|
(21), (22) Заявка: 2006115293/06, 03.05.2006
(24) Дата начала отсчета срока действия патента:
03.05.2006
(46) Опубликовано: 20.01.2008
(56) Список документов, цитированных в отчете о поиске:
ШНЕПП В.Б. Конструкция и расчет центробежных компрессорных машин. – М.: Машинострение, раздел 5.1, с.208-209. RU 2109176 C1, 20.04.1998. RU 2140578 C1, 27.10.1999. ЕР 0194837 A3, 17.09.1986. WO 97/32133 A1, 04.09.1997. DE 3738929 A1, 24.05.1989.
Адрес для переписки:
420029, г.Казань, Сибирский тракт, 40, ЗАО “НИИтурбокомпрессор им. В.Б. Шнеппа”
|
(72) Автор(ы):
Залялов Валерий Адельзянович (RU), Архипов Александр Иванович (RU)
(73) Патентообладатель(и):
Закрытое акционерное общество “Научно-исследовательский и конструкторский институт центробежных и роторных компрессоров им. В.Б. Шнеппа” (RU)
|
(54) КОРПУС СЖАТИЯ НА ОПОРНОЙ РАМЕ
(57) Реферат:
Изобретение относится к общему машиностроению, может быть использовано в компрессорной технике при проектировании компрессорных агрегатов и компрессорных установок и обеспечивает соосность ротора корпуса сжатия с приводным валом двигателя или мультипликатора. Этот технический результат достигается тем, что в корпусе сжатия ось корпуса зафиксирована относительно опорной рамы шпоночными соединениями, образованными в стыках каждой лапы корпуса с регулирующей прокладкой, зафиксированной относительно стойки опорной рамы посредством штифтов, при этом продольные оси каждой пары шпонок в диагонально расположенных лапах корпуса совпадают и пересекаются с общей осью другой пары шпонок в точке, лежащей на проекции в плане продольной оси корпуса, которая делит угол между осями двух пар шпонок пополам. 11 ил.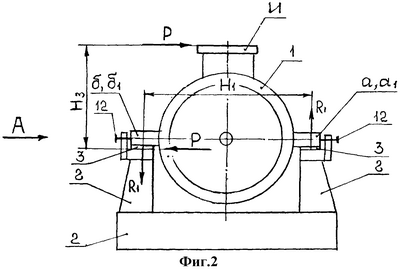
Предлагаемое изобретение относится к общему машиностроению и может быть использовано в компрессорной технике при проектировании компрессорных агрегатов и компрессорных установок.
Одним из необходимых условий нормальной работы корпуса сжатия является обеспечение соосности его ротора с приводным валом двигателя или мультипликатора. Это непростая задача, поскольку в процессе работы корпус сжатия подвергается значительному нагреву и на него воздействуют нагрузки от присоединенных к нему труб газовой коммуникации.
Конструктивно эта проблема решена, см. книгу В.Б.Шнеппа “Конструкция и расчет центробежных компрессорных машин”. – М.: Машиностроение, 1995 г. ББК 31.76 Шн 76 УДК 621.515, раздел 5.1, стр.208, 209, и заключается в следующем:
– опорные лапы корпуса сжатия 1 (будем называть его в дальнейшем – корпус), как правило, образованы диаметрально на его наружной цилиндрической поверхности по две с каждой стороны а, а1 и б, б1, расположены горизонтально, см. фиг.1 и опираются на стойки г опорной рамы 2 через регулирующие прокладки 3;
– в нижней части корпуса 1, на его цилиндрической поверхности, образованы продольные выступы в (шпонки), которые соединены с направляющими д опорной рамы 2 таким образом, что боковые перемещения выступов в исключены упорами е, но возможны перемещения вдоль оси корпуса и вертикально вниз.
При нагреве корпуса 1 изменения положения оси корпуса (его ротора) по высоте практически не происходит потому, что опорные плоскости лап аа1, бб1 проходят близко относительно оси корпуса, а боковое смещение оси исключено благодаря упорам е, препятствующим боковым смещениям выступов в корпуса 1.
Такое конструктивное решение является оптимальным для корпуса с нижним расположением патрубков ж газовой коммуникации потому, что при воздействии внешней нагрузки Р на опорную раму 2 воздействует изгибающий момент М=Р·Н и реакция R, равная по величине Р и направленная ей навстречу.
Изгибающий момент М воспринимается реакциями R1 опор г, которые образуют реактивный момент M=H1·R1. Очевидно, что в данном случае величина реакций R1 не будут значительными по величине ввиду небольшой величины Н.
Однако на практике возможные и другие конструктивные решения, когда патрубки И расположены в верхней части корпуса 1, фиг.1. В этом случае при воздействии внешней нагрузки Р на опорную раму 2 будет передаваться изгибающий момент M1=P·Н2, который будет существенно больше по величине, чем для корпуса с нижним расположением патрубков Ж. Этот момент будет также восприниматься реакциями R1 опор г, которые образуют реактивный момент M1=H1·R1. Отсюда видно, что реакции R1 опор в этом случае будут значительно больше, чем для корпуса с нижним расположением патрубков, а это потребует значительного усиления узлов крепления корпуса 1 к стойкам г рамы и усиления самой рамы 2. Кроме того, известное устройство фиксации оси корпуса неспособно воспринимать внешние нагрузки, действующие вдоль оси корпуса или под острым углом к ней.
Предлагаемое конструктивное решение позволяет исключить недостаток известной конструкции при сохранении его качества – сохранения расположения оси корпуса при его работе. В предлагаемом корпусе сжатия узлы фиксации – шпоночные соединения корпуса с опорной рамой перенесены с нижней части в среднюю часть корпуса 1, а именно – в стыки опорных лап корпуса со стойками г опорной рамы. Этим достигается существенное уменьшение плеча сил Н3<Н2 фиг.1, 2 для боковой нагрузки Р, действующей на патрубки И корпуса 1, а значит и существенное уменьшение нагрузок, действующих на стыки корпуса 1 с опорной рамой 2. В предлагаемом корпусе узлы фиксации оси способны воспринимать внешние нагрузки, действующие не только в поперечном направлении, но и вдоль оси корпуса или под острым углом к ней.
Предлагаемый корпус сжатия представлен на фиг.2÷8, 11.
На фиг.2 показан вид на корпус 1 с торца, со стороны приводного вала.
На фиг.3 показан вид на корпус 1 сбоку, по стрелке А.
На фиг.4 показан вид на корпус 1 сверху, по стрелке Б.
На фиг.5 показан крупным планом вид сверху на лапу б корпуса 1.
На фиг.6 показан продольный разрез узла соединения лапы б корпуса 1 со стойкой г опорной рамы 2.
На фиг.7 показан крупным планом в разрезе узел крепления лапы б корпуса 1.
На фиг.8 показан поперечный разрез узла соединения лапы б корпуса 1 со стойкой г опорной рамы 2.
На фиг.9, 10 показаны схемы действия внешних нагрузок на опоры рамы.
На фиг.11 показаны в перспективном изображении, в разрезе 1/4 части, в отсоединенном положении все элементы узла крепления лапы б корпуса 1 со стойкой г опорной рамы 2.
Сущность предлагаемого корпуса заключается в следующем. На наружной поверхности корпуса 1 образованы выступы в виде четырех опорных лап a, a1, б, б1, фиг.4. Лапы а, а1 расположены диаметрально по отношению лап б, б1 в горизонтальной плоскости, фиг.2. Каждая лапа опирается на стойку г опорной рамы 2 через регулирующие прокладки 3. В стыке каждой лапы а, a1, б, б1 с регулирующими прокладками 3 образованы шпоночные соединения 4, фиг.6.
Каждая регулирующая прокладка 3 зафиксирована относительно стойки г опорной рамы 2 посредством штифтов 5, фиг.5, 8. Шпоночные соединения 4, фиг.6 в стыках каждой лапы а, a1, б, б1 с регулирующими прокладками 3 устанавливают таким образом, чтобы продольные оси пары шпонок в лапах а, б1 совпали (общая ось К), фиг.4, и пересеклись с общей осью Л шпонок в лапах а1, б в точке О, находящейся на проекции, в плане, продольной оси М корпуса 1, которая делит угол между осями Л и К пополам.
Как показано выше для корпуса сжатия 1 с верхним расположением патрубков И, фиг.2, предложенное конструктивное решение фиксации его оси является более предпочтительным, так как перенесение узла фиксации с нижней части корпуса в его среднюю часть существенно уменьшает плечо действия боковой силы Р, т.е. Н3<Н2 и, как следствие, существенно уменьшает величину реакций опор R1. Совмещение в опорах корпуса 1 узла фиксации его оси позволяет более эффективно использовать стойки г опорной рамы 2, а также позволяет исключить из конструкции отдельный, специально предназначенный для фиксации оси корпуса узел в нижней части корпуса (выступы в, направляющие д, упоры е, см.фиг.1). Кроме того, узлы фиксации оси в предлагаемом корпусе способны воспринимать внешние нагрузки в любом направлении.
Однако простое механическое перенесение узла фиксации на лапы 1 корпуса 1 невозможно ввиду того, что в процессе работы корпус 1 нагревается и его опорные лапы а, а1, б, б1 перемещаются не вдоль оси корпуса 1, а под углом к ней. Рассмотрим перемещение точки О2 лапы а, фиг.4, относительно точки О при нагреве корпуса. Это перемещение можно представить как геометрическую сумму перемещений вдоль оси корпуса 1- L и в поперечном направлении – L1.
Величины перемещений определяются из соотношений

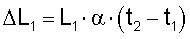
где L – расстояние от точки О до точки O1;
L1– расстояние от точки О1 до точки О2;
– коэффициент линейного расширения материала корпуса 1;
t1 – начальная температура корпуса 1;
t2 – конечная температура корпуса 1.
Угол наклона вектора перемещения точки О2 лапы корпуса 1 относительно оси М определяется из соотношения
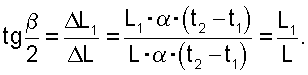
Следовательно, все точки опорных лап корпуса 1, лежащие на осях К и Л, будут при нагреве перемещаться вдоль этих осей, поэтому, расположив шпоночные соединения в лапах корпуса 1 вдоль осей К и Л, обеспечиваем свободное перемещение лап относительно стоек г опорной рамы 2, при этом положение точки О корпуса 1, лежащей на пересечении осей К и Л будет при нагреве оставаться неизменным, а так как проекция, в плане, оси М корпуса 1 проходит через точку О, а ее расположение относительно осей К и Л симметрично (угол ), значит и ее положение при нагреве будет неизменным.
Предложенное конструктивное решение достаточно просто и технологично. На каждой лапе а, а1, б, б1 корпуса 1, фиг.11, кроме отверстия Н для отжимного болта 6 и отверстия П для втулки 7 и шпильки 8 с гайками 9 выполняют отверстие Р для установки вкладыша 10, на нижнем конце которого выполнен выступ С с заходной фаской в виде шпонки. Вкладыш 10 устанавливают в отверстие Р и фиксируют стопорным кольцом 11, монтируемым в канавку Т.
На верхнем торце вкладыша 10 выполнены резьбовое отверстие Y для монтажа и извлечения вкладыша и пазы Ф, соосные с выступом С, для регулирования вкладыша по углу при сборке. На верхней плоскости каждой лапы а, а1, б, б1 выполняют контрольную риску X, совпадающую по направлению с соответствующей осью Л или К, фиг.4.
Между каждой опорной лапой а, а1, б, б1 и стойкой г опорной рамы 2 устанавливают регулирующие пластины 3, на верхних плоскостях которых выполнены шпоночные пазы Ц, имеющие наклон под углом к боковой кромке Ш и соответствующие по направлению осям Л и К. Выступающая за внешнюю кромку лапы пластина штифтуется штифтами 5 (после проведения регулировки) со стойкой г опорной рамы 2.
Для настройки по высоте оси М корпуса 1, фиг.3, 4, производят доработку нижней плоскости регулирующей пластины 3. Для обеспечения монтажа и демонтажа в пластинах 3 выполнены отверстия Щ и пазы Э для шпилек 8 и для отжимных болтов 6.
Сборка и регулирование корпуса сжатия 1 на раме 2.
Установку корпуса сжатия 7 на раму 2 производят, как правило, после установки мультипликатора.
1. Корпус 1 устанавливают на стойки г опорной рамы 2, при этом отверстия Ю, фиг.11, для установки шпилек 8 не выполнены.
2. Регулируют положение корпуса 1 так, чтобы ось его ротора М заняла соосное положение с соответствующим валом 14 мультипликатора, с обеспечением требуемого расстояния L между торцами валов, фиг.4. Регулирование по высоте производится отжимными болтами 6, по боковому смещению монтажными болтами 12 и по смещению вдоль оси корпуса 1 монтажными болтами 13.
3. После завершения регулирования производят замер фактического расстояния (зазора) S между опорными поверхностями лап корпуса 1 и стоек г рамы 2, а также разметку центров отверстий Ю на стойках г для установки шпилек 8.
4. Производят доработку регулирующих пластин 3 с нижней опорной поверхности до размеров, соответствующих замеренным фактическим зазорам S.
5. Корпус 1 демонтируют с рамы 2.
6. Производят сверление и нарезание резьбы в отверстиях Ю на стойках г рамы 2.
7. Корпус 1 повторно устанавливают на стойки г рамы 2 и проводят регулирование согласно п.2.
8. В зазор S между опорными поверхностями лап корпуса 1 и стойками г рамы 2 вводят доработанные регулирующие пластины 3, совмещая отверстия Щ и пазы Э и Ц с соответствующими отверстиями П, Н и Р в лапах корпуса 1, фиг.11.
9. В отверстия Р лап корпуса 1 устанавливают вкладыши 10, ориентируя пазы Ф по направлению рисок Х на лапах корпуса.
10. Убедившись, что выступ С вкладыша 10 вошел в ответный паз Ц пластины 3, в канавку Т устанавливают стопорное кольцо 11.
11. Отжимные болты 6 демонтируют, после чего проводят контроль прилегания поверхностей пластин 3 к сопрягаемым поверхностям лап корпуса 1 и стоек г опорной рамы 2.
12. Устанавливают втулки 7 так, чтобы обеспечить зазоры S1 и S2, фиг.7, с лапами корпуса 1, причем величина зазора S2 должна быть больше ожидаемого перемещения лапы относительно стойки г опорной рамы 2.
13. Устанавливают шпильки 8, затягивают гайки 9.
14. Производят совместную обработку отверстий в пластинах 3 и стойках г опорной рамы 2.
15. Устанавливают штифты 5.
16. Демонтируют монтажные болты 12 и 13.
Сборка и регулирование корпуса 1 на стойках г рамы 2 завершена.
Работа предлагаемого корпуса сжатия
После завершения сборки и регулирования корпуса 1 на раме 2, сборки трансмиссии, газовой коммуникации, других систем и проведения их проверки агрегат запускают. В процессе работы корпус 7 нагревается, при этом его опорные лапы a, а1, б, б1, зафиксированные шпоночными соединениями 4, фиг.6, со стойками г опорной рамы 2 перемещаются вдоль осей К и Л, фиг.4.
Крепление лап корпуса 1 к стойкам г шпильками 8 и гайками 9 через втулки 7 обеспечивает возможность их перемещения только в горизонтальной плоскости на величину зазора S2, фиг.7, рассчитанную на максимально возможную величину перемещения при нагреве. Перемещение лап a, a1, б, б1 по вертикали исключено, благодаря наличию буртов у втулок 7. Зазор S1 между буртом втулки 7 и верхней плоскостью лапы делает возможным перемещения только в горизонтальной плоскости. Опорные лапы a, a1, б, б1, перемещаясь вдоль осей К и Л, обеспечивают сохранение неизменного положения точки О корпуса, фиг.4, а значит и его оси М, проекция которой, в плане, проходит через эту точку и делит угол между осями К и Л пополам, то есть расположена симметрично относительно этих осей. Система шпоночных соединений опорных лап а, a1, б, б1 корпуса 1 с опорной рамой 2 позволяет воспринимать внешние нагрузки, действующие в любом направлении, благодаря тому, что шпонки в лапах a, б1 расположены вдоль оси К, а шпонки в лапах а1, б расположены вдоль оси Л, которые пересекаются под углом .
Взаимодействие внешних нагрузок с опорами рамы 2 поясняется на схемах, приведенных на фиг.9 и 10. Рассмотрим для простоты рассуждений случай, когда угол =90°С.
Известно, что шпоночные соединения способны воспринимать нагрузки, действующие по нормали к их боковым поверхностям. На схеме, приведенной на фиг.9, показано воздействие внешней нагрузки Р2 по направлению оси К. В этом случае в опорах II и IV рамы 2 возникают реакции R2, направленные навстречу силе Р2 и уравновешивающие ее. При воздействии внешней нагрузки P3 по направлению оси Л в опорах I и III рамы 2 возникают реакции R3, направленные навстречу силе Р3 и уравновешивающие ее.
На схеме, приведенной на фиг.10, показано воздействие внешней нагрузки P4 под острым углом к направлению осей Л и К, например вдоль оси М корпуса 1. В этом случае в опорах I и IV возникают реакции R4, направленные по нормали к осям Л и К. Каждую из этих реакций можно представить как геометрическую сумму составляющих и . Составляющие направлены параллельно оси М навстречу силе P4, а их сумма уравновешивает силу Р4. Составляющие в опорах I и IV направлены перпендикулярно оси М и уравновешивают друг друга.
При воздействии внешней нагрузки P5 перпендикулярно оси М в опорах III и IV возникают реакции R5, направленные по нормали к осям Л и К. Каждую из этих реакций можно представить как геометрическую сумму составляющих и . Составляющие направлены перпендикулярно оси М навстречу силе P5, а их сумма уравновешивает силу P5. Составляющие в опорах III и IV направлены вдоль оси М и уравновешивают друг друга.
Из рассмотрения схем очевидно, что наиболее предпочтительным с точки зрения нагружения опор является расположение опор I, II, III, IV, когда угол между осями Л и К составляет <90° или близок к нему, хотя и в других случаях при других углах система шпонок в опорах будет воспринимать все внешние нагрузки.
Формула изобретения
Корпус сжатия на опорной раме, на наружной поверхности которого образованы выступы в виде четырех опорных лап, расположенных диаметрально в горизонтальной плоскости по две с каждой стороны корпуса, опирающихся на стойки опорной рамы через регулирующие прокладки, а ось корпуса зафиксирована относительно опорной рамы шпоночными соединениями, отличающийся тем, что в нем шпоночные соединения образованы в стыках каждой лапы корпуса с регулирующей прокладкой, зафиксированной относительно стойки опорной рамы, например, посредством штифтов, при этом продольные оси каждой пары шпонок в диагонально расположенных лапах корпуса совпадают и пересекаются с общей осью другой пары шпонок в точке, лежащей на проекции в плане продольной оси корпуса, которая делит угол между осями двух пар шпонок пополам.
РИСУНКИ
|
|