|
(21), (22) Заявка: 2006137963/04, 27.10.2006
(24) Дата начала отсчета срока действия патента:
27.10.2006
(46) Опубликовано: 20.01.2008
(56) Список документов, цитированных в отчете о поиске:
US 5061741, 29.10.1991. US 5380496 A, 10.01.1995. SU 312447 A1, 07.06.1982. SU 458323 A1, 30.01.1975. US 4870143, 26.09.1989. EP 0137916 A2, 24.04.1985.
Адрес для переписки:
650043, г.Кемерово, ул. Красная, 6, к.204, КемГУ, патентный отдел, начальнику
|
(72) Автор(ы):
Шарыкин Олег Витальевич (RU), Шаповалов Виктор Владимирович (RU), Смирнов Дмитрий Владимирович (RU), Никифоров Виктор Дмитриевич (RU), Перевощиков Яков Петрович (RU), Степанов Валерий Николаевич (RU)
(73) Патентообладатель(и):
Шарыкин Олег Витальевич (RU), Шаповалов Виктор Владимирович (RU), Смирнов Дмитрий Владимирович (RU), Никифоров Виктор Дмитриевич (RU), Перевощиков Яков Петрович (RU), Степанов Валерий Николаевич (RU)
|
(54) СПОСОБ ПРОИЗВОДСТВА ПОЛИМЕРНЫХ МОНОДИСПЕРСНЫХ ЧАСТИЦ СУСПЕНЗИОННОЙ ПОЛИМЕРИЗАЦИЕЙ И УСТАНОВКА ДЛЯ ЕГО ОСУЩЕСТВЛЕНИЯ
(57) Реферат:
Изобретение относится к технологии производства полимерных гранул, используемых для получения ионообменных смол. Описан способ производства полимерных монодисперсных частиц суспензионной полимеризацией, включающий стадии: приготовление монодисперсных капель путем введения в камеру каплеобразующего устройства водной дисперсионной среды, содержащей стабилизатор дисперсии и образующей непрерывную фазу, эжектирование в водную дисперсионную среду гидрофобной жидкости мономера через отверстия фильеры струями вверх при действии регулярной вибрации для образования жидких капель мономера преимущественно равного размера в водной дисперсионной среде; проведение предварительной полимеризации путем введения в первый реактор полученных жидких капель мономера в водной дисперсионной среде, проведения полимеризации в псевдоожиженном слое с получением суспензии частично полимеризованных капель мономера в водной дисперсионной среде до степени, когда капли уже не могут сливаться или разбиваться; проведение окончательной суспензионной полимеризации при интенсивном перемешивании во втором реакторе; на стадии приготовления монодисперсных капель водную дисперсионную среду вводят в камеру каплеобразующего устройства при температуре 60-90°С, а гидрофобную жидкость мономера вводят в камеру каплеобразующего устройства при температуре 5-25°С или температуре окружающей среды. Также описана установка для производства полимерных монодисперсных частиц суспензионной полимеризацией. Технический эффект – расширение зоны монодиспергирования капель гидрофобной мономерной жидкости в каплеобразующем устройстве, позволяющее варьировать размеры получаемых монокапель, техническое и технологическое упрощение устройства установки. 2 н. и 11 з.п. ф-лы, 7 ил.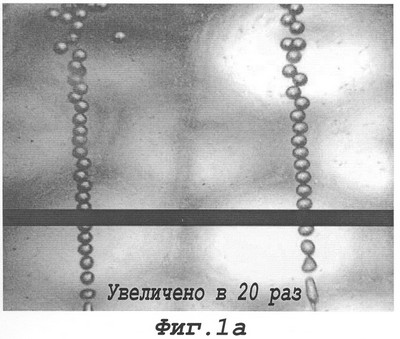
Изобретение относится к технологии производства полимерных гранул, используемых для получения ионообменных смол.
Производство монодисперсных сополимерных частиц включает стадии генерации монодисперсных капель и проведения суспензионной полимеризации, которая обычно проводится в два этапа: предварительная полимеризация монокапель в водной дисперсионной среде и окончательная полимеризация в отдельном аппарате с получением моносферических гранул.
Известен способ генерации монодисперсных капель в каплеобразующем устройстве (патент US 5 380 496, С 08 F 2/20, В 01 F 13/00, опубл. 10.01.1995), осуществляемый путем подачи в каплеобразующее устройство водной дисперсионной среды, эжектирования в нее через фильеру, имеющую, по меньшей мере, одно отверстие, гидрофобной жидкости мономера при действии регулярной вибрации для образования жидких мономерных капель преимущественно равного размера. При этом в качестве водной дисперсионной среды могут быть использованы водонерастворимые неорганические соли или их смеси, такие как фосфаты кальция, карбонат кальция и т.п., а в качестве мономерной жидкости – моновинильные и ди- и тривинильные соединения, примерами которых являются стирол, дивинилбензол, эфиры и нитрилы акриловой и метакриловой кислот, а также их смеси.
Данный способ предусматривает возможность создания условий образования струй, при которых в каплеобразующем устройстве создается область образования капель равного размера. Такими условиями являются скорость истечения жидкости мономера, частота и амплитуда вибрации.
Далее полученные монокапли в водной дисперсионной среде направляют в первый реактор для проведения частичной полимеризации и затем во второй реактор для окончательной суспензионной полимеризации.
Способ предназначен преимущественно для получения частиц относительно больших размеров – 1,0-0,5 мм.
По химико-физической сущности процесса наиболее близким является способ генерации капель (патент US 5 061 741, С 08 L 25/00, С 08 F 2/04, С 08 F 2/00, опубл. 29.10.1991), включающий подачу в камеру каплеобразующего устройства водной дисперсионной среды, содержащей стабилизатор дисперсии и образующей непрерывную фазу, эжектирование в водную дисперсионную среду гидрофобной жидкости мономера через множество отверстий фильеры струями вверх при действии вибрации или без нее для образования жидких капель мономера преимущественно равного размера в водной дисперсионной среде, имеющих плотность, меньшую плотности водной дисперсионной среды. При этом в качестве стабилизатора используют неорганическую водонерастворимую соль либо вещества, образующие в воде коллоидный раствор, такие как карбоксилэтилцеллюлоза, поливиниловый спирт, желатин или крахмал и т.д., в качестве мономерной жидкости обычно используют стирол, эфиры или нитрилы акриловой и метакриловой кислот, дивинилбензол, дивиниловый эфир диэтиленгликоля или их смеси в различных соотношениях и перекисные соединения (например, перекись бензоила) в качестве инициатора. Водную дисперсионную среду и жидкость мономера подают в каплеобразующее устройство при равной температуре обоих потоков от 0 до 40°С и в камере каплеобразования устанавливают температуру 20-25°С. Получают капли равного размера в пределах 0,3-1,0 мм.
Далее полимеризацию получаемых монодисперсных капель проводят в первом реакторе с частичной полимеризацией капель мономера и во втором реакторе с получением целевого продукта. Процесс ведут при перемешивании в обоих реакторах.
Основной недостаток данного способа заключается в том, что при подаче мономерной жидкости и водной дисперсионной среды с равной температурой обоих потоков в каплеобразующем устройстве создается довольно узкий интервал скоростей истечения мономера и частоты вибрации, при которых образуется очень узкая зона образования капель равного размера. Узкая зона монодиспергирования капель не позволяет получать монокапли разных размеров на одной фильере. При необходимости получения монокапель другого размера приходится производить замену фильеры.
Задачей по способу генерации капель является расширение зоны монодиспергирования капель гидрофобной мономерной жидкости в каплеобразующем устройстве, позволяющее варьировать размеры получаемых монокапель на одной фильере изменением частоты вибрации или скорости истечения, а также оптимизировать процесс и повысить эффективность работы каплеобразующего устройства. Кроме того, на этапе полимеризации ставится задача упрощения процесса на стадии частичной полимеризации в первом реакторе.
Поставленная задача решается путем применения способа генерации монодисперсных капель, включающего подачу в камеру каплеобразующего устройства водной дисперсионной среды, содержащей стабилизатор дисперсии и образующей непрерывную фазу, эжектирование в водную дисперсионную среду гидрофобной жидкости мономера через отверстия фильеры струями вверх при действии регулярной вибрации для образования жидких капель мономера преимущественно равного размера в водной дисперсионной среде, в котором предлагается водную дисперсионную среду вводить в камеру каплеобразующего устройства при повышенной температуре, а гидрофобную жидкость мономера вводить в камеру каплеобразующего устройства при пониженной температуре или температуре окружающей среды.
При этом водную дисперсионную среду вводят в каплеобразующее устройство при температуре от 60 до 90°С и гидрофобную жидкость мономера вводят при температуре от 5 до 25°С.
И температуру в камере каплеобразующего устройства устанавливают в пределах 40-60°С.
Кроме того, на стадии формирования капель в качестве стабилизатора капель в водной дисперсионной среде используют метилгидроксиэтилцеллюлозу при концентрации от 0,05 до 0,2% от объема водной дисперсионной среды.
И соотношение объемов гидрофобной жидкости мономера к водной дисперсионной среде составляет от 1:1 до 1:3 соответственно на всех стадиях.
И при линейной скорости истечения струи мономера в водную дисперсионную струю в пределах от 1,2 до 2,2 м/сек регулярную вибрацию в каплеобразующем устройстве ведут на частоте в диапазоне от 500 до 1500 Гц.
Особенностью также является осуществление контроля процесса образования жидких мономерных капель путем визуализации с помощью оптико-цифрового комплекса.
В данном изобретении в качестве физической основы генерации капель использован известный метод вынужденного капиллярного распада струи (ВКРС), который заключается в том, что струя гидрофобной жидкости при введении в водную среду через отверстие подвергается вибрационному активированию внешним источником вибрации с частотой, соответствующей резонансному распаду струи с образованием столбика капель равного размера в водной среде (фото на фиг.1а). Процесс можно визуально наблюдать с помощью оптико-цифрового комплекса. Условия обеспечения гидродинамического режима, при котором образуются мономерные капли равного размера в непрерывной фазе – водной дисперсионной среде, включают в себя ряд характеристик, основными из которых являются скорость потока струй мономера и частота вибрации. Согласно патенту US 5 380 496 не менее важной характеристикой является также амплитуда вибрации.
Однако задачей известных способов является лишь нахождение области монодиспергирования для установления устойчивого рабочего гидродинамического режима.
В отличие от известных способов экспериментально установлено, что устойчивость режима монодиспергирования возрастает в широком диапазоне частот вибрации и скорости истечения струи мономера, если диспергируемая и непрерывная фазы имеют разную температуру. При этом установлено, что оптимальным сочетанием является пониженная температура мономера 5-25°С и повышенная температура водной дисперсионной среды 60-90°С. На фиг.2а показана заштрихованная область устойчивого режима монодиспергирования при равной температуре обеих фаз – 20°С. На фиг.2б показана область монодиспергирования при температуре смеси мономеров 20°С и водной дисперсионной среды 78°С, при этом температура в камере каплеобразующего устройства составила 44°С.
Как видно на фиг.2а и 2б диапазон рабочих частот монодиспергирования находится в пределах 420-500 Гц при равных температурах обеих фаз и в пределах 500-1130 Гц при разных температурах фаз. Также несколько увеличивается интервал скорости истечения мономера при сохранении монодисперсного режима. Это позволяет во втором случае плавно регулировать диаметр капель на фильтре с диаметром отверстий, например, 200 микрон в диапазоне от 0,4 до 0,58 мм и существенно повышает устойчивость процесса при различных технологических колебаниях параметров процесса. На фиг.1б приведены стробоскопически отображенные фотографии, выполненные при помощи оптико-цифрового комплека. Фотографии получены в одинаковых условиях при единственном переменном параметре – частоте вибрации. Частота указана над каждым столбиком. В рассматриваемом процессе при монодисперсном режиме одному колебанию вибратора соответствует образование одной капли. Поэтому при постоянной скорости истечения струи увеличение частоты вибрации уменьшает диаметр капли и увеличивает их число в единицу времени, что показано на фиг.1б. Понижение температуры смеси мономеров, с одной стороны, позволяет уменьшить полимеризацию в зоне отверстий фильеры и продлить срок их службы от чистки до чистки, и, с другой стороны, повышает вязкость вытекающей струи. Одновременное повышение вязкости струи смеси мономеров и понижение вязкости нагретой водной дисперсионной среды, а также теплообмен между ними создают гидродинамические условия для расширения зоны монодиспергирования капель. При понижении температуры мономерной жидкости ниже 5°С возрастает опасность чрезмерного охлаждения водной среды и образования застойных зон в камере каплеобразования, а при повышении температуры выше 25°С ускоряется зарастание отверстий фильеры. Экспериментально установлено, что оптимальная температура смеси мономеров находится в интервале от 5 до 25°С, лучше от 10 до 15°С. В результате подбором сочетаний температур непрерывной и мономерной фаз область монодиспергирования капель может быть расширена в диапазоне частот от 500 до 1500 Гц. Визуальное наблюдение за процессом монодиспергирования капель, контролирование границ области монодиспергирования, оперативное регулирование параметров гидродинамического режима: частоты вибрации, скорости потока мономера и температуры потоков обоих фаз производится в режиме on-line с помощью оптико-цифрового комплекса (ОЦК), схема которого приведена на фиг.3.
В качестве мономерной смеси используется композиция, содержащая моновинильное соединение – стирол в количестве 80-85%, поливинильные соединения – дивинилбензол 7-10% и этилстирол 5-8%, а также перекись бензоила 0,3-0,6% в качестве инициатора. Наличие ди- и тривинильных сшивающих агентов в смеси обеспечивает устойчивость структуры получаемых капель при их мягком перемешивании в псевдоожиженном слое, так как вязкоупругое поведение капель достигается при небольшой (3-10%) степени конверсии уже на начальном этапе полимеризации.
В качестве стабилизатора дисперсии получаемых мономерных капель могут быть использованы водонерастворимые неорганические соли и их смеси либо соединения, образующие с водой коллоидные растворы, выбираемые в зависимости от требуемых условий, обеспечивающие плотность водной дисперсионной среды, достаточную для создания условий псевдоожиженного (обратно кипящего) слоя по отношению к плотности мономера. Для применяемой смеси мономеров в качестве оптимального стабилизатора выбрана метилгидроксиэтилцеллюлоза, марка МНЕС – 8000, промышленное название – кульминал. Оптимальные концентрации раствора кульминала различны для стадий формирования капель и их полимеризации. На стадии каплеобразования минимальная концентрация кульминала – 0,05%. При меньшей концентрации нарушается стабильность эмульсии и капли начинают слипаться. Максимальная концентрация – 0,2%, т.к. при более высоком ее значении возрастает вязкость водной дисперсионной среды и сокращается диапазон частот зоны монодиспергирорования. Концентрация кульминала – 0,2% обеспечивает стабильность эмульсии в условиях полимеризации.
Известно устройство для проведения суспензионной полимеризации (патент US 4870143, С 08 F 2/20, С 08 F 12/08, опубл. 26.09.1989), которое содержит каплеобразующее устройство, в которое через линию подачи подается мономерная жидкость и через отверстия фильеры с образованием капель равного размера вводится в водную дисперсионную среду, введенную в устройство через свою линию подачи; реактор башенного типа с коническими верхней и нижней частями, содержащий входное отверстие в верхней части для введения и формирования потока вниз водной дисперсионной среды и выходное отверстие в нижней части для ее вывода, линию циркуляции, подсоединенную к выходному отверстию для выведения водной дисперсионной среды и циркуляции ее во входное отверстие, линию подачи суспензии жидких капель мономера в водной дисперсионной среде, подсоединенную к линии циркуляции в верхней части, и линию выведения образуемых полимерных частиц в водной дисперсионной среде. В таком устройстве процесс суспензионной полимеризации осуществляется в одном аппарате за счет наличия линии циркуляции.
Наиболее близкой к предлагаемой по аппаратурному составу является установка для производства полимерных частиц равного размера суспензионной полимеризацией (патент US 5 380 496, С 08 F 2/20, В 01 F 13/00, опубл. 10.01.1995), включающая:
– устройство образования капель, содержащее, по меньшей мере, одну фильеру с, по меньшей мере, одним отверстием, через которое проходит жидкость мономера, имеющая плотность меньшую, чем плотность водной дисперсионной среды, и устройство для вибрации мономерной жидкости при проходе через поры, в котором каплеобразующее устройство также содержит линию циркуляции водной дисперсионной среды для контактирования водной дисперсионной среды с каплями по противоточной схеме;
– первый реактор, содержащий вход для введения водной дисперсионной среды, содержащей образованные капли; средство для циркуляции водной дисперсионной среды от нижней до верхней части реактора; средство для перемешивания водной дисперсионной среды, содержащей капли; и выход для вывода жидкой дисперсионной среды с частично полимеризованными каплями; при этом реактор частично полимеризует капли жидкости мономера, введенной из каплеобразующего устройства таким образом, что плотность капель не превышает плотности водной дисперсионной среды при заданной температуре полимеризации; а также
– второй реактор, содержащий вход для введения частично полимеризованных капель, выводимых из первого реактора во второй реактор, и средство для перемешивания капель и водной дисперсионной среды для дальнейшей полимеризации.
К недостаткам устройства можно отнести использование линии циркуляции водной дисперсионной среды в первом реакторе, требующей установки дополнительного оборудования в виде емкостей, насосов, теплообменников и регулирующих устройств расхода и температуры в линии циркуляции. Кроме того, наличие линии циркуляции усложняет отделение капель, производимое непосредственно из нижней части первого реактора.
Таким образом, задачей изобретения по устройству установки для суспензионной полимеризации является ее техническое и технологическое упрощение за счет исключения из ее контура обводной линии циркуляции водной дисперсионной среды.
Поставленная задача решается использованием установки для производства полимерных монодисперсных частиц суспензионной полимеризацией, включающей: каплеобразующее устройство, содержащее камеру для образования монодисперсных капель, фильеру с множеством отверстий для эжектирования струй гидрофобной жидкости мономера, средство для вибрации при эжектировании струй, а также вход для линии подачи водной дисперсионной среды выше фильеры, вход для линии введения гидрофобной жидкости мономера ниже фильеры и выход в верхней части камеры для отвода эмульсии образованных капель мономера в водной дисперсионной среде; первый реактор, содержащий вход в верхней части для введения эмульсии образованных капель мономера в водной дисперсионной среде, и выход в нижней части для вывода суспензии частично полимеризованных мономерных капель в водной дисперсионной среде; и второй реактор, содержащий вход для введения суспензии частично полимеризованных мономерных капель в водной дисперсионной среде, средство для перемешивания суспензии и выход для отвода целевого продукта, при этом первый реактор установки выполнен в виде, по крайней мере, одного трубчатого цилиндрического корпуса с коническими верхней и нижней частями при отношении длины к диаметру не менее 20:1 соответственно.
При этом отношение длины к диаметру первого реактора предпочтительно составляет (100-500):1 соответственно.
А также трубчатый цилиндрический корпус первого реактора выполнен разделенным внутренними перегородками на секции.
И конические верхняя и нижняя части корпуса имеют угол конусности не более 30°.
При этом первый реактор выполнен в виде каскада последовательно соединенных корпусов с равномерным вертикальным смещением последовательных корпусов вниз относительно друг друга.
Кроме того, каплеобразующее устройство снабжено средствами регулирования температуры водной дисперсионной среды и мономерной жидкости, введенными в линии их подачи.
Отличительной особенностью является также то, что в каплеобразующем устройстве часть стенки камеры над фильерой выполнена прозрачной и оно снабжено оптико-цифровым комплексом для визуального контроля процесса каплеобразования, который включает видеокамеру, установленную против прозрачной части стенки, соединенную с видеодисплеем, стробоскопический осветитель, установленный против прозрачной части стенки, соединенный через делитель частоты с генератором частоты и вибратором.
Процесс частичной полимеризации основан на проведении полимеризации полученных мономерных капель путем мягкого перемешивания в псевдоожиженном (обратном кипящем) слое, создаваемом потоком водной дисперсионной среды (ВДС) сверху вниз через обратный кипящий слой капель, образуемый за счет их меньшей плотности и плавучести, выносящей их вверх. Такое мягкое перемешивание не разрушает оболочку стабилизатора на поверхности капель и поэтому не происходит их слияние и дробление. Мягкое перемешивание в форполимеризаторе производится до тех пор, пока капли в ходе полимеризации не потеряют текучесть и клейкость, т.е. до степени конверсии от 3 до 10% (при наличии ди- и тривинильных компонентов в смеси мономеров), при которой вязкость капель становится достаточно высокой, чтобы при дальнейшем перемешивании мешалкой они могли сохранить свою форму. Оптимальные условия полимеризации и мягкое перемешивание в форполимеризаторе создаются при сочетании следующих факторов:
– температура форполимеризации 72-85°С;
– концентрация стабилизатора (кульминала) в водной дисперсионной среде -0,2±0,05% от объема ВДС;
– концентрация поливинилового мономера – 4-20% от общего веса мономеров;
– концентрация инициатора (перекись бензоила) в смеси мономеров 0,3-0,6 %;
– соотношение объемов мономерных капель и ВДС 1:(1-3);
– скорости подачи ВДС в расчете на пустое сечение трубчатого цилиндрического реактора от 9 до 15 м/час.
Температура нагрева эмульсии влияет на время пребывания капель в форполимеризаторе. Найдено, что при температуре 75°С время пребывания должно быть от 82 до 152 мин, при 80°С время пребывания от 40 до 108 мин, при 82,5°С время пребывания от 26 до 90 мин, при 85°С время пребывания от 19 до 74 мин.
Однако при малой температуре и большом времени пребывания капель в форполимеризаторе снижается производительность процесса.
А при большой температуре и малом времени пребывания капель в форполимеризаторе экзотермический процесс может стать трудноуправляемым, что может привести к вскипанию и выбросам реакционной массы.
Оптимальным сочетанием температуры и времени пребывания капель с достижением требуемой степени конверсии частичной полимеризации являются температура 80-82°С и время пребывания от 40 до 110 мин.
Таким образом, для достижения требуемой степени конверсии всех мономерных капель в процессе форполимеризации каждая капля должна находиться в первом реакторе от 40 до 110 мин. Это достигается увеличением длины трубчатого аппарата реактора. Установлено, что для достижения требуемых условий длина аппарата должна превышать его диаметр не менее, чем в 20 раз, возможно до 500 раз и предпочтительно может составлять (100-500):1.
Поэтому для осуществления процесса форполимеризации предлагается простая форма первого реактора в виде удлиненного трубчатого аппарата (корпуса), который может быть разделен на секции внутренними перегородками с отверстиями, которые предупреждают обратный проскок суспензии и направляют поток вниз.
Секционирование трубчатого аппарата форполимеризатора проводят путем выполнения в одном длинном трубчатом корпусе секций за счет установления внутренних перегородок с отверстием, как показано на фиг.5а, чтобы обеспечить преимущественно одностороннее движение эмульсии, без ее обратного тока либо один длинный трубчатый аппарат выполняют в виде каскада множества корпусов, каждый из которых имеет коническую верхнюю и нижнюю часть (5б). При этом в таких корпусах также могут быть выполнены внутренние перегородки (5в).
Таким образом, за счет удлинения корпуса первого реактора и его секцианирования удается избежать циркуляции раствора стабилизаторатора по обводной линии и применения дополнительного технологического оборудования на этапе частичной суспензионной полимеризации.
Изобретение поясняется прилагаемыми чертежами.
На фиг.1а дано изображение столбиков монокапель, образуемых из струй мономера при действии регулярной вибрации.
На фиг.1б показано изменение размеров капель при изменении частоты вибровозбуждения. Частота в Гц указана в верхней части каждого столбика капель.
На фиг.2а изображена диаграмма зоны монодиспергирования при одинаковой температуре потоков мономера и водной дисперсионной среды – 22°С.
На фиг.2б приведена та же диаграмма, но при разных температурах потоков: для водной дисперсионной среды – 78°С, для мономерной – 20°С.
На фиг.3 – схематичное изображение каплеобразующего устройства и оптико-цифрового комплекса для визуального контроля процесса каплеобразования.
На фиг.4 – принципиальная технологическая схема установки для производства монодисперсных частиц в непрерывном режиме.
На фиг.5 – схемы секционирования первого реактора (форполимеризатора).
Представленное на фиг.3 каплеобразующее устройство 1 содержит камеру 2 генерации капель, в нижней части которой размещена фильера 3 с множеством отверстий. Камера 2 имеет вход для подачи водной дисперсионной среды выше фильеры и вход для подачи смеси мономеров ниже фильеры. Вверху устройство 1 имеет вывод для отвода получаемой эмульсии капель мономера в водной дисперсионной среде. Под камерой 2 помещен вибратор 4, соединенный с генератором 5 частоты. Часть стенки камеры 2 над фильерой 3 выполнена прозрачной с круговым окошком 6, против которого с одной стороны установлена видеокамера 7, соединенная с видеодисплеем 8, и с другой стороны установлен стротоскопический осветитель 9, соединенный через делитель 10 частоты с генератором 5 частоты.
На фиг.4 представлена принципиальная технологическая схема установки для производства монодисперсных частиц в непрерывном режиме. Установка включает каплеобразующее устройство 1, содержащее фильеру 3 с множеством отверстий и вибратор 4. Через вход выше фильеры 3 в устройство подается водная дисперсионная среда, содержащая стабилизатор дисперсии, из емкости 11 с помощью насоса 12 через терморегулирующее устройство 13. И через вход ниже фильеры 3 в устройство подается жидкость, содержащая смесь мономеров, из емкости 14 с помощью насоса 15 через терморегулирующее устройство 16. Полученная суспензия мономерных капель в водной дисперсионной среде через выход верху устройства 1 подается на стадию предварительной полимеризации в первый реактор 17 (форполимеризатор) через терморегулирующее устройство 18. А также в первый реактор 17 подается водная дисперсионная среда из емкости 19 с помощью насоса 20. Первый реактор выполнен в виде одинаковых трубчатых корпусов 17, последовательно соединенных друг с другом в каскад. Из последнего корпуса каскада суспензия частично полимеризованных капель направляется во второй реактор на окончательную суспензионную полимеризацию и обработку готовых частиц. Второй реактор может быть выполнен из двух реакторов 21-22 с перемешивающими устройствами.
На фиг.5 представлены варианты изготовления первого реактора. Реактор может быть выполнен из множества секций в едином трубчатом корпусе (вариант а) в виде множества отдельных последовательно соединенных трубчатых корпусов, каждый из которых имеет коническую верхнюю и нижнюю части (вариант б). А также корпуса могут быть сами секционированы и равномерно вертикально смещены вниз относительно друг друга для обеспечения перетока суспензии самотеком за счет перепада уровней корпусов.
Способ приготовления полимерных монодисперсных частиц, таких как гранулы сополимеров для производства ионообменных смол, осуществляется следующим образом.
Пример 1.
Смесь мономеров из емкости 14 (фиг.4) насосом 15 через теплообменник 16 дозируется в количестве 28 мл/мин при температуре 18 -20°С в камеру 2 каплеобразующего устройства 1 под фильеру 3. В составе смеси используют стирол – 83,5%, дивинилбензол – 8%, этилстирол – 8% и перекись бензоила – 0,5%. Водная дисперсионная среда – 0,1% водный раствор стабилизатора – метилгидроксиэтилцеллюлозы (кульминала) в количестве 33 мл/мин при температуре 78°С из емкости 11 насосом 12 через теплообменник 13 дозируется в камеру 2 каплеобразующего устройства 1 в пространство над фильерой 3. Возбужденные вибрацией от электродинамического вибратора 4 при частоте 900 Гц струи смеси мономеров эжектризуются через отверстия фильеры 3 вверх в водную дисперсионную среду, где распадаются на монодисперсные капли в водной дисперсионной среде, образуя эмульсию. Фильера 3 имеет 8 отверстий диаметром 0,2 мм, у которых длина канала равна диаметру отверстия. Прозрачная часть стенки – смотровое окно 6 (фиг.3) камеры 2 позволяет фиксировать с помощью видеокамеры 7 технологический режим каплеобразования при освещении стробоскопом 9 и визуально наблюдать его на экране видеодисплея 8. Частота импульсов стробоскопа 9 выбирается кратной частоте возбуждения струй смеси мономеров при помощи делителя 10 частоты, который позволяет освещать участок каплеобразования и получать изображение, фиксируемое видеокамерой 7, каждой 4, 8, 16 или 32 капли. При этом на экране монитора наблюдается картина, изображенная на фиг.1. Благодаря регулярности (резонансности) процесса каждая последующая капля оказывается в пространстве и по времени в том же самом месте, что и предыдущая капля, благодаря чему картина на мониторе оказывается постоянной (застывшей). При таком режиме образуется столбик капель длиной до 10 мм. При нарушении режима столбик отсутствует либо не является монодисперсным (появление малых спутниковых капель, слившихся капель и т.п.).
Таким образом, устройство визуализации в виде оптико-цифрового комплекса позволяет проводить в режиме on-line регулирование расхода и скорости потока смеси мономеров, частоты вибрации, температуры обоих потоков (раствора стабилизатора и смеси мономеров) и др. и поддерживать режим в зоне монодиспергирования.
Благодаря разнице температур потоков смеси мономеров и раствора кульминала зона монодиспергирования значительно расширена, как показано на фиг.2б, что позволяет изменять размер капель, меняя частоту и скорость подачи смеси мономеров в диапазоне диаметров капель от 0,4 до 0,58 мм при диаметре отверстия фильеры, равном 0,2 мм (фиг.1б). На выходе из каплеобразующего устройства 1 к эмульсии непрерывно добавляется 0,5%-ный раствор стабилизатора в количестве 12-15 мл/мин, с тем чтобы концентрация кульминала в водной дисперсионной среде после смешения с эмульсией составляла 0,15-0,25%, после чего полученная эмульсия подогревается теплообменником 18 до температуры 75-78°С. В качестве теплообменника может использоваться первый корпус форполимеризатора 17, который в таком случае подогревается горячей водой с температурой до 120°С.
Процесс ведут путем непрерывного прохождения реакционной смеси по множеству последовательно соединенных корпусов первого реактора, обеспечивающих время пребывания в нем монодисперсных капель 40-110 мин.
Для проведения непрерывного процесса форполимеризации применялся аппарат из 4 трубчатых корпусов 17 (фиг.4) с внутренним диаметром 25 мм длиной одной секции 3 м. Корпуса соединены трубками и вертикально смещены относительно друг друга для перетока полимеризуемой эмульсии последовательно от 1-го до 4-го корпуса самотеком за счет перепада уровней корпусов на 150 мм (фиг.5б). Все корпуса находятся в одном общем кожухе и обогреваются горячей водой 75-76°С. Время пребывания капель в форполимеризаторе 40-110 мин, при этом степень конверсии составляет до 20%. Частично полимеризованные капли диаметром 0,48 мм на выходе из форполимеризатора имеют вязкоупругое состояние и не способны к дроблению или коалесценсии. Для предупреждения проскока незаполимеризованных капель использовали, с одной стороны, секционирование корпуса, применение от 2-х и более корпусов, и, с другой стороны, применение большой длины корпуса к его диаметру (100-500):1.
В реакторе обеспечивается равномерное по сечению (без байпасных потоков) кипение капель, для чего условная линейная скорость течения водной фазы (без учета объема капель мономеров) составляет от 9 до 15 м/час, а угол конусности верхней и нижней частей аппарата не более 30°(во избежание застойных зон на входе и выходе массы из реактора).
При данной конструкции первого реактора изменение температуры в секциях за счет тепловыделения реакции не превышает 1°С, т.е. удается отводить тепло без использования теплообменника на линии рецикла и получить частичную полимеризацию капель со степенью превращения (конверсии) до 10-20%.
На выходе реакционной массы из первого реактора 17 капли за счет процесса полимеризации при выбранных условиях становятся вязкоупругими, не способными к дроблению и слипанию. При этом степень полимеризации не превышает 20% и, следовательно, более 80% тепла реакции выделяется во втором реакторе. Количество тепла полимеризации для наиболее часто употребляемой смеси стирола и дивинилбензола таково, что вызывает вскипание реакционной массы и опасное повышение давления в аппаратуре. Поэтому во втором реакторе для интенсификации теплообмена требуется обеспечить сильное перемешивание и на этой стадии использованы стандартные реакторы с механическими мешалками.
Второй реактор разделен, как минимум, на две секции.
В первой секции 21 поддерживается температура от 72-82°С и достигается степень полимеризации до 90%.
Во второй секции 22 температура поддерживается более 90°С и полимеризация завершается до степени превращения более 99%.
Сополимеры, производимые по данной технологии и с использованием предлагаемой аппаратуры, применяются для производства ионообменных смол (как катионитов, так и анионитов), обладающих повышенными свойствами по прочности гранул в условиях эксплуатации и низким гидравлическим сопротивлением фильтрации.
Обеспечивая равномерную скорость фильтрации по всему сечению, фильтры, загруженные монодисперсными ионитами, имеют повышенную на 20% сорбционную емкость до проскока и сокращают расход регенирирующих веществ также на 20% по сравнению с фильтрами, загруженными полидисперсными ионообменными смолами.
Формула изобретения
1. Способ производства полимерных монодисперсных частиц суспензионной полимеризацией, включающий стадии: приготовление монодисперсных капель путем введения в камеру каплеобразующего устройства водной дисперсионной среды, содержащей стабилизатор дисперсии и образующей непрерывную фазу, эжектирование в водную дисперсионную среду гидрофобной жидкости мономера через отверстия фильеры струями вверх при действии регулярной вибрации для образования жидких капель мономера преимущественно равного размера в водной дисперсионной среде; проведение предварительной полимеризации путем введения в первый реактор полученных жидких капель мономера в водной дисперсионной среде, проведения полимеризации в псевдоожиженном слое с получением суспензии частично полимеризованных капель мономера в водной дисперсионной среде до степени, когда капли уже не могут сливаться или разбиваться; проведение окончательной суспензионной полимеризации при интенсивном перемешивании во втором реакторе, отличающийся тем, что на стадии приготовления монодисперсных капель водную дисперсионную среду вводят в камеру каплеобразующего устройства при температуре 60-90°С, а гидрофобную жидкость мономера вводят в камеру каплеобразующего устройства при температуре 5-25°С или температуре окружающей среды.
2. Способ по п.1, отличающийся тем, что температуру в камере каплеобразующего устройства устанавливают в пределах 40-60°С.
3. Способ по п.1, отличающийся тем, что на стадии формирования капель в качестве стабилизатора капель в водной дисперсионной среде используют метилгидроксиэтилцеллюлозу при концентрации от 0,05 до 0,2% от объема водной дисперсионной среды.
4. Способ по п.1, отличающийся тем, что соотношение объемов гидрофобной жидкости мономера к водной дисперсионной среде составляет от 1:1 до 1:3 соответственно на всех стадиях.
5. Способ по п.1, отличающийся тем, что при линейной скорости истечения струи мономера в водную дисперсионную среду в пределах от 1,2 до 2,2 м/с регулярную вибрацию в каплеобразующем устройстве ведут на частоте в диапазоне от 500 до 1500 Гц.
6. Способ по п.1, отличающийся тем, что осуществляют контроль процесса образования капель путем визуализации с помощью оптико-цифрового комплекса.
7. Установка для производства полимерных монодисперсных частиц суспензионной полимеризацией, включающая каплеобразующее устройство, содержащее камеру для образования монодисперсных капель, фильеру с множеством отверстий для эжектирования струй гидрофобной жидкости мономера, средство для вибрации при эжектировании струй, а также вход для линии подачи водной дисперсионной среды выше фильеры, вход для линии введения гидрофобной жидкости мономера ниже фильеры и выход в верхней части камеры для отвода эмульсии образованных капель мономера в водной дисперсионной среде;
первый реактор, содержащий вход в верхней части для введения эмульсии капель мономера в водной дисперсионной среде, и выход в нижней части для вывода суспензии частично полимеризованных мономерных капель в водной дисперсионной среде;
и второй реактор, содержащий вход для введения суспензии частично полимеризованных мономерных капель в водной дисперсионной среде, средство для интенсивного перемешивания суспензии и выход для отвода целевого продукта,
отличающаяся тем, что первый реактор выполнен в виде, по крайней мере, одного трубчатого цилиндрического корпуса с коническими верхней и нижней частями при отношении длины корпуса к диаметру не менее 20:1 соответственно.
8. Установка по п.7, отличающаяся тем, что отношение длины к диаметру первого реактора составляет предпочтительно (100-500):1 соответственно.
9. Установка по п.7, отличающаяся тем, что трубчатый цилиндрический корпус первого реактора выполнен разделенным внутренними перегородками на секции.
10. Установка по п.7, отличающаяся тем, что конические верхние и нижние части имеют угол конусности не более 30°.
11. Установка по п.9, отличающаяся тем, что первый реактор выполнен в виде каскада последовательно соединенных корпусов с равномерным вертикальным смещением последовательных корпусов вниз относительно друг друга.
12. Установка по п.7, отличающаяся тем, что каплеобразующее устройство снабжено средствами регулирования температуры водной дисперсионной среды и мономерной жидкости, введенными в линии их подачи.
13. Установка по п.7, отличающаяся тем, что в каплеобразующем устройстве часть стенки камеры над фильерой выполнена прозрачной и оно снабжено оптико-цифровым комплексом для визуального контроля процесса каплеобразования, который включает видеокамеру, установленную против прозрачной части стенки, соединенную с видеодисплеем, стробоскопический осветитель, установленный против прозрачной части стенки, соединенный через делитель частоты с генератором частоты и вибратором.
РИСУНКИ
|
|