|
(21), (22) Заявка: 2005140161/15, 22.12.2005
(24) Дата начала отсчета срока действия патента:
22.12.2005
(43) Дата публикации заявки: 20.09.2007
(46) Опубликовано: 27.02.2008
(56) Список документов, цитированных в отчете о поиске:
RU 2116383 C1, 27.07.1998. RU 2128731 C1, 10.04.1999. RU 2151824 C1, 27.06.2000. RU 2166566 C2, 10.05.2001. RU 2256730 C1, 20.07.2005.
Адрес для переписки:
660111, г.Красноярск, ул.Пограничников, 37, стр.1, ИТЦ филиала ООО “РУС-Инжиниринг” в г. Красноярск, нач. пат.-инф. отд. С.А.Пановой
|
(72) Автор(ы):
Фризоргер Владимир Константинович (RU), Манн Виктор Христьянович (RU), Анушенков Александр Николаевич (RU), Храменко Сергей Андреевич (RU), Матвиенко Валерий Александрович (RU), Чичук Евгений Николаевич (RU), Сорокин Виктор Владимирович (RU)
(73) Патентообладатель(и):
Общество с ограниченной ответственностью “Русская инжиниринговая компания” (ООО “РУС-Инжиниринг”) (RU)
|
(54) СПОСОБ ПРОИЗВОДСТВА АНОДНОЙ МАССЫ
(57) Реферат:
Изобретение может быть использовано при изготовлении самообжигающихся анодов алюминиевых электролизеров. Кокс разделяют не менее чем на две фракции: размером более 1,0 мм и менее 1,0 мм. Сначала смешивают фракцию кокса менее 1,0 мм с расплавленным пеком и одновременно со смешиванием измельчают кокс до пылевидной фракции размером менее 0,045 мм под воздействием гидроударно-кавитационного поля. Затем добавляют другую фракцию кокса. Полученную смесь перемешивают. Смешивание фракции кокса менее 1,0 мм и одновременное ее измельчение можно осуществлять при давлении менее 100 мбар. Фракцию кокса более 1,0 мм перед добавлением в смесь можно предварительно смешать с расплавленным пеком при давлении менее 100 мбар. Полученная анодная масса однородна, имеет стабильный состав. Обожженная анодная масса имеет кажущуюся плотность 1,54 кг/см3, прочность на сжатие – 50,9 МПа, общую пористость – 22,0%, удельное электрическое сопротивление – 59 мкОм·м, коэффициент относительного удлинения – 114, 6%. 2 з.п. ф-лы, 1 табл., 1 ил.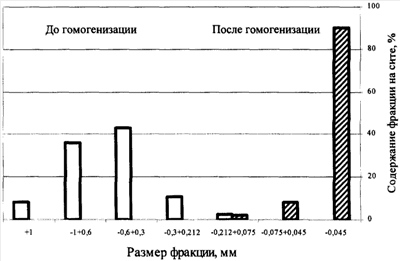
Изобретение относится к электродному производству, в частности к производству анодной массы для самообжигающихся анодов алюминиевых электролизеров.
Анодная масса представляет композицию нефтяного или пекового кокса с пеком каменноугольного или нефтяного происхождения. Основным требованием к анодной массе для самообжигающихся анодов является пластичность, которая определяет ее способность к самоуплотнению в условиях верхней расплавленной зоны анода. Анодная масса относится к высококонцентрированным дисперсным системам, седиментационная устойчивость которых и способность к самоуплотнению определяется концентрацией кокса-наполнителя и его взаимодействием с пеком-связующим. Особое внимание при производстве анодных масс уделяется количеству и составу пылевой фракции в шихте. Пылевая фракция обладает наибольшей адсорбционной поверхностью и является определяющей при определении потребности в пеке-связующем для обеспечения необходимой пластичности анодной массы. Композиция пылевой фракции и пека-связующего образует в анодной массе матричную структуру, в которой распределяются зерновые фракции. Свойства матричной структуры определяют седиментационную устойчивость анодной массы и способность к самоуплотнению в расплавленном состоянии. Известно, что увеличение содержания в шихте или увеличение тонины помола пылевой фракции приводит к улучшению качества анодной массы и повышает ее устойчивость к расслоению в самообжигающемся аноде. Однако плохая смачиваемость и склонность мелких частиц к агломерации при смешении с пеком не позволяют получить качественную анодную массу.
Известен способ производства анодной массы для самообжигающегося анода (М.А.Коробов, А.А.Дмитриев. Самообжигающиеся аноды алюминиевых электролизеров. М.: Металлургия, 1982), при котором пылевую фракцию готовят измельчением кокса в шаровых мельницах, смешивают с крупнозернистыми фракциями, подогревают и смешивают с расплавленным каменноугольным пеком.
Недостатком известного способа является нестабильность состава фракции – 0,075 мм, что является причиной больших колебаний пластичности и седиментационной неустойчивости анодной массы. Недостатком известного способа также является неравномерность распределения пека-связующего между частицами пылевой фракции при смешении из-за низкой смачиваемости частиц и их высокой способности к образованию агломератов. Неоднородность смешения приводит к непредсказуемому поведению анодной массы в условиях самообжигающегося анода.
Наиболее близким к предлагаемому изобретению является известный способ приготовления коксо-пековой композиции для углеродных изделий (Авт. свид. СССР № 816956, МПК С01В 31/02, 1981), включающий измельчение и разделение кокса на фракции, смешение тонкой фракции кокса (-0,09+0,01 мм) с расплавленным пеком, и затем введение в приготовленную смесь фракции кокса -3,0+0,09 мм.
Однако известный способ не обеспечивает стабильность состава фракции -0,09+0,01 мм и требует большой длительности смешения для получения однородной композиции (процесс приготовления коксо-пековой композиции занимает один час). Нестабильность состава фракции -0,09+0,01 мм приводит к нестабильности свойств анодной массы, а длительность процесса не совместима с требованиями многотоннажного производства анодной массы в алюминиевой промышленности.
Задачей изобретения является увеличение производительности процесса подготовки анодной массы и сокращение длительности процесса.
Технический результат заключается в получении анодной массы с высокими физико-механическими свойствами на основе однородной мелкодисперсной коксо-пековой композиции стабильного состава.
Указанный технический результат достигается тем, что в способе производства анодной массы, включающем измельчение и разделение кокса на фракции, смешивание одной фракции кокса с расплавленным пеком, добавление в полученную смесь другой фракции кокса и последующее перемешивание смеси, согласно заявляемому решению, разделение кокса производят не менее чем на две фракции размером более 1,0 мм и менее 1,0 мм, причем сначала смешивают фракцию кокса менее 1,0 мм с расплавленным пеком и одновременно со смешиванием измельчают кокс до пылевидной фракции размером менее 0,045 мм под воздействием гидроударно-кавитационного поля, после чего добавляют другую фракцию кокса и снова перемешивают.
Способ дополняют частные отличительные признаки, направленные также на достижение указанного технического результата.
Смешивание фракции кокса менее 1,0 мм и одновременно ее измельчение осуществляют при давлении менее 100 мбар.
Фракцию кокса более 1,0 мм перед добавлением в смесь предварительно смешивают с расплавленным пеком при давлении менее 100 мбар.
По отношению к прототипу у предлагаемого способа имеются следующие отличия. Разделение измельченного кокса производят не менее чем на две фракции: фракцию с размером частиц более 1,0 мм и фракцию с размером частиц менее 1,0 мм. Фракция – 1,0 мм используется для получения гомогенной мелкодисперсной коксо-пековой композиции с размером частиц кокса менее 0,045 мм. Гомогенную мелкодисперсную коксо-пековую композицию получают в результате объединения процессов смешивания и измельчения кокса в среде расплавленного пека в центробежном гидроударном диспергаторе, генерирующем поле последовательных гидроударных и кавитационных импульсов с частотой резонансного разрыва частиц. Под воздействием серии резонансных нагрузок в режиме «сжатие-разрежение» частицы кокса разрушаются до размера менее 0,045 мм. Образование новой поверхности при разрушении частиц кокса непосредственно в среде расплавленного пека обеспечивает отсутствие окисления и адсорбции атмосферных газов на поверхности, что обеспечивает хорошее смачивание частиц кокса. Кавитационные импульсы препятствуют образованию конгломератов частиц кокса в расплавленном пеке, что обеспечивают гомогенность пеко-пылевой композиции. Высокая дисперсность твердой фазы и эффективное смачивание поверхности разрушения способствуют возникновению подвижной структурной сетки в объеме связующего, в узлах которой располагаются частицы кокса. Введение в такую структурированную матрицу крупнодисперсных частиц обеспечивает их седиментационную устойчивость в расплавленной анодной массе. Анодная масса на основе гомогенной мелкодисперсной коксо-пековой композиции по структуре и устойчивости подобна концентрированным коллоидным системам, поэтому условно может быть названа “коллоидной”.
Анализ, проведенный заявителем, показал, что совокупность признаков является новой, а сам способ и устройство для его осуществления удовлетворяют условию изобретательского уровня ввиду новизны причинно-следственной связи “отличительные признаки – технический результат”.
Изобретение поясняется на диаграмме грансостава фракций кокса менее 1,0 мм до и после обработки коксо-пековой композиции в центробежном гидроударном диспергаторе, представленной на чертеже.
Предлагаемый способ производства “коллоидной” анодной массы реализуется следующим образом. Предварительно измельченный кокс делят на фракции +1,0 мм и -1,0 мм. Фракция кокса -1,0 мм и расплавленный пек совместно дозировано подают в центробежный гидроударный диспергатор. Фракция кокса -1,0 мм измельчается под действием гидроударных и кавитационных импульсов до размера менее 0,045 мм и одновременно гомогенизируется в среде расплавленного пека. Для удаления легколетучих компонентов и атмосферных газов подготовка мелкодисперсной коксо-пековой композиции может проводиться при остаточном давлении менее 100 мбар. Готовая мелкодисперсная коксо-пековая композиция поступает в накопительный резервуар, из которого используется для смешения с крупнодисперсной фракцией кокса более 1,0 мм в смесителе периодического или непрерывного действия. Крупнодисперсная фракция кокса более 1,0 мм перед смешением с мелкодисперсной коксо-пековой композицией может предварительно вакуумироваться до остаточного давления менее 100 мбар для удаления воздуха из порового пространства кокса.
Выполненные лабораторные эксперименты подтверждают эффективность предлагаемого способа. Мелкодисперсная коксо-пековая композиция обрабатывалась в течение 10 минут в центробежном гидроударном диспергаторе из каменноугольного пека и исходной фракции кокса размером -1,0 мм. Содержание твердой фракции в мелкодисперсной коксо-пековой композиции составляло 58%. На основе полученной мелкодисперсной коксо-пековой композиции была приготовлена анодная масса. В таблице представлены сравнительные результаты испытаний обожженных анодных масс, подготовленных известным (по прототипу) и предлагаемым способами.
Из данных, представленных в таблице, видно, что производство анодной массы по предлагаемому способу позволяет снизить удельное электрическое сопротивление и газопроницаемость, увеличить плотность и прочность анодной массы. Снижение удельного электрического сопротивления и газопроницаемости обеспечит снижение расхода электроэнергии и углерода при электролизе алюминия.
Таблица |
Показатель |
Единицы измерения |
Способ приготовления анодной массы |
Известный |
Предлагаемый |
Кажущаяся плотность |
кг/см3 |
1,51 |
1,54 |
Прочность на сжатие |
МПа |
47,8 |
50,9 |
Общая пористость |
% |
26,8 |
22,0 |
Удельное электрическое сопротивление |
мкОм·м |
66 |
59 |
Газопроницаемость |
nPm |
7,4 |
2,8 |
Коэффициент относительного удлинения |
% |
15,6 |
114,6 |
Формула изобретения
1. Способ производства анодной массы, включающий измельчение и разделение кокса на фракции, смешивание одной фракции кокса с расплавленным пеком, добавление в полученную смесь другой фракции кокса и последующее перемешивание смеси, отличающийся тем, что разделение кокса производят не менее чем на две фракции: размером более 1,0 мм и менее 1,0 мм, причем сначала смешивают фракцию кокса менее 1,0 мм с расплавленным пеком и одновременно со смешиванием измельчают кокс до пылевидной фракции размером менее 0,045 мм под воздействием гидроударно-кавитационного поля, после чего добавляют другую фракцию кокса.
2. Способ по п.1, отличающийся тем, что смешивание фракции кокса менее 1,0 мм и одновременное ее измельчение осуществляют при давлении менее 100 мбар.
3. Способ по п.1, отличающийся тем, что фракцию кокса более 1,0 мм перед добавлением в смесь предварительно смешивают с расплавленным пеком при давлении менее 100 мбар.
РИСУНКИ
|
|