|
(21), (22) Заявка: 2007124587/03, 02.07.2007
(24) Дата начала отсчета срока действия патента:
02.07.2007
(46) Опубликовано: 20.02.2009
(56) Список документов, цитированных в отчете о поиске:
RU 2079051 C1, 10.05.1997. RU 2163326 C2, 20.02.2001. GB 2359874 A, 05.09.2001. EP 0289355 A3, 02.11.1988. WO 8801711 A1, 10.03.1988.
Адрес для переписки:
129366, Москва, а/я 702, Н.Г. Макарову
|
(72) Автор(ы):
Кондра Евгений Иванович (RU), Фурсов Виктор Прокофьевич (RU)
(73) Патентообладатель(и):
Общество с ограниченной ответственностью “Интеллект-ресурс” (ООО “Интеллект-ресурс”) (RU)
|
(54) СПОСОБ ГАЗИФИКАЦИИ КОНДЕНСИРОВАННЫХ ТОПЛИВ И УСТРОЙСТВО ДЛЯ ЕГО ОСУЩЕСТВЛЕНИЯ
(57) Реферат:
Изобретение относится к области термической переработки конденсированных топлив. Способ газификации углеродсодержащих конденсированных топлив, в котором через слой топлива противоточно пропускают кислородсодержащий газифицирующий агент, поддерживают в слое топлива процесс его газификации. Ограничивают величину максимальной температуры в газификаторе заданными пределами, а также выводят из газификатора твердые и газообразные продукты переработки. Кроме того, осуществляют выравнивание значений расхода топлива по поперечному сечению газификатора, создают разрыв слоя топлива, а зону максимальной температуры удерживают в положении ниже указанного разрыва. Устройство для газификации углеродсодержащих конденсированных топлив, содержащее газификатор шахтного типа с верхней загрузкой, снабженный средствами загрузки топлива в рабочую зону газификатора, средствами подачи кислородсодержащего газифицирующего агента, средствами вывода получаемого газа, средствами выгрузки твердых продуктов переработки из рабочей зоны газификатора, а также средствами контроля температур в рабочей зоне. Кроме того, в устройство введено средство выравнивания значений расхода топлива по поперечному сечению рабочей зоны газификатора, выход которого расположен на расстоянии Lв=(0,2-0,75)Lрз от нижней границы рабочей зоны газификатора, где Lрз – длина рабочей зоны газификатора. Технический результат заключается в повышении равномерности распределения температур в слое топлива и повышении управляемости процессом. 2 н. и 4 з.п. ф-лы, 1 ил.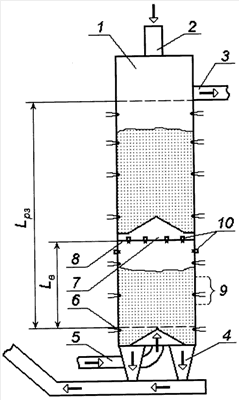
Изобретение относится к способам и устройствам для термической переработки конденсированных топлив путем их газификации.
Далее для исключения неоднозначности трактовки текста описания настоящего изобретения введем нижеследующие термины (выделены курсивом) и их определения.
Топливо – газифицируемый углеродсодержащий материал в чистом виде или с добавками кускового инертного материала.
Под конденсированными топливами в данной заявке подразумеваются содержащие свободный или химически связанный углерод материалы любого происхождения, например ископаемые топлива (уголь, торф, сланцы), биомасса (древесина, солома и т.п.), промышленные отходы (отходы углеобогащения или углепереработки, резинотехнические отходы и др.), коммунальные отходы (илы полей фильтрации, бытовой мусор).
Газификатор шахтного типа с верхней загрузкой – устройство, в котором может быть реализован заявляемый способ, представляющее собой вертикальную шахтную печь, снабженную датчиками для контроля профилей температур по высоте шахты газификатора, средствами для загрузки топлива и вывода газообразных продуктов переработки сверху шахты, а также средствами для выгрузки твердых продуктов и подачи кислородсодержащего газифицирующего агента снизу шахты.
Кислородсодержащий газифицирующий агент – кислород, воздух или другая смесь газов, содержащих кислород, например, парокислородная или паровоздушная смесь, дымовые газы, обогащенный кислородом воздух и т.п.
Противоточное пропускание – подача в газификатор кислородсодержащего газифицирующего агента и вывод из газификатора газообразных продуктов переработки таким образом, чтобы поток газов, проходящий через слой топлива, в любом месте слоя был направлен навстречу перемещению по шахте газификатора перерабатываемого топлива или твердых продуктов его переработки.
Рабочая зона газификатора – внутреннее пространство шахты газификатора, нижней границей которого является горизонтальная плоскость, проходящая через верхнюю точку элементов конструкции средств выгрузки твердых продуктов, а верхней границей – горизонтальная плоскость, проходящая через нижнюю точку элементов конструкции средств вывода газообразных продуктов переработки.
Зона максимальной температуры – область, в которой текущее значение температуры топлива в процессе газификации отличается от наибольшего из всех текущих значений температур топлива в данном газификаторе не более чем на заданную величину – температурную ширину зоны. Величина температурной ширины зоны задается как один из параметров для системы управления процессом переработки.
Заданное положение зоны максимальной температуры – такое пространственное положение зоны, когда ее верхняя и нижняя границы находятся в заданных оператором или системой регулирования пределах. Координаты верхнего и нижнего пределов положения границ зоны максимальной температуры по высоте шахты газификатора задаются в качестве параметров для системы управления процессом переработки топлива.
Ограничение заданного значения максимальной температуры в газификаторе – поддержание значения максимальной температуры в пределах, задаваемых в качестве параметров для системы управления процессом переработки топлива. Их значения зависят от вида перерабатываемого топлива и определяются термической стойкостью твердых продуктов его переработки и реакционной способностью образующегося кокса.
Область локального перегрева – область рабочей зоны газификатора, ограниченная участком поверхности внутренней стенки шахты, где температура превышает верхний предел, и конической поверхностью с вершиной на оси рабочей зоны и направляющей линией, ограничивающей этот участок поверхности внутренней стенки шахты.
Выравнивание значений расхода топлива по поперечному сечению газификатора – уменьшение локальных градиентов массового расхода топлива по поперечному сечению слоя топлива.
Перспективным направлением использования конденсированных топлив в энергетике является их газификация с получением генераторного газа, который сжигают в энергетических агрегатах для выработки тепла и/или электроэнергии. Замена прямого сжигания конденсированных топлив их газификацией позволяет повысить как экологическую чистоту, так и эффективность использования топлив в энергетике.
Например, КПД выработки электроэнергии в так называемом интегрированном с газификацией угля парогазовом цикле достигает 50%, что существенно превышает показатели традиционных угольных ТЭС, включая и чистоту выбросов в атмосферу. Недостатками чаще всего используемого в этой технологии способа газификации водно-угольной суспензии в спутном потоке под давлением с применением кислородного дутья (например, процесс ChevronTexaco) являются сложность конструкции газификатора, требующая больших капитальных затрат на его создание, большие внутренние затраты электроэнергии на выделение кислорода из воздуха, а также высокая пожаровзрывоопасность сосуда большого объема, работающего под давлением с использованием кислородного дутья.
Более традиционной для угля считается его газификация в плотном слое (например, метод Lurgi), которую осуществляют в газификаторе шахтного типа при противотоке паровоздушного газифицирующего агента и кускового угля определенного фракционного состава. В отечественной литературе подобную технологию с использованием противотока топлива и газифицирующего агента называют прямым процессом, в отличие от так называемого обращенного процесса, в котором топливо и газифицирующий агент подаются в газификатор спутно.
Недостатком газификации в плотном слое является чувствительность технологического процесса к свойствам перерабатываемого топлива, в частности к его фракционному составу и термической стойкости золы. Большое количество мелочи в топливе может приводить к неравномерной фильтрации газов по рабочему сечению газификатора, искривлениям температурного фронта с выходом температур в локальных областях за допустимые технологические пределы. Недостаточная термическая стойкость золы в сочетании с локальными перегревами может вызывать зашлаковывание газификатора с последующей остановкой процесса.
Известны также способы газификации в плотном слое других конденсированных топлив, помимо угля.
Так, известен способ утилизации маслоотходов или шламов и иных отходов, содержащих тяжелые, в том числе жидкие, углеводороды (см. патент РФ №2116570, кл. F23G 7/00, оп. 27.07.1998 г.). В соответствии с этим способом отходы загружают в реактор, в реактор подают кислородсодержащий газ и проводят реакцию горения с образованием газообразных продуктов горения и твердого остатка, и твердый остаток горения выгружают из реактора. Кислородсодержащий газ подают в реактор непрерывно в количестве, недостаточном для полного окисления отходов, причем кислородсодержащий газ подается таким образом, что он пропускается через слой твердого остатка, а газообразные продукты горения пропускают через слой свежих отходов для получения продукт газа, содержащего углеводороды и капли жидких углеводородов. При реализации изобретения переработка отходов может осуществляться без использования внешних источников тепла.
Недостатком этого способа является недостаточная управляемость температурным режимом процесса при возникновении искривлений температурного фронта, которые возникают из-за неравномерности движения перерабатываемого материала по поперечному сечению реактора, или неравномерности фильтрации газового потока по нему.
Известен способ переработки конденсированных горючих, преимущественно высоковлажных, таких как твердые бытовые отходы, отходы биомассы, илы и шламы, уголь, путем пиролиза и газификации органической составляющей отходов (см. патент РФ №2152561 С1, кл. F23G 5/027, оп. 10.07.2000 г.). По этому способу в реактор загружают шихту, которая, по крайней мере, частично состоит из горючих компонентов, а также, возможно, кускового твердого негорючего материала, и устанавливают газовый поток сквозь упомянутую загрузку путем подачи в реактор газифицирующего агента, содержащего кислород, водяной пар и углекислый газ. Газообразные и жидкие продукты переработки выводят в виде продукт газа из реактора, где последовательные сечения упомянутой загрузки последовательно пребывают в зонах нагревания, пиролиза, коксования, газификации и охлаждения, регулируют температуры в зоне горения в пределах от 800 до 1300°С, выгружают из реактора твердые продукты переработки, сжигают по крайней мере часть продукт газа, при этом в качестве газифицирующего агента используют дымовой газ, преимущественно в смеси с воздухом. По сравнению с предыдущим способом по патенту РФ №2116570 этот способ позволяет увеличить энергетическую эффективность передела топлив в газ, особенно топлив с высокой влажностью.
Недостатком этого способа также является недостаточная управляемость температурным режимом процесса при возникновении искривлений температурного фронта, которые возникают из-за неравномерности движения перерабатываемого материала по поперечному сечению реактора, или неравномерности фильтрации газового потока по нему.
Наиболее близким к настоящему изобретению является способ переработки твердых бытовых отходов (см. патент РФ №2079051, кл. F23G 5/027, оп. 10.05.1997 г.) путем загрузки последних в реактор, подачи в реактор газифицирующего агента, содержащего кислород, со стороны реактора, где происходит накопление твердых продуктов переработки, вывод твердых продуктов переработки из реактора, а также вывод из реактора продуктов сушки, пиролиза и горения в виде продукт газа так, что газификация проводится посредством последовательного пребывания отходов в зоне нагревания и сушки, зоне пиролиза, зоне горения (окисления) и зоне охлаждения, отличающийся тем, что максимальную температуру в реакторе поддерживают в пределах 700…1400°С путем регулирования по меньшей мере одного параметра, выбираемого из следующих: массовой доли а кислорода в газифицирующем агенте, массовой доли b негорючего материала в отходах и массовой доли с горючего материала в отходах, поддерживая при этом отношение А ab/с в пределах 0,1-4,0.
По сравнению с упомянутыми выше методами по патентам РФ №2116570 и №2152561 этот способ отчасти расширяет возможности управления максимальной температурой в реакторе за счет ввода воды в зону горения или охлаждения, однако не устраняет их основной недостаток, указанный выше.
Недостатком этого способа также является недостаточная управляемость процессом газификации при большой неравномерности распределения температур в слое топлива. Указанная неравномерность распределения температур обусловлена в известном способе тем, что из-за негомогенности перерабатываемого топлива возникают как неравномерности его перемещения по рабочему сечению газификатора, так и неравномерности встречного газового потока при его фильтрации через слой перерабатываемого топлива. При длительной работе эти неравномерности могут нарастать, приводя к формированию в слое перерабатывемого топлива практически неуправляемых локальных перегревов, и к необходимости остановки газификатора.
В подобном газификаторе, представляющем собой цилиндрическую вертикальную шахтную печь, футерованную огнеупорным бетоном, с диаметром рабочего сечения 1500 мм, и снабженную датчиками температуры для контроля температурного поля в рабочем пространстве, установленными на нескольких уровнях по высоте шахты по четыре датчика по периметру на каждом уровне, нами были проведены исследования паровоздушной газификации твердых бытовых отходов, старых автомобильных покрышек, древесных отходов различной влажности (20-50%) при их подаче в газификатор вместе с оборотным кусковым огнеупорным материалом (бой шамотного кирпича). Математическая обработка показаний датчиков температуры позволяла подробно отслеживать в реальном времени динамику изменений температурного поля на внутренней поверхности рабочего пространства шахты. При испытаниях было установлено, что надежно управлять температурным режимом процесса путем регулирования доли паров воды в газифицирующем агенте (изменением расхода пара) удается только при достаточно ровном температурном фронте, когда положения максимумов температур в разных частях рабочего сечения шахты сильно не различаются. В противном случае увеличение расхода пара очень слабо воздействовало на локальные разогревы в опережающих областях искривленного фронта. Температура в таком случае снижалась при увеличении расхода пара преимущественно в отстающих областях искривленного фронта, находящихся ближе к месту подачи в газификатор газифицирующего агента, что приводило к заметному уменьшению выхода и теплотворной способности газообразных продуктов переработки (генераторного газа). В тех случаях, когда максимальная температура в местах локальных разогревов достигала точки плавления золы, начинался процесс зашлаковывания, и в выгружаемом из газификатора твердом минеральном остатке появлялись спеки в виде агломератов кускового шамота, скрепленного затвердевшим шлаком. Как показывает опыт, зашлаковывание рабочего сечения шахты газификатора вызывает серьезные нарушения равномерности перемещения по нему перерабатываемой топливной смеси, что, в конце концов, может закончится прекращением ее перемещения по значительной части рабочего сечения шахты и последующей остановкой процесса.
К сожалению, наш опыт также показал, что эффективных «рычагов» для устранения искривлений температурного фронта в плотном слое при осуществлении процесса, заявленного в патенте РФ №2079051, очень мало. Вероятность возникновения подобных нештатных режимов удается уменьшить, принимая максимум профилактических мер, направленных на обеспечение равномерности подачи и перемещения перерабатываемого материала по рабочему сечению шахты, на исключение сепарации материала по размерам частиц и их плотности, на обеспечение равномерной фильтрации газифицирующего агента и образующегося генераторного газа по поперечному сечению. Такие профилактические меры включают соответствующую подготовку топлива, например, отсев мелочи, а также соответствующие доводки конструкции устройств загрузки-выгрузки, подачи газифицирующего агента и вывода генераторного газа, обеспечивающие равномерность потоков конденсированной и газовой фазы по рабочему сечению шахты газификатора.
Примеры такой доводки устройств загрузки-выгрузки известны. Например, устройство выгрузки реактора шахтного типа для переработки отходов (см. патент РФ №2210029, кл. F23G 5/00, оп. 10.08.2003 г.) позволяет осуществлять непрерывный процесс утилизации (переработки) различных видов промышленных отходов в реакторе с полной загрузкой его по высоте и порционной выдачей по мере накопления зольного остатка и отработанных инертных материалов без нарушения технологических режимов процессов горения, герметичности подколосникового пространства при исключении выбросов зольной пыли и вредных примесей в окружающую среду. Как отмечено в описании этого изобретения, конструктивное выполнение предложенного устройства позволяет осуществлять экологически чистый непрерывный процесс утилизации промышленных отходов с полной загрузкой (по вертикали) внутренней полости реактора промышленными отходами и дозированной (порционной) выдачей зольного остатка с отработанным инертным материалом. В этом устройстве колосниковая плита поддерживает слой перерабатываемого топлива, обеспечивает его перемещение вниз по шахте с заданной скоростью и позволяет выгружать материал практически идеально ровно по поперечному сечению реактора.
Известны также способы и устройства, обеспечивающие загрузку с равномерным распределением частиц материала по поперечному сечению загружаемого реактора и по высоте слоя, позволяющие формировать слой материала однородной структуры по объему загружаемого реактора. Например, способ загрузки катализаторов в реакторы технологических установок (см. патент РФ №2252067, кл. B01J 4/00, оп. 20.05.2005 г.) и загрузочное устройство (см. патент РФ №2222373, кл. B01J 4/00, B65G 65/32, оп. 27.01.2004 г.) обеспечивают равномерную подачу сыпучего материала с целью получения однородного по своим физико-механическим и гидродинамическим свойствам слоя частиц этого материала в реакторе.
Тем не менее, использование устройств равномерной загрузки-выгрузки и другие упомянутые выше профилактические меры для устранения искривлений температурного фронта при газификации в плотном слое не всегда предотвращают возникновение нештатных температурных режимов технологического процесса.
Численное моделирование процесса газификации углерода в противотоке кислородсодержащего газифицирующего агента в части газификации кокса подобное процессу, заявленному в патенте РФ №2079051, показывает, что максимальные температуры конденсированной фазы в реакторе развиваются в окислительной зоне вблизи ее границы с восстановительной зоной, где полностью исчерпывается подаваемый в реактор кислород, расходующийся на окисление кокса (см. РР10.05 V.Fursov, V.Rafeev. Stationary regimes of carbon gasification in the adiabatic reactor of finite length. International Conference on Combustion and Detonation Zel’dovich Memorial II. August 30 – September 3, 2004, Moscow, Russia). Именно в этой области при превышении допустимого температурного технологического предела начинается процесс зашлаковывания реактора. Ниже границы окислительной и восстановительной зон по потоку газов располагается зона, в которой преобладают реакции восстановления углекислого газа и паров воды горячим коксом. Это – зона относительно умеренных (600-800°С) температур, так как упомянутые реакции идут с сильным поглощением тепла. Такая температурная структура фронта газификации кокса в прямом процессе позволяет предложить новое техническое решение, способное существенно улучшить управляемость температурным режимом процесса.
Изобретение, относящееся к способу газификации углеродсодержащих конденсированных топлив в газификаторе шахтного типа с верхней загрузкой, решает задачу создания способа газификации углеродсодержащих конденсированных топлив с более высокой управляемостью температурным режимом технологического процесса по сравнению с известными способами газификации, реализующими прямой процесс в плотном слое.
Технический результат, обеспечиваемый изобретением, относящимся к способу, заключается в повышении равномерности распределения температур в слое топлива, в результате чего существенно повышается управляемость процессом газификации топлива.
Указанный технический результат достигается тем, что в способе газификации углеродсодержащих конденсированных топлив в газификаторе шахтного типа с верхней загрузкой, в котором через слой топлива противоточно пропускают кислородсодержащий газифицирующий агент, поддерживают в слое топлива процесс его газификации, обеспечивают заданное положение зоны максимальной температуры в газификаторе, управляя скоростью перемещения топлива по газификатору и/или расходом и/или составом кислородсодержащего газифицирующего агента, ограничивают величину максимальной температуры в газификаторе заданными пределами, а также выводят из газификатора твердые и газообразные продукты переработки, осуществляют выравнивание значений расхода топлива по поперечному сечению газификатора; ниже сечения, в котором осуществляют выравнивание значений расхода топлива, создают разрыв слоя топлива, а зону максимальной температуры удерживают в положении ниже указанного разрыва.
Указанный технический результат достигается также тем, что при ограничении максимальной температуры в газификаторе в разрыв слоя топлива вводят воду. При этом достигается дополнительный технический результат, заключающийся в повышении экономичности способа за счет уменьшения потребности в выработке пара, вводимого в кислородсодержащий газифицирующий агент, что позволяет увеличить энергетическую эффективность передела топлива в генераторный газ.
Указанный технический результат достигается также тем, что воду вводят непосредственно в точки поперечного сечения газификатора, соответствующие проекциям областей локальных перегревов на указанное поперечное сечение.
Устройства для газификации твердых топлив в плотном слое известны с 1930-х годов (газификаторы фирмы Lurgi в Германии, газификаторы фирмы Wellman в Великобритании). Такой газификатор представляет собой шахтную печь с верхней загрузкой и вращающимся колосником снизу для выгрузки золы. Основным недостатком такого устройства является отсутствие эффективных средств выравнивания расхода перерабатываемого топлива по поперечному сечению шахты в рабочей зоне газификатора. В довоенных отечественных образцах газификаторов подобного типа в стенке шахты делали специальные отверстия, через которые можно было осуществлять шуровку слоя топлива вручную, и тем самым устранять неоднородности его перемещения по рабочей зоне газификатора.
Наиболее близким к заявленному устройством является печь для термической переработки промышленных и бытовых отходов (см. патент РФ №2163326, кл. F23G 5/00, оп. 20.02.2001 г.). Загрузочное устройство печи снабжено механизмом разравнивания загружаемого топлива, что повышает равномерность его распределения по поперечному сечению шахты при загрузки печи.
Недостатком известного устройства также, как и газификаторов с прямым процессом в плотном слое, упомянутых выше, является нарастание неравномерности расхода перерабатываемого топлива по поперечному сечению газификатора при движении топлива от верхней границы рабочей зоны газификатора к зоне максимальной температуры, особенно при переработке топлив, неоднородных по своему составу и свойствам (влажности, количеству мелочи и др.). Такая неравномерность приводит к искривлениям температурного фронта в газификаторе и к формированию в слое перерабатывемого топлива практически неуправляемых локальных перегревов, вынуждающих останавливать технологический процесс.
Технический результат, обеспечиваемый изобретением, относящимся к устройству, заключается в повышении равномерности распределения температур в слое топлива за счет устранения неоднородности его потока по поперечному сечению в рабочей зоне газификатора, в результате чего существенно повышается управляемость процессом газификации топлива.
Указанный технический результат достигается тем, что в устройство для газификации углеродсодержащих конденсированных топлив, содержащее газификатор шахтного типа с верхней загрузкой, снабженный средствами загрузки топлива в рабочую зону газификатора, средствами подачи кислородсодержащего газифицирующего агента, средствами вывода получаемого газа, средствами выгрузки твердых продуктов переработки из рабочей зоны газификатора, а также средствами контроля температур в рабочей зоне, введено средство выравнивания значений расхода топлива по поперечному сечению рабочей зоны газификатора, выход которого расположен на расстоянии Lв=(0,2-0,75)Lрз от нижней границы рабочей зоны газификатора, где Lрз – длина рабочей зоны газификатора.
Указанный технический результат достигается также тем, что в устройстве для газификации углеродсодержащих конденсированных топлив в стенках газификатора на расстоянии (0,7-0,98)Lв от нижней границы его рабочей зоны установлены средства ввода воды в топливо. При этом достигается дополнительный технический результат, заключающийся в повышении экономичности процесса газификации за счет уменьшения потребности в выработке пара, вводимого в кислородсодержащий газифицирующий агент, что позволяет увеличить энергетическую эффективность передела топлива в генераторный газ.
На чертеже показана схема устройства для осуществления заявленного способа. Стрелками на схеме обозначены направления потоков топлива и газифицирующего агента, подаваемых в газификатор, а также генераторного газа и твердых продуктов переработки, выводимых из него.
Устройство для газификации углеродсодержащих конденсированных топлив содержит газификатор 1 шахтного типа с теплоизоляцией и футеровкой внутренних стенок шахты прочным огнеупором, выдерживающим высокие температуры и механическое воздействие перемещаемого по шахте топлива. В верхней части газификатор 1 снабжен средствами 2 для загрузки топлива. В качестве таких средств могут быть использованы шлюзовые устройства различной конструкции, например барабанные питатели или другие устройства, обеспечивающие контролируемую непрерывную или порционную загрузку топлива в газификатор с равномерным распределением топлива по поперечному сечению его рабочей зоны, верхняя и нижняя границы которой обозначены на схеме пунктиром. Конструкция шлюзового устройства должна также препятствовать поступлению воздуха в газификатор или утечкам генераторного газа в атмосферу.
В верхней части газификатор 1 также снабжен средствами 3 для вывода генераторного газа, которые могут включать трубопровод для транспортировки генераторного газа в горелку, в систему очистки или иные устройства для его утилизации, снабженные соответствующим тягодутьевым оборудованием, обеспечивающим отсос генераторного газа из газификатора 1.
В нижней части газификатор снабжен средствами 4 для выгрузки твердого остатка переработки топлива, которые могут включать, например, вращающийся колосник, затворы барабанного типа и транспортер для удаления золы. Эти средства обеспечивают равномерное по поперечному сечению нижней части рабочей зоны газификатора удаление из него накапливающегося по мере переработки топлива твердого остатка.
Нижняя часть газификатора снабжена также средствами 5 для подачи в него газифицирующего агента, которые могут включать вентилятор для подачи воздуха, парогенератор, соответствующие трубопроводы и другую необходимую арматуру для подачи и регулирования расхода воздуха, пара, или других газов, которые подсоединены к входному коллектору газифицирующего агента, из которого последний поступает в газификатор, например, через соответствующие отверстия в колоснике, входящем в состав средств 4, навстречу выгружаемому твердому остатку переработки.
Для контроля температурного поля на внутренней стенке шахты газификатор снабжен средствами 6, которые могут включать подключенные к системе регистрации и управления температурные датчики, например, термопары, устанавливаемые на нескольких уровнях по высоте газификатора по несколько штук по периметру на каждом уровне.
В соответствии с предлагаемым изобретением в устройство для газификации углеродсодержащих конденсированных топлив вводят средство 7 выравнивания значений расхода топлива по поперечному сечению рабочей зоны газификатора, выход которого 8 расположен на расстоянии Lв=(0,2-0,75)Lрз от нижней границы рабочей зоны газификатора, где Lрз – длина рабочей зоны газификатора. В одной из частных форм выполнения средство 7 может представлять собой устройство равномерной по поперечному сечению газификатора подачи сыпучего материала (распределительное устройство), выполненное, например, по патенту РФ №2222373. Однако оно обладает тем недостатком, что может привести к увеличению неравномерности расходов топлива (по поперечному сечению газификатора) в области, расположенной выше средства 7. В другой, наиболее предпочтительной, частной форме выполнения средство 7 может включать, например, устройство равномерной (по поперечному сечению газификатора) выгрузки материала и установленное под ним устройство для равномерного распределения частиц перемещаемого топлива по поперечному сечению газификатора ниже выхода 8 средства 7. Такая форма выполнения средства 7 обеспечивает формирование слоя топлива однородной структуры с равномерным по поперечному сечению газификатора распределением расходов топлива перед его поступлением в зону максимальной температуры 9 и не искажает распределение по поперечному сечению газификатора расходов топлива в области, расположенной выше средства 7. Устройство для равномерной выгрузки материала, выполненное, например, в соответствии с патентом РФ №2210029, обеспечивает почти идеально равномерное по сечению шахты перемещение топлива над ним. Однако оно не обеспечивает равномерного по сечению распределения топлива под ним. Эту задачу решает установка под устройством равномерной выгрузки распределительного устройства (устройства для равномерной подачи), выполненного, например, по патенту РФ №2222373. Таким образом, конструктивное исполнение средства выравнивания 7 в виде пары известных средств – «устройство для равномерной выгрузки + распределительное устройство (устройство для равномерной подачи)» обеспечивает одновременное выравнивание значений расхода топлива по поперечному сечению рабочей зоны газификатора как над средством 7, так и под ним.
, что каждое из устройств вышеупомянутой пары само по себе является устройством для выравнивания значений расхода топлива по поперечному сечению газификатора. Однако каждое из них в отдельности может лишь частично выполнить функцию средства 7 и обеспечить достижение заявляемого технического результата, так как задача достижения высокой управляемости температурным режимом технологического процесса наилучшим образом решается при условии равномерности расхода топлива по поперечному сечению газификатора по всей высоте его рабочей зоны как над средством 7, так и под ним.
Разумеется, элементы, составляющие средство 7, выполняются газопроницаемыми, чтобы при выравнивании значений расхода топлива по поперечному сечению рабочей зоны газификатора средство 7 не препятствовало равномерному противоточному пропусканию газов.
Указанный выше диапазон координаты расположения выхода 8 средства 7 относительно нижней границы рабочей зоны газификатора обеспечивает практическую осуществимость предлагаемого способа газификации с достижением заявляемого технического результата по следующим причинам. Как показывает численное моделирование процесса газификации кокса в газификаторе конечной длины (см. РР10.05 V.Fursov, V.Rafeev. Stationary regimes of carbon gasification in the adiabatic reactor of finite length. International Conference on Combustion and Detonation Zel dovich Memorial II. August 30 – September 3, 2004, Moscow, Russia), стационарное положение зоны максимальной температуры может быть обеспечено при соответствующих соотношениях скоростей подачи в газификатор топлива и газифицирующего агента практически в любом месте рабочей зоны газификатора. Однако при расположении зоны максимальной температуры вблизи верхней границы рабочей зоны газификатора, куда подается перерабатываемое топливо, резко снижается теплотворная способность получаемого газа из-за чрезмерного сужения зоны, в которой кокс реагирует с парами воды и углекислым газом с образованием основных горючих компонент – водорода и угарного газа. В другом предельном случае, когда зона максимальной температуры расположена вблизи нижней границы рабочей зоны, это ее положение по результатам численного моделирования является неустойчивым, и без жесткого управления она имеет тенденцию либо сместиться навстречу подаваемому газифицирующему агенту, «садясь» на нижний колосник, входящий в состав средств 4 для выгрузки твердого остатка, либо в противоположную сторону, приближаясь к средству 7. Кроме того, при расположении зоны максимальной температуры вблизи нижней границы рабочей зоны газификатора время пребывания кокса в зоне высокой температуры может стать недостаточным для его полного окисления, и в выгружаемом твердом остатке появится недогоревший углерод. По этим причинам оптимальным с точки зрения устойчивости положения зоны максимальной температуры, а также высокой эффективности процесса газификации топлива с получением достаточно калорийного газа и отсутствием недожога в твердом остатке является такое расположение средства 7, когда его выход расположен на расстоянии Lв от нижней границы рабочей зоны газификатора не ближе 0,2Lрз и не дальше 0,75Lрз.
Чтобы улучшить управляемость температурным режимом газификации и повысить ее энергетическую эффективность, в устройстве для газификации углеродсодержащих конденсированных топлив в стенках газификатора на расстоянии (0,7-0,98)Lв от нижней границы его рабочей зоны устанавливают средства 10 ввода воды в топливо. Средства 10 для подачи воды могут включать форсунки с соответствующими трубопроводами, насосами и другой необходимой арматурой, которые обеспечивают управляемую подачу воды в газификатор. Путем соответствующего расположения и юстировки форсунок добиваются равномерного распределения подачи воды по поперечному сечению рабочей зоны газификатора. Заявляемый диапазон координат расположения средств 10 относительно нижней границы рабочей зоны газификатора обеспечивает, с одной стороны, возможность юстировки форсунок таким образом, чтобы надежно распределить воду равномерно по поверхности слоя топлива ниже выхода 8, и, с другой стороны, чрезмерно не ограничивать высоту положения этой поверхности установкой форсунок на большом расстоянии от выхода 8 средства выравнивания 7. При большом расстоянии от форсунок до выхода 8 высокий слой топлива может не позволить подавать воду в области рабочей зоны газификатора вблизи его оси.
Другим возможным вариантом конструктивного решения задачи ввода воды с распределением ее по поверхности топлива ниже средства выравнивания 7 является снабжение этого средства средствами ввода воды 10. В этом варианте средство 7 может быть выполнено с возможностью подачи воды непосредственно через элементы конструкции средства 7 (например, путем использования полых элементов конструкции), или же соответствующие элементы средств ввода воды (трубопроводы, форсунки) могут быть установлены на элементах конструкции средства 7. В этом варианте может быть также предусмотрена возможность охлаждения элементов конструкции средства 7 подаваемой водой для устранения их нежелательного перегрева.
Заявленный способ осуществляется следующим образом.
Для инициирования процесса в газификатор загружают слой инертного материала для защиты средств 4 от воздействия высокой температуры. На этот слой загружают слой сухого легковоспламеняющегося топлива для розжига, например древесину или торф. На слой топлива для розжига загружают рабочее топливо. Опыт показывает, что при подаче в газификатор воздуха, нагретого до температур выше 250-300°С, после прогрева слоя инертного материала происходит воспламенение топлива для розжига. Воздух можно нагревать при помощи электронагревателей или горелок, работающих на газе или жидком топливе. После воспламенения топлива в газификаторе, контролируемого по показаниям датчиков температуры средств 6, нагрев воздуха прекращают. Подавая в газификатор при помощи средств 5 газифицирующий агент и выводя из него при помощи средств 3 образующиеся газы, обеспечивают противоточное пропускание газифицирующего агента через слой топлива, в котором формируют зону газификации с заданным положением зоны максимальной температуры 9. Процесс газификации в слое топлива поддерживают, периодически загружая в газификатор топливо при помощи средств 2, непрерывно подавая в газификатор 1 при помощи средств 5 кислородсодержащий газифицирующий агент и выводя из него при помощи средств 3 газообразные продукты переработки, а также выводя из газификатора твердые продукты при помощи средств 4.
Как показывает численное моделирование паровоздушной газификации углерода, показатели процесса могут быть улучшены путем добавления к газифицируемому углероду инертного материала, который, не участвуя в химических превращениях, обеспечивает оптимальное перераспределение потоков тепла между газовой и конденсированной фазой, в результате чего увеличивается так называемый химический коэффициент полезного действия, равный отношению теплоты сгорания холодного генераторного газа к теплоте сгорания исходного топлива. Так, например, при газификации высококачественных низкозольных углей с малой влажностью в прямом процессе получается относительно горячий генераторный газ. Если такой уголь перерабатывать совместно с кусковым термостойким инертным материалом (например, гранулами шамота), то температура генераторного газа может быть существенно снижена при одновременном увеличении его теплотворной способности. Это упрощает последующее использование генераторного газа, например, его очистку от смол и пыли, а также уменьшает удельный расход топлива при сжигании газа в тепловой машине.
Противоток газовой и конденсированной фазы в газификаторе с фильтрацией газов через слои перерабатываемого топлива создает за счет межфазного теплообмена условия для концентрации тепла, выделяющегося при окислении углерода, в средней части газификатора, где развивается наиболее высокая температура. Температурное поле на внутренней стенке шахты периодически контролируют средствами 6, включающими соответствующие датчики температуры, установленные на нескольких уровнях по высоте шахты.
В процессе газификации положение зоны максимальной температуры зависит от соотношения скорости перемещения топлива по газификатору и расхода и/или состава газифицирующего агента. При фиксированной скорости перемещения топлива и постоянном составе газифицирующего агента для каждого определенного положения зоны максимальной температуры существует соответствующая величина расхода газифицирующего агента, при которой эта зона будет неподвижна относительно газификатора. Эта величина определяется стехиометрией химических процессов, протекающих в зоне газификации. При большей величине расхода газифицирующего агента зона максимальной температуры будет перемещаться вдоль шахты газификатора вверх по направлению к средствам загрузки 2 и, наоборот, при меньшей величине расхода – вниз, по направлению к средствам выгрузки 4. При фиксированной величине расхода газифицирующего агента аналогичные перемещения зоны максимальной температуры будут происходить при изменении состава газифицирующего агента, например, при увеличении или уменьшении концентрации в нем кислорода. Изменение концентрации кислорода также, как и изменение расхода газифицирующего агента, приводит к отклонению от стехиометрии в зоне газификации и вызывает соответствующие перемещения ее положения в газификаторе.
Заданное положение зоны 9 максимальной температуры в газификаторе обеспечивают система управления или оператор, которые осуществляют соответствующие изменения скорости перемещения топлива по газификатору и/или расхода и/или состава кислородсодержащего газифицирующего агента. Например, при смещении верхней границы этой зоны 9 выше заданного предела увеличивают скорость перемещения топлива по газификатору путем соответствующего увеличения скоростей загрузки и выгрузки, или уменьшают расход газифицирующего агента, или концентрацию в нем кислорода. При смещении нижней границы этой зоны ниже заданного предела производят обратные вышеуказанным изменения параметра (параметров).
Величину максимальной температуры в газификаторе ограничивают заданными пределами. Их значения зависят от вида перерабатываемого топлива и определяются термической стойкостью твердых продуктов его переработки и реакционной способностью образующегося кокса. Верхний предел должен гарантировать недопущение процесса шлакования и, соответственно, задается тем ниже, чем ниже температура плавления золы. Например, при газификации различных марок углей верхний предел максимальной температуры может устанавливаться в диапазоне 1000…1200°. Нижний предел должен обеспечить достаточно высокую температуру для полного окисления образующегося из топлива кокса за время его пребывания в зоне газификации и, соответственно, задается тем выше, чем ниже реакционная способность кокса. Возможный диапазон нижнего предела максимальной температуры 600…800°С. Основным управляющим параметром при ограничении величины максимальной температуры в газификаторе является концентрация паров воды и/или углекислого газа в газифицирующем агенте, так как их реакции с горячим коксом идут с поглощением большого количества тепла. Соответственно, при выходе максимальной температуры за верхний предел система управления или оператор увеличивают концентрацию паров воды и/или углекислого газа в газифицирующем агенте и, наоборот, при выходе за нижний предел – уменьшают. Например, при использовании паровоздушной или парокислородной смеси эти изменения концентрации обеспечивают соответствующим увеличением или уменьшением количества водяного пара, вводимого в газифицирующий агент. При использовании смеси воздуха с дымовыми газами увеличивают или уменьшают количество вводимых в газифицирующий агент дымовых газов. В тех случаях, когда для уменьшения выбросов углекислого газа производится его выделение из генераторного газа или продуктов его сгорания, можно ограничивать величину максимальной температуры в газификаторе введением выделенного углекислого газа в газифицирующий агент и соответствующей регулировкой его количества.
В соответствии с предлагаемым изобретением для достижения заявляемого технического результата осуществляют выравнивание значений расхода топлива по поперечному сечению газификатора. Эту функцию выполняет средство выравнивания 7, которое установлено в средней части газификатора. Возможный вариант его конструктивного исполнения, обеспечивающий выполнение функции выравнивания расхода топлива в обеих частях рабочей зоны газификатора, приведен выше в описании устройства для реализации заявляемого способа.
Чтобы обеспечить условия для нормального функционирования средства 7, ниже его выхода 8 создают разрыв слоя топлива по всему поперечному сечению рабочей зоны путем соответствующего управления скоростью выгрузки твердых продуктов переработки при помощи средств 4. Очевидно, что при отсутствии такого разрыва средство 7 не сможет выполнять функцию выравнивания, так как увеличивать скорость продвижения топлива в областях поперечного сечения, где она замедлена, будет невозможно, не увеличив скорость выгрузки твердых продуктов переработки при помощи средств 4 и, тем самым, не создав разрыв слоя.
Зону максимальной температуры удерживают в положении ниже указанного разрыва. Для этого координаты верхнего и нижнего пределов положения границ зоны максимальной температуры по высоте шахты газификатора, задаваемые в качестве параметров для системы управления процессом переработки топлива устанавливают ниже указанного разрыва. Алгоритм обеспечения заданного положения зоны максимальной температуры путем управления скоростью перемещения топлива по газификатору, и/или расходом, и/или составом кислородсодержащего газифицирующего агента описан выше.
Такое взаимное расположение средства выравнивания 7 и заданного положения зоны максимальной температуры 9, с одной стороны, создает благоприятные условия для повышения однородности поля температур в этой зоне и управляемости их величинами и, с другой стороны, обеспечивает приемлемые условия, в которых функционирует средство 7, снижающие требования к жаростойкости и коррозионной стойкости его конструкции, так как оно располагается в зоне относительно умеренных температур с восстановительной средой. В эту часть рабочей зоны газификатора не проникает подаваемый с газифицирующим агентом кислород и температура перерабатываемого топлива относительно невысока (<800°С). Кислород полностью расходуется на окисление кокса в нижней части рабочей зоны газификатора, и, как было указано выше, в месте, где концентрация кислорода обращается в ноль, развивается максимальная температура. Выравнивание значений расхода перерабатываемого топлива непосредственно перед его поступлением в зону максимальных температур, куда оно перемещается в виде полукокса и кокса, существенно повышает равномерность распределения температур в слое топлива и, тем самым, заметно улучшает управляемость процессом его газификации.
При ограничении максимальной температуры в газификаторе в разрыв слоя топлива вводят воду при помощи средств 10, размещенных на внутренней поверхности корпуса газификатора 1 и/или на элементах конструкции средства 7 выравнивания значений расхода топлива по поперечному сечению рабочей зоны газификатора (подводящие трубопроводы не показаны). Это техническое решение позволяет получить дополнительные преимущества в оперативности управления температурным режимом процесса и его энергетической эффективности. Оперативность управления температурным режимом повышается за счет того, что, кроме эндотермичности реакции паров воды с горячим коксом, эффективному подавлению нежелательных разогревов способствует также и большая теплота испарения воды. Одновременно это позволяет увеличить и энергетическую эффективность процесса за счет замены части или всего водяного пара, вводимого в газифицирующий агент, водой, подаваемой в слой топлива. Тем самым энергозатратный подвод тепла от внешнего источника на парообразование подаваемой в газификатор воды заменяется отбором излишков тепла из высокотемпературных областей окисления кокса, что и увеличивает эффективность преобразования теплоты сгорания исходного топлива в теплоту сгорания генераторного газа.
Как было показано выше в описании заявляемого устройства, конструктивно задача ввода воды в слой топлива ниже средства выравнивания 7 может быть решена различными способами.
Одним из способов может быть подача воды через элементы конструкции самого средства 7. С одной стороны, это техническое решение усложняет конструкцию средства 7, но, с другой стороны, это одновременно может обеспечить и охлаждение элементов его конструкции.
Наличие разрыва по всему поперечному сечению слоя топлива под средством 7 позволяет реализовать более простой способ подачи воды в газификатор. В стенке шахты газификатора под средством 7 устанавливают средства 10 для подачи воды, например форсунки, обеспечивающие возможность равномерной подачи воды по всему поперечному сечению рабочей зоны газификатора путем их соответствующего расположения и юстировки. При отсутствии разрыва слоя топлива вода не может быть подана в высокотемпературные области равномерно по рабочему сечению газификатора через форсунки, установленные в стенке шахты. Попадая на раскаленный твердый материал и испаряясь, вода будет интенсивно охлаждать его лишь непосредственно вблизи стенок шахты, не достигая расположенных глубже центральных областей рабочего сечения у ее оси.
Пары воды могут поступать в верхнюю часть слоя, расположенную выше средства 7, из двух источников, одним из которых является подаваемая в газификатор с помощью средств 10 вода, и другим – водяной пар, подаваемый в него в составе газифицирующего агента с помощью средств 5. Оба этих источника предназначены, главным образом, для управления температурным режимом процесса газификации кокса, образующегося при термической переработке топлива. Выше было показано, каким образом можно ограничивать максимальную температуру в газификаторе путем изменения количества паров воды в газифицирующем агенте. При подаче воды с помощью средств 10, алгоритм ограничения максимальной температуры в газификаторе можно построить, например, таким образом, что доля водяного пара, вводимого в состав газифицирующего агента, устанавливает общий уровень максимальных температур в газификаторе, а подача воды с помощью средств 10 обеспечивает оперативное управление абсолютной величиной максимальной температуры в газификаторе для поддержания ее в заданных пределах путем соответствующего регулирования скорости подачи. Подачу воды в газификатор с помощью средств 10 увеличивают при превышении верхнего предела и, напротив, уменьшают при выходе температуры за нижний предел.
При установке достаточного количества температурных датчиков, обеспечивающих детальный контроль температурного поля, и при соответствующем управлении подачей воды через индивидуальные форсунки система управления может быть также настроена и на подавление локальных перегревов в областях, куда увеличение подачи воды можно производить «адресно» через ближайшую форсунку (форсунки). Это дает дополнительную возможность устранения неоднородностей в зоне максимальной температуры. Например, если в зоне максимальной температуры только с одной стороны рабочего сечения газификатора образуется область локального перегрева, то подачу воды можно увеличить через соответствующие форсунки только в те точки поверхности слоя топлива под средством 7, на которые проецируется эта область.
Как было указано выше, помимо значительного повышения управляемости температурным режимом процесса газификации подача воды в газификатор позволяет также поднять и энергетическую эффективность процесса. Это достигается путем снижения затрат энергии на выработку пара, вводимого в состав газифицирующего агента, часть которого в предлагаемом изобретении заменяется водой, подаваемой в газификатор с помощью средств 10. В ряде случаев реализации изобретения можно даже полностью отказаться от подачи пара в газификатор в составе газифицирующего агента, заменив его водой, подаваемой в газификатор с помощью средств 10. Решение о полном отказе от ввода пара в газифицирующий агент при газификации конкретного вида топлива может быть принято по результатам испытаний, которые зависят от ряда свойств газифицируемого топлива, таких как выход кокса, зольность и температура плавления золы.
Заявляемый способ газификации углеродсодержащих конденсированных топлив позволяет преодолеть недостаток известных технологий газификации в плотном слое, заключающийся в недостаточной управляемости температурным режимом процесса, что может приводить к плавлению золы, зашлаковыванию и остановке газификатора.
Предлагаемый способ позволяет также увеличить энергетическую эффективность выработки генераторного газа из конденсированных топлив за счет уменьшения затрат на производство пара или полного отказа от его подачи в газификатор в составе газифицирующего агента.
Изобретение обеспечивает метод и устройство, позволяющие эффективно перерабатывать в энергетический газ широкий спектр конденсированных топлив без внешнего подвода тепла.
Формула изобретения
1. Способ газификации углеродсодержащих конденсированных топлив в газификаторе шахтного типа с верхней загрузкой, в котором через слой топлива противоточно пропускают кислородсодержащий газифицирующий агент, поддерживают в слое топлива процесс его газификации, обеспечивают заданное положение зоны максимальной температуры в газификаторе, управляя скоростью перемещения топлива по газификатору, и/или расходом, и/или составом кислородсодержащего газифицирующего агента, ограничивают величину максимальной температуры в газификаторе заданными пределами, а также выводят из газификатора твердые и газообразные продукты переработки, отличающийся тем, что осуществляют выравнивание значений расхода топлива по поперечному сечению газификатора, ниже сечения, в котором осуществляют выравнивание значений расхода топлива, создают разрыв слоя топлива, а зону максимальной температуры удерживают в положении ниже указанного разрыва.
2. Способ газификации углеродсодержащих конденсированных топлив по п.1, отличающийся тем, что при ограничении максимальной температуры в газификаторе в разрыв слоя топлива вводят воду.
3. Способ газификации углеродсодержащих конденсированных топлив по п.2, отличающийся тем, что воду вводят непосредственно в точки поперечного сечения газификатора, соответствующие проекциям областей локальных перегревов на указанное поперечное сечение.
4. Устройство для газификации углеродсодержащих конденсированных топлив, содержащее газификатор шахтного типа с верхней загрузкой, снабженный средствами загрузки топлива в рабочую зону газификатора, средствами подачи кислородсодержащего газифицирующего агента, средствами вывода получаемого газа, средствами выгрузки твердых продуктов переработки из рабочей зоны газификатора, а также средствами контроля температур в рабочей зоне, отличающееся тем, что в устройство введено средство выравнивания значений расхода топлива по поперечному сечению рабочей зоны газификатора, выход которого расположен на расстоянии Lв=(0,2-0,75)Lрз от нижней границы рабочей зоны газификатора, где Lрз – длина рабочей зоны газификатора.
5. Устройство для газификации углеродсодержащих конденсированных топлив по п.4, отличающееся тем, что в стенках газификатора на расстоянии (0,7-0,98)Lв от нижней границы его рабочей зоны установлены средства ввода воды в топливо.
6. Устройство для газификации углеродсодержащих конденсированных топлив по п.4 или 5, отличающееся тем, что средство выравнивания значений расхода топлива по поперечному сечению рабочей зоны газификатора снабжено средствами ввода воды в топливо.
РИСУНКИ
MM4A – Досрочное прекращение действия патента СССР или патента Российской Федерации на изобретение из-за неуплаты в установленный срок пошлины за поддержание патента в силе
Дата прекращения действия патента: 03.07.2009
Извещение опубликовано: 20.05.2010 БИ: 14/2010
NF4A – Восстановление действия патента СССР или патента Российской Федерации на изобретение
Дата, с которой действие патента восстановлено: 27.05.2010
Извещение опубликовано: 27.05.2010 БИ: 15/2010
|
|