|
(21), (22) Заявка: 2006122095/11, 20.06.2006
(24) Дата начала отсчета срока действия патента:
20.06.2006
(46) Опубликовано: 10.03.2008
(56) Список документов, цитированных в отчете о поиске:
RU 2186269 C2, 27.07.2002. RU 2706960 C1, 10.04.1997. RU 2064615 C1, 27.07.1996. GB 1083003 A, 13.09.1967. US 2006063023 A1, 23.03.2006.
Адрес для переписки:
690059, г.Владивосток, ул. Верхнепортовая, 50А, МГУ им. Невельского, ЦОПИС
|
(72) Автор(ы):
Леонтьев Лев Борисович (RU), Хмелевская Ванда Болиславовна (RU), Рассказова Надежда Анатольевна (RU)
(73) Патентообладатель(и):
Федеральное государственное образовательное учреждение высшего профессионального образования “Морской государственный университет имени адмирала Г.И. Невельского” (RU)
|
(54) СПОСОБ ПОЛУЧЕНИЯ АНТИФРИКЦИОННОГО ПОКРЫТИЯ НА ТОНКОСТЕННЫХ СТАЛЬНЫХ ВКЛАДЫШАХ ОПОР СКОЛЬЖЕНИЯ
(57) Реферат:
Изобретение относится к области машиностроения и может быть использовано в роторных машинах, к которым предъявляются повышенные требования по быстроходности и возможности многократных пусков (остановов) машины. Согласно предлагаемому способу послойное плазменное напыление с раздельной подачей под срез сопла плазмотрона порошковых материалов олова и алюминия выполняют в два этапа. На первом этапе напыляют основной слой, подавая под срез сопла плазмотрона на предварительно подготовленный напыленный подслой порошковый материал сплава алюминия АO6. По достижении необходимой толщины основного слоя, не прекращая подачу сплава АO6, начинают второй этап напыления, образуя рабочий слой путем одновременной подачи с ним под срез сопла плазмотрона порошкового материала олова, при этом порошковый материал АO6 подают такого же состава входящих в него компонентов. Заканчивают второй этап напыления по достижении заданной толщины антифрикционного слоя. Порошковый материал сплава АO6 подают под срез сопла плазмотрона по двум трубкам, а олова – по третьей, при положении осей подающих трубок относительно друг друга под углом 120°. Технический результат: увеличение срока службы, повышение коррозионной стойкости, увеличение нагрузки схватывания, упрощение технологии, снижение себестоимости затрат на изготовление и восстановление тонкостенных вкладышей. 2 ил.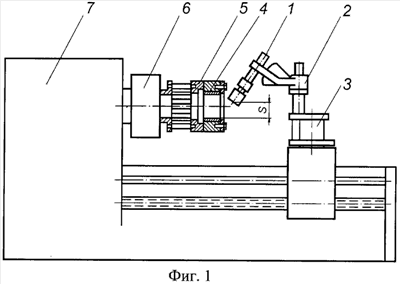
Изобретение относится к области машиностроения и может быть применено для изготовления и восстановления подшипников скольжения.
Известен «Способ получения многослойных покрытий на восстанавливаемых деталях» по а.с. СССР №1465226, Кл. В23Р 6/00, С23С 28/00, по которому производят плазменное напыление порошка, например, никель-алюминия, на восстанавливаемую деталь из легкоокисляющегося сплава, толщину слоя выбирают в пределах 0,5-0,9 мм. Затем оплавляют нанесенный слой электроэрозионным методом в режиме эрозии. После чего осуществляют наращивание основного слоя необходимого состава тем же электроэрозионным методом в режиме легирования.
Недостатком данного способа является сложный технологический процесс: напыление, последующее оплавление напыленного слоя, затем наращивание основного слоя электроэрозионным методом в режиме легирования, что делает данную технологию получения покрытия дорогостоящей и трудоемкой.
Известен «Способ получения антифрикционного покрытия на тонкостенных стальных вкладышах опор скольжения» (см. патент РФ №2076960), включающий послойное газотермическое напыление смеси порошков с последующей электроконтактной обработкой каждого слоя. При этом в качестве порошков используют порошок алюминиевого сплава с содержанием олова в виде частиц сферической формы, полученных вспомогательной операцией путем распыления этого сплава струей азота в атмосфере азота.
Недостатком данного способа является применение технологии приготовления смеси порошковых материалов вспомогательной операции, она является трудоемкой и дорогостоящей из-за сложности оборудования, а также то, что получение сплава не предотвращает электроконтактный процесс коррозии алюминий-олово, что снижает коррозионную стойкость, антифрикционные свойства и когезионную прочность нанесенного покрытия, т.е. снижает технический ресурс вкладышей опор скольжения.
Известен «Способ получения антифрикционного покрытия на тонкостенных стальных вкладышах опор скольжения» (см. патент РФ №2186269 С2, МПК F16C 33/04), принятый по достигаемому результату за прототип, включающий послойное плазменное напыление с раздельной подачей под срез сопла плазмотрона смеси порошковых материалов олова, меди, лантана и алюминия, имеющей следующее соотношение ингредиентов, мас.%:
Олово |
3,0-6,0 |
Медь |
0,3-0,6 |
Лантан |
Не менее 0,01 |
Алюминий |
Остальное |
и электроконтактную обработку каждого слоя. При этом первый, второй и третий совместно с четвертым компоненты смеси порошковых материалов в процессе напыления подают друг от друга отдельно под срез сопла плазмотрона по соответствующим трубопроводам, оси которых разнесены относительно друг друга на 120°, а плазменную струю закручивают.
Недостатком известного способа является достаточно высокий коэффициент трения, вследствие чего происходит повышенный износ антифрикционного материала, что приводит к снижению технического ресурса вкладышей опор скольжения.
Кроме того, в известном способе существует необходимость проводить электроконтактную обработку после напыления каждого слоя, что усложняет процесс напыления, причем особых изменений в структуре покрытия, после проведения электроконтактной обработки не наблюдается.
Необходимость раздельной подачи порошков различных компонентов значительно усложняет сам процесс напыления, приводит к увеличению себестоимости плазменного напыления порошковых материалов и стоимости изготовления и восстановления самих изделий, полученных данным способом.
Техническая задача, на решение которой направлен предлагаемый способ, – устранение указанных недостатков, а именно: увеличение срока службы антифрикционного покрытия вкладышей подшипников, за счет: снижения коэффициента трения, увеличения износостойкости. Так же задачей является снижение затрат на плазменное напыление порошковых материалов и, как следствие, снижение стоимости изготовления изделий, изготавливаемых или восстанавливаемых предложенным способом.
Указанная техническая задача достигается тем, что в известном способе получения антифрикционного покрытия на тонкостенных стальных вкладышах опор скольжения, включающем послойное плазменное напыление с раздельной подачей под срез сопла плазмотрона порошковых материалов олова и алюминия, в отличие от него в заявленном процесс напыления выполняют в два этапа, на первом из которых напыляют основной слой, подавая под срез сопла плазмотрона на предварительно подготовленный напылением подслой порошковый материал сплава алюминия АО6, состоящего из компонентов, мас.%:
Олово |
5,0-6,0 |
Медь |
0,3-0,6 |
Лантан |
Не менее 0,01 |
Алюминий |
Остальное |
По достижении необходимой толщины напыленного основного слоя, не прекращая подачу порошкового материала сплава алюминия АО6, начинают второй этап напыления, образуя рабочий слой путем одновременной подачи с ним под срез сопла плазмотрона порошкового материала олова при соблюдении следующего состава, мас.%
Олово |
12,0-14,0 |
Сплав АО6 |
Остальное, |
при этом порошковый материал сплава алюминия АО6 подают такого же состава входящих в него компонентов. Заканчивают второй этап напыления по достижении заданной высоты антифрикционного слоя, причем порошковый материал сплава АО6 подают под срез сопла плазмотрона по двум трубкам, а порошковый материал олова – по третьей, при положении осей подающих трубок относительно друг друга под углом 120°.
Заявленные ограничительные и отличительные признаки обеспечивают предлагаемому техническому решению достижение поставленной технической задачи, а именно: увеличение срока службы антифрикционного покрытия вкладышей подшипников и, соответственно, самого вкладыша, улучшения триботехнических свойств антифрикционного покрытия: снижение коэффициента трения, увеличение износостойкости; снижение стоимости их изготовления и восстановления.
Так, для достижения технического результата необходимо без усложнения технологического процесса напыления проведением электроконтактной обработки произвести процесс напыления в два этапа, где на первом этапе на предварительно напыленный подслой, под срез сопла плазмотрона подают известный порошковый материал сплава алюминия АО6, получая тем самым основной слой известных компонентов, а именно следующих компонентов, мас.%:
Олово |
5,0-6,0 |
Медь |
0,3-0,6 |
Лантан |
Не менее 0,01 |
Алюминий |
Остальное |
При этом достигаются необходимые свойства основного слоя, благодаря материалу АО6 и присущим ему свойствам: высокие механические свойства и удовлетворительные триботехнические свойства, т.е. достаточно высокий коэффициент трения и низкая нагрузка схватывания, в результате чего понижается износостойкость, но так же обеспечивается высокая адгезия основного слоя, за счет чего повышается долговечность покрытия.
Первый этап напыления завершают, когда достигается необходимая толщина основного слоя.
На втором этапе происходит образование рабочего слоя, за счет подачи порошкового материала олова, причем подачу олова начинают, не прерывая процесса напыления порошкового материала сплава алюминия АО6, и производят ее при соблюдении следующего состава, мас.%
Олово |
12,0-14,0 |
Сплав АО6 |
Остальное |
При этом сплав АО6 выдерживают такого же состава компонентов и заканчивают напыление рабочего слоя по достижении заданной толщины антифрикционного слоя в целом. Причем порошковый материал сплава АО6 подают по двум трубопроводам, а порошковый материал олова – по третьему, тем самым достигается приведенный выше состав компонентов олова и сплава АО6.
Подачу компонентов производят под срез сопла плазмотрона по соответствующим трубопроводам, при стандартном положении осей подающих трубопроводов, относительно друг друга под углом 120°. Такая подача порошковых материалов обеспечивает равномерное распределение зерен олова в матрице сплава АО6, за счет того что олово не растворимо в алюминии. При этом механические свойства полученного соединения АО6 + олово (12-14%) близки к свойствам известного материала АО6, а триботехнические свойства (коэффициент трения ниже, высокая нагрузка схватывания, высокая износостойкость) выше, чем триботехнические свойства, присущие известному материалу АO20.
Наносимый основной слой (материал АО6) требуемой толщины с высокими механическими свойствами, который обеспечивает высокую долговечность вкладыша, и последующее нанесение, без перерыва, тонкого рабочего слоя ( 15% обычно от толщины всего антифрикционного покрытия), состоящего из порошков АО6 и олова (12-14%), обеспечивают в совокупности высокие механические и триботехнические свойства всего антифрикционного покрытия вкладыша подшипника.
В итоге предложенный способ обеспечивает механические свойства на уровне свойств известного сплава АО6, а триботехнические свойства выше не только по сравнению со сплавом АО6, но и по сравнению с известным лучшим материалом сплава АO20, в результате того, что в заявленном способе олово находится в виде включений компактной формы в более прочной матрице металла АО6, что является весьма существенным.
Данный результат подтвержден проведенными исследованиями.
Таким образом, обеспечивается достижение поставленной технической задачи, а именно: снижение коэффициента трения, увеличение износостойкости, увеличение когезионной прочности. Это позволяет повысить срок службы антифрикционных покрытий, отпадает необходимость использовать послойную электроконтактную обработку, усложняющую технологический процесс напыления, также снижается расход дорогостоящего материала олова, по сравнению, если бы применялся известный материал АO20 для напыления всего антифрикционного слоя, что, в свою очередь, позволяет снизить себестоимость плазменного напыления порошковых материалов и стоимость изготовления и восстановления изделий, изготавливаемых или восстанавливаемых предложенным способом.
Кроме того, при использовании заявленного способа нанесения покрытия достигается дополнительный эффект: увеличивается предел выносливости, т.к. олово имеет компактную форму и не является концентратом напряжений, а поэтому увеличиваются нагрузка схватывания и когезионная прочность.
Заявленный способ поясняется следующими графическими материалами.
На фиг.1 изображена схема напыления внутренней поверхности вкладышей подшипников.
На фиг.2 изображена схема раздельной подачи присадочного материала.
Предлагаемый способ поясняется на примере конкретного получения антифрикционного покрытия на тонкостенных стальных вкладышах опор скольжения методом плазменного напыления.
Процесс напыления антифрикционного покрытия, реализующий заявляемый способ, осуществляют на специальном участке, оснащенном установкой УН-120 для плазменного напыления (не показано), которая содержит: плазмотрон 1 типа С2В3 с источником питания АПР-404 (не показано). Плазмотрон закреплен на суппорте 2 в специальной оснастке 3.
Способ осуществляют следующим образом. Вначале выполняют подготовительные операции. Мойку и обезжиривание вкладышей 4 производят в соответствии с ТУ на ремонт дизеля. Затем протачивают внутреннюю поверхность вкладыша 4 до «чистого» металла. Для увеличения прочности сцепления наносимого покрытия с основой производят струйно-абразивную обработку проточенной внутренней поверхности вкладышей на установке для пескоструйной обработки (не показана), режим обработки: давление воздуха 0,4-0,5 МПа (4-5 ат), диаметр сопла 5-7 мм, расстояние от среза сопла до поверхности вкладыша 50-100 мм, угол наклона сопла к обрабатываемой поверхности детали 60-90°, время обработки 30-40 с. Для струйно-абразивной обработки используют электрокорунд нормальный марок 12А, 15А зернистостью 1,0-1,5 мм. Затем приступают к процессу напыления вкладыша.
Напыление вкладышей производят в специальном приспособлении 5, устанавливаемом в патроне 6 токарного станка 7 (фиг.1).
Для напыления вкладышей используются следующие порошковые материалы: ПТ-Ю5Н (могут быть и другие) – в качестве подслоя, сплав АО6 – в качестве основного слоя, наносимого на первом этапе, и (АО6 + 12-14% олова (Sn)) – в качестве рабочего, наносимого на втором этапе напыления.
Сначала наносят покрытие – подслой порошком ПТЮ-5Н толщиной 0,05-0,1 мм по одному, двум или по трем трубопроводам плазмотрона, соблюдая следующие параметры режима напыления: напряжение на дуге 160-180 В, сила тока 130-150 А, расход плазмообразующего газа (воздух) 45-50 л/мин, расстояние S сопло-деталь 80-100 мм.
Далее выполняют напыление основного и рабочего слоев и производят его при использовании плазмообразующего газа воздух и следующих параметрах режима напыления: напряжение на дуге 200-220 В, сила тока 120-140 А, расход газа 45-50 л/мин, расстояние сопло-деталь 80-100 мм (фиг.1).
Напыление основного слоя – это первый этап напыления – производят на плазмотроне 1 порошком сплава АО6 по двум трубкам 8 в держателях 9 до достижения необходимой толщины напыляемого слоя. Затем выполняют второй этап напыления: не прекращая подачу порошкового материала сплава алюминия АО6 под срез сопла (не показано) плазмотрона 1, подают порошковый материал олова по третьей трубке 8, выдерживая соотношение компонентов, мас.%:
Олово |
12,0-14,0 |
Сплав АО6 |
Остальное, |
где сплав АО6 имеет соотношение компонентов, мас.%:
Олово |
5,0-6,0 |
Медь |
0,3-0,6 |
Лантан |
Не менее 0,01 |
Алюминий |
Остальное |
Точка пересечения осей трубопроводов 8 совпадает с осью плазмотрона 1 (фиг.2).
Напыление рабочего слоя на втором этапе производят до достижения необходимой толщины напыляемого слоя. Толщина рабочего слоя после окончательной механической обработки составляет 0,05-0,08 мм. Суммарная толщина напыленного покрытия составляет не более 0,5-0,6 мм.
Для напыления используют порошки фракции 40-80 мкм.
Для сравнения приведены результаты исследования механических и триботехнических свойств трех видов антифрикционных покрытий при работе в одинаковых условиях: заявляемого – смеси порошков АО6 + Sn (12-14%), известного – порошка сплава АO20, которые по химическому составу одинаковы, но технология получения этих покрытий различна, и известного порошка сплава АО6.
Причем, парой трения для каждого из покрытий являлась сталь 35.
Использовалась установка УН-120 (не показано) для плазменного напыления, которая содержит: плазмотрон С2В3 с источником питания АПР-404, плазмообразующий газ воздух, параметры режима: угол наклона плазменной струи 90°, напряжение на дуге 220 В, дистанция напыления 100 мм. Исследования триботехнических свойств проводили на машине трения СМЦ-2 при капельной подаче масла марки M14 в зону трения (6 капель в минуту) в течение 12 ч при нагрузке 2 кН.
При исследовании были получены следующие результаты:
Заявленный материал покрытия АO6 + Sn (12-14%) дает следующие результаты: когезионная прочность 105 МПа, количество циклов до разрушения 16×106, нагрузка схватывания 3,8 кН, коэффициент трения 0,035, потенциал коррозии 10 мВ.
Материал АO20 дает результаты: когезионная прочность 98 МПа, количество циклов до разрушения 10×106, нагрузка схватывания 3,3 кН, коэффициент трения 0,045, потенциал коррозии 12 мВ.
Результаты материала АО6: когезионная прочность 110 МПа, количество циклов до разрушения 18×106, нагрузка схватывания 2,5 кН, коэффициент трения 0,06, потенциал коррозии 15 мВ.
Исследования в итоге показали, что коэффициент трения у заявленного материала покрытия ниже, чем у материала АO20 на 22% и ниже известного материала АО6, используемого в прототипе на 42%; нагрузка схватывания у заявленного материала покрытия выше, чем у материала АO20 на 13% и выше известного материала АО6, используемого в прототипе на 34%; потенциал коррозии заявленного покрытия ниже, чем у покрытия материала АO20 на 17% и ниже, чем у материала АО6, в известном способе на 33%.
Таким образом, использование нового способа нанесения антифрикционного покрытия позволит: повысить срок службы антифрикционных покрытий за счет понижения коэффициента трения, повышения коррозионной стойкости и увеличения нагрузки схватывания. Использование способа эффективно при изготовлении и восстановлении тонкостенных вкладышей двигателей.
Формула изобретения
Способ получения антифрикционного покрытия на тонкостенных стальных вкладышах опор скольжения, включающий послойное плазменное напыление с раздельной подачей под срез сопла плазмотрона порошковых материалов олова и алюминия, отличающийся тем, что процесс напыления выполняют в два этапа, на первом из которых напыляют основной слой, подавая под срез сопла плазматрона на предварительно подготовленный напыленный подслой порошковый материал сплава алюминия АO6, состоящего из компонентов, мас.%:
Олово |
5,0-6,0 |
Медь |
0,3-0,6 |
Лантан |
Не менее 0,01 |
Алюминий |
Остальное, |
и по достижении необходимой толщины напыленного основного слоя, не прекращая подачу порошкового материала сплава алюминия АО6, начинают второй этап напыления, образуя рабочий слой путем одновременной подачи с ним под срез сопла плазмотрона порошкового материала олова при соблюдении следующего состава, мас.%:
Олово |
12,0-14,0 |
Сплав АO6 |
Остальное, |
при этом порошковый материал сплава алюминия АO6 подают такого же состава входящих в него компонентов, и заканчивают второй этап напыления по достижении заданной толщины антифрикционного слоя, причем порошковый материал сплава АO6 подают под срез сопла плазмотрона по двум трубкам, а порошковый материал олова – по третьей при положении осей подающих трубок относительно друг друга под углом 120°.
РИСУНКИ
|
|