|
(21), (22) Заявка: 2007132886/06, 03.09.2007
(24) Дата начала отсчета срока действия патента:
03.09.2007
(46) Опубликовано: 27.02.2009
(56) Список документов, цитированных в отчете о поиске:
RU 2100733 С1, 27.12.1997. SU 347547 А1, 10.08.1972. RU 2181186 С1, 10.04.2002. FR 2657422 А, 26.07.1991.
Адрес для переписки:
109469, Москва, Марьинский парк, 23, к.1, кв.46, А.И. Худякову
|
(72) Автор(ы):
Худяков Алексей Иванович (RU)
(73) Патентообладатель(и):
Худяков Алексей Иванович (RU)
|
(54) ПРОТИВОТОЧНЫЙ ПЛАСТИНЧАТЫЙ ТЕПЛООБМЕННИК
(57) Реферат:
Изобретение предназначено для применения в теплотехнике, а именно в любых отраслях техники для подогрева или охлаждения газообразных сред при высоких термодинамических параметрах и больших расходах теплоносителей. Противоточный пластинчатый теплообменник содержит теплообменные элементы, выполненные из попарно сложенных пластин, причем каждая пластина имеет, по крайней мере, две теплопередающих и четыре коллекторных части для подвода и распределения теплоносителей, коллекторная часть теплоносителя большего давления располагается между теплопередающими частями, а коллекторная часть теплоносителя меньшего давления – по всей ширине пластины со сторон его входа и выхода. Коллекторные части пластины теплоносителя большего давления перегорожены поперечной выштамповкой на раздающий коллектор и сборный коллектор, на длине участка противоточного движения теплоносителей коллекторные части отделены от теплопередающих частей продольными выштамповками, ограниченными по длине участком входа теплоносителя из раздающего коллектора в теплопередающие части и участком выхода теплоносителя в сборный коллектор. На теплопередающих частях пластины выполнены гофры под углом наклона к сторонам пластины, отличным от 90 градусов. По периметру пластины выполнены отбортовки, закрывающие при сварке (пайке) от утечек теплоноситель меньшего давления, а по внешней стороне каждой теплопередающей части выполнены дополнительные отбортовки, препятствующие при сварке (пайке) утечкам теплоносителя большего давления. Изобретение позволяет повысить эффективность теплообменника и уменьшить число коллекторов и трубопроводов. 2 з.п. ф-лы, 5 ил.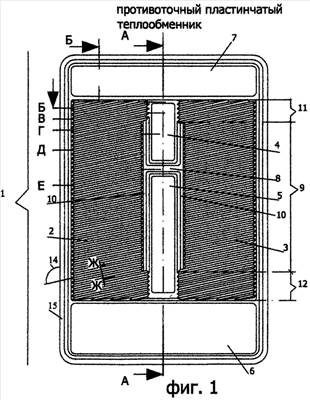
Изобретение относится к теплотехнике и может быть использовано в любых отраслях техники для подогрева или охлаждения газообразных сред с высокими термодинамическими параметрами, в том числе для подогрева воздуха газотурбинной установки (ГТУ) большой мощности, использующей закрытую систему циркуляции теплоносителей.
Существуют противоточные пластинчатые теплообменники, содержащие корпус и пакет гофрированных теплопередающих пластин, стянутых с помощью стяжных элементов [Барановский Н.В., Коваленко Л.М., Ястребенецкий А.Р. Пластинчатые и спиральные теплообменники. М.: Машиностроение, 973]. Теплообменный элемент таких теплообменников состоит из отдельных пластин, которые уплотняются прокладками. Пластины имеют форму прямоугольника и четыре отверстия для подвода и отвода теплоносителей. Эти теплообменники имеют ограниченную размерами пластины площадь фронта и применяются для жидких сред при невысоких параметров сред (Р 25 бар, Т 140°С).
Существуют аналогичные теплообменники без прокладок, в которых пластины соединены пайкой или сваркой [Проспекты фирм “Альфа Ловаль”, “SWEP”]. Они позволяют повысить параметры сред, но размеры отверстий и их расположение по углам пластины ограничивают пропускную способность и, следовательно, мощность теплообменника.
Наиболее близким к предлагаемому изобретению является теплообменник [Патент РФ№2100733], в котором теплоносители подаются в пакет гофрированных теплопередающих пластин различными способами. Один теплоноситель подается в пакет через отверстия в пластинах, а второй теплоноситель подается в корпус с размещенным в нем пакетом, а из корпуса – непосредственно в пакет. Такое решение позволяет значительно увеличить расход второго теплоносителя или использовать среду с меньшей плотностью (например, воздух).
Недостаток такого теплообменника состоит в ограниченном расходе теплоносителя через отверстия в пластинах и наличие дополнительного элемента – корпуса, увеличивающего габариты и массу всего теплообменника. Рациональная область их применения – газожидкостные теплообменники.
Предлагаемый теплообменник отличается от прототипа тем, что каждая пластина имеет, по крайней мере, две теплопередающие части и четыре коллекторные части для подвода и распределения теплоносителей, коллекторная часть теплоносителя большего давления располагается между теплопередающими частями, а коллекторная часть теплоносителя меньшего давления – по всей ширине пластины со сторон его входа и выхода.
Теплообменник также отличается тем, что коллекторные части пластины теплоносителя большего давления перегорожены поперечной выштамповкой на раздающий коллектор и сборный коллектор, на длине участка противоточного движения теплоносителей коллекторные части отделены от теплопередающих частей продольными выштамповками, ограниченными по длине участком входа теплоносителя из раздающего коллектора в теплопередающие части и участком выхода теплоносителя в сборный коллектор.
Теплообменник также отличается тем, что на теплопередающих частях пластины выполнены гофры под углом наклона к сторонам пластины, отличным от 90 градусов, по периметру пластины выполнены отбортовки, закрывающие при сварке (пайке) от утечек теплоноситель меньшего давления, а по внешней стороне каждой из теплоотдающих частей выполнены дополнительные отбортовки, препятствующие при сварке (пайке) утечкам теплоносителя большего давления.
Технической задачей, которую решает предложенное устройство, является повышение эффективности теплообменника, упрощение обвязки теплообменника и уменьшение массы трубопроводов.
Техническим результатом, который обеспечивает решение поставленной задачи, является применение наиболее эффективной противоточной схемы движения теплоносителей и уменьшение числа коллекторов и трубопроводов путем использования одного коллектора для подвода и одного коллектора для отвода теплоносителя высокого давления к (от) двум(х) теплопередающим(х) частям(ей) теплообменника и по одному коллектору для подвода и отвода теплоносителя низкого давления, по крайней мере, к (от) двум(х) и более теплопередающим(х) частям(ей) теплообменника.
Технический результат обеспечивается тем, что противоточный пластинчатый теплообменник содержит теплообменные элементы, выполненные из попарно сложенных пластин, причем каждая пластина имеет, не крайней мере, две теплопередающие части и четыре коллекторные части для подвода и распределения теплоносителей, коллекторная часть теплоносителя большего давления располагается между теплопередающими частями, а коллекторная часть теплоносителя меньшего давления – по всей ширине пластины со стороны входа и выхода теплоносителя.
Технический результат также обеспечивается тем, что коллекторные части пластины теплоносителя большего давления перегорожены поперечной выштамповкой на раздающий коллектор и сборный коллектор, на длине участка противоточного движения теплоносителей коллекторные части отделены от теплопередающих частей продольными выштамповками, ограниченными по длине участком входа теплоносителя из раздающего коллектора в теплопередающие части и участком выхода теплоносителя в сборный коллектор.
Технический результат также обеспечивается тем, что на теплопередающих частях пластины выполнены гофры под углом наклона к сторонам пластины, отличным от 90 градусов, по периметру пластины выполнены отбортовки, закрывающие при сварке (пайке) от утечек теплоноситель меньшего давления, а по внешней стороне каждой из теплопередающих частей выполнены дополнительные отбортовки, препятствующие при сварке (пайке) утечкам теплоносителя большего давления.
На фиг.1 показан вид спереди на пластину теплообменника; на фиг.2 – сечения по АА, Б-Б, В-В, Г-Г, Д-Д, Е-Е, Ж-Ж фиг 1; на фиг; 3 – схема расположения гофр теплообменника при повороте соседней пластины на 180 градусов; на фиг.4, 5 – пластины с уменьшенным числом коллекторов при увеличенной площади теплопередающей поверхности.
Противоточный пластинчатый теплообменник содержит теплообменные элементы, выполненные из попарно сложенных пластин 1 (фиг.1, 2, 3). Каждая пластина 1 имеет, по крайней мере, две теплопередающие части 2, 3 и четыре коллекторные части 4, 5, 6, 7 для подвода и распределения теплоносителей. Коллекторная часть теплоносителя большего давления 4, 5 располагается между теплопередающими частями 2, 3, а коллекторная часть теплоносителя меньшего давления 6, 7 – по всей ширине пластины 1 со сторон его входа и выхода. Такое расположение позволяет объединить коллекторы теплоносителя меньшего давления двух и более теплопередающих поверхностей в один коллектор 6 входа и один коллектор 7 выхода и сократить число коллекторов и число трубопроводов (фиг.4, 5). Общее число коллекторов и, следовательно, трубопроводов рассчитывается по зависимости
NКОЛ(ТР)=NТПП+2·ZСТ-(ZСТ-1),
где NТПП – число теплопередающих поверхностей,
ZСТ – число столбцов расположения теплопередающих поверхностей (на фиг.4 расположен один столбец, а на фиг.5 – два).
Коллекторные части 4, 5 пластины 1 для теплоносителя большего давления разделены поперечной выштамповкой 8 на раздающий 4 и выборный 5 коллекторы (фиг.1, 2). На длине участка противоточного движения теплоносителей 9 коллекторные части 4, 5 теплоносителя большего давления отделены от теплопередающих частей 2, 3 продольными выштамповками 10, ограниченными по длине участками входа 11 теплоносителя из раздающего коллектора 4 в теплопередающие части 2, 3 и участками выхода 12 теплоносителя в сборный коллектор 5.
На теплопередающих частях 2, 3 пластины 1 выполнены гофры 13 под углом 14 наклона к сторонам пластины 1, отличным от 90 градусов, а по периметру пластины 1 – отбортовки 15, закрывающие при сварке (пайке) от утечек теплоноситель меньшего давления. По внешней стороне на каждой из теплопередающих частей 2, 3 выполнены дополнительные отбортовки 16, препятствующие при сварке (пайке) утечкам теплоносителя большего давления. Теплообменник работает следующим образом.
Теплоноситель низкого давления и более высокой температуры (например, газ после турбины газотурбинной установки) поступает через отверстия 17 в коллекторную часть подвода 6 теплоносителя низкого давления и распределяется по каналам, образованным попарно сложенными пластинами 1. Для увеличения поверхности теплообмена, жесткости пластины и изменения коэффициентов теплоотдачи и сопротивления пластины имеют гофры 13, расположенные под углом 14. Теплота через стенку пластины 1 передается теплоносителю высокого давления с меньшей температурой. Отбортовки 15, расположенные по периферии пластины 1, препятствуют утечке теплоносителя низкого давления в окружающую среду и направляют его в коллекторную часть отвода 7 теплоносителя низкого давления и затем через отверстия 18 в следующий элемент системы.
Теплоноситель высокого давления с низкой температурой (например, газ после компрессора) поступает в коллекторную часть подвода 4 теплоносителя высокого давления и затем через участок входа 11 распределяется по каналам обеих теплопередающих частей 2 и 3. Воспринимая тепло, переданное через стенку от теплоносителя с более высокой температурой, теплоноситель высокого давления поступает через участок выхода 12 в коллектор 5 и далее в трубопроводы (на фиг. не показаны). Коллекторные части 4 и 5 разделены перегородкой 8 между собой, а перегородкой 10 – от теплопередающих частей 2 и 3. Для предотвращения утечки в наружную среду пластина 1 имеет по контуру дополнительную отбортовку 16.
Формула изобретения
1. Противоточный пластинчатый теплообменник, содержащий теплообменные элементы, выполненные из попарно сложенных пластин, отличающийся тем, что каждая пластина имеет, по крайней мере, две теплопередающие и четыре коллекторные части для подвода и распределения теплоносителей, коллекторная часть теплоносителя большего давления располагается между теплопередающими частями, а коллекторная часть теплоносителя меньшего давления – по всей ширине пластины со сторон его входа и выхода.
2. Противоточный пластинчатый теплообменник по п.1, отличающийся тем, что коллекторные части пластины теплоносителя большего давления перегорожены поперечной выштамповкой на раздающий коллектор и сборный коллектор, на длине участка противоточного движения теплоносителей коллекторные части отделены от теплопередающих частей продольными выштамповками, ограниченными по длине участком входа теплоносителя из раздающего коллектора в теплопередающие части и участком выхода теплоносителя в сборный коллектор.
3. Противоточный пластинчатый теплообменник по любому из пп.1 и 2, отличающийся тем, что на теплопередающих частях пластины выполнены гофры под углом наклона к сторонам пластины, отличным от 90°, по периметру пластины выполнены отбортовки, закрывающие при сварке (пайке) от утечек теплоноситель меньшего давления, а по внешней стороне каждой теплопередающей части выполнены дополнительные отбортовки, препятствующие при сварке (пайке) утечкам теплоносителя большего давления.
РИСУНКИ
|
|