(21), (22) Заявка: 2007104311/02, 05.02.2007
(24) Дата начала отсчета срока действия патента:
05.02.2007
(43) Дата публикации заявки: 10.08.2008
(46) Опубликовано: 20.01.2009
(56) Список документов, цитированных в отчете о поиске:
SU 333204 A, 05.05.1972. SU 954449 A1, 30.08.1982. SU 988884 A, 15.01.1983. SU 2253684 C2, 10.06.2005. GB 808556 A, 04.02.1959. US 5759308 A, 02.06.1998. US 2003094218 A, 22.05.2003. SU 779415 A, 15.11.1980.
Адрес для переписки:
123104, Москва, а/я 129, Б. Козихинский пер., 7, кв.9, В.В. Овчинникову
|
(72) Автор(ы):
Алексеев Вячеслав Владимирович (RU), Силина Валентина Ивановна (RU), Овчинников Виктор Васильевич (RU)
(73) Патентообладатель(и):
Алексеев Вячеслав Владимирович (RU), Силина Валентина Ивановна (RU), Овчинников Виктор Васильевич (RU)
|
(54) СПОСОБ ТЕРМИЧЕСКОЙ ОБРАБОТКИ ИЗДЕЛИЙ ИЗ ВЫСОКОПРОЧНЫХ МАРТЕНСИТНОСТАРЕЮЩИХ СТАЛЕЙ
(57) Реферат:
Изобретение относится к области машиностроения и может быть использовано в различных отраслях промышленности при термической обработке деталей из мартенситностареющих сталей, например, 08Х15Н5Д2Т, 06Х14Н6Д2МБТ, 10Х14Н4АМЗ и 07Х16Н6. Для повышения ударной вязкости изделие отжигают при 650-670°С в течение 6-10 часов, затем нагревают под закалку в печи до 1000-1070°С, выдерживают в течение 2-3 часов и охлаждают сначала с печью до 880-900°С с выдержкой при этой температуре в течение 2,5-3 часов, а затем в воде подвергают отпуску и старению. 2 табл., 2 ил.
Изобретение относится к области машиностроения и может быть использовано в различных отраслях промышленности при термической обработке деталей из мартенситностареющих сталей, например, 08Х15Н5Д2Т, 06Х14Н6Д2МБТ, 10Х14Н4АМЗ и 07Х16Н6.
Известен способ термической обработки деталей из высокопрочных мартенситностареющих сталей, заключающийся в отжиге при 660°С в течение 6 ч и закалке с 1000°С при выдержке 3 ч с охлаждением в воде до потемнения поверхности деталей, далее на воздухе с последующим старением после механической обработки деталей (Потак Я.М. Высокопрочные стали. М.: Металлургия, 1972, с.146).
Недостатком описанного способа является снижение механических и коррозионных свойств. В частности, значение ударной вязкости на образцах с трещиной при температуре -70°С до КСТ равным 0,015 МДж/м2. Снижение коррозионных свойств происходит из-за наличия карбидных выделений по границам аустенитного зерна на отдельных партиях металла.
Наиболее близким по технической сущности к заявляемому способу термической обработки является способ термической обработки изделий из высокопрочных мартенситностареющих сталей, включающий отжиг при 650-670°С в течение 6…10 часов, нагрев под закалку до 1000…1070°С в течение 2…3 часов, отпуск и старение (Авторское свидетельство СССР №333204, C21D 1/78, 6/00, 1972).
Недостаток прототипа заключается в том, что он также не позволяет исключить появление в структуре стали карбидных выделений по границам зерен, что сопровождается появлением хрупких зон в изломе образцов.
Предлагаемый способ термической обработки мартенситностареющих сталей обеспечивает повышение ударной вязкости при комнатной и отрицательной температурах.
Технический результат, на достижение которого направлен заявляемый способ, обеспечивается отжигом при 650…670°С в течение 6…10 часов, нагревом под закалку до 1000…1070°С в течение 2…3 часов и охлаждением с печью до 880…900°С с выдержкой при этой температуре в течение 2,5…3 часов, а затем в воде, отпуском и старением.
Заявляемый способ включает в себя следующую последовательность операций:
1. Отжиг при 650…670°С в течение 6…10 часов;
2. Закалка: нагрев до 1000…1070°С, выдержка 2…3 часа, охлаждение с печью до 880…900°С, выдержка 2,5…3 час с последующим охлаждением в воде;
3. Обработка холодом при температуре -70°С с выдержкой 2 часа;
4. Отпуск при 340…360°С в течение 2…3 часов;
5. Старение после механической обработки деталей по соответствующей технологии для каждой конкретной марки стали.
Подробнее сущность заявляемого способа поясняется фотографиями:
– на фиг.1 приведена микроструктура стали 07Х16Н6 после термической обработки по известной технологии по а.с. №333204;
– на фиг.2 приведена микроструктура стали 07Х16Н6 после термической обработки по заявляемому способу.
Проведение отжига при температуре 650…670°С в течение 6…10 часов обеспечивает регулирование количества остаточного аустенита перед закалкой стали. Кроме того, при температуре отжига менее 650°С наблюдается наличие в структуре стали карбидной сетки. При температуре отжига более 670°С снижение коррозионной стойкости стали. При времени выдержки менее 6 часов отмечено понижение коррозионной стойкости стали. При увеличении времени выдержки при отжиге более 10 часов отмечается резкое снижение коррозионной стойкости стали из-за выпадения карбидов.
Нагрев под закалку определяет уровень механических свойств стали. При температуре нагрева под закалку менее 1000°С отмечается снижение предела прочности стали. При температуре закалки более 1070°С прочность стали увеличивается, однако резко снижается значение ударной вязкости.
При времени выдержки при нагреве под закалку менее 2,5 часов наблюдается снижение коррозионной стойкости стали за счет образования сетки карбидов по границам зерен. Увеличение времени выдержки при нагреве под закалку более 3 часов сопровождается резким снижением относительного удлинения стали.
В процессе медленного охлаждения с 1000…1070°С до 890°С происходит выпадение небольшого количества частиц карбидной фазы типа (FeCr)23С6 по границам зерен аустенита, которое обеспечивается разницей в растворимости элементов при 1000 и 890°С. Выделения, находящиеся в мелкодисперсном виде, коагулируют при последующей выдержке при 890°С, уменьшая тем самым энергию границ зерна, что снижает скорость диффузионных процессов при последующем охлаждении.
Исследования показали, что увеличение температуры свыше 900°С, например до 950°С, не дает положительного эффекта, так как недостаточна доля выделившихся частиц, приводящих к уменьшению энергии границы. Уменьшение температуры ниже 880°С вызывает возникновение значительного количества коагулированных карбидов.
Отсутствие карбидных выделений при охлаждении с 880…900°С подтверждено металлографическим (фиг.2), электронномикроскопическим, рентгеноструктурным и микрорентгеноспектральным анализом.
Проводилась термическая обработка деталей из мартенситностареющей стали 08Х15Н5Д2Т, у которой точка начала карбидных выделений составляет 950°С, конца карбидных выделений 650°С, температура начала мартенситного превращения 130°С. Детали обрабатывали по режимам, приведенным в табл.1. Результаты испытаний представлены в табл.2.
Коррозионная стойкость оценивалась при выдержке в растворе состава: CuSO4 – 110 г/дм3; Н2SO4 – 55 г/дм3 и базе испытаний 10 часов.
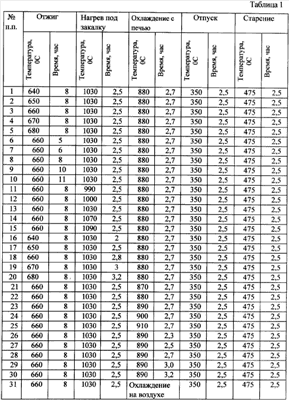 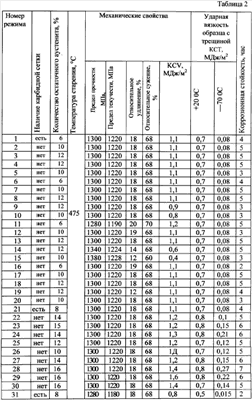
Использование заявляемого способа термической обработки деталей из высокопрочных мартенситностареющих сталей обеспечивает получение структуры без карбидных выделений, увеличение коррозионной стойкости и повышение надежности изделий в эксплуатации.
Формула изобретения
Способ термической обработки изделий из высокопрочных мартенситностареющих сталей, включающий отжиг при 650-670°С в течение 6-10 ч, нагрев под закалку в печи до 1000-1070°С, выдержку в течение 2-3 ч и охлаждение сначала с печью до 880-900°С с выдержкой при этой температуре в течение 2,5-3 ч, а затем в воде, отпуск и старение.
РИСУНКИ
|