|
(21), (22) Заявка: 2007131680/06, 20.08.2007
(24) Дата начала отсчета срока действия патента:
20.08.2007
(46) Опубликовано: 27.02.2009
(56) Список документов, цитированных в отчете о поиске:
RU 2244147 С2, 10.01.2005. RU 2104405 С1, 10.02.1998. FR 2787514 А1, 23.06.2000. DE 2848114 А1, 17.05.1979. DE 3800064 А1, 13.07.1989.
Адрес для переписки:
614038, г.Пермь, ул. Ак. Веденеева, 28, ОАО НПО “Искра”
|
(72) Автор(ы):
Афанасьев Евгений Алексеевич (RU), Бурикова Рахиля Ибрагимовна (RU), Климов Юрий Федорович (RU)
(73) Патентообладатель(и):
Открытое акционерное общество Научно-производственное объединение “Искра” (RU)
|
(54) СПОСОБ ОПРЕДЕЛЕНИЯ ОКИСЛИТЕЛЬНОЙ СТОЙКОСТИ УГЛЕРОД-УГЛЕРОДНОГО КОМПОЗИЦИОННОГО МАТЕРИАЛА
(57) Реферат:
Изобретение относится к ракетной технике и может быть использовано при создании сопловых насадков из углерод-углеродного композиционного материала (УУКМ) к соплам жидкостных ракетных двигателей (ЖРД), работающих, в том числе, в условиях одновременного воздействия окислительной среды на обе поверхности насадка: высокотемпературной окислительной газовой среды на рабочую (внутреннюю) поверхность и воздуха – на наружную. Способ определения окислительной стойкости углерод-углеродного композиционного материала, в том числе с защитным покрытием, используемого в сопловом насадке жидкостного ракетного двигателя, включает изготовление образца, испытание образца воздействием высокотемпературной окислительной газовой средой, определение уноса композиционного материала и покрытия. При этом образец вырезают в виде пластины из технологического припуска насадка, а испытание проводят таким образом, что с одной стороны пластину обдувают вдоль ее поверхности высокотемпературным газовым потоком до достижения в ней температуры, реализуемой в штатных условиях работы насадка, а с другой стороны пластину обдувают окислительной средой, например воздухом или смесью кислорода с инертным газом в требуемой пропорции. Изобретение обеспечивает повышение достоверности определения окислительной стойкости УУКМ и защитных покрытий, используемых для изготовления сопловых насадков к соплам ЖРД. 4 ил.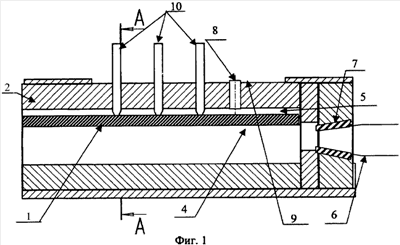
Изобретение относится к ракетной технике и может быть использовано при создании сопловых насадков из углерод-углеродного композиционного материала (УУКМ) к соплам жидкостных ракетных двигателей (ЖРД), работающих, в том числе, в условиях одновременного воздействия окислительной среды на обе поверхности насадка: высокотемпературной окислительной газовой среды на рабочую (внутреннюю) поверхность и воздуха – на наружную.
Известен способ определения окислительной стойкости УУКМ, предназначенного для изготовления сопловых насадков к соплам ЖРД, включающий изготовление трубчатого цилиндрического образца, испытание образца воздействием высокотемпературной окислительной газовой средой на внутреннюю поверхность образца (с помощью плазмотрона) с последующим измерением унесенных УУКМ (см. Материалы 26-й международной конференции «Композиционные материалы в промышленности» 29.05-02.06.2006, г.Ялта).
Недостаток известного способа заключается в том, что результаты испытания, полученные на трубчатом цилиндрическом образце, нельзя однозначно переносить на полноразмерный насадок, так как:
– с учетом особенностей композиционных материалов и специфики технологии их получения материал цилиндрического образца по структуре и свойствам будет отличаться от материала насадка,
– условия испытания не позволяют одновременно воздействовать окислительной средой на обе поверхности образца и, тем самым, в полной мере имитировать условия работы насадка.
Технической задачей изобретения является повышение достоверности определения окислительной стойкости УУКМ и защитных покрытий, используемых для изготовления сопловых насадков к соплам ЖРД.
Технический результат достигается тем, что в способе определения окислительной стойкости УУКМ, в том числе с защитным покрытием, используемого в сопловом насадке жидкостного ракетного двигателя, включающем изготовление образца, испытание образца воздействием высокотемпературной окислительной газовой средой, определение уноса композиционного материала и покрытия, образец вырезают в виде пластины из технологического припуска насадка, а испытание проводят таким образом, что с одной стороны пластину обдувают вдоль ее поверхности высокотемпературным газовым потоком до достижения в ней температуры, реализуемой в штатных условиях работы насадка, а с другой стороны пластину обдувают окислительной средой, например воздухом или смесью кислорода с инертным газом в требуемой пропорции.
На фиг.1 представлено приспособление для испытания материала на окислительную стойкость.
На фиг.2 представлен разрез по А-А на фиг.1.
На фиг.3 представлен график изменения температуры при испытании образца в приспособлении для испытания материала на окислительную стойкость.
На фиг.4 представлен график изменения температуры при испытании насадка в газодинамической трубе.
Способ осуществляется следующим образом. Из технологического припуска насадка вырезают образец 1 в виде пластины. Помещают образец 1 в камеру 2 приспособления для испытания материала на окислительную стойкость 3, изготовленного из огнеупорного материала, разделяя при этом камеру 2 на два канала (нижний 4 и верхний 5). В нижний канал 4 с помощью газовой горелки 6 подается поток горячего газа через сопло конусной формы 7. В верхнем канале 5 через отверстие 8, открытое в крышке 9 приспособления 3, к поверхности образца 1 дополнительно подается воздух или смесь кислорода с инертным газом в требуемой пропорции. Там же устанавливаются термообразователи 10 для контроля температуры поверхности образца 1. Таким образом, реализуются штатные условия работы насадка, при которых одну сторону обдувает высокотемпературный газовый поток, другую – окислительная среда. Определяют характер и величину уноса защитного покрытия и композиционного материала.
Пример.
Образец из УУКМ размером 25х4х80 мм был помещен в рабочую камеру, в которой на одну поверхность образца воздействовали газовым потоком, создаваемым с помощью газовой горелки с рабочей смесью, состоящей из кислорода (расход Q=7,5 л/мин, давление Р=5 атм) и ацетилена (Q=18,5 л/мин, Р=1 атм), а на другую поверхность осуществлялась подача воздуха за счет естественной тяги. Образец нагрели со скоростью 60°/мин до 1150°С и выдержали при температуре выше 1000°С в течение 600 сек. Сравнение графиков изменения температуры образца в приспособлении и изменения температуры полноразмерного насадка при испытании в газовой динамической трубе показало их идентичность (см. графики на фиг.3 и фиг.4). Характер уноса материала образца также близок к характеру уноса материала насадка.
Полученные результаты свидетельствуют о том, что предлагаемый способ с допустимой долей приближения моделирует условия воздействия газового потока на натурный насадок и позволяет с минимальными затратами проводить работы по выбору материалов и защитных покрытий для насадков сопловых блоков ЖРД.
Формула изобретения
Способ определения окислительной стойкости углерод-углеродного композиционного материала, в том числе с защитным покрытием, используемого в сопловом насадке жидкостного ракетного двигателя, включающий изготовление образца, испытание его воздействием высокотемпературной окислительной газовой средой, определение уноса композиционного материала и покрытия, отличающийся тем, что образец вырезают в виде пластины из технологического припуска насадка, а испытание проводят таким образом, что с одной стороны пластину обдувают вдоль ее поверхности высокотемпературным газовым потоком до достижения в ней температуры, реализуемой в штатных условиях работы насадка, а с другой стороны пластину обдувают окислительной средой, например воздухом или смесью кислорода с инертным газом в требуемой пропорции.
РИСУНКИ
|
|