(21), (22) Заявка: 2006101164/02, 18.01.2006
(24) Дата начала отсчета срока действия патента:
18.01.2006
(43) Дата публикации заявки: 27.07.2007
(46) Опубликовано: 10.02.2009
(56) Список документов, цитированных в отчете о поиске:
RU 2156811 C1, 20.09.2000. US 5466278 A, 14.11.1995. US 4913734 A, 03.04.1990. RU 2182603 C2, 20.05.2002. US 5480474 A, 02.01.1996. US 5431710 A, 11.07.1995. КУРУНОВ И.Ф. и др. Состояние и перспективы бездоменной металлургии железа. – М.: ОАО «Черметииформация», 2002, с.с.129-138.
Адрес для переписки:
113461, Москва, ул. Каховка, 31, корп.1, кв.1, А.Б.Усачеву
|
(72) Автор(ы):
Буровой Исаак Абрамович (RU), Усачев Александр Борисович (RU)
(73) Патентообладатель(и):
Буровой Исаак Абрамович (RU), Усачев Александр Борисович (RU)
|
(54) СПОСОБ ПРЯМОГО ПРОИЗВОДСТВА СТАЛИ ИЗ ЖЕЛЕЗОСОДЕРЖАЩИХ МАТЕРИАЛОВ
(57) Реферат:
Изобретение относится к области металлургии и предназначено для прямого непрерывного производства стали из неокускованной руды, железорудных концентратов, железосодержащих отходов. Изобретение обеспечивает прямое получение стали с содержанием углерода 0,2-2,0% и допустимым содержанием примесей в едином реакционном пространстве. Единое реакционное пространство образуют плавильно-восстановительное подпространство со слоем жидкого шлака, рафинировочное подпространство со слоем рафинируемого металла, расположенным под слоем жидкого шлака, и промежуточный слой “шлак – рафинируемый металл – газ” между указанными слоями. Железосодержащие материалы, включая легирующие и разжижающие добавки, кислородсодержащее дутье и твердое углеродистое топливо непрерывно подают в слой жидкого шлака. Обеспечение в промежуточном слое турбулентно-диффузионного переноса оксидов железа и капель восстановленного металла, содержащихся в слое шлака, в промежуточный слой и слой рафинируемого металла. При этом обеспечивают взаимодействие кислорода, выделяющегося при распаде оксидов железа, и подаваемого извне потока кислорода и/или кислородсодержащего газа и/или их смеси с углеродом и одновременное протекание процесса рафинирования в промежуточном и рафинировочном слоях. 13 з.п. ф-лы, 3 ил.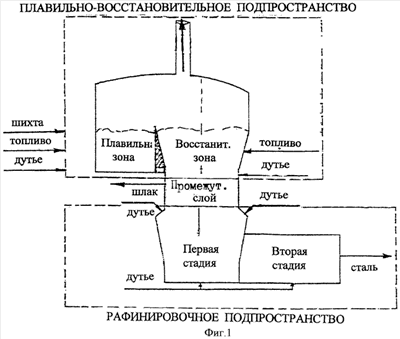
Настоящее изобретение относится к области металлургии, в частности к черной металлургии, и предназначено для прямого непрерывного производства стали из неокускованной железной руды, железорудных концентратов, железосодержащих отходов и других железосодержащих материалов.
Производство стали обычно основано на следующих двух основных операционных стадиях:
восстановление железа из железосодержащих материалов и получение железоуглеродистого продукта – чугуна с относительно высоким содержанием углерода;
рафинирование полученного железоуглеродистого продукта – чугуна с целью уменьшения содержания в нем углерода и примесей до заданных пределов и получения стали.
Осуществление современной технологии производства стали в виде двух последовательных операций (стадий) на двух самостоятельных металлургических агрегатах имеет еще один весьма существенный (экономический) недостаток – практически из-за использования двух независимых агрегатов резко увеличивается себестоимость производства стали.
Известен способ жидкофазного восстановления металла из барботируемого расплава, содержащего окислы железа в установке «Ромелт», где восстановленный металл поступает в независимые агрегаты на рафинирование, например в конвертеры, электропечи или другие устройства (1).
Такая стыковка печи Romelt с агрегатами для рафинирования несколько сокращает, но не исключает необходимость дополнительного подогрева металла; операция рафинирования проводится в полунепрерывном режиме, требует самостоятельного обслуживания и, соответственно, затрат.
Наиболее близким по технической сущности и достигаемому результату является способ производства стали в агрегате “желобчатого” типа для восстановления Fe и рафинирования полученного чугуна от углерода. В начале желоба устанавливается агрегат для восстановления Fe; далее, продвигаясь по желобу, расплав Fe попадает в агрегат для рафинирования от углерода. Таким образом, по мнению авторов, в агрегате осуществляется “прямое” получение стали из железосодержащего сырья (2).
Однако фактически этот агрегат отличается только способом транспортировки металла из зоны восстановления в зону рафинирования; с точки зрения экономической – это два последовательно работающих независимых агрегата с самостоятельными затратами, которые просто суммируются.
Задачей предложенного изобретения является создание новой технологии рафинирования чугуна, которую можно будет совместить с элементами современной технологии восстановления в едином реакционном пространстве и которая позволит получать в этом пространстве прямо сталь с содержанием углерода в пределах 0,2-2,0% и допустимым содержанием примесей.
Для осуществления процесса прямого производства стали предлагается структура “единого” реакционного пространства, в котором рафинировочное (Р) подпространство располагается по вертикали под плавильно-восстановительным (ПВ) подпространством.
Обмен потоками капель восстановленного металла, шлака и газа между обоими подпространствами проводится через располагаемый между ними промежуточный “шлако-газо-металлический” слой.
Заявленный способ прямого непрерывного производства стали из железосодержащих материалов, находящихся в виде слоя жидкого рафинируемого металла и слоя жидкого шлака, включает следующие стадии:
– образование единого реакционного пространства плавильно-восстановительным подпространством со слоем жидкого шлака, рафинировочным подпространством со слоем рафинируемого металла, расположенным под слоем жидкого шлака, содержащим перерабатываемые железосодержащие материалы и капли восстановленного металла, и промежуточным слоем “шлак – рафинируемый металл – газ” между указанными слоями,
– непрерывную подачу в слой жидкого шлака железосодержащих материалов, включая легирующие и разжижающие добавки, кислородсодержащего дутья и твердого углеродистого топлива,
– непрерывное удаление полученной при рафинировании стали, шлака и отходящих газов из реакционного пространства,
– подачу кислорода и/или кислородсодержащего газа или инертного газа и/или их смеси в промежуточный слой и слой рафинируемого металла,
– обеспечение в промежуточном слое турбулентно-диффузионного переноса оксидов железа и капель восстановленного металла, содержащихся в слое шлака, в промежуточный слой и слой рафинируемого металла с обеспечением при этом взаимодействия кислорода, выделяющегося при распаде оксидов железа, и подаваемого извне потока кислорода и/или кислородсодержащего газа и/или их смеси, с углеродом, и обеспечением одновременного протекания процесса рафинирования в промежуточном и рафинировочном слоях;
– интенсификацию переноса капель восстановленного металла и оксидов железа из шлакового слоя и интенсификацию протекания процесса рафинирования выделяющейся в процессе рафинирования окисью углерода,
– импульсное или непрерывное управление подачей загружаемого твердого углеродистого топлива, и/или подачей кислорода и/или кислородсодержащего газа и/или инертного газа и/или их смеси
– и управление потоком перерабатываемой шихты,
с обеспечением стабилизации технологического режима подачей указанных выше управляющих компонентов, необходимых для осуществления процесса производства стали в соответствии с заданным регламентом по температуре процесса, содержанию углерода, кислорода и примесей в производимой стали, содержанию оксидов железа и твердого углеродистого топлива в шлаке.
Слои указанного жидкого рафинируемого металла и шлака образованы бескоксовым восстановлением железа и некоторых примесей из перерабатываемых железосодержащих материалов, выбранных из группы, включающей, в частности, измельченные железосодержащие руды, железорудные концентраты, железосодержащие отходы, железосодержащий лом.
Рафинирование включает обезуглероживание жидкого металла и удаление примесей.
Бескоксовое восстановление осуществляют в образованном едином реакционном пространстве.
Для интенсификации процесса рафинирования возбуждают колебания в рафинируемом слое металла, например, с помощью импульсных прерываний подачи твердого топлива с продолжительностью импульсов (0,01-0,5) часа и амплитудой (0,1-0,7) от его расхода.
Заданное содержание кислорода в рафинируемом металле обеспечивают кислородом оксидов железа, а в случае недостаточного его количества – дополнительным дутьем путем верхней и/или комбинированной продувки через боковые и/или донные и/или вертикальные фурмы.
После достижения заданного содержания углерода и примесей в рафинировочном слое подача кислорода дополнительными фурмами осуществляется в количестве, достаточном для окисления углерода и примесей до заданного содержания в потоке металла, поступающего с каплями из плавильно-восстановительного подпространства.
Перенос оксидов железа и капель восстановленного металла из шлакового слоя в промежуточный слой “шлак – рафинируемый металл – газ” и из этого слоя в слой рафинируемого металла обеспечивают кислородсодержащим дутьем и реакционными газами, поступающими из рафинировочного слоя посредством барботажа шлакового слоя, турбулентной диффузией и изменениями межфазной поверхности промежуточного слоя, барботажем рафинируемого расплава и при необходимости подачей дополнительными боковыми, донными или вертикальными фурмами кислородсодержащего дутья и/или инертного газа и/или их смеси.
Осуществляют управление процессом по содержанию углерода, кислорода и примесей в стали, содержанию оксидов железа и углерода в шлаке, достигающем промежуточного слоя “шлак – рафинируемый металл – газ”, а также температурой процесса.
Содержание окислов железа в шлаке обеспечивают в пределах 0,1-15%.
Содержание кислорода, углерода и примесей в стали, углерода и оксидов железа в шлаке на выходе из реакционного пространства, также содержания СО и CO2 в отходящих газах определяют дискретно или непрерывно.
Стадия управления включает регулирование состава и количества подаваемого железосодержащего материала, твердого углеродистого топлива и легирующих и разжижающих добавок, при этом все твердое углеродистое топливо подают в барботирующий шлаковый слой сверху.
Управление включает регулирование состава и количества подаваемого железоуглеродистого материала, твердого углеродистого топлива и легирующих и разжижающих добавок, при этом перед подачей твердого углеродистого топлива мелкие его фракции отсеивают от основного потока и подают через специальные фурмы в потоке инертного газа.
Для достижения требуемого содержания углерода и примесей в стали, реакционное подпространство рафинировочного слоя разделено, по меньшей мере, на две последовательно действующие зоны.
На фиг.1 приведена предлагаемая структура реакционного пространства устройства для прямого производства стали.
На фиг.2 представлена печь для прямого производства стали (поперечный разрез).
На фиг.3 представлена печь для прямого производства стали (продольный разрез).
В верхнем ПВ-подпространстве реакционного пространства проводятся операции сжигания твердого топлива, плавление шихты и восстановление в барботирующем шлаковом расплаве железа и примесей для получения промежуточного продукта – чугуна; ПВ-подпространство при необходимости, в зависимости от перерабатываемого сырья, может быть разделено перегородкой на две операционные зоны – плавильную и восстановительную. Например, такая необходимость возникает при переработке измельченной (100% – 20 мм) железосодержащей руды, лома (скрапа) или других немелкозернистых отходов. Над барботирующим шлаком ПВ-подпространство имеет зону дожигания выделяющихся газов при плавке сырья и восстановлении железа, которые далее поступают в системы утилизации тепла и экологической очистки отходящих газов перед выбросом в атмосферу.
В средней зоне, в интенсивно перемешиваемом промежуточном слое “шлак-газ-металл”, продолжается процесс восстановления, но благодаря достаточно высокой концентрации металлической фазы и интенсивному перемешиванию одновременно начинается активное взаимодействие поступающих из ПВ-подпространства капель полученного промежуточного продукта (чугуна), невосстановленной FeO шлака и кислорода, а также перенос этих веществ в Р-подпространство. Из Р-подпространства проходит обратный перенос потока образующихся при рафинировании газов, в основном содержащих окись углерода F(CO), в ПВ-подпространство для использования при восстановлении перерабатываемых оксидов железа.
Промежуточный слой выполняет фактически функции положительной обратной связи для нижней зоны – Р-подпространства, так как интенсивность перемешивания в промежуточном слое, зависящая в основном от F(CO), определяет во многом подачу кислорода на рафинирование и интенсивность протекания этого процесса.
Из средней зоны металлическая фаза поступает на рафинирование, а шлаковая эмульсия, содержащая восстановленный металл, отводится в отстойную зону, откуда, после разделения, шлак выводится из системы, а оседающий металл возвращается в нижний слой рафинируемого металла.
В нижней зоне поступивший промежуточный продукт рафинируется и доводится по техническим характеристикам до заданных требований.
Процесс рафинирования может проводиться в одну стадию, в нижнем рафинировочном слое, непосредственно взаимодействующем с промежуточным слоем и верхним слоем.
При необходимости возможно двухстадийное рафинирование со сменой шлака. Первая предварительная стадия – обескремнивание, десульфурация, дефосфорация и частичное обезуглероживание, вторая стадия – продолжение рафинирования и предварительная доводка. В случае необходимости проводят внепечную обработку для окончательной доводки стали до соблюдения регламента.
На фиг.2 представлена схема реализации способа в шахтно-ванной печи. В комплекс печи входят питатели для загрузки через патрубок 14 железосодержащего материала 1, легирующих и разжижающих добавок, твердого углеродистого топлива 2 в плавильное пространство верхней зоны, фурмы 15, находящиеся на высоте Н3 для подачи кислорода или кислородсодержащего газа 3 в зону дожигания 9, фурмы 16, находящиеся на высоте Н2 для подачи в верхнюю плавильно-восстановительную зону кислородсодержащего газа 3 или специальные фурмы 16′ для подачи отсеяных мелких фракций твердого углеродистого топлива 38 в потоке инертного газа 10 при раздельной подаче мелких и крупных фракций, дополнительных фурм 17 на высоте Н4 для подачи в промежуточный слой “шлак – рафинируемый металл – газ” кислорода, кислородсодержащего и/или инертного газа 4 (с целью увеличения переноса в этот слой окислов железа и из этого слоя в рафинировочное подпространство кислорода, подачи реагентов и интенсификации процесса рафинирования), донные фурмы 17′ для интенсификации перемешивания рафинируемого металла и подачи кислородсодержащего и/или инертного газа 5 в нижнюю зону рафинирования. Донные фурмы 17′ могут использоваться для подачи реагентов.
Емкость для рафинирования 11 с подиной 12 имеет канал 22 (фиг.3) для выпуска стали, выполненный в стенке емкости для рафинирования и канал 23, расположенный с противоположной стороны и предназначенный для выведения шлака и уносимого с ним металла в отстойную зону 21 (после чего шлак удаляют через сифонное устройство, а металл возвращается в рафинировочное подпространство. Далее металл поступает через второе сифонное устройство на агрегаты внепечной обработки получаемой стали для доведения его состава до соответствия заданному регламенту).
Вывод технологических газов из шахты производится через газоход 24 (фиг.3)
Емкость для рафинирования и шахта могут иметь в горизонтальном сечении круглую, эллипсоидную или прямоугольную форму; все фурмы 15, 16 и 17 установлены на соответствующих уровнях боковых стен шахты 13 и емкости 11. Донные фурмы 17′ установлены по площади подины 12 на некотором расстоянии друг от друга.
С целью снижения расхода огнеупорных материалов и повышения длительности межремонтных компаний печи, часть шахты печи, а также стены и дно емкости для рафинирования целесообразно охлаждать. При этом на охлаждаемых поверхностях шахты устанавливаются кессоны с водяным охлаждением и на их внутренних стенах образуется шлаковый гарнисаж, который способствует уменьшению тепловых потерь.
При производстве стали в процессе рафинирования металл может кипеть в нижней зоне. Поэтому кессоны, применяемые для защиты огнеупорных стен на уровне шлака, не могут быть использованы для защиты стен кипящей металлической ванны.
Гарнисаж, образующийся на стенах плит с тепловыми трубами, заполненными расплавленным высокотемпературным наполнителем, принят в данной конструкции для защиты огнеупорной кладки емкости 11 и подины 12.
Здесь надо заметить, что тепловые трубы решают только задачу уменьшения износа футеровки; из-за того, что металл при рафинировании будет кипеть; рассчитывать на длительную стойкость огнеупорной футеровки без предлагаемой специальной защиты в виде металлического гарнисажа не приходится.
В верхнюю зону непрерывно подаются перерабатываемые железосодержащие материалы, требуемые компоненты шлака, твердое углеродистое топливо и кислородсодержащий газ. Кислород поступающего газа обеспечивает сжигание части топлива с выделением тепла, которое расходуется на плавление подаваемых твердых материалов и поддержание заданного теплового режима. Остальная часть топлива расходуется на восстановление содержащихся в загружаемых железосодержащих материалах окислов металлов и образование жидких продуктов плавки – шлака и железоуглеродистого промежуточного продукта.
Рассматриваются две схемы подачи твердого углеродистого топлива. Одна – с загрузкой всего топлива в верхнюю зону сверху и вторая – при которой мелкие фракции отсеиваются и вдуваются потоком газа на нижней границе верхней зоны, а остальная часть, как было описано выше, загружается в верхнюю зону сверху.
Процессы плавления перерабатываемой шихты и восстановления могут быть в ПВ-подпространстве отделены друг от друга перегородкой. В этом случае соответственно разделяются потоки подаваемого топлива (восстановителя) и кислородсодержащего газа. При этом мелкие фракции углеродистого топлива преимущественно используются для плавления, а крупные – для восстановления.
В верхней зоне подаваемые потоки кислородосодержащего газа обеспечивают барботаж находящегося там расплава для интенсификации процессов тепломассообмена при плавлении и восстановлении.
Расплав поступает далее в промежуточный слой, а технологические газы, образовавшиеся при сжигании топлива и восстановлении, направляются в зону дожигания, расположенную в пределах верхней зоны непосредственно над барботирующим расплавом.
Технологический режим верхней зоны определяет степень восстановления окислов железа и примесей, а также содержание углерода в шлаке, достигающем промежуточного эмульсионного слоя.
В средней зоне, в пределах слоя, осуществляется непрерывное интенсивное турбулентно-диффузионное перемешивание и перенос указанных выше продуктов. Интенсивность переноса зависит от потока капель железосодержащего промежуточного продукта и потока шлака, а также от поступающих из зоны рафинирования отходящих газов и от потоков дополнительно подаваемого кислорода и/или кислородсодержащего газа и/или инертного газа через боковые и/или донные фурмы.
В нижней зоне эффективность рафинирования железоуглеродистого промежуточного продукта и получение заданного содержания углерода и примесей в стали практически зависят от выбранной структуры Р-подпространства и организации технологического процесса во всем реакционном пространстве, так как достаточно большое количество кислорода для рафинирования поступает с невосстановленными окислами железа, содержащимися в шлаке.
В изобретении рассматриваются две структуры организации Р-подпространства с одностадийным и двухстадийным рафинированием и два режима для обеих структур: первый, когда кислород поступает с окислами Fe и в виде направленных струй на уровне нижней границы промежуточного слоя (вариант с верхней продувкой) и второй, когда добавляется донная подача кислорода и/или СО2 и/или воздуха и/или инертных газов и/или их различных смесей (вариант с комбинированной продувкой). Комбинированная продувка позволяет реализовать технологические режимы с более высокими удельными производительностями и меньшими расходами топлива.
Полученная сталь выводится в основном из нижней зоны при одностадийном рафинировании и поступает перед разливкой, при необходимости, на внепечную обработку и доводку под заданный регламент. Отвальный шлак из отстойной зоны выводится через сифонное устройство.
При двухстадийном рафинировании с прямоточным движением металла и шлака после первой стадии, основная часть шлака выводится из системы; на вторую стадию рафинирования подается новый шлак. Выпуск металла и шлака со второй стадии рафинирования проводится так же, как и в случае одностадийного рафинирования. При противоточном движении металла и шлака движение шлака изменяется только на второй стадии; выпуск металла и шлака проводится с разных концов второй стадии; при этом используется схема, описанная при одностадийном выпуске произведенного металла и полученного шлака.
В верхнем подпространстве происходит плавление перерабатываемых железосодержащих материалов, а также восстановление железа и примесей; здесь важно заметить, что восстановление окислов железа протекает по “цепному” механизму, причем в зарождении цепи участвует диоксид углерода СО2, получаемый в этой зоне при горении углеродистого топлива.
Из верхней зоны капли восстановленного промежуточного полупродукта и невосстановленный оксид железа, содержащийся в шлаке, поступают в активно перемешиваемый промежуточный слой, начинается взаимодействие оксида железа с восстановленным металлом, которое приводит к распаду оксида на атомы (ионы) железа и кислорода. За счет образовавшихся атомов (ионов) кислорода начинается реакция обезуглероживания получаемого при восстановлении полупродукта до содержания углерода, соответствующего регламенту для получения стали. Этот процесс продолжается в “нижнем” рафинировочном подпространстве.
В результате протекания реакции обезуглероживания начинает выделяться окись углерода, которая усиливает перемешивание в промежуточном слое, соответственно растет коэффициент турбулентно-диффузионного переноса и межфазная поверхность в промежуточном слое, что приводит к росту скоростей протекающих химических реакций и увеличению доставки кислорода. Возрастает скорость процессов безуглероживания и металл закипает или начинает барботировать. Интенсифицируется рафинирование металла от примесей. Описанный цикл представляет собой не что иное, как “положительную” обратную связь.
Положительная обратная связь процесса обезуглероживания подцеживает режим рафинирования в одной из привлекательных областей бистабильной динамической системы – “промежуточный слой рафинировочное подпространство”, позволяющей получать содержание углерода в металле 0,2-2,0%.
Так, поддерживая желаемое содержание кислорода в расплаве, непрерывное рафинирование успешно приводит к получению стали.
Предпочтительно, чтобы заранее заданное содержание углерода и примесей в металле можно было бы поддерживать и при необходимости корректировать изменениями потоков подаваемого твердого углеродистого топлива и/или потоком перерабатываемой шихты и/или потоком дутья.
Процесс рафинирования может проводиться либо непрерывно, либо образуя определенный вид колебательного процесса в промежуточном эмульсионном и рафинировочном слоях. Этот колебательный процесс значительно интенсифицирует массообмен между поступающим кислородом и углеродом расплава.
Содержание оксида железа, кислорода и углерода периодически проверяются и корректируются для поддержания рабочего режима. Желательно, при достижении требуемого рабочего режима, частично заменить донную подачу кислородсодержащего газа подачей инертного газа, например аргона или другого газа.
Предложенный способ прямого производства стали предполагает несколько технологий пуска печи.
Первая с предварительным наведением шлака и расплава на базе чугуна.
Вторая с предварительным наведением шлака и расплава на базе стали.
Основное отличие обеих технологий состоит в том, что после окончания подготовительного периода, перед переходом на режим нормальной эксплуатации, масса загруженного металла по первой технологии имеет содержание углерода 4,5-4,8%, а по второй, в основном, не более 1,0-2,0%.
Первый вариант технологии пуска с промежуточным выходом на чугун:
– в печь одновременно загружают железосодержащий материал и твердое углеродистое топливо,
– одновременно с загрузкой осуществляют подачу кислородосодержащего газа,
– начинается окисление топлива и выделение тепла,
– начинается плавление железосодержащего материала и флюсов; при этом благодаря избытку поданного топлива начинается процесс восстановления до образования жидких продуктов плавки – шлака и промежуточного железоуглеродистого продукта (чугуна),
– проводят выпуск шлака, полученного расплава (чугуна) и технологических газов, образующихся в процессе плавки. Начинается наладка технологического режима.
Второй вариант пуска с промежуточным выходом на чугун:
– в печь одновременно загружают железосодержащий материал и твердое углеродистое топливо,
– в печь заливают жидкий шлак, полученный при производстве черных металлов, например, в электропечах (вместо жидкого шлака может использоваться чугун или другой железосодержащий расплав на базе чугуна),
– повторяют последнюю стадию из первого варианта пуска (т.е. выпуск шлака, полученного расплава и технологических газов, проводится наладка технологического режима).
Третий вариант пуска с промежуточным выходом на чугун:
– шлаковый расплав наводится путем загрузки в печь и плавления твердых оксидных материалов или их смеси, например доменных, конвертерных, мартеновских и др. шлаков, оксидов металлов – CaO, MgO, SiO2, Al2О3 и др. Выше уровня поверхности расплава подают кислородсодержащий газ, начинается подача твердого углеродистого топлива, повторяется последняя стадия первого варианта пуска.
Приведенные варианты пуска печи фактически используют принятый способ пуска печи Romelt для производства чугуна. В технологии производства стали это только начальный этап, так как при этом получают расплав с содержанием углерода 4,5-4,8%. После следует основной этап перевода печи на производство стали, когда снижают содержание углерода до 0,2-0,3% или другой заданной величины. После достижения заданного уровня содержания углерода и примесей поддерживается достигнутый режим. Начинается обычная эксплуатация печи.
Возможен запуск печи с выходом прямо на сталь, но такой вариант намного сложнее, так как требует проведения всех пусковых операций при более высоких температурах и, самое главное, не позволяет провести предварительную наладку стационарного режима при выпуске чугуна.
Рассмотрим вариант запуска печи с одностадийным рафинированием для “верхней” и “комбинированной” продувки с выходом на сталь.
Итак, согласно одному аспекту настоящего изобретения, второй операционный этап описываемой технологии должен обеспечить изменение содержания углерода в расплаве от 4,5% до заданного в производимой стали и дальнейшее поддержание этого содержания на заданном уровне.
Первый, основной, подэтап – это снижение содержания углерода в массе находящегося в печи расплавленного металла до заданного содержания С (0,2-0,3%), чтобы дальше перевести печь на стационарный режим.
В изобретении предлагается использовать для окисления углерода расплава при ограниченных удельных производительностях по стали до 1 т/м2 пода*час в основном кислород FeO шлака по схеме, эквивалентной “верхней” продувке. Небольшая добавка потока кислорода или кислородсодержащей смеси в этом случае может быть необходима для подачи реагентов в рафинируемый слой металла.
Первый вариант позволяет непрерывно управлять потоком поступающего таким образом кислорода путем импульсного прерывания (уменьшения) непрерывного потока твердого углеродистого топлива, поступающего в печь.
Импульсное прерывание подачи твердого углеродистого топлива в работающую печь вызывает эквивалентное импульсное (резкое) возрастание содержания FeO в промежуточном эмульсионном слое “шлак – рафинируемый металл” и эквивалентное изменение поступления кислорода из шлака. Путем подачи нескольких импульсов, прерывающих подачу топлива на интервале до 5-6 часов, удается осуществить переход технологического процесса от режима с выпуском промежуточного продукта (чугуна) к режиму с выпуском стали. При этом постепенно падает содержание углерода в получаемом металле до заданного уровня, которое дальше поддерживается системами автоматического управления. Наилучшие показатели интенсификации процесса рафинирования получены при импульсных прерываниях подачи твердого топлива с продолжительностью импульсов в пределах 0,01-0,5 часа и амплитудой 0,1-0,7 расхода подаваемого топлива.
Описанный механизм протекания процесса получения полупродукта (чугуна) и производства стали стал возможен благодаря принятой структуре единого реакционного пространства.
Источники информации
1. USA Patent 4913734 from 04.03.1990. Int. C1. С21В 11/08; F27 В.
2. USA Patent 5431710 from 07.11.1995. Int. C1. С21В 13/14.
Формула изобретения
1. Способ прямого непрерывного производства стали из железосодержащих материалов, находящихся в виде слоя жидкого рафинируемого металла и слоя жидкого шлака, включающий образование единого реакционного пространства плавильно-восстановительным подпространством со слоем жидкого шлака, рафинировочным подпространством со слоем рафинируемого металла, расположенным под слоем жидкого шлака, содержащим перерабатываемые железосодержащие материалы и капли восстановленного металла, и промежуточным слоем “шлак – рафинируемый металл – газ” между указанными слоями, непрерывную подачу в слой жидкого шлака железосодержащих материалов, включая легирующие и разжижающие добавки, кислородсодержащего дутья и твердого углеродистого топлива, непрерывное удаление полученной при рафинировании стали, шлака и отходящих газов из реакционного пространства, подачу кислорода и/или кислородсодержащего газа или инертного газа и/или их смеси в промежуточный слой и слой рафинируемого металла, обеспечение в промежуточном слое турбулентно-диффузионного переноса оксидов железа и капель восстановленного металла, содержащихся в слое шлака, в промежуточный слой и слой рафинируемого металла с обеспечением при этом взаимодействия кислорода, выделяющегося при распаде оксидов железа, и подаваемого извне потока кислорода и/или кислородсодержащего газа и/или их смеси, с углеродом, и обеспечением одновременного протекания процесса рафинирования в промежуточном и рафинировочном слоях, интенсификацию переноса капель восстановленного металла и оксидов железа из шлакового слоя и интенсификацию протекания процесса рафинирования выделяющейся в процессе рафинирования окисью углерода, импульсное или непрерывное управление подачей загружаемого твердого углеродистого топлива, и/или подачей кислорода, и/или кислородсодержащего газа, и/или инертного газа, и/или их смеси и управление потоком перерабатываемой шихты с обеспечением стабилизации технологического режима подачей указанных выше управляющих компонентов, необходимых для осуществления процесса производства стали в соответствии с заданным регламентом по температуре процесса, содержанию углерода, кислорода и примесей в производимой стали, содержанию оксидов железа и твердого углеродистого топлива в шлаке.
2. Способ по п.1, при котором слои указанного жидкого рафинируемого металла и шлака образованы бескоксовым восстановлением железа и некоторых примесей из перерабатываемых железосодержащих материалов, выбранных из группы, включающей, в частности, измельченные железосодержащие руды, железорудные концентраты, железосодержащие отходы, железосодержащий лом.
3. Способ по п.1, в котором рафинирование включает обезуглероживание жидкого металла и удаление примесей.
4. Способ по п.2, в котором бескоксовое восстановление осуществляют в образованном едином реакционном пространстве.
5. Способ по п.1, в котором для интенсификации процесса рафинирования возбуждают колебания в рафинируемом слое металла, например, с помощью импульсных прерываний подачи твердого топлива с продолжительностью импульсов (0,01-0,5) ч и амплитудой (0,1-0,7) от его расхода.
6. Способ по п.1, в котором заданное содержание кислорода в рафинируемом металле обеспечивают кислородом оксидов железа, а в случае недостаточного его количества – дополнительным дутьем путем верхней и/или комбинированной продувки через боковые, и/или донные, и/или вертикальные фурмы.
7. Способ по п.6, в котором после достижения заданного содержания углерода и примесей в рафинировочном слое, подача кислорода дополнительными фурмами осуществляется в количестве, достаточном для окисления углерода и примесей до заданного содержания в потоке металла, поступающего с каплями из плавильно-восстановительного подпространства.
8. Способ по п.1, в котором перенос оксидов железа и капель восстановленного металла из шлакового слоя в промежуточный слой “шлак – рафинируемый металл – газ” и из этого слоя в слой рафинируемого металла обеспечивают кислородсодержащим дутьем и реакционными газами, поступающими из рафинировочного слоя посредством барботажа шлакового слоя, турбулентной диффузией и изменениями межфазной поверхности промежуточного слоя, барботажем рафинируемого расплава и при необходимости подачей дополнительными боковыми, донными или вертикальными фурмами кислородсодержащего дутья и/или инертного газа и/или их смеси.
9. Способ по п.1, в котором осуществляют управление процессом по содержанию углерода, кислорода и примесей в стали, содержанию оксидов железа и углерода в шлаке, достигающем промежуточного слоя “шлак – рафинируемый металл – газ”, а также температурой процесса.
10. Способ по п.9, в котором содержание окислов железа в шлаке обеспечивают в пределах 0,1-15%.
11. Способ по п.1, в котором содержание кислорода, углерода и примесей в стали, углерода и оксидов железа в шлаке на выходе из реакционного пространства, также содержания СО и СО2 в отходящих газах определяют дискретно или непрерывно.
12. Способ по п.9, в котором стадия управления включает регулирование состава и количества подаваемого железосодержащего материала, твердого углеродистого топлива и легирующих и разжижающих добавок, при этом все твердое углеродистое топливо подают в барботирующий шлаковый слой сверху.
13. Способ по п.9, в котором управление включает регулирование состава и количества подаваемого железоуглеродистого материала, твердого углеродистого топлива и легирующих и разжижающих добавок, при этом перед подачей твердого углеродистого топлива мелкие его фракции отсеивают от основного потока и подают через специальные фурмы в потоке инертного газа.
14. Способ по п.1, в котором для достижения требуемого содержания углерода и примесей в стали, реакционное подпространство рафинировочного слоя разделено, по меньшей мере, на две последовательно действующие зоны.
РИСУНКИ
|