(21), (22) Заявка: 2007101562/28, 16.01.2007
(24) Дата начала отсчета срока действия патента:
16.01.2007
(46) Опубликовано: 20.09.2008
(56) Список документов, цитированных в отчете о поиске:
ХИМЧЕНКО Н.В. УЛЬТРАЗВУКОВОЙ СТРУКТУРНЫЙ АНАЛИЗ МЕТАЛЛИЧЕСКИХ МАТЕРИАЛОВ И ИЗДЕЛИЙ. – М.: МАШИНОСТРОЕНИЕ, 1976, с.17. RU 2231056 С1, 20.06.2004. RU 2187102 C2, 10.08.2002. RU 2262694 С1, 20.10.2005. RU 2141652 C1, 20.11.1999. US 4539848, 10.09.1985. US 5804727 A, 08.09.1998. JP 2001343366 A, 14.12.2001.
Адрес для переписки:
197376, Санкт-Петербург, ул. Проф. Попова, 5, СПГЭТУ, патентный отдел, К.И. Берковской
|
(72) Автор(ы):
Паврос Сергей Константинович (RU), Паврос Кирилл Сергеевич (RU), Курков Александр Валентинович (RU)
(73) Патентообладатель(и):
Государственное образовательное учреждение Высшего профессионального образования “Санкт-Петербургский государственный электротехнический университет “ЛЭТИ” (RU)
|
(54) СПОСОБ ИЗМЕРЕНИЯ СРЕДНЕГО РАЗМЕРА ЗЕРНА МАТЕРИАЛА УЛЬТРАЗВУКОВЫМ МЕТОДОМ
(57) Реферат:
Использование: для измерения среднего размера зерна материала ультразвуковым методом. Сущность: осуществляют излучение преобразователями импульсов упругих волн нормально к поверхности плоского изделия последовательно на двух частотах f и fj, принимают первые донные импульсы на этих частотах и измеряют их амплитуды, при этом дополнительно измеряют амплитуду второго донного импульса на частоте f и n-го донного импульса на частоте fj, находят отношение амплитуд первого и второго донного импульсов на частоте f и первого и n-го донного импульсов на частоте fj, причем fj=f/m, a m=n-1, где n – целое нечетное число, а средний размер зерна D материала вычисляют по соответствующей математической формуле. Технический результат: обеспечение контроля среднего размера зерна материала без применения эталонных образцов. 2 ил.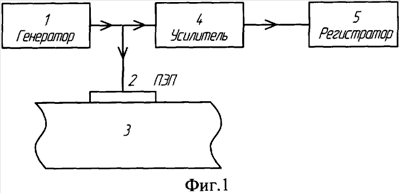
Предлагаемое изобретение относится к области неразрушающих испытаний материалов и изделий ультразвуковым методом. Главным образом оно может быть использовано для измерения структурных характеристик конструкционных материалов в металлургической, машиностроительной и других отраслях промышленности
В промышленности для определения структурных характеристик материалов, в частности среднего размера зерна используют метод металлографического анализа [Шулаев И.Л. Контроль в производстве черных металлов. М: Металлургия, 1978]. Сущность этого метода состоит в измерении зерен материала, видимых визуально или в микроскоп на шлифованной, полированной и протравленной кислотами поверхности образцов, вырезанных из соответствующих участков изделий. Недостатком такого метода является длительность и трудоемкость измерений, определение среднего размера зерна поверхностного участка материала.
Известен интегральный способ оценки структуры материала по критерию «хорошая»- «плохая» с помощью ультразвука [Крауткрамер Й., Крауткрамер Г. Ультразвуковой контроль материалов. Справочник, М.: Металлургия, 1991]. Он заключается в прозвучивании контролируемых изделий эхо-методом на заданной частоте f и сравнении амплитуды донного сигнала на эталонном образце с «хорошей» структурой с амплитудами донных сигналов на испытуемых изделиях. При уменьшении амплитуды донного сигнала в изделии на определенную величину относительно амплитуды донного сигнала на эталонном образце структура считается «плохой» и изделие бракуется.
Такой способ можно реализовать при контроле серийных изделий, когда их толщина совпадает с толщиной эталонного образца. Недостатком такого способа является невозможность определения среднего размера (или балла зерна) и существенное влияние на результаты контроля качества акустического контакта.
Наиболее близким по технической сущности и достигаемому результату является способ определения среднего размера зерна материала (балла), основанный на измерении структурных коэффициентов [Химченко Н.В. Ультразвуковой структурный анализ металлических материалов и изделий. М.: Машиностроение, 1976, с.17]. Под структурным коэффициентом понимается отношение амплитуд донных импульсов Aj при контроле эхо-методом в контактном варианте Kj=Aj/A, измеренных на частоте fj и частоте f<
Для реализации этого способа необходимо в образце материала контролируемого изделия такой же толщины, что и эталонные образцы, с помощью пьезоэлектрического преобразователя возбудить на частоте f импульс упругой волны, получить донный эхо-сигнал от его противоположной грани (дна образца) и измерить его амплитуду A. Затем установить в ту же точку на поверхности образца преобразователь с рабочей частотой fj>>f, возбудить импульс упругой волны, получить донный эхо-сигнал и измерить его амплитуду Aj. Структурный коэффициент Kj, определяемый отношением амплитуд эхо-сигналов Aj/A или их разностью [дБ], после этого сравнивается с полученными аналогичными значениями структурных коэффициентов на эталонных образцах с известным средним размером зерна.
Недостатком такого способа является необходимость изготовления большого числа эталонных образцов с различным значением среднего размера зерна и невозможность проведения измерений таким способом на изделиях с различной толщиной.
Технической задачей, решаемой изобретением, является разработка способа контроля среднего размера зерна материала без применения эталонных образцов.
Поставленная задача решается тем, что, как и в известном способе, излучают импульсы упругих волн нормально к поверхности изделия последовательно на двух частотах f и fj, измеряют амплитуды первых донных сигналов на этих частотах, дополнительно измеряют амплитуду второго донного импульса на частоте f и n-го донного импульса на частоте fj, находят отношение амплитуд первого и второго донного импульсов на частоте f и первого и n-го донного импульсов на частоте fj, причем fj=f/m, a m=n-1, где n – целое нечетное число, а средний размер зерна D материала вычисляют по формуле:
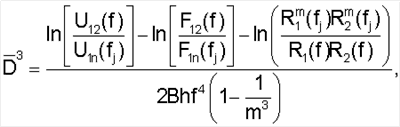
где U12(f) – отношение амплитуды первого донного сигнала ко второму на частоте f;
U1n(fj) – отношение амплитуды первого донного импульса к n-му донному импульсу на частоте fj=f/m;
F12(f)=F1(f)/F2(f) – отношение функций, учитывающих дифракционное расхождение звуковых пучков для первого F1 и второго F2 донных импульсов на частоте f;
F1n(fj)=F1(fj)/Fn(fj) – отношение функций, учитывающих дифракционное расхождение звуковых пучков для первого F1 и n-го Fn донного импульсов на частоте fj;
R1(f) и R1(fj) – коэффициенты отражения звуковых пучков от донной поверхности изделия на частоте f и fj соответственно;
R2(f) и R2(fj) – коэффициенты отражения звуковых пучков от поверхности преобразователя на частоте f и fj соответственно;
h – толщина изделия;
В – коэффициент, характеризующий рассеяние звука в материале изделия.
Амплитуды донных импульсов измеряют на частотах f и fj при установке соответствующих преобразователей на один и тот же участок поверхности изделия.
Достигаемый технический результат состоит в упрощении измерений, сокращении времени и уменьшении затрат на проведение измерений.
Сущность предлагаемого изобретения поясняется чертежами, где на фиг.1 представлена схема измерения, а на фиг.2 – временные диаграммы.
Предлагаемый способ заключается в следующем. Генератор высокочастотных электрических колебаний 1 возбуждает преобразователь 2 на частоте f, соответствующей собственной резонансной частоте преобразователя. Ультразвуковой импульс, создаваемый этим преобразователем в режиме излучения, распространяется в контролируемом изделии 3 и последовательно отражается от свободной донной поверхности изделия и от верхней его поверхности, на которой установлен преобразователь, работающий уже в режиме приема. Преобразователь последовательно принимает эхо-сигналы, однократно U1(f) (фиг.2а, сигнал 1) и двукратно U2(f) (фиг.2а) отраженные от дна изделия, преобразует их в соответствующие электрические сигналы, которые усиливаются усилителем их в соответствующие электрические сигналы, которые усиливаются усилителем 4, их амплитуды измеряются регистрирующим устройством 5, а затем находят отношение амплитуд этих сигналов.
Амплитуды этих сигналов, в соответствии с уравнением акустического тракта [Ермолов И.Н. Теория и практика ультразвукового контроля. М.: Машиностроение, 1981. 240 с.], записываются в виде:

где KU – коэффициент двойного электромеханического преобразования на частоте f;
U1 – амплитуда возбуждающего электрического напряжения на частоте f, подаваемого от генератора 1 на преобразователь 2;
R1 – коэффициент отражения звукового пучка от донной поверхности изделия;
R2 – коэффициент отражения звукового пучка от верхней поверхности изделия, на которой расположен преобразователь 2, работающий в режиме приема;
F1 и F2 – функции, учитывающие дифракционное расхождение звуковых пучков, зависящие от волнового размера преобразователя и пройденного им расстояния [Khimunin A.S., Numerikal Calculation of the Diffraction Corrections for the Precise Measurment of Vetrasound Absorption. Acustica, 1972, v27, №4, p.173-181];
– коэффициент затухания ультразвуковых колебаний в материале изделия;
h – толщина контролируемого изделия.
Коэффициент затухания ультразвука в конструкционных поликристаллических материалах в области >>D может быть представлен как:

где П – коэффициент поглощения; Р – коэффициент рассеяния; D – средний размер зерна материала; – длина волны ультразвука в материале изделия на рабочей частоте; А и В – коэффициенты, не зависящие от частоты.
С учетом выражений (1) и (2) отношение амплитуд первого и второго донных сигналов можно записать в виде:

Затем в ту же точку на поверхности контролируемого изделия устанавливают ультразвуковой преобразователь с резонансной частотой fj=f/m, излучают в изделие 3 импульс упругих волн, принимают отраженные от донной и передней поверхности сигналы и измеряют амплитуды первого и n-го донных импульсов и находят их отношение. Параметры m и n выбирают по соотношению:

В соответствии с уравнением акустического тракта [Ермолов И.Н. Теория и практика ультразвукового контроля. М.: Машиностроение, 1981. 240 с.] амплитуды этих донных импульсов можно записать в виде:

Соотношение амплитуд первого и n-го донных импульсов с учетом (2), (4) и (5) может быть записано в виде:

Используя выражения (3) и (6), получаем отношение:

из которого следует:
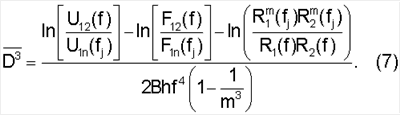
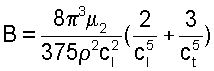
где сl и ct – скорости распространения продольных и поперечных волн в материале изделия;
– плотность материала;
=C11-C12-2C44 – параметр, характеризующий степень упругой анизотропии металла;
Cij – упругие модули монокристалла.
Для стали численное значение параметра В представлено в [Ермолов И.Н., Ермолов М.И. Ультразвуковой контроль. Учебник для специалистов первого и второго уровней квалификации. М. 1998. 170 с].
Коэффициент отражения звукового пучка от донной поверхности изделия R1 может быть вычислен по формуле:
R1=(zм-zв)/(zм-zв),
где zм и zв – акустические сопротивления материала изделия и воздуха.
Методика расчета коэффициента отражения R21 и R2 близки к единице. Поэтому в первом приближении без большой ошибки последний член в числителе выражения (7) можно положить равным нулю.
Рассмотрение предлагаемого способа показывает, что для его реализации не требуется использование эталонных образцов, что приводит к упрощению процесса измерения и дает возможность его применить для экспресс-контроля среднего размера зерна материала акустическим методом.
Формула изобретения
Способ измерения среднего размера зерна материала в плоском изделии путем излучения преобразователями импульсов упругих волн нормально к его поверхности последовательно на двух частотах f и fj, приема первых донных импульсов на этих частотах и измерения их амплитуд, отличающийся тем, что дополнительно измеряют амплитуду второго донного импульса на частоте f и n-го донного импульса на частоте fj, находят отношение амплитуд первого и второго донного импульсов на частоте f и первого и n-го донного импульсов на частоте fj, причем fj=f/m, a m=n-1, где n – целое нечетное число, а средний размер зерна D материала вычисляют по формуле:
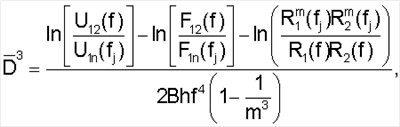
где U12(f) – отношение амплитуды первого донного сигнала ко второму на частоте f;
U1n(fj) – отношение амплитуды первого донного импульса к n-му донному импульсу на частоте fj=f/m;
F12(f)=F1(f)/F2(f) – отношение функций, учитывающих дифракционное расхождение звуковых пучков для первого F1 и второго F2 донных импульсов на частоте f;
F1n(fj)=F1(fj)/Fn(fj) – отношение функций, учитывающих дифракционное расхождение звуковых пучков для первого F1 и n-го Fn донного импульсов на частоте fj;
R1(f) и R1(fj) – коэффициенты отражения звуковых пучков от донной поверхности изделия на частоте f и fj, соответственно;
R2(f) и R2(fj) – коэффициенты отражения звуковых пучков от поверхности преобразователя на частоте f и fj, соответственно;
h – толщина изделия;
В – коэффициент, характеризующий рассеяние звука в материале изделия.
РИСУНКИ
|