(21), (22) Заявка: 2007120226/02, 30.05.2007
(24) Дата начала отсчета срока действия патента:
30.05.2007
(46) Опубликовано: 27.01.2009
(56) Список документов, цитированных в отчете о поиске:
БРАУНШТЕЙН О.Е. и др. Продольная прокатка полосы с малой сопряженной конусностью. – Изв. ВУЗов. Черная металлургия, №4, 2002, с.18-22. SU 1600872 А1, 23.10.1990. SU 373039 А, 18.06.1973. JP 55094707 А, 18.07.1980.
Адрес для переписки:
398600, г.Липецк, ул. Московская, 30, ЛГТУ, НИО
|
(72) Автор(ы):
Бельский Сергей Михайлович (RU), Мухин Юрий Александрович (RU), Бахаев Константин Вячеславович (RU)
(73) Патентообладатель(и):
ГОСУДАРСТВЕННОЕ ОБРАЗОВАТЕЛЬНОЕ УЧРЕЖДЕНИЕ ВЫСШЕГО ПРОФЕССИОНАЛЬНОГО ОБРАЗОВАНИЯ ЛИПЕЦКИЙ ГОСУДАРСТВЕННЫЙ ТЕХНИЧЕСКИЙ УНИВЕРСИТЕТ (ГОУ ВПО ЛГТУ) (RU)
|
(54) СПОСОБ ПРОКАТКИ ЛИСТОВОЙ СТАЛИ
(57) Реферат:
Изобретение предназначено для улучшения плоскостности прокатываемых полос при асимметричной прокатке тонколистовой стали. В прокатной клети установлены два комплекта рабочих валков – верхний и нижний, бочки которых выполнены в виде усеченных конусов, причем валки развернуты друг относительно друга на 180° таким образом, что их оси сохраняют параллельность. Снижение уровня остаточных напряжений в полосе обеспечивается за счет того, что величину конусности валков устанавливают в диапазоне, обеспечивающем направление поперечной составляющей суммарной скорости скольжения металла в очаге деформации от середины полосы к ее кромкам при сохранении зон опережения и отставания. Диапазон значений конусности валков регламентируется математической зависимостью. 2 ил. 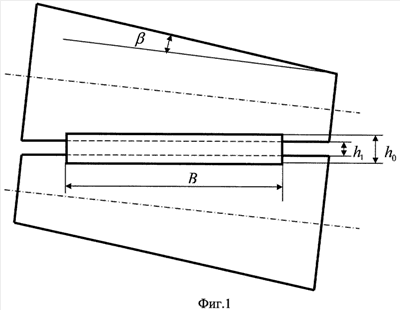
Изобретение относится к прокатному производству, а точнее к способам асимметричной прокатки тонколистовой стали в клетях станов горячей и холодной прокатки.
Известен способ прокатки полос, улучшающий плоскостность воздействием на поперечное перемещение металла в очаге деформации – усилия противоизгиба прикладываются к рабочим валкам с вогнутой симметричной профилировкой (SU 1761314 А1). При этом оси нагруженных рабочих валков обращаются выпуклостями друг к другу при сохранении межвалкового зазора чечевицеобразной формы. Недостатком этого способа является высокая величина усилий противоизгиба.
Известен способ прокатки листовой стали в чистовых клетях трио Лаута (RU 2152277 С1). Профилирование валков выполняется с коническим участком в средней части и цилиндрическими участками – по краям прокатываемой полосы, причем верхний и нижний валки развернуты по отношению к среднему на 180°. Недостатком этого способа является недостаточная конусность и прокатка краев полосы цилиндрическими участками валков, что не позволяет развиться поперечным перемещениям металла, улучшающим плоскостность прокатываемой полосы.
Наиболее близким по технической сущности и достигаемому результату является способ прокатки листовой стали, описанный в статье О.Е.Браунштейна, В.И.Базайкина, В.Е.Громова «Продольная прокатка полосы в валках с малой сопряженной конусностью» (Изв. вузов. Черн. металлургия. №4, 2002. С.18-22). Однако для упрощения анализа формоизменения и напряжений в очаге деформации авторы намеренно предполагают отсутствие смещения металла в поперечном направлении. Ради этого они направляют верхнюю и нижнюю поверхности полосы параллельно оси конического валка, что искажает картину распределения обжатий полосы (по мнению авторов абсолютное обжатие больше со стороны валка большего радиуса). Но именно поперечное смещение металла в очаге деформации (которое они не учитывают) и обуславливает улучшение плоскостности прокатываемой полосы.
Задачей изобретения является повышение качества прокатываемых полос, преимущественно за счет улучшения их плоскостности из-за развивающихся процессов поперечного течения металла в очаге деформации при тонколистовой прокатке.
Поставленная цель достигается тем, что в предлагаемом способе прокатки полос, включающем прокатку в конических рабочих валках, развернутых относительно друг друга на 180° и установленных с перекосом для сохранения горизонтального положения межвалкового зазора, направление поперечной составляющей суммарной скорости скольжения металла в очаге деформации от середины полосы к ее кромкам при сохранении зон опережения и отставания обеспечивают конусностью Р валков, устанавливаемой в пределах в соответствии с зависимостью
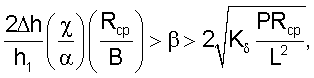
где h – абсолютное обжатие, мм;
h1 – выходная толщина, мм;

– коэффициент трения;
Rcp – радиус среднего сечения валка, мм;
В – ширина полосы, мм;
– конусность – угол между образующей и осью валка, рад;
К – податливость валка на изгиб при действии усилия прокатки, мм/т;
Р – усилие прокатки, т;
L – длина бочки валка, мм.
Предлагаемый способ (фиг.1) расширяет диапазон конусности рабочих валков, снимает ограничение на прокатку краев полосы в цилиндрических частях валков, не требует повышенных усилий противоизгиба и устанавливает количественный уровень величины конусности и перекоса установки рабочих валков в зависимости от усилия прокатки и ширины полосы, перенося воздействие на плоскостность полосы с регулирования поперечной разнотолщинности и/или усилий противоизгиба, известного из прототипа и аналогов, на величину конусности рабочих валков.
Известно, что разность вытяжек по ширине полосы может привести к отклонению от плоскостности полосы, проявляющемуся в виде волнистости или коробоватости. Известно также, что поперечное течение металла в очаге деформации снижает неравномерность вытяжек. Поперечному течению способствует скольжение металла вдоль оси бочки рабочих валков, направленное от середины полосы к ее кромкам.
Для учета влияния поперечного течения металла в очаге деформации на снижение остаточных напряжений по ширине полосы вводят коэффициент , причем 0< <1:

где  ост – величина остаточных напряжений, Н/мм2;
Е – модуль упругости материала полосы, Н/мм2;
 – разность между вытяжкой в текущей точке по ширине полосы и средней вытяжкой;
– средняя вытяжка.
Если представить неравномерность вытяжек разложением Фурье
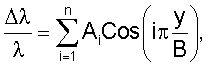
где Ai и i – амплитуда и номер гармоники неравномерности вытяжек;
y – координата вдоль бочки валка, мм;
В – ширина полосы, мм;
то коэффициент запишется в следующем виде:
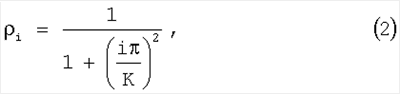
где 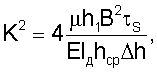
– коэффициент трения;
h1 – выходная толщина, мм;
s – сопротивление пластической деформации при сдвиге, Н/мм2;
lд – длина очага деформации, мм;
hср – средняя толщина, равная , мм;
h – абсолютное обжатие, мм.
Условия, облегчающие поперечное течение металла, повышают выравнивающую способность очага деформации и, тем самым, снижают уровень остаточных напряжений в полосе, улучшая ее плоскостность. В предлагаемом способе прокатки таким условием является поперечное скольжение валка по металлу в очаге деформации, направленное от середины полосы к ее кромкам. Поперечная составляющая суммарной скорости скольжения в очаге деформации на верхнем и нижнем рабочих валках при отсутствии изгиба осей рабочих валков:

где ;
.
Остальные обозначения понятны из рассмотрения фиг.2. Характер скольжения металла по валкам зависит от величины их конусности (фиг.2). Под действием усилия прокатки ось рабочего валка прогибается (величина стрелы прогиба – ), а поперечные сечения рабочих валков, соответствующие кромкам полосы, поворачиваются в противоположных направлениях.
Из-за этого величина поперечной составляющей суммарной скорости скольжения в очаге деформации уменьшается. Угол поворота сечений равен

где Р – усилие прокатки, Н;
K – податливость рабочего валка на изгиб при действии усилия прокатки, равная 
L – длина бочки, мм.
Поперечная составляющая суммарной скорости скольжения в очаге деформации на верхнем и нижнем рабочих будет направлена от середины полосы к ее кромкам при

Дополнительное выравнивание вытяжек, получаемое благодаря созданию условий, облегчающих поперечное течение металла, имеет вид

где 
Полоса не потеряет плоскую форму после прокатки, если

где 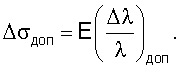
Если разность радиусов нижнего и верхнего валков в сечениях, соответствующих кромкам полосы, превысит некоторое граничное значение, в очаге деформации на валке с большим радиусом может исчезнуть зона опережения, т.е. процесс прокатки превратится в процесс прокатки-волочения, управление которым отличается от управления процессом продольной прокатки с двумя зонами. Граничное значение величины конусности определяется следующим образом:

где 
Для придания межвалковому зазору горизонтального положения в плоскости прокатки поступают одним из следующих двух способов:
1) середину нижнего валка собранных комплектов конических валков выставляют на линию прокатки; устанавливают перекос нижнего валка со стороны большего основания и верхнего со стороны меньшего основания, равный L; увеличивают позицию каждой стороны пары на ;
2) середину нижнего валка собранных комплектов конических валков выставляют на линию прокатки; устанавливают перекос нижнего валка со стороны меньшего основания и верхнего со стороны большего основания, равный L, уменьшают позицию каждой стороны пары на .
Предлагаемый способ прокатки полос реализуется следующим образом.
Собранные комплекты рабочих валков с конусностью, удовлетворяющей выражению (5), заваливаются в клеть. Межвалковый зазор устанавливается в горизонтальное положение одним из способов, описанных выше. Далее процесс прокатки идет, как обычно. При этом поперечная составляющая суммарной скорости скольжения в очаге деформации на верхнем и нижнем рабочих валках направлена от середины полосы к ее кромкам, обеспечивая дополнительное выравнивание вытяжек по ширине полосы и, тем самым, улучшая плоскостность прокатываемой полосы.
Пример. Прокатка полосы 2,0×1550 мм производится в последней клети семиклетевой чистовой группы стана 2000 со следующими параметрами: абсолютное обжатие h=0,2 мм, усилие прокатки Р=700 т (7 МН), радиус рабочего валка R=400 мм, модуль упругости полосы Е=105 Н/мм2, коэффициент трения =0,3. При податливости рабочего валка на изгиб К =8,0·10-5 мм/т необходимая конусность, вычисленная по формуле (5), составит =0,0047. Граничное значение величины конусности по формуле (9) гр=0,023. Придаем рабочим валкам конусность =0,005, что соответствует разности радиусов оснований конического валка 10 мм. Выставляем середину нижнего рабочего валка на линию прокатки и устанавливаем перекос нижнего валка со стороны большего основания и верхнего со стороны меньшего основания, равный 10 мм, затем увеличиваем позицию каждой стороны пары на 5 мм. Критические остаточные напряжения прокатываемой полосы (при которых полоса теряет плоскую форму) кр=2,7 Н/мм2, снижение за счет дополнительного выравнивания  доп=2,2 Н/мм2, тогда суммарные остаточные напряжения станут равными 0,5 Н/мм2. Этот уровень остаточных напряжений не приводит полосу к потере плоской формы.
Предлагаемый способ позволяет прокатывать полосы с повышенными требованиями к плоскостности.
Формула изобретения
Способ прокатки полос, включающий прокатку в выполненных в виде усеченных конусов валках, развернутых друг относительно друга и установленных с сохранением горизонтального положения межвалкового зазора, отличающийся тем, что направление поперечной составляющей суммарной скорости скольжения металла в очаге деформации от середины полосы к ее кромкам при сохранении зон опережения и отставания обеспечивают конусностью валков, устанавливаемой в пределах в соответствии с зависимостью
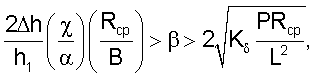
где h – абсолютное обжатие, мм;
h1 – выходная толщина, мм;

– коэффициент трения;
Rср – радиус среднего сечения валка, мм;
В – ширина полосы, мм;
– конусность – угол между образующей и осью валка, рад;
К – податливость валка на изгиб при действии усилия прокатки, мм/т;
Р – усилие прокатки, т;
L – длина бочки валка, мм.
РИСУНКИ
|