|
(21), (22) Заявка: 2007128685/04, 25.07.2007
(24) Дата начала отсчета срока действия патента:
25.07.2007
(46) Опубликовано: 20.03.2009
(56) Список документов, цитированных в отчете о поиске:
RU 2296827 C1, 10.04.2007. US 5165909 A, 24.11.1992. EP 0665187 A1, 02.08.1995. US 3378345 A, 16.04.1968. GB 2184819 A, 01.07.1987. SU 1621566 A1, 23.03.1993.
Адрес для переписки:
392000, г.Тамбов, Советская, 106, ТГТУ, патентный отдел
|
(72) Автор(ы):
Ткачев Алексей Григорьевич (RU)
(73) Патентообладатель(и):
Государственное образовательное учреждение Высшего профессионального образования “Тамбовский государственный технический университет” ГОУ ВПО “ТГТУ” (RU)
|
(54) СПОСОБ ПОЛУЧЕНИЯ ВОЛОКНИСТЫХ УГЛЕРОДНЫХ СТРУКТУР КАТАЛИТИЧЕСКИМ ПИРОЛИЗОМ
(57) Реферат:
Изобретение относится к технологии получения волокнистых углеродных материалов каталитическим пиролизом. Способ получения заключается в том, что в нижней части реактора размещают соединенный с приводом вращения диск, над которым устанавливают открытую снизу осадительную камеру, в которой распыляют катализатор в виде пылевидного сплава на основе никеля. В реактор непрерывно подают исходный продукт – углеводородный газ – и нагревают его до 600-1150°С, а газообразные продукты пиролиза также непрерывно отводят. Готовый продукт вместе с катализатором охлаждают. Перед пуском реактора в работу под осадительной камерой на диске помещают липкую пленку и включают распылительное устройство. После прекращения подачи катализатора пленку разрезают на части и определяют количество катализатора, осажденного на единицу площади пленки, по результатам которого регулируют равномерность подачи пылевидного катализатора. Осаждение пылевидного катализатора ведут при выключенном приводе вращения диска и пониженном давлении. Изобретение обеспечивает достижение максимальной производительности и качества волокнистых углеродных структур при различных размерах частиц пылевидного катализатора. 3 з.п. ф-лы, 5 ил.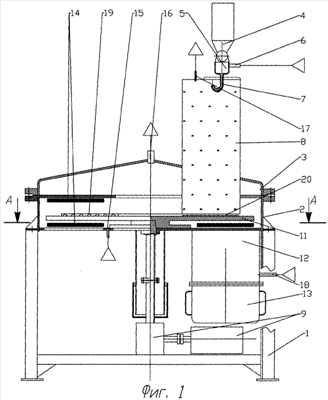
Изобретение относится к технологии получения волокнистых углеродных материалов методом пиролиза ароматических и неароматических углеводородов.
Технология получения волокнистых углеродных материалов заключается в проведении пиролиза углеводородных газов либо углеродосодержащих материалов в присутствии катализаторов преимущественно на основе дисперсного никеля, либо сплавов на его основе, а также других активных металлов с последующим охлаждением продуктов пиролиза.
Изобретение касается углеродистых волокон, характеризующихся в основном постоянным диаметром, длиной приблизительно в 5 раз больше диаметра, упорядоченной внешней областью каталитически выращенных кристаллов и их кратным числом, в основном непрерывными слоями упорядоченных углеродных атомов, имеющих наружный диаметр между приблизительно 3,5 и 70 нанометрами.
Известен способ карбонизации углеродосодержащих материалов, включающий подачу жгутов обрабатываемого углеродосодержащего материала в реактор, содержащий теплоизолированный корпус с муфелем, перемещение жгутов через полость реактора при одновременной подаче горячего и холодного инертного газа и отводе продуктов пиролиза, с дополнительным температурным воздействием на газ при проведении пиролиза и отбор обработанных жгутов в промежуточный объем при их охлаждении. (см., например, патент Великобритании GB 2184819, МПК D01F 9/22, D01F 9/32, от 01.07.1987 г.).
Недостатком такого способа является низкая производительность процесса карбонизации, связанная с невозможностью поддержания постоянства температуры при перемещении в полости печи жгутов с обрабатываемым материалом, а также ограничениями по температуре из-за опасности перегрева продукта, приводящего к термическому разложению готового продукта, что влечет за собой ухудшение его свойств. Другим недостатком является необходимость обработки исходного материала перед карбонизацией и непригодность этого способа получать продукты путем каталитического пиролиза.
Наиболее перспективным является способ, позволяющий обрабатывать исходные газообразные углеводородные продукты. В этом случае предварительная обработка исходного материала сводится к минимуму. В патенте США №5165909, МПК D01F 9/10, от 24 ноября 1992 года описан способ непрерывного получения углеродных волокон, который включает контактирующее формирование волокон на катализаторе, содержащем металлические частицы, с газом, содержащим углерод. Процесс синтеза осуществляют непрерывно за счет непрерывной подачи в реакционную зону содержащего атомы углерода газа и содержащего металл катализатора и выведение из реакционной зоны продуктов пиролиза, причем газ после очистки вновь возвращают в реакционную зону. В качестве содержащего углерод газа может использоваться окись углерода, различные углеводороды, в том числе содержащих кислород, такие как формальдегид, уксусный альдегид, ацетон, метанол, этиловый спирт или их смесь, а также ароматические углеводороды: бензол, толуол, ксилол, кумол, этилбензол, нафталин, фенантрен, антрацен или их смеси. Кроме того, могут использоваться неароматические углеводороды, такие как метан, этан, пропан, этилен, пропилен или ацетилен или их смеси. При этом предпочтение отдается углеводороду – метану. В качестве катализатора используют сплавы и металлы: железо, кобальт или никель в виде частиц, имеющих диаметр между 3,5 и 70 нанометрами с жаропрочной добавкой оксида алюминия, силиката алюминия, и химические соединения на основе углерода.
Согласно патенту синтез ведут при контакте газа с катализатором в течение от 10 секунд до 30 минут и при давлении от одной десятой до десяти атмосфер, и температуре от 900 до 1150°С. Способ получения волокнистых углеродных структур каталитическим пиролизом заключается в том, что в реактор подают исходный продукт – углеводородный газ – и распыляют катализатор в виде сплава на основе никеля, который нагревают до температуры 600-1150°С, при этом непрерывно подают в реактор углеводородный газ и отводят газообразные продукты пиролиза и готовый продукт вместе с катализатором охлаждают на поверхности фильтра, установленного на входе циркуляционного компрессора. Пиролиз проводят в вертикальной печи, в верхней части которой располагают патрубок подачи углеводородного газа, ленточные нагреватели и бункер с катализатором. На нижней части бункера с катализатором располагают питательный клапан, который подает в реакционную зону печи катализатор в виде порошкообразного никеля с добавлением окиси алюминия. В нижней части располагают второй патрубок подачи углеводородного газа. Расстояние между питающим клапаном и вторым патрубком подачи углеводородного газа является реакционной зоной, ниже которой расположено основание печи, снабженное фильтром, являющимся сборником готового продукта перед его выгрузкой, полость между фильтром и нижней частью корпуса реактора соединена с входом циркуляционного компрессора.
Однако полученные таким способом продукты пиролиза подвергаются длительному нагреву потоком циркулирующего горячего газа, содержащего смесь углеводородного газа, продуктов пиролиза и катализатора, что обуславливает разброс свойств готового продукта, т.е. в продукте кроме углеродных волокон могут образовываться вкрапления графита и сажи, которые снижают качество продукта. Другими недостатками известного способа является невозможность равномерного распределения порошкообразного катализатора по всему живому сечению печи и неравномерность температурного поля в реакционной зоне. Это приводит к снижению эффективности пиролиза.
Перечисленные недостатки устраняет способ получения волокнистых углеродных структур каталитическим пиролизом, заключающийся в том, что в продутый аргоном реактор распыляют катализатор в виде пылевидного сплава на основе никеля, нагревают до температуры 600-1150°С, после чего производят непрерывную подачу углеводородного газа и отвод газообразных продуктов пиролиза, и по окончании процесса пиролиза готовый продукт вместе с катализатором охлаждают, в реактор с нагревателями, размещенными над и под установленным диском, струйным распылителем подают инертный газ и катализатор, поступающий в распылитель через дозатор в камеру-осадитель, имеющую вид перевернутого стакана с сечением в виде сектора вращающегося диска, в котором производят осаждение пылевидного катализатора на верхнюю поверхность диска при включенном приводе вращения диска слоем 1-3 мм, затем подают углеводородный газ со стороны нижней поверхности диска, который нагревают, при этом отвод газообразных продуктов пиролиза осуществляется через патрубки, которые размещены в верхней части реактора и камеры-осадителя, и по окончании процесса пиролиза включают привод вращения диска и скребком удаляют твердые продукты пиролиза в охлаждаемую емкость отбора продуктов пиролиза, в которую также подают инертный газ. (патент РФ № 2296827, МПК D01F 9/127, D01F 9/133, от 03.08.2005 г.).
Однако этому способу присущ недостаток, заключающийся в сложности калибровки системы подачи катализатора, без чего невозможно достижение равномерности распределения катализатора на вращающемся диске. Неравномерность распределения катализатора приводит к снижению производительности и качества продукта. Снижение качества обнаруживается по наличию сажевых включений и свидетельствует о неравномерности слоя катализатора либо о чрезмерной его толщине.
По совокупности общих признаков в качестве прототипа выбран способ по патенту РФ № 2296827.
Задачей изобретения является повышение производительности и качества продукта при различных гранулометрических характеристиках катализатора.
Задача решается тем, что согласно способу получения волокнистых углеродных структур каталитическим пиролизом, заключающемуся в том, что в нижней части реактора размещают соединенный с приводом вращения диск, над которым устанавливают открытую снизу осадительную камеру, в которой распыляют катализатор в виде пылевидного сплава на основе никеля, после чего в реактор подают исходный продукт – углеводородный газ -, которые нагревают до температуры 600-1150°С, при этом в реактор непрерывно подают углеводородный газ и отводят газообразные продукты пиролиза, готовый продукт вместе с катализатором охлаждают, причем перед пуском реактора в работу под осадительной камерой на диске помещают липкую пленку и включают распылительное устройство, после прекращения подачи катализатора пленку разрезают на части и определяют количество катализатора, осажденного на единицу площади пленки, по результатам которого регулируют равномерность подачи пылевидного катализатора.
Осаждение пылевидного катализатора ведут при выключенном приводе вращения диска.
При подаче катализатора в реакторе снижают давление ниже атмосферного.
Липкую пленку с осажденными пылевидными частицами накрывают вторым слоем липкой пленки и полученный пакет разрезают на отдельные участки.
Помещение под осадительной камерой на диске липкой пленки перед пуском реактора в работу и включением распылительного устройства и разрезание на части пленки после прекращения подачи катализатора позволяет определить количество катализатора, осажденного на единицу площади пленки. Это позволяет оценить работу системы подачи катализатора. По результатам сравнения различных участков можно судить о равномерности подачи пылевидного катализатора и получить необходимую информацию по регулировке совместной работы дозатора, распылительного устройства и привода вращения диска и обеспечить достижение оптимальной работы реактора, При этом слой осажденного катализатора должен превышать в полтора раза размер частиц катализатора. Это обеспечивает достижение максимальных производительности и качества продукта для каждого вида катализатора.
Проведение осаждения пылевидного катализатора при выключенном приводе вращения диска позволяет численно оценить эффективность совместной работы системы дозирования и распылительного устройства, что, в свою очередь, позволяет снизить потребное для калибровки количество катализатора и продолжительность дозирования.
Снижение в реакторе при подаче катализатора давления ниже атмосферного позволяет воспроизвести динамические характеристики разогретой газовой среды, что повышает точность определения величины регулировки.
Получение пакетов их двух слоев липкой пленки с осажденными пылевидными частицами, когда нижнюю липкую пленку накрывают вторым слоем липкой пленки, после чего их разрезают на отдельные участки, позволяет исключить ошибки измерения из-за ссыпания части избыточного количества катализатора на соседние участки.
На фиг.1 показан общий вид устройства для получения волокнистых углеродных материалов; на фиг.2 – сечение по А-А, на котором показано взаимное расположение вращающегося диска, камеры-осадителя, скребка и емкости готового продукта; на фиг.3 показана выноска I с расположением липкой пленки и участков взвешиваемой пленки; на фиг.4 – вариант расположения липкой пленки при проведении дозирования катализатора на диске внутри камеры-осадителя и на фиг.5 показано сечение пакета из двух листов липкой пленки.
Реализация предлагаемого способа осуществляется в реакторе для получения волокнистых углеродных структур каталитическим пиролизом. Реактор содержит корпус, выполненный в виде смонтированного на раме 1 основания 2 и крышки 3. На крышке 3 смонтирован узел подачи катализатора в виде дозатора 4 и распылителя 5, сообщающегося трубопроводом 6 с линией подачи нейтрального газа – аргона, а трубопроводом 7 – с камерой-осадителем 8. Камера-осадитель 8 выполнена в виде перевернутого стакана с сечением в форме сектора и установлена в крышке 3 над соединенным с содержащим электродвигатель, муфты и редуктор приводом вращения 9 и взаимодействующим с неподвижным скребком 10 вращающимся диском 11, смонтированным на основании 2. В основании 2 выполнено отверстие, соединенное с цилиндрической обечайкой 12, соединенной разъемом со сборником 13 готового продукта. На внутренних поверхностях основания 2 и крышки 3 закреплены нагреватели 14, расположенные над и под вращающимся диском 11. Основание 2 снабжено расположенным под вращающимся диском 11 патрубком 15 подачи углеводородного газа – метана. На крышке 3 и камере-осадителе 11 расположены патрубок 16 отвода газообразных продуктов пиролиза. Сборник готового продукта 13 соединен с линией подачи инертного газа 18. На фиг.1 показан слой катализатора и продукта 19, находящийся на вращающемся диске 11. На фиг.1, 3 и 4 показано размещение листов липкой пленки 20 и размещение взвешиваемых ее участков 21 (на фиг.3). При использовании второй липкой пленки 22 образуются удобные для контроля пакеты, как показано на фиг.5.
Предлагаемый способ реализуют следующим образом.
Перед пуском реактора в работу и при каждой замене марки катализатора крышку 3 отсоединяют от основания 2 и на вращающийся диск 11 при отключенном приводе вращения устанавливают предварительно взвешенную липкую ленту 20 под камерой-осадителем 8. После этого крышку 3 вновь устанавливают на основание 2 и производят дозирование катализатора, для чего через трубопровод 6 и трубопровод 7 в камеру-осадитель 8 подают аргон и при включенном дозаторе 4 через распылитель 5 в полость камеры-осадителя 8 подают катализатор в пылевидной форме. Одновременно через патрубок 16 в полости реактора вакуумным насосом (не показан) создают разрежение 100-200 кПа. Продолжительность дозирования определяют опытным путем и выбирают обычно равным половине прохождения проекции камеры-осадителя 8 на вращающемся диске 11. После этого отключают узел дозирования и вакуумный насос. Вновь снимают крышку 3 и поверхность пленки 20 с осажденным катализатором 19 накрывают слоем пленки 22, после чего ее удаляют с диска 11. После этого пленки 21 и 22, образующие пакет, разрезают на отдельные участки 21, которые взвешивают и сравнивают между собой. При калибровке ректоров с малым диаметром вращающегося диска 11 пленку 22 можно не устанавливать. После этого по результатам сравнения выполняют одно или несколько из перечисленных действий:
– производят поворот трубопровода 7 в горизонтальной плоскости;
– регулируют подачу дозатора 4;
– изменяют расход аргона, подаваемого в распылитель 5 по трубопроводу 6;
– изменяют скорость вращения диска 11.
Такие действия выполняют повторно, чтобы убедиться в правильности калибровки системы дозирования, и после достижения положительного результата приступают к эксплуатации реактора. Для этого перед работой полость реактора продувают аргоном для удаления из полости атмосферного воздуха, так как в смеси с метаном или другим углеводородным газом в полости реактора может образоваться взрывоопасная смесь, что недопустимо, исходя из правил техники безопасности. Для этого через линию подачи инертного газа 18 в сборник готового продукта 13 подают аргон, который вытесняет атмосферный воздух из полости реактора через патрубки 16 и 17. Для ускорения вытеснения воздуха включают привод вращения диска 11. Через трубопровод 6 и трубопровод 7 в камеру-осадитель 8 подают аргон и при включенном дозаторе 4 через распылитель 5 в полость камеры-осадителя 8 подают катализатор в пылевидной форме. При вращении диска 11 приводом 9 на диск осаждают ровным слоем катализатор 19. В обескислороженную полость реактора, образованную смонтированным на раме 1 основанием 2 и крышкой 3, при включенных нагревателях 14 через патрубок 15 подают метан, который подогревают нагревателями 14. Разогретый метан взаимодействует со слоем катализатора на верхней поверхности вращающегося диска 11 с образованием нановолокнистой структуры на поверхности частиц катализатора и газообразных продуктов пиролиза, содержащих водород. Одновременно с этим из полости реактора вытесняют аргон через патрубок 16. При взаимодействии метана с катализатором на поверхности частиц катализатора образуется продукт, этот процесс продолжается до прекращения работы катализатора, и тогда включают привод вращения диска 11. При вращении диска 11 скребком 10 продукт направляют через цилиндрическую обечайку 12 в сборник 13 готового продукта. Для исключения изменения свойств продукта в обечайку 12 – по линии инертного газа 18 подают аргон. Не прореагировавший с катализатором газ вместе с продуктами пиролиза отводят через патрубок 16 как в процессе пиролиза, так и при окончании работы. После этого отключают привод вращения диска 11 и процесс повторяют. В конце работы после охлаждения продукта сборник 13 отсоединяют от цилиндрической обечайки 12, и синтезированный продукт выгружают из нее.
Пример 1. Перед началом работы на вращающийся диск устанавливают предварительно взвешенную липкую ленту 20 и включают подачу катализатора, содержащего 90% никеля и 10% окиси магния, в количестве от 40 до 50 г до образования слоя на пленке до 0,4 мм, после чего подачу катализатора отключали. Результат взвешивания показал увеличение массы образцов к центру реактора на 15%. После увеличения давление аргона в трубопроводе 6 на 0,02 МПа расхождение в весах образцов составило 3 %.
Пример 2. В реакторе по примеру 1 во всех образцах было обнаружено превышение уровня дозирования на 10%. Для устранения чрезмерной толщины напыляемого слоя устанавили скорость вращения диска 36 минут вместо установленной до этого продолжительности одного оборота 40 мин. Результат: 52 г дополнительного готового продукта без вредных примесей.
Предлагаемый способ обеспечивает получение волокнистых углеродных материалов с повышенным выходом продукта и высоким качеством.
Формула изобретения
1. Способ получения волокнистых углеродных структур каталитическим пиролизом, заключающийся в том, что в нижней части реактора размещают соединенный с приводом вращения диск, над которым устанавливают открытую снизу осадительную камеру, в которой распыляют катализатор в виде пылевидного сплава на основе никеля, после чего в реактор подают исходный продукт – углеводородный газ, которые нагревают до температуры 600-1150°С, при этом в реактор непрерывно подают углеводородный газ и отводят газообразные продукты пиролиза, и готовый продукт вместе с катализатором охлаждают, отличающийся тем, что перед пуском реактора в работу под осадительной камерой на диске помещают липкую пленку и включают распылительное устройство, после прекращения подачи катализатора пленку разрезают на части и определяют количество катализатора, осажденного на единицу площади пленки, по результатам которого регулируют равномерность подачи пылевидного катализатора.
2. Способ получения волокнистых углеродных структур каталитическим пиролизом по п.1, отличающийся тем, что осаждение пылевидного катализатора ведут при выключенном приводе вращения диска.
3. Способ получения волокнистых углеродных структур каталитическим пиролизом по п.1, отличающийся тем, что при подаче катализатора в реакторе снижают давление ниже атмосферного.
4. Способ получения волокнистых углеродных структур каталитическим пиролизом по п.1, отличающийся тем, что липкую пленку с осажденными пылевидными частицами накрывают вторым слоем липкой пленки и полученный пакет разрезают на отдельные участки.
РИСУНКИ
|
|