|
(21), (22) Заявка: 2007108992/02, 12.03.2007
(24) Дата начала отсчета срока действия патента:
12.03.2007
(46) Опубликовано: 20.12.2008
(56) Список документов, цитированных в отчете о поиске:
RU 2069145 C1, 20.11.1996. DE 3044252 A1, 03.06.1982. GB 2044146 A, 15.10.1980. Основы проектирования и технология изготовления абразивного и алмазного инструмента. /Под ред. В.Н.Бакуля. – М.: Машиностроение, 1975, с.255-256.
Адрес для переписки:
61103, Украина, г. Харьков, ул. 23 августа, 51Б, кв.69, А.Б. Черенову
|
(72) Автор(ы):
Черенов Алексей Борисович (UA)
(73) Патентообладатель(и):
Черенов Алексей Борисович (UA)
|
(54) ПРАВЯЩИЙ КАРАНДАШ
(57) Реферат:
Изобретение относится к области абразивной обработки и может быть использовано при производстве абразивного правящего инструмента. В глухом центральном отверстии корпуса правящего карандаша запрессована вставка с равномерно расположенными по окружности или соосно корпусу режущими элементами. Длина последних превышает наибольший размер их поперечного сечения. На режущие элементы надета шайба, имеющая соосные режущим элементам отверстия и жестко прикрепленная к корпусу и вставке. Режущие элементы выполнены с рабочими кромками, расположенными в одной плоскости, перпендикулярной оси правящего карандаша. В результате повышается точность расположения режущих элементов и обеспечивается возможность поочередной правки одним режущим элементом или одновременной правки двумя смежными режущими элементами, что способствует снижению расхода алмазного правящего инструмента и повышению качества и производительности шлифования. 4 з.п. ф-лы, 8 ил.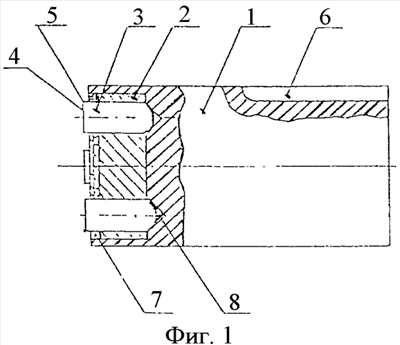
Изобретение относится к конструкциям и производству абразивного правящего инструмента.
Достаточно качественная обработка абразивных кругов при шлифовании деталей с высокими требованиями к их геометрическим параметрам достигается известным инструментом для правки шлифовальных кругов – алмазно-металлическими карандашами с монокристаллом алмаза или несколькими кристаллами, расположенными цепочкой (Основы проектирования и технология изготовления абразивного и алмазного инструмента / Под ред. В.Н.Бакуля. М.: Машиностроение, 1975, с.255, рис.96 и с.256, табл.41 тип Ц).
Минимальная масса режущих элементов в этом инструменте составляет 0,03-0,05 карата, что соответствует их размерам в продольном направлении, равным 1,4-1,8 мм.
При центральном расположении режущих элементов в инструменте долговечность такого инструмента очень мала, т.к. в инструменте, выполненном в виде цилиндра с конусом в его рабочей части, вершиной которого является режущий элемент, этот режущий элемент удерживается недостаточно надежно, а это приводит к тому, что режущий элемент выпадает из корпуса, использовав полезно только одну треть своей величины. Поэтому на практике алмазный инструмент такого типа обеспечивает удовлетворительные результаты тогда, когда масса режущего элемента составляет не менее 0,08-0,10 карата, что соответствует его размерам в продольном направлении, равным 2,0-2,3 мм, которые являются более дорогими.
Однако стойкость их невелика, поэтому режущий элемент после притупления его рабочих кромок необходимо переориентировать, перечеканивать, запаивать и т.д. При этом после двух-трех перечеканок режущий элемент больше вообще не пригоден к работе.
Более надежно удерживаются режущие элементы в правящем карандаше, наиболее близком по технической сущности к заявляемому (см. патент РФ №2069145, МПК 6 В24D 18/00, В24В 53/00, опубл. Бюл. №32, 20.11.96 г.), содержащем корпус, в глухом центральном отверстии которого запрессована вставка с равномерно расположенными по окружности режущими элементами, длина которых превышает наибольший размер поперечного сечения, причем режущие элементы выполнены в виде призмы или цилиндра из поликристаллического материала с нанесенным на их наружную поверхность адгезионно-активным покрытием.
Недостатком такого инструмента является невозможность изготовить правящий карандаш с необходимой точностью расположения режущих элементов равномерно по окружности или по оси корпуса правящего карандаша, а это не позволяет в производственных условиях установить его для работы на станке с минимальными затратами времени, т.к. каждый раз при переустановке правящего карандаша, вызванного износом режущего элемента, приходится искать нужное его положение методом пробных правок. На это уходит много времени и, кроме того, требуется высокая квалификация обслуживающего персонала. Использование в качестве режущих элементов цилиндров и призм из поликристаллического материала также не способствует получению высокого качества правки и снижает, в конечном счете, производительность и качество шлифовальной обработки, а также ограничивает технические возможности использования правящего инструмента.
В основу изобретения поставлена задача такого усовершенствования правящего карандаша, при котором за счет повышения точности взаимного расположения режущих элементов и расположения рабочих кромок в одной плоскости обеспечивается возможность поочередной правки одним режущим элементом или одновременно двумя смежными режущими элементами, что обеспечивает значительное снижение расхода алмазного правящего инструмента, а также повышение качества и производительности шлифовальной обработки.
Для решения этой задачи правящий карандаш, содержащий корпус, в глухом центральном отверстии которого запрессована вставка с равномерно расположенными по окружности или соосно корпусу режущими элементами, длина которых превышает наибольший размер поперечного сечения, согласно изобретению снабжен шайбой с отверстиями по числу режущих элементов, жестко прикрепленной к корпусу и вставке, рабочие кромки режущих элементов расположены в одной плоскости, перпендикулярной оси правящего карандаша, при этом на корпусе правящего карандаша выполнена базирующая канавка, а на дне глухого отверстия выполнены лунки, соосные с режущими элементами и отверстиями в шайбе, выполненной из материала более термостойкого, чем материал вставки; кроме того, количество режущих элементов в одном правящем карандаше связано с размерами режущих элементов в поперечном сечении и расстоянием между ними по дуге окружности их расположения зависимостью, выраженной формулой n= d/(p+S), где
n – количество режущих элементов в правящем карандаше;
р – максимальный размер режущего элемента в поперечном сечении, мм;
d – диаметр окружности расположения режущих элементов, мм;
S – минимальное расстояние между двумя смежными режущими элементами по дуге
окружности расположения режущих элементов, мм, при этом S определено опытным путем и должно удовлетворять условию S больше или равно 2 мм, т.к. при меньшем расстоянии между двумя смежными режущими элементами не обеспечивается надежное закрепление их в правящем карандаше.
Причинно-следственная связь между предлагаемой совокупностью признаков и достигаемым техническим эффектом состоит в следующем.
Наличие в правящем карандаше шайбы с отверстиями по числу режущих элементов, жестко прикрепленной к корпусу и вставке, расположение рабочих кромок режущих элементов в одной плоскости, перпендикулярной оси правящего карандаша, а также выполнение на корпусе правящего карандаша базирующей канавки, а на дне глухого отверстия лунок, соосных режущим элементам и отверстиям в шайбе, выполнение шайбы из материала более термостойкого, чем материал вставки, и установление опытным путем зависимости между количеством режущих элементов в одном правящем карандаше и их размерами в поперечном сечении позволяют обеспечить высокую точность взаимного расположения режущих элементов в правящем карандаше как в процессе его изготовления, так и в процессе эксплуатации.
Предложенная конструкция правящего карандаша имеет преимущества перед известными, заключающиеся в том, что за счет использования каждого из «n» режущих элементов можно значительно увеличить суммарную стойкость правящего карандаша. Кроме того, правка шлифовального круга таким карандашом более стабильна, а следовательно, обеспечивает более высокое качество обработки и производительность.
На фиг.1 и 2 показан общий вид предлагаемого правящего карандаша (вид сбоку и спереди соответственно); на фиг.3 и 4 представлена схема правки шлифовального круга единичным режущим элементом правящего карандаша при наличии в нем четырех режущих элементов (вид сбоку и вид сверху соответственно); на фиг.5 и 6 – схема правки шлифовального круга одновременно двумя смежными режущими элементами правящего карандаша (вид сбоку и вид сверху соответственно); на фиг.7 – схема, показывающая притупление режущих элементов в 4-лезвийном правящем карандаше; на фиг.8 – схема, показывающая притупление единичного режущего элемента, расположенного соосно корпусу правящего карандаша.
Правящий карандаш (фиг.1 и 2) состоит из металлического корпуса 1, в глухом отверстии которого запрессована вставка 2 с закрепленными в ней режущими элементами 3, длина которых превышает наибольший размер поперечного сечения, расположенными равномерно по окружности диаметром d с центром на оси правящего карандаша. Все грани 4 каждого из «n» режущих элементов 3 (на фиг.1 и 2 режущих элементов n=4) расположены в одной плоскости, перпендикулярной оси правящего карандаша, а пересечения наружных поверхностей режущих элементов 3 и граней 4 образуют рабочие кромки 5, которые также находятся в одной плоскости. При этом режущие элементы 3 выполнены преимущественно из кристаллов природных или синтетических алмазов высокой прочности, имеющих форму цилиндров, призм, усеченных конусов или пирамид. Кристаллы алмазов могут иметь и комбинированную из перечисленных выше форму, главное условие, чтобы их длина была больше максимальной диагонали в поперечном сечении кристалла. При этом для получения максимальной точности взаимного расположения не только режущих элементов 3 правящего карандаша, но и их рабочих кромок 5 кристаллы алмазов преимущественно овализованы с максимальным приближением их формы к цилиндру.
Для удобства ориентирования режущих элементов 3 правящего карандаша относительно поверхности шлифовального круга, подвергаемого правке, на наружной боковой поверхности корпуса 1 выполнена продольная базирующая канавка 6. Шайба 7 с отверстиями, соосными режущим элементам 3, жестко прикреплена к корпусу 1 и вставке 2, а лунки 8, выполненные на дне глухого отверстия, в котором запрессована вставка 2, соосные режущим элементам 3, обеспечивают высокую точность взаимного расположения режущих элементов 3 в корпусе 1 правящего карандаша.
Наличие в правящем карандаше одного режущего элемента 3, расположенного соосно с корпусом 1, является частным случаем общего решения задачи, т.к. рабочие кромки 5 его также расположены в одной плоскости и периодический поворот правящего карандаша вокруг его оси позволяет использовать каждый раз новый участок рабочих кромок 5 без дополнительной наладки.
На схемах, иллюстрирующих процесс правки шлифовального круга 9, показанных на фиг.3-6, видно, как производится правка шлифовального круга 9 единичным режущим элементом 3 и одновременно двумя смежными режущими элементами 3.
На фиг.7 показана последовательность образования граней притупления Г1 и Г2 в процессе эксплуатации правящего карандаша, содержащего четыре режущих элемента 3. Установив правящий карандаш в устройство для правки шлифовального круга 9 с использованием базирующей канавки 6 в корпусе 1 правящего карандаша, тем самым устанавливают один из режущих элементов 3 в рабочее положение, т.е. в положение правки шлифовального круга 9 в соответствии с заданным циклом шлифовальной обработки детали. В процессе эксплуатации правящего карандаша рабочая кромка 5 режущего элемента 3 притупляется, образуя грань притупления Г1, после чего правящий карандаш поворачивают вокруг его оси на 90 градусов и производят правку шлифовального круга 9 смежным с ним режущим элементом 3 и.т.д. до получения грани притупления Г1 на четвертом режущем элементе 3. Затем правящий карандаш поворачивают вокруг его оси на 45 градусов, при этом в рабочее положение против шлифовального круга 9 устанавливаются одновременно два смежных элемента 3, и правка шлифовального круга 9 производится двумя смежными режущими элементами 3, образуя грани притупления Г2. Повернув правящий карандаш вокруг его оси 4 раза, получим восемь граней притупления Г2. Описанные операции последовательной правки сначала одним режущим элементом 3, затем двумя смежными режущими элементами 3 можно повторить еще один или несколько раз (это зависит от размера диагонали режущего элемента 3 в поперечном сечении) до полного притупления рабочих кромок 5 всех четырех режущих элементов 3, после чего правящий карандаш снимают с эксплуатации и восстанавливают его рабочие кромки 5 путем доводки граней 4 режущих элементов 3 в плоскости, перпендикулярной оси правящего карандаша одним из известных способов. В примере, показанном на фиг.8, когда правящий карандаш содержит один соосно расположенный режущий элемент 3, в процессе эксплуатации образуются сначала четыре грани притупления Г1, затем – четыре грани притупления Г2, после чего цикл эксплуатации правящего карандаша можно повторить и при полном притуплении рабочих кромок 5 правящий карандаш снимают с эксплуатации и восстанавливают его рабочие кромки 5 путем доводки граней 4 в плоскости, перпендикулярной оси правящего карандаша.
Использование правящих карандашей, выполненных по предложенному техническому решению, обеспечивает значительное снижение себестоимости процесса правки абразивных кругов в шлифовальном производстве, повышает качество и производительность шлифования.
Формула изобретения
1. Правящий карандаш, содержащий корпус, в глухом центральном отверстии которого запрессована вставка с равномерно расположенными по окружности или соосно корпусу режущими элементами, длина которых превышает наибольший размер поперечного сечения, отличающийся тем, что он снабжен шайбой, имеющей соосные режущим элементам отверстия, надетой на режущие элементы и жестко прикрепленной к корпусу и вставке, причем режущие элементы выполнены с рабочими кромками, расположенными в одной плоскости, перпендикулярной оси правящего карандаша.
2. Карандаш по п.1, отличающийся тем, что на наружной боковой поверхности корпуса выполнена базирующая канавка.
3. Карандаш по п.1, отличающийся тем, что дно глухого центрального отверстия выполнено с лунками, соосными режущим элементам и отверстиям в шайбе.
4. Карандаш по п.1, отличающийся тем, что шайба выполнена из материала более термостойкого, чем материал вставки.
5. Карандаш по п.1, отличающийся тем, что количество режущих элементов связано с размерами режущих элементов в поперечном сечении и расстоянием между ними по дуге окружности их расположения и определено по формуле
n= d/(р+S),
где n – количество режущих элементов в правящем карандаше;
р – максимальный размер режущего элемента в поперечном сечении, мм;
d – диаметр окружности расположения режущих элементов, мм;
S – минимальное расстояние между двумя смежными режущими элементами по дуге окружности расположения режущих элементов, определенное опытным путем и удовлетворяющее условию S 2 мм.
РИСУНКИ
|
|