|
(21), (22) Заявка: 2007114128/02, 16.04.2007
(24) Дата начала отсчета срока действия патента:
16.04.2007
(46) Опубликовано: 20.01.2009
(56) Список документов, цитированных в отчете о поиске:
RU 2153955 С2, 10.08.2000. US 2005/0092455 A1, 05.05.2005. КУРДЮМОВ А.В. и др. Производство отливок из сплавов цветных металлов. – М.: Металлургия, 1986, с.247-250. ВОСКОБОЙНИКОВ В.Г. и др. Общая металлурги. – М.: Металлургия, 1998, с.494, 495.
Адрес для переписки:
105005, Москва, ул. Радио, 17, ФГУП “ВИАМ”
|
(72) Автор(ы):
Мубояджян Сергей Артемович (RU), Каблов Евгений Николаевич (RU), Сорокин Анатолий Борисович (RU), Будиновский Сергей Александрович (RU), Фоломейкин Юрий Иванович (RU)
(73) Патентообладатель(и):
Федеральное государственное унитарное предприятие “Всероссийский научно-исследовательский институт авиационных материалов” (ФГУП “ВИАМ”) (RU)
|
(54) СПОСОБ ПОЛУЧЕНИЯ ЛИТЫХ ТРУБНЫХ ИЗДЕЛИЙ ИЗ СПЛАВОВ НА ОСНОВЕ НИКЕЛЯ И/ИЛИ КОБАЛЬТА
(57) Реферат:
Изобретение относится к области металлургической промышленности. Способ включает плавление шихтовых материалов и заливку расплава в предварительно нагретую литейную форму, осуществляемые в двухкамерной вакуумно-индукционной печи. Заливку литейной формы расплавом осуществляют со скоростью 20-50 кг/мин в керамическую оболочковую форму с литниково-питающей системой или форму из литейного графита с заливочной чашей. В качестве сплавов на основе никеля и/или кобальта используют сплавы системы Me-Cr-Al, Me-Cr-Al-Y, где Me-Ni, Co или Ni-Co. Заливку литейной формы проводят при температуре расплава 1420-1600°С. Шихтовые материалы содержат до 60% литейных отходов. Достигается повышение коэффициента использования металла и производительности литых заготовок. 6 з.п. ф-лы, 2 ил.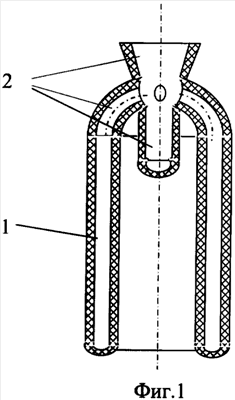
Изобретение относится к области металлургии и машиностроения и может использоваться в авиационном и энергетическом турбостроении, в частности, для получения трубных катодов из материалов покрытий, используемых в качестве расходного материала при вакуумно-дуговом или магнетронном испарении и нанесении ионно-плазменных защитных покрытий на лопатки и другие детали авиационных и промышленных газотурбинных двигателей и установок.
Известен способ получения литых катодов или мишеней из сплавов на основе никеля и кобальта для процесса вакуумно-дугового нанесения покрытий (ЕР 1111086).
Согласно известному способу катод получают путем изготовления слитка из материала катода одним из известных способов, например вакуумно-индукционной плавкой, и последующего электронно-лучевого плавления слитка, рафинирования расплава и его заливки в охлаждаемый кристаллизатор с подвижным подом. Таким способом удается получать заготовки катодов в виде цилиндрических прутков.
Недостатком известного способа является многостадийность технологии изготовления катода и большая трудоемкость процесса его получения.
Известны также способы получения литых катодов в виде цилиндрических прутков, где для получения слитка используется многолучевой электронный нагрев расплавляемого слитка и кристаллизатора (патент США №4838340) или используется многолучевой нагрев и промежуточный лоток для плавки и рафинирования сплава или промежуточная воронка (патенты США №4838340, 4588729, 4190404).
Недостатком известных способов является сложность технологии изготовления слитков для катода и большая трудоемкость процесса его получения, а также высокая стоимость получаемых слитков.
Известен также способ изготовления полой катодной мишени, включающий получение заготовки, содержащей тантал, ниобий или их сплавы, поперечную холодную прокатку заготовки и проведение холодной обработки прокатанной заготовки для получения фасонной заготовки (патент РФ №2261288).
Однако этот способ не позволяет получать методом холодной прокатки трубные изделия из хрупких сплавов для покрытий, имеющих высокую температуру хрупко-вязкого перехода (800°С), что является его недостатком.
Наиболее близким по технической сути к предлагаемому изобретению является способ получения литых трубных изделий из сплавов на основе никеля или кобальта, включающий плавление шихтовых материалов и заливку расплава в предварительно нагретую литейную форму в вакууме, охлаждение литейной формы с отливкой, удаление отливки из формы и ее механическую обработку (Патент РФ №2153955).
Известный способ позволяет получать трубные изделия из сплавов на основе никеля и кобальта. Однако для получения качественных отливок с высокой плотностью 98% требуется специальная формовка литейной формы опорными наполнителями с высокой и низкой теплопроводностью, что повышает трудоемкость изготовления трубных изделий, так как требует каждый раз разделения наполнителей высокой и низкой теплопроводности после удаления отливки из формы. При охлаждении отливки незначительные изменения в тепловом режиме заливки формы или теплоотводе от формы внешней и внутренней части отливки приводят к образованию горячих трещин на внешней поверхности отливки, что приводит к браку по литью и, соответственно, снижает коэффициент использования шихтовых материалов (КИМ). Кроме того, для получения трубных изделий в известном способе используется одноцикловый способ производства, что приводит в целом к снижению производительности способа.
Технической задачей предлагаемого изобретения является создание способа получения качественных литых трубных изделий из металлических материалов с плотностью не менее 98%, обеспечивающего высокий коэффициент использования металла (КИМ) и высокую производительность процесса.
Для достижения технической задачи предложен способ получения литых трубных изделий из сплавов на основе никеля и/или кобальта, включающий плавку шихтовых материалов и заливку расплава в предварительно нагретую литейную форму в вакууме, охлаждение литейной формы с отливкой, удаление отливки из формы и ее механическую обработку, в котором плавку и заливку расплава в литейную форму проводят в двухкамерной вакуумно-индукционной печи, при этом в процессе плавки проводят легирование и очистку расплава при электромагнитном его перемешивании, а заливку литейной формы расплавом осуществляют со скоростью 20-50 кг/мин.
В качестве литейной формы используют керамическую оболочковую форму с литниково-питающей системой или форму из литейного графита с заливочной чашей.
В качестве никелевых и кобальтовых сплавов используют сплавы системы Ме-Cr-Al, Me-Cr-Al-Y, где Me-Ni, Co или Ni-Co
Легирование расплава осуществляют одним или несколькими элементами, выбранными из ряда, включающего кремний, тантал, рений, гафний, вольфрам, молибден, ниобий, титан, железо, бор, углерод или лигатуру на их основе.
Заливку литейной формы проводят при температуре расплава (1420-1600)°С.
Сплавы на основе никеля и кобальта при высоком содержании в них хрома и алюминия (в сумме свыше 25% по массе) обладают в контакте с жаропрочными никелевыми сплавами на воздухе и в продуктах сгорания авиационного и дизельного топлива высокой жаростойкостью и коррозионной стойкостью. Нанесение этих сплавов на лопатки и другие детали авиационных и промышленных турбин обеспечивает ресурс этих деталей, работающих при температурах 900-1150°С.
Использование в качестве литейной формы керамической оболочковой формы или формы из литейного графита позволяет повысить податливость внутренней части оболочки формы. Это обеспечивает получение цилиндрических трубных металлических отливок из никелевых и/или кобальтовых сплавов различного легирования, так как при кристаллизации расплава и последующем охлаждении отливки и ее термической усадки имеет место разрушение внутренней части литейной формы, что, в свою очередь, предохраняет от образования на внутренней поверхности отливки горячих трещин при обычном формовании литейной формы. При этом снижается взаимодействие жидкого расплава с материалом формы, что также обеспечивает получение качественных отливок.
Для формы из литейного графита в качестве стержня используют трубу с толщиной стенки до 5 мм, а заливочную чашу используют частично для формирования прибыльной части отливки.
Использование в качестве вакуумно-индукционной плавильной печи двухкамерной печи, содержащей плавильно-заливочную и загрузочную камеры, разделенные вакуумным затвором, обеспечивает непрерывный цикл получения литых трубных изделий и их высокое качество благодаря тому, что в плавильно-заливочной камере постоянно поддерживается высокий вакуум, и нагретая футеровка не имеет контакта с воздушной атмосферой. Непрерывный цикл получения литых трубных изделий наряду с последовательной заливкой нескольких форм обеспечивает высокую производительность процесса.
Электромагнитное перемешивание расплава, его очистка путем рафинирования и раскисления углеродом и редкоземельными элементами, заливка расплава в предварительно нагретую до определенной температуры литейную форму при скоростях 20-50 кг/мин обеспечивают высокое качество отливок (плотность не менее 98%).
Предварительно нагретую литейную форму помещают в загрузочную камеру непосредственно перед завершением процесса плавки. В зависимости от состава сплава процесс плавки длится от 2 до 3 ч. Поэтому подача литейной формы в плавильно-заливочную камеру непосредственно перед завершением процесса плавки обеспечивает минимальное снижение температуры формы за счет ее радиационного охлаждения в вакууме, чем также достигается высокое качество отливок. Заливка литейной формы расплавом при скоростях 20-50 кг/мин также способствует получению качественной отливки. При скоростях заливки меньше 20 кг/мин на отливках могут образоваться дефекты в виде «непропая», обусловленные быстрой кристаллизацией на стенках формы струй металла с окислением их поверхности, что при продолжающейся заливке формы не позволяет получить металлургическую связь между основной отливкой и закристаллизовавшимися струйками первичного металла на внутренней поверхности литейной формы. Обычно этот дефект проявляется при использовании графитовой литейной формы, имеющей относительно низкую температуру предварительного нагрева. Максимально возможная скорость заливки 50 кг/мин определяется пропускной возможностью заливочной чаши графитовой оболочковой формы или литниково-питающей системы керамической литейной формы, а также механической прочностью литейной формы. Заливка при скорости 20 кг/мин и более обеспечивает получение качественных отливок.
Использование керамических оболочковых форм с литниково-питающей системой или форм из литейного графита с заливочной чашей позволяет устранить пористость в цилиндрической части отливки при минимальной прибыли отливки, что позволяет увеличить КИМ. Увеличение КИМ достигается также и за счет использования в плавке литейных отходов и за счет очистки расплава, позволяющей исключить брак при литье трубных отливок и получать плотные, качественные отливки.
Для формы из литейного графита в качестве стержня (формообразующего элемента внутренней полости трубного изделия) используют трубу из литейного графита с толщиной стенки до 5 мм, причем заливочная чаша, также выполненная из литейного графита, выполняет частично роль прибыльной части отливки, что позволяет для графитовых литейных форм уменьшить прибыльную часть по высоте отливки до (10-12)%, что также приводит к увеличению КИМ.
Дополнительное легирование сплавов на основе никеля и/или кобальта одним или несколькими элементами, выбранными из ряда, включающего кремний, тантал, рений, гафний, вольфрам, молибден, ниобий, титан, железо, бор, углерод или лигатуру на их основе, позволяет расширить номенклатуру литых трубных изделий и получать катоды, которые используются для вакуумно-дугового и магнетронного испарения в установках для нанесения ионно-плазменных жаростойких покрытий, а также различные полые изделия из жаростойких сплавов, используемые в качестве каналов для протекания горячих газов или в качестве каркаса для специальных нагревательных печей.
Получению качественной отливки из сплавов на основе никеля или кобальта способствует также то, что заливку формы в зависимости от конкретного состава сплава проводят в диапазоне температур расплава (1420-1600)°С, что обеспечивает оптимальный тепловой режим при кристаллизации отливки и формирование пористости и рыхлоты либо в литниково-питающей системе отливки, либо в самой верхней части отливки и литейной чаше для случая графитовой литейной формы.
Охлаждение отливки до температуры, равной или менее 1/2 температуры плавления сплава, осуществляется в вакууме. Последующее охлаждение отливки в воздушной среде, что, с одной стороны, не оказывает влияния на качество отливки, а с другой стороны, позволяет загрузить новую форму в загрузочную камеру и тем самым реализовать непрерывный цикл литья при производстве литых трубных изделий, чем в основном достигается высокая производительность способа. Производительность также повышается за счет одновременной загрузки нескольких литейных форм и их последовательной заливке.
Для получения качественной отливки оболочковую керамическую форму перед нагревом предварительно формуют в опоку и нагревают опоку с формой до температуры (950-1050)°С, что обеспечивает направленную кристаллизацию отливки от основания к прибыльной части, чем достигается минимальная пористость и рыхлота в трубной цилиндрической отливке. При этом вся пористость формируется в литниково-питательной части отливки.
Таким образом, совокупность существенных признаков предлагаемого изобретения позволяет получать качественные трубные отливки для изготовления трубных изделий – катодов или мишеней, каналов и каркасов из жаростойких сплавов на основе никеля и кобальта при максимально высоких коэффициенте использования шихтовых материалов и производительности способа.
Сущность изобретения поясняется следующими примерами.
Пример 1. Для получения литого трубного катода из сплава системы Ni -Cr-Al-Y использовали чистые шихтовые материалы – Ni, Cr, Al, Y или лигатуру Ni-Y и 50% литейных отходов никелевых сплавов (отработанные катоды, прибыльную часть отливок). Подготавливали шихтовые материалы и литейные отходы, производили их загрузку в плавильно-заливочную камеру вакуумно-индукционной печи и начинали откачку воздуха в этой камере. В качестве литейной формы использовали керамическую оболочковую форму, показанную на фиг.1. Форма содержит цилиндрическую оболочковую часть 1, переходящую в литниково-питающую систему 2 с заливочной чашей, соединенной с частью 1 формы при помощи 4-х рожковых питателей. Керамическую оболочковую литейную форму формовали в цилиндрическую опоку и нагревали в печи опоку с формой до температуры 950°С. Для плавки и заливки трубных изделий использовали двухкамерную вакуумно-индукционную печь с плавильно-заливочной и загрузочной камерами, разделенными вакуумным затвором. После достижения в плавильно-заливочной камере вакуума 0,6 Па начали процесс плавки. После полного расплавления шихты проводили очистку расплава первичным рафинированием металла при электромагнитном его перемешивании (ЭМП). Затем проводили присадку раскислителей. Затем вводили в расплав алюминий, и после присадки алюминия включали ЭМП. После присадки алюминия опоку (или опоки) с керамической оболочковой формой, нагретую в печи до 950°С, размещали в загрузочную камеру печи и начинали откачку вакуума в этой камере, и после достижения вакуума в загрузочной камере 0,6 Па открывали вакуумный затвор и перемещали опоку с формой в плавильно-заливочную камеру на позицию заливки. Одновременно с размещением опоки с формой в загрузочную камеру давали присадку лигатуры никель-иттрий или чистого иттрия, проводили ЭМП и начинали заливку формы расплавом со скоростью 35 кг/мин при температуре расплава 1510-1520°С. При загрузке в печь нескольких форм производили последовательную заливку этих форм при соблюдении температурно-скоростного режима заливки. Затем после кристаллизации отливки опоку перемещали в загрузочную камеру и начинали процесс охлаждения отливки, закрывали затвор, разделяющий камеры печи, и начинали плавку следующей порции металла. После охлаждения залитой формы до температуры 1/2 температуры плавления сплава подавали воздух в загрузочную камеру печи, производили выгрузку опоки с залитой формой и подготавливали загрузочную камеру печи к следующей загрузке. Таким образом, обеспечивался непрерывный цикл производства отливок. После охлаждения отливки производили выгрузку отливки с формой из опоки, затем очищали отливку от керамики, отрезали прибыльную часть отливки и проводили механическую обработку для получения трубного изделия (катода или мишени) требуемых размеров и чистоты поверхности. Полученное изделие имело плотность 98,7% при КИМ – 94%. Производительность составляла 6 отливок в рабочую смену (две плавки с заливкой трех форм за плавку).
Пример 2. Пример аналогичен примеру 1 и отличается тем, что для получения трубного изделия – газового коллектора, работающего в условиях сульфидной коррозии, из сплава системы Co-Cr-Al-Y или Co-Ni-Cr-Al-Y использовали чистые шихтовые материалы – Со, Ni, Cr, Al, Y или лигатуру Al-Y и 60% отходов. Заливку формы, нагретой до 1000°С, производили при температуре расплава 1580-1600°С при скорости заливки 20 кг/мин. Полученное изделие имело плотность 98,4%, при КИМ – 93,8%. Производительность составляла 6 отливок в рабочую смену (две плавки с заливкой трех форм за плавку).
Пример 3. Пример аналогичен примеру 1 и отличается тем, что для получения трубного изделия – катода в качестве сплава использовали сплав системы Ni-Cr-Al-Y, дополнительно легированный одним или несколькими тугоплавкими элементами W, Hf, Та и Si, и использовали чистые шихтовые материалы. В качестве литейной формы использовали форму из литейного графита, показанную на фиг.2. Форма состояла из основания 3, внутреннего тонкостенного (толщина стенки 3-5 мм) трубного цилиндрического стержня 4, внешней тонкостенной цилиндрической обечайки 5, заливочной чаши 7 с 12 отверстиями для заливки металла и фиксатора 6. Все элементы формы выполнены из литейного графита. Основание 3 и заливочная чаша 7 обеспечивали соосность стержня 4 и внешней обечайки 5, а фиксатор 6 предохраняет заливочную чашу 7 от осевого перемещения вверх. Заливку формы из литейного графита, нагретую до 450°С, проводили при температуре металла 1560-1580°С со скоростью 50 кг/мин. Полученное изделие имело плотность 98,8%, КИМ – 93,6%. Производительность составляла 6 отливок в рабочую смену (две плавки с заливкой трех форм за плавку).
Пример 4. Пример аналогичен примеру 3 и отличается тем, что в качестве сплава трубного изделия – катода использовали высокотемпературный износостойкий сплав с карбидным упрочнением системы Ni-Cr-Mo-W-Fe-Ti-Al-Si-C-B. Заливку металла проводили при температуре расплава 1420-1430°С со скоростью 40 кг/мин в литейную оболочковую графитовую форму, нагретую до 400°С. Полученное изделие имело плотность 98,2%, КИМ – 94,5%. Производительность составляла 6 отливок в рабочую смену (две плавки с заливкой трех форм за плавку).
Из приведенных примеров видно, что предлагаемый способ позволяет получать трубные изделия из металлических сплавов на основе никеля и/или кобальта, в том числе сплавов системы Me-Cr-Al, Me-Cr-Al-Y, где Me-Ni, Co или Ni-Co, и позволяет увеличить в 3-4 раза производительность при литье трубных заготовок по сравнению с известным способом, а также обеспечивает КИМ на уровне 94%, что по оценкам на 20-25% превышает КИМ, достигаемый при известном способе получения трубных изделий.
Лабораторные исследования трубных изделий, полученных в соответствии с предлагаемым техническим решением, показали, что новый способ позволяет получать металлические трубные изделия высокой чистоты. Испытания трубных изделий (катодов) в установках для вакуумно-дугового испарения показали, что предлагаемый способ обеспечивает получение качественных покрытий на лопатках газотурбинных двигателей.
Формула изобретения
1. Способ получения литых трубных изделий из сплавов на основе никеля и/или кобальта, включающий плавку шихтовых материалов и заливку расплава в предварительно нагретую литейную форму в вакууме, охлаждение литейной формы с отливкой, удаление отливки из формы и ее механическую обработку, отличающийся тем, что плавку и заливку расплава в литейную форму проводят в двухкамерной вакуумно-индукционной печи, при этом в процессе плавки проводят легирование и очистку расплава при его электромагнитном перемешивании, а заливку литейной формы расплавом осуществляют со скоростью 20-50 кг/мин.
2. Способ по п.1, отличающийся тем, что в качестве литейной формы используют керамическую оболочковую форму с литниково-питающей системой или форму из литейного графита с заливочной чашей.
3. Способ по п.1, отличающийся тем, что в качестве сплавов на основе никеля и/или кобальта используют сплавы системы Me-Cr-Al, Me-Cr-Al-Y, где Me-Ni, Co или Ni-Co.
4. Способ по п.1, отличающийся тем, что легирование расплава осуществляют одним или несколькими элементами, выбранными из ряда, включающего кремний, тантал, рений, гафний, вольфрам, молибден, ниобий, титан, железо, бор, углерод или лигатуру на их основе.
5. Способ по п.1, отличающийся тем, что заливку литейной формы проводят при температуре расплава 1420-1600°С.
6. Способ по п.1, отличающийся тем, что последовательно заливают расплавом несколько литейных форм.
7. Способ по п.1, отличающийся тем, что шихтовые материалы содержат до 60% литейных отходов.
РИСУНКИ
|
|