(21), (22) Заявка: 2007105422/02, 13.02.2007
(24) Дата начала отсчета срока действия патента:
13.02.2007
(43) Дата публикации заявки: 20.08.2008
(46) Опубликовано: 27.02.2009
(56) Список документов, цитированных в отчете о поиске:
RU 2073749 C1, 20.02.1997. RU 2155305 C2, 27.08.2000. RU 2002857 C1, 15.11.1993. SU 1836496 A3, 23.08.1993. SU 1694703 A1, 30.11.1991. US 5961811 A, 05.10.1999. WO 2004081260 A1, 23.09.2004.
Адрес для переписки:
660111, г.Красноярск, ул. Пограничников, 37, стр.1, ИТЦ филиала ООО “РУС-Инжиниринг” в г. Красноярск, начальнику патентно-информационного отдела С.А. Пановой
|
(72) Автор(ы):
Вергазова Галина Дмитриевна (RU), Пингин Виталий Валерьевич (RU), Мурашкин Анатолий Иванович (RU)
(73) Патентообладатель(и):
Общество с ограниченной ответственностью “Русская инжиниринговая компания” (RU)
|
(54) СПОСОБ ПОЛУЧЕНИЯ ХОЛОДНОНАБИВНОЙ ПОДОВОЙ МАССЫ
(57) Реферат:
Изобретение относится к области цветной металлургии, в частности к производству углеродных материалов, применяемых для футеровки подины электролизера. Способ включает приготовление углеродной шихты, смешивание углеродной шихты со специальной добавкой, пластификатором и связующим. Углеродную шихту готовят непрерывного гранулометрического состава с максимальным размером углеродного зерна не более 8 мм. Содержание фракций определяют внутри области, ограниченной кривыми, построенными по граничным значениям содержания фракций, мм/мас.%: 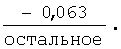
Определены оптимальные параметры приготовления и смешивания углеродной шихты. В качестве углеродной шихты используют смесь электрокальцинированного антрацита и искусственного графита. Обеспечивается получение холоднонабивной подовой массы с повышенным объемным расширением при обжиге, пониженной пористостью и меньшим максимальным размером пор. 3 з.п. ф-лы, 3 ил., 2 табл.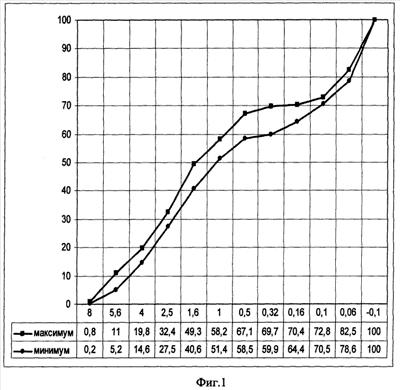
Изобретение относится к области цветной металлургии, в частности к производству углеродных материалов, применяемых для футеровки подины электролизера.
Углеродная футеровка электролизеров формируется из подовых и боковых углеродных блоков, соединенных межблочными швами с подовой массой. Подовая масса используется для заполнения пространства (швов) между подовыми блоками в подине электролизера, а также для соединения бортовых блоков с подовыми по периферии ванны. Основные проблемы в работе электролизера возникают из-за протеков электролита и металла через межблочные или периферийные швы. Для их исключения необходима холоднонабивная подовая масса, расширяющаяся при обжиге с образованием мелкокопористой структуры и прочно соединяющая подовые блоки между собой, а также подовые блоки с боковыми блоками.
Как правило, способ приготовления холоднонабивной подовой массы включает основные операции приготовления углеродной шихты и смешивания ее со связующим и специальными добавками (или без них) в разных температурных условиях.
Известен способ приготовления холоднонабивной подовой массы для алюминиевых электролизеров (патент РФ №2128731, кл. С25С 3/08; С04В 35/52, 1999), включающий приготовление углеродсодержащей шихты, смешивание ее со связующим и органической пластифицирующей добавкой. Связующим является среднетемпературный пек, нагретый до 130-170°С, который вводят в предварительно нагретую до 130-140°С углеродсодержащую шихту наполнителя. В качестве органической пластифицирующей добавки используют высокомолекулярные продукты фракционирования каменноугольной смолы или нефтяных остатков, нагретые до температуры 30-80°С.
Массовая доля компонентов в составе массы:
– органическая пластифицирующая добавка 5-7%;
– связующее 13-15%;
– углеродсодержащая шихта (углеродсодержащие отходы катодов и анодов, хвосты флотации угольной пены, природный графит) – остальное.
Время смешивания органической пластифицирующей добавки составляет (0,5-0,75) от времени смешивания углеродсодержащей шихты со связующим.
Известный способ приготовления холоднонабивной подовой массы снижает пористость обожженной массы с 33-34% до 27-29%.
Основным недостатком известного способа является высокая пористость подовой массы после обжига, что не исключает проблему пропитки швов электролитом и проникновения металла.
Известен способ изготовления массы для алюминиевых электролизеров (патент РФ №2073749, кл. 25С 3/06, 1997), включающий смешивание коксовой шихты со связующим и тугоплавким компонентом. Дополнительно в состав массы вводят ингибитор окисления – глиноземсодержащее вещество, которое предварительно подают в связующее перед смешиванием его с коксовой шихтой.
Известный способ приводит к повышению стойкости к окислению и снижению пористости в 3-4 раза при условии добавления в подовую массу 20-21% глиноземсодержащего вещества.
Способ имеет ряд недостатков:
– в составе подовой массы допускается содержание глиноземсодержащего вещества до 22%, что значительно снижает набоечные свойства массы и требует дополнительного содержания связующего в массе – до 30%, вместо типичных 12-15% для холоднонабивных подовых масс, что увеличивает выделение летучих веществ при обжиге подины в 2 раза;
– присутствие в составе массы мелкодисперсного глиноземсодержащего вещества значительно повышает прочность подовой массы после обжига и значительно снижает пластичность массы, что отражается на показателе механической прочности массы при изгибе;
– введение глиноземсодержащего вещества в расплавленное связующее значительно затрудняет его смачивание связующим, что исключает получение в дальнейшем однородной массы, так как при указанном соотношении соответственно 18-22% глиноземсодержащего вещества и 15-30% связующего на 100% массы происходит «сухое» смешивание компонентов при явном недостатке связующего.
– глиноземсодержащее вещество является сырьем для получения алюминия и его наличие в подовой массе может в присутствии электролита привести к восстановлению алюминия, с последующим образованием карбидов алюминия, которые, в свою очередь, разрушают футеровку.
Наиболее близким по технической сущности и достигаемому результату является техническое решение по патенту РФ №2155305 (С 25С 3/08; С04 В 35/52, 2000), включающее приготовление углеродной шихты наполнителя, смешивание ее со специальной добавкой, пластификатором и жидким углеродным связующим. Массовая доля компонентов в подовой массе составляет, мас.%: углеродная шихта 74.0 – 89,0; специальная добавка 0,6-6,6; пластификатор 0,4-3,4;. связующее 10,0 -16,0.
В качестве углеродного наполнителя используют термоантрацит или электрокальцинированный антрацит с размером зерна от 0 до 15 мм заданного гранулометрического состава, мм/мас.%:

В качестве связующего используют композицию среднетемпературного каменноугольного пека марки Б и поглотительного масла со следующими показателями:
динамическая вязкость при 50°С |
50 сП |
выход коксового остатка |
38% |
В качестве пластификатора – многоатомный спирт жирного ряда – диэтиленгликоль.
В качестве специальной добавки используют борную кислоту, буру, оксид бора, карбид бора.
Время приготовления холоднонабивной подовой массы:
Смешивание углеродной шихты со специальной добавкой – 5 мин.
Смешивание смеси с пластификатором – 5 мин.
Смешивание смеси со связующим – 20 мин.
Состав холоднонабивной подовой массы и известный способ ее получения имеют ряд недостатков, что не гарантирует высокое качество межблочных швов:
– по составу холоднонабивной подовой массы: свойства массы зависят от гранулометрического состава и свойств наполнителя. Применение грубодисперсного углеродного наполнителя с максимальным размером зерна 15 мм повышает макропористость холоднонабивной подовой массы, снижает уплотняемость необожженной массы и объемное расширение массы при обжиге. В составе холоднонабивной подовой массы по прототипу используется только один вид наполнителя – термоантрацит с разной степенью термической обработки. Широкое применение в подине электролизеров графитовых и графитированных подовых блоков требует разработки новых составов подовых масс с повышенным содержанием графитовой составляющей для соединения указанных типов блоков;
– по способу приготовления холоднонабивной подовой массы: время смешивания компонентов холоднонабивной подовой массы – важный показатель, так как длительный процесс приводит к переизмельчению частиц наполнителя, особенно электрокальцинированного антрацита, повышению его внешней удельной поверхности и перераспределению связующего из межзернового пространства в поры, что приводит к дополнительной усадке холоднонабивной подовой массы при обжиге. В прототипе приводится только время смешивания в лабораторных условиях и отсутствует продолжительность смешивания компонентов в промышленных условиях.
Температура смешивания компонентов в прототипе дается также для лабораторных условий, т.е. комнатная, откуда не следует значение температуры для промышленного способа получения холоднонабивной подовой массы.
Задачей изобретения является повышение качества межблочных швов из холоднонабивной подовой массы за счет обеспечения ее мелкопористой структуры при высоком расширении при обжиге посредством варьирования таких параметров, как размер зерна наполнителя, содержание пылевой фракции, применения непрерывного гранулометрического состава шихты наполнителя, изменения продолжительности операций и температурных режимов получения массы.
Технический результат заключается в способе получения холоднонабивной подовой массы, обладающей повышенным объемным расширением при обжиге, пониженной пористостью и меньшим максимальным размером пор.
Основная роль межблочных швов – соединить подовые блоки и предотвратить проникновение электролита и расплава алюминия под подовые блоки.
При разработке способа получения подовой массы учитывалось условие, что подовая масса при обжиге должна заполнять межблочные швы, соответственно подвергаться необратимому расширению.
С точки зрения химического состава, который нужно получить, ключевым вопросом является плотная мелкопористая структура, характеризуемая преобладающим размером пор и кривой распределения пор по размеру. Вопрос решается посредством варьирования таких параметров, как размер фракции углеродной шихты, содержание пылевой фракции, последовательность и продолжительность операций и температурные условия приготовления массы. Для определения распределения пор по размеру применяется ртутная порометрия.
Известно, что чем выше общая пористость, чем больше размер пор в обожженной холоднонабивной подовой массе, тем быстрее проникает электролит, смачивает поверхность и активизирует взаимодействие с алюминием с образованием карбида алюминия, снижающего прочность материала и приводящего к раскрытию швов. Образование и последующее разложение карбида алюминия относится к электрохимическим процессам, происходящим внутри и на поверхности углеродных межблочных швов. Как только электролит проникает в поры, появляется возможность образования карбида алюминия. При одинаковой открытой пористости разные углеродные материалы могут иметь большую разницу в структуре материала и распределении пор по размерам.
Как правило, после 96 часов электролиза швы подовой массы и подовые блоки в ванне практически полностью пропитываются электролитом. В порах размером более 100 мкм формирование карбида алюминия проявляется в большей степени, чем в порах размером менее 10 мкм. Значительно медленнее идет процесс пропитки массы с размером пор менее 5 мкм.
В случае макропористого материала наблюдается усиление проникновения электролита в шов подовой массы, что увеличивает возможность образования карбида алюминия в порах и разъединения частиц. Более того, в подовой массе с высокой пористостью прочность связи между частицами будет низкая из-за пор, снижающих площадь контакта между частицами. Снижение площади контакта ведет к ослаблению структуры и способствует износу посредством разъединения частиц /P.Rafiei,F.Hiltmann, М. Hylan, B.James & B.Welch, Electrolytic degradation within cathode materials. Light Metals 2001, 2001, p.747-752/.
Указанный технический результат достигается тем, что в способе получения холоднонабивной подовой массы для алюминиевых электролизеров, включающем приготовление углеродной шихты, смешивание углеродной шихты с борной кислотой в качестве добавки, пластификатором и связующим, согласно заявляемому изобретению углеродную шихту готовят непрерывного гранулометрического состава с максимальным размером углеродного зерна не более 8 мм, при этом содержание фракций определяют внутри области, ограниченной кривыми, построенными по граничным значениям содержания фракций, мм/мас.%:
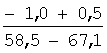
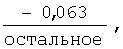
температуру углеродной шихты поддерживают 55±10°С, температуру добавки – 30±10°С, температуру пластификатора – 45±10°С, температуру связующего – 65±10°С, а температуру приготовления холоднонабивной подовой массы – не более 80°С, причем общее время приготовления подовой массы составляет не более 45 минут, время приготовления углеродной шихты составляет не более 0,22; время смешивания углеродной шихты с добавкой и пластификатором – не более 0,33; время смешивания со связующим – не более 0,45 от общего времени приготовления подовой массы.
Способ дополняют частные отличительные признаки, направленные также на решение поставленной задачи:
углеродную шихту готовят с внешней удельной поверхностью 120-170 м2/кг;
в качестве углеродной шихты используют смесь
электрокальцинированного антрацита и искусственного графита при
следующем содержании компонентов, мас.%:
электрокальцинированный антрацит |
70-85 |
искусственный графит |
15-30 |
– искусственный графит вводят в углеродную шихту в виде фракции с размером зерна (-4+0,5) мм.
Заявляемый способ отличается от прототипа использованием умельченного непрерывного гранулометрического состава углеродной шихты, определяемого заданной областью и абсолютными значениями внешней удельной поверхности углеродной шихты, вовлечением в состав углеродной шихты искусственного графита заданной фракции и количества, а также временными и температурными режимами смешивания углеродной шихты с добавкой, пластификатором и связующим.
Таким образом, анализ прототипа, как наиболее близкого по совокупности существенных признаков аналога, позволяет выявить новую совокупность существенных по отношению к техническому результату отличительных признаков, изложенных в формуле изобретения. Следовательно, заявленное изобретение соответствует условию «новизна».
Для проверки соответствия заявленного изобретения условию «изобретательский уровень» заявитель провел дополнительный поиск известных решений, чтобы выявить признаки, совпадающие с отличительными от прототипа признаками.
Результаты поиска показали, что заявленное изобретение не вытекает явным образом из известного уровня техники, поскольку из уровня техники определенного заявителем не выявлен аналог, характеризующийся признаками, тождественными всей совокупности отличительных признаков заявленного способа, направленной на достижение технического результата. Следовательно, заявляемое изобретение соответствует условию «изобретательский уровень».
Способ поясняется фигурами 1-3, где на фиг.1 показана заявляемая область непрерывного гранулометрического состава, на фиг.2 показано распределение пор по размерам в холоднонабивной подовой массе по заявляемому способу с преобладающим размером пор 2,0-5,0 мкм, на фиг.3 показано распределение пор по размерам в холоднонабивной подовой массе по прототипу с преобладающим размером пор 90 мкм.
Предлагаемый способ реализуется следующим образом.
В формуле изобретения заявлены абсолютные значения граничных значений содержания фракций, необходимых для построения области непрерывного гранулометрического состава углеродной шихты, а именно, мм/мас.%:
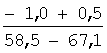
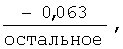
По представленным абсолютным значениям строится графическая зависимость содержания фракций от размера фракций, представленная на фиг.1. Область, ограниченная двумя граничными кривыми, является заявляемой областью непрерывного гранулометрического состава и охватывает весь диапазон возможных сочетаний содержания фракций, обеспечивающих положительный эффект. Широкий интервал значений гарантирует достижение положительного эффекта при соответствии внешней удельной поверхности шихты 120-170 м2/кг;
Использование в предлагаемом способе в качестве углеродной шихты электрокальцинированного антрацита или смеси электрокальцинированного антрацита и искусственного графита непрерывного гранулометрического состава с максимальным размером зерна 8 мм позволяет изменить упаковку частиц холоднонабивной подовой массы таким образом, что снижается пористость холоднонабивной подовой массы в обожженном состоянии, а также размер пор, с преобладанием пор размером 2-2,5 мкм вместо 90 мкм в холоднонабивной подовой массе по прототипу.
Это происходит потому, что частицы крупного размера, из которых состоит холоднонабивная подовая масса по прототипу, не способны эффективно присоединяться друг к другу при уплотнении. Большой размер пор указывает на то, что количества пылевой фракции и средних частиц недостаточно для заполнения полостей большего размера, образованных частицами большего размера, что соответствует композиции состава.
Использование шихты непрерывного гранулометрического состава по предлагаемому способу приводит к получению микропористой структуры холоднонабивной подовой массы в уплотненном состоянии. Частицы небольшого размера, из которых состоит холоднонабивная подовая масса, способны эффективно присоединяться друг к другу с образованием меньших полостей. Большая часть этих полостей затем может быть заполнена пылевой фракцией и мелкими частицами.
Кривые распределения пор по размерам, полученных методом ртутной порометрии по МВИ «Кайзер» на ртутном порозиметре «Autopore 9220» для двух холоднонабивных подовых масс, различаются разбросом в распределении пор и преобладающими размерами пор. Большинство размеров пор, обнаруженных в образцах холоднонабивной подовой массы по предлагаемому способу, соответствует диапазону 2-5 мкм, о чем свидетельствуют кривая распределения пор по размерам (по высоте и площади пика) (фиг.2). Холоднонабивная подовая масса по прототипу (фиг.3) при одинаковой открытой пористости с холоднонабивной подовой массой по предлагаемому способу имеет больший диапазон разброса пор по размерам при преобладающем размере пор 60-90 мкм.
Пределы технологических параметров предлагаемого способа обосновываются следующим:
По п.1 формулы. Касается приготовления углеродной шихты непрерывного гранулометрического состава с максимальным размером зерна наполнителя не более 8 мм определяемой областью, ограниченной кривыми, построенными по граничным значениям содержания фракций, мм/мас.%:
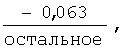
Экспериментальная область заявленного непрерывного гранулометрического состава углеродной шихты, построенная по приведенным выше значениям, представлена на фиг.1. В таблице 1 приведены примеры холоднонабивных подовых масс по предлагаемому способу и прототипу, в том числе представлены гранулометрические составы углеродной шихты, температурные и временные режимы получения холоднонабивной подовой массы. Как видно из приведенных показателей качества холоднонабивной подовой массы на основе углеродной шихты заявленного предела гранулометрического состава, соответствующего содержанию фракций и области между кривыми на фигуре 1, холоднонабивная подовая масса по примерам 1-5, табл.2 удовлетворяет заявляемым требованиям. Выход за пределы заявленного гранулометрического состава углеродной шихты (примеры 6-7) приводит к повышенной усадке и увеличению пористости холоднонабивной подовой массы после обжига. Повышение пористости всегда приводит к снижению механической прочности обожженной холоднонабивной подовой массы. Превышение требований по пористости при запредельных значениях гранулометрического состава шихты объясняется тем, что наблюдается нарушение плотности упаковки частиц при запредельных значениях содержания отдельных фракций. При избытке крупных фракций и недостатке мелких увеличивается как общая, так и открытая пористость при средних размерах пор более 20 мкм (пример 8).
При избытке мелких фракций повышается упаковка частиц, что при недостатке крупных частиц приводит к усадке массы при обжиге, повышению плотности и механической прочности. Выход за верхние заявляемые пределы по содержанию мелких фракций, особенно менее 0,1 мм, приводит к повышению внешней удельной поверхности шихты и недостатку пластификатора и связующего. Для получения холоднонабивной подовой массы с требуемым уровнем пластичности требуется повышенное запредельное количество пластификатора и связующего, необходимого для получения уплотняющейся холоднонабивной подовой массы. При заявленных значениях содержания пластификатора и связующего значительно снижается уплотняемость (формуемость) холоднонабивной подовой массы, что приводит к большой усадке при обжиге и снижению механической прочности холоднонабивной подовой массы (пример 7). Качество уплотнения такой холоднонабивной подовой массы при набойке швов значительно снижается.
Касается температурных режимов приготовления холоднонабивной подовой массы. Известен прием предварительного подогрева углеродной шихты перед смешиванием со связующим. (Фиалков А.С.Углеграфитовые материалы М., Энергия, 1979).
В предлагаемом решении авторы предлагают свои температурные режимы приготовления холоднонабивной подовой массы, основанные на исследовании адсорбционной способности электрокальцинированного антрацита и искусственного графита к связующему и пластификатору, а также в соответствии с требованиями к уплотняемости холоднонабивной подовой массы, зависящей от вязкости связующего, которая, в свою очередь, обеспечивается температурным интервалом.
По предлагаемому способу температура предварительного нагрева углеродной шихты составляет 55±10°С, что обеспечивает активизацию поверхностной активности углерода, достаточную для взаимодействия с добавками, пластификатором и связующим.
Заявляемая температура добавки 30±10°С.
Заявляемая температура пластификатора 45±10°С.
Заявляемая температура связующего 65±10°С.
Заявляемая температура приготовления массы не более 80°С.
Выход за верхние заявляемые температурные пределы приводит к излишней пропитке углеродной шихты связующим и снижению спекаемости подовой массы при обжиге, перегрев пластификатора и связующего приводит к повышению выделения летучих веществ, что приводит к повышению пористости и снижению прочности (пример 14).
Выход за нижние пределы по температуре компонентов приводит к недостаточному смачиванию углеродной шихты пластификатором и связующим и их неравномерному распределению по поверхности углеродной шихты, что также снижает кажущуюся плотность обожженной холоднонабивной подовой массы и ее прочность, а также повышает пористость (пример 13).
Касается временных режимов приготовления холоднонабивной подовой массы. Временные режимы получены путем экспериментальных испытаний и результатов и проверки однородности состава массы по всему объему смесителя. Процесс получения холоднонабивной подовой массы осуществляется в одном смесителе, начиная с перемешивания углеродной шихты до выгрузки готовой холоднонабивной подовой массы. Соответственно этапы равномерного распределения компонентов, пропитки углеродных частиц связующим и пластификация межчастичных прослоек должны быть разделены во времени.
Авторами предлагаются временные режимы, отработанные на экспериментальных замесах с контролем способности к уплотнению в межблочных швах.
Заявляемые временные режимы приготовления холоднонабивной подовой массы относятся к получению холоднонабивной подовой массы в смесителе периодического действия: время приготовления углеродной шихты составляет не более 0,22 от общего времени приготовления холоднонабивной подовой массы; время смешивания углеродной шихты с добавкой и пластификатором составляет не более 0,33 от общего времени приготовления подовой массы; время смешивания со связующим составляет не более 0,45 от общего времени приготовления холоднонабивной подовой массы, при общем времени приготовления холоднонабивной подовой массы – не более 45 минут.Выход за заявляемые пределы по временным режимам не обеспечивает достижение поставленной цели (примеры 15,16).
По п.2 формулы. Касается внешней удельной поверхности углеродной шихты. Как следует из таблицы 1, холоднонабивные подовые массы на основе углеродной шихты, соответствующей заявленным требованиям к гранулометрическому составу и величине внешней удельной поверхности шихты, удовлетворяют требованиям к качеству подовой массы.
Выход за заявляемые пределы по минимальной величине внешней удельной поверхности шихты приводит к повышению пористости холоднонабивной подовой массы, пример 6, табл.2.
Выход за заявляемые пределы по величине максимальной внешней удельной поверхности шихты приводит к недостатку пластификатора и связующего в холоднонабивной подовой массе, что снижает уплотняемость холоднонабивной подовой массы при набойке в швах и снижает механическую прочность холоднонабивной подовой массы после обжига, пример 7, табл.2.
По п.3 формулы. Касается содержания искусственного графита в углеродной шихте. Авторы предлагаемого изобретения предлагают использовать в составе углеродной шихты до 30% искусственного графита со следующими показателями:
удельное электросопротивление, мкОм.м |
не более 100 |
истинная плотность, г/см3 |
не менее 2,1 |
содержание золы, % |
не более 0,2 |
содержание влаги, % |
не более 0,1 |
В табл.1 приведены составы холоднонабивных подовых масс (примеры 9-12) с содержанием 15, 30, более 30 и менее 15% искусственного графита в углеродной шихте. Оптимальные показатели качества получены при содержании искусственного графита в шихте 30%, пример 10, табл.2. Введение 30% искусственного графита в состав углеродной шихты холоднонабивной подовой массы обеспечивает требуемый уровень величины удельного элетросопротивления и механической прочности при сжатии с образованием мелкопористого материала. Выход за заявляемые пределы по минимальному содержанию графита приводит к его перераспределению между частицами электрокальцинированного антрацита и нивелированию его индивидуальных свойств. Свойства холоднонабивной подовой массы в этом случае не отличаются от масс на углеродной шихте с содержанием 100% электрокальцинированного антрацита (пример 12, табл.2). Выход за максимальное содержание искусственного графита (пример 11, табл.2) приводит к снижению механической прочности подовой массы и снижению остаточного объемного расширения после обжига при увеличении преобладающего размера пор до 10 мкм.
По п.4 формулы. Касается фракционного состава искусственного графита. Цель введения искусственного графита в углеродную шихту – повышение электропроводности холоднонабивной подовой массы. Проведенные авторами исследования показали, что достаточное повышение электропроводности холоднонабивной подовой массы достигается при увеличении содержания искусственного графита в шихте до 30%, а при более высоком содержании графита наблюдается снижение прочностных свойств. С учетом требований к формированию мелкопористого обожженного материала были испытаны разные составы углеродной шихты для холоднонабивной подовой массы с применением крупных, средних и мелких (тонкого помола) фракций искусственного графита с анализом поровой структуры обожженных масс.Оптимальные результаты по поровой структуре получены в случае использования искусственного графита в виде фракции (-4+0,5) мм.
В случае применения искусственного графита в виде тонкого помола – фракции (-0,5+0)мм совместно с электрокальцинированным антрацитом приводит к образованию трещинообразных пор в обожженной холоднонабивной подовой массе из-за разницы упругих свойств фракции менее 0,063 мм антрацита и графита.
Крупная фракция углеродной шихты при получении холоднонабивной подовой массы загружается в смеситель в первую очередь и находится в смесителе самое длительное время. Поэтому применение графита в виде фракции (-8+4)мм приводит к получению случайного гранулометрического состава углеродной шихты из-за дополнительного измельчения крупного графита при совместном смешивании с абразивным электрокальцинированным антрацитом.
Примеры конкретного выполнения примеров:
Пример 1. Для приготовления холоднонабивной подовой массы используют
электрокальцинированный антрацит с зерном |
размером (-8+0)мм со следующими характеристиками: |
удельное электросопротивление, мкОм.м |
560 |
истинная плотность, г/см3 |
1,88 |
содержание золы, % |
4,8 |
содержание влаги, % |
0,4 |
Готовят углеродную шихту, состоящую из 100% электрокальцинированного антрацита(ЭКА) следующего гранулометрического состава, мм/мас.%:


Удельная поверхность шихты составляет 150 м /кг.
Содержание компонентов в холоднонабивной подовой массе, мас.%:
углеродная шихта (100% ЭКА) |
– 83,0 |
добавка (борная кислота) |
1,5 |
пластификатор (диэтиленгликоль) |
– 1,5 |
связующее |
– 14,0 |
Для приготовления холоднонабивной подовой массы используют связующее со следующими характеристиками:
динамическая вязкость при 50°С |
475 сП |
выход коксового остатка |
36% |
Приготовление холоднонабивной подовой массы ведут следующим образом: в смеситель периодического действия из дозатора загружают крупную, среднюю и пылевую часть шихты электрокальцинированного антрацита. В момент окончания загрузки включается перемешивание шихты с одновременным обогревом смесителя. Перемешивание и подогрев шихты до 55°С осуществляется в течение 10 минут. В подготовленную шихту загружают добавку (борную кислоту) с температурой 30°С, которую перемешивают с углеродной шихтой около 5 минут. Затем вводят пластификатор с температурой 45°С. Общее время смешивания углеродной шихты с добавкой и пластификатором составляет 15 минут. На подготовленную смесь углеродной шихты с добавками загружают связующее с температурой 65°С и перемешивают содержимое в смесителе 20 минут. После окончания смешивания температура выгружаемой холоднонабивной подовой массы 75°С. Общее время приготовления холоднонабивной подовой массы составляет 45 минут.
Испытания холоднонабивной подовой массы проводят в соответствии с требованиями ТУ 1914-071-05785218-99, в соответствии с которыми прессуют образцы из холоднонабивной подовой массы под давлением (19,6±2) МПа при температуре 25°С в течение 120 с. Спрессованные образцы обмеряют для последующего расчета объемного расширения после обжига.
Кажущуюся плотность определяют на образцах диаметром 60 мм, высотой 60 мм после обжига до 1000°С в углеродной засыпке со скоростью обжига 100°С/час и выдержкой при конечной температуре в течение 3 часов. Обожженные образцы взвешивают, обмеряют и рассчитывают кажущуюся плотность и объемное расширение.
Обожженные образцы испытывают на удельное электросопротивление по ГОСТ 23776, разд.2 и механическую прочность при сжатии по ГОСТ 23775.
Открытую пористость определяют по ГОСТ 2409-95, общую пористость в соответствии с ТУ 1914-071-05785218-99 по относительной разнице истинной и кажущейся плотностей обожженной массы.
Кривые распределения пор по размерам получают методом ртутной порометрии по методике « Kaiser» на ртутном порозиметре «Autopore 9220».
Пример 17 (по прототипу)
Для приготовления холоднонабивной подовой массы используют электрокальцинированный антрацит с зерном размером (-15+0)мм.
Готовят углеродную шихту из электрокальцинированного антрацита следующего гранулометрического состава, мм/мас.%:

Удельная поверхность шихты составляет 120 м2/кг.
Содержание компонентов в холоднонабивной подовой массе, мас.%:
углеродная шихта (100% ЭКА) |
84,0 |
добавка (борная кислота) |
1,5 |
пластификатор (диэтиленгликоль) |
1,5 |
связующее |
13,0 |
Для приготовления массы используют связующее со следующими характеристиками:
динамическая вязкость при 50°С |
350 сП |
выход коксового остатка |
38% |
Приготовление холоднонабивной подовой массы ведут следующим образом: в смеситель емкостью 10 л без обогрева загружают углеродную шихту, вводят добавку комнатной температуры, перемешивают в течение 5 минут, заливают пластификатор и дополнительно перемешивают еще 5 минут. Связующее с температурой 50°С заливают в последнюю очередь и перемешивают в течение 20 минут. Общее время приготовления холоднонабивной подовой массы составляет 30 минут.
Время приготовления холоднонабивной подовой массы:
Смешивание углеродной шихты с добавкой – 5 мин.
Смешивание с пластификатором – 5 мин.
Смешивание со связующим – 20 мин.
Испытание холоднонабивной подовой массы ведет в соответствии с требованиями ТУ 1914-071-05785218-99, в соответствии с которыми прессуют образцы из массы с давлением (19,6±2)МПа при температуре 25°С в течение 120 с.
Спрессованные образцы обмеряют для последующего расчета объемного расширения после обжига.
Кажущуюся плотность определяют на образцах диаметром 60 мм, высотой 60 мм после обжига до 1000°С в углеродной засыпке со скоростью обжига 100°С/час и выдержкой при конечной температуре в течение 3 часов. Обожженные образцы взвешивают, обмеряют и рассчитывают кажущуюся плотность и объемное расширение.
Обожженные образцы испытывают на удельное электросопротивление по ГОСТ 23776, разд.2 и механическую прочность при сжатии по ГОСТ 23775.
Открытую пористость определяют по ГОСТ 2409-95, общую пористость в соответствии с ТУ 1914-071-05785218-99 по относительной разнице истинной и кажущейся плотностей обожженной массы.
Кривые распределения пор по размерам получают методом ртутной порометрии по методике « Kaiser» на ртутном порозиметре «Autopore 9220».
В таблице 2 представлены результаты испытания холоднонабивных подовых масс, приготовленных по 17 примерам. Полученные холоднонабивные подовые массы в соответствии с заявляемым способом по примерам 1-5, 9,10 позволяют получить мелкопористый обожженный материал с высокими эксплуатационными свойствами.
Выход за заявляемые пределы по гранулометрическому составу и удельной поверхности углеродной шихты (примеры 6-8), по содержанию графита в углеродной шихте (примеры 11,12), а также температурным и временным режимам (примеры 13-16) не обеспечивает достижение технического результата.
Изобретение применимо при изготовлении холоднонабивной подовой массы для заполнения межблочных и периферийных швов алюминиевых электролизеров и позволяет повысить эксплуатационную стойкость углеродных подин при эксплуатации.
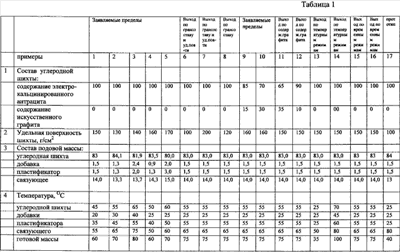 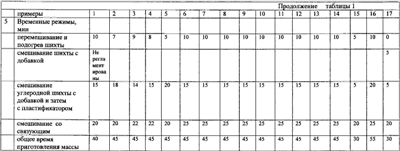
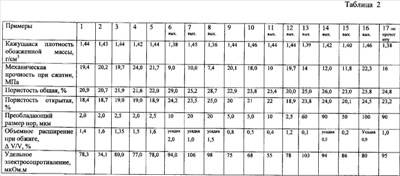
Формула изобретения
1. Способ получения холоднонабивной подовой массы для алюминиевых электролизеров, включающий приготовление углеродной шихты, смешивание углеродной шихты с борной кислотой в качестве добавки, пластификатором, и связующим, отличающийся тем, что углеродную шихту готовят непрерывного гранулометрического состава с максимальным размером углеродного зерна не более 8 мм, при этом содержание фракций определяют внутри области на фиг.1,
ограниченной кривыми, построенными по граничным значениям содержания фракций, мм/мас.%: 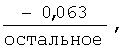
температуру углеродной шихты поддерживают 55±10°С, температуру добавки
-30±10°С, температуру пластификатора -45+10°С, температуру связующего-
65±10°С, а температуру приготовления холоднонабивной подовой массы – не
более 80°С, причем общее время приготовления подовой массы составляет не
более 45 мин, время приготовления углеродной шихты составляет не более
0,22, время смешивания углеродной шихты с добавкой и пластификатором – не
более 0,33, время смешивания со связующим – не более 0,45 от общего времени приготовления подовой массы.
2. Способ по п.1, отличающийся тем, что углеродную шихту готовят с внешней удельной поверхностью 120-170 м2/кг.
3. Способ по п.1, отличающийся тем, что в качестве углеродной шихты используют смесь электрокальцинированного антрацита и искусственного графита при следующем содержании компонентов, мас.%:
электрокальцинированный антрацит |
70-85 |
искусственный графит |
15-30 |
4. Способ по п.3, отличающийся тем, что искусственный графит вводят в углеродную шихту в виде фракции с размером зерна (-4,0+0,5) мм.
РИСУНКИ
|