|
(21), (22) Заявка: 2005103599/15, 07.07.2003
(24) Дата начала отсчета срока действия патента:
07.07.2003
(30) Конвенционный приоритет:
10.07.2002 DE 10230982.5
(43) Дата публикации заявки: 27.08.2005
(46) Опубликовано: 10.01.2009
(56) Список документов, цитированных в отчете о поиске:
RU 2072195 С1, 20.01.1997. RU 2089585 С1, 10.09.1997. RU 2163947 С2, 10.03.2001. GB 1202303 А, 12.08.1970. US 3655578 А, 11.04.1972. US 3012973 А, 12.12.1961. GB 3630954 А, 28.12.1971.
(85) Дата перевода заявки PCT на национальную фазу:
10.02.2005
(86) Заявка PCT:
EP 03/07235 (07.07.2003)
(87) Публикация PCT:
WO 2004/007367 (22.01.2004)
Адрес для переписки:
105064, Москва, а/я 88, ООО “КВАШНИН, САПЕЛЬНИКОВ И ПАРТНЕРЫ”, пат.пов. В.П.Квашнину, рег.№ 4
|
(72) Автор(ы):
ПУППЕ Лотар (DE), ПАНТКЕ Дитрих (DE)
(73) Патентообладатель(и):
Х.К. Штарк ГмбХ (DE)
|
(54) СОДЕРЖАЩИЙ ГУАНИДИНКАРБОНАТКРЕМНИЕВЫЙ ЗОЛЬ
(57) Реферат:
Изобретение относится к области получения коллоидных растворов для сохранения бумаги. Высокодисперсный стабильный кремниевый золь с агрегированными частицами, ВЕТ-поверхностью больше или равной 100 м2/г и содержанием ионов гуанидиния от 0,05 до 15 мас.%, получают способом взаимодействия при температуре между 50°С и 100°С свежего золя с гуанидинкарбонатом, предпочтительно, в присутствии основания. Процесс проводят в многоступенчатом каскадном реакторе. Концентрирование проводят выпариванием растворителя или ультрафильтрацией. Изобретение обеспечивает возможность получения стабилизированного кремнезоля с желаемой ВЕТ-поверхностью. 2 н. и 15 з.п. ф-лы, 1 табл., 3 ил.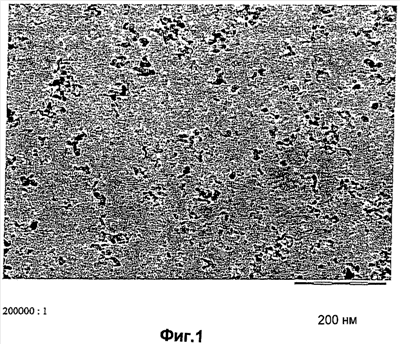
Настоящее изобретение относится к содержащему ионы гуанидиния кремниевому золю, к способу его получения и концентрирования, а также к его применению, например, при сохранении бумаги.
Кремниевые золи являются устойчивыми к седиментации коллоидными растворами аморфного диоксида кремния в воде или спиртах и других полярных растворителях. Они, большей частью, являются водными жидкостями, и имеющиеся на сегодняшний день коммерческие продукты, от части, имеют высокую концентрацию твердого вещества – до 60 мас.% диоксида кремния.
Кремниевые золи имеют разностороннее использование. Например, их используют в качестве связующего для точного литья, для волокон в области огнеупоров (жаропрочных материалов) и при получении катализаторов, в качестве агентов покрытия для пленок (антиблокирование) или кремнистой листовой стали, в текстильном секторе для отделки тканей, предотвращающей раздвижку нитей, в строительном секторе в качестве добавки в торкрет-бетон (пневмобетон) или в качестве биндера (вяжущего, связующего) для использования в противопожарной и тепловой защите, в качестве полировального средства в электронике или также в бумажном секторе при сохранении бумаги или в качестве добавки в покрытия для специальной бумаги.
Традиционные кремниевые золи являются молочно-мутными от сверхопалесцирующих до бесцветно-светлых в зависимости от размера частиц диоксида кремния. Частицы кремниевого золя имеют диаметр от 3 нм до 250 нм, предпочтительно, от 5 нм до 150 нм. Частицы, как правило, шарообразны, пространственно (объемно) ограничены и, преимущественно, электрически отрицательно заряжены. Внутри отдельных частиц обычно находится решетка из силоксановых связей, образованная соединением [SiO4]-тетраэдров или поликремниевых кислот. На поверхности часто расположены группы SiOH. Предпочтительными для различного использования являются стабильные кремниевые золи со специфической поверхностью от около 30 до 1200 м2/г.
При этом стабильность кремниевых золей приобретает большое значение. Особенно кремниевые золи, содержащие очень тонкие частицы диоксида кремния, то есть кремниевые золи с очень высокой специфической поверхностью, склонны к гелеобразованию, в результате чего часто необходима стабилизация. Распространенными методами стабилизации кремниевых золей являются обработка гидроксидами щелочных металлов или модификация поверхности алюминием.
В патенте США US-A-5643414 описан коллоидный высокодисперсный кремниевый золь с высокой специфической поверхностью (ВЕТ-поверхностью) свыше 500 м2/г, стабилизированный обработкой поверхности ионами алюминия. В патенте США US-A-5603805 также описан стабилизированный алюминием кремниевый золь, который, действительно, имеет поверхность менее 700 м2/г.
В патентной публикации США US 6310104 В1 описан тонкодисперсный коллоидный борсиликат. Согласно патентной публикации США US 6310104 В1 такие коллоидные борсиликаты превосходят коллоидные кремниевые золи при использовании в качестве средства для сохранения бумаги.
Общим для всех этих стабилизированных материалов является то, что для стабилизации они содержат на поверхности соединения Si-O-Al или Si-O-B.
Кроме того, из патента США US-A-5221497 известен кремниевый золь, содержащий, так называемые, структурированные или агломерированные друг с другом частицы. Такие структурированные частицы состоят из мелких частичек, собранных в цепеобразные или даже пространственные структуры, в результате чего частица имеет продолговатую структуру. Отдельные частицы в каждом случае расположены в плоскости, в результате чего образуются двухмерные структуры. Для стабилизации необходимо присутствие оксида щелочного металла. Такие кремниевые золи рекомендуются для использования при сохранении бумаги.
В патенте США US-A-3630954 в качестве сырья для получения свежего золя используют, среди прочего, гуанидинсиликат. Согласно примеру 8 для этого сначала получают раствор аморфного гуанидинсиликата при взаимодействии гидроксида гуанидина и кремниевого золя. Затем его деионизируют посредством диметиламиносульфокатионита. На этой стадии удаляют значительную часть ионов гуанидиния и образуют диметиламиносодержащий кремниевый золь, причем мольное соотношение диоксида кремния и гуанидиноксида составляет 7,5:1, а количество диметиламина составляет около 1 моля. Поверхность, определенная основным титрованием по Sears, составляет 1500 м2/г. Золь содержит большое количество диметиламина, обусловленное условиями получения.
При получении кремниевого золя обычно сначала получают свежий золь. При этом речь идет о не содержащем щелочи растворе диоксида кремния, который образуется, например, при удалении катионов щелочных металлов из жидкого стекла. Высаждающийся свежий золь очень не стабилен и поэтому его сразу же стабилизируют повторным подщелачиванием и наращиванием на имеющихся частицах кремниевого золя с одновременной, промежуточной или последующей термической обработкой. Для достижения желаемого содержания диоксида кремния в кремниевых золях затем может дополнительно следовать процесс концентрирования водного раствора. Концентрирование может осуществляться, например, термически упариванием или ультрафильтрацией через мембраны. Для этого пригодны керамические мембраны. Часто кремниевый золь стабилизируют, для чего раствор подщелачивают до мольного соотношения SiO2:Na2O от 40 до 130:1, нагревают часть раствора для увеличения размера частиц до 60-100°С, а затем непрерывно добавляют оставшийся раствор свежего золя и дают возможность наращиваться на уже имеющихся частицах. Одновременно или последовательно может быть предпринято концентрирование раствора до желаемой концентрации. Однако подщелаченный неорганическими основаниями тонкодисперсный кремниевый золь имеет тот недостаток, что специфическая поверхность (ВЕТ-поверхность) не остается стабильной. Поэтому такие кремниевые золи, как правило, стабилизируют ионами алюминия (К. К. Her, The Chemistry of Silica, Wiley & Sons, New York, 1979, Seiten 407-410).
Стабильность к необратимому гелеобразованию с образованием силикагеля, причиной которого является пространственная сшивка с образованием между частицами связей Si-O-Si, уменьшается с возрастанием содержания диоксида кремния, повышением загрязнения электролита и с уменьшением размера частиц. Обычно высокодисперсные кремниевые золи, например, имеющие размеры частиц менее 6 нм, обеспечивают регулирование только до более низкой концентрации твердого вещества, например менее 20 мас.%, чем грубые кремниевые золи из грубых частиц размером более 50 нм, у которых содержание твердого вещества может достигать до 60 мас.%. Повышение стабильности тонкодисперсных кремниевых золей достигается за счет того, что осуществляют поверхностное модифицирование ионами алюминия, как это описано в «The Chemistry of Silica von Her, John Wiley, 1978, Seite 407-410». Однако это поверхностное модифицирование проводится непосредственно после получения кремниевых золей, для чего требуется дополнительная рабочая стадия. Кроме того, в некоторых случаях высокое содержание алюминия при использовании нежелательно.
Задачей настоящего изобретения является получение кремниевых золей, особенно с высокой специфической поверхностью, отличающихся высокой стабильностью, без необходимости модификации ионами алюминия, которые могут использоваться, в особенности, сохранении бумаги.
Теперь было неожиданно установлено, что стабильные высокодисперсные кремниевые золи с агрегированными частицами получают, если в процессе получения использовать гуанидинкарбонат.
Поэтому объектом изобретения является способ получения кремниевого золя, в котором свежий золь подвергают взаимодействию с гуанидинкарбонатом.
При точном проведении реакции, контроле рН, температурном контроле и целевом регулировании (контроле) времени выдержек (обработок) может быть получен продукт с желаемой специфической поверхностью (ВЕТ-поверхностью).
Способ обеспечивает возможность получения стабилизированных кремнезолей с ВЕТ-поверхностью от 100 до 1200 м2/г и концентрацией твердого вещества, например, от 0,05 до 15 мас.%.
При взаимодействии согласно изобретению используют свежий кремниевый золь. При этом речь идет о не содержащем щелочи растворе диоксида кремния, который получают, например, удалением ионов щелочных металлов из жидкого стекла. Обычно употребляемым методом удаления щелочи (обесщелачивания) является обработка разбавленных растворов жидкого стекла смолами-катионитами в Н+-форме. Пригодными ионитовыми смолами являются, например, Lewatit®-типы фирмы Bayer AG. Предпочтительно, растворы жидкого стекла с содержанием диоксида кремния менее 10 мас.% пропускают через ионообменные колонны с кислыми ионитами. Важным является короткое время выдержки в ионообменной зоне, в которой значение показателя рН растворов, предпочтительно, составляет от 5 до 7 для того, чтобы уменьшить гелеобразование в растворе и окремнение смолы-ионита. Получение этих высокодисперсных кислых свежих золей известно, например, из патентов США US-A-2244325 и США US-A-3468813. Для повышения стабильности при хранении, то есть увеличения предельного срока хранения кислых свежих золей, осуществляют охлаждение свежих золей до температуры 0-15°С, предпочтительно, 4-10°С.
Что касается используемого по изобретению свежего золя, то речь идет, преимущественно, о водной системе с содержанием диоксида кремния от 4 до 8 мас.%, предпочтительно, от 5 до 7 мас.%. Как правило, используют свежие золи, содержащие частицы диоксида кремния со средним диаметром частиц, определенным ультрацентрифугированием, менее 5 нм. Предпочтительно используемые свежие золи имеют показатель рН от 2 до 4, особенно предпочтительно, от 2 до 3.
Под указанными показателями рН, если не оговаривается иное, подразумевают показатели рН, определенные при 25°С.
Согласно изобретению свежий золь подвергают взаимодействию с гуанидинкарбонатом. При этом гуанидинкарбонат используют, предпочтительно, в виде водного раствора. Концентрация водного раствора гуанидинкарбоната, предпочтительно, составляет от 5 до 30 мас.%.
Свежий золь и гуанидинкарбонат подвергают взаимодействию друг с другом, предпочтительно, в таких количествах, что массовое соотношение диоксида кремния к гуанидинкарбонату составляет от 150 до 0,2, наиболее предпочтительно, от 60 до 15.
Взаимодействие, предпочтительно, проводят при показателе рН, измеренном при температуре реакции от 8 до 12. Особенно предпочтительно, если при взаимодействии показатель рН, измеренный при температуре реакции, составляет от 8 до 10, наиболее предпочтительно, от 8,5 до 9,5.
Взаимодействие осуществляют, например, при температуре от 25 до 100°С, преимущественно, от 50 до 100°С, особенно предпочтительно, от 80 до 100°С.
Взаимодействие свежего золя с гуанидинкарбонатом согласно изобретению может производиться в присутствии другого основания. Это гарантирует поддержание определенного значения показателя рН и уменьшение гелеобразования. В качестве основания может использоваться, например, калийное или натриевое жидкое стекло, гидроксид калия и/или гидроксид натрия. Предпочтительно, в качестве основания используют натриевое жидкое стекло. Обычно торговое натриевое жидкое стекло имеет состав Na2O·3,34SiO2 и обычно его получают сплавлением кварца с содой или плавлением смеси сульфата натрия и угля, причем получают прозрачное бесцветное стекло, так называемое, кусковое стекло. Это кусковое стекло в размолотой форме реагирует с водой при повышенной температуре и давлении с образованием коллоидных сильно щелочных растворов, которые затем подвергают еще очистке. Известен также спосо6, при котором высокодисперсный кварц или другое пригодное сырье на основе диоксида кремния в гидротермальных условиях со щелочью непосредственно превращается в водные жидкие стекла.
Основание используют, преимущественно, в мольном соотношении диоксида кремния к оксиду натрия от 80 до 20, особенно, предпочтительно от 60 до 30.
Основание может дозироваться, например, в виде водного раствора в реактор, в котором проводят взаимодействие свежего золя и гуанидинкарбоната. Можно также добавлять все основание целиком или по частям непосредственно в раствор гуанидинкарбоната, и эту смесь затем подвергать взаимодействию со свежим золем. Второй вариант предпочтительнее.
Способ по изобретению можно осуществлять непрерывно или периодически. Предпочтительным является непрерывный процесс.
При непрерывном проведении реакции, предпочтительно, свежий золь и водный раствор гуан ид и н карбоната непрерывно вводят в реактор, причем устанавливают рН, измеренный при температуре реакции, от 8 до 12 и температуру между 25°С и 100°С, а время обработки выбирают таким, чтобы полученный кремниевый золь имел ВЕТ-поверхность больше или равную 100 м2/г.
Специфическая поверхность может быть определена либо ВЕТ-методом (S.Brunauer, P.H.Emmet und E.Teller, J. Am. Soc., 1938, 60, S.309) на подвергнутом сушке порошке диоксида кремния, или непосредственно в растворе титрованием согласно G.W. Sears (Analytical Chemistry, Bd. 28, S. 1981, Jg. 1956). В настоящем описании, если не указано иное, специфическую поверхность определяют ВЕТ-методом.
Взаимодействие, преимущественно, проводят при температуре от 50 до 100°С, наиболее предпочтительно, при температуре от 80 до 100°С.
Время взаимодействия, в основном, определяется реакционным объемом и подводимым потоком (притоком) и отводимым потоком (оттоком). В реактор с реакционным объемом от 0,5 до 1 л, предпочтительно, подают от 1,0 до 6,5 л/ч свежего золя и от 0,1 до 0,5 л/ч водного раствора гуанидинкарбоната. На отток можно влиять особенно тем, что во время взаимодействия выпаривают определенное количество воды, причем количество выпаренной воды регулируют выбором температуры.
Способ по изобретению, предпочтительно, проводят в многоступенчатом каскаде реакторов, особенно, в реакторном каскаде из трех расположенных друг за другом реакционных емкостях.
При этом все эдукты (реагенты) подают в первую реакционную емкость. Но возможно также часть потока эдуктов направлять во вторую и последующие реакционные емкости. Однако важно, чтобы, по меньшей мере, часть свежего золя и гуанидинкарбоната подавалась в первую реакционную емкость.
Проведение реакции в многоступенчатом каскаде реакторов способствует созданию пространственно разделенных стационарных режимов относительно значений показателя рН, температуры, среднего размера диаметра частиц, содержания оксида натрия и концентраций диоксида кремния, а также времени взаимодействия. Особенное значение имеет время взаимодействия в каждом реакторе, в который добавляют свежий золь, так как там, предпочтительно, протекает процесс наращивания до более крупных по размеру частиц. Среднее время взаимодействия, предпочтительно, регулируют выпаренным или подлежащим выпариванию количеством воды и добавкой свежего золя в каждый из реакторов, причем посредством выпаривания воды одновременно осуществляется концентрирование. Специфическая ВЕТ-поверхность полученного кремниевого золя определяется главным образом температурой и временем взаимодействия в реакционной емкости, в который вводят эдукты (реагенты).
Аппаратура, в которой осуществляют способ по изобретению, предпочтительно, состоит из нескольких, по меньшей мере, двух расположенных друг за другом и соединенных друг с другом перепускных реакторов. Содержимое каждого из реакционных емкостей перемешивают. Из реакторов посредством соответствующих источников тепла отводится определенное количество дистиллята. Посредством дозирующих устройств осуществляют добавление исходных веществ:
свежего золя, гуанидинкарбоната и, при необходимости, основания, в реакторы, по меньшей мере, в первый из реакторов, расположенный по направлению потока веществ.
При осуществлении способа по изобретению в каскаде реакторов следят за тем, чтобы во всех реакционных емкостях устанавливалось значение показателя рН, измеренного при температуре реакции от 8 до 12, а температура в первом реакторе находилась между 25°С и 100°С. Температура в других реакторах, предпочтительно, составляет от 60°С до 100°С.
Если в одном или нескольких реакционных емкостях устанавливается температура, приблизительно равная температуре кипения используемого растворителя, предпочтительно, воды, то происходит выпаривание растворителя. Таким образом, может быть повышена концентрация диоксида кремния в продукте. Этот процесс называется концентрированием.
При пуске каскада реакторов должно устанавливаться вышеописанное и характерное для изобретения стационарный режим в отношении показателя рН, температуры и среднего времени взаимодействия. Для запуска не требуется обеспечивать все реакторы многоступенчатой аппаратуры соответствующим питанием. Достаточно иметь или получать соответствующее питание в первом реакторе. В качестве питания годится, например, водный щелочной коллоидный раствор кремниевого золя с показателем рН больше 8; водный щелочной коллоидный раствор кремниевого золя, содержащий от 0,1 до 10 мас.% гуанидинкарбоната с показателем рН более 8 или водный щелочной раствор гуанидинкарбоната, содержащий от 0,1 до 10 мас.% гуанидинкарбоната.
Хотя непрерывный способ является предпочтительным, но возможно также осуществление процесса периодическим методом. При этом в реактор загружают, например, по меньшей мере, часть свежего золя и водного раствора гуанидинкарбоната, а остальную часть свежего золя и водного раствора гуанидинкарбоната дозируют в реакционную смесь, причем температуру регулируют так, чтобы выпарить некоторое количество растворителя, соответствующее дозированному количеству свежего золя и водного раствора гуанидинкарбоната.
Как уже отмечалось выше, концентрация диоксида кремния может быть повышена уже в процессе получения посредством выпаривания части растворителя. Однако за процессом собственно получения может также следовать отдельный процесс концентрирования. Концентрирование может осуществляться, например, опять термически посредством выпаривания или также ультрафильтрацией через мембраны. Для этого пригодны, например, керамические мембраны.
Объектом настоящего изобретения является, кроме того, кремниевый золь, полученный способом по изобретению.
Объектом изобретения является также кремниевый золь со специфической ВЕТ-поверхностью от 100 до 1200 м2/г, причем кремниевый золь содержит от 0,05 до 15 мас.% ионов гуанидиния в расчете на общую массу кремниевого золя.
Кремниевый золь по настоящему изобретению имеет низкое содержание алюминия, предпочтительно, менее 50 частей на млн, которым можно пренебречь. Несмотря на это, он характеризуется высокой стабильностью при высокой ВЕТ-поверхности, причем можно устанавливать содержание твердого вещества кремниевого золя до 15 мас.% диоксида кремния.
Концентрация диоксида кремния в кремниевом золе по изобретению, предпочтительно, составляет от 3 до 15 мас.% от общей массы кремниевого золя.
Кремниевый золь, предпочтительно, содержит от 0,1 до 15 мас.% ионов гуанидиния, наиболее предпочтительно, от 0,5 до 10 мас.%.
Кремниевый золь, преимущественно, имеет ВЕТ-поверхность от 300 до 1200 м2/г, более предпочтительно, от 500 до 1000 м2/г, наиболее предпочтительно, от 700 до 1000 м2/г.
В одном из особенных вариантов осуществления изобретения кремниевый золь имеет ВЕТ-поверхность от 400 до 650 м2/г.
Частицы диоксида кремния кремниевого золя по изобретению обладают, преимущественно, широким распределением частиц по размерам, 3-300 нм. Для измерения размеров частиц в нанометрической области помимо электронно-микроскопической фотосъемки, пригодны другие различные методы, такие, например, как лазерно-корреляционная спектроскопия, фотоно-корреляционная спектроскопия, ультразвуковые измерения или измерения с ультрацентрифугированием (седиментацией). Особенно пригодна для определения распределения частиц по размерам ультрацентрифуга, благодаря ее высокой разделяющей способности.
Особенность этих методов измерения заключается в том, что перед собственно измерением осуществляют фракционирование дисперсии по величине частиц. Как известно, в гомогенной дисперсии крупные частицы осаждаются быстрее имеющихся частиц среднего размера и мелких частиц. При просвечивании ячейки ультрацентрифуги лазерным светом в зависимости от времени наступает явно выраженное изменение интенсивности. По этому изменению интенсивности можно рассчитать изменение концентрации частиц и отсюда распределение частиц по размеру.
Поэтому размеры частиц диоксида кремния в кремниевом золе по изобретению определяют посредством ультрацентрифуги.
Средний диаметр частиц диоксида кремния золей по изобретению составляет, преимущественно, от 3 до 30 нм, причем это показатель также определяют посредством обычных коммерческих ультрацентрифуг.
Кремниевый золь по изобретению имеет, предпочтительно, показатель рН от 2 до 12. Особенно предпочтительно значение показателя рН находится между 8 и 11. Область между рН 5 и рН 6 менее предпочтительна, так как кремниевый золь в этой области имеет лишь незначительную стабильность. Затем при показателях рН выше 12 наступает нарастающая пептизация и растворение частиц с образованием раствора силиката щелочного металла.
Высокодисперсный кремниевый золь по изобретению, как правило, имеет агрегированные частицы, когда отдельные сферические частицы диоксида кремния расположены вместе друг с другом и образуют нерегулярные структуры, причем сферические частицы диоксида кремния могут располагаться как в виде цепочки, так и в пространственной форме.
В одном из особенных вариантов кремниевый золь по изобретению не содержит аминов.
На Фиг.1 приведен электронно-микроскопический трансмиссионный снимок (снимок, полученный с помощью просвечивающей электронной микроскопии) кремниевого золя по изобретению. Увеличение составляло 200000:1. Явно видна агрегация частиц.
Кремниевые золи по изобретению обычно имеют вязкость менее 10 мПа·с при содержании твердого вещества 10 мас.%. Указанную вязкость определяют вискозиметром Гепплера при температуре 20°С. Вязкость, предпочтительно, составляет от 1,8 до 2,2 мПа·с при содержании твердого вещества 10 мас.%. Вязкость кремниевого золя зависит, в особенности, от содержания диоксида кремния, размера частиц диоксида кремния, сшивки частиц и содержания электролитов.
Кремниевый золь по изобретению имеет молярное соотношение SiO2/N от 2 до 20, предпочтительно, от 4 до 12. Определение соотношения SiO2/N осуществляют обычным элементным анализом.
Почти все частицы при контакте с жидкостью имеют на своей поверхности заряд. Дзета-потенциал является важным и полезным индикатором заряда поверхности, который может привлекаться для предсказания и контроля стабильности коллоидной суспензии или эмульсии («Zeta Potential A New Approach» by В.В.Weiner, W.W.Tscharnuter and D.Fairhurst, Firmenschrift Brookhaven Instruments). Чем выше дзета-потенциал, тем больше вероятность, что суспензия останется стабильной, так как заряженные частицы взаимно отталкиваются и не агломерируют. Поэтому дзета-потенциал может использоваться для контроля стабильности коллоидной суспензии. Чем выше дзета-потенциал кремниевого золя, тем, следовательно, выше стабильность золя. Коллоидные суспензии с хорошей стабильностью имеют дзета-потенциал между (-30) и (-60) мВ. Коллоидные суспензии со стабильностью от хорошей до экстремальной имеют дзета-потенциал от (-60) и (-100) мВ. При величинах дзета-потенциала ниже (-15) мВ золь не стабилен.
В предпочтительном варианте осуществления кремниевый золь по изобретению имеет дзета-потенциал от (-20) и (-80) мВ, предпочтительно, от (-30) и (-60) мВ.
В предпочтительном варианте осуществления изобретения дзета-потенциал определяют потенциометром Zeta PALS.
По расположению полос ИК-спектра кремниевых золей можно получить представление о структуре. При этом особый интерес может представлять положение пика полос Si-O-колебаний (vsi-o). Поэтому в предпочтительном варианте кремниевый золь по изобретению имеет положение пика полос колебаний Si-O при волновом числе от 1113 см-1 до 1080 см-1, в особенности, от 1113 см-1 до 1100 см-1, наиболее предпочтительно, от 1112 см-1 до 1104 см-1. Дополнительно к вышеописанным пикам полос колебаний Si-O кремниевый золь по изобретению вследствие содержания ионов гуанидиния имеет полосы деформационных колебаний ( N-H) при волновом числе в области от 1750 см-1 до 1640 см-1. ИК-спектры измеряют преобразованием Фурье инфракрасным спектрофотометром Digilab FTS 4000. Достаточно точное расположение полос и формы полос получают при следующих условиях регистрации: спектральная разрешающая способность – 1 см-1; аподизация – камерный кар; фактор нулевого наполнения – по меньшей мере, 2; число сканирований – 32. Согласно инструкции DIN-Vorschrift 55350, часть 13 измерения проводят шестикратно, причем должно, предпочтительно, достигаться стандартное относительное отклонение менее чем 0,1%. Образцы препарируют в виде KBr-прессованной формы. При этом обнаруживается, что спектры не имеют восходящей основной линии (эффект Христиансена, от рассыпания на мелкие частицы), а имеют наибольшие затухания в области 0,7 и 1,3 А. Данные волнового числа относятся к максимуму соответствующих полос (максимум абсорбции). Расположение ИК-полос кремниевого золя по изобретению отличается от кремниевых золей, не относящихся к изобретению, во-первых, величиной пика полос колебаний Si-O, а во-вторых, полос деформационных колебаний N-H ионов гуанидиния вследствие отсутствия ионов гуанидиния в кремниевых золях, не относящихся к изобретению.
На Фиг.2 показан ИК-спектр кремниевого золя по изобретению.
На Фиг.3 показан ИК-спектр кремниевого золя, не относящегося к изобретению.
Кремниевые золи обычно не стабильны к добавке электролита, например, к такой добавке как хлорид натрия, хлорид аммония и фторид калия. Поэтому кремниевы золи по изобретению, предпочтительно, не содержат добавок электролитов.
Кремниевые золи по изобретению пригодны для ряда использовании. Например, можно назвать использование в качестве связующего для точного (прецизионного) литья, в области огнеупорных материалов при получении катализаторов, в качестве агентов покрытий, в текстильном секторе, в бумажном секторе, для отделки тканей, предотвращающей раздвижку нитей, в строительном секторе и в качестве полировальных средств для электроники.
Особенно предпочтительным может быть использование кремниевых золей по изобретению при улавливании сохранении бумаги. Для этого кремниевые золи, как правило, используют в смеси с катионоактивными полимерами. В качестве катионоактивных полимеров могут быть использованы все полимеры, обычно используемые при получении бумаги в качестве средства повышения удерживающей способности и/или влагопрочности. Пригодны как природные полимеры, например полимеры на основе углеводов, так и синтетические полимеры. В качестве примеров могут быть названы канонизированные крахмалы и катионизированные полиакриламиды, полиэтиленимины, полиамидоамины и поли-(диаллил-диметиламмонийхлорид). Предпочтительными катионоактивными полимерами являются катионизированные крахмалы и катионизированные полиакриламиды.
Количество кремниевого золя по изобретению и катионоактивного полимера, которые используют при получении бумаги, может варьироваться в широких пределах и, среди прочего, зависит от вида бумажного сырья, присутствия наполнителей и от других условий.
Количество используемого кремниевого золя, как правило, должно составлять, по меньшей мере, 0,01 кг кремниевого золя в расчете на диоксид кремния на одну тонну сухих волокон и, при необходимости, наполнителей. Предпочтительно, используют от 0,1 до 2 кг кремниевого золя в расчете на диоксид кремния на одну тонну сухих волокон и, при необходимости, наполнителей.
Добавление кремниевого золя и катионоактивных полимеров при получении бумаги осуществляют обычным образом и описано, например, в патенте США US-A-5643414.
В последующем изобретение дополнительно поясняется примерами, причем необходимо понимать, что эти примеры не ограничивают изобретение.
Пример 1
Использовали аппаратуру, состоящую из трех расположенных друг за другом и соединенных друг с другом проточных реакторов из стекла.
Содержимое каждого реактора перемешивают пропеллерной мешалкой. Обогрев содержимого реакторов осуществляют непосредственно паром. Для этого внутрь реакторов помещают нагревательные змеевики, по которым пропускают пар. Вторичный пар отводят через водяной холодильник, конденсируют и затем измеряют объем конденсата.
В первом из трех проточных реакторов через подающее устройство вводили полученный согласно патенту США US-A-2244325 кислый свежий золь. Подающее устройство выбирали таким образом, чтобы можно было бы также вводить добавки в отдельно выбранные реакторы.
Через дозирующее устройство можно было также добавлять раствор гуанидинкарбоната и, возможно, раствор другого основания.
Для повышения стабильности при хранении, то есть увеличения предельного срока хранения, свежего золя, названный раствор охлаждали до температуры 4-10°С.
Щелочной раствор гуанидинкарбоната не подвергали охлаждению, его использовали при температуре окружающей среды. Это был гуанидинкарбонат фирмы Agrolinz.
В трех реакторах устанавливали стационарный режим со средним временем выдержки 14 минут в 1-м реакторе, 16 минут во 2-м реакторе и 20 минут в 3-м реакторе. Для этого прибавляли 3200 мл в час свежего золя, содержащего 5,6 мас.% диоксида кремния, в первый реактор и 260 мл щелочного раствора гуанидинкарбоната в час также в первый реактор, а в последующих реакторах выпаривали 1160 мл воды.
Щелочной раствор гуанидинкарбоната содержал в 945 мл воды 47,7 г гуанидинкарбоната и 9,3 г водного раствора едкого натрия (45 мас.%-ного раствора).
В период стационарного режима в 1-ом реакторе устанавливали температуру 91°С, во 2-м реакторе – 100°С и в 3-м реакторе – также 100°С. Концентрация диоксида кремния в процессе стационарного режима изменялась от 5,6 мас.% в 1-м реакторе до 9,5 мас.% в 3-м реакторе.
Получили высокодисперсный кремниевый золь со структурированными частицами, имеющий плотность 1,065 г/мл, показатель рН 9,7 и ВЕТ-поверхность 480 м2/г.
Пример 2
В описанной в Примере 1 аппаратуре устанавливали стационарный режим со средним временем выдержки: 14 минут в 1-м реакторе, 16 минут во 2-м реакторе и 20 минут в 3-м реакторе, добавлением 1600 мл свежего золя с концентрацией диоксида кремния 5,6 мас.% в час в первый реактор и 128 мл щелочного раствора гуанидинкарбоната в час также в первый реактор и выпариванием 390 мл воды. Щелочной раствор гуанидинкарбоната содержал в 945 мл воды 45,7 г гуанидинкарбоната и 8,4 г водного раствора калия.
Во время стационарного режима в 1-ом реакторе устанавливали температуру 85°С, во 2-м реакторе – 100°С и в 3-м реакторе – также 100°С. Концентрация диоксида кремния изменялась от 5,6 мас.% в 1-м реакторе до 6,1 мас.% в 2-м реакторе.
После 3 часов обработки в стационарном режиме получили в погоне кремниевый золь с содержанием диоксида кремния 6,1 мас.%, показателем рН 8,71 и ВЕТ-поверхностью 698 м2/г.
Пример 3
В этом примере использовали водный раствор гуанидинкарбоната, не содержащий дополнительно основания.
Взаимодействие осуществляли в описанной в Примере 1 аппаратуре. Устанавливали стационарный режим со средним временем выдержки 14 минут в 1-м реакторе, 16 минут во 2-м реакторе и 20 минут в 3-м реакторе. Для этого добавляли 1600 мл свежего золя с концентрацией диоксида кремния 5,6 мас.% в час и 128 мл водного раствора гуанидинкарбоната в час в 1-ый реактор, а в последующих реакторах выпаривали 1160 мл воды.
Водный раствор гуанидинкарбоната содержал в 950 г воды 50 г гуанидинкарбоната.
Во время стационарного режима устанавливали температуру в 1-ом реакторе 87°С, во 2-м реакторе – 100°С и в 3-м реакторе – также 100°С. Концентрация диоксида кремния изменялась от 5,6 мас.% в 1-м реакторе до 5,8 мас.% в 2-м реакторе.
Получили высокодисперсный кремниевый золь со структурированными частицами, имеющий плотность 1,031 г/мл, показатель рН 8,46 и ВЕТ-поверхность 538 м2/г.
Пример 4
В аппаратуру из трехгорловых колб с перемешиванием объемом 2 л помещали 1 л деионизированкой воды и нагревали до 80°С. Затем дозировали 3200 мл кислого свежего золя (5,6 мас.% диоксида кремния) и 256 мл щелочного раствора гуанидинкарбоната в час. Щелочной раствор гуанидинкарбоната содержал в 925 г деионизированной воды 47,5 г гуанидинкарбоната и 9,3 г водного раствора гидроксида натрия (45 мас.%-ного раствора). Насосом откачивали 3456 мл реакционного раствора в час. Среднее время выдержки составило 17 минут.
Полученный кремниевый золь имел содержание диоксида кремния 5,7 мас.%, ВЕТ-поверхность 541 м2/г и показатель рН 8,7.
Пример 5
Этот пример показывает, что кремниевый золь по изобретению может быть получен по периодическому процессу.
В аппаратуру из трехгорловых колб объемом 6 л загружали 3 л смеси, полученной смешением 5064 г кремниевого золя, 3836 г воды, 171,5 г твердого гуанидинкарбоната и 90,2 г натрового жидкого стекла фирмы Cognis. Смесь нагревали до 80°С. Затем дозировали 168 мл/ч описанной смеси и одновременно из реакционной смеси удаляли 168 мл/ч конденсата. Кислый свежий золь (5,6 мас.% диоксида кремния) получали как описано в патенте США US-A-2244325.
После 36 часов получили кремниевый золь со структурированными частицами, имеющий содержание диоксида кремния 12,35 мас.%, ВЕТ-поверхность 300 м2/г и показатель рН 10,4.
У кремниевого золя по изобретению (KBr-прессованные формы, KBr-Pressling) снимали ИК-спектр (Фиг.2). По положению пиков полос колебаний Si-O определяли точным (прецизионным) измерением согласно DIN 55350 (6 измерений) волновое число 1107 см-1.
Для сравнения снимали ИК-спектр не относящегося к изобретению кремниевого золя (KBr-прессованные формы), не содержащего ионов гуанидиния (Фиг.3) и также определяли точным измерением согласно DIN 55350 (6 измерений) волновое число 1114 см-1 для положения пика полосы колебания Si-O.
Результаты точного измерения следующие:
Измерение номер |
Кремниевый золь без ионов гуанидиния (не по изобретению) |
Кремниевый золь, содержащий ионы гуанидиния (по изобретению) |
1 |
1114 |
1105 |
2 |
1116 |
1107 |
3 |
1114 |
1107 |
4 |
1114 |
1107 |
5 |
1115 |
1107 |
6 |
1114 |
1106 |
Кремниевый золь, не относящийся к изобретению, получали следующим образом.
В аппаратуру из трехгорловых колб с перемешиванием объемом 6 л загружали 11,72 г 45%-ного натрового щелока с 250 г деионизированной воды при 80°С. Затем прибавляли в течение 5 минут при перемешивании через капельную воронку 3000 г свежего золя с 5,6 мас.% диоксида кремния (полученного, как описано в патенте США US-A-2244325). Отношение SiO2/Na2O соответствовало 44. При этом температура снижалась до 40°С. Нагревали до 60°С и выдерживали при этой температуре 30 минут, а затем нагревали до температуры кипения и концентрировали раствор при нормальном давлении до содержания твердого вещества диоксида кремния 9,5 мас.%. Кремниевый золь имел ВЕТ-поверхность 535 м2/г и показатель рН 10,06.
Формула изобретения
1. Способ получения кремниевого золя, отличающийся тем, что свежий золь в реакторе подвергают взаимодействию с гуанидинкарбонатом в присутствии основания, благодаря чему осуществляют контроль показателя pH, при температуре между 50 и 100°С, причем среднее время выдержки выбирают так, чтобы полученный кремниевый золь имел ВЕТ-поверхность, большую или равную 100 м2/г, а концентрирование осуществляют выпариванием растворителя или ультрафильтрацией.
2. Способ по п.1, отличающийся тем, что основанием является натриевое жидкое стекло, калийное жидкое стекло, гидроксид калия и/или гидроксид натрия.
3. Способ по п.1, отличающийся тем, что взаимодействие осуществляют при показателе pH от 8 до 12, измеренном при температуре реакции.
4. Способ по п.1, отличающийся тем, что процесс осуществляют непрерывно.
5. Способ по п.1, отличающийся тем, что в реактор непрерывно подают свежий золь и водный раствор гуанидинкарбоната, причем устанавливают показатель pH от 8 до 12.
6. Способ по п.1, отличающийся тем, что взаимодействие осуществляют при температуре от 80 до 100°С.
7. Способ по п.5, отличающийся тем, что в реактор дополнительно добавляют основание.
8. Способ по п.5, отличающийся тем, что реактором является многоступенчатый каскадный реактор, причем эдукты, предпочтительно, вводят в первый реактор.
9. Способ по п.8, отличающийся тем, что показатель pH, измеренный при температуре реакции, во всех реакторах составляет от 8 до 12, а температуру в первом реакторе поддерживают между 50 и 100°С, а в последующих реакторах – между 60 и 100°С.
10. Способ по одному из пп.1-3, отличающийся тем, что взаимодействие осуществляют периодически, причем, по меньшей мере, часть свежего золя и водного раствора гуанидинкарбоната подают в реактор, а остаток свежего золя и водного раствора гуанидинкарбоната дозируют в реакционную смесь и температуру устанавливают такой, чтобы выпарить количество растворителя, соответствующее дозированному остатку свежего золя и водного раствора гуанидинкарбоната.
11. Способ по одному из пп.1-9, отличающийся тем, что концентрирование выпариванием растворителя или ультрафильтрацией осуществляют во время или после взаимодействия свежего золя с гуанидинкарбонатом.
12. Способ по п.10, отличающийся тем, что концентрирование выпариванием растворителя или ультрафильтрацией осуществляют во время или после взаимодействия свежего золя с гуанидинкарбонатом.
13. Кремниевый золь с ВЕТ-поверхностью от 100 до 1200 м2/г, отличающийся тем, что кремниевый золь содержит от 0,05 до 15 мас.% ионов гуанидиния от общей массы кремниевого золя и имеет показатель pH от 2 до 12 и ИК-положение пиков полос колебаний Si-О при волновом числе от 1113 см-1 до 1080 см-1.
14. Кремниевый золь по п.13, отличающийся тем, что он имеет BET-поверхность от 300 до 1200 м2/г.
15. Кремниевый золь по п.13, отличающийся тем, что он не стабилизирован алюминием и не содержит амина.
16. Кремниевый золь по п.13, отличающийся тем, что он имеет отношение SiO2:N от 2 до 20.
17. Кремниевый золь по п.13, отличающийся тем, что он имеет дзета-потенциал от (-20) до (-80) мВ.
РИСУНКИ
TK4A – Поправки к публикациям сведений об изобретениях в бюллетенях “Изобретения (заявки и патенты)” и “Изобретения. Полезные модели”
Напечатано: (54) СОДЕРЖАЩИЙ ГУАНИДИНКАРБОНАТКРЕМНИЕВЫЙ ЗОЛЬ
Следует читать: (54) СОДЕРЖАЩИЙ ГУАНИДИНКАРБОНАТ КРЕМНИЕВЫЙ ЗОЛЬ
Номер и год публикации бюллетеня: 1-2009
Код раздела: FG4A
Извещение опубликовано: 20.02.2010 БИ: 05/2010
TZ4A – Поправки к описаниям изобретений
Часть описания, где обнаружена ошибка: Текст опис., страница 4, строка 27
Напечатано: (K.K.Her, The Chemistry…
Следует читать: (K.K.Iler, The Chemistry…
Номер и год публикации бюллетеня: 1-2009
Извещение опубликовано: 20.02.2010 БИ: 05/2010
TZ4A – Поправки к описаниям изобретений
Часть описания, где обнаружена ошибка: строки 37-38
Напечатано: «The Chemistry of Silica von Her,…
Следует читать: «The Chemistry of Silica von Iler,…
Номер и год публикации бюллетеня: 1-2009
Извещение опубликовано: 20.02.2010 БИ: 05/2010
TZ4A – Поправки к описаниям изобретений
Часть описания, где обнаружена ошибка: страница 9, строки 47-48
Напечатано: В качестве примеров могут быть названы канонизированные крахмалы…
Следует читать: В качестве примеров могут быть названы катионизированные крахмалы…
Номер и год публикации бюллетеня: 1-2009
Извещение опубликовано: 20.02.2010 БИ: 05/2010
TZ4A – Поправки к описаниям изобретений
Часть описания, где обнаружена ошибка: страница 11, строки 23-24
Напечатано: …, ВЕТ – поверхность 541 м2/г…
Следует читать: …, ВЕТ – поверхность 541 м2/г…
Номер и год публикации бюллетеня: 1-2009
Извещение опубликовано: 20.02.2010 БИ: 05/2010
|
|