от содержащихся в нем взвешенных твердых частиц смеси, а затем на конденсацию содержащихся в нем водяных паров с последующей подачей в режиме замкнутого цикла на охлаждение смеси, измельчение и фракционирование смеси на крупную, среднюю и мелкую фракции с последующим покрытием в смесителе посредством форсунок средней фракции слоем жира, подогретого в конденсаторе, и выводом ее в качестве готового продукта, возврат крупной фракции на доизмельчение и отвод мелкой фракции на гранулирование, получение насыщенного пара в парогенераторе с электронагревательными элементами и предохранительным клапаном, подачу пара в пресс-гранулятор, отвод взвешенных частиц, образовавшихся при очистке воздуха, из циклона в пресс-гранулятор; измерение расхода рассыпного комбикорма, расхода и температуры горячих гранул, расходов крупной, средней и мелкой фракций, расхода жира, расхода и давления пара на тепловую обработку мелкой фракции в пресс-грануляторе, влагосодержания воздуха до и после охлаждения смеси, расхода и температуры очищенного воздуха, расхода и давления насыщенного пара после парогенератора, уровня конденсата в парогенераторе с воздействием на производительность парогенератора, расхода и температуры воздуха, подаваемого на охлаждение смеси рассыпного комбикорма с горячими гранулами, новым является то, что воздух перед подачей его на охлаждение смеси рассыпного комбикорма и горячих гранул предварительно охлаждают в теплообменнике-рекуператоре пароэжекторной холодильной машины, состоящей из эжектора, испарителя, теплообменника-рекуператора, конденсатора, регулирующего вентиля, сборника конденсата, насоса и парогенератора с предохранительным клапаном, работающих по замкнутому термодинамическому циклу, путем теплопередачи от хладагента, в качестве которого используется вода, к воздуху через разделяющую стенку поверхности теплообмена, полученный в парогенераторе рабочий пар под давлением направляют в сопло эжектора, при этом в испарителе пароэжекторной холодильной машины создается пониженное давление и температура, с последующей подачей эжектируемых паров хладагента из испарителя в теплообменник-рекуператор для охлаждения воздуха, подаваемого на охлаждение смеси рассыпного комбикорма с горячими гранулами, образовавшуюся смесь паров хладагента и рабочего пара после эжектора разделяют на два потока, один из которого направляют в пресс-гранулятор, а другой – в конденсатор для подогрева жира, причем одну часть образовавшегося в конденсаторе водяного конденсата подают в испаритель для пополнения убыли воды, а другую вместе с конденсатом, образовавшимся при охлаждении воздуха в теплообменнике-рекуператоре, отводят сначала в сборник конденсата, а затем в парогенератор с образованием замкнутого цикла, при этом дополнительно измеряют величину разрежения в испарителе и расход паров хладагента на входе и выходе из теплообменника-рекуператора, уровень конденсата в испарителе, по измеренным значениям влагосодержания воздуха до и после охлаждения смеси и его расходу в теплообменнике-рекуператоре определяют количество водяных паров в отработанном воздухе, по которому устанавливают коэффициент эжекции пароэжекторной холодильной машины воздействием на соотношение расходов рабочего пара, подаваемого в сопло эжектора, и эжектируемых паров хладагента, путем изменения расхода рабочего пара, определяют текущее значение коэффициента теплопередачи от хладагента к воздуху через охлаждающую поверхность теплообменника-рекуператора по температуре воздуха на входе и выходе из теплообменника-рекуператора, температуре хладагента на входе в теплообменник-рекуператор и расходу воздуха, подаваемого на охлаждение смеси рассыпного комбикорма и горячих гранул, причем при отклонении температуры воздуха, подаваемого на охлаждение смеси рассыпного комбикорма и горячих гранул, от заданного интервала значений в сторону увеличения увеличивают коэффициент теплопередачи путем уменьшения коэффициента эжекции воздействием на увеличение расхода рабочего пара, а при отклонении температуры воздуха, подаваемого на охлаждение смеси рассыпного комбикорма и горячих гранул, от заданного интервала значений в сторону уменьшения уменьшают коэффициент теплопередачи путем увеличения коэффициента эжекции воздействием на уменьшение расхода рабочего пара, при этом по температуре жира после конденсатора устанавливают заданное давление жира перед форсунками на входе в смеситель.
На чертеже представлена схема, реализующая предлагаемый способ.
Схема содержит гравитационный смеситель 1; теплообменник 2; охладитель 3; валковый измельчитель 4; просеивающую машину 5; пресс-гранулятор 6; смеситель 7; циклон 8; эжектор 9; испаритель 10; теплообменник-рекуператор 11; конденсатор 12; регулирующий вентиль 13; сборник конденсата 14; насос 15; парогенератор 16; предохранительный клапан 17; вентилятор 18; насос для жира 19, гидроцилиндр 20; линии: подачи рассыпного комбикорма 21 и горячих гранул 22 в гравитационный смеситель 1, подачи смеси гранул с рассыпным комбикормом 23 в валковый измельчитель 4, подачи продуктов измельчения 24 в просеивающую машину 5, возврата крупной фракции комбикорма на доизмельчение 25 в валковый измельчитель 4, подачи средней фракции 26 в смеситель 7, подачи мелкой фракции 27 в пресс-гранулятор 6, отвода взвешенных частиц 28 из циклона 8 в пресс-гранулятор 6, отвода отработанного воздуха 29 из охладителя 3 в циклон 8, подачи охлажденного воздуха 30 из теплообменника-рекуператора 11 в охладитель 3, отвода рабочего пара 31 из парогенератора 16 в эжектор 9, отвода паров хладагента 32 из испарителя 10 через теплообменник-рекуператор 11 в эжектор 9, подачи смеси паров хладагента и рабочего пара 33 в пресс-гранулятор 6, подачи смеси паров хладагента и рабочего пара 34 в конденсатор 12; отвода конденсата 35 из конденсатора 12 в испаритель 10, отвода конденсата 36 из конденсатора 12 в сборник конденсата 14, подачи конденсата 37 из теплообменника-рекуператора 11 в сборник конденсата 14, подачи конденсата 38 из сборника конденсата 14 в парогенератор 16, подачи жира 39 в смеситель 7; датчики: расхода 40-51, температуры 52-56, давления 57-59, влагосодержания 60 и 61, влажности 62, частоты вращения валков измельчителя 63, расстояния между валками измельчителя 64, угла наклона вибросит к горизонту 65, амплитуды 66 и частоты 67 колебания вибросит, уровня 68 и 69; микропроцессор 70; исполнительные механизмы 71-86 (А, Б, В, Г, Д, Е, Ж, З, И, К, Л, М, Н, О, П, Р, С, Т, У, Ф, X, Ц, Ч, Ш, Щ, Ы, Ь, Э, Ю, Я – входные каналы управления, а, б, в, г, д, е, ж, з, и, к, л, м, н, о, п, р – выходные каналы управления).
Способ осуществляется следующим образом.
Исходный рассыпной комбикорм, поступающий на обработку по линии 21, направляют на смешивание с горячими гранулами, вышедшими из матрицы пресса-гранулятора 6 по линии 22, в гравитационный смеситель 1. Гравитационный смеситель 1 позволяет без механического воздействия на продукт получить однородную смесь рассыпного комбикорма и горячих гранул. После смесителя 1 смесь попадает в теплообменник 2, в котором происходит тепло- и влагообмен между горячими гранулами и поступившим рассыпным комбикормом. Все тепло горячих гранул утилизируется и используется для нагрева рассыпного комбикорма, что позволяет не только обеспечить его обеззараживание, но и повысить прочность гранул.
В охладителе 3 смесь гранул и рассыпного комбикорма охлаждается воздухом, который проходит предварительную подготовку (охлаждается и осушается) в теплообменнике-рекуператоре 11 пароэжекторной холодильной машины путем рекуперативного теплообмена между хладагентом и воздухом через поверхность охлаждающего элемента теплообменника-рекуператора.
Смесь охлажденных гранул и рассыпного комбикорма далее по линии 23 подают на измельчение (вальцовый станок или валковый измельчитель 4, рабочий зазор устанавливают в пределах 1,0 2,5 мм в зависимости от назначения комбикорма).
Измельченные гранулы и рассыпной комбикорм фракционируют на просеивающей машине 5, у которой диаметр отверстий верхнего сита составляет 3,0 4,5 мм, нижнего 1,8 2,0 мм в зависимости от рецепта вырабатываемых комбикормов. Крупную фракцию (сход верхнего сита) по линии 25 направляют на доизмельчение в валковый измельчитель 4, мелкую фракцию (проход нижнего сита) подают по линии 27 на гранулирование в пресс-гранулятор 6 с диаметром отверстий матрицы, например, 4,7 5,0 мм. Среднюю фракцию (проход верхнего и сход нижнего сита), представляющую собой комбикорм выровненного гранулометрического состава, подают по линии 26 в смеситель 7, где покрывают кормовым жиром слоем 0,5 1,0 мм путем распыливания с помощью форсунок, доводя содержание жира до 3 5% от объема получаемой средней фракции, и выводят в виде готовой продукции.
Подогрев жира перед форсунками до температуры 65 70°С уменьшает его вязкость до 16,5·10-3 Па. При этом создаются благоприятные условия для равномерного распыливания жира, обеспечивается надежная работа форсунок с минимальными потерями времени на регенерацию рабочих поверхностей, вызванную облитерацией и образованием налета, снижается нагрузка на насос подачи жира в смеситель.
Пароэжекторная холодильная машина, включающая эжектор 9, испаритель 10, теплообменник-рекуператор 11, конденсатор 12, регулирующий вентиль 13, сборник конденсата 14, насос 15 и парогенератор 16 с предохранительным клапаном 17, работает по следующему термодинамическому циклу.
В парогенераторе 16 с электронагревательными элементами и предохранительным клапаном 17 при затрате электроэнергии образуется рабочий пар, который поступает по линии 31 в сопло эжектора 9. Причем потенциальная энергия рабочего пара превращается в кинетическую энергию струи, которая вытекает с большой скоростью, и под действием энергии струи эжектируются пары хладагента. При этом в испарителе 10 создается пониженное давление и температура. Образовавшиеся пары хладагента поступают по линии 32 из испарителя 10 в теплообменник-рекуператор 11 на охлаждение воздуха, подаваемого на охлаждение смеси рассыпного комбикорма и горячих гранул, а затем в эжектор 9. Образовавшуюся смесь паров хладагента и рабочего пара после эжектора разделяют на два потока: один по линии 33 подают в пресс-гранулятор 6, а другой по линии 34 – в конденсатор 12. Конденсируясь, он отдает теплоту кормовому жиру, который затем подают по линии 39 на форсунки смесителя 7. Одну часть образовавшегося в конденсаторе водяного конденсата по линии 35 направляют через регулирующий вентиль 13 в испаритель 10 для пополнения убыли воды. Другую его часть отводят по линии 36 в сборник конденсата 14, куда также отводят по линии 37 конденсат, который образовался при охлаждении воздуха в теплообменнике-рекуператоре 11. Далее конденсат из сборника 14 насосом 15 подают по линии 38 в парогенератор 16 с образование замкнутого цикла.
Отработанный воздух после охлаждения смеси рассыпного комбикорма и горячих гранул сначала направляют по линии 29 в циклон 8 для очистки от содержащихся в нем взвешенных твердых частиц смеси, а затем на охлаждение с образованием конденсата в теплообменник-рекуператор 11. Охлажденный и осушенный воздух с помощью вентилятора 18 по линии 30 вновь подают на охлаждение смеси рассыпного комбикорма и горячих гранул в охладитель 3 с образованием замкнутого цикла. При этом взвешенные частицы, образовавшиеся при очистке воздуха, из циклона 8 отводят по линии 28 в пресс-гранулятор 6.
Информация о ходе процесса приготовления комбикормов, подготовки воздуха, пара и жира с помощью датчиков 40-69 передается в микропроцессор 70, который по заложенному в него программно-логическому алгоритму осуществляет оперативное управление технологическими параметрами с учетом накладываемых на них двухсторонних ограничений, обусловленных как получением готового продукта высокого качества, так и экономической целесообразностью. Вторичные приборы, цифроаналоговые ЦАП и аналого-цифровые АЦП преобразователи на схеме не показаны.
По текущим значениям расхода рассыпного комбикорма в лини 21 и горячих гранул в линии 22 перед их смешиванием, измеряемым соответственно датчиками 40 и 41, микропроцессор 70 устанавливает расход воздуха на охлаждение смеси горячих гранул и рассыпного комбикорма в линии 30, измеряемый датчиком 47, воздействием на мощность регулируемого привода вентилятора 18 посредством исполнительного механизма 81.
По информации датчиков 42 и 43 о расходах смеси рассыпного комбикорма и гранул в линии 23 и крупной фракции в линии возврата на доизмельчение 25 микропроцессор 70 устанавливает производительность измельчителя 4 воздействием на частоту вращения валков с помощью исполнительного механизма 74, текущее значение которой определяется датчиком 63. По текущей влажности смеси гранул и рассыпного комбикорма, измеряемой датчиком 62, оценивают структурно-механические свойства продукта, подаваемого на измельчение, в зависимости от которых устанавливают с помощью исполнительного механизма 75 расстояние между валками, измеряемое датчиком 64.
Качество процесса сортирования в просеивающей машине 5 полученных продуктов измельчения на валковом измельчителе 4 микропроцессор 70 непрерывно оценивает по текущему соотношению расходов крупной и средней фракций соответственно в линиях 25 и 26 с помощью датчиков 43 и 45. При отклонении соотношения расходов крупной и средней фракций от заданного значения, например, в сторону увеличения микропроцессор по трем каналам управления осуществляет коррекцию режима просеивания, заключающегося в подаче управляющих воздействий в следующей последовательности: сначала на увеличение частоты колебаний, затем на увеличение амплитуды колебаний с помощью исполнительных механизмов 77 и 78 и далее на уменьшение угла наклона сит к горизонту с помощью гидроцилиндра 20 посредством исполнительного механизма 76. Текущие значения перечисленных параметров передаются в микропроцессор соответственно с датчиков 65, 66, 67. Каждый последующий канал управления срабатывает после того, как предыдущий выйдет на свои ограничения, то есть полностью исчерпывает свой собственный ресурс. Если по первому каналу управления увеличение частоты колебаний сит до предельно допустимого максимального значения не обеспечит достижения соотношения расходов крупной и средней фракций заданного значения, то сработает второй канал управления, то есть микропроцессор воздействует на увеличение амплитуды колебаний до достижения предельно допустимого максимального значения. Если достигается равенство текущего соотношения расходов крупной и средней фракций заданному значению, то микропроцессор прекращает подачу управляющего воздействия по третьему каналу управления. В противном случае срабатывает третий канал управления, предусматривающий уменьшение угла наклона сит до выполнения условия, при котором соотношение расходов крупной и средней фракций будет равно заданному.
Изменение текущего значения соотношения расходов крупной и средней фракций от заданного в сторону увеличения свидетельствует о снижении производительности по готовому продукту – расходу средней фракции и перерасходу электроэнергии на процесс измельчения за счет увеличения расхода крупной фракции в линии ее возврата 25 на валковый измельчитель 4.
В случае отклонения текущего значения соотношения крупной и средней фракций от заданного значения в сторону уменьшения возникает ситуация, при которой высокий выход готовой продукции (расход средней фракции) не оправдан интенсивными режимами измельчения и сортирования из-за чрезмерно высоких энергозатрат, приходящихся на единицу получаемой продукции. В этом случае микропроцессор 70 в той же последовательности осуществляет воздействие сначала на уменьшение частоты колебаний, затем на уменьшение амплитуды колебаний и далее на увеличение угла наклона сит к горизонту. При выполнении условия, при котором достигается равенство текущего значения соотношения крупной и средней фракций заданному, микропроцессор прекращает подачу управляющих воздействий по всем трем каналам управления.
Расход жира, текущее значение которого определяется датчиком 51 в линии его подачи 39 в смеситель 7, устанавливается микропроцессором в зависимости от расхода средней фракции в линии 26 посредством исполнительного механизма 86. При этом по текущему значению температуры жира, измеряемому датчиком 56, установленным после конденсатора 12 в линии 39, микропроцессор 70 устанавливает заданное давление жира перед форсунками на входе в смеситель 7 воздействием на мощность регулируемого привода насоса для жира 19 посредством исполнительного механизма 82. При отклонении текущего значения температуры жира от заданного в сторону увеличения его вязкость снижается, а следовательно, и снижается его давление в линии 39 перед форсунками. В этом случае микропроцессор повышает мощность на привод насоса 19 с помощью исполнительного механизма 82 до тех пор, пока давление жира перед форсунками не достигнет заданного значения, которое измеряют датчиком 58. При отклонении текущего значения температуры жира от заданного в сторону уменьшения давление жира перед форсунками уменьшают.
По информации датчика 41 о суммарном расходе мелкой фракции с просеивающей машины 5 и отделившихся твердых частиц смеси в циклоне 8, подаваемых в пресс-гранулятор 6 соответственно по линиям 27 и 28, микропроцессор 70 устанавливает мощность регулируемого привода пресса-гранулятора 6 посредством исполнительного механизма 83.
По измеренным значениям влагосодержания воздуха до и после охлаждения смеси в охладителе 3 и его расходу с помощью датчиков 60, 61 и 46 микропроцессор определяет количество водяных паров в отработанном воздухе по формуле:
U=(xвых-xвх) свV,
где хвх, хвых – влагосодержание сушильного агента на входе и выходе из охладителя 3, кг/кг; св – плотность сухого воздуха, кг/м3; V – объемный расход воздуха, м3/ч,
в соответствии с которым устанавливают коэффициент эжекции пароэжекторной холодильной машины воздействием на соотношение расходов рабочего пара, подаваемого в сопло эжектора 9, и эжектируемых паров хладагента, захватываемых из испарителя 10 через теплообменник-рекуператор 11 путем изменения расхода рабочего пара в линии 31 с помощью исполнительного механизма 71.
По информации датчиков 47, 53, 54, 55 микропроцессор непрерывно вычисляет текущее значение коэффициента теплопередачи от хладагента к воздуху через охлаждающую поверхность теплообменника-рекуператора 11 по формуле:
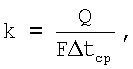
где Q=V с (t1-t2) – количество теплоты, подаваемой отработанным воздухом в теплообменник-рекуператор 11 пароэжекторной холодильной машины, кДж/ч; с, – средние значения теплоемкости, кДж/(кг·К), плотности, кг/м3, воздуха; V – объемный расход воздуха, м3/ч; F – площадь поверхности охлаждающего элемента теплообменника-рекуператора, м2; tср=(t1-t2)/ln[(t1-t3)/(t2-t3)] – среднелогарифмический температурный напор, С; t1, t2 – температура воздуха соответственно на входе и выходе из теплообменника-рекуператора, С; t3 – температура хладагента на входе в теплообменник-рекуператор, С,
и вырабатывает сигнал отклонения текущего значения коэффициента теплопередачи от заданного интервала значений в зависимости от текущего значения температуры воздуха, подаваемого на охлаждение смеси рассыпного комбикорма и горячих гранул, измеряемого с помощью датчика 54.
При отклонении текущего значения температуры воздуха, подаваемого на охлаждение смеси рассыпного комбикорма и горячих гранул, от заданного интервала в сторону увеличения микропроцессор увеличивает коэффициент теплопередачи путем увеличения коэффициента эжекции воздействием на увеличение расхода рабочего пара в эжекторе 9 с помощью исполнительного механизма 71. А при отклонении текущего значения температуры воздуха, подаваемого на охлаждение смеси рассыпного комбикорма и горячих гранул, от заданного интервала в сторону уменьшения микропроцессор уменьшает коэффициент теплопередачи путем уменьшения коэффициента эжекции воздействием на уменьшение расхода рабочего пара в эжекторе 9 с помощью исполнительного механизма 71
Информация о текущем значении уровня хладагента в испарителе 10 с помощью датчика 69 непрерывно передается в микропроцессор. При изменении уровня конденсата микропроцессор осуществляет двухпозиционное регулирование приводом регулирующего вентиля 13 с помощью исполнительного механизма 84. При достижении уровня хладагента в испарителе нижнего заданного значения микропроцессор вырабатывает сигнал на увеличение расхода конденсата через регулирующий вентиль в линии 35 и уменьшает расход при достижении верхнего заданного значения.
По информации датчика 57 микропроцессор осуществляет непрерывную стабилизацию давления насыщенного пара в парогенераторе 16 воздействием на мощность электронагревательных элементов посредством исполнительного механизма 79. При этом достигается заданная производительность парогенератора, контроль за которой обеспечивается датчиком расхода пара 48 в линии 31.
По текущей величине давления пара в прессе-грануляторе 6, измеряемой датчиком 59, микропроцессор устанавливает его расход в пресс-гранулятор по линии 33, измеряемый датчиком 49, посредством исполнительного механизма 72 с коррекцией по температуре горячих гранул, измеряемых датчиком 52 в линии их отвода 22 из пресса-гранулятора 6 в гравитационный смеситель 1. Таким образом, количество отводимой части насыщенного пара по линии 33 зависит от его давления в прессе-грануляторе 6 и температуры гранул в линии 22.
Оставшуюся часть перегретого пара подают по линии 34 в конденсатор 12 на нагрев жира. Образовавшийся в конденсаторе конденсат делят на два потока посредством исполнительных механизмом 73 и 84, работа которых синхронизирована.
Информация о текущем значении уровня конденсата в парогенераторе 16 с помощью датчика 68 передается в микропроцессор. При изменении уровня конденсата микропроцессор осуществляет двухпозиционное регулирование приводом питающего насоса 15 с помощью исполнительного механизма 80, включает питающий насос при достижении уровня конденсата в парогенераторе нижнего заданного значения и отключает его при достижении верхнего заданного значения.
В случае технологических и аварийных сбоев в работе парогенератора, связанных с возможным увеличением давления насыщенного водяного пара в его рабочем объеме, предусмотрен предохранительный клапан 17.
Пример реализации способа.
Способ управления процессом приготовления комбикормов реализован для поточной линии, установленной на Воронежском экспериментальном комбикормовом заводе для производства комбикормов заданной крупности с различными кормовыми добавками производительностью по готовому продукту 12,9 16,1 т/ч. Линия состоит из гравитационного смесителя У21-ДСП, контактного теплообменника, охладителя Б6-ДГВ-II, валкового измельчителя Б6-ДГВ-III, просеивающей машины У3-ДМП, пресса-гранулятора Б6-ДГВ-I. Процесс осуществляется со следующими техническими характеристиками:
Производительность смесителя, т/ч |
30 50 |
Расход воздуха на охлаждение 1 т продукции, м3 |
1300 1500 |
Влажность смеси перед измельчением, % |
13,0 14,5 |
Частота вращения валков, об/мин |
180 330 |
Расстояние между валками измельчителя, мм |
1,0 1,5 |
Амплитуда колебаний сит, мм |
9 11 |
Частота колебаний сит, об/мин |
420 450 |
Угол наклона сит к горизонту, град |
8 10 |
Влажность гранул после пресса-гранулятора, % |
15 18 |
Номинальная мощность привода пресса-гранулятора, кВт |
131,9 |
Для повышения энергетической эффективности технологической линии использовалась пароэжекторная холодильная машина со следующими характеристиками:
Низкотемпературные режимы охлаждения смеси рассыпного комбикорма и горячих гранул с пониженным влагосодержанием воздуха приводят к интенсивной конденсации влаги на поверхности частиц продукта в виде капельной жидкости или «тумана» и ее уносу из рабочей зоны охладителя с отработанным воздухом, быстро достигающим «точки росы».
Воздух после теплообменника-рекуператора пароэжекторной холодильной машины с влагосодержанием, например, 0,005 кг/кг подается в охладитель на охлаждение смеси рассыпного комбикорма и горячих гранул, а на выходе из охладителя влагосодержание отработанного воздуха составляет, например, 0,014 кг/кг. В соответствии с технической характеристикой охладителя Б6-ДГВ-II расход охлаждающего воздуха на 1 т продукта составляет 1500 м3. Следовательно, количество влаги, унесенной отработанным воздухом с поверхности частиц продукта из камеры охлаждения при производительности линии для кормопроизводства, например, 16 т/ч, определяется следующим образом:
U=(xвых-хвх) свGкк =(0,014-0,005)·1,0·16·1500=216 кг/ч,
здесь Gкк – производительность поточной линии по исходному рассыпному комбикорму, т/ч; – расход охлаждающего воздуха на 1 т продукции, м3.
Полученное количество влаги необходимо сконденсировать на поверхности охлаждающего элемента теплообменника-рекуператора. В процессе конденсации влаги отработанный воздух охлаждается до температуры, например, 7°С, что соответствует значению коэффициента теплопередачи от хладагента к воздуху через стенку охлаждающего элемента 10 Вт/м2·К и коэффициенту эжекции 0,4. При повышении температуры воздуха выше, например, 7°С микропроцессор подает сигнал на увеличение коэффициента теплопередачи, например, до 12 Вт/м2 путем уменьшения коэффициента эжекции до 0,3 за счет увеличения расхода рабочего пара, поступающего в эжектор под давлением 0,8 1,0 МПа.
Образовавшуюся смесь паров хладагента и рабочего пара после эжектора с давлением 0,2 0,3 МПа разделяют на два потока: один подают в пресс-гранулятор, а другой – в конденсатор.
В установившемся технологическом режиме работы линии приготовления комбикормов на процесс гранулирования мелкой фракции в пресс-гранулятор подается смесь паров хладагента и рабочего после эжектора под давлением, например, 0,2 МПа, что соответствует 120°С и удельному объему пара 0,892 м3/кг. При норме массового расхода пара, например, 50 кг на 1 тонну мелкой фракции, составляющей, например, 12% от расхода исходного рассыпного комбикорма, объемный расход пара на гранулирование составит:
Qn=qn·0,12Gкк·V=50·0,12·16·0,892=85,6 м3/ч,
где qn – удельный массовый расход пара, кг/т.
Поток пара, направляемый в конденсатор, конденсируется и отдает теплоту кормовому жиру, который, нагреваясь до температуры, например, 65°С, поступает на форсунки смесителя.
Образовавшийся конденсат направляют для пополнения убыли воды в парогенераторе и испарителе пароэжекторной холодильной машины.
Таким образом, предлагаемый способ позволяет не только обеспечить точность и надежность управления процессом приготовления комбикормов, но и создать условия для реализации безотходной технологии в непрерывном режиме эксплуатации основного и вспомогательного оборудования.
Дополнительные технологические приемы позволяют реализовать предлагаемый способ как энергосберегающую и экологически безопасную технологию, в частности обеспечить охлаждение воздуха с применением пароэжекторной холодильной машины в замкнутом контуре его рециркуляции и снизить при этом окисление продукта кислородом воздуха (чисто технологическая задача), устранить выброс пылевидной фракции с отработанным воздухом в атмосферу (экологическая задача), использовать рекуперацию теплоты конденсации отработанных паров после эжектора в конденсаторе пароэжекторной холодильной машины для нагрева жира (задача энергосбережения). В предлагаемом способе решается комплексная задача рационального энергоснабжения новых технологических операций, посредством которых осуществляется воздействие на сырье, что приобретает особую актуальность применения способа на предприятиях малой мощности, фермерских хозяйствах, мини-кормоцехах и делает способ более привлекательным для специалистов комбикормовой промышленности.
В таблице представлены результаты сравнения технико-экономических и качественных показателей комбикорма известного и предлагаемого способа.
Предлагаемый способ имеет следующие преимущества по сравнению с прототипом:
– обеспечивает стабильное качество готовой продукции за счет высокой точности и надежности управления в процессе приготовления комбикормов при эксплуатации пароэжекторной холодильной машины;
– обеспечивает повышение энергетической эффективности процесса охлаждения смеси горячих гранул и рассыпного комбикорма за счет кондиционирования воздуха в пароэжекторной холодильной машине;
– создает условия для снижения стоимости тонны вырабатываемого комбикорма выровненного гранулометрического состава на 5 10%;
– позволяет уменьшить энергозатраты при приготовлении комбикорма на 10 15%, так как нет необходимости в периодическом размораживании «снеговой шубы».
Показатели |
Известный способ |
Предлагаемый способ |
Гранулометрический состав продукта, %: |
 |
 |
крупная фракция (сход с сита 4 мм) |
4,0 |
4,0 |
средняя фракция |
 |
 |
(проход сита 4 мм /сход с сита 1 мм) |
94,5 |
94,5 |
мелкая фракция (проход сита 1 мм) |
1,5 |
1,5 |
Однородность смеси, % |
75 |
85 |
Массовая доля жира, % |
5,0 |
5,5 |
Затраты энергии в единицу времени, кВт/ч |
165 |
177,5 |
Производительность, т/ч |
14,3 |
16,0 |
Удельные энергозатраты, кВт/т |
11,54 |
10,09 |
Формула изобретения
Способ управления процессом приготовления комбикормов, включающий смешивание рассыпного комбикорма с горячими гранулами, вышедшими из пресса-гранулятора, выдерживание полученной смеси в теплообменнике, ее охлаждение воздухом, измельчение, фракционирование смеси рассыпного комбикорма и измельченных гранул на крупную, среднюю и мелкую фракции с последующим покрытием в смесителе средней фракции слоем жира, предварительно подогретого в конденсаторе и выводом ее в качестве готовой продукции, возврат крупной фракции на доизмельчение и отвод мелкой фракции на гранулирование, охлаждение воздуха в испарителе и его подачей в режиме замкнутого цикла на охлаждение смеси рассыпного комбикорма и горячих гранул, причем воздух перед подачей его на охлаждение смеси рассыпного комбикорма и горячих гранул охлаждают в теплообменнике-рекуператоре пароэжекторной холодильной машины, состоящей из эжектора, испарителя, теплообменника-рекуператора, конденсатора, регулирующего вентиля, сборника конденсата, насоса и парогенератора с предохранительным клапаном, работающих по замкнутому термодинамическому циклу, путем теплопередачи от хладагента, в качестве которого используется вода, к воздуху через разделяющую стенку поверхности теплообмена, кроме того, используют парогенератор с электронагревательными элементами и предохранительным клапаном для получения рабочего пара, который под давлением направляют в сопло эжектора, создавая при этом пониженное давление и температуру 4-7°С в испарителе пароэжекторной холодильной машины с подачей паров хладагента в теплообменник-рекуператор для охлаждения воздуха, а образовавшуюся смесь паров хладагента и рабочего пара после эжектора разделяют на два потока, один из которого направляют в пресс-гранулятор, а другой – в конденсатор для подогрева жира, причем одну часть образовавшегося в конденсаторе водяного конденсата подают в испаритель для пополнения убыли воды, а другую вместе с конденсатом, образовавшимся при охлаждении воздуха в теплообменнике-рекуператоре, отводят сначала в сборник конденсата, а затем в парогенератор с образованием замкнутого цикла, измерение расхода рассыпного комбикорма, расхода и температуры горячих гранул, расходов крупной, средней и мелкой фракций, расхода жира, расхода и давления пара на тепловую обработку мелкой фракции в пресс-грануляторе, влагосодержания воздуха до и после охлаждения смеси, расхода и температуры очищенного воздуха, расхода и давления насыщенного пара после парогенератора, уровня конденсата в парогенераторе с воздействием на производительность парогенератора, расхода и температуры воздуха, подаваемого на охлаждение смеси рассыпного комбикорма с горячими гранулами, отличающийся тем, что в процессе охлаждения в теплообменнике пароэжекторной машины смеси рассыпного комбикорма с горячими гранулами дополнительно измеряют величину разряжения в испарителе и расход паров хладагента на входе и выходе из теплообменника-рекуператора, уровень конденсата в испарителе, по измеренным значениям влагосодержания воздуха до и после охлаждения смеси и его расходу в теплообменнике-рекуператоре определяют количество водяных паров в отработанном воздухе, по которому устанавливают коэффициент эжекции пароэжекторной холодильной машины воздействием на соотношение расходов рабочего пара, подаваемого в сопло эжектора, и эжектируемых паров хладагента, путем изменения расхода рабочего пара определяют текущее значение коэффициента теплопередачи от хладагента к воздуху через охлаждающую поверхность теплообменника-рекуператора по температуре воздуха на входе и выходе из теплообменника-рекуператора, температуре хладагента на входе в теплообменник-рекуператор и расходу воздуха, подаваемого на охлаждение смеси рассыпного комбикорма и горячих гранул, причем при отклонении температуры воздуха, подаваемого на охлаждение смеси рассыпного комбикорма и горячих гранул, от заданного интервала значений в сторону увеличения увеличивают коэффициент теплопередачи путем уменьшения коэффициента эжекции воздействием на увеличение расхода рабочего пара, а при отклонении температуры воздуха, подаваемого на охлаждение смеси рассыпного комбикорма и горячих гранул, от заданного интервала значений в сторону уменьшения уменьшают коэффициент теплопередачи путем увеличения коэффициента эжекции воздействием на уменьшение расхода рабочего пара, при этом по температуре жира после конденсатора устанавливают заданное давление жира перед форсунками на входе в смеситель.
РИСУНКИ
|
|