|
(21), (22) Заявка: 2004112558/15, 23.04.2004
(24) Дата начала отсчета срока действия патента:
23.04.2004
(30) Конвенционный приоритет:
25.04.2003 FR 0305211
(43) Дата публикации заявки: 10.10.2005
(46) Опубликовано: 20.01.2009
(56) Список документов, цитированных в отчете о поиске:
US 6620311 B2, 16.09.2003. SU 1427002 A1, 30.09.1988. US 4447313 A, 08.05.1984. US 3268437 A, 23.08.1966. US 3245900 A, 12.04.1966.
Адрес для переписки:
129090, Москва, ул. Б.Спасская, 25, стр.3, ООО “Юридическая фирма Городисский и Партнеры”, пат.пов. Е.Е.Назиной, рег. № 517
|
(72) Автор(ы):
ГЕРЕ Кристоф (FR), КРЕССМАНН Стефан (FR), ВЕРСТРАТЕ Ян (FR)
(73) Патентообладатель(и):
ЭНСТИТЮ ФРАНСЭ ДЮ ПЕТРОЛЬ (FR)
|
(54) СПОСОБ ОБОГАЩЕНИЯ ТЯЖЕЛЫХ ЗАГРУЗОК ПРИ ПОМОЩИ ДЕЗАСФАЛЬТАЦИИ И ГИДРОКРЕКИНГА В КИПЯЩЕМ СЛОЕ
(57) Реферат:
Изобретение может быть использовано для переработки нефтяных фракций. Углеводородную загрузку подают по линии 1 в секцию 2 для дезасфальтации в присутствии растворителя. Фракцию асфальта и часть растворителя, нагнетаемого в секцию 2, извлекают через линию 4 и направляют к секции 5 для разделения растворителя и асфальта. Асфальт извлекают через линию 6. Растворитель извлекают через линию 7 и повторно нагнетают в секцию 2 через линии 8,1 и 3. Дезасфальтированную фракцию и часть нагнетаемого в секцию 2 растворителя извлекают через линию 9 и направляют к секции 10 для разделения растворителя и дезасфальтированной фракции. Растворитель извлекают через линию 8 и повторно нагнетают в секцию 2 по линиям 8,1 и 3. Изобретение позволяет достичь высокого выхода бензина, керосина и дизельного топлива из остатков от перегонки при атмосферном давлении или от вакуумной перегонки тяжелой нефти. 10 з.п. ф-лы, 2 ил.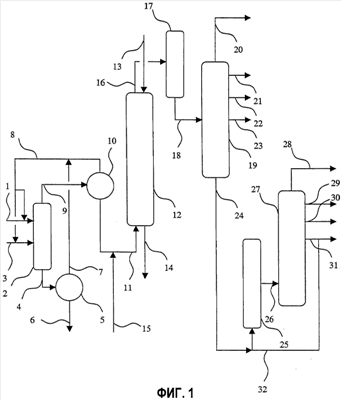
Настоящее изобретение относится к области переработки нефтяных фракций. В частности, оно касается способов обработки тяжелых загрузок, таких как остатки после перегонки при атмосферном давлении или после вакуумной перегонки.
Учитывая всевозрастающие потребности в реактивном топливе, бензине и дизельном топливе и постоянное снижение потребления мазута, все большее значение приобретает возможность высокоуровневой конверсии остаточных фракций.
Это особенно характерно для некоторых стран, где в основном добывают так называемую тяжелую нефть, например нефть “Атабаска” в Канаде, “Моришаль” в Венесуэле, содержащую очень мало легких дистиллятов. Действительно, эти виды тяжелой нефти содержат приблизительно 80 вес.% остатка при вакуумной перегонке. Эти виды нефти отличаются также низкой плотностью API со значением ниже 12.
Кроме того, тяжелые загрузки, такие как остатки от перегонки при атмосферном давлении и остатки от вакуумной перегонки, содержат значительные количества металлов, осадков и асфальтенов. При использовании этих загрузок в процессах термической конверсии, таких как восстановление с понижением вязкости, наличие в этих загрузках примесей, быстро приводит к коксованию и закупориванию емкостей в результате флокуляции и осаждения. При использовании этих же загрузок в процессах каталитической конверсии в стационарном слое наличие примесей требует применения защитного слоя для предохранения катализаторов очистки нефти и предупреждения чрезмерно быстрой дезактивации, для чего в таких установках необходимо увеличивать объем реакторов.
Кроме того, в установках для конверсии в стационарном слое конверсия загрузки ограничивается температурными уровнями, которые являются более низкими, чем в установках для конверсии в кипящем слое. Когда эти загрузки используют для конверсии в кипящем слое, наличие указанных примесей приводит к более частой замене катализатора.
Во французском патенте FR 2803596 описан способ конверсии дистиллятов, содержащий этап гидроконверсии в кипящем слое, этап разделения, на котором получают легкую фракцию и тяжелую фракцию, и этап каталитического крекинга тяжелой фракции. Такой способ способствует достижению более высоких уровней конверсии, но он, как правило, применяется для загрузок с конечной точкой кипения ниже 600°С. Кроме того, описанный в этом патенте способ не может применяться для переработки остатка от перегонки при атмосферном давлении или остатка от вакуумной перегонки тяжелой нефти.
Был разработан способ, устраняющий вышеупомянутые недостатки и позволяющий добиться высокого выхода бензина, керосина и дизельного топлива из остатков от перегонки при атмосферном давлении или от вакуумной перегонки тяжелой нефти. Этот способ обеспечивает также получение высококачественных продуктов, не требующих дополнительной очистки или проходящих лишь незначительную дополнительную очистку.
Объектом настоящего изобретения является, таким образом, способ обработки углеводородной загрузки, которая содержит по меньшей мере 90 вес.% соединений с температурой кипения, по меньшей мере, равной 340°С, отличающийся тем, что содержит следующие этапы, во время которых:
а) загрузку вводят в контакт с растворителем для получения дезасфальтированного эфлюента с содержанием асфальтенов (не растворимых в н-гептане по французскому стандарту NF-T-60-115), меньшим 3000 весовых пропромилле;
б) производят крекинг дезасфальтированного эфлюента в присутствии водорода и катализатора гидрокрекинга в реакторе с кипящим слоем таким образом, чтобы конвертировать по меньшей мере 50 вес.% фракции дезасфальтированного эфлюента, кипящего при температуре выше 500°С, в соединения с точкой кипения ниже 500°С;
в) эфлюент, полученный на этапе б), разделяют на фракции для получения бензина, керосина, дизельного топлива и первого остатка;
г) осуществляют каталитический крекинг по меньшей мере части этого первого остатка для получения эфлюента, содержащего бензин, керосин, дизельное топливо и второй остаток.
Преимуществом настоящего изобретения является получение способа, обеспечивающего наилучшую утилизацию тяжелых загрузок, таких как остатки от перегонки при атмосферном давлении или остатки от вакуумной перегонки, полученные из любых видов нефти, в частности из тяжелой нефти. Такая нефть, как правило, имеет плотность API ниже 12.
Другим преимуществом настоящего изобретения является получение способа, обеспечивающего повышенный общий выход бензина, керосина и дизельного топлива.
Другим преимуществом настоящего изобретения является получение способа, обеспечивающего производство бензина, керосина и дизельного топлива высокого качества и позволяющего ограничить количество и сложность операций дополнительной очистки.
Для лучшего понимания настоящего изобретения прилагаемые фигуры иллюстрируют два неограничительных варианта его осуществления.
Фиг.1 в качестве примера иллюстрирует вариант осуществления способа в соответствии с настоящим изобретением, последовательно содержащего этап дезасфальтации, этап гидроконверсии в кипящем слое, этап разделения на фракции путем перегонки при атмосферном давлении и этап каталитического крекинга типа FCC.
Фиг.2 в качестве примера иллюстрирует схему, аналогичную схеме, показанной на фиг.1, но в которой этап разделения на фракции содержит перегонку при атмосферном давлении и вакуумную перегонку, при этом дистиллят от вакуумной перегонки направляется на этап гидрокрекинга.
Загрузки, которые можно подвергать обработке способом в соответствии с настоящим изобретением, являются углеводородами, содержащими по меньшей мере 95 вес.% соединений с температурой кипения, по меньшей мере равной 340°С и могущей достигать 700°С и более и, например, составлять от 500°С до 700°С.
Углеводородная загрузка имеет конечную точку кипения, предпочтительно превышающую 600°С, еще предпочтительнее превышающую 650°С и еще предпочтительнее – превышающую 700°С.
Эти загрузки могут быть остатками от перегонки при атмосферном давлении и остатками от вакуумной перегонки. Например, эти загрузки могут быть остатками от прямых перегонок или от процессов конверсии, таких как коксование, процессов гидроконверсии в стационарном слое, таких как процесс HYVAHL, или процессов в кипящем слое, таких как процесс H-Oil. Загрузка может быть образована путем смешивания этих фракций в любой пропорции или путем разбавления в нефтяных фракциях с точкой кипения ниже 360°С.
Настоящее изобретение может представлять особенный интерес для переработки некоторых остатков тяжелой нефти, то есть нефти с низким содержанием дистиллятов. Обычно виды нефти “Атабаска” и “Моришаль” содержат 80% остатков от вакуумной перегонки. Как правило, их плотность API приближается к 10. По сравнению с другими сортами нефти эти виды тяжелой нефти содержат гораздо больше примесей, таких, например, как металлы (никель, ванадий, кремний и т.д.), углерод Конрадсона повышенного содержания, асфальтены, сера и азот.
Так, согласно предпочтительному варианту углеводородная загрузка содержит в основном остатки от перегонки при атмосферном давлении, по меньшей мере 90 вес.% которых представляют собой соединения с температурой кипения, по меньшей мере равной 600°С, и остатки от вакуумной перегонки тяжелой нефти, по меньшей мере 95 вес.% которых представляют собой соединения с температурой кипения, по меньшей мере равной 650°С.
Во время этапа а) способа в соответствии с настоящим изобретением загрузку вводят в контакт с растворителем для получения дезасфальтированного эфлюента. Эту операцию часто называют дезасфальтацией в присутствии растворителя. Она обеспечивает извлечение большей части асфальтенов и снижение содержания металлов. Во время такой дезасфальтации эти различные элементы концентрируются в эфлюенте, называемом асфальтом. Дезасфальтированный эфлюент, часто называемый дезасфальтированным маслом, отличается пониженным содержанием асфальтенов и металлов.
Одной из задач этапа дезасфальтации является, с одной стороны, максимальное получение дезасфальтированного масла и, с другой стороны, – удержание на определенном уровне и даже сведение к минимуму содержания асфальтенов. Это содержание асфальтенов, как правило, определяют как содержание асфальтенов, не растворимых в гептане. Для этого используют следующую методику. Навеску образца смешивают в конической колбе с гептаном при кипячении с обратным холодильником в течение 60 минут. Масса навески (m2) и объем используемого гептана являются функцией ожидаемого содержания асфальтенов. Более подробно об этом можно узнать в стандарте NF-T 60-115 от января 2002. После нагревания раствор охлаждают и помещают в затемненное место, как минимум, на 2 часа. Затем его пропускают через бумажный фильтр диаметром 110-125 и размером пор 2,5-3 мкм. Бумажный фильтр и его содержимое помещают в экстрактор с отгонкой. Асфальтены экстрагируют толуолом до полного растворения асфальтенов, находящихся на фильтре. Содержимое колбы резко выливают в выпарную чашку, предварительно высушенную в сушильной печи при 105°С в течение 30 мин. И затем взвешенную (масса m1). Затем колбу промывают толуолом,, промывную жидкость резко выливают в чашку, которую затем высушивают в сушильной печи при 105° в течение 30 мин и взвешивают (масса m3).
Содержание асфальтенов в % масс. Рассчитывают по формуле А=100(m3-m1)/m2,
где А означает массу асфальтенов, в %, m1 – массу пустой чашки в г, m2 – массу навески в г, m3 – масса чашки с асфальтенами, в г.
Согласно настоящему изобретению содержание асфальтенов в дезасфальтированном эфлюенте меньше 3000 весовых пропромилле.
Предпочтительно содержание асфальтенов в дезасфальтированном эфлюенте меньше 1000 весовых пропромилле, и предпочтительнее – меньше 500 весовых пропромилле.
При содержании асфальтенов менее 500 весовых пропромилле метод по стандарту NF-T 60-115 уже не является достаточным для измерения этого содержания. Заявитель разработал аналитический метод, включающий в себя количественный анализ асфальтенов продуктов прямой перегонки и тяжелых продуктов дезасфальтации остатков. Этот метод применим для значений концентрации асфальтенов ниже 3000 весовых пропромилле и выше 20 весовых пропромилле. Данный метод состоит в сравнении абсорбционной способности при 750 нм раствора пробы в толуоле и раствора пробы в гептане после фильтрования. Разность между двумя измеренными значениями коррелируют с концентрацией асфальтенов, не растворимых в гептане, при помощи калибровочного уравнения. Этот метод дополняет метод AFNOR Т60-115 и стандартный метод IP143, которые применяются при более высоких значениях концентрации.
Растворитель, используемый на этапе а) дезасфальтации, предпочтительно является парафиновым растворителем, бензиновой фракцией или конденсатами, содержащими парафины.
Предпочтительно используемый во время этапа а) растворитель содержит по меньшей мере 50 вес.% углеводородных соединений, содержащих от 3 до 7 атомов углерода, предпочтительно от 5 до 7 атомов углерода, еще предпочтительнее – 5 атомов углерода.
В зависимости от применяемого растворителя выход дезасфальтированного масла и качество этого масла могут меняться. Например, когда переходят от растворителя с 3 атомами углерода к растворителю с 7 атомами углерода, выход масла увеличивается, но одновременно увеличивается содержание примесей (асфальтены, металлы, углерод Конрадсона, сера, азот и т.д.).
В приведенной ниже таблице в качестве примера указано влияние числа атомов углерода в углеводородных соединениях растворителя на выход дезасфальтированного масла и на качество масла во время дезасфальтации остатка от вакуумной перегонки (ОВП) легкой арабской нефти.
Растворитель |
С3 |
С4 |
С5 |
Выход дезасфальтированного масла по отношению к |
Базис |
Базис+30 |
Базис+45 |
остатку от вакуумной перегонки, в вес.% |
|
|
|
Характеристики масла |
|
|
|
Плотность dl5/4 |
0,933 |
0,959 |
0,974 |
Сера (вес.%) |
2,6 |
3,3 |
3,7 |
Углерод Конрадсона |
1,9 |
5,9 |
7,9 |
(вес.%) |
|
|
|
Асфальтены С7 (вес.%) |
<0,05 |
0,07 |
0,15 |
Ni(ппм) |
1 |
3 |
7 |
V(ппм) |
1,5 |
2,5 |
15,5 |
Кроме того, для данного растворителя выбор рабочих условий, в частности, температуры и нагнетаемого количества растворителя, влияет на выход дезасфальтированного масла и на качество этого масла. Специалист может выбрать оптимальные условия, чтобы получить содержание асфальтена ниже 3000 весовых пропромилле.
Этап а) дезасфальтации можно осуществлять при помощи любого известного специалистам средства. Как правило, этап а) осуществляют в смесителе-отстойнике или в экстракционной колонне. Предпочтительно этап дезасфальтации осуществляют в экстракционной колонне.
В предпочтительном варианте реализации в экстракционную колонну подают смесь, содержащую углеводородную загрузку и первую часть загрузки растворителя, при этом объемное соотношение между частью загрузки растворителя и углеводородной загрузкой называют долей растворителя, нагнетаемого вместе с загрузкой. Целью этого этапа является тщательное смешивание загрузки с растворителем в экстракционной колонне. В декантационную зону в нижней части экстракционной колонны можно вводить вторую часть загрузки растворителя, при этом объемное соотношение между второй частью загрузки растворителя и углеводородной загрузкой называют долей растворителя, нагнетаемого в нижнюю часть экстракционной колонны. Объем рассматриваемой углеводородной загрузки в декантационной зоне, как правило, является объемом, подаваемым в экстракционную колонну. Сумму двух объемных соотношений между каждой из частей загрузки растворителя и углеводородной загрузкой называют общей долей растворителя. Отстаивание асфальта состоит в противоточной промывке чистым растворителем асфальтовой эмульсии в смеси «растворитель + масло». Ему способствует увеличение доли растворителя (по сути, речь идет о замене среды «растворитель + масло» средой чистого растворителя) и понижение температуры.
Общая доля растворителя предпочтительно превышает 4/1 и предпочтительнее превышает 5/1.
Эта общая доля растворителя раскладывается на долю растворителя, нагнетаемого с загрузкой, предпочтительно составляющую от 1/1 до 1,5/5, и на долю растворителя, нагнетаемого в нижнюю часть экстракционной колонны, предпочтительно превышающую 3/1 и еще предпочтительнее превышающую 4/1.
Кроме того, в предпочтительном варианте между головной и нижней частями колонны обеспечивают градиент температуры, позволяющий создать внутреннее орошение, тем самым улучшается разделение между масляной средой и смолами. Действительно, смесь «растворитель + масло», нагреваемая в головной части экстракционной колонны, обеспечивает осаждение фракции, содержащей смолу, которая опускается в нижнюю часть экстракционной колонны. Восходящий противоток смеси обеспечивает растворение при более низкой температуре фракций, содержащих смолу и являющихся самыми легкими.
Температура в головной части экстракционной колонны предпочтительно находится в пределах от 175 до 195°С. Температура в нижней части экстракционной колонны предпочтительно находится в пределах от 135 до 165°С.
Давление внутри экстракционной колонны, как правило, корректируют таким образом, чтобы все продукты находились в жидком состоянии. Предпочтительно это давление находится в пределах от 4 до 5 МПа.
Во время этапа б) способа в соответствии с настоящим изобретением осуществляют крекинг дезасфальтированного эфлюента в присутствии водорода и гидрокрекингового катализатора в реакторе с кипящим слоем по технологии T-Star, описанной, например, в статье «Heavy Oil Hydroprocessing», опубликованной в Aiche, Mar. 19-23, 1995, HOUSTON, Тех., лист 42d, или по технологии H-Oil, описанной, например, в статье, опубликованной в «NPRA Annual Meeting», Mar. 16-18, 1997, J.J.Colyar and L.I.Wilson, “The H-Oil Process: A Worldwide Leader In Vacuum Residue Hydroprocessing”.
Преимуществом такой гидроконверсии в реакторе с кипящим слоем по сравнению с реактором со стационарным слоем является то, что становится возможным достичь гораздо более высокого уровня конверсии благодаря более высоким температурам реакции. Преимуществом максимальной конверсии является снижение количества неконвертированного остатка, повышение выхода бензина, керосина и дизельного топлива, а также повышение качества продуктов. Таким образом, повышенные уровни конверсии по меньшей мере частично компенсируют потери в выходе дезасфальтированного эфлюента, возникающие из-за недостаточной чистоты дезасфальтированного масла, получаемого на этапе а) дезасфальтации. Так, несмотря на большее количество асфальта, получаемого на этапе а), в совокупности этапы а) и б) способствуют увеличению выхода бензина, керосина и дизельного топлива.
Согласно предпочтительному варианту реализации настоящего изобретения этап б) осуществляют с добавлением свежего катализатора и извлечением отработанного катализатора. В частности, присутствие асфальтенов снижает активность катализатора в кипящем слое в том, что касается гидродесульфурации, гидродеазотизации, снижения содержания углерода Конрадсона, гидрогенизации ароматических веществ, снижения содержания металлов, и приводит к повышению потребности в свежем катализаторе.
Обработка предварительно дезасфальтированного эфлюента с содержанием асфальтенов (не растворимых в гептане) ниже 3000 весовых пропромилле позволяет снизить потребность в замене катализатора. Действительно, дезасфальтированный эфлюент обладает более высокой реакционной способностью и меньшим дезактивирующим эффектом по сравнению с менее дезасфальтируемой загрузкой.
Конверсия в легкие продукты дезасфальтированного масла определяется следующей формулой:
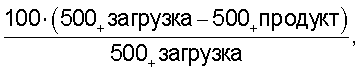
в которой 500+загрузка представляет собой массовую фракцию дезасфальтированного масла, состоящую из компонентов, кипящих при температуре выше 500°С, а 500+продукт является массовой фракцией продукта, состоящей из компонентов, кипящих при температуре выше 500°С.
В соответствии с настоящим изобретением условия этапа б) обеспечивают достижение конверсии, по меньшей мере равной 50 вес.%.
Предпочтительно конверсия дезасфальтированного эфлюента составляет по меньшей мере 70 вес.%, предпочтительно по меньшей мере 75 вес.% и еще предпочтительнее – по меньшей мере 80 вес.%.
Рабочие условия выбирают таким образом, чтобы обеспечить указанные показатели.
Так, процесс осуществляют при абсолютном давлении, достигающем от 5 до 35 МПа, предпочтительно от 6 до 25 МПа и еще предпочтительнее – от 8 до 20 МПа. Рабочая температура на этапе б) может достигать приблизительно от 350 до приблизительно 500°С. Эту температуру обычно корректируют в зависимости от необходимого уровня гидроконверсии легких продуктов. Пространственная часовая скорость (ПЧС) и частичное давление водорода являются важными факторами, которые выбирают в зависимости от характеристик обрабатываемого продукта и от необходимого уровня конверсии. Чаще всего ПЧС может находиться в диапазоне примерно от 0,1 ч-1 до примерно 10 ч-1, предпочтительно примерно от 0,2 ч-1 до примерно 5 ч-1. Количество водорода, смешиваемого с загрузкой, может составлять приблизительно от 50 до приблизительно 5000 Нм3/м3, предпочтительно приблизительно от 100 до приблизительно 1000 Нм3/м3 и еще предпочтительнее приблизительно от 200 до приблизительно 500 Нм3/м3 и выражается в нормальных кубических метрах (Нм3) на кубический метр (м3) жидкой загрузки.
Катализатор, применяемый на этапе б), предпочтительно является гидроконверсионным катализатором, содержащим аморфный носитель и по меньшей мере один металл или металлосодержащее соединение с гидрогенизирующей функциональной группой.
Как правило, применяют катализатор, пористость которого соответствует обработке металлосодержащих загрузок.
Гидрогенизирующая функциональная группа может быть обеспечена по меньшей мере одним металлом из группы VIII, например, никелем и/или кобальтом чаще всего в сочетании по меньшей мере с одним металлом из группы VIБ, например, молибденом и/или вольфрамом. Можно, например, использовать катализатор с содержанием никеля от 0,5 до 10 вес.%, предпочтительно от 1 до 5 вес.% (в виде оксида никеля NiO) и с содержанием молибдена от 1 до 30 вес.%, предпочтительно от 5 до 20 вес.% (в виде оксида молибдена МоО3). Общее содержание оксидов металлов групп VI и VIII может достигать приблизительно от 5 до приблизительно 40 вес.%, предпочтительно приблизительно от 7 до приблизительно 30 вес.%. В случае катализатора, содержащего металлы группы VI и группы VIII, весовое соотношение металлических оксидов между металлом (или металлами) группы VI и металлом (или металлами) группы VIII может достигать примерно от 1 до примерно 20, предпочтительно примерно от 2 до примерно 10.
Носитель катализатора на этапе б) можно выбирать из группы, содержащей глинозем, кремнезем, кремнеземистые глиноземы, магнезию, глины и смеси по меньшей мере двух из этих минералов. Этот носитель может также включать в себя другие соединения, такие как, например, оксиды, выбранные из группы, содержащей оксид бора, двуоксид циркония, оксид титана, фосфорный ангидрид. Предпочтительно используют носитель на основе глинозема. Обычно в качестве глинозема используют бета-глинозем или гамма-глинозем. Этот носитель, в частности, в случае глинозема может быть активирован фосфором и, возможно, бором и/или кремнием. В этом случае концентрация фосфорного ангидрида Р2О5 обычно ниже приблизительно 20 вес.%, предпочтительно ниже приблизительно 10 вес.% и по меньшей мере равна 0,001 вес.%. Концентрация триоксида бора В2О3, как правило, находится в пределах от 0 до примерно 10 вес.%. Чаще всего этот катализатор применяют в экструдированном виде.
Предпочтительно катализатор, применяемый на этапе б), приготовлен на основе никеля и молибдена, активирован фосфором и выполнен на носителе из глинозема.
Как правило, отработанный катализатор частично заменяют свежим катализатором путем извлечения в нижней части реактора и подачи свежего катализатора в верхнюю часть реактора. Извлечение и подача катализатора могут осуществляться через равные промежутки времени, то есть порциями, или непрерывно, или почти непрерывно. Можно, например, загружать свежий катализатор каждый день. Объем замены отработанного катализатора свежим катализатором может достигать примерно 0,05 кг на 10 кг на кубический метр загрузки. Извлечение и подачу катализатора осуществляют при помощи устройств, обеспечивающих непрерывную работу во время этапа б) гидроконверсии. Устройство, в котором осуществляют этап б), как правило, содержит рециркуляционный насос, обеспечивающий поддержание катализатора в состоянии суспензии в кипящем слое путем непрерывного нагнетания в нижнюю часть реактора по меньшей мере части жидкости, извлекаемой из головной части реактора. Можно также подавать извлекаемый из реактора отработанный катализатор в регенерационную зону, в которой удаляют содержащиеся в нем углерод и серу, а затем использовать этот регенерированный катализатор для этапа б) гидроконверсии.
На этапе в) способа в соответствии с настоящим изобретением полученный на этапе б) эфлюент разделяют на фракции для получения бензина, керосина, дизельного топлива и первого остатка. Этот остаток содержит соединения, имеющие точки кипения, превышающие точки кипения дизельного топлива.
Разделение на фракции на этапе в) может быть осуществлено любым способом, известным специалистам, например, путем перегонки. Можно производить перегонку при атмосферном давлении с последующей вакуумной перегонкой остатка, извлеченного во время перегонки при атмосферном давлении. Поэтому первый остаток может быть остатком от перегонки при атмосферном давлении или остатком от вакуумной перегонки.
Предпочтительно после этапа в) производят отделение твердых частиц катализатора. Эти твердые частицы катализатора чаще всего являются мелкими частицами, образующимися от механического разрушения катализатора, использованного на этапе б) гидроконверсии. Как правило, применяют ротационный фильтр, мешочный фильтр или центрифугирующую систему типа гидроциклона, последовательно соединенную с фильтрами или с отстойником. Этот дополнительный этап позволяет избежать быстрой дезактивации катализатора, применяемого на этапе г), вследствие присутствия молибдена в мелких частицах катализатора. Согласно частному варианту выполнения этого этапа фильтрования применяют по меньшей мере два параллельно соединенных сепараторных средства, одно из которых предназначено для осуществления разделения, в то время как другое предназначено для удаления оставшихся мелких частиц катализатора.
В случае, когда этап в) содержит вакуумную перегонку, получаемый дистиллят направляют на этап каталитического гидрокрекинга.
Этот этап гидрокрекинга, как правило, осуществляют по меньшей мере на одной фракции полученного от вакуумной перегонки дистиллята в присутствии водорода для получения эфлюента, содержащего бензин, керосин, дизельное топливо и остаток.
На этом этапе гидрокрекинга по меньшей мере часть первого остатка, полученного на этапе в), и, возможно, полученный от вакуумной перегонки дистиллят подвергают каталитическому гидрокрекингу в условиях, хорошо известных специалисту, для получения топливной фракции (содержащей бензиновую фракцию, керосиновую фракцию и газойлевую фракцию), которую обычно направляют, по меньшей мере частично, в топливные резервуары, и для получения фракции остатка.
В рамках настоящего изобретения выражение «каталитический гидрокрекинг» охватывает крекинг-процессы, содержащие по меньшей мере один этап конверсии фракции полученного от вакуумной перегонки дистиллята, на котором применяют по меньшей мере один катализатор в присутствии водорода.
Рабочие условия этапа гидрокрекинга обеспечивают конверсии по каждому периоду прохождения для получения продуктов, имеющих точки кипения ниже 340°С, предпочтительно ниже 370°С, содержание которых превышает 10 вес.%, предпочтительно превышает 15 вес.% и даже 40 вес.%.
Следовательно, выражение «каталитический гидрокрекинг» может охватывать мягкий гидрокрекинг, целью которого является гидроочистка, конвертирующая загрузку, полученную после процесса FCC, и классический гидрокрекинг.
Что же касается классического гидрокрекинга, то он включает в себя схемы на этапе, в первую очередь и как правило содержащем глубокую гидроочистку, целью которой является глубокое гидродеазотирование и глубокая десульфурация загрузки перед тем, как направить весь эфлюент собственно на катализатор гидрокрекинга, в частности, в случае, когда этот катализатор содержит цеолит. Он включает в себя также двухэтапный гидрокрекинг, содержащий первый этап, во время которого так же, как и при «одноэтапном» процессе, осуществляют гидроочистку загрузки, а также достигают конверсии загрузки порядка 40-60%. На втором этапе двухэтапного процесса гидрокрекинга обработке подвергают только фракцию загрузки, не конвертированную во время первого этапа.
Катализаторы для классической гидроочистки, как правило, содержат аморфный носитель и по меньшей мере один гидродегидрогенизирующий элемент (как правило, по меньшей мере один элемент из группы VIB и группы VIII неблагородных металлов, чаще всего по меньшей мере один элемент из группы VIБ и по меньшей мере один элемент из группы VIII неблагородных металлов).
Матрицы, которые могут использоваться в катализаторе гидроочистки отдельно или в смеси, являются, например, глиноземом, галогенсодержащим глиноземом, кремнеземом, кремнеземистым глиноземом, глинами (выбранными, например, из природных глин, таких как каолин или бентонит), магнезией, оксидом титана, оксидом бора, двуоксидом циркония, фосфатами алюминия, фосфатами титана, фосфатами циркония, углем, алюминатами. Предпочитают использовать матрицы, содержащие глинозем, в любых известных специалистам формах, предпочтительнее глиноземы, например, гамма-глинозем.
Описанные выше катализаторы, как правило, используются для обеспечения крекинга фракции полученного от вакуумной перегонки дистиллята в процессе мягкого гидрокрекинга, гидроочистки и на этапе гидроочистки при классическом гидрокрекинге.
Для осуществления такого крекинга загрузку, как правило, вводят в контакт в присутствии водорода по меньшей мере с одним из описанных выше катализаторов при температуре от 330 до 450°С, предпочтительно от 360 до 425°С, и под давлением от 4 до 25 МПа, предпочтительно меньше 20 МПа, и на пространственной скорости от 0,1 до 6 ч-1, предпочтительно от 0,2 до 3 ч-1, и с добавленным количеством водорода, определяемым таким образом, чтобы объемное соотношение в литрах водорода на литр углеводорода составляло от 100 до 2000 л/л.
В случае классического гидрокрекинга фракцию полученного от вакуумной перегонки дистиллята подвергают в зоне гидроочистки глубокой гидрообработке на описанном выше катализаторе для ее гидродесульфурации и гидродеазотизации перед тем, как полностью или частично подавать ее во вторую реакционную зону, содержащую катализатор гидрокрекинга.
Рабочими условиями в реакторе или реакторах этой второй реакционной зоны являются температура, превышающая 200°С, часто находящаяся в пределах от 250 до 480°С, предпочтительно от 320 до 450°С и еще предпочтительнее – от 330 до 420°С, давление, находящееся в пределах от 5 до 25 МПа, предпочтительно ниже 20 МПа, пространственная скорость, составляющая от 0,1 до 20 ч-1, предпочтительно от 0,1 до 6 ч-1 и еще предпочтительнее – от 0,2 до 3 ч-1, и количество водорода, добавляемое таким образом, чтобы объемное соотношение в литрах водорода на литр углеводорода составляло от 80 до 5000 л/л и чаще всего – от 100 до 2000 л/л.
Эта реакционная зона, как правило, содержит по меньшей мере один реактор, содержащий по меньшей мере один стационарный слой катализатора гидрокрекинга. Этому стационарному слою катализатора гидрокрекинга может предшествовать по меньшей мере один стационарный слой описанного выше катализатора гидроочистки. Катализаторы гидрокрекинга, используемые в процессах гидрокрекинга, как правило, являются двухфункциональными и сочетают в себе кислотную группу с гидрогенизирующей группой. Кислотную группу можно вносить в составе носителей, имеющих большую поверхность (как правило, от 150 до 800 м2.г-1) и поверхностную кислотность, таких как галогенсодержащие (в частности, хлорсодержащие или фторсодержащие) глиноземы, комбинации оксидов бора и алюминия, аморфные кремнеземистые глиноземы, называемые аморфными катализаторами гидрокрекинга, и цеолиты. Гидрогенизирующую группу можно вносить при помощи одного или нескольких металлов из группы VIII периодической системы элементов или при помощи комбинации из по меньшей мере одного металла из группы VIB периодической системы и по меньшей мере одного металла из группы VIII.
Катализатор гидрокрекинга может содержать по меньшей мере одну кислотную группу в кристаллическом виде, такую как цеолит Y, или аморфную кислотную группу, такую как кремнеземистый глинозем, по меньшей мере одну матрицу и одну гидродегидрогенизирующую группу. В случае необходимости он может также содержать по меньшей мере один элемент, выбранный из группы, содержащей бор, фосфор и кремний, по меньшей мере один элемент из группы VIIA (например, хлор, фтор), по меньшей мере один элемент из группы VIIB (например, марганец), по меньшей мере один элемент из группы VB (например, ниобий).
Во время этапа г) способа в соответствии с настоящим изобретением осуществляют каталитический крекинг по меньшей мере части первого остатка для получения эфлюента, содержащего бензин, керосин, дизельное топливо и второй остаток.
Специфические условия дезасфальтации на этапе а) способа в соответствии с настоящим изобретением являются такими, чтобы первый остаток, полученный из эфлюента на этапе б) гидроконверсии, имел степень чистоты, достаточную для того, чтобы обеспечить качественный крекинг во время этапа г). В частности, этап а) в соответствии с настоящим изобретением обеспечивает получение на выходе этапа б) эфлюента, предпочтительно имеющего содержание углерода Конрадсона ниже 10 вес.%, предпочтительно ниже 5 вес.%, и содержание азота ниже 3000 пропромилле, что способствует достижению повышенного уровня конверсии остатка, полученного на этапе б), и одновременно повышению выхода бензина, керосина и дизельного топлива. Так, строгое соблюдение условий на этапе а) в сочетании с условиями этапа б) гидроконверсии и этапа г) крекинга обеспечивает повышение выхода бензина, керосина и дизельного топлива в результате осуществления способа в соответствии с настоящим изобретением и улучшение качества этих продуктов. Следует также отметить, что в случае, когда этап г) содержит гидрокрекинг, получаемые в результате каталитического крекинга и каталитического гидрокрекинга продукты имеют качество, достаточное для их непосредственного применения или применения после незначительной дополнительной обработки.
По меньшей мере часть первого остатка, полученного на этапе в), подвергают каталитическому крекингу в условиях, хорошо известных специалистам, для получения, с одной стороны, топливной фракции (содержащей бензиновую фракцию и газойлевую фракцию), которую обычно, по меньшей мере частично, направляют в топливные резервуары, и, с другой стороны, смешанной фракции, которая может быть направлена, по меньшей мере частично или даже полностью, в резервуары для тяжелого топлива или рециркулирована, по меньшей мере частично или даже полностью, на этап г) каталитического крекинга. В рамках настоящего изобретения выражение «классический каталитический крекинг» охватывает крекинг-процессы, содержащие по меньшей мере один этап регенерации путем частичного сжигания, и процессы, содержащие по меньшей мере один этап регенерации путем полного сжигания, и/или процессы, содержащие одновременно по меньшей мере один этап регенерации путем частичного сжигания и по меньшей мере один этап регенерации путем полного сжигания.
Каталитический крекинг может представлять собой процесс, описанный в «Ullmans Encyclopedia of Industrial Chemistry», том A 18, 1991, стр.61-64. Обычно используют классический катализатор, содержащий матрицу, в случае необходимости, добавку и по меньшей мере один цеолит. Количество цеолита может меняться, но обычно составляет примерно от 3 до 60 вес.%, часто примерно от 6 до 50 вес.% и чаще всего – примерно от 10 до 45 вес.%. Обычно цеолит диспергируют в матрице. Количество добавки обычно составляет примерно от 0 до 30 вес.% и часто – примерно от 0 до 20 вес.%. Количество матрицы составляет остающуюся до 100 вес.% часть. Добавку, как правило, выбирают из группы, содержащей оксиды металлов группы IIА периодической таблицы элементов, таких, например, как оксид магния или оксид кальция, оксиды редкоземельных металлов и титанаты металлов группы IIА. Чаще всего матрица является кремнеземом, глиноземом, кремнеземистым глиноземом, кремнеземистой магнезией, глиной или смесями из двух и более указанных материалов. В качестве цеолита чаще всего используют цеолит Y.
Крекинг осуществляют в практически вертикальном реакторе либо в режиме восходящего потока (riser), либо в режиме нисходящего потока (dropper). Выбор катализатора и рабочих условий определяется получением необходимых продуктов в зависимости от обрабатываемой загрузки, как описано, например, в статье М.Марсилли, стр.990-991, опубликованной в журнале Французского Института Нефти за ноябрь-декабрь 1975 г., стр.969-1006. Обычно процесс осуществляют при температуре от примерно 450 до примерно 600°С, при времени нахождения в реакторе менее 1 минуты, часто примерно от 0,1 до примерно 50 секунд.
Каталитический крекинг может также быть каталитическим крекингом в псевдоожиженном слое, например, согласно процессу, разработанному заявителем и названному процессом R2R. Такой каталитический крекинг в псевдоожиженном слое может осуществляться известным специалистам образом при соблюдении условий, соответствующих крекингу для получения углеводородных продуктов с меньшим молекулярным весом. Реактор для каталитического крекинга в псевдоожиженном слое может работать в режиме восходящего потока или в режиме нисходящего потока. Хотя это и не является предпочтительным вариантом осуществления настоящего изобретения, но все же можно предусмотреть осуществление каталитического крекинга в реакторе с подвижным слоем. Предпочтительно в качестве катализаторов каталитического крекинга используют катализаторы, содержащие по меньшей мере один цеолит, обычно в смеси с соответствующей матрицей, такой, например, как глинозем, кремнезем, кремнеземистый глинозем.
Как правило, полученный на этапе г) эфлюент разделяют на фракции, чтобы получить по меньшей мере одну бензиновую фракцию, одну керосиновую фракцию, одну газойлевую фракцию и второй остаток. Это разделение на фракции можно осуществлять любым известным специалистам способом, таким, например, как перегонка. Как правило, осуществляют перегонку при атмосферном давлении с последующей вакуумной перегонкой остатка, полученного от перегонки при атмосферном давлении.
На фиг.1 и 2 схематически показаны основные варианты осуществления способа в соответствии с настоящим изобретением.
Как показано на фиг.1, обрабатываемая углеводородная загрузка поступает по линии 1 в секцию 2 для дезасфальтации в присутствии растворителя, при этом указанный растворитель поступает по линии 3. Фракцию асфальта и часть растворителя, нагнетаемого в секцию 2, извлекают через линию 4 и направляют к секции 5 для разделения растворителя и асфальта. Асфальт извлекают через линию 6. Растворитель извлекают через линию 7 и повторно нагнетают в секцию 2 через линии 8, 1 и 3. Дезасфальтированную фракцию, называемую обычно дезасфальтированным маслом, и часть нагнетаемого в секцию 2 растворителя извлекают через линию 9 и направляют к секции 10 для разделения растворителя и дезасфальтированного масла. Растворитель извлекают через линию 8 и повторно нагнетают в секцию 2 по линиям 8, 1 и 3. Предназначенное для гидрокрекинга дезасфальтированное масло поступает по линии 11 в секцию 12 гидроконверсии в кипящем слое. Добавляют катализатор на линии 13 и извлекают его на линии 14. Водород вводят на линии 15. Обработанный в секции 12 эфлюент направляют по линии 16 в сепараторную секцию 17, из которой после дросселирования через линию 18 извлекают эфлюент, который направляют в дистилляционную секцию 19, из которой извлекают газовую фракцию через линию 20, бензиновую фракцию через линию 21, керосиновую фракцию через линию 22 и газойлевую фракцию через линию 23. Остаток от перегонки при атмосферном давлении по линии 24 направляют в секцию 25 каталитического крекинга. Из секции каталитического крекинга эфлюент по линии 26 подают в дистилляционную секцию 27, из которой через линию 28 извлекают газовую фракцию, через линию 29 – бензиновую фракцию, через линию 30 – газойлевую фракцию и через линию 31 – смешанную фракцию, часть которой направляют в резервуар тяжелого топлива нефтеочистительного завода, при этом другую часть этой смешанной фракции, в случае необходимости, направляют по линии 32 в секцию каталитического крекинга 25, и оставшуюся часть, в случае необходимости, направляют в секцию 12 обработки в кипящем слое. Часть газойлевой фракции из линии 23, в случае необходимости, вместе с остатком из линии 24 направляют в секцию каталитического крекинга 25.
В частном варианте выполнения настоящего изобретения, показанном на фиг.2, остаток, полученный от перегонки при атмосферном давлении в секции 19, направляют по линии 24 на вакуумную перегонку 50, откуда через линию 51 извлекают фракцию дистиллята после вакуумной перегонки, а через линию 52 – фракцию остатка, полученного после вакуумной перегонки. Фракцию дистиллята от вакуумной перегонки направляют в зону каталитического гидрокрекинга. Фракцию дистиллята от вакуумной перегонки по линии 52 направляют в зону 25 каталитического крекинга согласно процессу, описанному со ссылкой на фиг.1.
Настоящее изобретение иллюстрируется нижеследующими примерами испытаний, проведенных в опытных установках.
Пример
Остаток, полученный от вакуумной перегонки (ОВП) тяжелой нефти, дезасфальтируют в присутствии пентана. Остаток от вакуумной перегонки имеет следующие характеристики:
Характеристики остатка от вакуумной перегонки |
|
D 15/4 |
1,06 |
Сера, вес.% |
5,7 |
Ni+V, вес.ппм |
500 |
Азот, вес.ппм |
6800 |
Нерастворимые асфальтены С7, вес.% |
17 |
Углерод Конрадсона, вес.% |
25 |
Рабочие условия этапа дезасфальтации: |
Общая доля растворителя, v/v |
5/1 |
Доля растворителя, нагнетаемого с загрузкой, v/v |
1/1 |
Доля растворителя в нижней части экстракционной колонны, v/v |
4/1 |
Температура в головной части экстракционной колонны,°С |
188 |
Температура в нижней части экстракционной колонны,°С |
158 |
Давление экстракционной колонны, МПа |
4,2 |
Выход дезасфальтированного масла составляет 62 вес.%, и выход асфальта составляет 38 вес.%. Выход рассчитывают, исходя из базового значения 100 (по массе) остатка от вакуумной перегонки.
Дезасфальтированное масло имеет следующие характеристики.
Дезасфальтированное масло |
|
Удельная плотность |
1,01 |
Содержание Никель+Ванадий, вес.ппм |
130 |
Содержание серы, вес.% |
4,6 |
Содержание азота, вес.% |
0,42 |
Углерод Конрадсона, вес.% |
12,0 |
Содержание асфальтенов (не растворимых в гептане) NF-T 60-115, вес.% |
<0,05 |
Дезасфальтированное масло в основном характеризуется содержанием асфальтенов (не растворимых в гептане) согласно стандарту NF-T 60-115, меньшим 0,05 вес.%, что отличает чистое дезасфальтированное масло очень высокого качества.
После этого указанное дезасфальтированное масло подают в присутствии водорода в опытный реактор с кипящим слоем для достижения уровня конверсии в 85 вес.% фракции 524°С+.
Этот реактор содержит 1 литр специального катализатора Т-STAR®, выпускаемого компанией AXENS под ссылочным номером HTS-458 специально для обработки в кипящем слое тяжелого сырья, содержащего металлы.
Процесс осуществляется в следующих рабочих условиях:
– ПЧС относительно уплотненного каталитического слоя: 0,8 ч-1
– Давление водорода: 13,5 МПа
– Рециркуляция водорода: 600 литров водорода на литр загрузки
– Температура в реакторе: 435°С
– Возраст катализатора: 29 дней
Общие характеристики катализатора:
Степень десульфурации HDS, % |
96,7 |
Степень деазотизации HDN, % |
71 |
Степень восстановления углерода Конрадсона |
90 |
HDCCR, % |
|
Степень деметаллизации HDM, % |
99, 9 |
Степень очистки от примеси X определяют следующим образом:
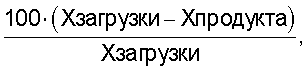
где Хзагрузки обозначает содержание примесей в загрузке, и Хпродукта обозначает содержание примесей в жидком продукте.
Структура выхода, получаемого после лабораторной перегонки ТВР жидкого эфлюента при атмосферном давлении, на выходе реактора с кипящим слоем:
Фракция |
Выход по весу по отношению к дезасфальтированному маслу |
Бензин 1 |
16 |
Керосин 1 |
13 |
Газойль 1 |
18 |
Остаток от перегонки при атмосферном давлении 1 |
42 |
На этом этапе выход бензина, керосина и дизельного топлива по отношению к недезасфальтированному остатку, полученному от вакуумной перегонки, составляет:
Фракция |
Выход по весу по отношению к недезасфальтированному остатку от вакуумной перегонки |
Бензин 1 |
16·0,62=9,9 |
Керосин 1 |
13·0,62=8,1 |
Газойль 1 |
18·0,62=11,2 |
Остаток 1 |
42·0,62=26,0 |
Характеристики сопутствующих продуктов:
Бензин 1 |
|
Сера/азот, вес.ппм |
<50/10 |
Плотность |
0,737 |
Керосин 1 |
|
Сера/азот, вес.ппм |
210/175 |
Плотность |
0,824 |
Газойль 1 |
|
Сера/азот, вес.ппм |
280/500 |
Плотность |
0,866 |
Цетановое число, ASTM D613 |
46 |
Остаток от перегонки при атмосферном давлении 1 |
|
Сера/азот, вес.ппм |
2950/2320 |
Плотность |
0,932 |
Водород RMN, вес.% |
11,8 |
Ni+V, вес.ппм |
<1 |
CCR, вес.% |
2,5 |
Получаемые на этом этапе дистилляты, в частности дизельное топливо, обладают качеством, позволяющим предусматривать незначительную гидрообработку для достижения ими характеристик в соответствии с современными требованиями.
Остаток 1 от перегонки при атмосферном давлении, называемый в рамках настоящего изобретения первым остатком, обрабатывают в классической установке каталитического крекинга. Полученный таким образом остаток характеризуется отличными свойствами чистоты и гидрогенизации. В частности, этот остаток характеризуется низким содержанием углерода Конрадсона, что обеспечивает понижение образования кокса.
Конверсия этого остатка в установке для осуществления процесса FCC на уровне 74 вес.% фракции 360°С+ с целью достижения максимального выхода бензина дает следующие показатели:
Газ и LPG |
|
вес.% остатка от перегонки при атмосферном давлении |
18, 6 |
Бензин2 |
|
вес.% остатка от перегонки при атмосферном давлении |
47,6 |
Содержание серы, вес.ппм |
90 |
Газойль2 (LCO) |
|
вес.% остатка от перегонки при атмосферном |
14, 8 |
давлении |
|
Содержание серы, вес.% |
0,390 |
Смешанная фракция (второй остаток согласно настоящему изобретению) |
|
вес.% остатка от перегонки при атмосферном давлении |
11,6 |
|
|
Кокс |
|
вес.% остатка от перегонки при атмосферном давлении |
7,4 |
Наконец, после этапов дезасфальтации, гидроконверсии в кипящем слое и каталитического крекинга общий выход бензина, керосина и дизельного топлива по отношению к недезасфальтированному остатку от вакуумной перегонки составляет:
Фракция |
Выход по весу по отношению к недезасфальтированному остатку от вакуумной перегонки |
Бензин 1+Бензин 2 |
9,9+12,4=22,3 |
Керосин 1 |
8,1 |
Газойль 1+Газойль 2 |
11,2+3,8=15,0 |
Остаток 2 |
3,0 |
Асфальт |
38 |
Кроме того, полученные дистилляты характеризуются незначительным содержанием примесей (например, серы в дизельном топливе), которое потребует незначительной дополнительной гидрообработки для достижения показателей в соответствии с современными требованиями. Эти дистилляты могут быть использованы в дальнейшем отдельно путем их коммерческой реализации.
Формула изобретения
1. Способ обработки углеводородной загрузки, которая содержит по меньшей мере 95 вес.% соединений с температурой кипения, по меньшей мере равной 340°С, отличающийся тем, что содержит следующие этапы, во время которых а) загрузку смешивают с растворителем для получения дезасфальтированного эфлюента с содержанием асфальтенов меньшим 3000 весовых пропромилле; б) производят крекинг дезасфальтированного эфлюента в присутствии водорода и катализатора гидрокрекинга в реакторе с кипящим слоем таким образом, чтобы конвертировать по меньшей мере 50 вес.% фракции дезасфальтированного эфлюента, кипящего при температуре выше 500°С, в соединения с точкой кипения ниже 500°С; в) эфлюент, полученный на этапе б), разделяют на фракции для получения бензина, керосина, дизельного топлива и первого остатка; г) осуществляют каталитический крекинг по меньшей мере части этого первого остатка для получения эфлюента, содержащего бензин, керосин, дизельное топливо и второй остаток.
2. Способ по п.1, отличающийся тем, что углеводородная загрузка имеет конечную точку кипения, превышающую 600°С.
3. Способ по любому из пп.1 или 2, отличающийся тем, что углеводородная загрузка в основном содержит остатки от перегонки при атмосферном давлении и остатки от вакуумной перегонки тяжелой нефти.
4. Способ по п.1, отличающийся тем, что содержание асфальтенов в дезасфальтированном эфлюенте имеет значение, меньшее 1000 весовых пропромилле.
5. Способ по п.1, отличающийся тем, что содержание асфальтенов в дезасфальтированном эфлюенте имеет значение, меньшее 500 весовых пропромилле.
6. Способ по п.1, отличающийся тем, что используемый на этапе а) растворитель содержит по меньшей мере 50 вес.% углеводородных соединений, содержащих от 3 до 7 атомов углерода.
7. Способ по п.1, отличающийся тем, что этап дезасфальтации осуществляют в экстракционной колонне.
8. Способ по п.1, отличающийся тем, что используемый на этапе б) катализатор является гидроконверсионным катализатором, содержащим аморфный носитель и, по меньшей мере, один металл или металлосодержащее соединение с гидрогенизирующей функциональной группой.
9. Способ по п.1, отличающийся тем, что вслед за этапом в) осуществляют отделение твердых частиц катализатора.
10. Способ по п.1, отличающийся тем, что этап в) содержит перегонку при атмосферном давлении с последующей вакуумной перегонкой.
11. Способ по п.10, отличающийся тем, что дистиллят, полученный от вакуумной перегонки, направляют на этап гидрокрекинга.
РИСУНКИ
|
|