|
(21), (22) Заявка: 2006112491/02, 05.04.2006
(24) Дата начала отсчета срока действия патента:
05.04.2006
(43) Дата публикации заявки: 10.11.2007
(46) Опубликовано: 27.08.2008
(56) Список документов, цитированных в отчете о поиске:
SU 1421249 A1, 30.10.1985. RU 2141879 C1, 27.11.1999. RU 2136467 C1, 10.09.1999. SU 1693807 A1, 30.07.1994. JP 11-090670 A, 06.04.1999. JP 57-039081 A, 04.03.1982.
Адрес для переписки:
199034, Санкт-Петербург, наб.Макарова, 8, ВАТТ им.генерала армии А.В.Хрулева, научно-вычислительный отдел, В.С.Панусу
|
(72) Автор(ы):
Панус Виктор Сергеевич (RU), Брусянин Дмитрий Владимирович (RU), Фролов Василий Иванович (RU)
(73) Патентообладатель(и):
Панус Виктор Сергеевич (RU), Брусянин Дмитрий Владимирович (RU), Фролов Василий Иванович (RU)
|
(54) СПОСОБ СВАРКИ В ЗАЩИТНОМ ГАЗЕ С ГАЗОДИНАМИЧЕСКИМ УДАЛЕНИЕМ СЛОЯ ЗАГРЯЗНЕНИЙ ИЗ ЗОНЫ СВАРКИ
(57) Реферат:
Изобретение относится к области сварки металлов, в частности к способам сварки в защитном газе. В зону сварки подают защитный газ, а на электрод – импульс тока. Одновременно в локальную зону контакта электрода с поверхностью детали направляют поток вспомогательного газа. Вспомогательный газ подают через наконечник горелки под давлением 5 МПа в виде ударных струй. Снижается трудоемкость процесса сварки за счет удаления с поверхности детали диэлектрического слоя загрязнений непосредственно в процессе сварки. 1 ил.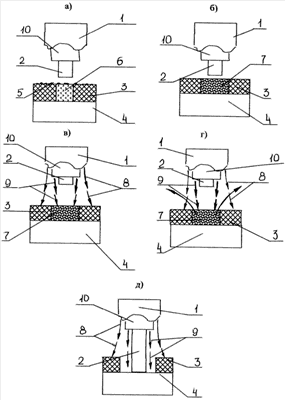
Изобретение относится к области сварки металлов, в частности к способам сварки в защитном газе.
Известно, что сварку в защитном газе широко применяют для восстановления неисправных деталей двигателя, трансмиссии, ходовой части автомобильной техники, изготовленных из тонколистовой стали, чугуна, цветных металлов и сплавов [1]. Однако поверхности свариваемых деталей часто покрыты слоем различных загрязнении: старыми лакокрасочными покрытиями, остатками топливосмазочных материалов, продуктами коррозии, асфальтобитумными отложениями, нагаром. По своим физическим свойствам эти загрязнения являются диэлектриками, препятствующими возбуждению сварочной дуги и ведению сварочного процесса. Основным недостатком процесса сварки в защитном газе является то, что детали в месте сварки необходимо тщательно очищать от слоя загрязнений для обеспечения надежного контакта сварочного электрода с деталью. Операция по отчистке свариваемых поверхностей от загрязнений является сложной и трудоемкой, требующей больших затрат времени и применения специального оборудования [2]. Известен способ очистки поверхности изделий, принимаемый за прототип, однако, он может быть применен как подготовительная операция перед сваркой, окраской и т.п. и требует затрат времени, использования дополнительного энергоемкого оборудования и специальных средств [3].
Технической задачей изобретения является снижение трудоемкости процесса сварки в защитном газе.
Техническая задача решена за счет того, что одновременно с подачей импульса тока на электрод и защитного газа к зоне сварки в локальную зону контакта электрода с поверхностью детали через наконечник горелки направляют поток вспомогательного газа под давлением 5 МПа в виде ударных струй.
На чертеже представлен процесс термического разрушения и удаления слоя загрязнений из зоны сварки кинетической энергией струи вспомогательного газа, где обозначены: поз.1 – сопло горелки, поз.2 – электрод, поз.3 – слой загрязнений, поз.4 – деталь, поз.5 – микровыступы, поз.6 – каналы прохождения электрического тока, поз.7 – термически разрушенный слой загрязнений, поз.8 – защитный газ, поз.9 – вспомогательный газ, поз.10 – наконечник горелки.
Способ сварки в защитном газе с газодинамическим удалением слоя загрязнений из зоны сварки осуществляется следующим образом. В начальный период процесса сварки на электрод 2 в момент касания слоя загрязнений 3 подается импульс тока большой мощности с максимальными параметрами: сила тока 800-900 А, напряжение 60-80 В, длительность импульса tи=1,5 мс, необходимый для образования каналов прохождения электрического тока 6 (пробоя диэлектрика) между электродом 2 и деталью 4 через микровыступы 5. (фиг.1а). При тепловом пробое диэлектрика прохождение тока сопровождается выделением «джоулева тепла», вследствие чего слой загрязнений термически разрушается (фиг.1б). Для удаления термически разрушенного слоя загрязнений 7 в локальную зону контакта сварочного электрода 2 с поверхностью детали 4 через наконечник горелки 10, под высоким давлением ( 5 МПа), вводится поток вспомогательного газа 9, представляющий собой одновременно подаваемые ударные струи, которые посредством кинетической энергии газодинамического напора удаляют из зоны сварки продукты термически разрушенного слоя загрязнений (фиг.1в, 1г).
С началом стабильного процесса сварки (фиг.1д) сила тока и напряжения автоматически снижаются до рабочего режима, однако тепла, выделяемого сварочной дугой, и теплопроводности свариваемого металла достаточно для дальнейшего термического разрушения слоя загрязнений в зоне сварки. Удаление термически разрушенного слоя при этом происходит струями вспомогательного газа по схеме, описанной выше (фиг.1в, 1г), и дополнительно газодинамическим напором сварочной дуги.
Пример 1. Восстановление деталей с неподготовленными поверхностями проводили сваркой, с использованием многофункционального сварочного комплекса, обеспечивающего сварку деталей, изготовленных из чугуна, алюминиевых сплавов, конструкционных и легированных сталей, на режимах ММА, MIG/MAG, TIG. Импульсно-дуговой сваркой восстанавливали блоки цилиндров двигателя КамА3-740 (материал – чугун марки СЧ-21), имеющие трещины на боковых поверхностях. Заварку проводили без очистки свариваемых поверхностей от старой краски и слоя загрязнений. В качестве присадочного материала использовали проволоку Св-08Г2С диаметром 1,6 мм; скорость сварки 38 м/ч, защитный газ – СО2 (расход 8-9 л/мин), вспомогательный газ – CO2 (давление подачи в зону сварочной ванны 5 МПа), сила сварочного тока 80-100 А, напряжение дуги 18 В, сила тока в импульсе 600-700 А, длительность импульса 2,0 мс, частота импульсов 50 имп/с, угол наклона сварочной горелки 70-80°.
Пример 2. Проводили заварку трещин, пробоин, разрывов на кабинах, металлических кузовах, рамах автомобилей и корпусах гусеничных машин. Поверхности перечисленных деталей были покрыты слоем старой краски и твердыми частицами загрязнений (асфальтобитумные вещества), суммарная толщина слоя загрязнений составляла 0,5-0,7 мм. Заварку трещин осуществляли при следующих режимах: амплитуда тока импульса 750 А, сила тока в паузе 160 А, напряжение дуги 23 В, частота импульсов 100 имп/с, длительность импульса 2,5 мс, скорость сварки 19 м/ч. Сварочная проволока Св-08Г2С диаметром 1,2 мм, защитный газ – СО2 (давление подачи в зону сварочной ванны 5 МПа).
Таким образом, без трудоемкой предварительной операции – механической очистки свариваемых поверхностей от диэлектрического слоя – обеспечивается проведение процесса сварки.
ММА – ручная сварка покрытым электродом,
MIG – сварка в среде инертного газа электродной проволокой,
MAG – сварка в среде активного газа электродной проволокой,
TIG – дуговая сварка неплавящимся электродом в инертном газе.
Литература
1. Молодык Н.В., Зенкин А.С. Восстановление деталей машин. Справочник. – М.: Машиностроение, 1989.
2. Воловик Е.Л. Справочник по восстановлению деталей. – М.: Колос, 1981.
3. Описание изобретения к авторскому свидетельству SU 1421249 А1, Н05Н 1/00. «Способ очистки поверхности изделий», 30.10.1985, 5 л.
Формула изобретения
Способ сварки в защитном газе с газодинамическим удалением слоя загрязнений из зоны сварки, отличающийся тем, что одновременно с подачей импульса тока на электрод и защитного газа к зоне сварки в локальную зону контакта электрода с поверхностью детали через наконечник горелки направляют поток вспомогательного газа под давлением 5 МПа в виде ударных струй.
РИСУНКИ
|
|