|
(21), (22) Заявка: 2006124610/03, 10.07.2006
(24) Дата начала отсчета срока действия патента:
10.07.2006
(46) Опубликовано: 10.12.2007
(56) Список документов, цитированных в отчете о поиске:
SU 1305043 A1, 23.04.1987. SU 1052390 A1, 07.11.1983. RU 2003136887 A, 10.06.2005. RU 2188177 С2, 27.08.2002. SU 1794680 A1, 15.02.1993. SU 1787792 A1, 15.01.1993.
Адрес для переписки:
170044, г.Тверь, ул. Вагжанова, 14, АОЗТ ЦПТУ “Эффект”
|
(72) Автор(ы):
Какалия Андрей Викторович (RU), Мальков Лев Борисович (RU), Секержицкий Мечислав Антонович (RU), Степанов Валентин Леонидович (RU)
(73) Патентообладатель(и):
Какалия Андрей Викторович (RU), Мальков Лев Борисович (RU), Секержицкий Мечислав Антонович (RU), Степанов Валентин Леонидович (RU), Митрофаненко Николай Николаевич (RU), Секержицкий Антон Мечиславович (RU)
|
(54) ТЕХНОЛОГИЧЕСКАЯ ЛИНИЯ ДЛЯ ПРОИЗВОДСТВА ПРЕССОВАННЫХ СТРОИТЕЛЬНЫХ МАТЕРИАЛОВ
(57) Реферат:
Изобретение относится к области строительства, а более конкретно – к производству прессованных строительных материалов, например кирпича. Технологическая линия для производства прессованных строительных материалов содержит участки подачи сырьевых компонентов с бункерами и дозаторами, участок подготовки вяжущего, включающий смесители, гранулятор, аппарат для термической обработки гранул, гидратор для гашения извести, участок приготовления формовочной смеси, участок готовой продукции, включающий пресс, автоклав и транспортные средства. При этом участки подачи сырьевых компонентов дополнительно содержат смонтированные на бункерах рыхлители с колосниковой решеткой, имеющей расстояние между колосниками 50÷100 мм, камневыделительные вальцы, молотковую дробилку, дезинтегратор, на выходе из бункеров глинистого сырья, известняковых отходов, золы ТЭС соответственно, а также весовые дозаторы непрерывного действия. Участок для приготовления вяжущего содержит в качестве гидратора для гашения извести реактор с тарельчатым питателем, а в качестве аппарата для термической обработки гранул – агломерационную машину и, дополнительно, стержневую мельницу глубокого измельчения. Участок для приготовления формовочной смеси содержит стержневой смеситель-растиратель и, дополнительно, снабжен глиноболтушкой и шлам-бассейном с рамной мешалкой. Технический результат технологической схемы по производству прессованных изделий заключается в получении однородной смеси компонентов сырья на участках подачи сырья и приготовления вяжущего, в практически полном гашении гранул вяжущего в соответствии заданной норме соотношения компонентов, а также в повышении эффективности, экономичности производства и, в итоге, качества готовой продукции при определенном снижении стоимости ее производства. 1 ил., 1 табл.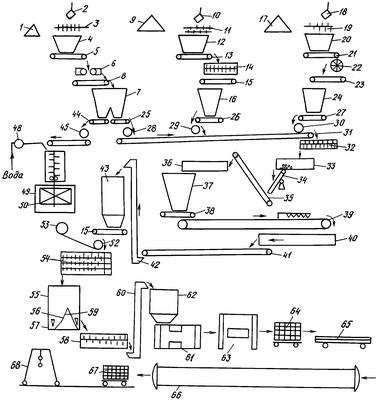
Технологическая линия относится к области строительства: производству прессованных строительных материалов, например кирпича.
Известна технологическая линия для производства кирпича (Авт. свид. СССР №1305043, кл. В28В 15/00, Бюл. №15, 1987, прототип).
Линия включает:
– Участки подачи сырьевых компонентов, оснащенные бункерами глинистого сырья, известняковых отходов и золы ТЭС и дозаторами;
– участок приготовления вяжущего, содержащий смеситель для перемешивания сырьевых компонентов, гранулятор, печь для обжига в качестве аппарата для термической обработки гранул, охладитель гранул, смеситель для получения формовочной массы, смеситель-бегуны для выравнивания ее состава;
– участок для приготовления формовочной смеси;
– участок готовой продукции, включающий пресс, автоклав и транспортные средства.
Недостатки известной линии:
– участки подачи сырьевых компонентов: грубый помол, неоднородность сырья, наличие каменистых включений, большое отклонение от заданной нормы соотношения компонентов на входе в смеситель для перемешивания сырьевых компонентов;
– участок для приготовления вяжущего: плохое перемешивание компонентов смеси на входе в печь обжига (т.н. шихты), двухступенчатое гашение гранул вяжущего, неполное гашение гранул, неоднородность формовочной смеси, недостаточная эффективность и высокая стоимость аппарата для термической обработки гранул;
– участок для приготовления формовочной смеси: гашение гранулированного вяжущего в гидраторе-мешалке приводит к резкому увеличению удельной поверхности и значительному затруднению перемешивания гашеного вяжущего с дополнительным количеством глинистого сырья, не прошедшего процесса измельчения, что не позволяет получить однородную формовочную смесь, даже учитывая применение для обработки смеси растирочных бегунов и активатора.
Технический результат технологической схемы по производству прессованных изделий заключается в получении однородной смеси компонентов сырья на участках подачи сырья и приготовления вяжущего, в практически полном гашении гранул вяжущего в соответствии заданной норме соотношения компонентов, в повышении эффективности, экономичности производства и, в итоге, качества готовой продукции при определенном снижении стоимости ее производства.
Технический результат достигается тем, что участки подачи сырьевых компонентов дополнительно содержат смонтированные на бункерах разрыхлители с колосниковой решеткой, имеющей расстояние между колосниками 50÷100 мм, камневыделительные вальцы, молотковую дробилку, дезинтегратор на выходе из бункеров глинистого сырья, известняковых отходов, золы ТЭС соответственно, и весовые дозаторы непрерывного действия, а участок приготовления вяжущего содержит в качестве гидратора для гашения извести реактор с тарельчатым питателем, а в качестве аппарата для термической обработки гранул агломерационную машину и, дополнительно, стержневую мельницу; участок для приготовления формовочной смеси – стержневой смеситель-растиратель и дополнительно снабжен глиноболтушкой и шлам-бассейном с рамной мешалкой.
Исследованием уровня техники установлено, что такого рода технологических линий для производства прессованных строительных материалов не обнаруживается.
Известна технологическая линия для производства кирпича (Авт. свид. СССР №1305043, кл. В28В 15/00).
Однако сравнение свойств совокупности признаков известной и заявляемой линий показывает, что:
– в известной технологической линии отсутствуют рыхлители сырьевых материалов на приемных бункерах, что не ограничивает поступление в рабочий объем бункеров конгломератов значительных размеров (более 100÷500 мм), особенно в зимнее время, при этом затрудняется прохождение материалов через питатели, а в заявляемой линии на бункерах установлены рыхлители с колосниковой решеткой – при расстоянии между колосниками 50÷100 мм, чем регламентированы размеры комьев сырья;
– в известной технологической линии на участке подачи глинистого сырья установлены вальцы грубого помола, не выполняющие функции удаления из суглинка крупных включений, без чего вальцы грубого помола не работоспособны, а в заявляемой линии на участке подачи глинистого сырья установлены камневыделительные вальцы, выполняющие одновременно функции удаления крупных включений и грубого измельчения;
– в известной технологической линии отсутствует оборудование по измельчению золы и известняка после приемных бункеров, а в заявляемой линии установлены дезинтегратор для первичного измельчения золы и молотковая дробилка для первичного измельчения известняка, что существенно улучшает процесс окончательного измельчения на заключительном этапе;
– в известной технологической линии применены питатели для подачи сырьевых материалов в производство, при этом не могут быть учтены влажность и плотность материала, а в заявляемой линии применены весовые дозаторы непрерывного действия с точностью до 1÷2%;
– в известной технологической линии для смешивания сырьевых компонентов шихты применяется смеситель непрерывного действия, как правило, лопастной, который не способен обеспечить необходимую однородность смешивания, в особенности не измельченных предварительно материалов, а в заявляемой линии применена стержневая мельница глубокого измельчения и смешивания;
– в известной технологической линии для обжига вяжущего применена вращающаяся печь, а в заявляемой линии – агломерационная машина с высокой энергетической и экологической эффективностью;
– в известной технологической линии обожженное вяжущее после охлаждения увлажняется и подвергается гашению в гидраторе-мешалке с последующим смешиванием с дополнительным количеством глинистого сырья в его естественном состоянии, а в заявляемой линии вяжущее и вводно-глиняная суспензия (шликер) с помощью весовых дозаторов смешивается в лопастном смесителе непрерывного действия в течение необходимого времени (от 1 часа);
– в известной технологической линии для обработки формовочной смеси перед прессованием применены бегуны и активатор с попыткой компенсировать издержки предыдущей обработки сырья, шихты и вяжущего, а в заявляемой линии применен стержневой смеситель-растиратель.
Сущность изобретения заключается в следующем.
Установленные на приемных бункерах рыхлители в сочетании с колосниковыми решетками обеспечивают первичное измельчение сырья с поступлением в рабочий объем бункеров комьев размером менее 100 мм.
Применение вместо вальцов грубого помола камневыделительных вальцов обеспечивает удаление из глинистого сырья крупных каменистых включений с одновременным выполнением функции грубого помола.
Применение для вторичного измельчения золы ТЭС и известняка, соответственно дезинтегратора и молотковой дробилки позволяет повысить эффективность подготовки сырья к следующим процессам.
Применение весовых дозаторов непрерывного действия позволяет повысить точность дозирования сырья до 1÷2% вместо 7÷15% для питателей объемной подачи.
Применение стержневой мельницы на заключительном этапе подготовки шихты позволяет за счет глубокого измельчения и смешивания предельно повысить качество шихты перед обжигом с доведением крупности зерен до 2÷3 мм.
Применение для обжига вяжущего агломерационной машины вместо вращающейся печи позволяет повысить теплоэффективность процесса обжига в 1,5 раза со снижением расхода топлива с 270 до 180 кг на 1 т вяжущего.
Смешивание негашеного вяжущего с глинистым сырьем с получением водной суспензии (шликера), содержащей необходимое количество воды затворения для последующего гашения извести в вяжущем после обжига, позволяет существенно повысить однородность формовочной смеси. Формовочная смесь приготавливается из шликера, изготавливаемого в глиноболтушке с применением весовых дозаторов воды и глины, и вяжущего, также дозируемого весовыми дозаторами, с последующим гашением в реакторе непрерывного действия, причем для обеспечения равномерности истечения смеси на донном питателе установлены отборочные скребки и конус по центру дискового питателя, а для глубокого перемешивания формовочной смеси с ее доувлажнением применен стержневой смеситель-растиратель с последующим прессование и тепловлажностной обработкой кирпича известным способом.
Применение реактора для гашения извести позволяет обеспечить необходимое время гашения смеси – не менее 1 часа, чем исключается “недогас” извести в процессе ее гашения в реакторе, а наличие на вращающейся тарелке питателя конуса и скребков позволяет обеспечить равномерность разгрузки смеси по сечению реактора.
Применение стержневого смесителя-растирателя взамен бегунов и активатора значительно упрощает процесс перемешивания смеси после ее гашения, позволяет измельчить комья смеси и доувлажнить ее до необходимой для прессования влажности (6÷8%).
В совокупности изложенное позволяет существенно улучшить качество подготовки, переработки, дозирования и приготовления шихты, повысить эффективность процесса приготовления формовочной смеси с получением изделий с оптимальными свойствами и физико-механическими показателями.
В таблице 1 представлены результаты физико-механических испытаний кирпича и ячеистых материалов, изготовленных на заявляемой технологической линии.
Состав оборудования, входящего в заявляемую линию, приведен в блок-схеме на чертеже.
1 – склад глинистого сырья, 2 – грейфер глинистого сырья, 3 – рыхлитель глинистого сырья, 4 – приемный бункер глинистого сырья, 5 – питатель приемного бункера глинистого сырья, 6 – камневыделительные вальцы, 7 – двухсекционный бункер, 8 – ленточный питатель двухсекционного бункера, 9 – склад золы ТЭС, 10 – грейфер золы ТЭС, 11 – рыхлитель золы ТЭС, 12 – приемный бункер золы ТЭС, 13 – питатель приемного бункера золы ТЭС, 14 – дезинтегратор, 15 – питатель дезинтегратора, 16 – расходный бункер золы ТЭС, 17 – склад известняковых отходов, 18 – грейфер известняковых отходов, 19 – рыхлитель известняковых отходов, 20 – приемный бункер известняковых отходов, 21 – питатель приемного бункера известняковых отходов, 22 – молотковая дробилка, 23 – питатель молотковой дробилки, 24 – расходный бункер известняковых отходов, 25 – питатель двухсекционного бункера глинистого сырья, 26 – питатель расходного бункера золы ТЭС, 27 – питатель расходного бункера известняковых отходов, 28 – весовой дозатор питателя двухсекционного бункера глинистого сырья, 29 – весовой дозатор питателя расходного бункера золы ТЭС, 30 – весовой дозатор питателя расходного бункера известняковых отходов, 31 – сборный конвейер, 32 – смеситель переработанных сырьевых материалов, 33 – стержневая мельница сырьевых материалов, 34 – гранулятор, 35 – конвейер гранулятора, 36 – сушилка, 37 – накопительный бункер, 38 – питатель накопительного бункера, 39 – агломерационная машина, 40 – холодильник, 41 – конвейер холодильника, 42 – элеватор гранул, 43 – расходный бункер гранул, 44 – питатель глинистого сырья, 45 – весовой дозатор питателя глинистого сырья, 46 – конвейер весового дозатора питателя глинистого сырья, 47 – глиноболтушка, 48 – ротационный дозатор, 49 – шлам-бассейн, 50 – рамная мешалка, 51 – питатель вяжущего, 52 – весовой дозатор вяжущего, 53 – дозатор шликера, 54 – лопастной смеситель, 55 – реактор, 56 – скребки тарельчатого питателя, 57 – тарельчатый питатель, 58 – стержневой смеситель-растиратель, 59 – конус тарельчатого питателя, 60 – элеватор, 61 – гидравлический пресс, 62 – расходный бункер гидравлического пресса, 63 – автомат-укладчик, 64 – вагонетка, 65 – электропередаточная тележка, 66 – автоклав, 67 – выкаточная лебедка, 68 – кран.
Технологическая линия для производства прессованных строительных материалов работает следующим образом.
Глинистое сырье из склада 1 грейфером 2 через рыхлитель 3, измельчающий крупные комья, поступает в приемный бункер 4 с питателем 5, из него сырье проходит через камневыделительные вальцы 6, от них – в двухсекционный бункер 7 с помощью ленточного питателя 8.
Зола ТЭС из склада 9 грейфером 10 через рыхлитель 11 поступает в приемный бункер 12, из которого питателем 13 подается в дезинтегратор 14. Измельченная зола питателем 15 загружается в расходный бункер 16.
Известняковые отходы из склада 17 грейфером 18 через рыхлитель 19 поступают в приемный бункер 20, из которого питателем 21 подаются в молотковую дробилку 22. Измельченный известняк питателем 23 загружается в расходный бункер 24.
Переработанные сырьевые материалы: глинистые отходы, зола ТЭС и известняк из бункеров 7, 16 и 24 соответственно питателями 25, 26, 27 и весовыми дозаторами 28, 29 и 30 в заданном весовом соотношении подаются в сборный конвейер 31, из него – в смеситель 32. Предварительно перемешанная смесь поступает в стержневую мельницу 33 глубокого измельчения и смешивания с доувлажнением до 18÷22%.
Соотношение компонентов смеси: зола – 50%, глинистые и известняковые отходы – по 25%.
Увлажненная смесь поступает в гранулятор 34, из которого конвейером 35 гранулы подаются в сушилку 36, подсушенные гранулы поступают в накопительный бункер 37, из него питателем 38 гранулы укладываются в тележки агломерационной машины 39, где обжигаются при температуре 950÷1150°С. Обожженные гранулы направляются в холодильник 40, из которого охлажденное до 100÷150°С вяжущее конвейером 41 и элеватором 42 загружается в расходный бункер 43.
Дополнительное количество глинистого сырья 10÷15% отбирается из бункера 7 питателем 44 и через весовой дозатор 45 конвейером 46 загружается в глиноболтушку 47, куда также поступает вода через ротационный дозатор 48. Приготовленная глино-водная суспензия (шликер) поступает в шлам-бассейн 49 с рамной мешалкой 50.
Вяжущее с помощью питателя 51, весового дозатора 52, а также шликер с помощью весового ковшевого дозатора 53 загружаются в лопастной смеситель 54.
Приготовленная смесь с влажностью 18÷20% загружается в реактор 55, в котором осуществляется гашение извести в вяжущем в течение не менее 1 часа. Гашеная смесь с влажностью 1÷2% и температурой 80÷95°С с помощью скребков 56 тарельчатого питателя 57 подается в стержневой смеситель-растиратель 58, в котором измельчаются комья смеси с ее доувлажнением до 6÷8%.
С помощью конуса 59 тарельчатого питателя 57 достигается равномерное по сечению и объему перемещение смеси в реакторе, чем обеспечивается равномерность ее гашения.
Готовая смесь элеватором 60 подается на гидравлический пресс 61 с расходным бункером 62. Отпрессованный сырец автоматом-укладчиком 63 укладывается в штабель на автоклавную вагонетку 64, которая с помощью электропередаточной тележки 65 загружается в автоклав 66, в котором сырец подвергается термообработке в сухим насыщенным паром при температуре 174÷210°С, давлении 8÷16 атм в течение 1,5+8+1 часов.
Готовый кирпич выкаточной лебедкой 67 выгружается на склад готовой продукции под кран 68.
Таблица 1 |
Характеристика производства кирпича на основе керамического вяжущего автоклавного твердения в сравнении с традиционным |
№ п/п |
Показатели |
Един. измер. |
Кирпич силикатный |
Кирпич керамический |
1. |
Сырье |
– |
Первичное: – песок кварцевый – известняк (известь) |
Вторичное: |
– зола ТЭЦ |
– суглинок – отсев известняка |
2. |
Вид кирпича |
– |
рядовой |
лицевой |
3. |
Размеры |
мм |
250×120×(65,88) |
250×120×(65,88; 138) |
4. |
Пустотность |
% |
8÷12 |
22,5÷25 |
5. |
Объемная масса |
кг/м3 |
|
|
|
– в плотном теле |
|
2000 |
1600 |
|
– пустотелость |
|
1800 |
1450 |
6. |
Теплопроводность кирпича в плотном теле |
 |
0,76 |
0,55 |
7. |
Марка средняя |
кг/см2 |
125 |
125 |
8. |
Морозостойкость |
цикл |
15 |
35 |
9. |
Расход теплоэнергии |
 |
330 |
270 |
10. |
Расход электроэнергии |
 |
55 |
50 |
11. |
Себестоимость |
 |
2200 |
2200 |
12. |
Цена реализации (на сентябрь 2003 г.) |
 |
2600 |
6000 |
Формула изобретения
Технологическая линия для производства прессованных строительных материалов, содержащая участки подачи сырьевых компонентов с бункерами и дозаторами, участок подготовки вяжущего, включающий смесители, гранулятор, аппарат для термической обработки гранул, гидратор для гашения извести, участок приготовления формовочной смеси, участок готовой продукции, включающий пресс, автоклав и транспортные средства, отличающаяся тем, что участки подачи сырьевых компонентов дополнительно содержат смонтированные на бункерах рыхлители с колосниковой решеткой, имеющей расстояние между колосниками 50÷100 мм, а также камневыделительные вальцы, молотковую дробилку, дезинтегратор на выходе из бункеров глинистого сырья, известняковых отходов, золы ТЭС, соответственно, и весовые дозаторы непрерывного действия, участок для приготовления вяжущего содержит в качестве гидратора для гашения извести реактор с тарельчатым питателем, а в качестве аппарата для термической обработки гранул – агломерационную машину и дополнительно стержневую мельницу глубокого измельчения, участок для приготовления формовочной смеси содержит стержневой смеситель-растиратель и дополнительно снабжен глиноболтушкой и шлам-бассейном с рамной мешалкой.
РИСУНКИ
MM4A – Досрочное прекращение действия патента СССР или патента Российской Федерации на изобретение из-за неуплаты в установленный срок пошлины за поддержание патента в силе
Дата прекращения действия патента: 11.07.2008
Извещение опубликовано: 10.07.2010 БИ: 19/2010
|
|