|
(21), (22) Заявка: 2007123209/06, 20.06.2007
(24) Дата начала отсчета срока действия патента:
20.06.2007
(46) Опубликовано: 27.03.2009
(56) Список документов, цитированных в отчете о поиске:
RU 6937 U1, 16.06.1998. RU 8514 U1, 16.11.1998. RU 2242057 С2, 10.12.2004. ЕР 0147183 А, 03.07.1985. DE 2845515 A, 31.05.1979.
Адрес для переписки:
630110, г.Новосибирск, ул. Б. Хмельницкого, 94, ОАО “Новосибирский завод химконцентратов”, патентно-информационный отдел
|
(72) Автор(ы):
Васильков Валерий Иванович (RU), Кислицкий Александр Антонович (RU), Онучин Николай Васильевич (RU), Шустов Мстислав Александрович (RU), Калюкин Александр Борисович (RU)
(73) Патентообладатель(и):
Открытое акционерное общество “Новосибирский завод химконцентратов” (RU)
|
(54) СПОСОБ ИЗГОТОВЛЕНИЯ НАПРАВЛЯЮЩЕГО КАНАЛА ТЕПЛОВЫДЕЛЯЮЩЕЙ СБОРКИ ЯДЕРНОГО РЕАКТОРА
(57) Реферат:
Изобретение относится к атомной промышленности и может быть использовано на предприятиях по изготовлению тепловыделяющих сборок преимущественно типа ВВЭР для АЭС. Способ включает сборку канальной трубы с захватной втулкой, имеющей проточку в зоне выполнения сварного шва. Последующую сварку ее с трубой прорезным швом, при котором проточку на захватной втулке выполняют с толщиной стенки, равной 0,3-0,5 толщины стенки канальной трубы, и шириной от двух до трех толщин этой стенки. Сборку втулки с трубой выполняют с зазором не более 20% от толщины стенки проточки. Сварку осуществляют с проплавлением стенки трубы на глубину до 0,8 от ее толщины, а сварку осуществляют на скорости 1-1,3 см/с, величине сварочного тока 10-15 мА и ускоряющем напряжении 30±1 кВ в течение 18-21 секунд. 1 з.п. ф-лы, 4 ил.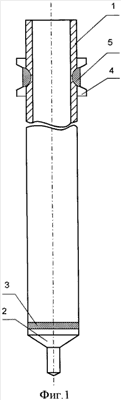
Изобретение относится к атомной промышленности, а именно – к изготовлению направляющих каналов, использующихся в конструкции тепловыделяющих сборок (ТВС) ядерных реакторов, в частности, типа ВВЭР-1000.
Конструктивно направляющий канал представляет собой канальную трубу, со стороны концов которой к ней прикреплены неразъемным соединением концевые детали, представляющие собой наконечник, захватную втулку, посредством которых осуществляется соединение канала с соответствующими узлами тепловыделяющей сборки. Сварные соединения каналов в составе ТВС воспринимают как статические, так и динамические нагрузки, связанные с транспортно-технологическими операциями при их изготовлении и эксплуатации, и являются одним из основных элементов, обеспечивающих жесткость каркаса ТВС.
Известен способ изготовления направляющего канала, согласно которому захватная втулка соединяется с трубой путем обжатия и деформации этой втулки (см. патент Германии №2845515, G21С 3/04, 1978 г.). Недостатком способа является невысокая конструкционная прочность сварного соединения и наличие большой степени деформации металла втулки, что не всегда приемлемо для сплавов циркония.
Наиболее близким по технической сущности и достигаемому результату к заявляемому является способ изготовления направляющего канала конструкции в соответствии с описанной в полезной модели №6937 (прототип), где соединение захватной втулки с трубой осуществляется путем выполнения прорезного сварного шва, соединяющего трубу и захватную втулку, на которой предварительно в зоне сварного шва выполняется кольцевая проточка, уменьшающая толщину стенки захватной втулки (см. описание работы направляющего канала). Недостатком известного решения является нестабильное качество сварного соединения из-за отсутствия регламентированных требований по его сборке и сварке, снижающих служебные характеристики канала.
Технической задачей изобретения является обеспечение требуемых служебных характеристик направляющего канала и повышение качества сварки.
Решение технической задачи достигается тем, что в способе изготовления направляющего канала тепловыделяющей сборки ядерного реактора, заключающемся в сборке канальной трубы с захватной втулкой, имеющей проточку в зоне выполнения сварного шва, и последующей сварке захватной втулки с канальной трубой, согласно изобретению проточку на захватной втулке выполняют с толщиной стенки проточки, равной 0,3-0,5 толщины стенки канальной трубы, и шириной, равной 2-3 толщинам стенки канальной трубы, сборку канальной трубы с захватной втулкой выполняют с зазором величиной, составляющей 20% или менее от толщины стенки проточки, а сварку осуществляют с проплавлением стенки канальной трубы на глубину не более 0,8 от ее толщины сварочным током величиной 10-15 тА, скоростью сварки 1-1,3 см/с и ускоряющем напряжении 30±1 кВ в течение 18-21 с.
Указанная совокупность признаков является новой, неизвестной из уровня техники и решает поставленную задачу, так как выполнение втулки с проточкой, имеющей в зоне выполнения сварного шва толщину стенки от 0,3 до 0,5 толщины стенки канальной трубы и ширину от двух до трех толщин этой стенки, позволяет с минимальным тепловложением выполнять сварные соединения, обеспечивающие необходимые прочностные характеристики вплоть до получения сварного соединения, не уступающего по прочности канальной трубе. Уменьшение толщины стенки проточки до размера менее 0,3 от толщины стенки канальной трубы приводит к образованию прожогов, особенно при существовании зазоров между свариваемыми деталями, близких к максимальным. Увеличение этого размера более 0,5 от толщины стенки канальной трубы затрудняет получение сварных соединений с гарантированным проваром.
При ширине проточки менее двух толщин стенки канальной трубы не удается стабильно получать сварные соединения с необходимой шириной сварного шва по линии соединения канальной трубы и захватной втулки. Если ширина проточки более трех толщин стенок канальной трубы, то снижаются прочностные характеристики сварного соединения, особенно при приближении ширины сварного шва к минимальному значению. Сборка захватной втулки с зазором более 20% от глубины проточки приводит к сварке с прожогами.
Выполнение данного способа позволяет получать сварные соединения требуемой прочности в широком диапазоне глубин проплавления. Требуемые прочностные характеристики сварного соединения обеспечиваются уже при глубине проплавления на уровне 0,1 мм, если при этом ширина сварного шва по зоне соединения захватной втулки с канальной трубой превышает полторы толщины стенки трубы. Другим фактором, лимитирующим возможность использования полученного сварного соединения, является отсутствие недопустимого провала металла трубы под сварным швом. Это требование обеспечивается при максимальной глубине проплавления, равной 0,8 от толщины стенки трубы.
Предъявляемые требования к сварным швам, в том числе и по отсутствию внутренних дефектов, обеспечиваются также за счет выполнения сварки при ускоряющем напряжении 30±1 кВ в течение 18-21 с, величине тока луча 10-15 мА и скорости сварки 1-1,3 см/с.
При превышении максимальных значений параметров режима имеют место недопустимые провисание металла оболочки под сварным швом, уменьшающие ее проходное сечение, и прожоги трубы. Сварка на режиме с минимальными значениями параметров не обеспечивает прочностные характеристики сварного соединения.
Способ изготовления направляющего канала тепловыделяющей сборки ядерного реактора поясняется чертежами:
на фиг.1 – направляющий канал;
на фиг.2 – схема полученного сварного соединения;
на фиг.3 – фотография реального сварного соединения трубы направляющего канала с захватной втулкой.
на фиг.4 – схема цикла сварки.
Конструкция направляющего канала представляет собой канальную трубу 1, к которой стыкозамковым швом 2 приварен наконечник 3 и установлена захватная втулка 4. Сварочный шов 5 выполнен с шириной зоны сплавления L и глубиной проплавления Н.
Предлагаемый способ осуществляется следующим образом.
К трубе 1 стыкозамковым швом 2 приваривают наконечник 3, после чего устанавливают захватную втулку 4 на расстоянии от торца трубы. Предварительно на захватной втулке 4 выполняют проточку. Втулку устанавливают на трубу с зазором А с последующей фиксацией в требуемом положении, предохраняющем ее от несанкционированного смещения при последующих транспорно-технологических операциях. Зазор А между деталями необходим, так как сплавы циркония достаточно мягкие и при взаимном трении склонны к образованию задиров, препятствующих качественной сборке и сварке. Далее собранную таким образом заготовку канала помещают в сварочную камеру электронно-лучевой установки, где на заданных режимах выполняют приварку втулки к трубе с образованием сварочного шва 5. При этом электронный луч наводится по центру перемычки, а сварку выполняют с предварительным прогревом соединения лучом меньшей, чем при сварке, мощности.
Примером конкретного выполнения способа является технология изготовления направляющих каналов тепловыделяющих сборок типа ВВЭР.
К канальной трубе из сплава циркония с одного конца приваривают наконечник, а с другого захватную втулку. Труба имеет диаметр 13,0 мм или 12,6 мм в зависимости от типа ТВС – при толщине стенки 0,9 мм и 0,5 мм соответственно. Захватная втулка выполняется с проточкой, имеющей толщину стенки 0,3 мм. Для трубы 13×0,9 мм сборка захватной втулки с трубой после их предварительного обезжиривания или протирки в зоне сварки спиртом выполняется с зазором до 0,1 мм. Фиксация захватной втулки на трубе осуществляется путем выполнения трех пуклевок, расположенных примерно под углом 120 градусов на проточке в зоне выполнения сварного шва. После этого партия каналов загружается в сварочную камеру установки для электронно-лучевой сварки. Сварка выполняется при разряжении не хуже 5×4·10-4 мм рт.ст. с предварительным прогревом зоны сварки электронным лучом. Прогрев необходим для дегазации поверхности свариваемых деталей в зоне сварки. Величина силы тока прогрева 5-6 мА. Длительность прогрева 1-1,5 оборота. После этого сила ток луча увеличивается. Для каналов с трубой 13×0,9 мм величина силы тока луча составляет 13-15 мА, для трубы диаметром 12,6×0,5 мм – 10-11 мА. Общее время сварки с учетом плавного спада тока до нуля составляет 18-21 с (см. фиг.4). Величина ускоряющего напряжения во время всего цикла сварки составляет 30±1 кВ, скорость сварки 1-1,3 см/с. В результате сварки на приведенном режиме формируется сварной шов с глубиной проплавления не более 0,8 от толщины стенки трубы, что исключает недопустимое провисание металла трубы под сварным швом и обеспечивает получение участка сплавления захватной втулки с трубой от 1,5 до 2,5 мм.
Формула изобретения
1. Способ изготовления направляющего канала тепловыделяющей сборки ядерного реактора, включающий сборку канальной трубы с захватной втулкой, имеющей проточку в зоне выполнения сварного шва, последующую сварку захватной втулки с канальной трубой, отличающийся тем, что проточку на захватной втулке выполняют с толщиной стенки, равной 0,3-0,5 толщины стенки канальной трубы, и шириной 2,0-3,0 толщин стенки канальной трубы, сборку захватной втулки с канальной трубой выполняют с зазором не более 20% от толщины стенки проточки, а сварку осуществляют с проплавлением стенки канальной трубы на глубину не более 0,8 от ее толщины,
2. Способ по п.1, отличающийся тем, что сварку осуществляют при скорости 1-1,3 см/с, величине сварочного тока 10-15 мA и ускоряющем напряжении 30±1 кВ в течение 18-21 секунды.
РИСУНКИ
|
|