|
(21), (22) Заявка: 2006129292/02, 14.01.2004
(24) Дата начала отсчета срока действия патента:
14.01.2004
(43) Дата публикации заявки: 20.02.2008
(46) Опубликовано: 20.12.2008
(56) Список документов, цитированных в отчете о поиске:
US 4794978 А, 03.01.1989. SU 1156829 А, 23.05.1985. US 3570586 А, 16.03.1971. ЕР 0798060 А1, 01.10.1997. DE 4121169 A1, 25.03.1993. GB 1388378 А, 26.03.1975.
(85) Дата перевода заявки PCT на национальную фазу:
14.08.2006
(86) Заявка PCT:
CH 2004/000014 (14.01.2004)
(87) Публикация PCT:
WO 2005/068108 (28.07.2005)
Адрес для переписки:
103735, Москва, ул.Ильинка, 5/2, ООО “Союзпатент”, А.А.Силаевой
|
(72) Автор(ы):
ЛАУЕНЕР Вильхельм Фридерих (CH), ЛАУЕНЕР Мартин (CH)
(73) Патентообладатель(и):
ЛАМЕК АГ (CH)
|
(54) СПОСОБ НЕПРЕРЫВНОЙ РАЗЛИВКИ ДЛЯ НЕПРЕРЫВНОГО ПОЛУЧЕНИЯ СЛИТКОВ ИЛИ ЛЕНТ ИЗ МЕТАЛЛИЧЕСКИХ И НЕМЕТАЛЛИЧЕСКИХ МАТЕРИАЛОВ, УСТАНОВКА НЕПРЕРЫВНОЙ РАЗЛИВКИ, СПОСОБ ЗАМЕНЫ БЛОКОВ
(57) Реферат:
Установка для получения слитков или лент из металлических или неметаллических материалов содержит гусеничный кристаллизатор, в котором по меньшей мере одна стенка состоит из блоков, выполненных в виде гусеничной ленты. Блоки свободно расположены на транспортном средстве с возможностью обеспечения деформации их в любом направлении при изменениях температуры. На части траектории гусеничной ленты стационарно установлены магниты, обеспечивающие притяжение блоков к направляющим и бесконтактное перемещение блоков по стационарно установленным магнитам. Исключается деформация блоков, снижаются затраты времени на замену блоков, обеспечивается получение слитков любой ширины с высоким качеством. 2 н. и 22 з.п. ф-лы, 15 ил.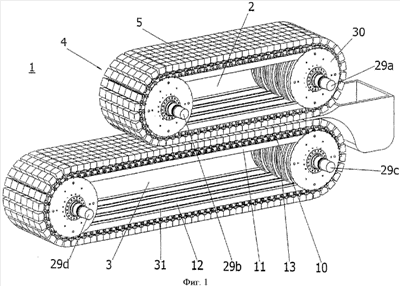
Изобретение относится к способу непрерывной разливки для непрерывного получения слитков или лент из металлических и неметаллических материалов с применением гусеничного кристаллизатора согласно ограничительной части п.1 формулы изобретения, установке непрерывной разливки согласно ограничительной части п.4 и способу замены блоков в установке непрерывной разливки по п.28.
Установки непрерывной разливки применяются для непрерывного получения слитков и лент, называемых ниже заготовками, в частности, из алюминия и его сплавов, других металлов, например цинка, меди, латуни и стали, а также из неметаллических материалов.
Такие способы и устройства были разработаны уже в предпоследнем и последнем столетиях. Здесь следует сослаться на труды Е.Hermann “Handbuch des Stranggiessens”, 1958, и “Handbook on Continuous Casting”, 1980 (Aluminium Verlag, Düsseldorf) (Э.Германн, «Справочник по непрерывной разливке», 1958 г. «Справочник по непрерывной разливке», 1980 г., издательство «Aluminium», г. Дюссельдорф). Наряду с другими конструкциями установок непрерывной разливки создавались также установки непрерывной разливки, в которых кристаллизатор, в котором затвердевает расплав, состоит из металлических блоков, расположенных по всей ширине кристаллизатора и встык друг к другу.
В целях поддержания трения между затвердевающей заготовкой и кристаллизатором по возможности на минимальном уровне блоки перемещали вместе с отливаемой заготовкой с одинаковой скоростью до конца кристаллизатора, где блоки поднимали над отливаемой заготовкой и с помощью цепных колес или по дуговым направляющим отводили на обратную сторону корпуса установки непрерывной разливки и после повторного разворота снова подавали на вход в кристаллизатор.
При этом в зависимости от производственных условий блоки могут состоять из антимагнитного или ферромагнитного материала, преимущественно из меди или алюминия, а также из чугуна или стали.
Разливочные устройства такого типа известны как установки непрерывного литья с гусеничным кристаллизатором, называемые согласно американской терминологии “Machine with Caterpillar-Mold” или “Block-Caster”.
Благодаря приводу блоки обращаются в виде бесконечных гусениц вокруг корпуса установки непрерывной разливки, причем конструкцией предусмотрены два расположенных друг против друга корпуса установки непрерывной разливки, которые позиционированы таким образом, что расстояние между обращенными друг к другу стенками кристаллизатора соответствует толщине отливаемой заготовки с учетом усадки расплава при своем затвердевании.
Другая конструкция отличается тем, что установка непрерывной разливки содержит только один корпус, охваченный гусеничной лентой, причем расплав разливается на гусеничную ленту и затвердевает на ней в виде заготовки. Предпочтительно, чтобы при затвердевании заготовка находилась в атмосфере защитного газа для предупреждения недопустимого окисления на верхней свободной стороне затвердевающего расплава.
Приводимое ниже описание относится специально к установкам непрерывной разливки с двумя противолежащими корпусами и гусеничными лентами. Что касается конструкции и назначения корпусов установки непрерывной разливки и гусениц, то описываемая ниже новизна относится к установкам непрерывной разливки только с одним корпусом и обращающейся гусеничной лентой.
Во время эксплуатации приготовленный в печи расплав поступает по желобу в ванну, расположенную на входной стороне установки непрерывной разливки по всей ширине кристаллизатора, в которой необходимый уровень металла поддерживается регулируемой подачей материала. Отсюда жидкий металл направляется через так называемое впускное сопло в кристаллизатор, ограниченный на входной стороне указанным соплом, на выходной стороне затвердевшей заготовкой и с обеих сторон так называемыми боковыми порогами. При этом направление вытягивания заготовки может быть вертикальным, горизонтальным или наклонным.
Скорость выходящей из кристаллизатора заготовки зависит от ее материала и толщины, а также от физических свойств материала блоков и его температуры на входе в кристаллизатор. Толщина заготовки, обычная для установок непрерывной разливки с гусеничным кристаллизатором, составляет от 1,5 до 3, преимущественно 2 см. Скорость заготовки на выходе из установки непрерывной разливки необходимо регулировать в соответствии с имеющимися условиями и приводить в соответствие с ними, она составляет обычно 2-12 м/мин. После выхода из установки непрерывной разливки затвердевшая заготовка подается обычным образом на последующие рабочие операции.
При движении кристаллизатора блоки воспринимают вследствие контакта с отливаемой заготовкой исходящее от нее тепло и охлаждаются при перемещении вокруг корпуса установки непрерывной разливки с помощью водного хладагента. Согласно опыту толщина блоков, в зависимости от аккумулируемого количества тепла, превышает толщину отливаемой заготовки в 3-5 раз.
Известные установки непрерывной разливки с гусеничным кристаллизатором связаны с большой проблемой, обусловленной физическими причинами.
Вследствие одностороннего нагрева при движении кристаллизатора происходит нежелательная деформация блоков, т.е. перекос, который возрастает с увеличением длины блоков. При этом стенки кристаллизатора становятся неровными, вследствие чего в известных в настоящее время конструкциях образуются местные зазоры между стенкой кристаллизатора и затвердевающей заготовкой. Помимо неравномерности толщины полученной заготовки такие зазоры вызывают неконтролируемый тепловой поток, направленный от заготовки на стенку кристаллизатора, вследствие чего в затвердевающем материале образуются местные, недопустимые тепловые напряжения, приводящие в формирующейся структуре заготовки к недопустимому растрескиванию. Кроме того, места стыкового соединения смежных блоков становятся неплотными, что приводит к образованию дефектов и грата на поверхности заготовки, так как расплав затекает в пустоты и зазоры в стенке кристаллизатора.
К этому добавляется еще проблема, связанная с уплотнением впускного сопла, выступающего внутрь зоны заливки и формирования заготовки, так как обратный поток расплава должен быть обязательно исключен. Очевидно, что уплотнение тем сложнее обеспечить, чем больше деформация блоков.
Тепловые напряжения значительно возрастают в том случае, когда последующее охлаждение блоков происходит на участке поверхности, называемом ниже передней стороной, контактировавшим до этого с расплавом.
В зависимости от величины температурной разницы между нагретыми и охлажденными поверхностями возникающие на этой стороне сдавливающие и растягивающие напряжения могут превысить предел упругости материала блоков, что вследствие усталости материала на передней стороне блоков приводит к сетчатому растрескиванию, из-за чего ухудшается поверхность литого изделия, обстоятельство, которое делает необходимым замену и последующую обработку применяемых блоков после их непродолжительного срока эксплуатации.
Вследствие упомянутой большой термической нагрузки на блоки их следует рассматривать как быстроизнашивающиеся детали, подлежащие периодической замене либо дополнительно обработанными, либо новыми блоками.
Хотя установки непрерывной разливки с гусеничным кристаллизатором и обладают неоспоримыми преимуществами в отношении качества изделий по сравнению с другими работающими в непрерывном режиме установками, однако установки современной конструкции в силу приведенных выше причин, за исключением описываемых ниже установок, смогли утвердиться только в производстве относительно узких заготовок, так как описанная проблематика резко возрастает с увеличением ширины кристаллизатора.
Из патентов США №3570586, №5979539 известны устройства, с помощью которых предпринята попытка воспрепятствовать перекосу блоков также в широких установках, а именно за счет того, что расположенные по всей ширине кристаллизатора балочные блоки закрепляются с помощью мощных крепежных элементов на стальных балках с практически постоянной температурой, момент инерции площадей которых в несколько раз превышает этот же момент блоков, в результате чего удается существенно предупредить недопустимую деформацию блоков. При этом охлаждение блоков происходит при обратном движении разбрызгиванием водного хладагента на стенки кристаллизатора. Эта известная концепция позволяет произвести существенное уширение установки по сравнению с другими конструкциями, благодаря чему с помощью новых или дополнительно обработанных блоков становится возможным производить в течение ограниченного времени заготовки из легированного алюминия высокого качества и шириной до 1,8 м. Такой результат объясняется тем, что наряду с принудительным сохранением плоскостности стенок кристаллизатора может также хорошо регулироваться их температура благодаря большой массе блоков и соответствующему охлаждению, чем достигается оптимальное протекание процесса затвердевания разливаемого материала, в результате чего наряду с повышением качества изделия становится возможным обрабатывать более широкий набор металлов и их сплавов.
Однако многолетний опыт показывает, что приведенные выше проблемы решаются с помощью описанной концепции крепления блоков лишь частично. Хотя деформация блоков вследствие температурного изменения исключена, однако согласно законам сопромата в них возникают соответственно большие напряжения, которые накладываются на образующиеся и без того в стенках кристаллизатора тепловые напряжения с одинаковым знаком, вследствие чего происходит сильное ускорение усталости материала, сопровождающееся образованием трещин. Поскольку после нагрева блоков на поверхность, находившуюся в контакте с отливаемой заготовкой, набрызгивается хладагент, то упомянутый выше эффект значительно ухудшается. Кроме того, как показывает опыт, несмотря на свое крепление на жестких балках блоки по прошествии определенного срока эксплуатации, тем не менее, подвержены короблениям, из-за чего, как указывалось выше, качество изделий снижается. Следствием такого недостатка является то, что после относительно непродолжительного срока эксплуатации блоки приходится заменять, что, учитывая прочность крепления на массивных балках, требует больших трудозатрат и, следовательно, приводит к простою, неблагоприятно сказывающемуся на рентабельности установки.
Учитывая имеющиеся познания и опыт в отношении установок непрерывной разливки с гусеничным кристаллизатором, становится очевидным, что их совершенствование для решения стоящих проблем имеет большое значение для соответствующей отрасли промышленности, так как данный способ разливки при необходимом усовершенствовании обеспечивает по отношению к другим видам разливки очевидные выгоды в отношении рентабельности, многообразия обрабатываемых материалов и их сплавов, а также качества изделия. Пришли к выводу, что успешная эксплуатация возможна лишь при следующих условиях:
A) концепция конструкции установки должна обеспечивать получение заготовок высокого качества при их любой, требуемой промышленностью ширине;
B) замена блоков должна производиться в течение небольшой доли от требуемого для этого времени, что необходимо для сведения к минимуму трудозатрат и простоев;
C) срок службы блоков должен быть значительно увеличен против существующего в настоящее время.
Опыт показывает, что деформация блоков при прохождении кристаллизатора для соблюдения требования равномерного протекания процесса затвердевания образующейся заготовки и, следовательно, теплового потока, поступающего от нее на стенку кристаллизатора, должна составлять, в зависимости от характера затвердевания отливаемой заготовки, не более 0,1-0,2 мм.
По физическим причинам при нагреве или охлаждении абсолютное изменение размера и формы свободного тела зависит от его размеров, коэффициента расширения соответствующего материала и температурных соотношений. Если, например, вытянутое тело прямоугольного сечения, какими являются в настоящее время блоки установок непрерывной разливки с гусеничным кристаллизатором, имеет асимметричный температурный профиль в отношении проходящей в продольном направлении тела средней линии по сечению, то реакцией тела является его прогиб. Если линейная мера длинного тела по сравнению с коротким телом увеличивается линейно, то абсолютная величина прогиба возрастает при одинаковом сечении тел и идентичном температурном профиле приблизительно в квадрате соотношения длин сравниваемых тел.
Из патента США №3570586 известен прием, при котором балочные блоки, расположенные по ширине кристаллизатора, режут на относительно короткие отрезки, называемые ниже блочными элементами, связывают их в боковом направлении с помощью тяг и образовавшиеся при этом блоки, жесткость которых снизилась по сравнению с монолитными блоками, закрепляют на жестких балках с практически постоянной температурой, за счет чего в значительной степени могут предупреждаться деформации при изменениях температуры в блоках.
Однако такая известная конструкция оказалась слишком дорогостоящей, так как при ней необходимо регулярно производить замену износившихся деталей. Кроме того, было установлено, что во время эксплуатации вследствие длительных изменений температуры происходят смещения элементов, в результате чего требуемая плоскостность блоков не обеспечивается на длительный срок. Следовательно, успех, ожидаемый на основании этого кажущегося решения, достигнут не был и из-за этого пришлось отказаться от его применения в производственной практике.
Кроме того, как упоминалось выше, соответствующая концепция, предусматривающая замену блоков, требует вследствие отсоединения и закрепления последних на своих балках больших трудозатрат и соответственно длительного простаивания всей производственной линии. Также при температурных изменениях элементы блоков лишены возможности свободной деформации из-за своего жесткого соединения с балкой, что, как уже было сказано, вызывает дополнительные напряжения в элементах и, следовательно, отрицательно влияет на их срок службы.
В изобретении поставлена задача создания установки непрерывной разливки, способной обеспечить экономически успешное применение установок непрерывного литья с гусеничным кристаллизатором в условиях, приведенных в пунктах А), В), С).
Поставленная задача решается в изобретении в способе непрерывной разливки с применением гусеничного кристаллизатора, признаки которого приведены в п.1 формулы изобретения, и установки непрерывной разливки, признаки которой приведены в п.4.
Преимущества изобретения состоят, главным образом, в том, что благодаря установке непрерывной разливки:
– при прохождении блоков через зону заливки и формирования слитка стенки кристаллизатора сохраняются ровными, благодаря чему по всей их ширине и длине возможны контролируемое охлаждение и равномерная толщина формируемой заготовки, что является условием получения этим способом изделий высокого качества из легированного материала и с любой шириной, необходимой для промышленности;
– возможна замена блоков в течение времени, составляющего небольшую долю от необходимого ранее времени, и благодаря этому
– трудозатраты и простои всей производственной установки при замене блоков могут быть сокращены до минимума.
Согласно предпочтительному варианту выполнения изобретения соотношение между частью t, на которой блоки удерживаются стационарными магнитами на транспортирующем средстве, и всей траекторией обращения U соответствующей гусеничной ленты, t:U, составляет 0,55-0,95. Этим достигается то преимущество, что блоки удерживаются стационарными магнитами только в том месте на транспортном средстве, где они могли бы упасть под действием силы тяжести. На участке, на котором стационарные магниты отсутствуют, блоки могут удаляться с помощью подъемника без отсоединения средств крепления от транспортного средства.
Другие предпочтительные варианты выполнения изобретения охарактеризованы в зависимых пунктах формулы изобретения.
Ниже подробнее поясняются изобретение и варианты его развития с помощью частично схематических изображений нескольких примеров выполнения.
При этом изображено на:
фиг.1 – вид в перспективе на вариант выполнения установки непрерывной разливки согласно изобретению с двумя гусеничными лентами;
фиг.2 – вид сбоку на кристаллизатор установки непрерывной разливки, вариант выполнения которой показан на фиг.1;
фиг.3 – сечение, выполненное перпендикулярно продольному направлению по гусеничной ленте в зоне приводной оси с электромагнитным перегибом гусеничной ленты и соответствующими токопроводами;
фиг.4 – увеличенный вырыв из изображения на фиг.3;
фиг.5 – увеличенный вырыв из изображения на фиг.3;
фиг.6 – вид в перспективе на раму с двумя блочными элементами в варианте выполнения установки непрерывной разливки согласно изобретению;
фиг.7 – частичный разрез по раме с двумя блочными элементами в варианте выполнения установки непрерывной разливки согласно изобретению на фиг.6;
фиг.8 – увеличенный вырыв из частичного разреза на фиг.7;
фиг.9 – вид в перспективе на траверсу с блоками в варианте выполнения установки непрерывной разливки согласно изобретению;
фиг.10 – увеличенный вырыв в соответствии с позицией Е на фиг.9;
фиг.11 – вид сбоку на блок в изображенном на фигурах 9 и 10 варианте выполнения установки непрерывной разливки согласно изобретению;
фиг.12 – разрез по А-А на фиг.11;
фиг.13 – увеличенный вырыв согласно позиции В на фиг.12;
фиг.14 – разрез перпендикулярно продольному направлению, выполненный по нижней гусеничной ленте в варианте выполнения установки непрерывной разливки согласно изобретению;
фиг.15 – разрез по В-В на фиг.14.
Приводимое ниже описание касается установок с двумя противолежащими корпусами и гусеничными лентами, в которых вытягивание заготовки производится горизонтально или в слегка наклонном направлении, однако по своему смыслу оно действительно и для установок с вытягиванием заготовки в вертикальном или сильно наклонном направлении, а также для установок с одной гусеничной лентой в той части, что касается конструкции гусеничной ленты и крепления блоков.
Принцип устройства описываемой установки непрерывной разливки 1 показан на фиг.1. Жидкий металл подается обычным образом через впускное сопло в кристаллизатор, образованный блоками 4 в виде гусеничных траков, обращающихся вокруг верхней и нижней гусеничных лент 2, 3 с помощью не показанного привода. С обеих сторон кристаллизатор выполнен закрытым согласно уровню техники не показанными стационарными или совместно передвигающимися боковыми порогами.
Как показано на фигурах 6, 7, например, два блочных элемента 5, смежных между собой в боковом направлении, связаны друг с другом с помощью рамы с возможностью теплового расширения. Каждая рама 7 содержит две разнесенные между собой в продольном направлении гусеничные ленты 2, 3, расположенные в боковом направлении и выполненные в виде прутков траверсы 6 из ферромагнитного материала, которые связаны друг с другом расположенными в продольном направлении гусеничных лент резьбовыми поперечными связями 23. Между каждыми двумя траверсами 6, в зависимости от ширины зоны заливки и формирования слитка, встроен один или несколько блочных элементов 5 таким образом, что поперечные связи 23 заходят в расположенные в продольном направлении, открытые с боков пазы 22 подвесных устройств 21. При этом боковые расстояния между поперечными связями 23 столь велики, что между этими связями 23 и стенкой пазов 22 сохраняется компенсационный зазор S в боковом направлении (фиг 8). Благодаря такому выполнению рам 7 блочные элементы 5 могут расширяться в боковом направлении, не испытывая помех со стороны поперечных связей 23. Кроме того, в зоне своих подвесных устройств 21 блочные элементы 5 выполнены сужающимися в продольном направлении гусеничных лент 2, 3 в соответствии с расстоянием между прутковыми траверсами 6. На своей нижней стороне траверсы 6 содержат зарубки 32, с помощью которых они заходят в цепи 10 (фиг.1).
Как изображено на фигурах 9-13, блочные элементы 5, расположенные в рамах 7 и прилегающие друг к другу с боков, объединены с возможностью пружинения с помощью тяг 16 с образованием блока 4, расположенного по всей ширине гусеничных лент 2, 3. Тяги 16 проложены вдоль траверс 6. Для беспрепятственного прохождения тяг 16 мимо блочных элементов 5 траверсы 6 выполнены сужающимися вверх. По боковым ограничивающим линиям собранного таким образом блока 4 тяги 16 заходят каждая в пружинящую опору 14, предусмотренную на расположенных снаружи рамах 7. Пружинящие опоры 14 примыкают снаружи к выступающим сбоку блочным элементам 5 и содержат выполненные в боковом направлении сверления 26, в которых располагаются надвинутые снаружи по тягам 16 натяжные пружины 15. На конце тяги 16 снабжены резьбой 27, на которую накручиваются гайки 18, создающие предварительный натяг. Кроме того, между гайками 18 и натяжными пружинами 15 расположено по одному нажимному сухарю 17. С помощью гаек 18 предварительной затяжки натяжные пружины 15 предварительно напрягаются в осевом направлении, в результате чего пружинящие опоры 14 прижимаются сбоку к блокам 4. В результате блочные элементы 5, расположенные по ширине корпуса 2, 3 установки непрерывной разливки, сжимаются под действием пружинного усилия и могут расширяться в боковом направлении встречно действию пружинных усилий.
Следовательно, описываемое ниже изобретение заключается в том, что расположенные по ширине кристаллизатора блоки 4 состоят в боковом направлении из нескольких частей, называемых далее блочными элементами 5, которые располагаются внутри рам 7 из намагничиваемого материала и удерживаются таким образом, что они беспрепятственно деформируются при изменении температуры и что составные блоки 4, как единое целое, располагаются на транспортных средствах в виде цепей 20 (фиг.2), снабженных преимущественно роликами 10 (фиг.15) и обращающихся по бесконечным траекториям вокруг соответствующих корпусов установки, причем между направляющими 11 (фиг.1) цепей 20 (фигуры 2, 3) на нижней стороне гусеничных лент 2, 3 расположены магниты, преимущественно магнитные направляющие 12 (фигуры 1, 5), а на входной и выходной сторонах 19а, 19b (фиг.2) кристаллизатора – стационарные магнитные дуговые направляющие 13 (фиг.1), которыми рамы 7 с нагруженными в них блочными элементами 5 и цепи притягиваются к направляющим 11 и перемещаются по ним таким образом, что рамы 7 скользят бесконтактно по неподвижным магнитным направляющим 12 и магнитным дуговым направляющим 13, при этом по ширине кристаллизатора могут располагаться несколько цепей 20, расстояние между которыми задается таким, чтобы исключался недопустимый прогиб находящихся на цепях 20 рам 7 и, следовательно, расположенных по ширине кристаллизатора составных блоков 4, в результате чего лишь при незначительной деформации относительно небольших блочных элементов 4 и благодаря их определенному постоянному положению внутри рам 7 образуются практически ровные стенки кристаллизатора, несмотря на температурные изменения при движении кристаллизатора и независимо от его длины и ширины, причем блоки 4 располагаются на верхней стороне корпусов 2, 3 установки непрерывной разливки свободно на цепях 20 и при замене с помощью снабженного захватным приспособлением подъемника могут быть сняты или посажены без дополнительных затрат времени и труда на их отсоединение и закрепление.
Размер блочных элементов 5 зависит от допустимой деформации при прохождении кристаллизатора. Согласно настоящему изобретению, основанному на исследованиях и опыте, размер блочного элемента 5 в боковом направлении не должен превышать 25 см (фиг.3 “h”).
Согласно настоящему изобретению максимальное расстояние между опорами рам, т.е. в данном случае расстояние между двумя цепями, не должно превышать 30 см (фиг.3 “i”).
Магнитные силы должны надежно удерживать блоки 4 на нижней стороне гусеничных лент 2, 3, а также на магнитных дуговых направляющих 13, расположенных на входной и выходной сторонах 19а, 19b кристаллизатора. Это условие может быть соблюдено только благодаря точному перемещению несущих блоки 4 рам 7 по магнитным рельсам 12 и магнитным дуговым направляющим, причем расстояние j между этими направляющими и скользящими по ним рамами 7 с блоками 4 по физическим причинам должно составлять лишь несколько десятых долей миллиметра (фиг.5).
Согласно изобретению названное условие соблюдается в том случае, когда стационарные магнитные дуговые направляющие 13 и дуги направляющих 11 цепей 20 содержат подшипники скольжения или качения 28 и располагаются между цепными колесами 30, находящимися в зацеплении с цепями 20 и сидящими на своих вращающихся приводных валах 29 на входной и выходной сторонах кристаллизатора, за счет чего достигается необходимая концентричность магнитных дуговых направляющих 13 с направляющими 11 цепей 20 и их точное позиционирование по отношению к гусеничным лентам 2, 3 и цепным колесам 30, в результате чего не оказывается воздействия на воздушный зазор между магнитными дуговыми направляющими 13 и перемещающимися по ним блоками 4 даже при смещении приводных валов 29 на корпусе установки непрерывной разливки при регулировке с целью установки наиболее оптимального расстояния между валами.
Согласно изобретению нижняя гусеничная лента 3 в установках непрерывной разливки с горизонтальным или слегка наклонным направлением вытягивания заготовки имеет на выходной стороне 19b большую длину (фиг.2 “k”), чем верхняя гусеничная лента (фиг.2 “I”), за счет чего расположенные на нижней гусеничной ленте блоки 4 аналогично верхним блокам могут беспрепятственно заменяться, при этом с помощью привода установки их постепенно смещают на удлинение (фиг.2 “k-I”).
Согласно изобретению на расположенном на выходной стороне удлинении нижней гусеничной ленты 3 может быть предусмотрено дополнительное охлаждение, воздействующее на верхнюю сторону выходящей заготовки, в результате чего скорость выхода полученной заготовки и, следовательно, производительность установки непрерывной разливки 1, а также срок службы блоков 4 существенно возрастают, поскольку соответственно уменьшается отбираемое от них количество тепла.
Охлаждение может производиться обдувкой поверхности заготовки воздухом или обрызгиванием жидким хладагентом, который известным образом отсасывается с поверхности заготовки и снова отводится в циркуляционный контур. Для замены блоков 4 охлаждающее устройство, снабженное преимущественно роликами и установленное на направляющие, смещается на необходимое расстояние в направлении вытягивания заготовки и этим обеспечивается доступ к блокам 4.
В установках непрерывной разливки с вертикальным или сильно наклоненным направлением вытягивания заготовки магнитное притяжение в верхней точке дуговых направляющих над участком из трех-четырех блоков 4 отсутствует, вследствие чего блоки на этом участке располагаются на цепях 20 свободно и, следовательно, при соответствующем дальнейшем движении цепей 20 все блоки 4 могут быть сняты и заменены.
Согласно настоящему изобретению замена блоков 4 отличается тем, что плита, подвешенная горизонтально на подъемнике, снабженная на нижней стороне уплотнениями и связанная с вакуумной системой, опускается на заменяемые блоки 4, затем приводится в действие вакуумная система, расположенная между плитой и блоками, путем открывания соответствующих клапанов, блоки 4 надежно присасываются к плите и могут быть заменены подъемником при доле затрат времени и труда, незначительной по отношению к прежним.
Очевидно, что приведенные в пунктах А) и В) условия могут быть также соблюдены применением опубликованных изобретений.
Использование магнитных сил в установках непрерывной разливки известно. В патенте США №4794978 описан боковой порог с его шарнирно соединенными между собой узлами, обращающимися по замкнутой траектории, при этом блоки порога состоят из держателя с постоянным магнитом и сменного блока из ферромагнитного материала, причем этот блок притягивается магнитом и таким образом удерживается на держателе. При этом блоки прочно установлены на магниты, обращающиеся по всей траектории, и в отличие от настоящего изобретения постоянно испытывают магнитное притяжение. Очевидно, что при замене блоков их приходится отсоединять в отдельности от держателя с приложением соответствующего усилия. При этом не предусмотрена и практически не осуществима одновременная замена нескольких блоков. Поскольку блоки порога должны состоять из ферромагнитного материала, то не представляется возможным применение однородных блоков с высоким коэффициентом теплопроводности, например, из меди или алюминия. В отличие от такого известного применения техническим решением согласно настоящему изобретению предусмотрены не совершающие совместное движение магниты, а неподвижные магнитные направляющие 12, по которым бесконтактно скользят блоки 4, причем магнитные направляющие 12 на верхней стороне гусеничных лент 2, 3 имеют нарушение сплошности, в результате чего блоки 4 на этом участке оказываются не закрепленными и удерживаются на цепях 20 под действием собственного веса, за счет чего их замена может производиться в самое короткое время.
Другой известный случай применения магнитных сил в установке непрерывной разливки с гусеничным кристаллизатором состоит согласно выложенному описанию изобретения Германии №4121169 А1 в том, что образующие кристаллизатор блоки разворачивают с помощью расположенных на обоих концах кристаллизатора устройств на 180° со стороны корпуса установки непрерывной разливки в сторону встречной направляющей, при этом блоки захватываются четырьмя установленными на крестовине магнитами и удерживаются ими во время перемещения.
Конструкция и назначение при таком применении значительно отличаются от описываемого изобретения, в котором не предусмотрено применение подвижных магнитных головок для перемещения блоков по направляющей. Групповая замена блочных элементов установки непрерывной разливки упомянутой раскрытой конструкции не предусмотрена и не осуществима.
В установках непрерывной разливки, в которых кристаллизатор состоит из совместно перемещающихся тонких стальных лент (Belt-Caster), нежелательному перекосу лент вследствие нагрева при прохождении через зону заливки и формирования слитка можно противодействовать магнитными силами (патент Англии №1388378, патент LX №79065).
Очевидно, что принципиальное отличие настоящего изобретения состоит в назначении и характере известных случаев применения магнитов. В данном изобретении исключается падение блоков 4, располагающихся без дополнительного крепления на дуговых направляющих на входе и выходе из зоны заливки и формирования слитка и на нижней стороне гусеничных лент 2, 3.
Для обеспечения существенно более длительного срока службы блоков 4 по сравнению с имеющимися в настоящее время установками непрерывной разливки необходимо до минимума снизить вызванные теплом, циклические чередующиеся напряжения для задержки образования трещин на передней стороне блоков 4 вследствие усталости их материала. Как уже описывалось выше, блоки 4 согласно изобретению удерживаются в их рамах 7 таким образом, что в случае температурных колебаний они могут беспрепятственно деформироваться по всем трем размерам для исключения возникновения в блоках 4 дополнительных вредных напряжений вследствие воздействующих на них извне крепежных усилий. В результате усталость материала блоков снижается и достигается более длительный срок эксплуатации.
Согласно варианту выполнения настоящего изобретения охлаждение предусмотрено только для задней стенки блоков 4, за счет чего в них постоянно присутствует равнонаправленный тепловой поток, благодаря которому существенно снижается разница между максимальной и минимальной температурами на критической передней стороне, что приводит также к снижению возникающих чередующихся тепловых напряжений, в результате чего достигается значительное продление срока службы блоков, свободная деформация которых не нарушается и, кроме того, передняя сторона которых охлаждается. Согласно известной практике срок службы блоков 4 может быть дополнительно существенно продлен за счет того, что на переднюю сторону блоков наносится теплоизоляционное защитное покрытие из керамического материала.
Согласно настоящему изобретению срок службы существенно увеличивается при размещении на передней стороне блоков 4 фольги толщиной в несколько десятых долей миллиметра, например, из стали или титана, прочность которой существенно превосходит прочность материала блоков, благодаря относительно меньшему коэффициенту теплопроводности она служит одновременно в качестве теплового экрана, в результате чего снижается максимальная температура на расположенной под фольгой поверхности материала блоков, что соответственно снижает возникающие и периодически чередующиеся тепловые напряжения и, следовательно, усталость.
Как упоминалось выше, дополнительное увеличение срока службы блоков 4 достигается вторичным охлаждением отлитой заготовки на удлинении нижнего корпуса установки непрерывной разливки.
При осуществлении описанных мероприятий соблюдается также указанное выше необходимое условие С).
Показанная на фигурах 14 и 15 система охлаждения блоков 4 в описанной установке непрерывной разливки действует следующим образом: охлаждающая жидкость под давлением подается в расположенный по всей ширине зоны заливки и формирования слитка короб и течет от него по каналам 8 подачи хладагента, расположенным на верхней стороне гусеничных лент 2, 3 параллельно направлению вытягивания заготовки между направляющими цепей 20, которые (каналы) содержат распределенные по длине сопла 9, подающие струю 34 хладагента на обратную сторону блоков 4, обеспечивая при этом равномерность охлаждения.
Согласно изобретению несколько сопл 9 установлены таким образом, что струи 34 хладагента передают блокам 4 импульс В, или при необходимости, встречно направлению вытягивания заготовки для оптимизации замыкающего усилия между последовательно перемещающимися рядами блоков в направлении вытягивания заготовки, задаваемого процессом разливки и являющегося наиболее благоприятным.
Для предупреждения нежелательного вытекания охлаждающей жидкости из гусеничных лент 2, 3 нагретую охлаждающую жидкость собирают в возвратной камере 35 хладагента и отсасывают известным образом с гусеничных лент 2, 3, и, как это принято в литейных установках, отводят в замкнутый циркуляционный контур, состоящий из воздухоотделителя, циркуляционного холодильника, емкости с хладагентом, насосов, фильтра, измерительно-регулирующих приборов и пр.
Цепи 20, несущие блоки 4, снабжаются преимущественно роликами 10 для снижения до минимума трения с направляющей 11. При этом ролики 10, по меньшей мере, одной цепи 20 перемещаются по направляющей 31 с боковыми направляющими, благодаря чему блоки 4 перемещаются в боковом направлении.
Приведение в действие цепей 20 с находящимися на них блоками 4 обеспечивается цепными колесами 30, расположенными на входной и выходной сторонах кристаллизатора рядом с направляющими 11, валы которых связаны с приводом с регулируемым числом оборотов.
Согласно изобретению блоки 4 на верхней гусеничной ленте 2 на выходной стороне 19b кристаллизатора приводятся в действие таким образом, что блоки 4 на нижней стороне, т.е. на участке кристаллизатора, сдвигаются вместе с обеспечением уплотнения под действием веса блоков 4, находящихся на дуговой направляющей на входной стороне, при этом в зависимости от условий трения между цепями 20 и направляющей 11 и величины наклона кристаллизатора к валу 29а, несущему цепные колеса 30 и расположенному на входной стороне 19а, сообщается соответствующий вращающий момент встречно направлению вращения для снижения усилия между расположенными друг на друге в кристаллизаторе рядами блоков до необходимой и допустимой величины.
Согласно изобретению аналогичный эффект достигается также на нижнем корпусе 3 установки непрерывной разливки, при этом приводной вал 29с цепей 20 располагается на входной стороне 19а кристаллизатора и валу 29d, расположенному на выходной стороне 19b, вместе с насаженными на него цепными колесами 30 сообщается соответствующий встречный вращающий момент, в результате чего ряды блоков сходятся в зоне кристаллизатора и накладываются друг на друга.
Хотя относительно небольшие блочные элементы 5 изменяют свои размеры при изменении температуры лишь незначительно, тем не менее, это обстоятельство необходимо учитывать.
Согласно изобретению решение этой проблемы состоит в том, что шарниры звеньев 26 цепи выполнены с зазором в продольном направлении, за счет чего шаг цепей 20 может приходить в соответствие с размером холодных и нагревающихся при перемещении кристаллизатора блоков 4 и с зубьями цепных колес 30.
В описанном выше способе приведения в действие блоки 4, в зависимости от их температуры, могут раздвигаться на противоположной от кристаллизатора стороне гусеничных лент 2, 3 благодаря наличию зазора в шарнирах цепей 20, при этом между последовательно расположенными блоками 4 образуются промежутки.
Согласно изобретению блоки 4 расположены поэтому в рамах 7 со смещением на величину u (фигуры 6, 15), благодаря чему постоянно обеспечивается перекрытие зазора и в зонах охлаждения предупреждается затекание охлаждающей жидкости между блоками 4 и попадание на стенку кристаллизатора.
Очевидно, что блоки 4, расположенные без закрепления на цепях 20, должны быть гарантированы от смещения по соответствующему звену 26 цепей.
Согласно изобретению звенья 26 цепей содержат зубья, входящие в зацепление с блоками 4, определяющими и фиксирующими их положение на обращающихся цепях 20.
Формула изобретения
1. Установка для получения слитков или лент из металлических или неметаллических материалов, содержащая гусеничный кристаллизатор, в котором по меньшей мере одна стенка состоит из блоков (4), отличающаяся тем, что блоки выполнены в виде гусеничных траков по меньшей мере одной гусеничной ленты, циркулирующих на транспортном средстве, при этом блоки (4) свободно расположены на транспортном средстве с возможностью обеспечения деформации их в любом направлении при изменениях температуры, причем по меньшей мере на части траектории по меньшей мере одной гусеничной ленты (2, 3) стационарно установлены магниты, обеспечивающие притяжение блоков к направляющим (11) и бесконтактное перемещение блоков по стационарно установленным магнитам транспортным средством.
2. Установка по п.1, отличающаяся тем, что магниты представляют собой постоянные магниты или преимущественно электромагниты.
3. Установка по п.2, отличающаяся тем, что в качестве магнитов предусмотрено определенное количество отдельных магнитов.
4. Установка по 1, отличающаяся тем, что блоки (4) расположены по ширине кристаллизатора и состоят из нескольких блочных элементов (5), установленных в рамах (7) и связанных между собой тягами (16) с натяжными пружинами (15), обеспечивающими при температурных изменениях в процессе литья беспрепятственное деформирование блоков, при этом блоки (4), объединенные рамами (7) в единое целое, расположены без механического крепления на гусеничных лентах (2, 3), а стационарно установленные магниты, притягивающие рамы (7) с расположенными в них блочными элементами (5) и транспортные средства к направляющим (11), представляют собой по меньшей мере одну неподвижную магнитную направляющую (12), расположенную между направляющими (11) транспортных средств на нижней стороне по меньшей мере одной гусеничной ленты (2, 3), и по меньшей мере одну неподвижную дуговую магнитную направляющую (13), расположенную на входной и выходной сторонах (19а, 19b) кристаллизатора.
5. Установка по п.1, отличающаяся тем, что по ширине кристаллизатора расположено несколько транспортных средств, преимущественно цепей (20), боковое расстояние i между которыми выбрано из условия исключения недопустимого прогиба расположенных на транспортных средствах рам (7) и блоков (4).
6. Установка по п.1, отличающаяся тем, что блоки (4) свободно расположены на транспортных средствах, по меньшей мере на части верхней стороны корпусов установки с возможностью съема при замене с помощью соответствующего подъемника с захватным приспособлением.
7. Установка по п.1, отличающаяся тем, что рамы (7) выполнены из ферромагнитного материала.
8. Установка по п.1, отличающаяся тем, что транспортные средства представляют собой цепи (20).
9. Установка по п.8, отличающаяся тем, что транспортные средства снабжены роликами (10).
10. Установка по п.4 или 5, отличающаяся тем, что длина h блочного элемента (5) в боковом направлении составляет не более 25 см.
11. Установка по п.8, отличающаяся тем, что расстояние i между транспортными средствами, несущими рамы (7), составляет не более 30 см.
12. Установка по п.1, отличающаяся тем, что она выполнена с горизонтальным или наклонным направлением вытягивания заготовки и содержит нижнюю и верхнюю гусеничные ленты (2,3), верхняя гусеничная лента (2) имеет длину l, меньшую, чем длина k нижней гусеничной ленты (3), при этом заменяемые блоки размещены на выступающей части нижней гусеничной ленты (3).
13. Установка п.4 или 12, отличающаяся тем, что гусеничные ленты (2, 3) содержат по два вала (29а, 29b, 29 с, 29d) с концентрически закрепленными на них цепными колесами (30), при этом дуговые магнитные направляющие (13) установлены на вращающихся валах (29) цепных колес (30) на подшипниках (28) скольжения или качения.
14. Установка по п.12, отличающаяся тем, что она снабжена устройством вторичного охлаждения заготовки, расположенным на выступающей за верхнюю гусеничную ленту (2) части нижней гусеничной ленты (3) с возможностью удаления при замене блоков (4).
15. Установка по п.1, отличающаяся тем, что она снабжена устройством охлаждения блоков (4) со стороны, обращенной к направляющим (11).
16. Установка по п.1, отличающаяся тем, что на переднюю сторону блоков (4), образующую стенку кристаллизатора, нанесено теплоизоляционное защитное покрытие, преимущественно из керамического материала.
17. Установка по п.1, отличающаяся тем, что на передней стороне блоков (4), образующей стенку кристаллизатора, расположена фольга из титана или стали или их сплавов толщиной преимущественно менее 0,5 мм.
18. Установка по п.1, отличающаяся тем, что она снабжена устройством для охлаждения блоков (4), имеющим множество сопел (9), установленных с возможностью сообщения блокам (4) струями (34) хладагента импульса в направлении вытягивания заготовки или встречно ему для оптимизации замыкающего усилия между последовательными рядами блоков в заданном наиболее оптимальном направлении вытягивания заготовки.
19. Установка по п.1, отличающаяся тем, что она снабжена приводом перемещения блоков (4), расположенным на верхней гусеничной ленте (2) на выходной стороне (19b) кристаллизатора, сообщающим валу (29а), расположенному на входной стороне (19а) кристаллизатора, вращающий момент встречно направлению движения.
20. Установка непрерывной разливки (1) по п.4, отличающаяся тем, что она снабжена приводом перемещения блоков (4), расположенным на нижней гусеничной ленте (3) на входной стороне (19а) кристаллизатора, сообщающим валу (29d) на выходной стороне (19b) с расположенными на нем цепными колесами (30) встречный вращающий момент для смыкания блоков и наложения их друг на друга.
21. Установка по п.8 или 9, отличающаяся тем, что каждая цепь (20) содержит шарнирно сочлененные звенья (26), причем шарниры выполнены с зазорами в продольном направлении для приведения в соответствие шага цепей (20) с размерами холодных и нагретых блоков (4) и с зубьями цепных колес (30).
22. Установка по п.1, отличающаяся тем, что блоки (4) расположены в рамах (7) со смещением, обеспечивающим перекрытие промежутков между блоками (4) в зонах охлаждения для исключения попадания охлаждающей жидкости на переднюю сторону блоков (4).
23. Установка по п.22, отличающаяся тем, что звенья (26) цепей содержат зубья, входящие в зацепление с рамами (7) блоков (4) для фиксирования их положения на транспортных средствах.
24. Способ замены блоков (4) в установке непрерывного получения слитков или лент, характеризующийся тем, что в установке, выполненной по любому из пп.4-23, на заменяемые блоки (4) посредством подъемника опускают плиту, имеющую на своей нижней стороне уплотнения и связанную с вакуумной системой, притягивают блоки к плите под действием вакуумной системы и заменяют их с помощью подъемника.
РИСУНКИ
|
|