Изобретения относятся к области литейного производства. Осуществляют разрушение отработанных литейных форм или стержней. Тугоплавкие частицы, полученные в результате разрушения, перемешивают с 0,1-3 мас.% частиц пуццолановой добавки и осуществляют термическую обработку смеси при температуре от 450 до 900°С. В качестве пуццолановой добавки используют вулканический пепел, пульверизованную топливную золу, зольную пыль, измельченный гранулированный доменный шлак, конденсированную тонкую кремнеземную пыль, аморфный диоксид кремния и прокаленный боксит. Достигается улучшение свойств регенерированной формовочной смеси. 2 н. и 13 з.п. ф-лы, 1 табл., 1 ил.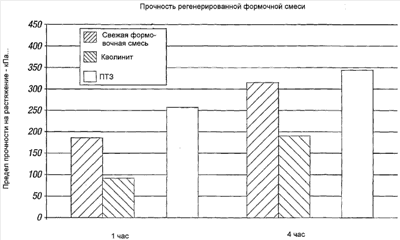
Данное изобретение относится к регенерации формовочных смесей, полученных из использованных литейных форм, которые изготавливали путем связывания формовочной смеси связующей фенольной смолой в водном щелочном растворе, отвержденной органическим сложным эфиром.
Существует растущая потребность в отправлении формовочных смесей, полученных из форм после литья, на рецикл. Потребность подпитывается не только стоимостью свежей формовочной смеси, но также и проблемами, связанными с утилизацией использованной формовочной смеси с нанесенным покрытием из смолы. В прошлом такой материал легко утилизировали на свалках, но недавно органы власти стали в большей мере проявлять сознательность в отношении охраны окружающей среды и на многих территориях появились строгие предписания, определяющие утилизацию таких материалов.
Один известный способ регенерации формовочной смеси включает истирание формовочной смеси, содержащей связующее, до разрушения агломератов на индивидуальные частицы. Несмотря на то, что способ истирания может обеспечить удаление под действием трения определенного количества смолы с частиц формовочной смеси, которые будут удаляться вместе с мелкими частицами, смола на поверхности частиц формовочной смеси остается, и характеристики освежения у формовочной смеси, регенерированной в результате истирания, уступают связующей способности для свежей формовочной смеси. В общем случае обычно используемые методики истирания делают возможным повторное использование вплоть до 85% формовочной смеси, содержащей связующую смолу, при этом остаток формовочной смеси отбрасывают.
Известные термические методики регенерации формовочной смеси после истирания включают нагревание формовочной смеси в псевдоожиженном слое до достаточно высокой температуры для эффективного удаления органической смолы и обеспечения низкого уровня выбросов из отходящего газа. Однако было обнаружено, что такой способ термической регенерации не является особенно успешным в случае формовочных смесей, содержащих связующее, отвержденное сложными эфирами, поскольку для зерен формовочной смеси наблюдается тенденция к агломерированию в установке для термической регенерации, что препятствует эффективному функционированию псевдоожиженного слоя при температурах, достаточно высоких для эффективного удаления связующего и обеспечения низкого уровня выбросов. При низких температурах удаление смолы происходит в недостаточной степени. Формовочная смесь, регенерированная при использовании известных термических методик, демонстрирует характеристики освежения, худшие в сопоставлении со свежей формовочной смесью и сопоставимые с формовочной смесью, регенерированной в результате истирания.
Представляется, что проблема агломерирования в системе термической регенерации обусловлена присутствием калия в системе связующей смолы, который в общем случае присутствует в виде гидроксида и соответствующих сложноэфирных солей калия. Постулируется, что во время термической обработки соединения калия разлагаются и/или расплавляются, что в результате приводит к агломерированию частиц формовочной смеси, при этом частицы связываются или слипаются друг с другом в такой степени, что ожижающий газ становится неспособен поддерживать состояние эффективного псевдоожиженного слоя.
Соединения калия можно было бы удалить в результате промывания формовочной смеси перед проведением термической обработки. Однако такое промывание значительно увеличило бы потребность в энергии для высушивания и термической обработки подвергнутой промыванию формовочной смеси, так что такая методика была бы нерентабельной.
Документ WO 94/05448 описывает способ, включающий термическую обработку регенерированной в результате истирания формовочной смеси, содержащей связующую фенольную смолу, отвержденную сложным эфиром, в котором перед термической обработкой регенерированную в результате истирания формовочную смесь вводят в контакт с добавкой, которая превращает соединения калия в форму, характеризующуюся температурой плавления, по меньшей мере, равной 600°С, и термическую обработку проводят при температуре, меньшей той, при которой получающееся в результате соединение калия будет плавиться.
Было обнаружено, что в результате превращения гидроксида и других солей калия в системе смолы, отвержденной сложным эфиром, в соединение калия, характеризующееся температурой плавления, превышающей 550°C, а предпочтительно превышающей 700°С, формовочную смесь можно будет подвергать термической обработке при достаточно высоких температурах для эффективного удаления нанесенного покрытия из смолы и обеспечения низкого уровня выбросов, но без агломерирования формовочной смеси. Кроме того, после термической обработки имеет место значительное уменьшение уровня содержания калия в формовочной смеси с нанесенным покрытием, и получающаяся в результате формовочная смесь демонстрирует характеристики освежения, превышающие соответствующие характеристики формовочной смеси, регенерированной в результате истирания, и зачастую сопоставимые с соответствующими характеристиками свежей формовочной смеси. Способ также делает возможным отправление на рецикл большего количества формовочной смеси в сопоставлении с обычно используемыми методиками.
Существует ряд соединений калия, характеризующихся температурой плавления, превышающей 550°С, включающих антимонид (812°С), метаборат (947°С), хлорид (776°С), хромат (975°С), фторид (880°С), иодид (723°С), молибдат (919°С), ортофосфат (1340°С), метафосфат (807°С), силикат (976°С) и сульфат (1069°С), бромид (730°С) и карбонат (891°С).
В соответствии с предпочтительным вариантом реализации добавка присутствует в виде водного раствора соединения, которое будет вступать в реакцию с гидроксидом калия с получением такого соединения калия. Растворы кислот или солей, подходящие для использования в качестве добавки, включают галогеноводородные кислоты, например HCl, HBr, HI, серную кислоту, борную кислоту и аммониевые соли таких кислот, такие как хлорид аммония.
Данный способ эффективен, но ему свойственны недостатки, заключающиеся в высокой степени коррозии компонентов установки для термической обработки, изготовленных из нержавеющей стали, и наличии трудностей, связанных с образованием очень тонкодисперсной пыли.
В документе WO 94/26439 описывают частицы тугоплавкой композиции, предназначенной для использования при изготовлении литейных форм и оболочковых форм, которая содержит смесь частиц тугоплавкого заполнителя, содержащего вымываемую щелочь в присутствии в качестве добавки к ней частиц активной глины, характеризующихся размером частиц, меньшим 0,5 мм.
Как утверждается, использование в композиции добавки в виде частиц активной глины оказывает действие, улучшающее величины прочности литейных форм и оболочковых форм, которые изготавливают при использовании композиции, в сопоставлении со случаем, когда в частицы тугоплавкого материала никакой добавки в виде частиц активной глины не вводят.
Частицы глины, которая может представлять собой глину, подвергнутую термической обработке, вступают в реакцию с солями щелочных металлов, которые присутствуют на поверхности тугоплавкого материала, так что при изготовлении литейных форм и оболочковых форм ионы щелочных металлов будут неспособны каким-либо существенным образом оказать неблагоприятное воздействие на последующую реакцию в используемой системе связующего при связывании частиц тугоплавкого материала друг с другом.
Примеры подходящих частиц глины включают каолины, каолины, подвергнутые термической обработке, смектиты, монтмориллониты, бентониты, вермикулиты, аттапульгиты, серпентины, глаукониты, иллиты, аллофан и имоголит. В числе данных материалов предпочтительными являются каолин и каолин, подвергнутый термической обработке.
Данному способу свойственен недостаток, заключающийся в том, что в подвергнутой обработке формовочной смеси остаются очень мелкодисперсные частицы глины, что в результате выражается в недостаточном удалении калия (или другого щелочного металла). На тугоплавкость и прочность формовочной смеси после освежения оказывается неблагоприятное влияние.
В документе US 6286580 описывается способ термической регенерации формовочной смеси, которую использовали для изготовления литейных форм или оболочковых форм и которая содержала связующее, использующее щелочную резольную фенолоформальдегидную смолу, включающий последовательные стадии:
(а) проведения истирания комков использованной и содержащей связующее формовочной смеси для разрушения комков до индивидуальных зерен формовочной смеси,
(b) добавления к зернам формовочной смеси углевода в количестве в диапазоне от 0,25% до 5,0% (масс.) при расчете на массу использованной формовочной смеси и
(с) проведения для формовочной смеси термической обработки в аппарате для термической регенерации таким образом, чтобы углевод был удален из формовочной смеси в результате сгорания.
Углевод предпочтительно представляет собой растворимый в воде углевод, поскольку углевод предпочтительно добавлять к формовочной смеси в виде раствора, для того чтобы тщательно диспергировать углевод в массе формовочной смеси. Углевод может представлять собой, например, моносахарид, такой как глюкоза, манноза, галактоза или фруктоза, или дисахарид, такой как сахароза, мальтоза или лактоза. Углевод также может являться производным, таким как многоатомный спирт.Примеры подходящих многоатомных спиртов включают этиленгликоль, который можно рассматривать в качестве производного наиболее простого моносахаридного гликольальдегида (СН2ОН·СНО), глицерин, который является производным моносахаридных глицеральдегидов (СН2ОН·СНОН·СНО), пентаэритрит, который является производным альдотетрозы, пятиатомные спирты, такие как ксилит, который является производным альдопентозы ксилозы, и шестиатомные спирты, такие как маннит, который является производным альдогексозы маннозы, или сорбит, который является производным любой одной из альдогексоз – глюкозы и гулозы. Углевод также может являться производным, таким как сахарная кислота, например глюконовая кислота. Также могут быть использованы и полисахариды или их производные. Примерами подходящего производного полисахарида являются гидролизаты крахмала, то есть крахмальные патоки или декстрины. Однако некоторые полисахариды и производные полисахаридов, например крахмал, простые эфиры целлюлозы и натрий-карбоксиметилцеллюлоза, являются менее желательными, поскольку их непросто растворить в воде и они могут стать причиной увеличения вязкости воды, что таким образом сделает их диспергирование в формовочной смеси более трудным. Также возможно использование и неочищенного углеводного материала, такого как мелассы.
Углеводная добавка предотвращает сплавление зерен формовочной смеси, и это в особенности выгодно тогда, когда термическую обработку проводят в установке с псевдоожиженным слоем. Поскольку добавка является органической, она полностью сгорает в ходе реализации способа термической обработки и не оставляет никаких нежелательных остатков, которые могли бы неблагоприятным образом сказаться на характеристиках освежения тогда, когда регенерированную формовочную смесь будут использовать повторно. Предпочтительные углеводные добавки являются растворимыми в воде, так что их можно будет легко диспергировать в формовочной смеси в виде водного раствора.
Известно, что данный способ работает, поскольку углевод предотвращает оплавление формовочной смеси и дает возможность легкоплавким щелочным соединениям вступать в реакцию с аморфным диоксидом кремния на поверхности зерна формовочной смеси. К тому времени, когда углеводы будут выжжены в термическом способе, соединения калия уже вступят в реакцию с формовочной смесью, и никаких легкоплавких соединений не останется. Однако данный способ оказался неудачным, поскольку удаление калия практически равно нулю, и уровень содержания калия в регенерированной формовочной смеси становился чрезмерно высоким при интенсивном повторном использовании. Величины прочности после освежения и тугоплавкость ухудшаются.
В настоящее время обнаружено, что при регенерации формовочной смеси могут быть использованы пуццолановые добавки.
В соответствии с настоящим изобретением предлагается способ получения частиц тугоплавкой композиции, предназначенной для использования при изготовлении литейных форм и оболочковых форм из отработанных литейных форм или оболочковых форм, полученных из тугоплавкого материала и связующей фенольной смолы, отвержденной сложным эфиром, при этом способ включает стадии разрушения отработанных литейных форм или оболочковых форм, перемешивания материала, получающегося в результате разрушения, с частицами пуццолановой добавки и проведения для смеси термической обработки при температуре в диапазоне от 450 до 900°С.
Пуццолановые добавки, подходящие для использования в изобретении, включают природные пуццоланы, встречающиеся в вулканическом пепле и в вулканическом туфе, и синтетические пуццоланы, такие как пульверизованная топливная зола, зольная пыль, измельченный гранулированный доменный шлак, конденсированная тонкая кремнеземная пыль, аморфный диоксид кремния и прокаленный боксит.
Обычной характеристикой пуццолановых добавок является уровень содержания в них реакционноспособного SiO2. В прошлом реакционноспособный SiO2 использовали для получения цементирующего материала, который является основой римского бетона, в результате проведения реакции с гидроксидом кальция при температуре окружающей среды с получением гидратированных силикатов кальция. Однако пуццолановые добавки также способны вступать в реакцию с гидроксидами и соединениями и других щелочных и щелочноземельных металлов. Реакционная способность данных пуццолановых добавок при температуре окружающей среды в основном относительно невелика, но при нагревании до обычных температур термической регенерации в диапазоне от 450 до 900°С реакция становится довольно быстрой. Пуццолановая добавка вступает в реакцию с щелочными остатками в регенерированной формовочной смеси быстрее, чем сама формовочная смесь, так что реакционноспособная часть остаточного щелочного материала вступит в реакцию с пуццолановой добавкой, а не с поверхностью формовочной смеси. После этого для соединений калия, остающихся на поверхности формовочной смеси, данная реакция предотвратит образование легкоплавких соединений (например, оксида калия) и протекание реакции со структурой аморфного диоксида кремния, присутствующего на поверхности некоторых зерен формовочной смеси на основе диоксида кремния, или диффундирование в данную структуру.
Пуццолановую добавку используют в форме частиц. В общем случае размер частиц добавки доходит вплоть до 0,5 мм. Несмотря на то, что очень мелкодисперсный материал работает точно так же хорошо, как и материал более грубого помола, с первым работать труднее, и предпочтительно основная часть частиц имеет размер, превышающий 45 мкм.
Пуццолановую добавку смешивают с частицами, полученными при разрушении отработанных литейных форм и оболочковых форм. Добавку можно вводить в виде твердой фазы, но удобно ее вводить в виде суспензии в воде, например, в виде взвеси, характеризующейся уровнем содержания твердой фазы, находящимся в диапазоне от 20 до 50% (масс.), предпочтительно равным приблизительно 40% (масс.). Для облегчения суспендирования частиц могут быть использованы обычные диспергаторы. В общем случае пуццолановую добавку добавляют в количестве в диапазоне от 0,1 до 3% (масс.) в расчете на массу твердой фазы, предпочтительно от 0,3 до 1,3% (масс.) в расчете на массу твердой фазы. Обычно пуццолановую добавку добавляют в виде взвеси, смешанной с гранулированным регенерируемым песком в обычно используемом в литейном производстве смесителе шнекового типа непрерывного действия, расположенном для проведения выпуска непосредственно в установку для термической регенерации.
Термическую обработку проводят при температуре в диапазоне от 400 до 900°С, предпочтительно от 450 до 750°С, в общем случае в течение периода времени продолжительностью от 20 минут до 12 часов, предпочтительно от 30 минут до 2 часов. Предпочтительная установка для термической обработки включает псевдоожиженный слой, хотя возможно использование и других установок для термической обработки. Для установок с псевдоожиженным слоем характерно протекание спекания (оплавления) формовочной смеси вследствие плавления соединений калия, и значение данного недостатка существенно уменьшается в результате использования пуццолановой добавки.
Способ в общем случае включает стадию удаления пыли и/или мелких частиц во время и/или после термической обработки. Удаление мелких частиц будет приводить к удалению как мелких частиц формовочной смеси, так и пуццолановой добавки и продуктов ее реакции. Желательно удалять любые количества пуццолановой добавки, поскольку она будет оказывать негативное воздействие на прочность после освежения. Удаление остаточной пуццолановой добавки, например, пульверизованной топливной золы, вместе с удалением мелких частиц протекает согласно наблюдениям легче, чем удаление добавок в виде глины, поскольку в ходе термической обработки статическое притяжение формируется в меньшей степени.
Изобретению свойственны преимущества, заключающиеся в том, что подходящие пуццолановые добавки являются относительно дешевыми, поскольку их получают из материала отходов, и они коммерчески доступны с подходящим гранулометрическим составом. Предпочтительным материалом является пульверизованная топливная зола, соответствующая документу BS3892 Part 1. Экспериментальная работа показала, что степень удаления калия из формовочной смеси при использовании способа изобретения является улучшенной в сопоставлении со случаем добавок в виде глины. Несмотря на то, что удаление калия происходит в меньшей степени в сопоставлении с тем, что получают при использовании добавок в виде кислот и кислых солей, в данном случае технологические недостатки последнего способа отсутствуют и становится возможной обработка формовочной смеси без оплавления или спекания формовочной смеси.
Подвергнутую обработке формовочную смесь, получающуюся в результате по способу изобретения, можно использовать для получения литейных форм и оболочковых форм в результате смешивания ее с подходящим жидким отверждаемым связующим, предпочтительно фенольной смолой, отверждаемой сложным эфиром. Связующее, разумеется, используют в количестве в диапазоне от 0,5 до 5% (масс.) в расчете на массу частиц тугоплавкой композиции. Получающуюся в результате композицию формуют, придавая ей желательные профиль или форму, и отверждают.Сложноэфирный отвердитель можно вводить в смесь в жидкой или твердой форме, или через полученную композицию можно пропускать газообразный сложный эфир, вызывающий отверждение связующего. Предпочтительная система связующего включает фенольную смолу NOVASET® 730 и отвердитель NOVASET® NH Medium (этиленгликольдиацетат), коммерчески доступные в компании Ashland UK Limited.
Изобретение будет проиллюстрировано в следующем далее примере.
Пример
Испытания проводили в лабораторных масштабах с использованием псевдоожиженного слоя с электрическим обогревом при температуре обработки 600°С. В печи с псевдоожиженным слоем для термической обработки в течение периода времени продолжительностью приблизительно 2 часа проводили обработку 10 кг регенерированной в результате истирания формовочной смеси, полученной с коммерческого литейного производства, до тех пор, пока не достигали температуры 600°С, которую выдерживали в течение 20 минут. После этого для подвергнутой термической регенерации формовочной смеси проводили охлаждение, просеивание через ячейки 1 мм и удаление пыли при использовании простого способа перемешивания/извлечения. Предполагается, что данное удаление пыли будет приводить к удалению основной части пыли, не прилипшей к формовочной смеси. Подвергнутую обработке формовочную смесь после этого смешивали со свежей формовочной смесью с соотношением 95:5, а после этого смешивали с 0,8% смолы NOVASET® 730 и 25% отвердителя NH Medium. Формовочной смеси после освежения давали возможность отвердиться, а после этого ее разрушали приблизительно до размера зерна и регенерировали еще раз в псевдоожиженном слое с электрическим обогревом. Данную методику повторяли вплоть до 10 раз.
Формовочную смесь, получающуюся в результате реализации данных методик, также подвергали испытанию, проводя трамбование образцов полученных смесей для испытаний с определением предела прочности при растяжении. Смесь в каждом случае формовали в виде нескольких образцов для испытаний на растяжение (известных под наименованием «собачьи кости») и давали ей возможность отвердиться. Измерения предела прочности при растяжении проводили, нагружая образцы при использовании тензометра Nene и измеряя нагрузку тогда, когда образцы разрушались на два куска. Образцы подвергали испытанию по истечении 1 часа и 4 часов по окончании смешения.
При использовании описанной методики сравнивали три добавки:
1. Пульверизованная топливная зола (ПТЗ), соответствующая документу BS3892 Part 1, добавляемая в виде взвеси с уровнем содержания твердой фазы 40% в количестве 1,5% (масс.) в расчете на массу формовочной смеси.
2. Суспензия подвергнутой термической обработке каолинитовой глины, полученная в соответствии с положениями патента WO 94/26439. Взвесь получали с уровнем содержания твердой фазы 30% и ее добавляли в количестве 1,5% (масс.) в расчете на массу формовочной смеси.
Результаты представлены в следующей далее таблице и на прилагаемом чертеже, который демонстрирует графическое представление прочности регенерированной формовочной смеси по истечении 1 часа и 4 часов после формования.
Таблица |
Добавка |
Прочности регенерированных формовочных смесей |
|
1 час (кПа) |
4 час (кПа) |
Свежая формовочная смесь |
186 |
316 |
ПТЗ по завершении 6 отправлений на рецикл |
256 |
344 |
Каолинит, 4 отправления на рецикл |
48 |
98 |
Каолинит, 6 отправлений на рецикл |
Отсутствие прочности |
Отсутствие прочности |
Данные результаты свидетельствуют о том, что ПТЗ изобретения приводит к получению результатов, превосходящих результаты для добавки в виде глины, в особенности тогда, когда удаление пыли протекает неэффективно.
1. Способ получения частиц тугоплавкой композиции из отработанных литейных форм или стержней, полученных из тугоплавкого материала и связующей фенольной смолы, отвержденной сложным эфиром, для использования при изготовлении литейных форм и стержней, включающий разрушение отработанных литейных форм или стержней, перемешивание частиц, полученных в результате разрушения, с частицами пуццолановой добавки и термическую обработку полученной смеси при температуре от 450 до 900°С.
2. Способ по п.1, в котором пуццолановую добавку выбирают из группы, состоящей из вулканического пепла, пульверизованной топливной золы, зольной пыли, измельченного гранулированного доменного шлака, конденсированной тонкой кремнеземной пыли, аморфного диоксида кремния и прокаленного боксита.
3. Способ по п.1, в котором в качестве пуццолановой добавки используют пульверизованную топливную золу.
4. Способ по любому из пп.1-3, в котором используют пуццолановую добавку, имеющую размер частиц меньше 0,5 мм.
5. Способ по п.1, в котором количество пуццолановой добавки составляет от 0,1 до 3 мас.% в расчете на массу твердой фазы.
6. Способ по п.5, в котором количество пуццолановой добавки составляет от 0,3 до 1,3 мас.% в расчете на массу твердой фазы.
7. Способ по п.1, в котором пуццолановую добавку добавляют к отработанной формовочной смеси в виде взвеси в воде.
8. Способ по п.7, в котором взвесь содержит от 20 до 50 мас.% твердой фазы.
9. Способ по п.1, в котором термическую обработку смеси проводят при температуре от 450 до 750°С.
10. Способ по п.1, в котором термическую обработку смеси проводят в течение периода времени от 20 мин до 12 ч.
11. Способ по п.10, в котором термическую обработку смеси проводят в течение периода времени от 30 мин до 2 ч.
12. Способ по п.1, в котором термическую обработку смеси проводят в псевдоожиженном слое.
13. Способ по п.1, в котором во время и/или после термической обработки смеси осуществляют удаление пыли и/или мелких частиц.
14. Способ изготовления литейной формы или литейного стержня, включающий разрушение отработанных литейных форм или стержней, полученных из тугоплавкого материала и связующей фенольной смолы, отвержденной сложным эфиром, перемешивание частиц, полученных в результате разрушения, с частицами пуццолановой добавки и термическую обработку полученной смеси при температуре от 450 до 900°С с получением частиц тугоплавкой композиции, получение формовочной смеси путем перемешивания частиц полученной тугоплавкой композиции с жидким отверждаемым связующим в количестве от 0,5 до 5 мас.% в расчете на массу частиц тугоплавкой композиции, формование композиции формовочной смеси с приданием ей желательных профиля или формы и отверждение связующего сложным эфиром.
15. Способ по п.14, в котором отверждение связующего проводят путем обработки полученной формы газообразным сложным эфиром.