|
(21), (22) Заявка: 2006123706/04, 31.03.2004
(24) Дата начала отсчета срока действия патента:
31.03.2004
(30) Конвенционный приоритет:
05.12.2003 US 60/527,480
(43) Дата публикации заявки: 20.01.2008
(46) Опубликовано: 20.03.2009
(56) Список документов, цитированных в отчете о поиске:
RU 2161167 С2, 27.12.2000. WO 99/51649 A1, 14.10.1999. WO 03/047839 A1, 12.06.2003. US 4414369 A, 08.11.1983. US 5539076 A, 23.07.1996.
(85) Дата перевода заявки PCT на национальную фазу:
05.07.2006
(86) Заявка PCT:
US 2004/009807 (31.03.2004)
(87) Публикация PCT:
WO 2005/061561 (07.07.2005)
Адрес для переписки:
101000, Москва, М.Златоустинский пер., д.10, кв.15, “ЕВРОМАРКПАТ”, пат.пов. И.А.Веселицкой, рег.№ 0011
|
(72) Автор(ы):
ШАННОН Портер С. (US), КУМАР Ракеш (US), ШИРОДКАР Прадип П. (US), ЭРМАН Фред Д. (US), ДЕЙВИС Марк Б. (US), ТРАПП Кейт У. (US), ДОНМИН Ли (US)
(73) Патентообладатель(и):
ЮНИВЕЙШН ТЕХНОЛОДЖИЗ, ЛЛС (US)
|
(54) ПОЛИЭТИЛЕНОВЫЕ ПЛЕНКИ
(57) Реферат:
Изобретение относится к полиэтиленовым пленкам и прежде всего к бимодальным полиэтиленовым композициям, предназначенным для получения пленок с низким содержанием примесей и повышенной технологичностью. Пленка включает полиэтиленовую композицию с плотностью от 0,940 до 0,970 г/см3 и величиной индекса расплава (I21), измеренной по методике ASTM-D-1238-F, 190°С/21,6 кг, от 4 до 20 дг/мин. Причем полиэтиленовая композиция состоит из высокомолекулярного компонента со среднемассовой молекулярной массой более 50000 и низкомолекулярного компонента со среднемассовой молекулярной массой менее 50000. Определенное сочетание полимерных свойств композиции удовлетворяют коммерческие требования для получения полиэтиленовых пленок, пригодных для получения пленок с помощью литья, формования с раздувом и других способов, при этом пленки характеризуются улучшенными технологическими характеристиками при сохранении высокого качества пленки, что проявляется в низком содержании гель-фракции, при одновременном сохранении величин прочности, гибкости и ударной вязкости. 2 н.п и 26 з.п. ф-лы, 7 ил., 6 табл.
Область изобретения
Настоящее изобретение относится к полиэтиленовым пленкам и прежде всего к бимодальным полиэтиленовым композициям, предназначенным для получения пленок с низким содержанием примесей и повышенной технологичностью.
Предпосылки создания изобретения
Бимодальные композиции из полиэтилена высокой плотности и прежде всего «бимодальные» или «мультимодальные» полиэтилены высокой плотности (“бПЭВП”) используют для получения пленок, предназначенных для получения ряда коммерческих продуктов, таких как пленки, трубы, литые изделия и т.п. Однако к недостаткам таких композиций относится относительно высокая стоимость, т.к. большинство бПЭВП получают в 2 или более стадии и/или в двух- или многостадийных реакторах по способам Dow, Basell, Borealis и Mitsui. Такие промышленные полимеризационные системы описаны в книге, например, John Scheirs & W. Kaminsky, Metallocene-Based Polyolefins, 2, 366-378, под ред. John Wiley & Sons, Ltd. (2000).
Более того, обработка 6ПЭВП связана с некоторыми коммерческими проблемами. Например, охлаждение пленок после экструзии полиэтилена является лимитирующим фактом при производстве пленок, прежде всего при экструзии ПЭВП, как описано в книге Film Extrusion Manual, Process, Materials, Properties, cc.497, TAPPI, (1992). Одним решением данной проблемы является проведение процесса по возможности при низкой температуре расплава. Однако учитывая бимодальную природу данных смол, плавление может быть неоднородным и/или для данных смол необходимо поддерживать относительно высокую температуру расплава. Для компенсации можно поддерживать высокие величины противодавления, но это приводит к возникновению других проблем, а также к повышению энергоемкости процесса. В связи с этим существует необходимость в пленках из 6ПЭВП, которые можно получить экструзией с высокой скоростью при относительно низкой температуре расплава с использованием более низкой нагрузки двигателя экструдера, сохраняя при этом высокое качество полученных пленок.
Другим преимуществом, которое имеет большое значение при производстве бПЭВП, является низкая стоимость процесса производства, которая обеспечивается при использовании однореакторных систем. Несмотря на то что однореакторные системы известны в качестве систем, с использованием которых получают бимодальные полиэтилены для изготовления пленок, как например, описано в статье Н.-Т. Liu и др., MACROMOL. SYMP., 195, 309-316 (2003), качество и технологические характеристики таких пленок не должны уступать аналогичным свойствам полиэтиленовых пленок, полученных в двухстадийных реакторах промышленного масштаба. Один объект настоящего изобретения относится к созданию такой пленки, т.к. авторами установлено, что при определенном сочетании полимерных свойств одновременно удовлетворяются как коммерческие требования для получения полиэтиленовых пленок, пригодных для получения пленок с помощью литья, формования с раздувом и других способов, а другой объект относится к получению таких пленок из полиэтиленовых композиций, полученных в одностадийном реакторе.
Краткое описание сущности изобретения
В одном объекте настоящего изобретения предлагается пленка, включающая полиэтиленовую композицию, предпочтительно бимодальный полиэтилен, характеризующийся плотностью от 0,940 до 0,970 г/см3 и величиной индекса расплава (I21) менее 20 дг/мин, причем полиэтиленовая композиция подвергается экструзии при температуре расплава Тm, величина которой удовлетворяет следующему соотношению: Тm 235-3.3 (I21), и удельной производительности от 1 (0,454 кг/ч/об/мин) до 1,5 фунт/ч/об/мин (0,681 кг/ч/об/мин), а пленка характеризуется величиной содержания гель-фракции менее 100.
В другом объекте настоящего изобретения предлагается пленка, включающая полиэтиленовую композицию, предпочтительно бимодальный полиэтилен, причем полиэтиленовая композиция включает высокомолекулярный компонент, характеризующийся среднемассовой молекулярной массой более 50000, и низкомолекулярный компонент, характеризующийся среднемассовой молекулярной массой менее 40000, или менее 20000, или менее 15000, или менее 12000; а плотность полиэтиленовой композиции составляет от 0,940 до 0,970 г/см3, величина I21 менее 20 дг/мин, величина Mw/Mn более 30, или 35, или 40, а также пленка характеризуется величиной гель-фракции менее 100.
В еще одном объекте настоящего изобретения полиэтиленовую композицию, использованную для получения пленок по настоящему изобретению, получают в одном реакторе, предпочтительно в одном газофазном реакторе непрерывного действия.
Различные объекты настоящего изобретения описаны со ссылкой на любой вариант или комбинацию вариантов осуществления изобретения, в которых описаны полимерная композиция, свойства экструзии полимерной композиции и пленка и которые будут описаны ниже более подробно.
Краткое описание фигур
На фигурах 1 и 2 показаны графики зависимости индекса расплава (I21) композиций по настоящему изобретению, описанных в примерах 1 и 2 ( ) и примерах для сравнения ( , ), от нагрузки двигателя и давления при экструзии с образованием пленки размером 0,5 мил, при этом производительность экструзии составляет от 1,84 до 1,90 фунт/ч/об/мин.
На фигурах 3,4 и 5 показаны графики ГПХ для сравнения профиля молекулярной массы композиций, описанных в примере 1 для сравнения с каждой композицией по настоящему изобретению, описанной в примерах 3, 4 и 5 (—–).
На фигурах 6 и 7 показаны графики зависимости величин индекса расплава (I21) композиций по настоящему изобретению, описанных в примерах 3 и 5-9 ( ) и примерах для сравнения (пронумерованные кружки), от нагрузки двигателя и давления при экструзии с образованием пленки размером 0,5 мил, при этом производительность экструзии составляет от 1,16 до 1,20 фунт/ч/об/мин.
Подробное описание настоящего изобретения
В настоящем изобретении предлагается пленка, включающая полиэтиленовую композицию, причем полиэтиленовая композиция в одном варианте включает высокомолекулярный компонент и низкомолекулярный компонент и в предпочтительном варианте характеризуется мультимодальным или бимодальным профилем ГПХ. Полиэтиленовая композиция характеризуется улучшенными технологическими характеристиками, а именно снижением нагрузки двигателя экструдера (или потребляемой энергии) по сравнению с другими полиэтиленовыми смолами с аналогичной плотностью и индексом расплава (I21). Другим признаком настоящего изобретения является высокая производительность при чрезвычайно низких температурах расплава. Описанные в данном контексте пленки характеризуются улучшенными технологическими характеристиками и сохраняют при этом высокое качество пленки, что проявляется, например, в низком содержании гель-фракции при одновременном сохранении величин прочности, гибкости и ударной вязкости, сопоставимых с полиэтиленами с аналогичной плотностью и I21.
Использованный в данном контексте термин «пленка» или «пленки» включает пленки, листы или мембраны толщиной от менее 1000 мкм, более предпочтительно от менее 500 мкм, еще более предпочтительно менее 200 мкм и наиболее предпочтительно от менее 100 мкм и включает пленки, полученные любым способом, известным в данной области техники, таким как литье или формование с раздувом, ориентированные или неориентированные, полученные экструзией или каландрованием, предпочтительно экструзией полиэтилена, как описано в данном контексте, и пленки разнообразного назначения, такого как заворачивание, защита, упаковка, расфасовывание, покрытие, соэкструзия с другими материалами; а также такие пленки характеризуется любыми требуемыми размерами: толщиной, длиной и т.п. Пленки по настоящему изобретению являются не только прозрачными пленками, но и могут представлять собой матовые или полупрозрачные или прозрачные, предпочтительно прозрачные пленки и характеризуются другими свойствами, как описано в данном контексте. Пленки по настоящему изобретению получают соэкструзией или в другом варианте наносят на другие листы/структуры и т.п. с образованием структур толщиной более 1000 мкм.
Преимущества пленок по настоящему изобретению, а именно использование более низких нагрузок двигателя при экструзии полимерных композиций для получения пленок и обеспечение более низких температур плавления при обеспечении необходимых в промышленном масштабе производительности и высокого качества пленки, которые подтверждаются низким уровнем содержания гель-фракции и/или высокой величиной FAR, описаны со ссылкой на любой вариант воплощения настоящего изобретения, как описано в данном контексте.
В одном объекте настоящего изобретения предлагается пленка, включающая полиэтиленовую композицию, плотность которой составляет от 0,940 до 0,970 г/см3 и величина I21 от 4 до 20 дг/мин, причем полиэтиленовая композиция подвергается экструзии при температуре расплава Тm, величина которой удовлетворяет следующему соотношению (I):

а производительность экструзии составляет от 1 (0,454 кг/ч/об/мин) до 1,5 фунт/ч/об/мин (0,681 кг/ч/об/мин), и содержание гель-фракции в пленке составляет менее 100. Величину I21 следует умножать на коэффициент 3,3. В другом варианте соотношения (I) температура расплава определяется по уравнению Тm 240-3,3 (I21), в еще одном варианте Тm 240-3,5 (I21) и в другом варианте Тm 235-3,5 (I21). Температура расплава означает температуру в нижнем участке зоны смешивания экструдера, который используется для обработки полиэтиленовой композиции при формовании пленки по настоящему изобретению. В данном объекте настоящего изобретения температуры плавления определяют в системе экструдера, пригодного для получения пленки, описанной в данном контексте.
В одном варианте полиэтиленовую композицию получают при экструзии с производительностью от 1,00 фунта полиэтилена/ч/об/мин (0,454 кг/ч/об/мин) до 1,45 фунта полиэтилена/ч/об/мин (0,648 кг/ч/об/мин) при температуре расплава Тm, величина которой удовлетворяет уравнению Тm 235-3,3 (I21).
В другом варианте полиэтиленовую композицию получают при экструзии с производительностью от 1,00 фунта полиэтилена/ч/об/мин (0,454 кг/ч/об/мин) до 1,40 фунта полиэтилена/ч/об/мин (0,636 кг/ч/об/мин) при температуре расплава Тm, величина которой удовлетворяет уравнению Тm 235-3,3 (I21).
В еще одном варианте полиэтиленовую композицию получают при экструзии с производительностью от 1,00 фунта полиэтилена/ч/об/мин (0,454 кг/ч/об/мин) до 1,30 фунта полиэтилена/ч/об/мин (0,590 кг/ч/об/мин) при температуре расплава Тm, величина которой удовлетворяет уравнению Тm 235-3,3 (I21). В другом варианте нижний предел производительности составляет 1,10 фунт полиэтилена/ч/об/мин (0,499 кг/ч/об/мин).
Примеры требуемых температур расплава Тm полиэтиленовых композиций по настоящему изобретению включают величины менее 206°С, или 204°С, или 202°С, или 200°С, или 198°С, или 196°С, или 190°С, или 188°С, или 186°С, или 184°С, или 182°С, или 180°С, или 179°С, и в другом варианте температура расплава составляет по крайней мере 170°С или по крайней мере 175°С. В еще одном варианте нижний предел температуры расплава равен минимальной температуре расплава, требуемой для получения пленок, описанных в данном контексте, при определенных производительности и скорости на выходе из головки экструдера, описанных в данном контексте.
В другом варианте воплощения настоящего изобретения улучшенные экструзионные свойства пленок, описанных в данном контексте, указывают в виде модуля экструдера, в предпочтительном варианте предпочтительные скорости на выходе из головки экструдера, как описано в настоящем изобретении, обеспечиваются в шнековом экструдере с размером винтового канала 50 мм и соотношением L/D (относительная длина шнека) 21:1. Таким образом, в одном варианте пленку по настоящему изобретению получают при экструзии полимерной композиции при температуре расплава Тm, которая удовлетворяет соотношению Тm 235-3,3 (I21), со скоростью на выходе из головки экструдера от 10 до 20 фунтов полимера/ч/дюйм окружности головки экструдера (от 0,179 до 0,357 кг/ч/мм), а в другом варианте со скоростью головки экструдера от 10 до 15 фунтов полимера/ч/дюйм окружности головки (от 0,179 до 0,268 кг/ч/мм). В данном объекте настоящего изобретения температуры расплава определяют в системе экструдера, пригодного для получения пленки, описанной в данном контексте.
В основном пленки по настоящему изобретению характеризуются улучшенными температурами расплава по сравнению с известными пленками из полиэтилена бПЭВП, которые характеризуются величиной I21 от 4 до 20 дг/мин, независимо от способа их получения или способа получения указанных полиэтиленовых композиций, использованных для получения пленок по настоящему изобретению. Указанное выше соотношение (I) справедливо для данного набора характеристик экструдера. В одном варианте указанное усовершенствование в более общем виде выражается соотношением Тm Тm X-3,3 (I21), где Тm X означает температуру расплава, линейно экстраполированную к величине I21=0 для любого заданного набора характеристик экструдера. В большинстве случаев температуры расплава полиэтиленовых композиций, использованных для получения пленок по настоящему изобретению, составляют величины ниже на 2-20°С по сравнению с соответствующими величинами для бПЭВП, описанных в предшествующей области техники и характеризующихся аналогичными величинами I21 (в интервале от ±2 до ±3 единицы).
Другой объект настоящего изобретения относится к пленке, включающей полиэтиленовую композицию, плотность которой составляет от 0,940 до 0,970 г/см3 и величина I21 от 4 до 20 дг/мин, причем полиэтиленовая композиция подвергается экструзии при температуре расплава Тm, величина которой на 2-4 или 10-20°С ниже по сравнению с температурой расплава полиэтиленовой композиции с аналогичной плотностью и величиной I21, полученной с использованием двух- или многостадийного реактора и экструзии в аналогичных условиях, при этом содержание гель-фракции в пленке составляет менее 100. Такие двух- или многостадийные процессы и реакторы известны в данной области техники, например описаны в статьях F.P.Alt и др., Macromol. Symp., 163. 135-143 (2001) и Metallocene-Based Polyolefins, 2, 366-378 (2000); и в патентах США №№ 6407185, 4975485, 4511704. Использованный в данном контексте термин «полиэтиленовая композиция, полученная с использованием многостадийного реактора» означает полиэтиленовые композиции, полученные с использованием многостадийного процесса, включающего соединенные последовательно два или более реакторов, или один реактор, эксплуатируемый в многостадийном режиме, как описано в приведенных выше ссылках. В данном объекте настоящего изобретения температуры расплава пленок по настоящему изобретению предпочтительно являются сопоставимыми с величинами полиэтиленовых композиций, полученных в многостадийном реакторе, т.е. указанные температуры расплава (величины I21) находятся в интервале ±3 дг/мин, более предпочтительно ±2 дг/мин и еще более предпочтительно в интервале ±1 дг/мин.
В еще одном объекте настоящего изобретения предлагается пленка, включающая полиэтиленовую композицию, причем полиэтиленовая композиция включает высокомолекулярный компонент, характеризующийся среднемассовой молекулярной массой более 50000, и низкомолекулярный компонент, характеризующийся среднемассовой молекулярной массой менее 40000, или менее 20000, или менее 15000, или менее 12000; а плотность полиэтиленовой композиции составляет от 0,940 до 0,970 г/см3, величина I21 менее 20 дг/мин, величина Mw/Mn более 30, или 35, или 40, а также пленка характеризуется содержанием гель-фракции менее 100. Другие характеристики полиэтиленовой композиции описаны ниже в данном контексте.
Качество пленок по настоящему изобретению характеризуется содержанием гель-фракции, как описано в данном контексте. В одном варианте содержание гель-фракции в пленках составляет менее 100, в другом варианте содержание гель-фракции составляет менее 60, в еще одном варианте содержание гель-фракции составляет менее 50, в еще одном варианте содержание гель-фракции составляет менее 40 и в еще одном варианте содержание гель-фракции составляет менее 35. Описанные в другом варианте пленки по настоящему изобретению характеризуются в одном варианте величиной FAR более +20, в другом варианте более +30 и в еще одном варианте более +40. Разнотолщинность пленок по настоящему изобретению в одном варианте составляет менее 16% от общей толщины пленки, в другом варианте менее 13% и в еще одном варианте менее 10%.
Полиэтиленовую композицию, использованную для получения пленок по настоящему изобретению, можно обрабатывать экструзией при более низких величинах мощности и давлении при данных величинах производительности и температуре расплава по сравнению с известными ранее условиями обработки. Для данного экструдера в одинаковых условиях полиэтиленовые композиции по настоящему изобретению перерабатывают экструзией при более низких нагрузках двигателя (на 1-10% ниже) по сравнению с бимодальными полиэтиленовыми композициями, которые характеризуются плотностью от 0,940 до 0,970 г/см3 и величиной I21 менее 20 дг/мин. В другом варианте усовершенствование составляет снижение нагрузки двигателя экструдера на величину от 2 до 5% по сравнению с сопоставимыми бимодальными полиэтиленовыми композициями.
Другими словами, для данного экструдера полиэтиленовые композиции по настоящему изобретению, характеризующиеся описанными выше свойствами, в одном варианте обрабатывают экструзией при нагрузке двигателя менее 80% от максимальной нагрузки двигателя, и в другом варианте менее 77% от максимальной нагрузки двигателя, и в еще одном варианте менее 75% от максимальной нагрузки двигателя, и в другом варианте от 66 до 80% максимальной нагрузки двигателя, и в еще одном варианте от 70 до 77% максимальной нагрузки двигателя, причем требуемый интервал в % включает любую комбинацию любого верхнего предела с любым нижним пределом. Указанные предпочтительные свойства обеспечиваются при температуре расплава и производительности в пределах, описанных в данном контексте.
Пленки по настоящему изобретению характеризуются свойствами, пригодными для применения в промышленности. Например, пленки по настоящему изобретению характеризуются в одном варианте пределом прочности на разрыв в продольном направлении MD от 9000 до 15000 фунтов на кв. дюйм и пределом прочности на разрыв в поперечном направлении TD от 9000 до 15000 фунтов на кв. дюйм, в другом варианте относительным удлинением при разрыве MD от 200 до 350% и относительным удлинением при разрыве TD от 200 до 350%, в еще одном варианте прочностью на раздир по Элмендорфу MD от 10 до 30 г/мил и прочностью на раздир по Элмендорфу TD от 20 до 60 г/мил; и в одном варианте прочностью при мгновенном ударе (F50) более 150 г, и более 170 г в другом варианте. Указанные величины определены при испытаниях по методикам, описанным в данном контексте ниже.
В одном варианте пленок по настоящему изобретению полиэтиленовые композиции, использованные для получения пленок, практически не содержат «твердых материалов, ухудшающих качества пленки». Такие «твердые материалы, ухудшающие качества пленки», представляют собой зоны неоднородности материала в составе полиэтиленовой композиции, которые обладают различными свойствами. В одном варианте твердая гелевая составляющая характеризуется температурой плавления по данным дифференциальной сканирующей калориметрии (DSC) от 125°С до 133°С, или в другом варианте от 126°С до 132°С; кроме того, в одном варианте твердая гелевая составляющая характеризуется величиной I21 менее 0,5 дг/мин, и в другом варианте менее 0,4 дг/мин; а также в одном варианте величиной вязкости (при скорости сдвига 0,1 рад/с при 200°С) более 1000 МП, и в другом варианте более 1200 МП, при этом твердая гелевая составляющая характеризуется наличием любого одного или комбинации нескольких описанных выше свойств. Термин «практически не содержащий твердых материалов, ухудшающих качества пленки» означает, что твердые гелевые частицы (если они вообще присутствуют) в одном варианте присутствуют в количестве не более 1 мас.% в расчете на общую массу полиэтиленовой композиции, и в другом варианте менее 0,01 мас.%, и в еще одном варианте менее 0,001 мас.%.
Для получения полиэтиленовых композиций, предназначенных для изготовления пленок по настоящему изобретению, можно использовать любые требуемые способы полимеризации олефинов, например газофазную, эмульсионную полимеризацию или полимеризацию в растворе, которые известны для полимеризации олефинов с образованием полиолефинов. В одном варианте используют два или более последовательно соединенных реакторов, таких как, например, последовательно расположенные газофазный и эмульсионный реакторы, или два последовательно расположенных газофазных реактора, или два последовательно расположенных эмульсионных реактора. В другом варианте используют один реактор, предпочтительно один газофазный реактор. Более предпочтительно в последнем варианте высокомолекулярный (ВМ) полиэтилен включают в состав низкомолекулярного (НМ) полиэтилена одновременно в одном реакторе с образованием полиэтиленовой композиции в присутствии полимеризующихся мономеров и биметаллической композиции катализатора. В одном варианте «полиэтиленовая композиция» представляет собой бимодальную полиэтиленовую композицию, содержащую более 80%, предпочтительно более 90% этиленовых мономерных звеньев, а остальные мономерные звенья являются С3-С13олефинами и диолефинами, как описано ниже.
В одном варианте ВМ и НМ полиэтилены включают друг в друга последовательно или одновременно, предпочтительно одновременно с использованием одного, двух или более реакторов любой пригодной конструкции, или в предпочтительном варианте их включают друг в друга одновременно с использованием одного полимеризационного реактора. В предпочтительном варианте воплощения настоящего изобретения для получения полиэтиленовой композиции используют полимеризационный газофазный реактор с псевдоожиженным слоем катализатора, как описано в патентах США №№4302566, 5834571 и 5352749, обычно включающий по крайней мере один реактор, и в предпочтительном варианте только один реактор.
В одном варианте НМ полиэтилен является гомополимером или сополимером полиэтилена, включающим от 0 до 10 мас.% С3-С10– -олефиновых мономерных звеньев, и прежде всего гомополимером этилена или сополимером этилена и 1-бутена, 1-пентена или 1-гексена. НМ полиэтилен характеризуется рядом свойств. В одном варианте среднемассовая молекулярная масса НМ полиэтилена составляет менее 50000, а другие варианты описаны ниже.
В одном варианте ВМ полиэтилен является гомополимером или сополимером полиэтилена, включающим от 0 до 10 мас.% С3-С10– -олефиновых мономерных звеньев, и прежде всего гомополимером этилена или сополимером этилена и 1-бутена, 1-пентена или 1-гексена. В одном варианте среднемассовая молекулярная масса ВМ полиэтилена составляет более 50000, а другие варианты описаны ниже. Полиэтиленовая композиция по настоящему изобретению, включающая по крайней мере ВМ и НМ полимеры, характеризуются также рядом параметров, описанных ниже.
Для получения полиолефинов при полимеризации олефинов используют катализаторы. Пленки по настоящему изобретению получают с использованием любой композиции катализаторов, которую используют для получения полиэтиленовых композиций и пленок, описанных в данном контексте. В одном варианте пленки получают из полиэтиленовых композиций, которые образуются при полимеризации с использованием одного класса катализаторов, или в другом варианте комбинации двух или более катализаторов аналогичного класса, или в еще одном варианте комбинации двух или более различных классов катализаторов. В предпочтительном варианте пленки, включающие полиэтиленовые композиции, описанные в данном контексте, получают полимеризацией с использованием биметаллической композиции катализаторов. Такие биметаллические каталитические композиции включают по крайней мере два, предпочтительно два соединения, содержащие металлы групп 3-10, при этом оба металла являются одинаковыми или различными металлами с одинаковыми или различными координационными сферами, составом заместителей в центральном атоме металла или лигандов, связанных с центральным атомом металла. Примеры пригодных катализаторов полимеризации олефинов, которые смешивают любым способом с образованием биметаллической каталитической композиции, включают, без ограничения перечисленным, металлоцены, катализаторы Циглера-Натта, металл-амидные катализаторы, описанные, например, в патентах США №№ 6593438, 6380328, 6274684, 6333389, заявках WO 99/01460 и WO 99/46304, и катализаторы на основе хрома, как описано в патенте США № 3324095, включающие, например, циклопентадиенилы хрома, оксиды хрома, алкилзамещенные производные хрома, а также их варианты, нанесенные на подложку, и их модифицированные варианты. В другом варианте биметаллическая каталитическая композиция представляет собой комбинацию двух или более каталитических соединений одного класса.
В предпочтительном варианте биметаллическая каталитическая композиция, использованная для получения полимерных композиций, описанных в данном контексте, включает металлоценовый и титансодержащий катализатор Циглера-Натта, например, описанный в патенте США № 5539076 и в заявке WO 02/090393, которые включены в настоящее описание в виде ссылок. Предпочтительны каталитические соединения, нанесенные на подложку, и в предпочтительном варианте оба каталитических компонента нанесены на подложку в смеси с «первичным» активатором, в предпочтительном варианте с алюмоксаном, при этом в предпочтительном варианте подложка является неорганическим оксидом.
В одном варианте в присутствии металлоценового компонента катализатора в составе биметаллической каталитической композиции получают НМ полиэтилен для полиэтиленовой композиции, которую используют для получения пленок. Металлоценовые каталитические соединения, как описано в данном контексте, включают соединения типа «полный сандвич», содержащие два лиганда Ср (циклопентадиенильные лиганды и изолобальные аналоги циклопентадиенила), связанные по крайней мере с одним атомом металла групп 3-12, и одну или более уходящих групп, связанных по крайней мере с одним атомом металла. Прежде всего лиганд(ы) Ср выбирают из группы, включающей замещенные и незамещенные циклопентадиенильные лиганды и изолобальные аналоги циклопентадиенила, примеры которых, без ограничения перечисленным, включают циклопендадиенил, инденил, флуоренил и другие структуры. В данном контексте указанные соединения называются «металлоценами» или «металлоценовыми компонентами катализатора».
Использованная в данном контексте система для определения групп элементов Периодической таблицы является «новой» системой нумерации групп Периодической таблицы элементов, как описано в книге CRC Handbook of Chemistry and Physics, под ред. David R.Lide, CRC Press, 81-oe изд. (2000).
Атом металла «М» металлоценового каталитического соединения выбирают из группы, включающей в одном варианте атомы групп 4, 5 и 6, и в предпочтительном варианте атомы Ti, Zr, Hf, и в еще более предпочтительном варианте атом Zr. Лиганд(ы) Ср образуют по крайней мере одну химическую связь с атомом металла М с образованием «металлоценового каталитического соединения». В одном объекте настоящего изобретения металлоценовые каталитические компоненты по настоящему изобретению характеризуются формулой (II):

где М имеет значения, описанные выше, каждый Х связан с М, каждая группа Ср образует химическую связь с М, а n равно 0 или целому числу от 1 до 4, или в предпочтительном варианте 1 или 2.
Лиганды СрA и СрB в формуле (II) означают одинаковые или различные циклопентадиенильные лиганды или изолобальные аналоги циклопентадиенила, каждый из которых или оба содержат гетероатомы и каждый из которых или оба замещены группой R. В одном варианте СрA и СрB независимо выбирают из группы, включающей циклопентадиенил, инденил, тетрагидроинденил, флуоренил и их замещенные производные.
Каждый из лигандов СрA и СрB формулы (II) независимо является незамещенным или замещенным любым одним заместителем R или их комбинацией. Примеры заместителей группы R, использованные в формуле (II), и заместители в кольце формулы (II), без ограничения перечисленным, включают водород, C1-С6алкил, С2-С6алкенил, С3-С6циклоалкил, С6-С10арил или алкиларил и их комбинации.
Каждый Х в формулах (II) и (III) независимо выбирают из группы, в предпочтительном варианте включающей ионы галогенов (фторид, хлорид, бромид), гидриды, С1-С12алкил, С2-С12алкенил, С6-С12арил, С7-С20алкиларил, С1-С12алкокси, С6-С16арилокси, С7-С18алкиларилокси, С1-С12фторалкил, С6-С12фторарил и содержащие гетероатом С1-С12углеводороды и их замещенные производные, и в наиболее предпочтительном варианте фторид.
В другом объекте настоящего изобретения металлоценовый компонент катализатора включает соединения формулы (II), где СрA и СрB соединены друг с другом по крайней мере через одну мостиковую группу (А), такую как структура формулы (III):

Такие мостиковые соединения формулы (III) называются «мостиковыми металлоценами». СрA, СрB, М, Х и n в структуре (III) имеют значения, определенные выше при описании формулы (II); причем каждый лиганд Ср связан с М, и (А) образует химическую связь с каждой группой Ср. Примеры мостиковой группы (А), без ограничения перечисленным, включают двухвалентные углеводородные группы, содержащие по крайней мере один атом группы 13-16, такой как, без ограничения перечисленным, по крайней мере один из атомов углерода, кислорода, азота, кремния, алюминия, бора, германия и олова и их комбинации; причем гетероатом может содержать заместители С1-С12алкил или арил, при условии образования нейтральной молекулы, не содержащей свободной валентности. Мостиковая группа (А) содержит также заместители R, описанные выше (при описании формулы (II)), включающие атомы галогенов и железа. Прежде всего примеры мостиковой группы (А), без ограничения перечисленным, включают C1-С6алкилены, замещенные C1-С6алкилены, кислород, серу, R’2C=, R’2Si=, -Si(R’)2Si(R’2)-, R’2Ge=, R’P= (где “=” означает двойную химическую связь), где R’ независимо выбирают из группы, включающей гидрид, C1-С10алкил, арил и замещенный арил.
В одном варианте в присутствии компонента катализатора Циглера-Натта в составе биметаллической каталитической композиции получают ВМ полиэтилен для полиэтиленовой композиции, который используют для получения пленок по настоящему изобретению. Катализаторы Циглера-Натта описаны в книге Ziegler Catalysts 363-386, G.Fink, R.Mulhaupt и H.H.Brintzinger, eds., Springer-Verlag (1995) и RE 33683. Примеры таких катализаторов включают оксиды, алкоксиды и галогениды переходных металлов групп 4, 5 или 6, прежде всего оксиды, алкоксиды и галогениды титана, циркония или ванадия в комбинации с соединениями магния, внутренними и/или внешними донорами электронов (спиртами, простыми эфирами, силоксанами и т.п.), алкилалюминием или алкилбором и алкилгалогенидами, а также подложками из неорганических оксидов.
В одном варианте катализатор Циглера-Натта используют в комбинации с материалом подложки, а также в присутствии или в отсутствие металлоценового компонента катализатора. Компонент катализатора Циглера-Натта смешивают с подложкой, наносят на нее или другим образом фиксируют на подложке с использованием ряда способов. Один из таких способов заключается в контактировании суспензии подложки в пригодном неполярном углеводородном разбавителе с магнийорганическим соединением, которое затем растворяется в неполярном углеводородном разбавителе для суспензии, при этом образуется раствор, из которого магнийорганическое соединение образует слой на подложке. Магнийорганическое соединение характеризуется формулой RMgR’, где R’ и R означают одинаковые или различные группы С2-С12алкил, или С4-С10алкил, или С4-С8алкил. По крайней мере в одном конкретном варианте магнийорганическим соединением является дибутилмагний.
В одном варианте магнийорганическое соединение и обработанная спиртом суспензия контактирует с соединением переходного металла. Пригодные соединения переходных металлов включают соединения металлов групп 4 и 5, которые растворимы в неполярном углеводороде, который используют для получения суспензии кремнезема. Примеры пригодных соединений переходных металлов групп 4, 5 или 6, без ограничения перечисленным, включают, например, галогениды титана и ванадия, оксигалогениды или алкоксигалогениды, такие как тетрахлорид титана (TiCl4), тетрахлорид ванадия (VCl4) и окситрихлорид ванадия (VOCl3), и алкоксиды титана и ванадия, в которых алкоксидный остаток содержит разветвленную или неразветвленную алкильную группу, содержащую от 1 до 20 атомов углерода, в предпочтительном варианте от 1 до 6 атомов углерода. Используют также смеси таких соединений переходных металлов. В предпочтительном варианте для получения магнийсодержащего катализатора Циглера-Натта в качестве исходных соединений переходных металлов используют TiCl4 или TiCl3.
В одном варианте катализатор Циглера-Натта контактирует с донором электронов, таким как тетраэтилортосиликат (ТЭОС), простым эфиром, таким как тетрагидрофуран, или органическим спиртом формулы R”OH, где R” означает группу С1-С12алкил, или С1-С8алкил, или С2-С4алкил и/или простой эфир или циклический эфир, такой как тетрагидрофуран.
Металлоценовый компонент и компонент катализатора Циглера-Натта контактирует с подложкой в любом порядке. В предпочтительном варианте осуществления настоящего изобретения первый компонент катализатора сначала контактирует с подложкой, как описано выше, а затем первый компонент катализатора на подложке контактирует со вторым компонентом катализатора.
При смешивании с образованием биметаллического компонента катализатора молярное соотношение второго компонента катализатора и первого компонента катализатора (например, молярное соотношение Ti:Zr) в одном варианте составляет от 0,1 до 100; в другом варианте от 1 до 50, в еще одном варианте от 2 до 20, в другом варианте от 3 до 12; в еще одном варианте от 4 до 10, в другом варианте от 4 до 8; при этом требуемое молярное соотношение компонента Ti и компонента Zr составляет любую комбинацию любого верхнего предела с любым нижним пределом, которые указаны в данном контексте.
Способ полимеризации, использованный для получения полиэтиленовых композиций, пригодных для изготовления пленок по настоящему изобретению, предпочтительно включает введение композиции катализатора на подложке в полимеризационный реактор. Каталитические компоненты и активатор(ы) (металлоцен и компоненты катализатора Циглера-Натта) смешивают с подложкой любым способом, известным в данной области техники. Предпочтительно каталитические компоненты наносят на подложку в присутствии по крайней мере одного активатора, предпочтительно алюмоксана. В другом варианте в полимеризационный реактор вводят другой активатор, предпочтительно алкилалюминий, в виде отдельного компонента. В наиболее предпочтительном варианте биметаллическую каталитическую композицию, предпочтительно включающую металлоцен и компонент катализатора Циглера-Натта, вводят в один реактор, предпочтительно в газофазный реактор с псевдоожиженным слоем катализатора, в условиях полимеризации, пригодных для получения бимодальной полиэтиленовой композиции, описанной в данном контексте.
Подложки, способы нанесения на подложки, модификация и активация подложек для катализаторов с одним активным центром, таких как металлоцены, описаны, например, в статье G.G.Hlatky, Chem. Rev., 100 (4), 1347-1374 (2000). Использованный в данном контексте термин «подложка» означает любой материал подложки, в одном варианте пористый материал подложки, включающий неорганический или органический материалы подложки. В одном варианте наиболее предпочтительные материалы подложки включают диоксид кремния, оксид алюминия, алюмосиликат, хлорид магния, графит и их смеси. Наиболее предпочтительной подложкой является диоксид кремния. В предпочтительном варианте подложкой является неорганический оксид, предпочтительно диоксид кремния, характеризующийся средним размером частиц менее 50 мкм или менее 35 мкм, и объемом пор от 0,1 до 1 или 2 или 5 см3/г.
Подложку предпочтительно прокаливают. Пригодный интервал температуры прокаливания в одном варианте составляет от 500°С до 1500°С, в другом варианте от 600°С до 1200°С, в еще одном варианте от 700°С до 1000°С, в другом варианте от 750°С до 900°С, и в еще более предпочтительном варианте от 800°С до 900°С, при этом требуемый интервал включает любую комбинацию любого верхнего предела и любого нижнего предела, которые указаны в данном контексте. Прокаливание проводят в отсутствие кислорода и влаги при использовании, например, атмосферы сухого азота. В другом варианте прокаливание проводят в присутствии влаги и воздуха.
Подложка контактирует с другими компонентами каталитической системы любым способом. В одном варианте подложка контактирует с активатором с образованием ассоциата активатора и подложки, или «связанного активатора». В другом варианте компонент катализатора контактирует с подложкой с образованием «связанного компонента катализатора». В еще одном варианте подложка контактирует с активатором и компонентом катализатора одновременно или частично с каждым из них в любом порядке. Контактирование компонентов осуществляют любыми пригодными способами, например в растворе, в суспензии или в твердой форме, или в виде их комбинаций, и при контактировании компоненты нагревают при температуре от 25°С до 250°С.
В одном варианте биметаллическая каталитическая композиция включает активатор по крайней мере одного, предпочтительно одного типа. Использованный в данном контексте термин «активатор» означает любое соединение или комбинацию соединений, нанесенные или не нанесенные на подложку, которые активируют катализатор с одним активным центром (например, металлоцены, металламидные катализаторы и т.п.), например, при образовании катионных производных компонента катализатора. Примеры таких активаторов включают кислоты Льюиса, такие как циклические или олигомерные поли(гидрокарбилалюминий оксиды). Предпочтительным активатором является алюмоксан, и более предпочтительным алюмоксан на подложке из неорганического оксида, причем перед контактированием с алюмоксаном подложку прокаливают.
В одном варианте в качестве активатора компонента Циглера-Натта в составе биметаллической каталитической системы в полимеризационный реактор предпочтительно добавляют также алкилалюминий. Алкилалюминиевый активатор представлен формулой AlR§ 3, где R§ выбирают из группы, включающей С1-С20алкил, С1-С20алкокси, галоген (хлор, фтор, бром), С6-С20арил, С7-С25алкиларил и С7-С25арилалкил. Примеры соединений алкилалюминия, без ограничения перечисленным, включают, триметилалюминий, триэтилалюминий, триизобутилалюминий, три-н-гексилалюминий, три-н-октилалюминий и т.п. Алкилалюминий предпочтительно не нанесен на подложку, на которую нанесены компоненты каталитической системы и «первичный» активатор (например, алюмоксан), а представляет собой отдельный компонент, который добавляют в реактор(ы).
Соединение алкилалюминия или смесь соединений, таких как триметилалюминий или триэтилалюминий, в одном варианте подают в реактор со скоростью от 10 мас.част./млн. до 500 мас.част./млн (скорость подачи алкилалюминия в массовых частях на млн сравнима со скоростью подачи этилена), в другом варианте от 50 мас.част./млн. до 400 мас.част./млн, в еще одном варианте от 60 мас.част./млн. до 300 мас.част./млн, в другом варианте от 80 мас.част./млн. до 250 мас.част./млн и в еще одном варианте от 75 мас.част./млн. до 150 мас.част./млн, причем требуемый интервал включает любые комбинации любого верхнего и любого нижнего пределов.
Для получения биметаллических каталитических композиций, описанных в данном контексте, используют также другие первичные или отдельно введенные активаторы, известные в данной области техники. Ионизирующие активаторы известны в данной области техники и описаны, например, в книге Eugene You-Xian Chen & Tobin J. Marks, Cocatalysts for Metal-Catalyzed Olefin Polymerization: Activators, Activation Processes, and Structure-Activity Relationships 100(4) Chemical Reviews 1391-1434 (2000). Примеры ионных ионизирующих активаторов, без ограничения перечисленным, включают триалкилзамещенные соли аммония, такие как триэтиламмонийтетра(фенил)бор и т.п., соли N,N-диалкиланилиния, такие как N,N-диметиланилинийтетра(фенил)бор и т.п.; соли диалкиламмония, такие как ди(изопропил)аммонийтетра(пентафторфенил)бор и т.п.; соли триарилкарбония (тритильные соли), такие как трифенилкарбонийтетра(пентил)бор и т.п., соли триарилфосфония, такие как трифенилфосфонийтетра(фенил)бор и т.п. и аналогичные соединения алюминия.
При использовании в качестве активатора циклического или олигомерного поли(карбилалюминийоксида), т.е. «алюмоксана», такого как металюмоксан «МАО», молярное соотношение активатора и компонента катализатора составляет в одном варианте от 2:1 до 100000:1, в другом варианте от 10:1 до 10000:1 и в еще одном варианте от 50:1 до 2000:1; наиболее предпочтительно алюмоксан нанесен на подложку из неорганического оксида таким образом, что при одновременном нанесении на подложку с металлоценом молярное соотношение алюминий (алюмоксан)/металл группы 4, 5 или 6 (металлоцен) составляет от 500:1 до 10:1 и более предпочтительно от 200:1 до 50:1.
Для получения полиэтилена с характеристиками, описанными в данном контексте, используют любой пригодный способ полимеризации олефинов (тип полимеризационного реактора и реакторного процесса, например полимеризация в газовой фазе, суспензии, растворе, при высоком давлении и т.п.). Производительность реактора(ов), в котором используют каталитическую систему, описанную в данном контексте, в одном варианте составляет более 500 фунтов/ч (230 кг/ч), в другом варианте более 1000 фунтов/ч (450 кг/ч), в еще одном варианте более 2000 фунтов/ч (910 кг/ч), в другом варианте более 10000 фунтов/ч (4500 кг/ч), в еще одном варианте более 20000 фунтов/ч (9100 кг/ч) и в другом варианте более 500000 фунтов/ч (230000 кг/ч).
Пленки по настоящему изобретению предпочтительно получают экструзией, литьем или литьем с раздувом из полиэтиленовой композиции, полученной с использованием газофазного реактора с псевдоожиженным слоем катализатора непрерывного действия, и прежде всего с использованием одного газофазного реактора с псевдоожиженным слоем непрерывного действия в одну стадию. Реактор данного типа и его оснащение известны и полностью описаны, например, в патентах США №№ 4003712, 4588790, 4302566, 5834571 и 5352749. В другом варианте процесс проводят в одном газофазном реакторе, как описано в патентах США №№ 5352749 и 5462999. В двух последних патентах описаны способы газофазной полимеризации, в которых используют псевдоожиженную полимеризационную среду в непрерывном потоке газообразных мономеров и необязательно «конденсирующего агента».
Вариант реактора с псевдоожиженным слоем, использованного при получении полиэтилена по настоящему изобретению, обычно включает реакционную зону и так называемую зону снижения скорости. Реакционная зона включает слой растущих частиц полиэтилена, сформированных частиц полиэтилена и незначительное количество частиц катализатора, псевдоожиженного в непрерывном потоке газообразного мономера и необязательно разбавителя для отвода тепла из полимеризационной смеси через реакционную зону. Необязательно, некоторые из рециркулирующих газов охлаждают и сжимают с образованием жидкостей, которые повышают теплоотводящую способность циркулирующего газового потока при повторном прохождении через реакционную зону. Пригодную скорость пополнения газового потока можно определить с помощью простого эксперимента. Добавление газообразного мономера в циркулирующий поток газа проводят со скоростью, равной скорости удаления продукта в виде частиц полиэтилена в смеси с мономером из реактора, а состав газа, проходящего через реактор, корректируют таким образом, чтобы в основном поддерживать равновесное состояние газообразной композиции в пределах реакционной зоны. Газ, поступающий из реакционной зоны, проходит через зону снижения скорости, в которой удаляются захваченные частицы. Более мелкие захваченные частицы и пыль удаляют с использованием циклона и/или тонкодисперсного фильтра. Газ проходит через линию рециркуляции и затем через теплообменник, в котором происходит удаление тепла полимеризации, затем газ сжимают в компрессоре и возвращают в реакционную зону. Так называемые «контролирующие агенты» (например, тетрагидрофуран, изопропиловый спирта, молекулярный кислород, соединения фенола, этоксилированные амины и т.п.) добавляют в любую зону реактора, как описано в данном контексте, и в определенном варианте их вводят в линию рециркуляции, предпочтительно в количестве от 0,1 до 50 мас.част./млн, и в еще одном варианте вводят в линию рециркуляции, расположенную выше теплообменника. Известно, что такие агенты приводят к снижению электростатического заряда и/или загрязнения реактора на больших поверхностях, линии рециркуляции, пластины в нижней части реактора и т.п.
В одном варианте объемная плотность псевдоожиженной полиэтиленовой композиции, полученной в реакторе(ах), составляет от 16 до 24 фунт/фут3 и в другом варианте от 16,5 до 20 фунт/фут3. Объемная производительность реактора(ов), используемых для получения полиэтиленовых композиций по настоящему изобретению, предпочтительно составляет от 5 до 20 фунт/ч/фут3, и более предпочтительно от 6 до 15 фунт/ч/фут3. Более того, время контакта в реакторе(ах), предпочтительно в одном реакторе, составляет от 1 до 7 ч, более предпочтительно от 1,2 до 6 ч и наиболее предпочтительно от 1,3 до 4 ч.
В варианте газофазного реактора с псевдоожиженным слоем температура псевдоожиженного слоя в реакторе находится в диапазоне от 70°С, или 75°С, или 80°С до 90°С, или 95°С, или 100°С, или 110°С, причем требуемый интервал температур включает любую комбинацию любого верхнего предела температуры с любым нижним пределом температуры. В основном температура в реакторе равна максимальной пригодной температуре с учетом температуры спекания полиэтиленового продукта в реакторе и образования загрязнений в реакторе или линии рециркуляции.
В варианте газофазного реактора с псевдоожиженным слоем давление газовой фазы в реакторе, которая включает водород, этилен, высшие сомономеры и другие газы, в одном варианте составляет от 1 (101 кПа) до 100 атм (10132 кПа), в другом варианте от 5 (506 кПа) до 50 атм (5066 кПа) и в еще одном варианте от 10 (1013 кПа) до 40 атм (4050 кПа).
Способ по настоящему изобретению предназначен для получения гомополимеров, включающих звенья этилена, и/или сополимеров, включающих звенья этилена и звенья по крайней мере одного или более других олефинов. Предпочтительно этилен сополимеризуют с -олефинами, содержащими в одном варианте от 3 до 12 атомов углерода, в другом варианте от 4 до 10 атомов углерода и в еще одном варианте от 4 до 8 атомов углерода. Более предпочтительно этилен сополимеризуют с 1-бутеном или 1-гексеном и наиболее предпочтительно этилен сополимеризуют с 1-бутеном с образованием полиэтиленовой композиции, предназначенной для получения пленок по настоящему изобретению.
Сомономер присутствует в любом количестве, соответствующем требуемому массовому процентному содержанию сомономера в конечном полимере. В одном варианте получения полиэтиленового продукта сомономер присутствует в смеси с этиленом в циркулирующем газообразном потоке в молярном соотношении от 0,005 (сомономер/этилен) до 0,100, в другом варианте от 0,0010 до 0,050, в еще одном варианте от 0,0015 до 0,040 и в другом варианте от 0,018 до 0,035.
Газообразный водород добавляют в полимеризационный реактор(ы) для регулирования свойств конечной полиэтиленовой композиции (например, величины I21 и/или I2, объемной плотности). В одном варианте молярное отношение водорода к общему количеству этиленового мономера (Н2/С2) в циркулирующем газообразном потоке составляет интервал от 0,001, или от 0,002, или 0,003 до 0,014, или 0,016, или 0,018, или 0,024, причем требуемый интервал соотношений включает любую комбинацию любого верхнего предела молярных соотношений с любым нижним пределом молярных соотношений, описанных в данном контексте. Иными словами, количество водорода в реакторе в любой момент времени в одном варианте составляет от 1000 част./млн до 20000 част./млн, в другом варианте от 2000 част./млн до 10000 част./млн, в еще одном варианте от 3000 част./млн до 8000 част./млн и в другом варианте от 4000 част./млн до 7000 част./млн, причем требуемый интервал включает любую комбинацию любого верхнего предела содержания водорода с любым нижним пределом содержания водорода, описанных в данном контексте.
Биметаллическую каталитическую композицию вводят в полимеризационный реактор любыми пригодными способами независимо от типа использованного полимеризационного реактора. В одном варианте биметаллическую каталитическую композицию подают в реактор в практически сухом состоянии, причем отдельную твердую форму катализатора не разбавляют или не смешивают с разбавителем перед подачей в реактор. В другом варианте каталическую композицию смешивают с разбавителем и подают в реактор, причем в одном варианте разбавителем являются алканы, такие как С4-С20алканы, толуол, ксилол, минеральное или силиконовое масло или комбинации указанных веществ, как описано, например, в патенте США № 5290745.
В одном варианте биметаллическую каталитическую композицию смешивают с не более 2,5 мас.% соли металла и жирной кислоты, такой как, например, стеарат алюминия, в расчете на массу каталитической системы (или ее компонентов), так, как описано в патенте США № 6608153. Другие пригодные металлы, использованные в комбинации с жирной кислотой, включают другие металлы группы 2 и групп 5-13. В еще одном варианте раствор соли металла и жирной кислоты подают в реактор. В другом варианте соль металла и жирной кислоты смешивают с катализатором и подают в реактор отдельно. Такие агенты смешивают с катализатором или подают в реактор в виде раствора или в суспензии в присутствии или в отсутствие каталитической системы или ее компонентов.
В другом варианте катализатор(ы) смешивают с активаторами и смешивают, например, в барабане или с использованием другого аппарата с не более 2,5 мас.% (в расчете на массу каталитической композиции) антистатика, такого как этоксилированный или метоксилированный амин, например Kemamine AS-990 (фирмы ICI Specialties, Bloomington Delaware).
Полиэтиленовые композиции, описанные в данном контексте, в одном варианте являются мультимодальными и бимодальными, предпочтительно бимодальными, и включают в одном варианте по крайней мере один ВМ полиэтилен и по крайней мере один НМ полиэтилен. Термин «бимодальный», использованный при описании полиэтиленовой композиции, означает «бимодальное (двухвершинное) молекуляно-массовое распределение», при этом данный термин использован в более широком значении в данном контексте по сравнению с термином, использованным в опубликованных работах и выданных патентах. Например, в данном описании одну полиэтиленовую композицию, включающую полиолефины по крайней мере с одним идентифицируемым высокомолекулярным массовым распределением и полиолефины по крайней мере с одним идентифицируемым низкомолекулярным массовым распределением, называют «бимодальным» полиолефином. Такие высоко- и низкомолекулярные полимеры идентифицируют с использованием метода обращения свертки, который позволяет установить наличие двух полимеров на кривой ГПХ с широкими пиками или на кривой ГПХ с пиками и плечом для бимодальных полиолефинов по настоящему изобретению, и в другом варианте кривая ГПХ бимодальных полимеров по настоящему изобретению содержит отдельные пики с областью перекрывания, как показано на фигурах 3-5. Полиэтиленовые композиции по настоящему изобретению характеризуются комбинацией свойств.
В одном варианте полиэтиленовая композиция включает поли(этилен-со-1-бутен) или поли(этилен-со-1-гексен), предпочтительно поли(этилен-со-1-бутен), причем количество сомономера составляет от 0,1 до 5 мол.% в расчете на массу полимерной композиции, в основном в расчете на массу НМ полиэтилена в полиэтиленовой композиции.
Полиэтиленовые композиции по настоящему изобретению в одном варианте характеризуются плотностью в интервале от 0,940 г/см3 до 0,970 г/см3, в другом варианте от 0,942 г/см3 до 0,968 г/см3, в еще одном варианте от 0,943 г/см3 до 0,965 г/см3 и в другом варианте от 0,944 г/см3 до 0,962 г/см3, причем требуемый интервал плотности полиэтиленовых композиций включает любую комбинацию любого верхнего предела плотности с любым нижним пределом плотности, описанными в данном контексте.
Полиэтиленовые композиции по настоящему изобретению характеризуются молекулярно-массовыми характеристиками, которые определяют, например, методом ГПХ, описанной в данном контексте. Полиэтиленовые композиции по настоящему изобретению в одном варианте характеризуются величиной среднечисловой молекулярной массы (Mn) от 2000 до 70000, в другом варианте от 10000 до 50000, и в еще одном варианте величиной среднемассовой молекулярной массы (Mw) от 50000 до 2000000, в другом варианте от 70000 до 100000 и в еще одном варианте от 80000 до 800000. Бимодальные полиолефины по настоящему изобретению в одном варианте характеризуются также величиной z-средней молекулярной массы (Mz) в интервале более 200000, в другом варианте более 800000, в еще одном варианте более 900000, в другом варианте более 1000000, в еще одном варианте более 1100000, в другом варианте более 1200000 и в еще одном варианте менее 1500000, при этом требуемый интервал величин Mn, Mw или Mz включает любую комбинацию любого верхнего предела с любым нижним пределом, как описано в данном контексте.
Полиэтиленовые композиции по настоящему изобретению характеризуются молекулярно-массовым распределением или, другими словами, отношением среднемассовой молекулярной массы к среднечисловой молекулярной массе (Mw/Mn) или «индексом полидисперсности» от более 30 или 40 в предпочтительном варианте и в одном варианте в интервале от 30 до 250, в другом варианте от 35 до 220 и в еще одном варианте от 40 до 200, при этом требуемый вариант включает любую комбинацию любого верхнего предела с любым нижним пределом, как описано в данном контексте. Полиэтиленовые композиции характеризуются также «z-средним» молекулярно-массовым распределением (Mz/Mw) в одном варианте от 2 до 20, в другом варианте от 3 до 20, в еще одном варианте от 4 до 10, в другом варианте от 5 до 8 и в еще одном варианте от 3 до 10, при этом требуемый интервал величин включает любую комбинацию любого верхнего предела с любым нижним пределом, как описано в данном контексте.
Полиэтиленовые композиции по настоящему изобретению в одном варианте характеризуются индексом расплава (MI или I2, измеренным по методике ASTM-D-1238-E 190°С/2,16 кг) в одном варианте в интервале от 0,01 дг/мин до 50 дг/мин, в другом варианте от 0,02 дг/мин до 10 дг/мин и в еще одном варианте от 0,03 дг/мин до 2 дг/мин, при этом требуемый интервал величин включает любую комбинацию любого верхнего предела с любым нижним пределом, как описано в данном контексте. Полиэтиленовые композиции по настоящему изобретению в одном варианте характеризуются индексом текучести (FI или I21, измеренным по методике ASTM-D-1238-F, 190°С/21,6 кг) в одном варианте в интервале от 4 дг/мин до 20 дг/мин, в другом варианте от 4 дг/мин до 18 дг/мин, в еще одном варианте от 5 дг/мин до 16 дг /мин и в другом варианте от 6 дг/мин до 14 дг/мин, при этом требуемый интервал величин I21 включает любую комбинацию любого верхнего предела с любым нижним пределом, как описано в данном контексте. В некоторых вариантах полиэтиленовые композиции по настоящему изобретению характеризуются отношением индексов расплава (I21/I2) от 80 до 400, в другом варианте от 90 до 300 и в еще одном варианте от 100 до 250 и в другом варианте от 120 до 220, причем требуемый интервал величин I21/I2 включает любую комбинацию любого верхнего предела с любым нижним пределом, как описано в данном контексте.
В другом варианте полиэтиленовые композиции включают более 50 мас.% ВМ полиэтилена в расчете на общую массу композиции, в другом варианте более 55 мас.%, в еще одном варианте от 50 до 80 мас.%, в другом варианте от 55 до 75 мас.% и в другом варианте от 55 до 70 мас.% при этом содержание в мас.% определяют методом ГПХ.
Более того, полиэтиленовые композиции по настоящему изобретению в одном варианте характеризуются динамической вязкостью при 200°С и 0,1/с от 100 кП до 3000 кП, в другом варианте от 300 кП до 1400 кП, в еще одном варианте от 350 кП до 1000 кП, в другом варианте от 400 кП до 800 кП и в еще одном варианте от 500 кП до 700 кП. Величины динамической вязкости, указанные в разделе Примеры в настоящем описании, измеряли по методике ASTM D4440-95 в атмосфере азота (зазор головки вискозиметра 1,5 мм и параллельные пластины размером 25 мм при 200°С и 0,1/с).
В другом объекте настоящего изобретения полиэтиленовая композиция, предназначенная для получения пленок, характеризуется эластичностью более 0,60, в другом варианте более 0,61, в еще одном варианте более 0,62 и в другом варианте более 0,63.
Отдельные компоненты полиэтиленовой композиции описаны со ссылкой на определенные варианты осуществления изобретения, и в одном варианте полиэтиленовая композиция включает один ВМ полиэтилен и один НМ полиэтилен; и в другом варианте полиэтиленовая композиция включает в основном один ВМ полиэтилен и один НМ полиэтилен.
В одном варианте молекулярно-массовое распределение (Mw/Mn) ВМ полиэтилена составляет интервал от 3 до 24, в другом варианте от 4 до 24, в еще одном варианте от 6 до 18, в другом варианте от 7 до 16 и в одном варианте от 8 до 14, при этом требуемый интервал величин включает любую комбинацию любого верхнего предела с любым нижним пределом, как описано в данном контексте. ВМ полиэтилен в одном варианте характеризуется среднемассовой молекулярной массой в интервале более 50000, в другом варианте от 50000 до 1000000, в еще одном варианте от 80000 до 900000, в другом варианте от 100000 до 800000 и в одном варианте от 250000 до 700000, при этом требуемый интервал величин включает любую комбинацию любого верхнего предела с любым нижним пределом, как описано в данном контексте. Массовая фракция ВМ полиэтилена в полиэтиленовой композиций изменяется в зависимости от требуемых свойств полиэтиленовой композиции, в одном варианте массовая фракция ВМ полиэтилена составляет интервал от 0,3 до 0,7, в другом предпочтительном варианте от 0,4 до 0,6 и в еще одном предпочтительном варианте от 0,5 до 0,6.
В одном варианте молекулярно-массовое распределение (Mw/Mn) ИМ полиэтилена составляет интервал от 1,8 до 6, в другом варианте от 2 до 5 и в еще одном варианте от 2,5 до 4, при этом требуемый интервал величин включает любую комбинацию любого верхнего предела с любым нижним пределом, как описано в данном контексте. В одном варианте среднемассовая молекулярная масса НМ полиэтилена находится в интервале от 2000 до 50000, в другом варианте от 3000 до 40000, в еще одном варианте от 4000 до 30000, при этом требуемый интервал величин содержания НМ полиэтилена в полиэтиленовой композиции включает любую комбинацию любого верхнего предела с любым нижним пределом, как описано в данном контексте. В другом варианте средне-массовая молекулярная масса НМ полиэтилена составляет менее 50000, в другом варианте менее 40000, в еще одном варианте менее 30000, в другом варианте менее 20000, в одном варианте менее 15000 и в еще одном варианте менее 13000. В одном варианте величина I2 для НМ полиэтилена составляет от 0,1 дг/мин до 10000 дг/мин, в другом варианте от 1 дг/мин до 5000 дг/мин и в еще одном варианте от 100 дг/мин до 3000 дг/мин, а величина I21 составляет от 2,0 дг/мин до 300000 дг/мин, в другом варианте от 20 дг/мин до 150000 дг/мин и в еще одном варианте от 30 дг/мин до 15000 дг/мин, при этом требуемый интервал величин I2 и I21 включает любые комбинации любого верхнего предела с любым нижним пределом, как описано в данном контексте. Величины I2 и I21 для НМ полиэтилена определяют с использованием любых методик, известных в данной области техники, и в одном варианте определяют методом обращения свертки на кривой ГПХ.
Гранулы полиэтиленового материала получают способами, описанными в данном контексте для получения полиэтиленовой композиции. Необязательно, полиэтиленовую композицию смешивают с одной или более добавок. В зависимости от физического способа получения полиэтиленовой смеси с одной или более добавками перед превращением смеси в конечный пленочный продукт проводят достаточно интенсивное смешивание до образования однородной смеси. Один способ смешивания добавок с полиолефином заключается в контактировании компонентов в барабане или в других аппаратах для физического перемешивания, при этом полиолефин получают в реакторе в виде гранул. При необходимости за этой стадией следует смешивание в расплаве в экструдере. Другой способ смешивания компонентов заключается в смешивании в расплаве полиолефиновых гранул с добавками непосредственно в экструдере, брабендере или другом аппарате для смешивания расплавов, предпочтительно в экструдере. Примеры пригодных экструдеров включают экструдеры конструкции Farrel и Kobe. Так как не предполагается, что смешивание с добавками влияет на определяемые свойства полиэтиленовых композиций, описанных в разделе Примеры, плотность, реологические и другие свойства полиэтиленовых композиций определяют после смешивания композиций с добавками.
Примеры добавок включают, без ограничения перечисленным, технологические добавки, такие как фторэластомеры, полиэтиленгликоли и поликапролактоны, антиоксиданты, агенты зародышеобразования, поглотители кислот, пластификаторы, стабилизаторы, антикоррозионные агенты, порообразователи вещества, другие адсорбенты ультрафиолетового излучения, такие как антиоксиданты, приводящие к разрыву цепи и т.п., тушители, антистатики, глиданты, пигменты, красители и наполнители, а также отверждающие агенты, такие как пероксид.
Прежде всего содержание анитиоксидантов и стабилизаторов, таких как органические фосфиты, амины с заторможенной конформацией и фенолсодержащие антиоксиданты, в полиолефиновых композициях по настоящему изобретению составляет в одном варианте от 0,001 до 2 мас.%, в другом варианте от 0,01 до 1 мас.% и в еще одном варианте от 0,05 до 0,8 мас.%; иными словами, от 1 до 5000 част./млн в расчете на общую массу полимерной композиции, и в более предпочтительном варианте от 100 до 3000 част./млн. Примеры пригодных органических фосфитов, без ограничения перечисленным, включают трис(2,4-ди-трет-бутилфенил)фосфит (IRGAFOS 168) и дифосфит ди(2,4-ди-трет-бутилфенил)пентаэритрита (ULTRANOX 626). Примеры аминов с заторможенной конформацией, без ограничения перечисленным, включают поли[2-N,N’-ди(2,2,6,6-тетраметил-4-пиперидинил)гександиамин-4-(1-амино-1,1,3,3-тетраметилбутан)симтриазин] (CHIMASORB 944) и бис(1,2,2,6,6-пентаметил-4-пиперидил)себакат (TINUVIN 770). Примеры фенолсодержащих антиоксидантов, без ограничения перечисленным, включают пентаэритритиловый эфир тетракис(3,5-ди-трет-бутил-4-гидроксифенил)пропионовой кислоты (IRGANOX 1010), 1,3,5-три(3,5-ди-трет-бутил-4-гидроксибензилизоцианурат (IRGANOX 3114), трис(нонилфенил)фосфит (TNPP) и октадецил-3,5-ди-(трет)-бутил-4-гидроксигидроциннамат (IRGANOX 1076), другие добавки включают стеарат цинка и олеат цинка.
В одном варианте содержание наполнителей составляет от 0,1 до 5 мас.%, в другом варианте от 0,1 до 2 мас.%, в еще одном варианте от 0,2 до 1 мас.% и наиболее предпочтительно от 0,02 до 0,8 мас.%. Требуемые наполнители включают, без ограничения перечисленным, диоксид титана, карбид кремния, диоксид кремния (и другие осажденные или неосажденные оксиды кремния), оксид сурьмы, карбонат свинца, цинковые белила, литопон, циркон, корунд, шпинель, апатит, порошкообразный барит, сульфат бария, магнезит, сажа, ацетиленовая сажа, доломит, карбонат кальция, тальк и соединения гидротальцита с ионами Mg, Са или Zn с Al, Cr или Fe и СО3 и/или HPO4, гидратированные или негидратированные, порошкообразный кварц, гидрокарбонат-хлорид магния, стекловолокно, глина, оксид алюминия и другие оксиды и карбонаты металлов, гидроксиды металлов, хром, фосфор и бромированные антипирены, триоксид сурьмы, диоксид кремния, силикон и смеси описанных выше соединений. Такие наполнители прежде всего включают любые другие наполнители и порообразующие наполнители и подложки, известные в данной области техники.
В основном наполнители, антиоксиданты и другие аналогичные добавки включены в состав полиэтиленовых композиций по настоящему изобретению в количестве менее 2 мас.%, предпочтительно менее 1 мас.% и более предпочтительно менее 0,8 мас.% в расчете на общую массу композиции.
В одном варианте на стадии образования пеллетов в полиэтиленовую композицию добавляют также окислитель в качестве реакционноспособного компонента. В данном объекте полиэтиленовые композиции по настоящему изобретению подвергают экструзии в присутствии окислителя, предпочтительно кислорода, как описано в заявке WO 03/047839. В одном варианте в процессе экструзии при образовании пленки в полиэтиленовую композицию добавляют от 0,01 или 0,1 или 1 до 14 или 16 SCFM (стандартных кубических фунтов в минуту) кислорода, причем точное количество зависит от типа использованного экструдера и других условий. Другими словами, в одном варианте при экструзии в полимерную композицию добавляют от 10 до 21 об.% кислорода в атмосфере инертного газа, такого как азот. В одном варианте в экструдер добавляют достаточное количество кислорода для повышения величины I21/I2 полиэтиленовой композиции, образующейся в реакторе(ах), т.е. от 1 до 40% и в другом варианте от 5 до 25%. Полученные таким образом пеллеты используют затем для экструзии пленок по настоящему изобретению в отдельной установке, например, в установке Alpine.
Полученные гранулированные полиэтиленовые композиции, в присутствие или в отсутствие добавок формуют любыми способами в пленки: формованием с раздувом или литьем пленок или любыми другими способами для получения пленок, например, одноостно- или двухостноориентированные пленки, как описано в книге Plastics Processing (Radian Corporation, Noyes Data Corp. 1986). В наиболее предпочтительном варианте полиэтиленовые композиции по настоящему изобретению формуют в пленки, как описано в книге Film Extrusion Manual, Process, Materials, Properties (TAPPI, 1992). Еще более предпочтительными пленками по настоящему изобретению являются пленки, полученные экструзией с раздувом, способы получения которых в основном описаны, например, в книге Film Extrusion Manual, Process, Materials, Properties, cc.16-29.
Для получения пленок по настоящему изобретению используют любые экструдеры, пригодные для экструзии ПЭВП (плотность более 0,940 г/см3), эксплуатируемые в любых требуемых условиях для полимерных композиций, описанных в данном контексте. Такие экструдеры известны специалистам в данной области техники и включают экструдеры в одном варианте с диаметром шнека от 30 до 150 мм и в другом варианте от 35 до 120 мм, причем производительность таких экструдеров составляет в одном варианте от 100 до 1500 фунтов/ч и в другом варианте от 200 до 1000 фунтов/ч. В одном варианте используют шнековый экструдер, относительная длина L/D экструдера составляет в одном варианте от 80:1 до 2:1, в другом варианте от 60:1 до 6:1, в еще одном варианте от 40:1 до 12:1 и в другом варианте от 30:1 до 16:1.
Можно использовать однослойную или многослойную головку. В одном варианте используют однослойную головку размером от 50 до 200 мм, в другом варианте используют однослойную головку размером от 90 до 160 мм и в еще одном варианте используют однослойную головку размером от 100 до 140 мм; в одном варианте используют головку с номинальным зазором от 0,6 до 3 мм, в другом варианте от 0,8 до 2 мм и в еще одном варианте от 1 до 1,8 мм, причем требуемая головка может включать комбинацию любых вариантов, описанных в данном контексте. В предпочтительном варианте предпочтительная производительность обеспечивается при использовании шнекового экструдера размером 50 мм и соотношением L/D 21:1.
Температура в зонах экструдера, горловины и адаптера экструдера находится в интервале в одном варианте от 150°С до 230°С, в другом варианте от 160°С до 210°С и в еще одном варианте от 170°С до 190°С. В одном варианте температура в головке составляет интервал от 160°С до 250°С, в другом варианте от 170°С до 230°С и в еще одном варианте от 180°С до 210°С.
Таким образом, пленки по настоящему изобретению в другом варианте могут включать любые варианты по настоящему изобретению или комбинацию любых вариантов, описанных в данном контексте. Варианты осуществления настоящего изобретения без ограничения перечисленным иллюстрируются следующими примерами без ограничения объема изобретения.
Примеры
Следующие примеры относятся к газофазным способам полимеризации, которую проводят в реакторе с псевдоожиженным слоем катализатора, производительность которого составляет более 500 фунтов/ч (230 кг/ч) продукта со скоростью от 8 до 40 т/ч или более, с использованием сомономера этилена и 1-бутена, при этом получают полиэтиленовую композицию. В таблицах указаны различные образцы полимеров и пленок, полученных из данных образцов, а также условия реакции, в ходе которой отбирали образцы («примеры»). Описаны также различные свойства полученных полимерных продуктов и пленок. Продукты, описанные в примерах 1 и 2, получали экструзией в отсутствие кислорода (без заданных свойств), как описано ниже, в то время как продукты, описанные в примерах 3-9, получали экструзией в присутствие кислорода (с заданными свойствами), как описано в заявке WO 03/047839, включенной в настоящее описание в качестве ссылки. В примерах для сравнения описаны стандартные композиции, из которых получали пленки стандартными методами.
Псевдоожиженный слой реактора включает гранулы полиэтилена. Реактор пассивировали алкилалюминием, предпочтительно триметилалюминием. В каждом цикле газоообразные потоки этилена и водорода поступали в газовую линию рециркуляции, расположенную над псевдоожиженным слоем. Газы подавали в зону, расположенную ниже линии рециркуляции теплообменника и компрессора. Жидкий 1-бутеновый сомономер вводили в зону над псевдоожиженным слоем реактора. Контрольный агент (если он используется, в большинстве случаев изопропиловый спирт), который влияет на расщепление смолы и снижает загрязнение, прежде всего загрязнение нижней пластины, подавали в газообразной или жидкой форме в зону над псевдоожиженным слоем реактора в газовую линию рециркуляции. Отдельные потоки этилена, водорода и сомономера 1-бутена регулировали таким образом, чтобы обеспечить конечные условия в реакторе, как указано в каждом примере. Концентрацию газов измеряли с помощью хроматографа, встроенного в систему реактора.
В примерах 1 и 2 отбирали образцы после полимеризации, которую проводили в течение 3-4 сут в одном газофазном реакторе с псевдоожиженным слоем катализатора диаметром 8 футов и слоем катализатора высотой (от нижней пластины распределителя до начала зоны расширения) 38 футов. В примерах 3-9 отбирали образцы после другого цикла полимеризации, которую проводили в течение 3-4 сут в одном газофазном реакторе с псевдоожиженным слоем катализатора диаметром 11,3 фута и слоем катализатора высотой (от нижней пластины распределителя до начала зоны расширения) 44,6 футов.
В каждом цикле полимеризации, описанной в примерах по настоящему изобретению, биметаллический катализатор на подложке вводили непосредственно в псевдоожиженный слой с использованием очищенного азота. Скорость подачи катализатора регулировали таким образом, чтобы обеспечить приблизительно постоянный уровень производительности. В каждом цикле катализатор получали в присутствии диоксида кремния, дегидратированного при 875°С, и металлоценового соединения Ср2МХ2, где Ср означает н-бутилзамещенное циклопентадиенильное кольцо, М означает цирконий, а Х означает фтор. Источником титана для компонента Циглера-Натта являлся TiCl4.
В каждом цикле реакционноспособный слой растущих полиэтиленовых частиц поддерживали в псевдоожиженном состоянии с помощью непрерывного питающего потока и рециркулирующего газа, которые проходили через зону реакции. Как указано в таблицах, в каждом цикле полимеризации в примерах по настоящему изобретению использовали определенную температуру в реакторе («температуру слоя катализатора»), а именно приблизительно 95°С. В процессе каждого цикла температуру в реакторе поддерживали на приблизительно постоянном уровне, снижая или повышая температуру рециркулирующего газа для компенсации любых изменений скорости теплообразования в процессе полимеризации.
Полимерные композиции, описанные в примерах, подвергали экструзии в 4-дюймовых смесителях Фаррела (или Кобе) непрерывного действия (4UMSD) при скорости 500 фунт/ч, потребляемой удельной мощности на входе 0,125 л.с.-ч/фунт, при этом получали гранулы. Добавляли также набор добавок, например, полимерные композиции, описанные в примерах 1-9, включали 800 част./млн продукта IRGANOX 1010 (пентаэритритилтетракис-3-(3,5-ди-трет-бутил-4-гидроксифенил)пропионат), 200 част./млн продукта IRGAFOS 168 (трис(2,4-ди-трет-бутилфенил)фосфит) и 1500 част./млн стеарата цинка. Композиции, описанные в примерах 1 и 2, подвергали экструзии в атмосфере азота (0% кислорода), композиции, описанные в примерах 3-9, подвергали экструзии в присутствии определенного количества кислорода, как описано в заявке WO 03/047839.
Свойства полимерных композиций описаны в таблицах. Соотношение “I21:HMW:MFR” рассчитывали с использованием I21 для высокомолекулярного компонента и величин I21 и I2 с использованием следующего эмпирического уравнения (IV):

где I21 и I21 определяют по методике ASTM, описанной в данном контексте. Соотношение “I21:HMW:DSR” рассчитывали с использованием I21 для высокомолекулярного компонента и определенных величин динамической вязкости с использованием следующего уровня (V):

где
* x (пуазы) означает комплексную вязкость, определенную при 200°С и частоте х,
G’x (дин/см2) является действительной составляющей модуля сдвига, определенного при 200°С и частоте х, и
G”x (дин/см2) является мнимой составляющей модуля сдвига, определенной при 200°С и частоте (рад/с) х.
Указанные величины определяли с использованием динамического реометра Rheometrics Dynamic Stress с параллельными пластинами длиной 25 мм, зазором головки приблизительно 1,4 мм, при напряжении 10000 дин/см2 и по методике, описанной в стандарте ASTM D4440-01, «Стандартный способ испытания пластмасс: Динамо-механические свойства, определение реологических свойств расплава».
Образцы, описанные в примерах 1 и 2, обрабатывали экструзией на установке для формования с раздувом (условия описаны в таблице 2), при этом размер шнеков (21 d) экструдера составляет 50 мм и экструдер включает узел питания из ЛПЭНП (номер по каталогу Alpine 171764). Температуру плавления Тm измеряли с помощью иммерсионной термопары в узле адаптера вблизи выходного отверстия экструдера. Для охлаждения экструдера использовали охлажденный воздух (на внешней поверхности пузыря).
Ниже описаны другие методы анализа:
Толщину пленок измеряли согласно методу ASTM D374-94, способ С.
FI (I21): индекс текучести (I21) измеряли согласно методу ASTM D 1238 при 190°С, 21,6 кг.
MI (I2): индекс расплава (I2) измеряли согласно методу ASTM D 1238 при 190°С, 21,6 кг.
MFR: отношение индексов текучести и расплава определяли как соотношение I21/I21.
Плотность (г/см3) определяли с использованием образцов, вырезанных из сжатых слоев, которые формовали согласно методу ASTM D-4703-00, в условиях ASTM D618, методика А, и измерения проводили согласно ASTM D1505-03.
Эластичность определяли специальным методом по соотношению G’/G”, измеренному при 0,1 рад/с. G’ и G” измеряли на реометре Stress Rheometer (при 200°С на динамическом реометре Dynamic Stree Rheometer) при осцилляционном сдвиге и постоянном напряжении 1000 Па. Величины G’ и G” при 0,1 рад/с выбирали для определения эластичности.
Комплексную вязкость * измеряли на реометре Stress Rheometer при 0,1 рад/с и 200°С.
FAR: “внешний вид пленки” определяли специальным методом, согласно которому полимер подвергали экструзии в стандартных условиях и полученную пленку исследовали визуально на наличие поверхностных дефектов. Пленку сравнивали с набором стандартных пленок и величину FAR оценивали по специальной шкале с участием оператора. Стандартные пленки характеризуются величиной FAR в интервале от -50 до +50, и пленки с величиной FAR +20 и более пригодны для коммерческого использования.
Содержание гель-фракции определяли с использованием следующих приборов: экструдер фирмы Optical Control Systems GmbH (OCS), модель МЕ-20, система для формования пленок OCS, модель CR-8, и прибор для определения содержания геля OCS, модель FS-5. Экструдер МЕ-20 включает стандартный шнек 3/4” с соотношением компрессии 3:1 и относительной длиной L/D 25:1, а также включает зону подачи сырья, зону компрессии и зону дозировки. В экструдере использовали все твердые контроли, двигатель для движения шнека при переменной частоте и переменном токе, 5 зон нагревания, включая 3 зоны для барабана, 1 зону для измерения температуры плавления и давления и 1 зону для головки. Головка экструдера представляет собой головку типа «рыбий хвост» с фиксирующими губками размером 4” с зазором головки приблизительно 20 мил. Испытание образцов проводили на фирме Southern Analytical, Inc., Houston TX.
Система для отливки пленок включает изготовленные из нержавеющей стали двойные хромированные и полированные охлаждающие валки, изготовленный на станке точный воздушный шабер, зажимные резиновые валки, проталкивающие пленку через определитель содержания гель-фракции, и устройство для наматывания пленки в рулон. Зажимные валки вращаются отдельно от охлаждающих валков и их скорость вращения или натяжение регулируется. В систему включен также узел охлаждения/нагревания для охлаждающих вальцов, в котором используют этиленгликоль. В систему включены также стальные полозья, датчики разрыва пленки и другие узлы. Пленки, полученные, как описано в примерах 3-9, характеризуются толщиной 1 мил (25 мкм), а пленки, описанные в примерах сравнения С2, С3 и С5 толщиной 2 мил (50 мкм).
Определитель содержания гель-фракции включает цифровую камеру на 2048 пикселей, галогеновую лампу, компьютер для обработки изображений и программное обеспечение Windows NT4. Система камера/лампа встроена в систему для формования пленок между охлаждающими валками и обжимными валками, а степень разрешения указанной системы составляет 50 мкм. Такие системы позволяют выявить малейшие дефекты размером 50 мкм на 50 мкм.
Гранулированные образцы подвергали экструзии при постоянных температуре экструзии (180°С в зоне подачи, 190°С в остальных зонах) и постоянной температуре охлаждающего валка 40°С. Скорость движения экструдера и охлаждающих валков незначительно изменяли в зависимости от образца, чтобы обеспечить образование из каждого образца пленок с оптимальными свойствами. При проведении дополнительных экспериментов был определен один набор рабочих условий, пригодный для экструзии всех образцов. Параметры определителя содержания гель-фракции устанавливали следующим образом: 10 различных размеров начиная от 50-100 мкм с шагом в 100 мкм, 4 различных формы от правильной круглой формы до более продолговатой формы и два уровня чувствительности (один для гелей и один для черных пятен). Уровень детектирования гелей или чувствительность составляли 35 по шкале от 0 до 100.
После установки параметров в камере в экструдер подавали первый образец (в большинстве случаев в течение приблизительно 20 мин) или до установления стабильных или «равновесных» условий. Равновесие определяли по линии тренда содержания геля на оси у и времени на оси х. Затем проводили испытания на 3 м пленки при ее продвижении через камеру. Для определения повторяемости испытания проводили в 3 удачных повторах для каждого образца. В конце оценки каждых 3 м2 результаты распечатывали в виде таблицы. После очистки для первого образца проводили испытания 3 м2 пленки второго образца в трех повторах и распечатывали результаты.
Все гелевые остальные образцы испытывали на содержание геля аналогичным образом, но для некоторых образцов незначительно изменяли скорость экструдера, скорость охлаждающих валков и толщину полученной пленки. В ходе испытаний просматривали изображения реальных пленок (в виде «мозаики» изображений), чтобы убедиться в правильности анализа, чтобы исключить повторную идентификацию одного и того же геля или чтобы не пропустить гели. Для гранулированных образцов был установлен один набор рабочих условий, пригодных для всех образцов, включая толщину пленки, чтобы сравнивать все полученные результаты.
Табличные данные определителя гель-фракции нормированы на толщину. Каждый образец измеряли в трех повторах. Данные, полученные при испытаниях, использовали для расчета суммы всех гелей размером 200 мкм или менее. Данные трех повторов для каждого образца усредняли, затем среднюю величину делили на толщину в мил. Результаты определителя гель-фракции выражали в виде числа гелей размером менее 200 мкм в образце пленки 3 м2, или на 7,62×10-5 м3.
Напряжение мгновенного удара F50 измеряли на пленке по методике ASTM D 1709, способ А.
Разрыв по Элмендорфу измеряли на пленке по методике ASTM D 1922.
Секущий модуль 1% – измеряли на пленке по методике ASTM D 882.
Гельпроникающая хроматография (ГПХ). Величины Mw/Mn, Mz/Mw, Mw (сред немассовая молекулярная масса) и Mn (среднечисловая молекулярная масса) и содержание ВМ компонента в % и т.п. определяли методом ГПХ на колонках со сшитым полистиролом с использованием последовательности колонок с различным размером пор: 1 колонка менее 1000, 3 колонки с различным размером пор 5×10(7); растворитель 1,2,4-трихлорбензол при 145°С, детекция по показателю преломления. По данным ГПХ определяли содержание высокомолекулярного и низкомолекулярного компонентов методом обращения свертки с использованием модели Весслау, где величина Р снижена для низкомолекулярного пика до 1,4, как описано в статье Е.Broyer & R.F.Abbott, Analysis of molecular weight distribution using multicomponent models, ACS Symp. Ser., 197 (Comput. Appl. Appl. Polym. Sci.), 45-64 (1982).
В примере для сравнения 2 («С2») описан бимодальный поли(этилен-со-1-бутен) Dow UNIPOL II 2100, полученный в двухстадийном газофазном реакторе в присутствии катализатора Циглера-Натта.
В примере 3 для сравнения («С3») описан бимодальный поли(этилен-со-1-бутен) Mitsui HD7960, полученный в двухстадийным эмульсионным способом (фирмы ExxonMobil Chemical Co).
В примере для сравнения 4 («С4») описан бимодальный поли(этилен-со-1-бутен) Mitsui HD7755, полученный двухстадийным эмульсионным способом (фирмы ExxonMobil Chemical Co).
В примере для сравнения 5 («С5») описан бимодальный поли(этилен-со-1-бутен) Alathon L5005, полученный двухстадийным способом (фирмы Equistar Chemicals).

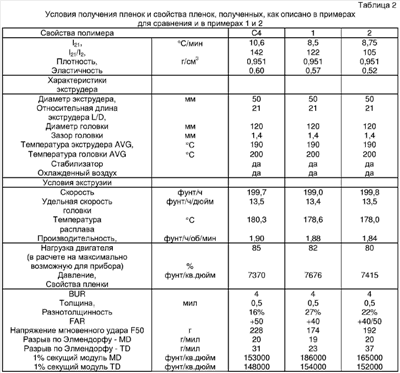
Описанные в примерах 1 и 2 полимерные композиции, полученные в одном газофазном реакторе в присутствии биметаллического катализатора, как описано в данном контексте, характеризуются неожиданными улучшенными технологическими характеристиками по сравнению с общеизвестными бимодальными полимерами, полученными в двух реакторах. Более низкая мощность, как показано на фиг.1 и 2, представляет значительное преимущество для производства пленок, т.к. композиции по настоящему изобретению можно получить более простым способом, что приводит к снижению их рыночной стоимости. Эти результаты действительно являются неожиданными, поскольку величины I21 для образцов, описанных в примерах 1 и 2, ниже по сравнению с величинами для образцов, полученных в примерах для сравнения, и, следовательно, количество потребляемой мощности для формования пленок через головку экструдера должно повышаться, а не понижаться.
Другим преимуществом являются значительно более низкие температуры расплава образцов, описанных в примерах 1 и 2, по сравнению с образцами в примерах для сравнения, что приводит к улучшению их технологических характеристик. В примерах по настоящему изобретению описаны температуры расплава менее 180°С и в одном предпочтительном варианте менее 179°С при сохранении высокой удельной скорости на выходе из головки экструдера по крайней мере 10 фунтов полимера/ч/дюйм окружности головки и высокой производительности. Таким образом, при равных нагрузках двигателя и/или давлении в примерах 1 и 2 по сравнению с примером С4 производительность должна быть выше по крайней мере на 1,90 фунтов полиэтилена/ч/об/мин (0,83 кг/ч/об/мин) при равных температурах расплава.
Условия получения полиэтиленовых композиций в реакторе, соответствующие условиям получения пленок в примерах 3-9, показаны в таблице 3 ниже. Свойства полиэтиленовой композиции в соответствующих примерах указаны в таблице 4. Для получения пленок, описанных в примерах 3-9, для определения соотношения Tm 235-3,3 (I21) и других вариантов использовали следующие приборы и условия: экструзионная система Alpine со шнековым экструдером размером 50 мм, относительной длиной L/D 21:1, температурный профиль в экструдере 180°С и в зоне головки экструдера 190°С, соотношение BUR 4:1 (соотношение при раздуве, т.е. отношение диаметра исходного пузыря к диаметру головки экструдера), производительность на выходе 200 фунт/ч и головка размером 120 мм с щелью 1,4 мм с использованием конструкции шнека высокой плотности, одного воздушного зажимного кольца (с охлажденным воздухом) и внутренним стабилизатором пузыря, размер шнека 21 d из ПЭВП 50 мм и узел подачи из ПЭВП (номер по каталогу Alpine 116882). Температуру расплава Tm измеряли с использованием иммерсионной термопары в узле адаптера вблизи выходного отверстия экструдера. Образцы, описанные в примерах 3-9, обрабатывали в присутствии кислорода (пленки с заданными свойствами). Условия экструзии и свойства пленок, полученных в примерах 3-9, описаны в таблицах 5 и 6.
Образцы, полученные в примерах 3-9, характеризуются отсутствием запаха. Несмотря на обработку образцов, описанных в примерах 3-9, кислородом (которые, таким образом, характеризуются в среднем большими величинами I21 и I2), они обладают преимуществами по настоящему изобретению, поскольку такие полимеры можно обрабатывать более простым способом по сравнению с полимерами, известными в предшествующем уровне техники.
Таблица 3. Условия полимеризации образцов, описанных в примерах 3-9 |
Характеристика |
Единицы |
3 |
4 |
5 |
6 |
7 |
8 |
9 |
Кол-во ПЭ в течение 24 ч |
тонны |
156 |
156 |
156 |
156 |
156 |
156 |
156 |
H2/C2 |
моль/моль |
0,0085 |
0,0085 |
0,009 |
0,009 |
0,009 |
0,009 |
0,009 |
С4/С2 |
моль/моль |
0,0272 |
0,0272 |
0,021 |
0,021 |
0,021 |
0,0183 |
0,0183 |
Отношение С4/С2 в потоке |
кг/кг |
0,0166 |
0,0166 |
0,0122 |
0,0122 |
0,0122 |
0,0122 |
0,0122 |
Парциальное давление С2 |
кПа |
1400 |
1400 |
1400 |
1400 |
1400 |
1400 |
1400 |
Активность Ti |
кг ПЭ/кг катализатора |
6766 |
* |
5327 |
5927 |
6762 |
5819 |
5915 |
Количество ТМА в реакторе |
мас. част./млн |
103 |
* |
96 |
102 |
107 |
101 |
123 |
Температура в реакторе |
°С |
95 |
95 |
95 |
95 |
95 |
95 |
95 |
* величину не определяли, предполагается, что она приблизительно равна полученным ранее данным |
Таблица 4. Свойства полиэтиленовых пленок, полученных, как описано в примерах 3-9, и в примерах для сравнения |
Пример |
Плотность (г/см3) |
I21 (°С/мин) |
I21/I2 |
Мw/Mn |
эластичность |
С2 |
0,949 |
10,38 |
160 |
26 |
0,68 |
С3 |
0,952 |
11,9 |
133 |
– |
0,60 |
С5 |
0,950 |
8,6 |
152 |
– |
0,64 |
3 |
0,949 |
8,39 |
137 |
84 |
0,62 |
4 |
0,949 |
9,38 |
157 |
83 |
0,65 |
5 |
0,949 |
11,12 |
168 |
90 |
0,62 |
6 |
0,948 |
8,09 |
146 |
82 |
0,61 |
7 |
0,947 |
8,61 |
146 |
81 |
0,61 |
8 |
0,950 |
10,01 |
174 |
91 |
0,64 |
9 |
0,951 |
11,5 |
196 |
110 |
0,65 |
Таблица 5. Прочие свойства полиэтилена, полученного, как описано в примерах 3-9, и в примерах для сравнения |
Св-во |
Ед. |
3 |
4 |
5 |
6 |
7 |
0 |
9 |
С2 |
С3 |
С5 |
Свойства полимера |
HM Mw |
|
7823 |
8620 |
8644 |
8698 |
8709 |
7959 |
6389 |
21454 |
– |
– |
BM Mw |
|
444443 |
480543 |
505190 |
539136 |
456299 |
494016 |
493254 |
481868 |
– |
– |
BM MWD |
|
8,5 |
7,3 |
7,2 |
7,6 |
6,5 |
7,0 |
12,0 |
4,3 |
– |
– |
Таблица 6. Свойства и условия экструзии пленок, полученных, как описано в примерах 3-9, и в примерах для сравнения |
Св-во |
Ед. |
3 |
4 |
5 |
6 |
7 |
8 |
9 |
С2 |
С3 |
С5 |
Условия экструзии |
Темп. распл. |
°С |
201 |
196 |
195,5 |
206 |
204 |
194 |
193 |
209 |
200,5 |
212 |
Давление |
Фунт/кв. дюйм |
8550 |
8200 |
8250 |
8980 |
8780 |
8210 |
8110 |
8200 |
7960 |
8450 |
Нагрузка двигателя |
% |
77% |
71% |
74% |
78% |
77% |
75% |
74% |
82% |
77% |
80% |
Производительность. |
фунт/ч/об/мин |
1,16 |
1,17 |
1,18 |
1,17 |
1,17 |
1,18 |
1,18 |
1,18 |
1,19 |
1,19 |
Толщина |
мил |
0,5 |
0,5 |
0,5 |
0,5 |
0,5 |
0,5 |
0,5 |
0,5 |
0,5 |
0,5 |
BUR |
|
4:1 |
4:1 |
4:1 |
4:1 |
4:1 |
4:1 |
4:1 |
4:1 |
4:1 |
4:1 |
FAR |
|
40/50 |
40/50 |
40/50 |
40/50 |
40/50 |
40/50 |
50 |
50 |
50 |
40 |
Содерж. геля |
|
199 |
34 |
36 |
29 |
32,5 |
31 |
28 |
– |
218 |
33 |
DDI |
г |
182 |
– |
201 |
178 |
180 |
194 |
– |
219 |
270 |
166 |
Разрыв MD |
г/мил |
21 |
– |
24 |
20 |
22 |
25 |
– |
24 |
17 |
22 |
Разрыв TD |
г/мил |
30 |
– |
31 |
32 |
27 |
31 |
– |
41 |
53 |
27 |
Предел прочн. на разрыв MD |
фунт/кв. дюйм |
11632 |
– |
11389 |
12324 |
11156 |
11140 |
– |
12228 |
11019 |
11406 |
Предел прочн. на разрыв TD |
фунт/кв. дюйм |
11639 |
– |
10942 |
10404 |
12275 |
10863 |
– |
12746 |
11784 |
10816 |
Отн. удл. при раст. MD |
% |
278% |
– |
288% |
251% |
252% |
275% |
– |
299% |
408% |
279% |
TD отн. удл.при раст. |
% |
278% |
– |
273% |
304% |
288% |
259% |
– |
322% |
356% |
385% |
Пред. текуч. MD |
фунт/кв. дюйм |
5840 |
– |
5376 |
6009 |
5786 |
5374 |
– |
5186 |
5325 |
5293 |
Пред. текуч. TD |
фунт/кв. дюйм |
4697 |
– |
4575 |
4548 |
4725 |
4568 |
– |
– |
4335 |
4627 |
Разр. удл. MD |
% |
3% |
– |
4% |
5% |
5% |
5% |
– |
– |
8% |
5% |
Разр. удл. TD |
% |
6% |
– |
4% |
4% |
4% |
4% |
– |
– |
5% |
6% |
Пленки, описанные в примерах 3-9, характеризуются высоким качеством, о чем свидетельствуют высокие величины FAR и низкое содержание гель-фракции. При равных величинах FAR образцов, описанных в примерах 1 и 2, они также характеризуются одинаково низким содержанием гель-фракции. Следовательно, обработка кислородом не влияет на качество пленки.
Более того, преимущества пленок по настоящему изобретению подтверждаются следующими данными. Прежде всего при относительно высокой производительности значительно снижается нагрузка двигателя, определенная в процентах от максимально возможной для данного прибора нагрузки двигателя, т.е. нагрузка составляет менее 77-78% для примеров 3-9 по сравнению с каждым образцом, полученным в примерах для сравнения, для которых нагрузка значительно выше. Кроме того, температуры расплава для образцов, полученных в примерах по настоящему изобретению, значительно ниже по сравнению с примерами для сравнения. Образцы, описанные в примерах 3-9, подчиняются также соотношению Тm 235-3,3 (I21), при этом полиэтиленовую композицию подвергают экструзии с производительностью от 1 до 1,5 фунт/ч/дюйм, как показано на графике на фиг.6. Более того, более общее выражение Тm Тm x-3,3 (I21) также выполняется при сравнении примеров 1 и 2 и примеров 3-9, хотя каждый набор образцов подвергался экструзии в разных условиях и с различными конструкциями шнеков экструдеров.
Прежде всего преимущества настоящего изобретения представляются очевидными при сравнении нагрузок двигателей (%) и температур расплавов образцов, описанных в примерах 3-9 и примерах для сравнения, как указано в таблице 5, и на графиках на фиг.6 и 7. В то время как для образцов, описанных в примерах по настоящему изобретению, наблюдается тенденция к снижению температур расплава и нагрузок двигателя при увеличении величины I21, для сравнительных образцов эти величины увеличиваются.
Как следует из сравнения величин производительности, температуры расплава и нагрузки двигателя, в настоящем изобретении предлагается значительное усовершенствование по сравнению с предшествующим уровнем техники, даже по сравнению с уровнем техники, в котором описаны бимодальные продукты, полученные в одном реакторе, как описано в статье Н.-Т. Liu и др., Macromol. Symp.195, 309-316 (July, 2003). Пленки, полученные, как описано в работе Liu и др, из полимеров, характеризующиеся технологическими параметрами: величиной I21 6,2°С/мин и плотностью 0,95 г/см3, не обладают такими преимуществами, как пленки по настоящему изобретению. Следовательно, в настоящем изобретении предлагается значительное усовершенствование по сравнению с предшествующим уровнем техники, т.е. по сравнению с бимодальными полимерами с величинами I21 менее 20 и плотностью в интервале от 0,930 до 0,970 г/см3, причем указанное преимущество является достаточно значительным с учетом больших количеств полимеров, подвергающихся переработке в промышленных экструдерах.
Несмотря на то что настоящее изобретение описано и иллюстрировано со ссылкой на определенные варианты его осуществления, специалистам в данной области техники следует понимать, что возможно множество модификаций, не описанных в данном контексте. В связи с этим объем изобретения определен только в прилагаемых пунктах формулы изобретения. Более того, определенные признаки настоящего изобретения указаны в интервалах от ряда верхних пределов до ряда нижних пределов. Следует понимать, что все интервалы, полученные любой комбинацией таких пределов, включены в объем настоящего изобретения, если не указано иное.
Формула изобретения
1. Пленка, включающая полиэтиленовую композицию, которая характеризуется плотностью от 0,940 до 0,970 г/см3, полиэтиленовая композиция включает высокомолекулярный компонент, характеризующийся среднемассовой молекулярной массой более 50000, и низкомолекулярный компонент, характеризующийся среднемассовой молекулярной массой менее 50000; и величиной индекса расплава (I21), измеренной по методике ASTM-D-1238-F, 190°С/21,6 кг, от 4 до 20 дг/мин, причем полиэтиленовая композиция подвергается экструзии при температуре расплава Тm, величина которой удовлетворяет следующему соотношению:
Tm 235-3,3 (I21),
причем полиэтиленовая композиция подвергается экструзии с производительностью от 1 до 1,5 фунтов/ч/об/мин, а полученная из полиэтиленовой композиции пленка характеризуется величиной содержания гель-фракции менее 100.
2. Пленка по п.1, отличающаяся тем, что полиэтиленовая композиция включает высокомолекулярный компонент, характеризующийся среднемассовой молекулярной массой более 50000, и низкомолекулярный компонент, характеризующийся среднемассовой молекулярной массой менее 40000.
3. Пленка по п.1, отличающаяся тем, что величина Mw/Mn полиэтиленовой композиции составляет более 35.
4. Пленка по п.1, отличающаяся тем, что величина Mw/Mn полиэтиленовой композиции составляет более 50.
5. Пленка по п.1, отличающаяся тем, что полиэтиленовая композиция включает высокомолекулярный компонент, характеризующийся среднемассовой молекулярной массой более 150000, и низкомолекулярный компонент, характеризующийся среднемассовой молекулярной массой менее 35000.
6. Пленка по п.1, отличающаяся тем, что полиэтиленовая композиция включает высокомолекулярный компонент, характеризующийся среднемассовой молекулярной массой более 250000, и низкомолекулярный компонент, характеризующийся среднемассовой молекулярной массой менее 35000.
7. Пленка по п.1, отличающаяся тем, что эластичность полиэтиленовой композиции составляет более 0,60.
8. Пленка по п.1, отличающаяся тем, что полиэтиленовая композиция не содержит твердых веществ, ухудшающих качества пленки.
9. Пленка по п.1, отличающаяся тем, что пленку получают по многостадийному способу, включающему:
(а) получение полиэтиленовой композиции, включающее включение высокомолекулярного полимера в низкомолекулярный полимер при контактировании этилена и С3-С12– -олефинов, алкилалюминия и биметаллической каталитической композиции,
(б) экструзию полиэтиленовой композиции с образованием гранул при необязательном добавлении кислорода, при этом получают пеллеты полиэтиленовой композиции,
(в) выделение гранул полиэтиленовой композиции,
(г) экструзию гранул полиэтиленовой композиции в экструдере для формования пленки.
10. Пленка по п.9, отличающаяся тем, что на стадии (б) в полиэтиленовую композицию добавляют от 0,01 до 14 стандартных кубических фунтов в минуту (SCFM) кислорода.
11. Пленка по п.1, отличающаяся тем, что полиэтиленовую композицию получают в одном газофазном реакторе непрерывного действия.
12. Пленка по п.1, отличающаяся тем, что содержание гель-фракции в пленке составляет менее 50.
13. Пленка по п.1, отличающаяся тем, что содержание высокомолекулярного компонента по данным гельпроникающей хроматографии (ГПХ) составляет более 50 мас.% в расчете на общую массу полиэтиленовой композиции.
14. Пленка по п.1, отличающаяся тем, что экструзию полиэтиленовой композиции проводят при нагрузке двигателя менее 80% от максимально возможной нагрузки двигателя.
15. Пленка, включающая полиэтиленовую композицию, которая характеризуется
а) плотностью от 0,940 до 0,970 г/см3,
б) величиной Mw/Mn, составляющей более 35;
в) величиной индекса расплава (I21), измеренной по методике ASTM-D-1238-F, 190°С/21,6 кг, от 4 до 20 дг/мин;
и дополнительно характеризуется тем, что полиэтиленовая композиция подвергается экструзии при температуре расплава Тm, величина которой удовлетворяет следующему соотношению:
Tm 235-3,3 (I21),
причем полиэтиленовая композиция подвергается экструзии с производительностью от 1 до 1,5 фунтов/ч/об/мин, а полученная из полиэтиленовой композиции пленка характеризуется величиной содержания гель-фракции менее 100.
16. Пленка по п.15, отличающаяся тем, что полиэтиленовая композиция включает высокомолекулярный компонент, характеризующийся среднемассовой молекулярной массой более 50000, и низкомолекулярный компонент, характеризующийся среднемассовой молекулярной массой менее 40000.
17. Пленка по п.15, отличающаяся тем, что величина Mw/Mn полиэтиленовой композиции составляет более 35.
18. Пленка по п.15, отличающаяся тем, что величина Mw/Mn полиэтиленовой композиции составляет более 50.
19. Пленка по п.15, отличающаяся тем, что полиэтиленовая композиция включает высокомолекулярный компонент, характеризующийся среднемассовой молекулярной массой более 150000, и низкомолекулярный компонент, характеризующийся среднемассовой молекулярной массой менее 35000.
20. Пленка по п.15, отличающаяся тем, что полиэтиленовая композиция включает высокомолекулярный компонент, характеризующийся среднемассовой молекулярной массой более 250000, и низкомолекулярный компонент, характеризующийся среднемассовой молекулярной массой менее 35000.
21. Пленка по п.15, отличающаяся тем, что эластичность полиэтиленовой композиции составляет более 0,60.
22. Пленка по п.15, отличающаяся тем, что полиэтиленовая композиция не содержит твердых веществ, ухудшающих качества пленки.
23. Пленка по п.15, отличающаяся тем, что пленку получают по многостадийному способу, включающему:
(а) получение полиэтиленовой композиции, включающее включение высокомолекулярного полимера в низкомолекулярный полимер при контактировании этилена и С3-С12– -олефинов, алкилалюминия и биметаллической каталитической композиции,
(б) экструзию полиэтиленовой композиции с образованием гранул при необязательном добавлении кислорода, при этом получают пеллеты полиэтиленовой композиции,
(в) выделение гранул полиэтиленовой композиции,
(г) экструзию гранул полиэтиленовой композиции в экструдере для формования пленки.
24. Пленка по п.23, отличающаяся тем, что на стадии (б) в полиэтиленовую композицию добавляют от 0,01 до 14 стандартных кубических фунтов в минуту (SCFM) кислорода.
25. Пленка по п.15, отличающаяся тем, что полиэтиленовую композицию получают в одном газофазном реакторе непрерывного действия.
26. Пленка по п.15, отличающаяся тем, что содержание гель-фракции в пленке составляет менее 50.
27. Пленка по п.15, отличающаяся тем, что содержание высокомолекулярного компонента по данным гельпроникающей хроматографии (ГПХ) составляет более 50 мас.% в расчете на общую массу полиэтиленовой композиции.
28. Пленка по п.15, отличающаяся тем, что экструзию полиэтиленовой композиции проводят при нагрузке двигателя менее 80% от максимально возможной нагрузки двигателя.
РИСУНКИ
|
|