|
(21), (22) Заявка: 2007119102/02, 23.05.2007
(24) Дата начала отсчета срока действия патента:
23.05.2007
(46) Опубликовано: 27.02.2009
(56) Список документов, цитированных в отчете о поиске:
ЛАХТИН Ю.М. и др. Химико-термическая обработка металлов. – М.: Металлургия, 1985, с.251-252. RU 2222637 С1, 27.01.2004. SU 1617051 А1, 30.12.1990. SU 263358 А, 04.11.1970. JP 60-116762 А, 24.06.1985. JP 10-168556 А, 23.06.1998.
Адрес для переписки:
105118, Москва, пр-кт Буденного, 16, ФГУП “ММПП “САЛЮТ”, Правовое управление, С.Е. Кирееву
|
(72) Автор(ы):
Поклад Валерий Александрович (RU), Оспенникова Ольга Геннадиевна (RU), Шкретов Юрий Павлович (RU), Бобырь Александр Владимирович (RU), Лукина Валентина Васильевна (RU), Абраимов Николай Васильевич (RU)
(73) Патентообладатель(и):
Федеральное государственное унитарное предприятие “Московское машиностроительное производственное предприятие “САЛЮТ” (ФГУП “ММПП “САЛЮТ”) (RU)
|
(54) СПОСОБ НАНЕСЕНИЯ ПОКРЫТИЙ НА ЖАРОПРОЧНЫЕ СПЛАВЫ
(57) Реферат:
Изобретение относится к области химико-термической обработки, а именно к способам нанесения покрытий на жаропрочные сплавы на основе никеля и может использоваться для защиты деталей от солевой коррозии. Способ включает последовательное диффузионное насыщение сплава кобальтом и алюминием в циркулирующей среде, содержащей галогениды. Диффузионное насыщение проводят при температуре >900°С, но не выше температуры закалки сплава на основе никеля. При этом насыщение кобальтом проводят в среде, содержащей компоненты при следующем соотношении, мас.%: галогенид аммония – 0,2-15, источник кобальта – 85-99,8. В качестве галогенида аммония используют йодистый аммоний или хлористый аммоний, или бромистый аммоний, или фтористый аммоний, или их смесь. Технический результат – повышение качества и долговечности покрытия. 1 з.п. ф-лы, 2 ил.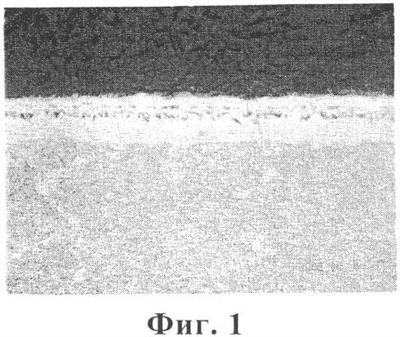
Изобретение относится к металлургии, в частности к химико-термической обработке, и может использоваться для защиты деталей от солевой коррозии.
Известен способ получения кобальтовых диффузионных покрытий путем использования оксидов кобальта СоО, Со2O3, Со3O4 в смеси с хлористым аммонием NH4Cl. Покрытие получали путем нагрева стали 3 на воздухе в указанном составе смеси при температуре 1100°С. За 40-60 минут путем восстановления кобальта водородом, выделяющимся при диссоциации соли NH4Cl, получали слой толщиной 30-50 мкм. [Горбунов Н.С., Горячев П.Т. – Получение кобальтовых покрытий из парогазовой фазы II. Сб. Защитные покрытия на металлах. – Л.: Наука, 1972, с.63-67].
Применение оксидов кобальта в смеси с хлористым аммонием NH4Cl не обеспечивает необходимого качества получаемого покрытия, обусловленного наличием водяного пара. В покрытии наблюдается значительное количество неметаллических включений. Кроме того, спекание частиц кобальта затрудняет формирование покрытия в полостях, щелях и отверстиях, например таких, как охлаждаемые лопатки газовых турбин. Забивание полостей спекающимися частицами затрудняет их очистку после насыщения кобальтом (кобальтирование) и приводит к неоправданной отбраковке деталей.
Известен также способ нанесения покрытий на жаропрочный сплав на основе никеля, включающий последовательное диффузионное насыщение сплава элементами в циркулирующей галогенидной среде (Лахтин Ю.М., Арзамасов Б.Н. «Химико-термическая обработка металлов». – М.: «Металлургия», 1985, с.247-252) – прототип. Однако данный способ не обеспечивает получение качественного защитного покрытия из-за нестабильности поверхностного слоя и низкой стойкости покрытия к солевой коррозии в условиях циклического изменения температуры, тем самым уменьшая долговечность покрытия.
Технический результат заявленного способа – повышение качества и долговечности покрытия.
Указанный технический результат достигается тем, что в предлагаемом способе нанесения покрытий на жаропрочный сплав на основе никеля, включающем последовательное диффузионное насыщение сплава элементами в циркулирующей среде, содержащей галогениды, диффузионное насыщение проводят при температуре >900°С, но не выше температуры закалки сплава на основе никеля, последовательно кобальтом и алюминием, причем насыщение кобальтом проводят в среде, содержащей компоненты при следующем соотношении, мас.%:
галогенид аммония – 0,2-15
источник кобальта – 85-99,8.
При этом в качестве галогенида аммония можно использовать йодистый аммоний, или хлористый аммоний, или бромистый аммоний, или фтористый аммоний, или их смесь.
Диффузионное насыщение можно осуществить при температуре >900°С, но не выше температуры закалки сплавов, поскольку при нагреве выше температуры закалки возможно локальное оплавление структурных составляющих и снижение характеристик жаропрочности защищаемых сплавов.
При содержании галогенидов аммония, которые используются в качестве активатора, в количестве менее чем 0,2 мас.% процесс диффузионного осаждения кобальта протекает крайне медленно и насыщение кобальтом (кобальтирование) неэффективно. При увеличении содержания галогенидов аммония свыше 15 мас.% происходит выброс излишков газовой смеси в атмосферу в связи с резким нарастанием избыточного давления в реторте для газового кобальтирования, кроме того, при увеличении давления больше атмосферного не происходит увеличения скорости процесса кобальтирования.
Процесс газового кобальтирования деталей проводят при температуре 900-1200°С в течение 1-20 часов. В процессе изотермической выдержки протекают реакции переноса кобальта на поверхность деталей из жаропрочных сплавов путем замещения атомов кобальта в галогенидах элементами с более высокой, чем у кобальта, активностью к галогенам. В переносе участвуют легирующие элементы сплавов, например: Al, Nb, Ti,
3CoCl2+2Аl 3Со+2АlСl3;
CoCl2+Nb Co+NbCl2;
3CoCl2+2Ti 3Co+2TiCl3,
а также водород – продукт диссоциации солей хлорида, фторида, йодида кобальта:
CoCl2+Н2 Со+2НСl;
CoF2+H2 Co+2HF;
CoI2+H2 Со+2HI.
Кобальт повышает прочность сцепления покрытия со сплавом, а также образует оксидную пленку, которая растворяется в солевом осадке на лопатках турбин со скоростью на порядок меньшей, чем скорость растворения пленки оксида никеля на никелевых сплавах, например, при солевой коррозии по механизму основного флюсования оксидов при температуре 900-950°С.
Для усиления защитных свойств после кобальтирования проводят алитирование или хромоалитирование деталей известными способами в порошковой или газовой среде. Полученное покрытие представляет собой -фазу (Ni,Co) Al и содержит повышенную концентрацию кобальта во внешней зоне 25-30%, что обеспечивает повышение на 70-85% стойкости к солевой коррозии в условиях циклического изменения температуры на деталях.
При реализации способа нанесения покрытий на сплавы может быть использована специальная установка, например, приведенная в патенте RU №2270880 С1, 27.02.2006 г. С23С 10/14, в которой осуществляют процесс диффузионного насыщения в циркулирующей газовой среде.
На фиг.1 приведена микроструктура покрытия на сплаве ЧС88У после диффузионного насыщения кобальтом (кобальтирование).
На фиг.2 приведена микроструктура покрытия на сплаве после диффузионного насыщения кобальтом и алюминием (кобальталитирование).
Примеры нанесения слоя покрытия методом диффузионного насыщения в циркулирующей галогенидной среде с различным составом компонентов для насыщения в рабочей камере приведены ниже.
Пример 1.
В муфель загружали детали из сплавов ЧС88У, ЧС104, ЖС32, ЖС6У и состав, содержащий кобальт 90% и йодистый аммоний 10%. Из муфеля откачивали воздух до давления 10-1 мм рт.ст. и нагревали до температуры 1030°С в течение 4-х часов. Получали слой покрытия толщиной 30-40 мкм, содержащий 37-39% кобальта. Затем проводили газовое алитирование в среде, содержащей алюминий и соль хлористого алюминия AlCl3 при температуре 1000°С в течение 6 часов. Получали покрытие толщиной 50 мкм, содержащее 28% алюминия и 35% кобальта.
Пример 2.
В муфель загружали детали из тех же сплавов, что и в примере 1, а для переноса кобальта использовали состав, содержащий кобальт 90,5% и смесь хлористого и йодистого аммония в количестве 9,5%, взятых в соотношении NH4Cl:NH4I=1:3. За 4 часа при температуре 970°С получали покрытие толщиной 12-15 мкм. Содержание кобальта в покрытии на сплавах составило 40-53%. Затем проводили газовое алитирование при температуре 1000°С в течение 6 часов. Получали покрытие толщиной 48 мкм, содержащее 27% кобальта и 28% алюминия. Основной структурной составляющей покрытия является -фаза (Ni,Co) Al.
Пример 3.
Повторяли процесс, изложенный в примере 1, а для переноса кобальта использовали состав, содержащий кобальт 90% и фтористый аммоний в количестве 10%. После кобальтирования получали покрытие толщиной 18-22 мкм. Содержание кобальта в покрытии составило 23-26%. Затем проводили газовое алитирование при 1000°С в течение 6 часов. Получали покрытие толщиной 50 мкм, содержащее 28-29% алюминия и 12-15% кобальта.
Таким образом, использование предлагаемого способа позволяет получать защитное покрытие, обеспечивающее, по сравнению с существующими, следующие преимущества:
– повышение на 70-85% стойкости к солевой коррозии в условиях циклического изменения температуры на деталях;
– увеличение стабильности поверхностного слоя;
– увеличение долговечности покрытия на деталях.
Формула изобретения
1. Способ нанесения покрытий на жаропрочный сплав на основе никеля, включающий последовательное диффузионное насыщение сплава элементами в циркулирующей среде, содержащей галогениды, отличающийся тем, что диффузионное насыщение проводят при температуре >900°С, но не выше температуры закалки сплава на основе никеля, последовательно кобальтом и алюминием, причем насыщение кобальтом проводят в среде, содержащей компоненты при следующем соотношении, мас.%:
галогенид аммония |
0,2-15 |
источник кобальта |
85-99,8 |
2. Способ по п.1, отличающийся тем, что в качестве галогенида аммония используют йодистый аммоний, или хлористый аммоний, или бромистый аммоний, или фтористый аммоний, или их смесь.
РИСУНКИ
|
|